电弧喷涂锌铝涂层耐腐蚀实验报告
电弧喷涂锌铝合金涂层的防腐机理和应用现状
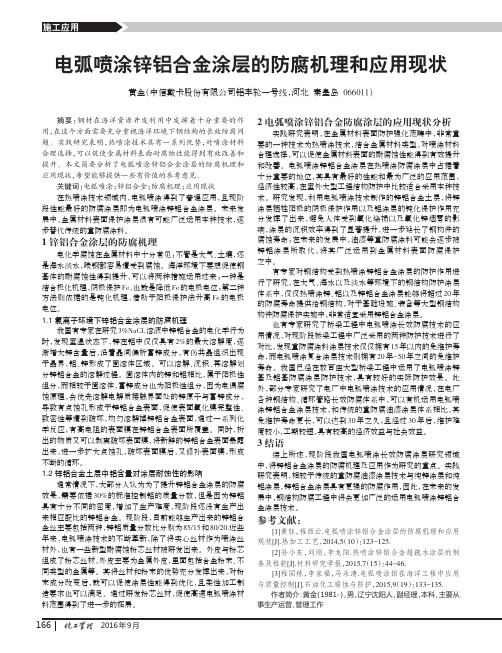
2016年9月电弧喷涂锌铝合金涂层的防腐机理和应用现状黄金(中信戴卡股份有限公司铝车轮一号线,河北秦皇岛066011)摘要:钢材在海洋资源开发利用中发挥着十分重要的作用,在这个方面需要充分重视海洋环境下钢结构的长效防腐问题。
实践研究表明,热喷涂技术具有一系列优势,对喷涂材料合理选择,可以促使金属材料表面耐腐蚀性能得到有效改善和提升。
本文简要分析了电弧喷涂锌铝合金涂层的防腐机理和应用现状,希望能够提供一些有价值的参考意见。
关键词:电弧喷涂;锌铝合金;防腐机理;应用现状在热喷涂技术领域内,电弧喷涂得到了普遍应用,且现阶段性能最好的防腐涂层即为电弧喷涂锌铝合金涂层。
未来发展中,金属材料表面保护涂层很有可能广泛运用本种技术,逐步替代传统的重防腐涂料。
1锌铝合金涂层的防腐机理电化学腐蚀在金属材料中十分常见;不管是大气、土壤,还是海水淡水,碳钢都容易遭受到腐蚀。
海洋环境下要想促使钢基体的耐腐蚀性得到提升,可以将两种措施运用过来;一种是结合极化机理,阴极保护Fe,也就是降低Fe的电极电位;第二种方法则依据的是钝化机理,借助于阳极保护法升高Fe的电极电位。
1.1氯离子环境下锌铝合金涂层的防腐机理我国有专家在研究3%NaCL溶液中锌铝合金的电化学行为时,发现室温状态下,锌在铝中仅仅具有2%的最大溶解度,逐渐增大锌含量后,沿着晶间偏析富锌成分,有伪共晶组织出现于晶界,铝、锌形成了固溶体区域。
可以溶解、沉积、再溶解划分锌铝合金的溶解过程。
固溶体内的锌和铝相比,属于阳极性组分,而相较于固溶体,富锌成分也为阳极性组分,因为电偶腐蚀原理,会优先溶解电解质接触界面处的锌原子与富锌成分,导致有点蚀孔形成于锌铝合金表面,促使表面氧化膜完整性、致密性等遭到破坏,均匀溶解掉锌铝合金表面,通过一系列化学反应,有高电阻的表面膜在锌铝合金表面所覆盖。
同时,析出的物质又可以剥离破坏表面膜,将新鲜的锌铝合金表面暴露出来,进一步扩大点蚀孔,破坏表面膜后,又修补表面膜,形成不断的循环。
电弧喷涂Zn-Al在油罐长效防腐中的应用研究

热喷涂层与有机涂层复合实现油罐长效防腐的研究1 本项目的目的意义金属材料的腐蚀遍及国民经济的各个领域,给国家带来了重大的经济损失。
腐蚀是从材料的表面开始的,因此很久以来人们就采用各种方法在钢铁表面形成各种保护层,以使易腐蚀的基体与外部腐蚀环境隔离。
最常用的防腐方法有涂料、金属镀层、热浸Zn 或Al 涂层以及使用耐腐蚀的金属和非金属材料等。
鉴于此,原油储罐主要采用的抗腐蚀技术措施是:涂装有机底漆,连接Zn块作为牺牲阳极,重点部件换用不锈钢材料等。
采取这些措施后,对于储罐防腐蚀有一定的效果,但油田使用后的腐蚀问题仍然相当严重。
油罐不同部位的腐蚀状况不同:水层与底泥层段钢板坑蚀穿孔,是原油储罐失效的最常见形式。
主要原因是该层段积聚了水中含有大量的富氧离子,成为较强的电解质溶液,产生化学腐蚀;加上油中固体杂质和油罐腐蚀产物大量沉积于罐底,它们与油罐罐底有不同的电极电位,这就形成了腐蚀电池,产生了电化学腐蚀。
加强对原油储罐腐蚀防护的研究,开发新型高效、经济合理的防腐技术,以减少泄漏事故的发生显得尤为重要,并且日益引起石油领域的关注。
2 热喷涂防腐的技术现状热喷涂技术自上世纪30 年代开始在防腐方面应用。
由于其对大型钢结构件有较好的现场施工性,工艺简单,防腐效果优异,可获得较厚的涂层,并可预计涂层的寿命,很快得到广泛重视,正日益取代油漆和热浸、电镀。
经过几十年的应用证明,热喷涂技术是钢铁结构件长效防腐的最好方法,这个结论已得到世界许多国家的政府和工业界所认可。
英国标准BS 5493:1977《钢铁结构防腐蚀保护层的使用规程》中指出,只有喷Zn、Al涂层才能保证在各种工业及海洋环境中维持20年而无需维护;美国焊接学会进行的19年腐蚀试验及LaQue腐蚀中心的34年海洋环境使用性能报告也有力地说明了在各种不利的环境下,Zn、Al 涂层长效防护的有效性。
目前用于防腐蚀的热喷涂技术主要有火焰喷涂和电弧喷涂两种。
国外在上世纪70年代后期逐渐成熟的电弧喷涂工艺具有速度快、喷涂效率高、能源利用率高、涂层性能好、施工周期短、现场施工方便等明显优越性,在钢铁构件长效防腐中应用广泛。
Zn(OH)2、Al(OH)3对锌、铝镀层腐蚀行为的影响的开题报告

Zn(OH)2、Al(OH)3对锌、铝镀层腐蚀行为的影响的开题报告题目:Zn(OH)2、Al(OH)3对锌、铝镀层腐蚀行为的影响摘要:本研究主要研究Zn(OH)2、Al(OH)3对锌、铝镀层腐蚀行为的影响。
通过利用多种表面分析技术来研究涂覆有Zn(OH)2、Al(OH)3的锌、铝镀层的腐蚀性能及微观形貌。
实验结果表明,涂覆了Zn(OH)2、Al(OH)3的锌、铝镀层比未经涂覆处理的锌、铝镀层具有更好的耐腐蚀性能。
同时,Zn(OH)2、Al(OH)3的使用对于减缓锌、铝镀层的腐蚀速率和减少腐蚀产物的形成有着显著的效果。
关键词:锌、铝镀层;Zn(OH)2、Al(OH)3;耐腐蚀性能;腐蚀产物一、研究背景锌和铝是常见的金属材料,广泛应用于制造工业和日常用品中。
锌、铝材料的耐腐蚀性是决定其使用寿命的关键因素之一。
然而,在特定工作条件下,锌、铝材料表面可能会发生腐蚀现象,导致减少其使用寿命和性能,因此有必要对其进行防腐处理。
Zn(OH)2、Al(OH)3是一种常用的防腐涂层材料,在许多工业中被广泛应用,可以有效防止金属表面的腐蚀。
然而,在实际应用中,锌、铝镀层的腐蚀防护效果与涂覆层的质量有直接关系。
因此,对于Zn(OH)2、Al(OH)3对锌、铝镀层腐蚀行为的影响研究具有重要的意义。
二、研究目的本研究旨在探究Zn(OH)2、Al(OH)3防腐涂层对于锌、铝镀层的腐蚀行为的影响,并研究其防腐效果的机理。
通过多种表面分析技术,研究不同涂覆层下锌、铝镀层的耐腐蚀性能、微观形貌以及腐蚀产物的组成。
三、研究方法1.材料制备锌、铝材料是由商业化供应商提供的,涂覆Zn(OH)2、Al(OH)3的锌、铝镀层由溶液法制备,溶液中的活性成分为ZnO、AlO(OH)等。
2.涂布及实验过程涂布方法采用浸涂法和喷涂法。
在涂布处理后,样品将进行腐蚀测试,腐蚀测试将在盐水溶液中进行,测试过程中将记录锌、铝材料及其涂覆层的质量减少情况,同时使用SEM/EDX、XRD等表面分析技术分析腐蚀产物和微观形貌以及腐蚀机理。
电弧喷涂锌铝合金涂层的防腐机理和应用现状

[ 2 】舒亮 , 包 志 坚 ,张爱 青 。一种 2 - ( 2 -噻吩基 )乙醇对
0 引言
电弧 喷 涂是 一 种较 为 常用 的热 喷 涂技 术 , 随 着 科学 技术 的不 断进 步 , 热喷 涂技 术也 取得 了一 定的 改进 与完善 , 并得 到 了越来越 广泛 的应用 , 其在 实际应用 过程 中表 现 出了不可替 代
王金 辉 ( 中信 戴卡 股份 有 限公 司 , 河北 秦 皇 岛 0 6 6 0 0 0 )
摘要 : 锌 铝合金 涂层是一种应用十分 广泛的防腐 手段 , 在金 属材 料表 面喷 涂锌 铝合 金涂层 , 可以对金属材料 实施有 效 的保护 , 能 够预 防金属材 料的腐蚀 , 从 而有利于延 长金属材 料的使用寿命 , 也有 利于减少金属 材料 的维护与保养成本。 电弧喷涂是一种较为 常用的热喷涂技术, 电弧喷涂锌 铝合金涂层是现 阶段防腐性能最 好的涂层之 一, 在我 国有 着 良好的发展 前景与广 阔的发展 空间。 本篇论文 中, 笔者主要 对 电弧喷涂锌铝合金涂层 的防腐机理进行 了 探 讨, 并分析 了电弧喷涂锌铝合金 涂层 的应用现状 , 以供 参考 。 关键 词 : 电弧喷涂 ; 锌 铝合金 涂层 ; 防腐机 理
金涂 层 中含有 锌 、 铝 以及微 量 的稀土 元素 , 相 比较 于常 规热 镀
锌, 热镀锌铝 合金涂 层的耐 大气腐蚀 特性较好 , 且 涂敷性 较好 ,
因此能够 使涂 层、 合金 层之 间的结 合长期保 持稳定 。
上接3 1 页( 文 章 题 目 :优 势 通 道 识 别 综 合 评 价 指 l 电弧喷 涂 锌铝合 金 涂层 的 防腐机 理 标体 系 在油 井 生产 管理 的 应用 ) 对 于金 属材料 来 说 , 最为 常见 的一种腐 蚀类 型便 是 电化
Zn-Al和Al-RE热喷涂涂层的耐蚀性研究

G P的 5 。因此 , D % 随着 经 济 的发展 , 效地 阻 止 或 效 和 最 经 济 的 方 法 。 为 对 比研 究 热 喷 涂 z — 1 有 n A 和
延缓钢结构腐蚀越来越迫切 。
A 一 E涂 层 的耐 蚀 性 , 者 考 察 了 两种 涂 层 在 铜 加 1R 笔
热 喷涂 锌 、 涂 层 自 2 世 纪 2 年 代 首 次 在 英 速 醋 酸 盐 雾 试 验 中 的 腐 蚀 行 为 并 探 讨 了其 腐 蚀 防 铝 0 0 国应 用 以来 , 到 了世 界 各 国 的高 度 重 视 并 沿 用 至 护 机 理 得
第7 卷
第6 期
装 备 环 境 工 程
E I ME T E V R N N A E G N E I G QU P N N I O ME T L N I E R N
2 1年 1月 00 2
Z — 和 AlR n AI — E热喷涂涂层 的耐蚀性研 究
梁义 , 魏世丞 刘毅 王玉江 徐滨士 , , ,
r s e tv l e p c ie y.Th ir tu t r e m c osr c u e ofZn— 1a d —RE o tngsbe o e a fe o r i n — n A1— A c a i f r nd a tr c roso we e a l z d b s a i g e e r ni r na y e y c nn n lcto c
Ke o ds Zn A1 o t g;A1 RE c ai g;CAS yw r : — ai c n 一 o t n S;c ro i nr ssa c o so e itn e
钢结 构 的腐蚀 与 防护 一直 备受 世界 各 国的关 注 今 16 3J , 。我 国从 2 世 纪 5 年 代 末 开 始 热 喷 涂 锌 、 0 0 铝
FBE、玻璃钢、电弧喷涂防腐层罐道耐磨试验报告

FBE、玻璃钢、电弧喷涂防腐层罐道耐磨试验报告
目的:本试验通过磨损试验的结果评定涂层的使用寿命。
试验方法:采用称重法来实现耐磨性能的评定。
称重法采
用试样在试验前后质量之差值来表示耐磨性能的评定方法,由于两试样间的磨损所引起的磨损量,可以采用精度达万
分之一克的DTG160分析天平上,称量出试样试验前后质量
之差来获得。
试验标准:GB/T 1768-2006 色漆和清漆耐磨性的测定旋
转橡胶砂轮法。
评判依据:MT/T5017-2011煤矿井筒装备防腐蚀技术规范
1、附录A,表A.1(热喷锌、铝)长效防腐涂层,涂层总
厚度≥250μm使用年限20年以上;
2、附录B,表B.2井筒装备常用的玻璃钢复合材料,涂层
厚度4mm使用年限20年以上。
试验结果:
1、矿用环氧树脂涂层(FBE)磨损失重0.036mg;
2、罐道用玻璃钢外覆材料磨损失重0.088mg;
3、电弧喷涂长效防腐涂层磨损失重0.143mg.
试验分析:玻璃钢耐磨损也是电弧喷涂长效防腐涂层的两
倍以上,但因玻璃钢涂层厚与钢材的膨胀比不同、挠度系
数也不同,玻璃钢使用的是不饱和聚酯树脂,与钢芯的结
合能力远不如环氧树脂,所以玻璃钢层容易出再脱壳现象,影响其使用寿命。
按电弧喷涂长效防腐涂层厚度≥250μm使用年限20年
计算,矿用环氧树脂涂层(FBE)厚度≥350μm使用年限为111年,保守使用也在40~50年。
超音速电弧喷涂锌铝合金涂层的制备及在海水中的腐蚀行为研究

超音速电弧喷涂锌铝合金涂层的制备及在海水中的腐蚀行为研究梁国;魏伟;王玉纯;贾传宝;张婧;常德春【摘要】This paper introduces the process and technology of preparing Zn-Al alloy coating by supersonic velocity arc spraying. The coating was tested by electrochemical methods. The results show Zn-Al coating play a sacrificial anode role in corrosion process, and there is passive film in the surface of Zn-Al coating after immersing. So the base alloys are effectively protected.%本文介绍了超音速电弧喷涂技术制备锌铝合金涂层的过程和工艺,对涂层进行了电化学测试。
结果表明合金涂层可以起到牺牲阳极的作用,同时浸泡一段时间之后合金涂层表面可以生成钝化膜。
锌铝涂层可以保护钢铁基体不被腐蚀。
【期刊名称】《全面腐蚀控制》【年(卷),期】2014(000)009【总页数】3页(P55-56,81)【关键词】超音速电弧喷涂;锌铝合金;腐蚀【作者】梁国;魏伟;王玉纯;贾传宝;张婧;常德春【作者单位】中国人民解放军济南军区72502部队,山东济南250330;中国人民解放军济南军区72502部队,山东济南250330;中国人民解放军济南军区72502部队,山东济南250330;山东省科学院海洋仪器仪表研究所,山东青岛266001;山东省科学院海洋仪器仪表研究所,山东青岛266001;中国海洋大学化学化工学院,山东青岛266100【正文语种】中文【中图分类】TG174.44近年来,国家积极推进海洋强国建设,不断提高海洋资源开发能力,发展海洋经济。
6061铝合金表面电弧喷涂纯铝涂层的研究
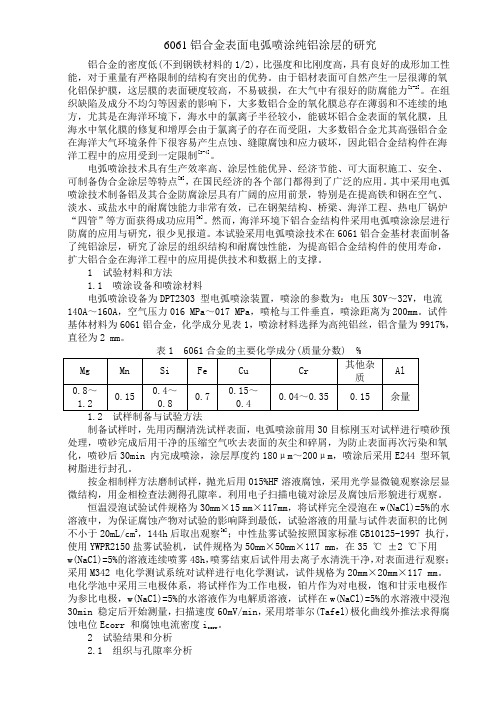
6061铝合金表面电弧喷涂纯铝涂层的研究铝合金的密度低(不到钢铁材料的1/2),比强度和比刚度高,具有良好的成形加工性能,对于重量有严格限制的结构有突出的优势。
由于铝材表面可自然产生一层很薄的氧化铝保护膜,这层膜的表面硬度较高,不易破损,在大气中有很好的防腐能力[1-2]。
在组织缺陷及成分不均匀等因素的影响下,大多数铝合金的氧化膜总存在薄弱和不连续的地方,尤其是在海洋环境下,海水中的氯离子半径较小,能破坏铝合金表面的氧化膜,且海水中氧化膜的修复和增厚会由于氯离子的存在而受阻,大多数铝合金尤其高强铝合金在海洋大气环境条件下很容易产生点蚀、缝隙腐蚀和应力破坏,因此铝合金结构件在海洋工程中的应用受到一定限制[3-4]。
电弧喷涂技术具有生产效率高、涂层性能优异、经济节能、可大面积施工、安全、可制备伪合金涂层等特点[5],在国民经济的各个部门都得到了广泛的应用。
其中采用电弧喷涂技术制备铝及其合金防腐涂层具有广阔的应用前景,特别是在提高铁和钢在空气、淡水、或盐水中的耐腐蚀能力非常有效,已在钢架结构、桥梁、海洋工程、热电厂锅炉“四管”等方面获得成功应用[6]。
然而,海洋环境下铝合金结构件采用电弧喷涂涂层进行防腐的应用与研究,很少见报道。
本试验采用电弧喷涂技术在6061铝合金基材表面制备了纯铝涂层,研究了涂层的组织结构和耐腐蚀性能,为提高铝合金结构件的使用寿命,扩大铝合金在海洋工程中的应用提供技术和数据上的支撑。
1 试验材料和方法1.1 喷涂设备和喷涂材料电弧喷涂设备为DPT2303 型电弧喷涂装置,喷涂的参数为:电压30V~32V,电流140A~160A,空气压力016 MPa~017 MPa,喷枪与工件垂直,喷涂距离为200mm。
试件基体材料为6061铝合金,化学成分见表1,喷涂材料选择为高纯铝丝,铝含量为9917%,直径为2 mm。
表1 6061合金的主要化学成分(质量分数) %制备试样时,先用丙酮清洗试样表面,电弧喷涂前用30目棕刚玉对试样进行喷砂预处理,喷砂完成后用干净的压缩空气吹去表面的灰尘和碎屑,为防止表面再次污染和氧化,喷砂后30min 内完成喷涂,涂层厚度约180μm~200μm,喷涂后采用E244 型环氧树脂进行封孔。
- 1、下载文档前请自行甄别文档内容的完整性,平台不提供额外的编辑、内容补充、找答案等附加服务。
- 2、"仅部分预览"的文档,不可在线预览部分如存在完整性等问题,可反馈申请退款(可完整预览的文档不适用该条件!)。
- 3、如文档侵犯您的权益,请联系客服反馈,我们会尽快为您处理(人工客服工作时间:9:00-18:30)。
电弧喷涂锌铝涂层耐腐蚀实验报告
一、实验背景
水工钢闸门是水电站、水库、水闸、船闸等水工建筑物中控制水位的重要水工钢构件,其制造量约为500万吨,保有量十分巨大。
水工钢闸门由于长期浸水,在阴暗潮湿、干湿交替、高速水流、风浪、水生物腐蚀等恶劣环境下工作,经多年运行后很容易被腐蚀,出现绣皮泛起、局部绣坑密布,导致整个结构强度削弱,降低了钢闸门的承载能力,还要消耗大量的人力、物力、财力。
Zn-13A1涂层具有良好的耐腐蚀性能,以高速电弧喷涂方式将之喷到水工钢闸门表面可以有效防止表面腐蚀。
二、实验目的
本实验针对内陆水库及水电站工程,模拟其水工钢闸门的运行环境,研究Zn-13A1涂层对水工钢闸门的保护程度及对比分析不同保护涂层(Zn跟Zn-13A1)对防腐蚀能力的优劣程度。
三、实验器材
NaCl溶液,Q235钢板,棕刚玉砂,喷砂机,高性能电弧喷涂设备,超声清洗机,电子天平,防腐涂料,交流阻抗测试仪,M273 型电位仪,5208 型锁相放大器焊机,铜导线等。
四、实验过程
1、制备浸泡液:质量分数为5%的NaCl溶液。
2、加工试样,将Q235钢板加工成72片尺寸为12 mm*12mm*3mm的试样,将之分为九组,每组8片。
3、采用颗粒度为14~18#的棕刚玉砂对前六组试样表面进行喷砂处理。
喷砂操作时,压缩空气的工作压力为0.6 MPa,喷砂距离为150~200 mm,喷砂角度为70°~80°。
4、使用TLAS-III 型高性能电弧喷涂设备制备Zn-13A1涂层,电压45V,电流120A;制备Zn涂层,电压40V,电流120A。
5、丙酮超声清洗3min后烘干,将54片试样沉重,并记录,剩余的18个试样用于随时观察腐蚀情况。
6、将清洗过的试样画出工作界面:10mm*10mm;试样多余的部分用防腐涂料密封,露出10mm*10mm的工作界面。
同时将做电化学测试的试样焊接铜导线,以便测试其极化曲线和阻抗。
7、将全部处理好的试样放入浸泡液中,按照GBT19746-2005《金属和合金的腐蚀盐溶液周浸试验》标准进行全浸泡试验。
8、每组试验在浸泡液中浸泡120h(5d),240h(10d),360h(15d),480h(20d),600h (25d),720h(30d)之后将之进行表面清洗,清洗方法为:清水冲掉表面盐分,然后超声
清洗3min烘干。
然后进行a表面观察和扫描电镜观察,并记录观察结果;b取出表面的防腐涂料,称量腐蚀之后的重量,并记录;c测量锈蚀的计划曲线;d测量锈蚀的阻抗值。
9、绘制失重率的时变曲线,计算腐蚀速率,对计划曲线和阻抗曲谱进行分析,分析试验待测涂层的防腐性能。
四、实验结果与讨论
1、扫描电镜观察
腐蚀完毕后丙酮超声清洗3min,烘干后进行扫描电镜观察如图所示,图1为腐蚀3天后3种试样表面腐蚀坑内腐蚀产物的微观形貌。
无涂层试样已经被严重腐蚀,表面结构疏松,附着力差。
纯Zn涂层表面存在细小针状、取向不同的腐蚀产物,但由于针状腐蚀产物的数量较少,对腐蚀介质的阻碍能力较弱。
Zn-13Al涂层的腐蚀坑内存在大量细小的针状腐蚀产物,对腐蚀介质具有较强的阻碍能力。
图2为涂层出现第一锈点时的表面形貌图,经3天腐蚀实验之后,无涂层试样出现第一锈点,局部存在轻微鼓泡现象;12天时,纯Zn涂层表面出现较多的锈点,并有鼓泡和开裂现象,涂层明显鼓起,附着力很差,防护性能基本丧失;26天时,Zn-13Al涂层表面出现少量锈点,也出现了鼓包和开裂现象,其特征与纯Zn的形貌特征类似。
(a)无涂层(b)Zn涂层(c)Zn-13Al涂层
图1 腐蚀3d后的表面形貌
(a)无涂层(b)Zn涂层(c)Zn-13Al涂层
图2对应第一锈点出现时的表面形貌
2、计算失重
取出表面的防腐涂料,称量腐蚀之后的重量,记录如下,图3为全浸泡腐蚀试验中涂层
图3 涂层试样单位面积的质量损失随时间的变化曲线
3、涂层耐腐蚀性能检测
图4为在浓度为5%的NaCl溶液中,Zn-13Al涂层与基体的自腐蚀电位E与时间t的曲线。
分析可知,Zn-13Al涂层自腐蚀电位一直低于基体,从电化学的角度来讲,Zn-13Al涂层在电解质溶液中发生电化学腐蚀时,可实现牺牲阳极(涂层),保护阴极(基体)的功能。
在浸泡初期,Zn-13Al涂层自腐蚀电位快速提升,并逐渐趋于稳定,这表明在涂层表面形成了保护膜。
图4 Zn-13Al涂层与基体(Q235钢)的自腐蚀电位E与时间t关系曲线图5为Zn-13Al涂层浸泡1 h、20 h、500 h之后的极化曲线。
分析可知,涂层浸泡(1h 与
20 h)之后,出现较为明显的钝化现象,表明在涂层表层,形成了钝化膜(Al(OH)3)。
Zn-13Al 涂层腐蚀电位稳步增加,其电流密度显著降低,这表明涂层具有较好的耐腐蚀性。
浸泡500 h 之后,该涂层处于溶解阶段。
这表明Zn-13Al涂层颗粒较细,涂层较均匀,孔隙率较小,获得致密的组织结构,达到减少腐蚀通道的目的。
腐蚀反应进行到一定程度之后,因腐蚀产物堵塞,Cl-1难以利用涂层表面缺陷进入到涂层;其自封闭效果更为明显。
这有效提升了其腐蚀产物层的稳定性,进而使Zn-13Al涂层获得良好的耐腐蚀性能。
图5 不同时间Zn-13Al涂层的极化曲线
五、结论与展望
1、Zn-13Al涂层形成细小致密、稳定的针状腐蚀产物,可以有效填补涂层中的孔隙,切断腐蚀介质的快速通道,具有良好的自封闭性。
2、Zn-13Al涂层腐蚀电位低,腐蚀电流密度小,具有良好的阴极保护能力和耐蚀性能。
3、Zn-13Al涂层的耐蚀性能优于纯锌涂层,腐蚀形貌宏观表现为均匀腐蚀。
4、利用电弧喷涂方式将Zn-13Al涂层喷到水工钢闸门表面,可以有效提高水工钢闸门耐蚀性,延长其寿命,较小不必要的人力、物力与财力。