螺纹紧固件失效分析案例(第2部分)
螺纹紧固件常见失效模式分析

螺纹紧固件常见失效模式分析机械类产品装配中,零件与零件之间主要依靠紧固件联接。
其中螺纹紧固件应用最为广泛,紧固件的性能及联接效果直接影响到产品的性能和安全以及使用寿命。
紧固件的失效是常见机械类产品质量问题产生的原因,因此螺纹紧固件失效模式的潜在原因分析,对产品的质量提升有重要的意义。
1 螺纹紧固件常见的失效模式在我们工作中遇到的螺纹紧固件主要的失效模式看分为:①装配拧拉断裂;②螺纹受剪切力拧断;③应力集中部位使用后断裂;④疲劳断裂;⑤延时断裂;⑥零件扭矩报警;⑦螺纹滑牙。
2 常见失效模式的原因分析2.1 装配拧拉断裂拧拉断裂特征为断裂部位明显缩颈伸长,造成拧拉断裂的常见原因主要是由于联接面摩擦系数过小;拧紧或预紧时施加的扭矩过大、施加扭矩时套筒与螺纹不同轴、施加扭矩时速度过快;零件本身的性能强度不够以及紧固面与螺纹中心线垂直度超差。
2.2 螺纹受剪切力拧断受剪切力拧断的断口部位一般有螺旋状,无明显缩颈,造成螺纹受剪切力拧断的常见原因是由于螺纹在拧紧过程中被卡死,例如:螺纹变形、相互联接的牙型不一致、螺纹有焊渣灯情况;螺栓拧进的断面被顶住,如螺母为盲孔的有效螺纹深度不够。
2.3 应力集中部位使用后断裂应力集中部位使用后断裂常见表现在螺栓头部及头部与螺纹杆过度的直角部位,造成应力集中部位断裂的常见原因为头部与螺纹杆过度的直角部位圆角过小;螺栓冷镦成型时在头部的塑性流线存在缺陷。
被联接面与螺栓垂直度超差。
2.4 疲劳断裂在螺栓连接后使用的过程中主要的断裂为疲劳断裂,造成疲劳断裂的常见原因有:预紧力不足;夹紧力衰减过大;螺栓尺寸、性能不合格;零件之间的相互配合、装配环境、使用工况不能满足设计要求。
2.5 延时断裂延时断裂常见原因为氢脆,氢脆是在生产过程(如电镀、焊接)中进入钢材内部的微量氢,在内部残余的或外加的应力作用下导致材料脆化甚至开裂。
常见易发生氢脆的紧固件有:自攻钉/弹性垫圈/8级以上的经过电镀表面处理的螺栓。
螺纹紧固件常见的失效模式分析

能 满 足设 计 要 求 。
2 . 5 延时 断裂
延时断裂常见原因为氢脆 , 氢脆是 在生产过程 ( 如电镀 、 焊 接) 中进入钢材 内部 的微量氢 , 在内部残余 的或外 加的应力作 用下导致材料脆化甚 至开裂 。常见易发生氢脆的紧 固件 有 : 自 攻钉/ 弹性垫圈, 8 级以上的经过电镀表 面处理 的螺栓 。
螺 纹 连 接 常 常 出现 螺 纹 滑 牙 , 造 成 螺 纹 滑 牙 的 主 要原 因有
情况 ; 螺栓拧进 的断面被顶住 , 如螺母为盲孔 的有效螺纹深 度
不够 。
2 . 3 应 力集 中部位 使 用后 断 裂
应力 集中部位使用后 断裂常见表现在螺 栓头部及头部 与 螺纹杆过度 的直角部位 , 造成应力集 中部位断裂的常见原因为 头部 与螺纹杆过度 的直角部位圆角过小 ; 螺栓冷镦成型时在头 部的塑性 流线存在缺陷 。 被联接 面与螺栓垂直度超差。
机 械类 产品装配 中 ,零 件与零件之 间主要依靠紧 固件联 接。 其 中螺纹 紧固件应用最 为广泛 , 紧固件的性 能及联接效 果 直接影响到产品的性能和安全以及使用寿命 。 紧固件 的失效是 常见机械类产 品质量问题产生的原因 , 因此螺纹 紧固件失效模 式 的潜在原 因分析 , 对 产品的质量提升有重要 的意义 。
螺纹脱碳 : 常见现象为装 配时感觉扭矩加不上 , 螺栓拆下后 , 发 现螺纹全部 或部分被磨平 , 以及螺栓螺纹或者螺母孔表面硬度
低; 内外螺纹尺寸配合 : 相配合 的联接付接触面积小 , 有两种情
况: 一是接 齿合的螺纹扣数 少 , 二是 螺纹与螺纹不在 中径 以内 接触( 即精度配合不好 , 螺栓螺纹和螺母 的螺纹接触不够 ) 。 同时 , 在装配方法 上如果装配不对孔 , 强拧也会 造成螺纹 滑牙 ; 螺纹摩擦系数过小 : 表面涂层 、 表 面粗糙 度 、 表 面润滑剂 不合理和螺栓螺纹或者螺纹孔有异物 , 损坏螺纹 以及螺栓跟螺 母的螺距 、 角度变异都会导致螺纹滑牙。
螺纹连接件表面涂层失效分析一例

图2 正常批次连接件拧紧—松开试验曲线图 (拧紧力矩=14 N·m)
2.2 连接件表面涂层厚度的检测
采用金相截面检测的方法对两组试验件螺纹连
接部位的表面涂层厚度进行测量。结果显示,正常件
的最大涂层厚度为42.6 μm(图4),符合局部最大
涂层厚度≯50μm的要求;而缺陷件的最大涂层厚度 为100.7μm(图5),是最大涂层厚度要求的2倍。
生 产现场
SHOP
SOLUTION
螺纹连接件表面涂层失效分析一例
摘要:通过实例介绍了一种分析汽车制动管路连接件失效原因的方法,即使用扭矩测试仪分析
汽车管路联接的拧紧和松开过程,并结合失效件螺纹表面涂层厚度的金相检测,可以准确、快速地
判定由螺纹连接件表面涂层造成的连接失效,为螺纹连接件表面涂层不良的检测分析提供了直观和
完整的级进模冲压工艺实例见图22。
图22 某级进模冲压工艺简图
AT &M
(上接第58页)
表1 试验结果汇总表
检测项目
正常件
轴向预紧力(拧紧力矩14 N·m)/kN
5.80~6.66
旋转角度(拧紧力矩14 N·m)/(°)
133~168
最大松开扭矩/N·m
7.71~10.21
螺纹摩擦系数
0.22~0.25
图1 正常件(左)与失效件(右)密封面变形情况的对比
纹连接件各5件,在汽车管路联接扭矩测试仪上连接 汽车制动管路和对手件,模拟实际装车过程的连接拧 紧情况。
在试验台上对两组试验件分别使用扭矩扳手平 稳、匀速地施加拧紧力矩至规定值,然后再反向松开 螺纹连接件,扭矩测试仪上的力值传感器、转角传感 器和扭矩传感器在拧紧和松开过程中会实时记录轴向 预紧力、拧紧力矩和扭矩扳手的转角等数据;通过专 用的数据采集软件可将实时记录的试验数据值绘制成 连续的连接件拧紧—松开试验曲线图(图2和图3), 对比两组试验曲线图就能够清楚、直观地看出这两
螺纹紧固件失效分析案例(第1部分)

螺纹紧固件失效分析案例全国紧固件标准化技术委员会机械工业通用零部件产品质量监督检测中心二〇〇八年6月序机械产品失效是一门关于研究机械产品质量的综合性技术学科,主要研究失效的规律与机理。
机械零件的失效是在特定的工作条件下,当其所具备的失效抗力指标不能满足工作条件的要求时发生的。
导致零件失效的本质原因可能是材料本身的失效抗力不足,也可能是零件存在与设计或制造等过程有关的缺陷。
产品的早期失效往往是产品质量低劣或质量管理不善及科学技术水平不高的直接反映。
失效发生后能否尽快作出正确的判断,确定失效原因,制定防止失效的措施,则是衡量有关科技人员技术水平的重要标志。
加入WTO后,我国的产品将参与国际市场的竞争,于是提高产品质量成为提高竞争力的关键因素。
失效分析则是定量评定产品质量的重要基础,也是保证产品可靠性的重要手段。
机械科学研究总院、机械工业通用零部件产品质量监督检测中心在进行大量失效分析的基础上(包括对断裂、腐蚀和磨损的深入研究,特别是断口、裂纹和痕迹分析),分析了可能出现失效的形式和类型,以供大家在生产中借鉴,在生产工艺中加以避免出现失效的可能;同时,在今后的质量纠纷中维护自己的正当权益。
机械工业通用零部件产品质量监督检测中心熊学端研究员从事了几十年失效分析研究工作,有很深的理论造诣,积累了丰富的失效分析经验,本文中列举了部分螺纹紧固件失效分析案例,希望能够为生产企业及用户提供良好的参考和借鉴;同时,中心愿为生产企业和用户在今后的失效分析中提供技术咨询和指导。
全国紧固件标准化技术委员会目 录第一部分 失效分析概述 (1)1. 失效定义 (1)2. 失效分析的意义、目的 (1)3. 失效的来源 (1)4. 失效分析的思路、方法 (1)5. 断口分析 (2)6. 断口分析部分名词术语 (3)第二部分 失效分析案例 (7)1. 汽车上臂螺栓断裂原因分析 (7)2. 溜冰鞋螺钉、螺母断裂原因分析 (12)3. 紧定螺钉断裂原因分析报告 (20)4. 连杆螺栓断裂原因分析 (25)5. 汽车轮毂螺栓断裂原因分析 (29)6. M8×55高强度螺栓断裂原因分析 (33)7. 高压开关螺栓断裂原因分析报告 (37)8. 沟槽刚性接头紧固螺栓断裂原因分析报告 (42)9. 定位螺钉断裂原因分析 (47)10. M36×280高强度螺栓断裂原因分析 (53)11. 高压线塔联结螺栓断裂原因分析 (59)12. 中压电器用螺栓断裂原因分析报告 (64)13. 网架螺栓断裂原因分析 (66)14. 螺钉断裂原因分析 (69)15. 吊环螺钉断裂失效分析 (73)16. 螺栓失效原因分析 (79)第一部分 失效分析概述在具体讲述螺纹紧固件失效分析案例以前,先对失效分析的定义、意义、目的;失效的来源;失效分析的思路与方法;断口分析和名词术语等做一简单叙述。
SCM435螺栓断裂失效分析

s261体视显微镜下对断口进一步观察,断面干净、色泽呈亮灰色、结构粗糙,可观察到断裂的起源位于螺栓的近表面应力集中处,裂纹快速扩展区及剪切唇都明显可见,具有脆性断裂的典型特征。
图3所示为螺栓断口体视显微形貌。
用JSM-IT300扫描电镜对断口进行观察分析,断1#与断2#裂纹源位置相同,但裂纹源处并未发现有非金属夹杂等其他缺陷,整个断口都呈沿晶断裂,属脆性断裂。
图4、图5所示为断口扫描电镜形貌。
(3)化学成分分析 用ARL4460直读光谱仪对4根螺栓进行化学成分分析,螺栓化学成分如表1所示。
结果表明,2根失效螺栓化学成分与2根未失效螺栓化学成分基本一致,且都符合标准规定。
(4)微观组织检验 将1#断裂螺栓和4#未断螺栓切据后加工成金相试样,用4%硝酸酒精腐(a )断裂1 (b )断裂2图3 螺栓断口体视显微形貌图4 1#断口扫描电镜形貌有微小次生裂纹,呈沿晶断裂特征。
1#和4#螺栓都呈现回火马氏体组织,马氏体位向特征明显,马氏体板条界和板条内部析出大量细小的碳化物颗粒。
组织中也存在一定数量的大颗粒碳化物,该碳化物尺寸在1μm 左右,为奥氏体化时未溶碳化物,如图6、图7所示。
(5)维氏硬度检测 将1#断裂螺栓沿中心纵向剖开(见图8),在维氏硬度试验机上进行硬度检测,结果(见表2)未见异常,符合标准要求。
(6)非金属夹杂物金相评级检验 按GB/T10561—2005规定A 法对1#、4#螺栓进行非金属夹杂物评级。
从夹杂物评级中未(a ) (b )图1 1#断裂螺栓的宏观形貌(a ) (b )图2 2#断裂螺栓的宏观形貌蚀,在金相显微镜和扫描电镜下观察,1#试样在裂纹源处发现(a)(b)(c)(d)图6 1#螺栓次生裂纹形貌和扫描电镜组织形貌(a)(b)图7 4#螺栓扫描组织形貌图8 1#螺栓硬度检测部位表2 1#螺栓硬度检测结果(HV)位置Min Max平均纵向404418410.9横向405416408.6图5 2#断口扫描电镜形貌表1 螺栓化学成分(质量分数)(%)螺栓C Si Mn P S Cr Mo Al 1#(断裂)0.370.230.750.0170.0020.990.190.029 2#(断裂)0.380.220.770.0160.0020.980.180.031 3#(未断裂)0.370.250.760.0170.0020.980.190.030 4#(未断裂)0.360.240.760.0170.002 1.000.180.031图9 1#断裂螺栓氢析出曲线图10 4#未断螺栓氢析出曲线断裂特征。
紧固件典型失效形式及案例解析过载断裂
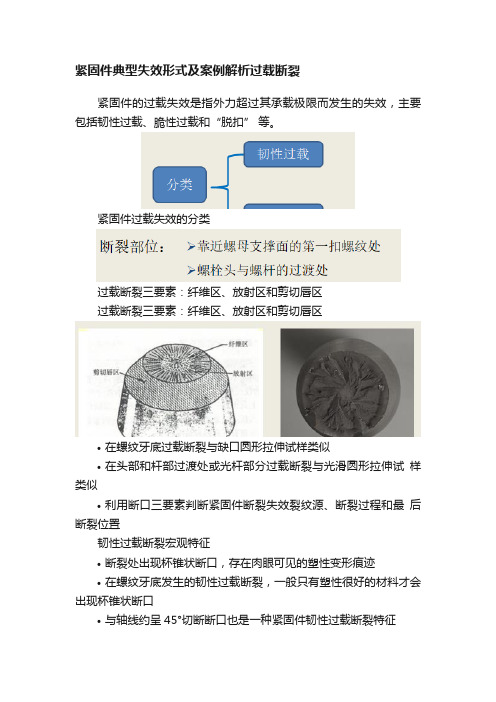
紧固件典型失效形式及案例解析过载断裂紧固件的过载失效是指外力超过其承载极限而发生的失效,主要包括韧性过载、脆性过载和“脱扣” 等。
紧固件过载失效的分类过载断裂三要素:纤维区、放射区和剪切唇区过载断裂三要素:纤维区、放射区和剪切唇区•在螺纹牙底过载断裂与缺口圆形拉伸试样类似•在头部和杆部过渡处或光杆部分过载断裂与光滑圆形拉伸试样类似•利用断口三要素判断紧固件断裂失效裂纹源、断裂过程和最后断裂位置韧性过载断裂宏观特征•断裂处出现杯锥状断口,存在肉眼可见的塑性变形痕迹•在螺纹牙底发生的韧性过载断裂,一般只有塑性很好的材料才会出现杯锥状断口•与轴线约呈45°切断断口也是一种紧固件韧性过载断裂特征•断口表面较粗糙、色泽灰暗、呈纤维状或鹅毛绒状•从紧固件表面一侧起源向另一侧扩展的过载断裂断口上,源区存在由表面起始的扩展棱线,最后断裂区一般有剪切唇•由表面周向起源,最终断裂区位于紧固件心部的过载断裂断口上,可见由周向边缘起始的扩展棱线,断口心部为纤维区韧性过载断裂宏观特征的应用•影响紧固件韧性过载断裂宏观特征的主要因素:受力状态和材料的塑性•通过断裂外观形态、宏观塑性变形方式、纤维的形态等对紧固件受力状态进行初步的判断例:拉伸应力导致的断裂:断口往往呈杯锥状或呈与应力轴45°的斜断口韧性过载断裂宏观特征的应用例:冲击应力或弯矩作用时:断口宏观特征上也可见放射棱线和剪切唇,但剪切唇在紧固件圆周上不完整例:扭转拉伸应力作用下断口呈现明显的“漩涡状”扭转痕迹韧性过载断裂微观特征•韧窝是紧固件韧性断裂的主要微观特征,但并非充要判据•判断紧固件是韧性断裂还是脆性断裂更为关键的在于紧固件断裂前是否发生可察觉的塑性变形紧固件韧性过载原因案例解析案例解析某螺栓在安装过程发生异常断裂失效存在“月牙形”高温氧化色原始断面根据扭矩、轴力、扭矩系数之间的关系抗拉强度扭矩系数K编号断裂扭矩NmMPa1-1 431.9 1222 0.0722-1 510 1240 0.084从图表中数据可以看出,螺纹和垫片未润滑和润滑后吹干扭矩系数和摩擦系数变化较小,而润滑后对扭矩系数和摩擦系数有显著的影响,从1#模拟安装情况可以看出,扭矩未达到530Nm前,就出现屈服现象。
几种紧固件断裂现象及原因分析[2]
![几种紧固件断裂现象及原因分析[2]](https://img.taocdn.com/s3/m/5a2e9442fe4733687e21aa3a.png)
冷镦紧固件的生产检验工艺流程
1、化学成分 2、表面脱碳及偏析
进料 ——— 拉拔 ——— 球化退火
3、脱碳层检验
———拉拔———冷镦———滚丝 ———热处理————表面处理
6、螺纹检验
7、破断拉力 8、硬度 9、脱碳层源自4、外径检验5、尺寸检验
10、盐雾 试验
一、几种冷拔工艺引起的失效实例 1、一次形变量太大引起内部拉断
40Cr
38CrSi 20MnTiB 30CrMnTi 30CrMnSi 20CrNi3A 12Cr2Ni4A
250~350 200-280 ℃
300~370 ℃
250~380 ℃ 250~350 ℃ 250~350 ℃ 300~400 ℃
第二类回火脆性 500 ~550 ℃ 510~610 ℃ 500~650 ℃ 450~550 ℃ 520 ℃ 左右 500~600 ℃ 450~650 ℃ 450~550 ℃ 490-550 ℃ 400~450℃ 460~650 ℃ 450~550 ℃
37CrNi3
480~550 ℃
举40Cr钢为例
•40Cr 300~370 ℃ 450~650 C 用40Cr做10.9级℃螺栓, •硬度要求是HRC34—39 •一般热处理工艺是: 淬火温度860 ℃ ,回火温度500 ℃
三、脱碳层检验
1、线材球化退火后的脱碳层检验
2、电镀后的脱碳层检验
镀锌为例
二、网带炉热处理
1、较大件的热处理 (Φ30以上) 42CrMo Ms:360℃ Mf:170 ℃
2、如何解决回火脆性
常用钢产生回火脆性的温度范围 钢号 第一类回火脆性 30Mn2 250~ 350 ℃ 25Mn2V 250~ 350 ℃ 35SiMn 45Mn2B 20MnVB 200~260 ℃ 40MnVB 200~350℃ ℃
汽车螺纹紧固件几种失效案例分析

摘要:高强度紧固件在连接结构中的失效经常出现,失效的模式和原因各种各样,有设计、材料、制造、热处理、装配等多方面原因,本文针对几种汽车用螺纹紧固件的失效案例,从头部R 角、材料选用、延迟断裂、疲劳断裂等方面分析了失效的模式和原因,提出了改进的建议和方案,对紧固件的制造和装配有一定的指导意义。
关键词:螺纹紧固件疲劳延迟断裂松动中图分类号:TH131.3文献标识码:BDOI :10.19710/ki.1003-8817.20180142汽车螺纹紧固件几种失效案例分析裕莉莉李海东郭学敏王吉洋井琦张薇(中国第一汽车集团有限公司研发总院,长春130011)作者简介:裕莉莉(1987—),女,工程师,硕士研究生,研究方向为连接技术与金属材料研究检验。
1前言高强度紧固件在连接中失效经常会遇到,失效的模式和原因各种各样,有设计、材料、制造、热处理、装配等多方面原因,多种问题可以归结为三大类:即设计、制造、使用。
目前,高强度紧固件企业在材料选择、加工制造、热处理方面等几个方面技术日臻完善,这类问题出现的概率大幅地减少。
一般整机行业对紧固件方面不重视,对安装扭矩、摩擦系数、扭矩系数及其分配比例知之甚少;这样,往往会在高强度紧固件安装使用中出现一些问题。
现主要针对几种典型的螺纹紧固件失效案例进行分析。
2失效案例分析2.1头部R 角失效某型车扭杆弹簧调整支架与车架连接螺栓断裂,螺栓的断裂位置均发生在头部R 角处,如图1所示。
对失效螺栓的断口进行分析可知,螺栓均为疲劳断裂,如图2所示。
该螺栓规格M14,10.9级,硬度检验结果为(34-36)HRC ,符合GB/T 3098.1-2010中的技术要求。
该螺栓可能是螺栓头部R 角处制造问题,(R 角过小导致应力集中),产生的局部应力集中造成图1失效螺栓形貌断裂处1#2#图2断口形貌(b )2#螺栓(a )1#螺栓疲劳断裂。
对于螺纹紧固件,在GB/T 3098.1-2010中明确规定,在拉伸试验时,螺栓的断裂位置,不应断裂在头部或头部与杆部交接处。
- 1、下载文档前请自行甄别文档内容的完整性,平台不提供额外的编辑、内容补充、找答案等附加服务。
- 2、"仅部分预览"的文档,不可在线预览部分如存在完整性等问题,可反馈申请退款(可完整预览的文档不适用该条件!)。
- 3、如文档侵犯您的权益,请联系客服反馈,我们会尽快为您处理(人工客服工作时间:9:00-18:30)。
5.金相组织分别对未断与断裂螺钉和螺母各1件纵向解剖进行金相观察。
图8为试样末浸蚀时的低倍形貌。
a 25×b 50×c 25×图8 螺钉纵剖金相磨面(a、b—螺钉,c—螺母)从图可以清楚地看到,螺钉在牙的侧面存在明显的裂纹,每个牙上裂纹的位置与形态完全一致,将裂纹放大后(图8b)可以明确判断,上述裂纹实际上是螺钉在搓丝过程中形成的折叠。
折叠处(图8b中的A处)的显微硬度为540HV,0.05明显要高于其他部位的渗碳层的硬度,此系A处两面渗碳的结果,这点同时也说明上述裂纹在热处理前业已存在。
另外,对一个断裂的螺钉解剖后发现,在过渡圆角处存在细微裂纹(图9),浸蚀后观察,该裂纹沿晶扩展(图10),这与断口源区扫描电镜下观察到的沿晶断裂特征(图3)完全吻合。
在裂纹周围也未发现非金属夹杂物聚集和沉淀相析出。
图9 断裂螺钉圆角处的裂纹50× 图10 图9裂纹浸蚀后的放大形貌500×螺母牙顶形成双峰(图8C),这也是搓丝工艺不当所形成的。
双峰鞍部形成的不规则尖缺口将对随后的热处理及使用均将产生不利影响。
图11为螺钉渗碳层的低倍形貌及渗层组织,渗碳层为回火屈氏体。
断裂与未断裂螺钉的芯部组织均为板条马氏体,未断螺钉的马氏体板条更粗大些(图12)。
25× 100×图11 螺钉渗碳层形貌及组织a断裂螺钉 b未断螺钉图12 螺钉的芯部组织500×图13为螺母的渗碳层组织,断裂与未断裂螺母的渗碳层组织相同,均系回火屈氏体。
断裂螺母与未断裂螺母的芯部组织则完全不同(图14)。
图13 螺母的渗碳层组织250×a 断裂螺母b 未断螺母图14 螺母的芯部组织 500×断裂螺母芯部组织为绌片状珠光体+铁素体,而未断者为板条马氏体。
这与表1中螺母测定的硬度值完全对应。
6.含氢量分析根据螺钉断口形貌特征及延时断裂特征,加之螺钉经酸洗后镀锌,怀疑有渗H2现象[1]。
因此,对螺钉进行了含氢量测定,采用高频加热——热导法(QB-Q-05-81)。
为了对比,对螺钉和螺母经除H2处理与未除H2处理(原始态)各1件进行了测定。
结果如表2。
表2螺钉H2含量原始态 含H2量0.0005(5ppm)螺钉220℃×3h除H2含H2量0.0006(6ppm)原始态 含H2量0.0006(6ppm)螺母230℃×3h除H2含H2量0.0003(3ppm)显然,螺钉镀锌过程中已显著渗H2,尽管尝试了除氢处埋,螺钉没有显示出效果(和除氢温度和时间不够有关),螺母中的含氢量虽降低了一半,但仍然很高。
三、结果分析1.原材料从螺钉、螺母的金相组织可以初步判断,材料为低碳钢。
螺钉的断裂表明与材料成分没有关系,因此对材料的化学成分未作且也无必要进行分析。
螺钉的非金属夹杂物未见异常。
2.机加工从检验结果可以明显看出,无论是螺钉还是螺母,在机加工过程中均存在明显的缺陷。
螺钉在搓丝过程中产生了严重的折叠,折叠形成的尖锐缺口,在随后的热处理过程中极易诱使缺口继续扩展。
另外,这种折叠缺口沿周向分布,与外加载荷主应力垂直,由于应力集中效应,很容易使螺钉拧紧时产生的拉应力作用下造成裂纹缓慢扩展,最终导致失稳断裂。
螺钉双峰齿顶的形成同样也是加工螺纹时工艺不当产生的,双峰之间鞍部的尖锐缺口对螺钉的使用性能不利。
3.热处理检验结果表明,螺钉和螺母渗碳层分布及组织没有发现异常。
但断裂螺母的芯部组织为P+F混合组织,完伞不同于未断螺母的板条马氏体组织。
P+F混合组织的力学性能明显要低于板条马氏体,这种混合组织的形成显然是热处理失误的结果。
从螺钉硬度检测结果看,螺钉表面硬度最高值为487HV0.05,高于技术要求(480HV)的上限。
螺母的表而硬度最高值达到36.5~40HRC,大大高丁技术要求28~32HRC的值。
过高的硬度将使螺钉变脆,尤其是在螺钉表面加工质量不良或存在微裂纹的情况下,更易诱发裂纹的形成和快速扩展。
4.氢脆金属材料中存在H,将导致材料脆化。
断口形貌及显微组织(图3,图10)2量测定,表明,螺钉和螺母断口源区为沿晶断口,并观察到鸡爪花样,以及含H2现象。
氢含量过高,将使材料的说明螺钉在电镀(包括酸洗)过程中产生了渗H2塑性、缺口拉伸强度降低,甚至在材料内部形成微裂纹,造成在静载条件下的延时断裂。
存在于金属的原子氢,随着时间的推移,向夹杂、晶界、位错等处移动,形)。
在材料内部产生可高达13000个大气压的压力。
当有氢存在时,成氢分子(H2甚至在小于材料屈服强度40%的外加应力条件下,几个小时便会引起破坏[2],这种破坏在材料强度高、应力集中较严重的零件中表现尤为明显。
资料[2]中指出,当碳钢的抗拉强度超过105psi(700Mpa)时,极易导致氢损伤。
根据硬度与强度的换算,螺钉和螺母表面层的最低强度极限已达1185Mpa,加之螺纹机加工造成的缺陷引起应力集中,说明螺钉已存在产生氢脆的强度条件。
金属材料中允许的氢含量为多少,尚无严格的标准,但对材料造成损害是确定无疑的。
含氢量的多寡仅表现为对材料损伤程度的差别,因为这里还涉及到一个外力门槛值问题。
换句话说,含氢量高时,在不高的外力作用下便会产生氢致断裂。
含几个ppM氢的碳钢构件发生氢致开裂的案例很多,甚至在含O.6ppM氢的情况出现断裂的案例也并不罕见[2][3],何况被检螺钉中的氢含量高达6ppM。
螺钉中增氢的原因是由于在酸洗、电镀过程中操作不当引起的。
可靠的方法是在电镀后增加一道除氢处理。
综上所述,螺钉在机加工、热处理、酸洗和电镀过程中均存在轻重程度不同的缺陷。
在此必须强调一点的是,断在螺钉过渡圆角处主要是氢脆的结果,而断在螺纹终止处的螺钉、螺母主要是螺纹加工中形成的缺陷及氢脆联合作用所为。
四、结论1.螺钉在螺纹加工过程中形成的缺陷(折叠、双峰)和酸洗、电镀过程中产生渗氢是螺钉静载延时断裂的主要原因;2.螺钉和螺母表面硬度过高(尤其是螺母),以及螺母的芯部组织的不同(有的为P+F,有的为M板条),说明热处理工艺不稳定,对螺钉的使用寿命有一定的影响。
参考文献:[1]L.Engel Rasterelektronenmikroskopische Untersuchungen Von Metallsschaden[2]美国金属学会 金属手册 第八版第十章 1975年[3]中国机诫工程学会材料学会主编 轴及紧固件的失效分析 1988年3. 紧定螺钉断裂原因分析报告某公司送检两个失效紧定螺钉,两个螺钉在使用中约经100次开合后便发生断裂。
螺钉规格为M8×25。
送检样品均为断裂后靠螺钉头部的一段(以下简称为1号钉和2号钉)。
一、检验1.外观图1为送检的两个断钉的外观形貌,根据其头部为内六角的结构形式,可判断螺钉的性能等级为45H(GB/T3098.3-2000)。
螺钉表面经发黑处理,宏观未见塑性变形及伤痕。
断口与螺钉轴线垂直,为切断型断裂。
图1 断钉外观形貌2.断口断口经丙酮和超声波反复清洗后,在扫描电镜下观察。
图2为两个断口的低倍形貌。
1号钉 2号钉图2 两个断口的低倍形貌由图可见,两个螺钉均在牙根处断裂。
1号钉断口比较平坦,裂纹扩展线依稀可见。
2号钉扩展线比较明显。
两个螺钉断口均可分成为三个区域:断裂起始区;裂纹扩展区;最后瞬断区。
根据裂纹放射扩展线的收敛方向,可以确定断裂的起始源区。
1号钉断裂源区为一个,2号钉断裂源区为两个(图2中箭头所指),2号钉两个断裂源区引发的断裂面相交处形成一个明显的剪切台阶。
由放射条带的收敛处不是一个点,而是一个区可判断,断裂源区存在的是条带状缺陷。
将1号钉断裂源区高倍放大(图3),从图象中可以看到,源区附近的一个窄小区域显示出沿晶断裂特征,并可见腐蚀产物形貌。
基体的断裂微观形貌为准解理+撕裂棱+二次裂纹。
2号钉的断口微观形貌(图4)与1号钉的完全相同。
a bc d图3 1号钉断口扫描电镜微观形貌a-断裂源区的沿晶形貌;b-图a 的放大c-邻近源区的螺钉表面的网状裂纹(箭头所指)d-螺钉基体的断裂形貌(准解理+撕裂棱+二次裂纹)a bc d图4 2号钉断口扫描电镜微观形貌a、b、c——两个断裂源区的沿晶断裂以及邻近源区的螺钉表面的网状裂纹(箭头所指) d-螺钉基体的断裂形貌(准解理+撕裂棱+二次裂纹)3.金相沿螺钉轴向切取试样做金相观察。
图5为螺钉原材料中的非金属夹杂(两个螺钉的情况相同,仅以1号钉为例示如图5)。
根据GB/T10561-1989(ASTM标准评级图)评定,各类夹杂物级别为A类:0.5级 B类:1级C类:0.5级 D类:1.5级图5 螺钉材料中的非金属夹杂物 100×螺钉基体的金相组织均为保持马氏体位向的回火屈氏体(图6),2号钉的组织比较粗大。
1号钉 2号钉图6 螺钉的基体组织 500×在两个螺钉的金相磨面上可观察到同样下述缺陷特征(图7):①牙顶折叠裂纹牙顶折叠裂纹的最大深度:1号钉为0.18mm,2号钉为0.20mm。
另外在2号钉的牙侧,中径线以下也观察到一条深度为0.024mm的折叠裂纹。
②牙底、牙侧的锯齿状缺口和网状裂纹在牙底观察到的网状裂纹及深度与断口源区存在一薄层沿晶断裂特征相吻合。
a 25×b 100×c 100×d 250×e 25×f 100×g 100× h 250×图7 两个螺钉的缺陷a、b、c、d-1号钉的牙顶折叠裂纹以及牙侧、牙底的锯齿状缺口及网状裂纹e、f、g、h、i-2号钉的牙顶、牙侧折叠裂纹以及牙侧、牙底的锯齿状缺口及网状裂纹4.硬度1号钉:514 HV102号钉:506 HV10二、分析讨论检测结果表明,两个螺钉的硬度均在GB/T3098.3-2000所规定的450-560 HV 范围内。
材料的非金属夹杂和金相组织未见异常。
两个螺钉在生产制造中存在同样的下述两个问题:1.牙顶折叠裂纹如前面所述,两个螺钉的牙顶折叠裂纹深度都超过0.18mm,根据GB/T5779.3-2000的规定,该尺寸的螺钉牙顶折叠裂纹深度最大值不允许超过0.17mm,据此可以认为,所分析的两个螺钉为不合格品。
2.牙底的锯齿状缺口及裂纹由螺钉牙底直径小和它的形状特征决定了该处为最容易破断的区域,牙底存在的如图7所示的缺口及网状裂纹将使该处的工作应力进一步提升,从而导致螺钉的断裂。
根据两个螺钉牙侧、牙底密布的缺口及网状裂纹,以及断口源区的沿晶断裂特征和存在的腐蚀产物形貌,可以推断,该类缺陷的产生是由于螺钉在酸洗、发黑的过程中过腐蚀的结果。
三、结论1.两个螺钉断裂的原因完全相同,都是由于牙底存在尖锐缺口及网状裂纹引起的。