零部件标准化流程图
标准化工作流程图
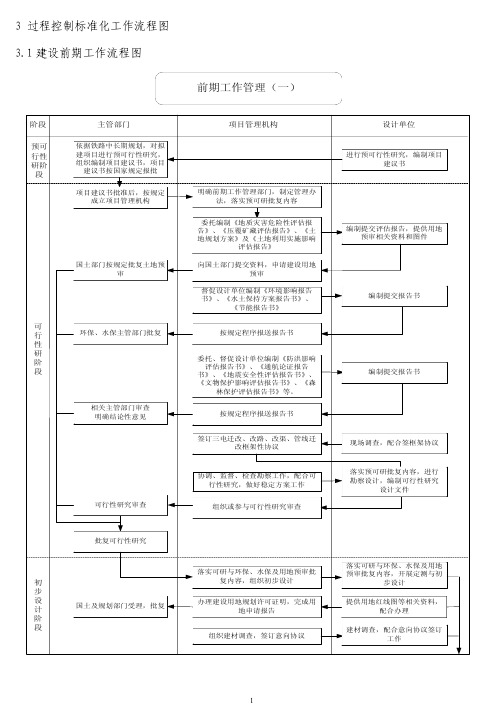
题问关有迁拆地征调协
迁拆地征施实 府政民人上以级县托委
沟界地挖、桩 界地放�核复场现
图线 红 地 用 供 提� 桩 交 场 现
桩交场现织组
备 准 工 施
订签的 要 纪 或 议 协性 施 实 与 参
议协施实迁拆地征实落门 部关有府政方地促督�法 办、准标偿补迁拆地征定 商府政方地与�文批地用 目项设建、要纪部省据依
果结量测报汇�量 测通贯责负�桩交 量测、底交术技加参
料资量测正校�桩 交量测、底交术技责负
纸图计设 核复�量测通贯线全、桩 交量测、底交术技织组
告 报收验工竣保环制编托委
计设程工保环善完
题 问 缺 漏保 环 决 解调 协
况情施 实的施措保环结总和查检 理 监 常日 行 进 量 质程工其及容内工 施保环的位单工施 对责负�案方和施 措保环期工施据根 工 施织组计设织组工施的 准批照按�求要》书告 报为行境环《行执格严 施措保环的中 计设织组工施性施实批审
点SPG级B设布道轨砟有 �点SPG级A设布道轨砟无 ,路线上以及h/mk002于对
点SPG级B设布织组道轨砟 有�点SPG级A设布织组道轨 砟无,路线上以及h/mk002于对
究 研 性 行 可
订签的议协架框与参 �料资术技供提�测初
议协架框等移迁线管、渠 改、路改、移改电三订签位 单权产关相与位单计设织组
段 阶 施 实
同合工施入纳容内要重为 作期工、量质的程工保环将
报上并见意成形�章篇 护保境环件文计设步初审预
用费及施措关有实 落�章篇护保境环制编
章 篇护保境环制编织组复批按
段 阶 设 初
请申查审出提门部管主向
点重 的护保境环解了查调与参
�告报项 专区感敏含�告报价评 境环制编并托委受接
零部件APQP流程图

手工件选厂
部
工装件 选厂
订单
锁定设 计数据 和图纸
样件鉴定
试生产订单
小批 鉴定
产能分 析报告
APQP启
APQP启动
FTF会
S
动会
会议纪要
议纪要
T
A
APQP启
动表格
供应商APQP小 组成员名单
图纸问 题清单
供应商质量保证 责任人申报书
FTF会 议纪要
供应商小组可行性承诺
过程流程图(初始)
供 应 商
供应商设备、工装、 模具清单(初始)
心
关重
工装件图纸
手工件图纸(更改单)
特性
(更改单)
采 购
手工件选厂
部
工装件 选厂
订单
锁定设 计数据 和图纸
样件鉴定
试生产订单
小批 鉴定
产能分 析报告
APQP启
APQP启动
FTF会
S
动会
会议纪要
议纪要
T
A
APQP启
动表格
供应商APQP小 组成员名单
图纸问 题清单
供应商质量保证 责任人申报书
供应商小组可行性承诺
第二次拜访 试生产监察
监察报告
已开启 的质量 问题跟 踪、闭
环
PSW签署 (2阶段)
过程流程图 (试生产) PFMEA(试生产) 控制计划(试生产) 检查基准书 分供方清单
DV试验报告
PV试验计划 ISIR报告
初始过程研究 测量系统分析
作业指导书 防错技术及装置
PV试 验报告
过程流 程图
PFMEA
控制 计划
CC
VS
SKO
标准化[SOP]流程图制作规范方案
![标准化[SOP]流程图制作规范方案](https://img.taocdn.com/s3/m/40da6c1d5627a5e9856a561252d380eb629423e9.png)
标准化<SOP>流程图制作规范一、前言二、目的三、流程图符号四、流程图结构说明五、流程图绘製原则六、范例一,前言标准作业流程的意义「标准作业流程」<SOP>是企业界常用的一种作业方法, 其目的在使每一项作业流程均能清楚呈现,任何人只要看到流程图,便能一目了然, 有助于相关作业人员对整体工作流程的掌握.製作流程图的优点:<一>所有流程一目了然,工作人员能掌握全局.<二>更换人手时,按图索骥,容易上手.<三>所有流程在绘製时,很容易发现疏失之处,可适时予以调整更正,使各项作业更为严谨. 二.目的一、为建立本部作业标准化<SOP>流程图之可读性及一致性,参考美国ANSI系统流程图标准符号,及道勤企业管理顾问**「效率会议」标准流程,製作符号及范例.二、本规范流程图绘製,採用由上而下结构化程式设计<Top-down Structured Programming>观念.三、对于製作流程图共通性目标,本规范亦列出流程图绘製原则.三.流程图符号选取图示电脑的Word 软体中,工具列─插入─图片─快取图案─流程图符号名称意义准备作业<Start> 流程图开始处理<Process> 处理程序决策<Decision> 不同方案选择终止<END> 流程图终止路径<Path> 指示路径方向文件<Document> 输入或输出文件使用某一已定义的处理程序预定义处理〕Predefined Process>连接<Connector> 流程图向另一流程图的出口;或从另一地方的入口批注〕Comment〔表示附注说明的用四.流程图结构说明顺序结构<Sequence>图形:意义:处理程序顺序进行.语法:DO处理程序1 THEN DO处理程序2实例:运用时机:本结构适用于具有顺序发生特性的处理程序,而绘制图形上下顺序就是处理程序进行顺序.选择结构<Selection>A. 二元选择结构<基本结构>图形:意义:流程依据某些条件,分别进行不同处理程序.语法:IF 条件 THEN DO 处理程序1 ELSE DO 处理程序2实例:运用时机:1.2.3.图形:意义:流程依据某些条件,分别进行不同处理程序.语法:FOR 条件PCASE 1 DO 处理程序1CASE 2 DO 处理程序2CASE n DO 处理程序n实例:运用时机:·本结构是二元选择结构的变化,流程依据选择或决策结果,择一进行不同处理程序.·选择或决策结果路径名称,可用不同文字,来叙明不同路径的处理程序.A. REPEAT-UNTIL结构图形:意义:重复执行处理程序直到满足某一条件为止,即直到条件变成真<True>为止.语法:REPEAT-UNTIL 条件 DO 处理程序实例:运用时机:·本结构适用于处理程序依据条件需重复执行的情况,而当停止继续执行的条件成立后,即离开重复执行循环至下一个流程.·本重复结构是先执行处理程序,再判断条件是否要继续执行.图形:意义:除了在执行处理程序的前,得先测试条件外,DO-WHILE结构和REPEAT-UNTIL结构很相似,若条件为伪<False>,就不再执行处理程序.语法:DO-WHILE 条件 DO 处理程序实例:运用时机:·本结构适用于处理程序依据条件需重复执行的情况,而当停止继续执行的条件成立后,即离开重复执行循环至下一个流程.·本重复结构是先判断条件是否成立,再执行处理程序.五.流程图绘制原则行文简洁流程图分中心主轴及旁支说明,主轴内各流程图文字请键入KEY WORD,各细部流程若需补充说明,请精简条列以虚线旁支说明,每点以不超过二行为原则<请见范例>.各项流程有办理部门者应注明.各项步骤有选择或决策结果,如"可、否"、"通过、不通过"或其它相对文字时,请回馈校正流程是否有遗漏,以避免悬而未决状况.注意各流程图组合的合理性、并考虑是否需建置分表或合成简要总表,分表与总表应以符号、颜色或字段等区隔,使人一目了然.流程图符号绘制排列顺序,为由上而下,由左而右.处理程序请以阿拉伯数字,由1开始,依处理程序排列顺序编号,并以文字依处理程序功能命名.文字命名部份,以"动词+受词"及简明扼要叙述为原则.若须表示处理程序的单位,则在编号的后面加上单位名称.[实例]处理程序若属并行操作关系,其编号请多加一码<如8.1,8.2等依序编号>,并宜排列在流程图同一高度,而下一个处理程序编号,则自动增加1<如9>.[实例]处理程序须以单一入口与单一出口<Single-Entry, Single-Exit>特性绘制.反折先不要画到作业单元上,而要画到路径线处.[实例]流程图一页放不下时,可使用连接符号连接下一页流程图.同一页流程图中,若流程较复杂,亦可使用连接符号来表明流程连接性.连接符号内请以数字标示,以资区别.同时注意流程图的目的是快速展示业务逻辑,不要画成蜘蛛网那反而成了迷宫阻碍快速理解便与流程图的初衷背道而驰了,新手容易犯此类问题.相同流程图符号宜大小一致.路径符号宜避免互相交叉.[实例]同一路径符号的指示箭头应只有一个[实例]开始符号在流程图中只能出现一次,但结束符号则不限.若流程图能一目了然,则开始符号及结束符号可省略.选择结构及重复结构的选择或决策条件,文字叙述应简明清晰,路径并加注"是"及"否"或其它相对性文字指示说明.流程图中若有参考到其它已定义流程,可使用已定义处理程序符号,不必重复绘制.[实例]流程图若一页绘制不下,可以使用阶层性分页绘制方式,并在处理程序编号上表示其阶层性. 第二页:处理程序2的阶层性分页绘制范例一二三四五。
新产品标准化作业流程图

参考文件/ 使用表单 /
产品结构评审 OK
产品工程师 各相关部门
会议记录
5.3
打功能手板
模具可行性评审
产品工程师 模具工程师 各相关部门
制样报告 会议记录
5.4
产品公差分析
产品工程师 各相关部门
/
5.5
2D图纸转换(含材料/
产品工程师 产品工程师 各相关部门 产品工程师 手板供应商
/
5.6
产品图(3D/2D)最终评审
试装样品确
出ECN改模
5.18
样品评审
试模
产品工程师 各相关部门
NG
OK
5.19 出ECN改模
全方位测试 NG (可靠性测试)
OK
产品工程师 TQC
试模
所有半成品物
产品工程师
5.20
小批量试产
产品工程师 各相关部门
1.模具组立调试好后,模具师傅开出试模 申请单给PMC安排试模,试模申请单需分 别发放给生产部、品保部、工程部等; 试模申请单 2.试模时,各部门相关人员需到试模现场 试模报告(含尺 进行跟进和确认,注塑调机技术员负责对 寸检验记录、成 试模时的成型参数进行调整,以使试出的 型参数等) 产品达到最佳效果,并记录相关参数和问 题点; 1.模具工程师和模具师傅需对模具结构和 产品结构进行确认; 2.模具QC需全方位跟进,并对试出的产品 试模报告 重点尺寸进行测量和产品结构、外观的确 认等; 1.模具工程师确认产品OK后,安排送5啤 样品给品保部实验室做全尺寸测量,所送 测量样品必须是合格的;2.品保部测试员 参照产品2D图对产品进行全尺寸测量,并 测试申请单 记录真实数据;3.产品工程师对试模合格 尺寸测量报告 的产品进行试装样品,以确认产品的装配 ECN 效果和性能;4.产品确认不合格需安排修 /改模的,由产品工程师开出ECN通知模具 部进行改模,模具QC对更改的相应部位进 行跟踪检验并记录; 1.样品装配后,产品工程师需召集相关部 门人员对样品的相关问题点进行评审,并 会议记录 确定改善方案; 试模申请单 2.模具改好后,需安排试模,具体试模要 求参照5.15; 1.样品评审合格后,产品工程师送样给实 验室做可靠性测试;2.品保部测试员参照 工程部提供的产品规格书及相关的通用标 准对产品进行全方位测试(含可靠性测 测试申请单 试),并填写可靠性测试报告;3.若样品 可靠性测试报告 评审不合格或可靠性测试不合格需更改, ECN 由产品工程师开出ECN对相应的结构或模 具进行修改,QC对更改的相应部位进行跟 踪检验并记录; 1.所有测试通过后,产品工程师需安排对 半成品物料进行封样;2.外购物料要求供 样品承认书 应商送承认书进行承认;3.产品工程师负 试模申请单 责师制定SOP、工艺流程图、包装规范、 产品规格书等;4.模具改好后,需安排试 模,具体试模要求参照5.15; 1.所有测试通过后,产品工程师开出试产 通知单给PMC安排计划对外购件的物料采 购及半成品生产,并计划装配拉线进行小 批量试产,生产部统计直通率(试产数量 根据不同型号产品评估确定); 试产通知单 2.小批量试产时,由生产部排拉组装生 产,产品工程师现场对每个工序进行技术 指导,品保部人员全程参与并检验和做相 关的测试、尺寸的测量等,并对每个工位 的问题点进行记录; 样品承认书
部件标准化流程

产品零部件标准化流程按照标准化对象分类,可以将零部件的标准化分为三类:第一类:结构的变更,即对不同结构的可进行标准化的相似零部件,在结构上进行标准化,统一为一种结构的配件,这种结构的变更根据变更的结果又可分为以原有某配件作为标准对其他配件进行变更和重新设计新的配件结构作为标准对原有配件进行变更。
这种结构的变更对产品的功能、质量有一定的影响,需要对变更后的配件进行物理性能验证,以保证标准化后配件能满足原有产品功能和质量方面的要求。
第二类:材料的变更,即对采用不同材料的可进行标准化的相似零部件,在材料方面进行标准化,统一为一种材料进行生产,此类变更对产品的质量有较大的影响,需要对变更后的配件进行全性能检验以保证标准化后配件的质量要求。
第三类:部分规格的的变更,如导管长度的标准化,此类变更对产品的质量和功能等基本无影响,只是通过统一某种规格来提高生产效率,降低生产成本,此类变更不需要对变更进行验证,只要满足变更后配件规格达到国标要求即可。
标准化流程图:1.收集产品各类配件信息各公司技术员收集公司内现有各种产品的配件信息,按照产品分类来统计各配件相关信息,包括数量,材料,规格,模具数量等基本信息,按统一格式形成分公司内配件信息汇总表,上交技术部。
2.分类整理、归纳技术部首先将各分公司技术员收集的所有配件的信息汇总,按照类别对各配件信息进行整理归纳,对同类零部件信息进行归纳汇总;然后,对同类零部件的所有图纸进行分析对比,找出各个规格的配件所存在的差异性,结合所对应产品的特性,分析其差异是否都是必须的,能否进行更换。
例:3.对可进行标准化的配件核算其标准化的效益和成本技术部对上一步分析中可以进行标准化的配件,根据根据各配件的年总需求量,单个配件所需要的原材料成本,加工成本,以及加工此类配件的模具的数量、精度等,对可进行标准化的配件从原材料成本、加工成本、换模成本等方面进行汇总,确定各标准化方案所带来的直接经济效益或成本,结合此标准化方案所带来的管理效益、质量效益等进行综合评比,以此来确定最佳的标准化方案。
对外加工零部件入出库流程图

顺序
工作流程
责任人/协助
备注
1
完工产品清点/包装
↓
车间操作工
按规定的料箱进行装箱包装
2
填写《产品标识卡》
↓
车间操作工
注明生产批次号
3
验收、清点
↓
仓管员/经办人
查看工件包装/标识,清点数量
4
登录
↓
仓管员
填录《产品验收入库单》ห้องสมุดไป่ตู้
5
单据打印
↓
物资统计核算员
整理当日入库单据,分车间打印单据
单据收存仓管员车间核算员仓管员每周一将上周单据结算联转物资统计核算员对外加工零部件出库流程图顺序工作流程责任人协助外协科线服员填写d22物料配送通知单仓管员核对物料及图号分拣工仓管员按d22物料配送通知单分拣物料打印物资统计核算员外销零部件物资退库退库流程图顺序工作流程责任人协助经办人填写材料退库厂申请单注明退库原因检验员经办人判明不合格品返工修复或报废物资统计核算员经办人办理红票反冲仓管员不合格品标识
4
接收
↓
仓管员
不合格品标识;返工修复件走“工件返工流程”;报废件走“工件报废流程”
5
记录
仓管员
4
运送
↓
物流公司司机
5
接收签字
↓
物流公司/仓管员
6
汇总/入帐
↓
仓管员
7
打印
物资统计核算员
外销零部件物资退库退库流程图
顺序
工作流程
责任人/协助
备注
1
办理退库手续
↓
经办人
填写《材料退库(厂)申请单》,注明退库原因
2
检验
标准化(SOP)流程图制作规范

一、前言二、目的三、流程图符号四、流程图结构说明五、流程图绘製原则六、范例一,前言标准作业流程的意义「标准作业流程」(SOP)是企业界常用的一种作业方法,其目的在使每一项作业流程均能清楚呈现,任何人只要看到流程图,便能一目了然,有助于相关作业人员对整体工作流程的掌握。
(一)所有流程一目了然,工作人员能掌握全局。
(二)更换人手时,按图索骥,容易上手。
(三)所有流程在绘製时,很容易发现疏失之处,可适时予以调整更正,使各项作业更为严谨。
一、为建立本部作业标准化(SOP)流程图之可读性及一致性,参考美国ANSI系统流程图标准符号,及道勤企业管理顾问有限公司「效率会议」标准流程,製作符号及范例。
二、本规范流程图绘製,採用由上而下结构化程式设计(Top-down Structured Programming)观念。
三、对于製作流程图共通性目标,本规范亦列出流程图绘製原则。
符号准备作业(处理(决策(终止(路径(文件(预定义处理(Predefined Process连接(批注四.流程图结构说明顺序结构(Sequence)图形:意义:处理程序顺序进行。
语法:DO处理程序1 THEN DO处理程序2实例:运用时机:本结构适用于具有顺序发生特性的处理程序,而绘制图形上下顺序就是处理程序进行顺序。
A. 二元选择结构(基本结构)图形:意义:流程依据某些条件,分别进行不同处理程序。
语法:IF 条件THEN DO 处理程序1 ELSE DO 处理程序2 实例:运用时机:1.2.3.图形:意义:流程依据某些条件,分别进行不同处理程序。
语法:FOR 条件PCASE 1 DO 处理程序1CASE 2 DO 处理程序2CASE n DO 处理程序n实例:运用时机:·本结构是二元选择结构的变化,流程依据选择或决策结果,择一进行不同处理程序。
·选择或决策结果路径名称,可用不同文字,来叙明不同路径的处理程序。
A. REPEAT-UNTIL结构图形:意义:重复执行处理程序直到满足某一条件为止,即直到条件变成真(True)为止。
零部件标准化流程图
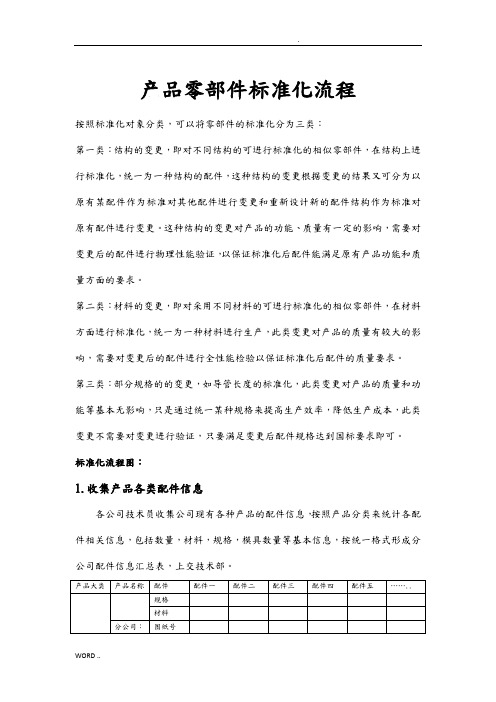
产品零部件标准化流程按照标准化对象分类,可以将零部件的标准化分为三类:第一类:结构的变更,即对不同结构的可进行标准化的相似零部件,在结构上进行标准化,统一为一种结构的配件,这种结构的变更根据变更的结果又可分为以原有某配件作为标准对其他配件进行变更和重新设计新的配件结构作为标准对原有配件进行变更。
这种结构的变更对产品的功能、质量有一定的影响,需要对变更后的配件进行物理性能验证,以保证标准化后配件能满足原有产品功能和质量方面的要求。
第二类:材料的变更,即对采用不同材料的可进行标准化的相似零部件,在材料方面进行标准化,统一为一种材料进行生产,此类变更对产品的质量有较大的影响,需要对变更后的配件进行全性能检验以保证标准化后配件的质量要求。
第三类:部分规格的的变更,如导管长度的标准化,此类变更对产品的质量和功能等基本无影响,只是通过统一某种规格来提高生产效率,降低生产成本,此类变更不需要对变更进行验证,只要满足变更后配件规格达到国标要求即可。
标准化流程图:1.收集产品各类配件信息各公司技术员收集公司现有各种产品的配件信息,按照产品分类来统计各配件相关信息,包括数量,材料,规格,模具数量等基本信息,按统一格式形成分公司配件信息汇总表,上交技术部。
2.分类整理、归纳技术部首先将各分公司技术员收集的所有配件的信息汇总,按照类别对各配件信息进行整理归纳,对同类零部件信息进行归纳汇总;然后,对同类零部件的所有图纸进行分析对比,找出各个规格的配件所存在的差异性,结合所对应产品的特性,分析其差异是否都是必须的,能否进行更换。
例:3.对可进行标准化的配件核算其标准化的效益和成本技术部对上一步分析中可以进行标准化的配件,根据根据各配件的年总需求量,单个配件所需要的原材料成本,加工成本,以及加工此类配件的模具的数量、精度等,对可进行标准化的配件从原材料成本、加工成本、换模成本等方面进行汇总,确定各标准化方案所带来的直接经济效益或成本,结合此标准化方案所带来的管理效益、质量效益等进行综合评比,以此来确定最佳的标准化方案。
- 1、下载文档前请自行甄别文档内容的完整性,平台不提供额外的编辑、内容补充、找答案等附加服务。
- 2、"仅部分预览"的文档,不可在线预览部分如存在完整性等问题,可反馈申请退款(可完整预览的文档不适用该条件!)。
- 3、如文档侵犯您的权益,请联系客服反馈,我们会尽快为您处理(人工客服工作时间:9:00-18:30)。
产品零部件标准化流程按照标准化对象分类,可以将零部件的标准化分为三类:第一类:结构的变更,即对不同结构的可进行标准化的相似零部件,在结构上进行标准化,统一为一种结构的配件,这种结构的变更根据变更的结果又可分为以原有某配件作为标准对其他配件进行变更和重新设计新的配件结构作为标准对原有配件进行变更。
这种结构的变更对产品的功能、质量有一定的影响,需要对变更后的配件进行物理性能验证,以保证标准化后配件能满足原有产品功能和质量方面的要求。
第二类:材料的变更,即对采用不同材料的可进行标准化的相似零部件,在材料方面进行标准化,统一为一种材料进行生产,此类变更对产品的质量有较大的影响,需要对变更后的配件进行全性能检验以保证标准化后配件的质量要求。
第三类:部分规格的的变更,如导管长度的标准化,此类变更对产品的质量和功能等基本无影响,只是通过统一某种规格来提高生产效率,降低生产成本,此类变更不需要对变更进行验证,只要满足变更后配件规格达到国标要求即可。
标准化流程图:1.收集产品各类配件信息各公司技术员收集公司现有各种产品的配件信息,按照产品分类来统计各配件相关信息,包括数量,材料,规格,模具数量等基本信息,按统一格式2.分类整理、归纳技术部首先将各分公司技术员收集的所有配件的信息汇总,按照类别对各配件信息进行整理归纳,对同类零部件信息进行归纳汇总;然后,对同类零部件的所有图纸进行分析对比,找出各个规格的配件所存在的差异性,结合所对3.对可进行标准化的配件核算其标准化的效益和成本技术部对上一步分析中可以进行标准化的配件,根据根据各配件的年总需求量,单个配件所需要的原材料成本,加工成本,以及加工此类配件的模具的数量、精度等,对可进行标准化的配件从原材料成本、加工成本、换模成本等方面进行汇总,确定各标准化方案所带来的直接经济效益或成本,结合此标准化方案所带来的管理效益、质量效益等进行综合评比,以此来确定最佳的标准化方案。
例如:某类配件的 A、B 规格经分析可以进行标准化整合,通过以下分析确定4.评审确定标准化方案技术部对以上收集整理分析的结果以及初步拟定的可行性方案召集产品技术部、工艺技术部、质量部、制造部、销售部共同进行评审,综合各部门意见共同确定最终的标准化方案。
5.标准化变更设计5.1结构变更5.1.1以原有某配件作为标准统一此类配件5.1.1.1验证用标准化配件替代其他配件对产品质量和功能的影响根据上阶段确定的标准化方案,以选择的原有某配件作为标准替代其他配件,验证此类配件代替其他配件后对该产品的质量和功能的影响是否达标。
首先由项目组成员提交验证申请,批准后由技术部进行验证,主要验证容:标准化配件各项质量和功能指标是否满足原有配件标准;替换后配件在产品中适配性是否满足要求;对于需蘸胶组装的配件要验证蘸胶组装后及灭菌处理后抗拉力、压力等指标是否合格;产品整体性能有无变化等。
5.1.1.2审批将上阶段的验证结果及标准化方案,上报技术部和质量部,由技术部和质量部审核,技术副总批准。
审批通过后,方可进行下阶段的验证,若审批不通过,则考虑换另一种配件作为标准配件,或是根据需求重新设计新的配件。
5.1.1.3小批量验证审批通过后,对标准化配件进行小批量的组装生产,由于标准化配件采用的是原有某配件,只涉及部分组装工序的改变,因此在小批量试生产中,只需要验证组装过程中原先没有出现过的相关配件间的组装工艺,记录新组装方式其中的劳动强度、工作效率及因配件原因导致的不良率等5.1.1.4临床试用将小批量生产的相关产品及时投放市场,跟踪产品在临床使用中的情况,如在运输过程中新配件脱落、与产品连接处断开等情况,临床使用中是否存在不易操作或是功能不良等问题。
以上由技术部派专门的技术员跟踪完成或是制定详细的信息采集单,由销售人员负责此类信息的收集与跟踪5.1.1.5评审临床试用结束后,召集产品技术部、工艺技术部、质量部、销售部、制造部、相关分公司负责人共同对试生产结果进行评审,评审容包括:在实际生产中,新设计的标准化零部件是否满足批量生产的条件;标准化配件是否有效的提升了产品的质量效益或是生产中的管理效益或是有效的降低了生产成本;以标准化配件取代其他配件的产品在实际的市场试用中是否还存在某些质量或功能性缺陷;是否在接下来开始大批量的生产。
根据评审的结果进行下一步的工作,若评审结果不可行,则终止或暂停此次变更,若需要改进,则重新确定是否继续采用原有某配件作为标准化配件,若原有配件不能满足要求则考虑重新设计新的配件作为标准化配件。
5.1.1.6变更相应的技术文件小批量生产结果经评审通过后,工艺技术部着手变更相应的技术文件,相关生产车间更换模具,为大批量生产做准备。
需变更技术文件:产品结构图纸、模具图纸、产品物料采购单、作业指导书、工艺技术卡、BOM5.1.1.7大批量生产相关分公司定制新的模具,模塑公司根据新的产品结构图纸和模具图纸重新制作模具或是对原有模具进行改制,生产车间根据变更后的相应的技术文件进行大批量的生产。
5.1.1.8市场跟踪产品进行大批量生产后,工艺技术部继续保持对此类产品的市场跟踪半年至一年时间,及时收集市场中反馈的问题,持续改进。
5.1.2重新设计新的配件作为标准统一此类配件5.1.2.1确定配件各项要求整合原有此类配件各项功能性和工艺性要求,对其中的差异性指标进行分析,结合产品的整体要求,重新确定新的统一的标准或要求。
确定配件各项要求中要及时与原设计人员及时沟通,了解相关注意事项或隐性要求,确保各项因素都在考虑围之,避免因忽略了某项因素而导致重新确定的指标或要求出现偏差,而最终导致重新设计的配件在最后的验证或临床试用中出现问题。
5.1.2.2重新设计配件图纸根据上阶段确定的标准和要求,重新绘制新的配件图纸。
5.1.2.3审批将上阶段确定的配件的标准和设计的图纸,上报至技术部审批,有技术部经理审核,技术副总批准。
审批容主要包括新的标准是否满足产品功能和质量要求,新设计图纸是否满足新标准5.1.2.4利用实验模具制造样品审批通过后,根据新绘制和设计的图纸,利用实验模具注塑少量的样品5.1.2.5样品检验首先对用实验模具注塑的样品进行外观检验,检验尺寸、形状、规格等是否符合设计要求;然后对样品进行拉力、应力等物理性能检验以及流量或过滤直径等功能性检验,验证样品是否满足所需配件的各项标准和要求;最后将样品与其他相关配件共同组装成为完整产品,验证样品与产品的匹配程度及产品的各项功能性、质量性指标是否合格5.1.2.6样品评审样品检验合格后,召集产品技术部、工艺技术部、质量部对样品验证结果进行评审,各部门对新配件的各项性能指标重新进行审核,共同确定此项变更是否满足产品要求。
5.1.2.7制定生产和检验标准样件评审通过后,由工艺技术部和质量部根据配件设计的各项指标和要求,重新制定新的配件的生产和检验标准,发往相关分公司5.1.2.8小批量验证相关分公司根据制定的生产和检验标准对新设计的配件进行小批量的试生产,各分公司技术员及时最终生产的情况并记录生产中的各项信息,如:新配件在组装过程中的难易程度,新配件的生产效率,原材料及二次料的使用情况等,若是机组配件,则还要考察配件在机组中的适用情况,组装机是否需要重新调整等。
5.1.2.9临床试用将小批量生产的相关产品及时投放市场,跟踪产品在临床使用中的情况,如在运输过程中新配件有无变形、开裂或是与产品连接处断开等情况,临床使用中是否存在不易操作或是功能不良等问题。
以上由技术部派专门的技术员跟踪完成或是制定详细的信息采集单,由销售人员负责此类信息的收集与跟踪5.1.2.10评审临床试用结束后,召集产品技术部、工艺技术部、质量部、销售部、制造部、相关分公司负责人共同对试生产结果进行评审,评审容包括:在实际生产中,新设计的标准化零部件是否满足批量生产的条件;标准化配件是否有效的提升了产品的质量效益或是生产中的管理效益或是有效的降低了生产成本;以标准化配件取代其他配件的产品在实际的市场试用中是否还存在某些质量或功能性缺陷;是否在接下来开始大批量的生产。
根据评审的结果进行下一步的工作,若评审结果不可行,则终止或暂停此次变更,若需要改进,则重新制订生产和检验标准,继续进行小批量验证。
5.1.2.11变更相应的技术文件小批量生产结果经评审通过后,工艺技术部着手变更相应的技术文件,相关生产车间更换模具,为大批量生产做准备。
需变更技术文件:产品结构图纸、模具图纸、产品物料采购单、作业指导书、工艺技术卡、BOM5.1.2.12大批量生产相关分公司定制新的模具,模塑公司根据新的产品结构图纸和模具图纸重新制作模具或是对原有模具进行改制,生产车间根据变更后的相应的技术文件进行大批量的生产。
5.1.2.13市场跟踪产品进行大批量生产后,工艺技术部继续保持对此类产品的市场跟踪半年至一年时间,及时收集市场中反馈的问题,持续改进。
5.2材料变更5.2.1确定材料性能指标根据上阶段评审确定的标准化方案,若选择作为替换其他配件的标准化配件涉及材料的改变,首先要根据原有配件的相关性能确定需要更换的材料的性能指标,包括:材料的密度、透明性、柔韧性、熔点、分子结构、药溶性、抗热寒性、价格围等5.2.2开发供应商根据上阶段确定的材料性能指标,寻找可满足要求的材料,若公司现有材料没有能满足要求的材料,则由工艺技术部会同采购部门共同开发新的材料供应商。
若公司现有材料可满足新材料性能指标,则分析市场上可满足要求的其他材料与公司材料的价格指标,选取最经济合理的材料作为标准化配件材料。
5.2.3审批将原配件材料性能指标、经分析所确定的材料性能指标、最终确定选择的材料性能指标以及供应商资料等相关资料和新材料验证申请上报主管部门审批。
5.2.4采购材料审批通过后,由采购部购置少批量实验用料,技术部对材料进行验证,检验所购材料各项性能指标是都满足要求。
(若材料是公司原有材料,则审批通过后跳过此步骤,直接进行下阶段的验证)5.2.5样品试制及检验利用原有模具或实验模具采用新材料生产相关配件,根据材料的性能指标合理调整相关的注塑工艺参数,记录最合理的工艺参数,在注塑过程中,及时记录新材料与模具的适配性(若模具不匹配则考虑重新设计模具),注塑时间,冷却时间及其他相关问题。
样件注塑完成后,对配件进行全性能检验,验证配件物理性能和化学性能是否达标,检验容:配件的抗拉力、压力检测;配件应力检验;注塑冷却后形变量;灭菌处理后形变量;各温度条件下韧性检验;老化试验;与药液、环己酮接触条件下的化学稳定性;高温灭菌条件下有无化学反应等检验以及流量(或是过滤直径或避光性能)等功能性检验。
5.2.6样品评审样件全性能检测结束后,召集产品技术部、工艺技术部、质量部共同对样件及各项检测结果,进行评审,判定新材料制造的新配件各项功能和质量性能是否达标,是否继续进行下阶段的小批量验证和临床试用。