金属半固态成形工艺概述
金属半固态成形

金属半固态成形一、引言金属半固态成形是一种新兴的金属成形技术,它是在半固态状态下对金属进行成形加工,具有高效、高精度、高质量等优点。
近年来,随着科技的不断进步和人们对产品质量的要求越来越高,金属半固态成形技术得到了广泛的应用和研究。
二、什么是金属半固态成形1.定义金属半固态成形是指在合适温度下,将金属材料加工到一定程度时,使其呈现出部分晶粒熔化和部分晶粒未熔化的状态。
这种状态被称为半固态状态。
在这个状态下进行成型加工可以得到具有优异性能的零件。
2.特点(1)高效:相比传统的铸造和锻造工艺,金属半固态成形具有更快的生产速度。
(2)高精度:由于采用了先进的数控技术和模具制造技术,使得加工精度更高。
(3)高质量:由于采用了先进的材料处理方法和模具制造技术,使得产品质量更高。
三、金属半固态成形的工艺流程1.原材料制备:将金属材料经过特殊处理,使其呈现出半固态状态。
2.模具设计:根据产品的形状和尺寸,设计出合适的模具。
3.加热处理:将金属材料加热到合适的温度,使其呈现出半固态状态。
4.成型加工:将半固态金属材料放入模具中进行成型加工。
5.冷却处理:将成型后的零件进行冷却处理,使其达到稳定状态。
6.后续加工:根据需要对零件进行后续加工和表面处理。
四、金属半固态成形的应用领域1.航空航天领域:由于航空航天领域对于零件质量和性能要求非常高,因此金属半固态成形技术在该领域得到了广泛应用。
例如飞机发动机叶片、涡轮叶片等高精度零部件都可以采用该技术进行生产。
2.汽车制造业:汽车制造业是金属半固态成形技术的另一个重要应用领域。
例如汽车发动机缸体、曲轴等高精度零部件都可以采用该技术进行生产。
3.医疗器械领域:金属半固态成形技术在医疗器械领域的应用也越来越广泛。
例如人工关节、牙科种植体等高精度零部件都可以采用该技术进行生产。
五、金属半固态成形的未来发展趋势1.智能化:随着科技的不断进步,金属半固态成形技术将更加智能化,通过计算机控制和自动化设备,使得生产效率更高、产品质量更稳定。
半固态成形发展概况及研究进展

半固态成形利用金属材料在固液共存状态下所特有的流变特性进行成形的技术。
首先要制造含有一定体积比例的非枝晶固相的固液混合浆料,成形方法有流变成形和触变成形两种。
优点:1、在工艺方面:成型温度低,延长模具寿命(热冲击小);节省能源;改善生产条件和环境。
2、在产品方面:铸件质量提高(减少气孔和凝固收缩);减少加工余量;零件的尺寸和精度能达到近终形;扩大压铸合金的范围并可以发展金属复合材料。
所谓半固态加工是指金属在凝固过程中,对其施以剧烈的搅拌作用或扰动作用,得到一种液态金属母液,其中均匀悬浮着一定量的球状初生固相或退化的枝晶固相的固2液混合浆料(也称流变浆料) ,对这种浆料进行的加工成型的方法。
半固态成型包括半固态流变成型和半固态触变成型两类,前者是将制备好的半固态浆料直接用于成型,如压铸成型(称为半固态流变压铸成型) ;后者是对制备好的半固态坯料进行重新加热使其达到半熔融状态,然后进行成型,如挤压成型(称为半固态触变挤压)[1]。
1半固态金属成形的发展及现状(半固态成形铝合金材料研究)半固态金属(SSM)成形技术自DavidSpencer于1971年首次提出至今,已有30多年历史【2-5】。
综观整个历史过程,其发展可以分为实验研究、应用研究和工程化应用三个阶段。
从20世纪70年代初开始,实验研究工作大约延续了15年。
这一阶段的研究主要集中在探索具有流变性和触变性的有色金属合金半固态试样的组织特征与制备方法上。
主要成果包括:①揭示了流变性和触变性坯料的组织特征;②提出了枝晶组织向非枝晶组织转变的物理模型:③研究了搅拌速度、强度以及温度等工艺参数对非枝晶化过程的影响规律:④初步探讨了半固态微观组织与流变性能的关系;⑤测试了半固态合金流变性能,并建立了相关的数学模型。
上世纪80年代中期是半固态成形技术应用研究的迅速发展阶段,并且从早期的有色金属合金扩展到高熔点合金以及复合材料的半固态成形。
这期间,开发与研制了包括电磁搅拌在内的多种半固态制坯技术与连铸设备;利用计算机模拟技术揭示了半固态合金充型过程;深入细致研究了成形工艺对产品组织性能影响的规律。
第9章半固态成形技术
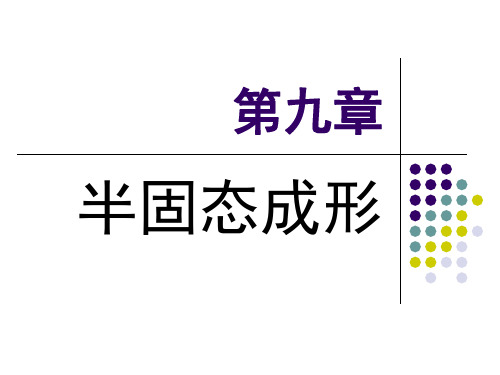
液态加工 (铸造成形)
半固态加工 (流变/触变成形)
固态加工 (塑性成形)
重力铸造 精密铸造 压力铸造
高流 速变 连铸 续造
铸 造
液态模锻 液态铸轧 连续铸挤 半固态轧制 半固态挤压 半固态压铸 半固态锻造
连连 续铸 带轻 液压 芯下 压 下
轧制 锻压 挤压 超塑成形 特种固体成形
图1 金属在高温下三态成形加工方法的相互关系
②枝晶臂根部熔断机制。
晶体在表面积减小的正常长大过 程中,枝晶臂由于受到流体的快速 扩散、温度涨落引起的热震动及在 根部产生应力的作用,有利于熔断, 同时固相中根部溶质含量较高,也 降低熔点,促进此机制的作用,机 理如图9所示。
图9 枝晶臂发生熔断示意图
③枝晶臂弯曲机制。 此机制认为,位错的产生并积累导致塑性变形。在两相区,位错
图8 球形微粒固态金属加工两种方法(流变成形和触变成形)的工艺流程图
半固态浆料搅动时的组织演变受很多因素影响,半固态浆料的 温度、固相分数和剪切速率是三个基本因素。
有色金属半固态组织的演变机制主要有以下三种:
①枝晶臂根部断裂机制。因剪切力的作用使枝晶臂在根部断裂。
最初形成的树枝晶是无位错和切口的理想晶体,很难依靠沿着自 由浮动的枝晶臂的速度梯度方向产生的力来折断。因此,必须加强 力搅拌,在剪切力作用下从根部折断。
(1)半固态成形技术定义
半固态成形原理
利用非枝晶半固态金属(Semi-Solid Metals,简称SSM)独有的 流变性和搅熔性来控制铸件的质量。
半固态 成形方法
流变成形 rheoforming
在金属凝固过程中,对其施以剧烈的搅拌作 用,充分破碎树枝状的初生固相,得到一种 液态金属母液中均匀地悬浮着一定球状初生 固相的固-液混合浆料(固相组分一般为50%左 右),即流变浆料,利用这种流变浆料直接进 行成形加工的方法称之为半固态金属的流变 成形。
半固态成形
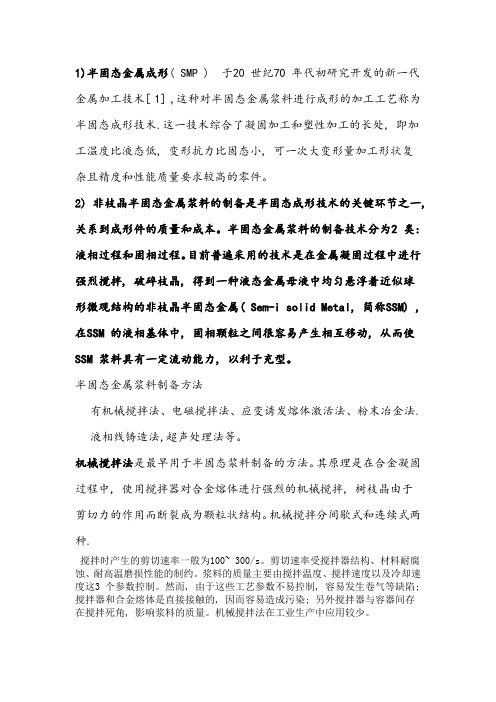
1)半固态金属成形( SMP ) 于20 世纪70 年代初研究开发的新一代金属加工技术[ 1] ,这种对半固态金属浆料进行成形的加工工艺称为半固态成形技术.这一技术综合了凝固加工和塑性加工的长处, 即加工温度比液态低, 变形抗力比固态小, 可一次大变形量加工形状复杂且精度和性能质量要求较高的零件。
2) 非枝晶半固态金属浆料的制备是半固态成形技术的关键环节之一, 关系到成形件的质量和成本。
半固态金属浆料的制备技术分为2 类: 液相过程和固相过程。
目前普遍采用的技术是在金属凝固过程中进行强烈搅拌, 破碎枝晶, 得到一种液态金属母液中均匀悬浮着近似球形微观结构的非枝晶半固态金属( Sem-i solid Metal, 简称SSM) , 在SSM 的液相基体中, 固相颗粒之间很容易产生相互移动, 从而使SSM 浆料具有一定流动能力, 以利于充型。
半固态金属浆料制备方法有机械搅拌法、电磁搅拌法、应变诱发熔体激活法、粉末冶金法.液相线铸造法,超声处理法等。
机械搅拌法是最早用于半固态浆料制备的方法。
其原理是在合金凝固过程中, 使用搅拌器对合金熔体进行强烈的机械搅拌, 树枝晶由于剪切力的作用而断裂成为颗粒状结构。
机械搅拌分间歇式和连续式两种.搅拌时产生的剪切速率一般为100~ 300/s。
剪切速率受搅拌器结构、材料耐腐蚀、耐高温磨损性能的制约。
浆料的质量主要由搅拌温度、搅拌速度以及冷却速度这3 个参数控制。
然而, 由于这些工艺参数不易控制, 容易发生卷气等缺陷; 搅拌器和合金熔体是直接接触的, 因而容易造成污染; 另外搅拌器与容器间存在搅拌死角, 影响浆料的质量。
机械搅拌法在工业生产中应用较少。
电磁搅拌法是应用最为广泛的一种方法。
它利用旋转磁场使金属液内部产生感应电流, 并在洛伦兹力的作用下发生强迫对流, 从而达到搅拌的目的。
产生旋转磁场的方法有两种, 一种是在感应线圈中通入交变电流, 另一种则采用旋转永磁体的方法。
半固态金属成形技术

二、半固态成形技术的发展简史
起源和发展
半固态加工起源于美国。20世纪70年代初,麻省理工学院 Spencer和Flemings等人发现凝固过程中的金属材料经强力搅 拌,会生成近球状晶或球状晶组织。 30多年的发展历程中,SSM技术在制坯、重熔加热、零件成 形、组织与力学性能、加工环节数值模拟以及合金流变学研究 等许多方面取得重大进展。目前,这项技术已广泛应用于汽车 工业领域,在航空、航天以及国防工业领域也正处于应用的起 步阶段,具有广阔的前景。 半固态金属加工技术是近多年来才诞生和发展起来的现代 冶金加工新技术。它虽然诞生晚, 但发展很快, 只用十几年的 时间就从试验室过渡到试生产, 又很快实现了产业化和商品化。 被世人称为新一代的合金成形工艺。
三、半固态金属加工的优缺点
优点:
(1) 由于在半固态, 合金具有独特的触变 行为, 可成型复杂的薄壁的零部件
(2)加工件的精度高, 几乎是近净成形, 尺 寸公差接近机加精度 (3)成形件表现平整光滑, 内部组织致密, 缺陷少, 晶粒细小, 力学性能高,可达锻 件性能
(4)节省原材料、能源, 生产同样的零部件, 它与普通铸造相比, 节能约35% (5)成品率高, 几乎达100%
半固态金属成形
一、概念
半固态金属成形技术(Semi-Solid Metal processing,SSM),它是利用在固-液态区间 获得一种液态金属母液中均匀地悬浮着一定固 相组分(50%-60%)合金的混合浆料进行加工 成形的方法。 半固态成形是利用金属材料从固态向液态, 或从液态向固态的转换过程中具有半固态的特 性所实现的成形。
影响因素对结构影响的具体分析
1、板长固定,不同板角下的组织形貌
20度
5度
7.5度
半固态金属铸造工艺

半固态金属铸造工艺引言半固态金属铸造(Semi-Solid Metal Casting, SSMC)是一种新兴的金属加工技术,它结合了传统铸造和塑性加工的优点,在制造高性能金属零件方面展现出巨大的潜力。
本文将介绍半固态金属铸造工艺的基本原理、优势和应用领域。
工艺原理半固态金属铸造工艺是指将金属材料在半固态(呈半固态状态)下进行铸造制作零件的技术。
其基本原理是通过精确控制金属的温度和组织结构,在高温下使金属呈现出部分固态和部分液态的状态,以便于形成高质量的零件。
半固态金属铸造的关键是控制金属的固相含量和液相形态。
固态粒子的存在可以提供一定的支撑力,防止破裂或变形,同时液态相的存在有助于金属的流动和充填。
通常使用精确控制温度和加热时间的方式,使金属逐渐达到半固态状态,在此状态下进行铸造。
工艺步骤半固态金属铸造工艺的一般步骤如下:1.材料准备:选择适合的金属合金,准备所需的原材料。
2.加热处理:将原材料放入特定的熔炼设备中,进行加热处理,使金属逐渐达到半固态状态。
3.浇注:将半固态金属倒入铸模中,通过重力或压力使金属充填整个模型空腔。
4.冷却固化:待金属充填完成后,让金属在模具中冷却和凝固,形成所需零件的形状。
5.取模:将模具打开,取出冷却固化后的零件。
6.精加工:对取模零件进行必要的机加工和表面处理,以获得最终产品。
工艺优势相对于传统的铸造工艺,半固态金属铸造具有以下优势:1.高成形性:半固态金属在流动性上表现出类似于塑料的特性,可实现复杂零件的精确铸造。
2.优良表面质量:由于金属呈半固态状态,能够更好地填充模具空腔,从而获得更高的表面质量和精度。
3.减少缺陷:半固态金属铸造可以有效减少常见的铸造缺陷,例如气孔和收缩缺陷。
4.提高材料性能:半固态处理能够使金属材料的晶粒变细,提高材料的强度和耐热性,同时减少金属的残留应力。
5.快速生产周期:相对于传统的金属加工方法,半固态金属铸造能够大幅缩短生产周期,提高生产效率。
半固态金属铸造工艺
半固态金属铸造工艺1. 引言半固态金属铸造是一种先进的金属加工工艺,它结合了传统金属铸造和金属注射成型的优点。
该工艺通过控制金属的凝固过程,使金属在部分凝固的状态下进行铸造,从而获得具有优异性能的金属零件。
本文将详细介绍半固态金属铸造的工艺流程、优势以及在工业中的应用。
2. 半固态金属铸造的工艺流程半固态金属铸造的工艺流程主要包括以下几个步骤:2.1 材料准备半固态金属铸造使用的材料主要是半固态金属(SSM)合金。
这些合金通常由金属基体和固态渣滓相组成。
在铸造过程中,需要对材料进行预处理,以达到适合半固态铸造的状态。
2.2 熔化与凝固控制熔化是半固态金属铸造的关键步骤之一。
合金需要在高温熔炉中被加热,达到液态状态。
接下来,通过控制冷却速度和温度梯度,使合金在部分凝固的状态下进行铸造。
2.3 注射成型在凝固过程控制好后,将半固态合金注入到铸造模具中。
模具通常采用金属材料或陶瓷材料制成,以确保注射后的零件具有较高的精度和表面质量。
2.4 冷却与处理注射完成后,零件需要经过冷却和处理过程。
冷却过程可以使用冷却液或空气来加速金属的凝固。
处理过程则包括去除模具、清洁表面以及进行热处理等步骤。
2.5 后续加工与检测铸造完成后的零件可能需要进行后续加工,如切割、车削、铣削等,以达到最终的形状和尺寸要求。
同时,对零件进行必要的检测和质量控制,确保产品的合格率。
3. 半固态金属铸造的优势半固态金属铸造相比传统的金属铸造具有以下优势:3.1 高成形性半固态金属铸造能够在低温、低应力条件下进行,使得金属能够更易于塑性变形,提高了材料的成形性能。
相比之下,传统的铸造工艺通常需要高温和高应力条件下进行,容易导致材料变形和裂纹。
3.2 较高的力学性能半固态金属铸造制备的零件具有较高的力学性能。
由于半固态金属在凝固过程中保持有一定的流动性,较完全凝固的材料具有更细小的晶粒尺寸和更好的晶界组织。
这使得材料的硬度、强度和韧性等力学性能得到了显著提高。
半固态压铸工艺过程
半固态压铸工艺( Semi-Solid(Metal(Casting,简称SSM或SSMC)是一种介于传统铸造和锻造之间的先进金属成型技术。
它利用金属在半固态状态下的流变特性进行成型,结合了铸造和锻造的优点。
半固态压铸工艺过程主要包括以下几个步骤:
1.(金属熔炼:首先将金属原料加热至熔点,形成液态金属。
2.(半固态处理:将液态金属冷却至半固态,即部分凝固状态。
这一过程可以通过搅拌、振动或其他方法实现,目的是使金属在半固态时形成均匀的微观结构,包括细小的固态颗粒和液态金属相。
3.(半固态金属的预热:将半固态金属加热至适当的温度,以确保其具有良好的流动性和可塑性。
这一步骤对于保证成型质量至关重要。
4.(压铸成型:将预热后的半固态金属注入压铸模具中。
由于半固态金属的流动性好,可以在较低的压力下填充模具,减少成型缺陷。
5.(冷却与凝固:半固态金属在模具中冷却并凝固,形成所需的零件形状。
6.(脱模与后处理:冷却后的零件从模具中取出,进行必要的后处理,如去毛刺、热处理、表面处理等,以满足最终产品的性能要求。
半固态压铸工艺的优点包括:
提高材料利用率:由于半固态金属的流动性好,可以减少材料浪费,提高材料利用率。
减少成型缺陷:半固态金属的流动性和可塑性有助于减少成型过程中的缺陷,如气孔、缩孔等。
提高生产效率:半固态压铸工艺可以在较低的压力下成型,缩短了生产周期,提高了生产效率。
改善产品性能:半固态压铸工艺可以产生细小的晶粒结构,提高材料的力学性能和耐磨性。
半固态压铸工艺广泛应用于汽车、航空航天、电子和消费品等领域,用于生产各种复杂的金属零件。
半固态成形
日本在20世纪80年代后期就组成了半固志成形公司, Speed Star Wheel公司已应用半固态成形技术牛产铝台金轮 毂。Rheotech公司包括了14个钢铁企业和4个有色金属公司, 从1988年到1994年共投资30亿日元进行开发研究半固态成形 技术。日本制钢所已批量生产镁合金半固态触变铸造机,可 以铸造壁厚为0.5mm的零件,据报道该公司已为全球制造了 100台。另外,日本宇部公司设计制造的新型流变铸造机既 可以进行半固态模锻,又可以进行触变铸造与流变铸造,该 机已出售给奥地利,在2000年投产。
(3)工艺参数控制严格,不利于实现工业生产。
由于半固态成形对固相率控制严格,这就要求温度及冷 却条件等因素控制在较小的波动范围内,这样对于工业生产 的实现提出了更高的要求。同时,利用机械搅拌制备高固相 率的半固态材料比较困难。另外,二次(重熔)加热技术是 半固态成形技术中一个重要的技术环节,在二次加热过程中 要求加热速度较快才能达到理想的效果,这样就对设备提出 了更高的要求。因此,在工业生产中某个参数稍有波动,或 者操作工人的疏忽等,都会对成形工艺有重大影响。因此, 不但技术条件要求严格,而且对操作者的素质提出了更高的 要求对操作者的素质一套严格的控制系统,并对工人的素质 进行提高,才能较好地实现工业化生产。
2. 成形性能好,可实现短流程生产。
半固态材料流动性能与变形性能良好,经过强烈搅拌的固相 分数为40% - 60%的半固态金属的表观黏度在0.1-10Pa.s之间,与 黄油(0.1 Pa.s)、甘油(l Pa.s)及蜂蜜( 10 Pa.s)的表观黏度相当,仅 比水或者液态金属的黏度高出2-4个数量级,表现出很好的流动 性。与固态成形相比,半固态金属中存在液相组元,塑性变形机 理不同于固态塑性成形。塑性变形主要是由于晶粒之间的旋转和 相对滑移引起的,液相起到“润滑”作用,金属流动阻力显著降 低,复杂的零件也可用很少的工步成形。由于半固态合金材料具 有特殊的流变性能,易于加工成形,半固态铸造直接可以生产出 精度较高的产品。与传统生产方法相比,半固态成形可实现近终 形生产,提高了生产率、节约了原材料。与常规金属模铸造相比, 半固态成形汽车零件生产率与成材率高的特点尤为突出。
金属半固态成形工艺概述
降低 , 呈现 粘性 流体 特性 , 在微 小外 力作 用下 可发 生变 形流动, 但 粘 度 比液态 金 属 高 。 容 易 控制 ; ③ 复合 材 料 制 备 和成 形 , 当固相分数在极 限值 ( 约 7 5 ) 以下 时, 浆料 可 以进 行搅 拌 , 并 可很 容 易混入 异种 材料 的粉
变成 形和触 变成 形 。流变成 形 是利用 流变 浆料 直接 进 行 成 形 。而触变 成形 是 将 流 变浆 料 凝 固成 锭 , 按需 要
型 及 冲 压 上 下 料 弧 面 凸 轮机 械 手 .
维普资讯
维普资讯
Ke y w or d s:M e t a l s e mi - s o l i d f o r mi n g; No n — d e n d r i t e s t r u c t u r a l s e mi - s ol i d m e t a l ; Th i x o f o r mi n g;
维普资讯
铸 造 技 术
F0 U NDRY TECH N0 L0 G Y
Vol _ 2 8 NO.1
J a n . 2 0 0 7
金 属 半 固态 成形 工 艺概 述
杨 妮 , 葛正 浩 , 任 威 , 李 晓 芳
( 陕西科 技 大学 机 电工程 学 院 , 陕西 咸 阳 7 1 2 0 8 1 )
末、 纤维; ④ 应用 广泛 , 凡具 有 固液 两 相 区的合 金均 可 实现半 固态加工 , 适 用 于多种 加工 工艺 , 如铸 造 、 轧制 、 挤压 和锻 压 , 也 正是 这个 优点 , 才产 生 了多种 金属半 固 态成 形工 艺 ] 。
- 1、下载文档前请自行甄别文档内容的完整性,平台不提供额外的编辑、内容补充、找答案等附加服务。
- 2、"仅部分预览"的文档,不可在线预览部分如存在完整性等问题,可反馈申请退款(可完整预览的文档不适用该条件!)。
- 3、如文档侵犯您的权益,请联系客服反馈,我们会尽快为您处理(人工客服工作时间:9:00-18:30)。
A & 金属半固态成形工艺
当前, 金属半固态成形的基本工艺方法可分为流 变成形和触变成形。流变成形是利用流变浆料直接 进行成形。而触变成形是将流变浆料凝固成锭, 按需
! 《 铸造技术》 "# $ %""&
! 杨! 妮等: 金属半固态成形工艺概述
・ #CB・
要将此金属锭切成一定大小, 然后重新加热至金属的 半固态温度区, 这时的金属锭称为半固态金属坯料, 再利用金属的半固态坯料进行成形加工。 %’ #! 半固态金属的触变成形 %’ #’ #! 触变注射成形 ( ()*+,-,./*01) 触变注射成形工艺 ( 图 #) 是由美国 2,3 4)5-*67. 公司开发的技术, #88% 年由日本制钢所引入并完成成 形机的研制开发, 现在是半固态加工领域中最成功、 应用最广的技术之一。触变注射成形技术采用了一 种所谓 “ 一体化” 的成形方式, 将压铸和注塑工艺合二 为一, 其中模具和成形材料与压铸工艺相似, 而工艺 过程接近于注塑成形。此外, 该方法集半固态金属浆 料的制备、 输送和成形过程于一体, 较好解决了半固 态浆料的保存和输送难题, 提高了生产效率。
[ ?] 艺 ( 图 %) 。触变挤压成形是注塑和挤压成形过程的
(图 C ) , 将高温液态合金通过进料口注入到搅拌室, 液 态合金在重力和螺旋杆的搅拌作用下, 缓慢冷却, 形 成半固态浆料, 当在注射口堆积一定体积时, 由注射 装置注射成形。
结合。半固态浆料的二次加热类似于注塑成形, 而模 具则为挤压成形模具。
图 C! 流变射铸成形 9*1’ C! I)5,:,;-*01 <0=56>*,0 -,./*01
随后, 英国 J;@05. 大学范仲云等人用双螺旋杆替
图 %! 触变挤压成形 9*1’ %! ()*+,:,;-*01 5+>;@A*,0 -,./*01
代了搅拌室的单螺旋杆, 发明了双螺旋半固态金属流
通常, 流变铸轧包括 R 个工序, 首先先将合金原料 加入到电阻坩埚中加热熔化, 进行质变处理。其次, 在室温下, 待温度降至固液两相区温度时, 对熔体进 行机械搅拌, 生成半固态浆料。最后, 在固相线温度 以上, 将半固态浆料导入铸轧辊进行铸扎成形。 32 32 S! 低过热度倾斜板浇注式流变铸造 非机械或非电磁搅拌的低过热度倾斜板浇注式 简称 %’+ , 是一 流变铸造技术, 也称 %D? ’HD0B7AL=8> ,
进行铸轧成形, 是将铸造和热轧两种工艺合为一体, 让铸轧辊把熔融浆料的大量热能带走, 使浆料在很短 时间内完成铸造结晶过程, 同时, 又对已形成铸造金属流变注射成形机 "=>2 <! )?=8@ABCD? EDF=@A01=G ’HD0I0CF=8> J8KDBL=08 M01G=8> M7BH=8D
[ 55 ] 铸轧成形工艺 ( 图 :) 。触变铸轧是对半固态金属
液态金属产生剧烈的紊流, 提高了浆料的制备效率, 同时, 能生成更细小的晶粒。该成形工艺最大的优势 是将浆料制备 过 程 与 注 射 充 型 过 程 分 开, 在工艺方 面, 控制更易实现, 且更具实用性, 如旧机改造, 在现 有的压铸机、 压轧机上, 只需添加半固态浆料制备装 置, 调整工艺参数, 就可以进行金属半固态成形, 这也 是小企业在投 资 不 太 大 的 情 况 下, 成功转型的好办 法。
!"#$%&’$: !"# $#%&’ (#$)*(+’), -+.$)/0 %#1"/+’+02 3&( )/%.+,41#, -.+$ /+/*,#/,.)%# (%.41%4.&’ (#$)*(+’), $#%&’’ ( 1"&.&1%#.)(%)1( &/, (#$)*(+’), $#%&’ -+.$)/0 1"&.&1%#.)(%)1(5 6/ %"# 7&()( +%")( ,%"# -+.$)/0 8.+1#(()/0 +- 9#%&’ :#$)*(+’), 3&( #’&7+.&%#,, )/1’4,)/0 %"# %");+-+.$)/0 &/, ."#+-+.$)/05 <% %"# (&$# %)$#, %"# 1"&.&1%#.)(%)1 &/, 4()/0*&.#& +- #=#.2 8.+1#(()/0 &.# #=&’4&%#,5 ()* +,%-#: 9#%&’ (#$)*(+’), -+.$)/0;>+/*,#/,.)%# (%.41%4.&’ (#$)*(+’), $#%&’;!");+-+.$)/0; ?"#+-+.$)/0
・ 5SS・
! "#$%&’( )*+,%#-#.(
/012 34 %02 5 6782 399:
[ ;] 变注射成形机 ( 图 <) , 双螺旋杆旋转剪切力大, 并使
统构成。剪切机构由内、 外两个同心圆锥筒构成, 其 内筒由电机带动转动, 外筒固定, 通过调整内筒转速 和升降内筒高度 ( 即调整内、 外筒之间的缝隙) , 使半 固态金属浆料 在 内、 外筒缝隙之间受到剧烈剪切作 用, 从而制备出晶粒细小、 组织均匀的半固态金属浆 料, 可进行后续的压铸、 挤压、 压轧或锻造加工。 32 32 R! 流变铸轧 半固态镁合金板带连续铸扎是比较典型的触变
图 B! 触变锻造 ( ()*+,) 图 #! 触变注射成形 ()*+,-,./*01 9*1’ #! ()*+,:,;-*01 <0=56>*,0 -,./*01 9*1’ B! ()*+,:,;-*01 :,;1*01 -,./*01
半固态锻造成形的优点是扩大了复杂成形件的 范围, 因半固态金属的流动性好, 又易于控制, 可准确 称量, 所以锻造耗能低, 切削量少, 材料利用率较高。 %’ %! 半固态金属的流变成形 %’ %’ #! 螺旋式半固态流变成形 美国 4,;05.. 大学 E701 F@, F 等人应用注射成形
& & 金属半固态成形技术是 !" 世纪 ?" 年代产生的新 技术
[ %]
金属的热容量低。与传统的液态成形相比, 半固态金 属未达熔点温度, 成形温度低, 对模具的热冲击小, 并 且由于半固态金属中已有相当分数的已凝固金属存 在, 所以凝固速度快, 生产效率高。 %+ !& 金属半固态成形的特点 凭借非枝晶半固态金属的优良特性, 使得金属半 固态加工与传统的加工方式相比, 具有几点明显的优 势: !与固态金属加工比较。半固态浆料具有流变性 和触变性, 变形抗力小, 提高成形速度, 进行复杂件成 形, 缩短加工周期, 利于节能节材, 可进行连续形状的 高速成形; "与液态金属加工比较。随着固相分数的 降低, 呈现粘性流体特性, 在微小外力作用下可发生
・ %@!・
铸造技术 ,-./012 3456/-7-82
9:;+ !* /:+ % <=>+ !""?
金属半固态成形工艺概述
杨& 妮, 葛正浩, 任& 威, 李晓芳
( 陕西科技大学机电工程学院, 陕西 咸阳 ?%!"*% )
摘要: 分析了非枝晶半固态金属的特性和半固态金属的成形特征, 在此基础上, 较详细介绍了金属半固态成形工艺, 包括触变 成形和流变成形技术。同时, 分析了各种成形工艺的优、 缺点以及应用范围。 关键词: 金属半固态成形; 非枝晶半固态金属; 触变成形; 流变成形
收稿日期: !""#$%"$%! ; & & 修订日期: !""’$%%$!( 作者简介: 杨& 妮 ( %)*!$& ) , 女, 陕西西安人, 硕士生+ 研究方向: 材料 成型及冲压上下料弧面凸轮机械手+
[ !]
材料制备和成形, 当固相分数在极限值 ( 约 ?#D ) 以下 时, 浆料可以进行搅拌, 并可很容易混入异种材料的 粉末、 纤维; 凡具有固液两相区的合金均 $应用广泛, 可实现半固态加工, 适用于多种加工工艺, 如铸造、 轧 制、 挤压和锻压, 也正是这个优点, 才产生了多种金属
这种成形方法为许多难于铸造和塑性加工的特 殊材料, 如金属基复合材料、 脆性材料和易偏析材料。 该工艺是将半固态坯料由料口进入二次加热室, 经过 加热处理, 使半固态坯料变成浆状, 然后流入搅拌器, 搅拌后, 在液态金属中均匀悬浮着一定固相组分的固 液混合体, 最后通过模具型口得到理想形状的材料。 %’ #’ B! 触变锻造 ( ()*+, :,;1*01) #88C 年, 斯图加特大学的成形技术学院 ( <9D ) 开 始了对铝、 黄铜等金属的触变锻造研究, 将半固态金 属坯料移入锻压模具内, 利用感应加热器进行二次加 热, 使半固态坯料处于具有成分确定且均匀的液态和 固态之间, 然后模具的一部分向另一部分运动并加压 成形, 其成形原理及半固态金属向模具型腔流动的情 况如图 B 示。
[ (] ; 变形流动, 但粘度比液态金属高, 容易控制 # 复合
, 它是在金属凝固过程中, 对其施以剧烈的搅
拌作用, 充分破碎树枝状的初生固相, 得到一种液态 金属母液, 其中均匀地悬浮着一定球状初生固相的固 B 液混合浆料。该技术自问世以来, 一直倍受重视, 发展至今, 随着 金 属 半 固 态 成 形 理 论 研 究 的 日 臻 完 善, 金属半固体成形工艺也渐进成熟。本文在介绍成 形原理的基础上, 介绍了金属半固态成形工艺。