导光板成形技术
导光板成形相关技术

成形时须注意的要点–成形开始
• 料管的温度在成形正要开始之前,分 二阶段来升温,等到达到成形温度之 后,进行充分的料管洗净,然后开始 生产。
• 升温完了后,如果使其长时间滞留的 话,会造成变黄或烧焦现象的发生。
14
成形时须注意的要点–成形中断、成形开始
• 在造成中断时,因为以成形温度而长时间让它 滞留的话,会造成变黄或烧焦的现象发生,所 以要把温度降低到200°C左右的保温状态。
29
导光板成形的要求质量
1) 透明度 2) 黄变度 3) 转写性 4) 平面度 5) 肉厚的均匀度
• LCD:Liquid Crystal Line Display • TFT:Thin Film Transistor
30
导光板的射出成形
31
仕样
1) 要做导光板、扩散板的成形时所必须的 仕样内容
在进行成形品的质量管理之下,重量及尺寸之反复的安 定性,被要求须具有高的水平。
4
成形时须注意的要点–模具温度
• 以2台模具调温机,在模穴侧、模仁侧控制各自 的温度,而设定温度在60°C~70°C。以2台模具 调温机来控制温度,由此,即使模穴侧、模仁侧 产生温度差而发生翘曲也能够修正。温度低的话, 在薄肉部会发生凹洼或流痕。而温度高的话,则 会造成翘曲的发生。还有,为了微细形状 (PATTERN)的转写,必须做80°C以上的高温设 定。再者,为了谋求升温时间的缩短及改善温度 的安定性,所以模具调温机的容量在确保充足的 容量同时,也必须要考虑在成形机模板和模具之 间设置热遮用射出压缩所得的效果
b. CAVITY内压力的均一化及翘曲、毛边的 消除:CAVITY内压力(从浇口到末端)能被 缓和而消除毛边。还有,在充填中利用进 行再型缔也会消除翘曲。
导光板成型技术台湾

K.C. Lin
K.C. Lin
1
光電產品範圍
source:光電科技協進會,2000年
K.C. Lin
2
塑膠光學特性
透光率─光線照射物體會有部分反射,光線進入後部分被吸收 而未被吸收而能透過材料之比例 折射率─由於各種材料結構不同,光線進入後進行之速度也會 不同,通常光線由外界進入後會有偏折之現象,而材料 折射率與入射與折射角度有一定之關係 雙折射率─異方向性之材料或受應力應變作用之材料,會使折 射率產生方向上的變化,在垂直平面上有不同折射率 光彈性─ 透明塑膠材料在受到應力作用時,其折射率將會產生 方向性,即材料平面上具兩個主軸應力,使得此材料 具有兩不同的折射率。當光線通過此材料時,沿二個 主軸應力方向振動的光波,彼此以不同的速率前進, 當穿出材料時就會有相對相位差產生。而此相位差正 比於平面上的兩個主軸應力值之差值
Like Butter
Crystalline
Like Ice
Broad Softening under Heating
Sharp Melting under Heating
TM : Melt Temperature TG : Glass Transition Temperature
Rigid Solid Flow
Soft Solid
Melt
Rigid Solid Flow
Soft Solid
Melt
source:Moldflow
K.C. Lin
8
Ideal shear flow
Y F dY
Stationary Plate Moving Plate V+dv V
Fixed
g=
光刻技术 导光板

光刻技术导光板光刻技术导光板是一种利用光刻技术制造的光学元件,具有高精度、高效率、低成本等优点。
在制造过程中,需要经过多个环节,包括材料选择、精密成型、表面处理、光路设计、质量检测等。
下面将分别介绍这些环节。
一、材料选择导光板的材料选择是制造过程中的关键环节之一。
常用的导光板材料包括PMMA、PC、PS等光学塑料,它们具有光学性能优良、加工方便、成本低廉等优点。
在选择材料时,需要根据导光板的用途和性能要求,综合考虑材料的透过率、折射率、热稳定性、机械强度等方面的因素。
二、精密成型精密成型是制造导光板的另一个关键环节。
由于导光板需要具有高精度、复杂的光路结构和高平整度等特点,因此需要进行精密成型。
常用的成型方法包括注塑成型和激光切割成型。
注塑成型可以通过模具将塑料熔体注入到型腔中,冷却后得到所需的形状和尺寸。
激光切割成型则是利用激光器将材料切割成所需的形状和尺寸。
在成型过程中,需要控制成型工艺参数,保证成型精度和质量。
三、表面处理表面处理是制造导光板的另一个重要环节。
表面处理的目的在于提高导光板的表面平整度和光洁度,降低散射和反射损失,提高光的透过率。
常用的表面处理方法包括研磨、抛光、镀膜等。
研磨和抛光可以通过机械或化学方法去除表面粗糙部分,使表面更加平整和光滑。
镀膜则是通过在表面涂覆一层透明薄膜,提高表面光学性能。
在表面处理过程中,需要控制处理工艺参数,保证处理质量和效果。
四、光路设计光路设计是制造导光板的另一个关键环节。
光路设计的主要任务是根据导光板的用途和性能要求,设计出合理且高效的光路结构,使光线能够按照所需的路径和方式传播。
在设计过程中,需要考虑光线的反射、折射、全反射等光学原理,以及材料的透过率、折射率等光学性能参数。
同时,还需要考虑制造工艺的可行性和难度,以保证设计的可实现性和可靠性。
五、质量检测质量检测是制造导光板的最后一个环节。
质量检测的主要任务是对导光板的各项性能指标进行检测和评估,保证其质量和性能符合要求。
导光板成型工艺
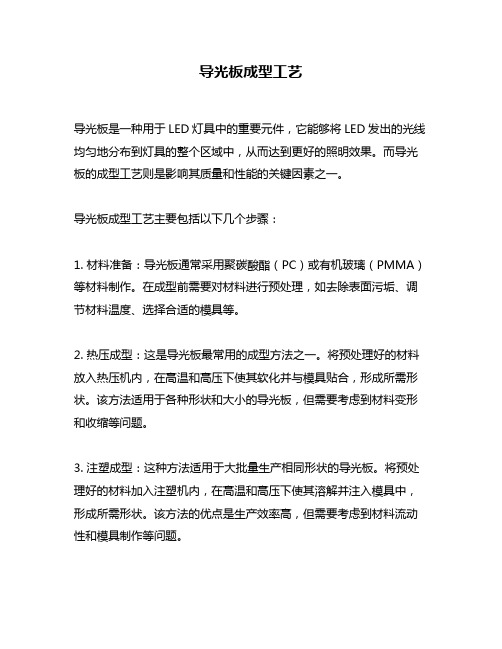
导光板成型工艺
导光板是一种用于LED灯具中的重要元件,它能够将LED发出的光线均匀地分布到灯具的整个区域中,从而达到更好的照明效果。
而导光板的成型工艺则是影响其质量和性能的关键因素之一。
导光板成型工艺主要包括以下几个步骤:
1. 材料准备:导光板通常采用聚碳酸酯(PC)或有机玻璃(PMMA)等材料制作。
在成型前需要对材料进行预处理,如去除表面污垢、调节材料温度、选择合适的模具等。
2. 热压成型:这是导光板最常用的成型方法之一。
将预处理好的材料放入热压机内,在高温和高压下使其软化并与模具贴合,形成所需形状。
该方法适用于各种形状和大小的导光板,但需要考虑到材料变形和收缩等问题。
3. 注塑成型:这种方法适用于大批量生产相同形状的导光板。
将预处理好的材料加入注塑机内,在高温和高压下使其溶解并注入模具中,形成所需形状。
该方法的优点是生产效率高,但需要考虑到材料流动性和模具制作等问题。
4. 拉伸成型:这种方法适用于制作薄型导光板。
将预处理好的材料放
入拉伸机内,在高温和高压下使其拉伸并与模具贴合,形成所需形状。
该方法的优点是可以制作出更薄、更轻的导光板,但需要考虑到材料
变形和收缩等问题。
总之,导光板成型工艺是一个复杂而关键的过程,对于LED灯具的照
明效果和使用寿命都有着重要影响。
因此,在进行导光板生产时需要
选择合适的成型方法,并注意各种细节问题,以确保生产出高质量、
高性能的导光板产品。
一种导光板的加工方法

一种导光板的加工方法
一种常见的导光板加工方法是热压法。
该方法使用透明材料(如聚碳酸酯、亚克力等)制成的板材作为导光板的基材,然后利用热压机的高温和高压将导光板模具中的光学结构与基材热压结合在一起。
具体步骤如下:
1. 准备导光板模具:根据设计需求,制作一个带有所需光学结构的导光板模具。
2. 准备基材:选取透明材料制成的板材,根据导光板模具的尺寸将基材切割成相应的形状。
3. 加热导光板模具:将导光板模具放入热压机中,加热至一定温度,通常为材料的玻璃化转变温度以上。
4. 定位基材:将切割好的基材放置在导光板模具的底部,确保其位置与模具中的光学结构完全对齐。
5. 热压结合:关闭热压机的压力系统,将压头降下,对基材进行高温高压的压力作用,使基材与光学结构紧密结合。
6. 冷却与固化:保持一定的时间,使热压后的导光板冷却,并使结构固化。
7. 取出导光板:打开热压机,取出导光板模具,此时基材和光学结构已经成为一个整体。
这种热压法加工的导光板制造工艺简单、成本较低,适用于生产大批量、尺寸较小的导光板。
同时,该加工方法能够保证导光板的光学性能,并且可以根据需要
进行模具的设计和改变,以满足不同的应用需求。
导光板注塑成型技术的研究的开题报告

导光板注塑成型技术的研究的开题报告导光板是一种广泛应用于照明、广告牌、显示屏、警示标识等领域的新型光学材料。
其优点包括高透光率、均匀的光分布、强度高、重量轻等,因此受到越来越多的关注和应用。
在制造导光板的过程中,注塑成型技术是一种常见的生产技术,具有生产效率高、准确度高、成本低等优点。
因此,研究导光板注塑成型技术的生产过程、工艺参数和产品性能等方面,对于提高导光板的质量、降低生产成本具有重要的意义。
本文旨在开展导光板注塑成型技术的研究,主要内容包括以下几个方面:一、导光板的介绍导光板是一种由光学级聚碳酸酯或下列之一的高分子材料制成的板材。
其主要特点包括:良好的尘土、水、以及化学品耐受性、良好的光学性能和均匀的光输出特性。
由于以上优势,导光板在应用市场中非常广泛。
二、注塑成型技术的研究进展注塑成型是一种将熔化的材料通过注入成型机进行加工加热塑性材料的工艺,并在加热过程中,在模具中制成所需的形状。
由于工艺简单、生产效率高、成本低等优点,注塑成型技术被广泛应用于导光板的生产过程中。
三、导光板注塑成型技术的生产过程导光板注塑成型技术的生产过程主要包括以下几个阶段:原料准备、预加热、注塑成型、冷却和成型品脱模、后处理等,每个阶段的质量控制对于提高导光板的质量、降低生产成本具有重要的意义。
四、导光板注塑成型技术的工艺参数优化生产过程中,注塑成型机的工艺参数对于产品质量起到了至关重要的作用。
本文将以压力、温度、注射速度等多个参数进行针对性探讨,并结合经验制定一套合理的注塑工艺流程,以提高导光板的质量,降低生产成本。
五、导光板注塑成型技术的产品性能测试为了验证调整后的生产工艺和参数和设计的导光板性能指标是否匹配,将进行导光板生产后的产品性能测试,为工艺优化提供有力的支撑。
六、结论本文将以实验方法为主进行研究,通过理论分析与实践操作相结合的方式,探讨导光板注塑成型技术的生产工艺,并进行相应的性能测试,以全面提升导光板的性能和品质,为未来相关领域的应用提供参考。
导光板和胶框注塑成型要点
导光板和胶框注塑成型要点导光板和胶框注塑成型要点首先介绍导光板(Light Guide)的原理:导光板是利用光学级压克力板材吸取从灯发出来的光在光学级压克力板材表面的停留,当光线射到各个导光点时,反射光会往各个角度扩散,然后破坏反射条件由导光板正面射出。
通过各种疏密、大小不一的导光点,可使导光板均匀发光。
反射片的用途在于将底面露出的光反射回导光板中,用来提高光的使用效率。
一:导光板模具要点:○1根据产品大小及出模数和机台吨位确定模架尺寸。
○2顶出系统:制作中在顶针下的合理(备注:顶出平衡,顺利脱模)的情况下数量尽量放少,以降低生产中顶针发热膨胀烧死断裂的比例及多余的毛边(以胶框为重点)。
○3冷却系统(备注:主要保持模具恒温)务必做好,才可以保证生产一直正常。
○4排气系统(备注:主要是排除成型过程模腔的气体和树脂产生的气体,减少阻力,以防前端树脂烧焦或产生的气体脏污)位置要合理(光源处要大要多)及深度Z控制在0.03mm以下。
○5脱模系统:模具要有脱模斜度(斜度就产品结构及厚度而定),模具产品横切面需要经过省模抛光处理,以至生产中脱模正常。
○6冷料井必需要有深度Z控制在2—4mm,主要是藏射嘴前端一点冷胶。
○7胶框针点浇口位置、大小、数量要合理(这样可以控制到产品的尺寸、变形、局部毛边及成型难易度等)二:试模要点:○1首先确认产品图档和模具编码是否一致,再看产品大小来确定机台吨位及机台号码。
○2在模具稼动、合模力、顶针长度、机械手确认OK后,试模初步要避免撑模现象(这样对机器保养很好)首先把机器的射胶压力、速度相对调小一点、位置放大点,再根据经验判断产品的熔胶量不可以过大,然后再按成型情况慢慢调试就OK。
○3产品成型及外观OK后首要品管确认产品结构,然再尺寸及导光板光学效果。
○4试模过程中要注意以下细节:a:顶出是否正常(顶针长度,顶出平衡,弹簧力度),b:脱模是否顺畅(看有没有粘模现象)c:冷却循环流道是否通畅(是否漏水,有没有堵塞),d:成型是否困难排气系统是否OK,e:浇口位置、数量是否正确(主要针对胶框),f:产品是否变形(看是顶出不平衡、还是残余应力粘模引致),以上问题对能否生产顺利很是重要,需要及时跟模具部门沟通且尽快改善以备生产。
导光板注塑成型工艺流程
导光板注塑成型工艺流程下载温馨提示:该文档是我店铺精心编制而成,希望大家下载以后,能够帮助大家解决实际的问题。
文档下载后可定制随意修改,请根据实际需要进行相应的调整和使用,谢谢!并且,本店铺为大家提供各种各样类型的实用资料,如教育随笔、日记赏析、句子摘抄、古诗大全、经典美文、话题作文、工作总结、词语解析、文案摘录、其他资料等等,如想了解不同资料格式和写法,敬请关注!Download tips: This document is carefully compiled by theeditor. I hope that after you download them,they can help yousolve practical problems. The document can be customized andmodified after downloading,please adjust and use it according toactual needs, thank you!In addition, our shop provides you with various types ofpractical materials,such as educational essays, diaryappreciation,sentence excerpts,ancient poems,classic articles,topic composition,work summary,word parsing,copy excerpts,other materials and so on,want to know different data formats andwriting methods,please pay attention!导光板注塑成型工艺是一种将LED光线通过注塑成型技术固定在塑料导光板上的工艺。
导光板成型工艺
导光板成型工艺
导光板成型工艺是一种用于光学器件制造的重要工艺,它可以有效地改善光学器件的光学性能和使用效果。
导光板通常是由光学级材料制成的,具有高透明度和优良的光学性能,它可以将光线引导到需要的位置,提高光学器件的亮度和清晰度。
导光板的成型工艺主要包括材料选择、模具设计、注塑成型、后处理等步骤。
首先是材料选择,导光板通常采用光学级聚合物材料,如聚碳酸酯(PC)、聚甲基丙烯酸甲酯(PMMA)等,这些材料具有优异的光学性能和加工性能,能够满足导光板的制造要求。
接下来是模具设计,模具的设计直接影响导光板的成型质量和性能。
在模具设计中,需要考虑导光板的形状、尺寸、厚度等因素,保证导光板的光学表面光滑度和尺寸精度。
此外,还需要考虑模具的冷却系统,确保导光板成型过程中温度均匀分布,避免产生缺陷。
注塑成型是导光板成型工艺的关键步骤,通过将加热熔融的光学级材料注入到模具中,经过冷却凝固后得到导光板的成品。
在注塑成型过程中,需要控制注塑温度、压力和速度等参数,确保导光板的成型质量和表面光滑度。
最后是导光板的后处理,包括去除模具、修整边缘、热处理等步骤,以提高导光板的光学性能和稳定性。
通过后处理,可以进一步改善导光板的表面光滑度和透明度,确保其在光学器件中的应用效果。
总的来说,导光板成型工艺是一项复杂的工艺过程,需要在材料选择、模具设计、注塑成型和后处理等方面进行精心设计和控制。
只有通过科学合理的工艺流程和严格的质量控制,才能生产出具有优异光学性能和稳定性的导光板产品,满足不同光学器件的需求。
希望随着技术的不断进步和工艺的改进,导光板制造工艺能够实现更高的精度和效率,为光学器件的发展提供更好的支持和保障。
导光板生产工艺流程
导光板生产工艺流程嘿,朋友们!今天咱就来聊聊导光板生产工艺流程这档子事儿。
你说导光板像啥?就好比是灯光世界里的神奇魔法板呀!它能让光线乖乖听话,按照我们想要的方式去照亮。
那这神奇的导光板咋来的呢?首先就是材料准备啦,就像厨师要准备好食材一样。
得挑那些高质量的材料,这可不能含糊。
然后呢,就是注塑成型啦,就好像捏泥巴一样,把材料变成我们需要的形状。
你想想,这多有意思呀!接着,就是网点设计啦。
这可就像给导光板画上独特的妆容,让它变得与众不同。
网点设计得好,那光线出来的效果就特别棒,就跟化了个美美的妆一样让人眼前一亮呢!再来就是印刷啦,这一步就像是给导光板穿上漂亮的衣服。
把那些图案啊、标记啊都印上去,让它变得更有个性。
然后就是检验啦!这可重要啦,就像考试一样,得看看这导光板合不合格。
要是有啥毛病,那可不行,得赶紧挑出来。
经过这么多步骤,一个高质量的导光板才算诞生啦!你说这过程是不是很神奇?就像变魔术一样。
咱再想想,要是没有这一道道严谨的流程,那导光板能好用吗?那光线还能那么听话地照亮我们想要的地方吗?肯定不能呀!所以说呀,这生产工艺流程可真是太重要啦!大家都知道,好东西都是精心打造出来的。
导光板也不例外呀!从材料到最后的成品,每一步都得认真对待,不能有丝毫马虎。
这就跟我们做人做事一样,得认真负责,才能有好结果。
而且呀,这导光板在我们生活中可太重要啦!手机呀、电脑呀、电视呀,到处都有它的身影。
没有它,我们的这些电子设备能那么好用吗?能有那么清晰漂亮的显示效果吗?所以说呀,别小看了这导光板生产工艺流程,它可关系着我们生活中的点点滴滴呢!我们得尊重每一个生产环节,感谢那些在背后默默付出的工人们。
他们就像魔术师背后的助手,没有他们,哪来这么神奇的导光板呀!你们说是不是这个理儿?。
- 1、下载文档前请自行甄别文档内容的完整性,平台不提供额外的编辑、内容补充、找答案等附加服务。
- 2、"仅部分预览"的文档,不可在线预览部分如存在完整性等问题,可反馈申请退款(可完整预览的文档不适用该条件!)。
- 3、如文档侵犯您的权益,请联系客服反馈,我们会尽快为您处理(人工客服工作时间:9:00-18:30)。
LSCOM 10
4
1. 鎖模力計算 鎖模力(F)=模具內平均壓力(P)*投影面積(S)*1.1 例:以 CH05 為例,長:289.75mm;寬:219.15mm 1. F=28.975*21.915*1.2*400*0.001=304.7 噸 304.7 噸/450 噸=68%(PCX 之最低設定)。 2. F=28.975*21.915*600*0.001=380.8 噸 380.8 噸/450 噸=84%(PCX 之最高設定)。 三、充填(FILL):將溶融之塑料以高速注入模穴使其填滿模穴各部份位置,由於螺 射出速度與流量成正比,為了得到均勻的流動狀態,螺桿射出位 置及速度控制是非常重要的。其可防止縫合線、噴流痕、縮水…. 等等不良項目。 (成形機畫面)
成形條件考慮: 成形條件考慮: 速度效應
2
※縮短充填時間或提高射速以避免塑料過度冷卻,並利用黏滯加熱升高料溫。
※充填速度太快會使塑料波前分子鏈配向及排氣不及問題加劇,反使熔接強度降低,如圖 2 所示
縫合線的成因
噴流造成的縫合線
通常若澆口尺寸過小,塑料在充填寬度和厚度較大的模穴時,若成型條件控制不良則易發生噴流(Jetting), 如下圖所示。由噴流產生的塑料並不循序自進澆口逐漸填模,而是以蛇形流的方式噴射到模穴中,然後 塑料自澆口對面側逐漸堆積。塑料蛇形流堆積時相互壓縮造成所謂的手風琴效應(Accordion Effect),最後 在蛇形流彎角堆疊區域形成流痕,是為由噴流所造成的縫合線。
5
Cavity)模具,塑料熔膠通常透過注道(Sprue,或叫豎流道)由澆口(Gate)填入模穴或模腔 (Cavity)中;對於多模穴(Multi-Cavity)模具通常需利用流道系統將塑料分配到各模穴中。 通常螺桿依設定的行程曲線(Ram-Speed Profile)以及射壓曲線(Injection Pressure)前 進,由於塑料黏度甚高,因此加工溫度需高於熔點(一般在 180oC 以上);射壓(指射嘴處壓 力)高達 150~250MPa (也就是 1500~2500 atm 或 or 21,000~36,000 psi)。模溫一般採用冷模 (如 60oC)。充填時間短則 0.5 秒~1 秒;長則 5~10 秒,視模穴數目及模具大小而定。 在充填過程中,由於模穴尚未填滿,塑料前緣為大氣壓狀態(或是抽真空)。在正 常充填過程下,若射壓夠高,塑料將以設定的流量曲線(或是螺桿行程曲線)順利填模。 此階段稱為流率控制 (Flow-Rate Controlling ) 階段。但隨著充填範圍增加,塑料填模的 流動阻力將逐漸增加,反映出來的就是模穴壓力(Cavity Pressure)的增加。模穴壓力是一 種背壓(Back Pressure),是塑料流動阻力的表徵:模穴壓上升越快,代表流動阻力越大。塑 料在充填過程中需能克服流動阻力迅速填滿模穴;否則若射壓不足,射速不夠,流動就會 停止造成短射(Short Shot)。 在模穴將填滿時,模穴壓會發生上昇的現象,此時已經難以流率控制螺桿前進。 一般會將操作切換至壓力控制(Pressure-Controlling)階段,而操作過程也切換至保壓 (Packing)階段。 充填過程是塑料在模穴中成型的起始步驟,因此是一個十分重要的過程。由於牽 涉塑料流動以及傳熱,塑料性質會隨溫度壓力及剪切率等變量分布而異,加上熔膠波前 (Melt Front)是隨時間而異的自由面流動(Free Surface Flow),因此也是一個十分複雜的過 程。 充填過程的影響 1. 塑料黏度:塑料黏度影響其加工性(Processability),與溫度、壓力、剪切率等變量分
射出成型的充填過程(Filling Stage)指的是塑料填模(Mold Filling)的過程。在射出機 的動作上 射出機射嘴(Nozzle)開啟 處於鬆退狀態螺桿向前推進 將位於儲料區(Reservoir) , , , 已塑化(Plasticated)完畢而呈現熔膠(Melt )狀態的塑料射進模穴中。對於單模穴(Single
成形機控制 HM11 HM12 HM13 HM14 HM15
二、鎖模力(Clamp)控制 (成形機畫面)
功能簡介:LSCOM
修改後模式 延遲時間結束 LSCOM 同 時 計 算 壓縮延遲 開始 P1 壓縮 射出延遲 開始射出
說明:以目前功能而言,使用 LSCOM 功能 MOLD SEPARATION ,實際 XH POSITION 為 4.2mm,表示模具合模開度為 4.2mm, 另延遲時間如上圖所示。
※最終使用性能(End-Use Performance)考量:將縫合線移至非受力面、肉厚較厚處或具結構補強處,以 避免應力集中引起破壞,補償可能產生的熔接強度下降。對於具有裝配孔的塑件縫合線生成方式 的考慮尤其重要。圖 1 顯示一帶有圓孔的塑件在成形時由於進澆口數目與位置差異造成所形成的縫 合線有所差異,以產品強度而言,熱縫合線數目較少且強度較強,是較佳的設計。
8
四、保壓階段:由於溶膠具有彈性且以溶融態填滿模穴,因此在冷凝過程中 比容(cm3/g)降低而造成體積收縮。固在充填達 100%後仍必 須加壓將融膠擠入模穴,除了可克服成品的體積收縮外,亦 可藉此調整成品重量使其進入公差範圍。
成形條件考慮: 成形條件考慮: 壓力效應
※充填壓力不足會產生較明顯及較弱的縫合線,因此提高射壓/保壓、螺桿前進時間、保壓時間,以 增加縫合線介面有效壓力(Effective Pressure),也會使熔接強度獲得改善。
HEN 及 HN 約低於 H1 溫度 10℃ 主要為保持料管溫度。 註:影響固化層的因素為模溫、H1 溫度、射出速度。因固化層較厚,阻力較大,
1
所以提高塑料流動性為提高溶膠溫度。 成形條件考慮: 成形條件考慮: 溫度效應 ※提高料溫使熔接溫度增加以提昇熔接強度。通常溫度是影響熔接強度以及外觀最明顯 的成形因素。這是由於高溫增加塑料分子鏈的活動力(Mobility),使熔接區域的分子擴散 (Molecular Diffusion)、縫合(Knitting)及糾纏(Entanglement)現象提昇,破壞在熔接面的分子 鏈平行配向情形,增加分子鏈間相互穿插滲透的程度,因此使熔接強度隨之增加。圖 1 說明料溫、模溫對於熔接強度的影響。在塑料成形溫度範圍內,提高料溫使熔接強度增 加,但若料溫過高會造成塑料劣化(Degradation),反使熔接強度下降。
導光板成形技術(慨論) 射出成形流程由塑料至成形大致可分為
塑化 充填 保壓 冷卻
一、塑化(Melt): 機台參數設定: ◆ 加熱料筒設定:占熱量來源約 30%。 (成形機畫面)
每段溫度設定要點 溫度 H5 H2~H4 H1 約 220℃ 各段溫度依序增加 5 ℃ 約 260℃~275℃ 主要影響塑料之流動性,溫度愈高流動性愈好, 通常 GH-1000S 最高設定 275℃,為防止塑料黃 化。 說明 為各段溫度最低,防止溫度過高,易使 HOPPER 因塑料溶解造成阻塞。
梯形體積=(2.09+0.65)*219.25/2*289.75=86993.3mm3=86.99cm3
7
成品重量=體積*密度=86.99(cm3)*1.19(g/cm3)=103.448g 模穴內總重量=成品重量+料頭重量=130.448+4.44=107.89g 螺桿內塑料溶融體積=3.14/4*D2*S=107.89g 3.14/4*60 *S=107.89;S=36.5mm(LS5 之位置) 設 LS4=5mm;則 LS5=41.5mm
450T 螺桿半徑:30mm ※當轉速設定太快時,塑料易造成黃化。因此轉速控制是非常重要的
◆ 熱澆道溫度:大尺寸一模兩穴熱澆道溫度起伏過大會影響流動不均情形。
電熱線 NT M1 G1 M2 G2 1 3 5 7 9 2 4 6 8 10
3
測溫線 13 15 17 19 21 14 16 18 20 22
螺桿轉數
例:設 280T 轉速約 50rpm,450T 需要多少轉? V(切線速度)=R(半徑)*W(角速度) Rrrr V W=2*3.14*N(轉速);W=2*3.14*50=314rad/s V=25*314=7850mm/s
280T 螺桿半徑:25mm V 7850=30*W;W=261.67rad/s 261.67=2*3.14*N;N=41.67rpm 故可知當 280T 50 轉時 450T 僅需 41 轉。
◆ Screw 迴轉及背壓控制:占熱量來源約 70%。 慨念:1.V(切線速度)=R(半徑)*ω(角速度) -----計算不同噸數轉數。 2.未考慮螺桿溝距深度及摩擦係數。 機台噸數 130T 160T 280T 450T 450T 550T
2
螺桿直徑 Φ32 Φ40 Φ50 Φ60 Φ70 Φ90
※由於溫度越高,分子鏈間的活動力(Mobility)及擴散(Diffusion)越明顯,熔接強度越強,因
五、冷卻階段:融膠於模穴內逐漸冷卻,此時續壓壓力必須配合冷卻過程, 作適當的調配。並以不使溶膠由未凝固的澆口產生逆流為原 則,續壓時間必須一直維持到澆口處的溶膠不發生流動為止。
10
6
布有關。 因此隨產品/模具設計及充填加工參數設定而有所差異。塑料黏度分布是造成流動阻 力差異,以及充填過程塑料流向不同的主因。 2. 塑件表面分子鏈配向(Molecular Chain Orientation):在射出過程中分子鏈大體延主要流 動方向配向,使其物性產生流動方向以及垂直流動方向的差異性,也使塑料在射出 後性質與原料有所差異。分子鏈配向性影響塑件翹曲狀況以及機械性質。對於摻拌 玻璃纖維強化(Glass Fiber-Reinforced)的塑料,纖維配向(Fiber Orientation)更是對塑件性 質有所影響。 3. 塑料結晶度(Crystallinity) : 對於結晶性塑料在充填過程中,有時會因為分子鏈排向結 果造成再結晶。這種流動引發結晶(Flow-Induced Crystallization)會釋出結晶熱影響溫 度、造成塑件變色黃化、以及影響塑件翹曲性質等。 4. 塑料熱劣解(Thermal Degradation) : 在充填過程中由於高剪切率摩擦所造成的黏滯加 熱(Viscous Heating)會使塑料產生局部升溫的效果。若溫度超過塑料的熱劣解溫度, 會使塑料發生燒焦劣化的問題。 5. 塑件外觀(Appearance)及表面品質(Surface Quality) : 是充填過程影響塑件性質的主要 部分。不良的充填問題如噴流(Jetting)、包封(Air Trap)、流痕(Flow Mark)以及縫合線 (Welding Line)等,都會對塑件外觀及表面性質造成不良影響。 6. 塑件強度(Strength) : 縫合線等充填問題會造成缺陷、形成應力集中(Stress Concentration),降低成型塑件機械強度。 例:Ls5 位置之決定(以 CH05 為例)。 厚邊厚度:2.09mm;薄邊厚度:0.65mm 長度:289.75mm;寬度:219.15mm