多层薄膜生产工艺
ldd工艺技术

ldd工艺技术LDD(Low-dose Dielectric Deposition)工艺技术是一种低剂量多层介电薄膜沉积方法。
该技术主要应用于微电子器件中的绝缘层的制备,以及提高器件性能和可靠性。
LDD工艺技术的核心是使用较低的剂量沉积介电薄膜。
传统的沉积方法通常会使用较高的剂量,这可能导致薄膜中的缺陷增加,增加电学导通、击穿和漏电等问题。
而LDD工艺技术通过控制沉积的剂量,可以在实现所需介电性能的同时,尽可能减少薄膜中的缺陷。
LDD工艺技术的另一个重要特点是多层沉积。
在传统的沉积过程中,通常只会增加一层介电薄膜。
而LDD工艺技术通过多次进行低剂量沉积,并在每层之间进行退火和修饰工序,可以形成更为完整和均匀的介电层结构。
这样的多层结构可以有效地减少薄膜中的缺陷,提高电学性能和可靠性。
LDD工艺技术的应用范围非常广泛。
在微电子器件中,绝缘层的制备十分重要。
LDD工艺技术可以用来制备绝缘层,以提供电学隔离、防止电子漏泄和电磁干扰等作用。
此外,LDD工艺技术还可以应用于光电器件的制备,如太阳能电池、显示屏等。
这些器件也需要具有一定的绝缘层,以提高其电学性能和可靠性。
在LDD工艺技术的具体实施中,有几个关键因素需要考虑。
首先是沉积剂量的控制,这决定了薄膜的质量和性能。
较低的剂量可以降低缺陷数量,但过低的剂量可能导致薄膜质量下降。
其次是退火和修饰工序的设计,这对形成完整的多层介电结构至关重要。
实验和模拟技术可以帮助优化这些参数,以实现最佳工艺条件。
总之,LDD工艺技术是一种提高微电子器件性能和可靠性的重要方法。
通过低剂量沉积和多层结构的设计,可以有效地减少介电薄膜中的缺陷,提高器件的电学性能和可靠性。
在微电子器件制备和光电器件制备等领域都有广泛的应用前景。
随着技术的不断发展,LDD工艺技术将不断优化和改进,进一步推动微电子行业的发展。
多层共挤流延膜

多层共挤流延膜
多层共挤流延膜是一种塑料薄膜的生产工艺,通过将多个不同的熔体层以共挤的方式挤出到一起,形成多层结构的薄膜。
这种工艺可以利用不同材料的特性,使得膜具有更好的性能和功能。
多层共挤流延膜可以应用于各种领域,例如包装行业、农业覆盖膜、建筑材料等。
不同层次的材料可以提供不同的特性,例如抗水性、氧隔离性、耐热性、机械强度等。
此外,多层共挤流延膜还可以实现复合材料的制备,通过将不同的材料层结合在一起,达到更多的功能要求。
多层共挤流延膜的生产过程中需要使用共挤挤出机,通过控制挤出头的结构和温度,调节每层材料的厚度和比例。
同时,也需要对材料进行适当的配方设计和工艺参数的优化,以确保薄膜的质量和性能。
总之,多层共挤流延膜是一种利用共挤技术将多个材料层挤出到一起形成多层结构的塑料薄膜制备工艺,可以实现多种功能和特性的要求。
BOPP生产设备与工艺
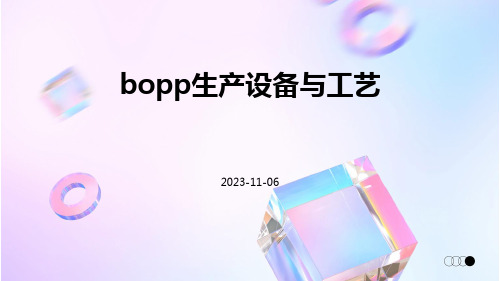
设备兼容性与工艺协调
设备的兼容性决定了不同工艺流程的协调和配合,对生产效率和 成本控制具有重要影响。
设备更新与工艺进步
新设备的引入和更新能够推动工艺技术的进步,提高生产效率和 产品质量。
工艺对设备的需求
组成
冷却设备主要由冷却风嘴、冷却辊和张力辊等组成。
工作原理
物料经过挤压机后进入冷却设备,通过冷却风嘴和冷却辊的作用,将物料表面的热量迅速 散去,同时保持物料的张力和稳定性,以避免物料在冷却过程中出现变形和皱褶等问题。
牵引机
作用
牵引机的主要作用是将挤出的薄膜按照要求的速度和张力进行牵引,以保证薄膜的厚度和宽度。
成薄膜,同时对薄膜进行塑化和拉伸。
02
组成
挤出机主要由传动装置、挤压装置、冷却系统和控制系统等组成。
03
工作原理
物料经过喂料装置进入挤出机,在挤压装置的作用下被加热、压缩和
塑化,然后通过冷却系统进行冷却和拉伸,最后通过牵引机和收卷机
等设备进行收卷和加工。
冷却设备
作用
冷却设备的主要作用是将挤出的薄膜迅速冷却,以防止薄膜粘连和粘结。
清理散热器
定期清理散热器表面的灰尘和杂物,提高散热效 果。
检查冷却液
定期检查冷却设备中的冷却液是否充足,并更换 变质或污染的冷却液。
牵引机的维护与保养
检查牵引速度
定期检查牵引机的牵引速度是否稳定,以确保产品质量。
检查电机和传动系统
定期检查牵引机的电机和传动系统是否正常工作,防止设备卡 滞或损坏。
清理牵引轮
06
bopp生产设备与工艺的 发展趋势
半导体制造技术—第四讲:淀积工艺

提供反应物质:反应气体是淀积过程中形成薄膜的主要物质来源 控制反应速率:反应气体的浓度和流量可以控制反应速率从而影响薄膜的厚度和质量 影响薄膜性质:反应气体的种类和比例可以影响薄膜的性质如导电性、光学性能等 参与化学反应:反应气体在淀积过程中参与化学反应形成所需的薄膜材料
半导体制造技术之淀 积工艺
汇报人:
目录
添加目录标题
淀积工艺概述
淀积工艺的原理
淀积工艺的应用
淀积工艺的优缺点
淀积工艺的未来展 望
添加章节标题
淀积工艺概述
淀积工艺是半导体制造过程中的关键步骤之一 主要目的是在硅晶圆上沉积一层或多层薄膜 薄膜可以是金属、氧化物、氮化物等 淀积工艺包括化学气相淀积(CVD)、物理气相淀积(PVD)等方法
研究方向:新型材料、新工艺、新设备 技术挑战:提高性能、降低成本、提高可靠性 研发目标:实现更高性能、更低成本、更可靠的淀积工艺 研发成果:新型材料、新工艺、新设备的研发和应用
太阳能电池:利用淀积工艺制造高效太阳能电池提高光电转换效率 燃料电池:利用淀积工艺制造高性能燃料电池提高能源转换效率 储能设备:利用淀积工艺制造高性能储能设备提高储能效率和稳定性 电动汽车:利用淀积工艺制造高性能电动汽车电池提高续航里程和充电速度
物理淀积的优 点是沉积速度 快沉积层厚度 均匀沉积层质
量高
化学淀积是一种通过化学反应在半导体 表面形成薄膜的过程
化学淀积可以分为气相化学淀积和液相 化学淀积两种类型
气相化学淀积是通过化学反应在半导体 表面形成薄膜的过程
液相化学淀积是通过化学反应在半导体 表面形成薄膜的过程
化学淀积工艺可以应用于半导体制造中的各 种薄膜制备如氧化物、氮化物、金属等
【2024版】微电子工艺之薄膜技术

二、外延掺杂及杂质再分布
3.杂质再分布
再分布:外延层中的杂质向衬底扩散;
衬底中的杂质向外延层扩散。
总杂质浓度分布:各自扩散的共同结果。
①衬底杂质的再分布(图3-21)
初始条件:N2(x,0)=Nsub,x<0; N2(x,0)=0,x>0; 边界条件一:衬底深处杂质浓度均匀,即
当vt» D1t 时,有
N1x,t
Nf 2
erfc
2
x D1t
二、外延掺杂及杂质再分布
当vt»2 D1t 时,有
N1(x,t)≈Nf
③总的杂质分布(图3-24)
N(x,t)=N1(x,t)± N2(x,t) “+”: 同一导电类型;
“-”:相反导电类型;
三、自掺杂(非故意掺杂)
1.定义
N 2 x
x 0
二、外延掺杂及杂质再分布
边Jd界条D件2 二Nx:2 在xx外f 延J层b 表J s面 (h2x=vxfN)2 ,扩x f 散,t 流密度Jd为
解得:
N2x,t
N sub 2
erfc
2
x D2 t
v h2 2h2
v
ex
p
D2
vt
x erfc
2vt x 2 D2t
①当hG» ks,则 NGS≈NG0,V= ks(NT/ NSi) Y,是表面反 应控制。
②当ks» hG,则 NGS ≈0, V= hG(NT/ NSi) Y,是质量转 移控制。
二、外延掺杂及杂质再分布
1. 掺杂原理-以SiH4-H2-PH3为例
薄膜组件封装工艺简介薄膜组件封装工艺简介

超声波焊 接
功率测试
合
装接线盒
格
清洗包装 入库
检验 不合格
返修
裁切PVB 摊铺PVB
背玻璃清 洗
合背板
高压釜
层压工序 成品层压
半成品层压
薄膜组件封装工艺简介薄膜组件封装 工艺简介
二、清洗工序
薄膜组件封装工艺简介薄膜组件封装 工艺简介
清洗工序:
清洗工序的作用:把钢化玻璃清洗干净,达到 工艺要求; 封装车间清洗机所清洗的是电池的背玻璃,这 种背板玻璃是一种钢化玻璃;
薄膜组件封装工艺简介薄膜组件封装 工艺简介
PVB的性质:
(2)PVB的化学性质: 涂料具有高适用性、弹性、高韧性、兼容性。 耐强碱、耐油性、可挠性与低温抗冲击性。 添加可塑剂后,皮膜柔软性特优。 使用胶合安全玻璃中间膜,使玻璃具有强大的 耐冲击与耐穿透力。 与无机材质之接着强度、架桥性、放蚀性优良。 依PVB之不同能基(Functional group)可溶于醇、 酮、酯等类溶剂。
薄膜组件封装工艺简介薄膜组件封装 工艺简介
层压:(非晶)
1)钢化玻璃 2)PVB胶膜 3)前电池板
背板玻璃 PVB胶膜
前电池板
薄膜组件封装工艺简介薄膜组件封装 工艺简介
层压:(晶硅)
1)钢化玻璃 2)EVA 3)电池串 4)EVA 5)背板(TPT)
薄膜组件封装工艺简介薄膜组件封装 工艺简介
薄膜组件封装工艺简介薄膜组件封装 工艺简介
以非晶硅车间1#层压机为例, 具体的介绍层压机的性能:
薄膜组件封装工艺简介薄膜组件封装 工艺简介
三、层压机工序 裁切与摊铺
薄膜组件封装工艺简介薄膜组件封装 工艺简介
PVB材料的概述:
薄膜材料与技术

薄膜材料与技术引言薄膜材料是一种在厚度范围内具有特定性能和结构的材料,它在多个领域中发挥着重要作用。
薄膜技术是制备、改进和应用薄膜材料的一套方法和工艺。
本文将介绍薄膜材料的定义、制备方法、常见应用以及未来的发展趋势。
薄膜材料的定义薄膜材料是在纳米尺度至微米尺度范围内的一种特殊材料,其厚度通常在0.1nm到100μm之间。
相比于传统材料,薄膜材料具有较高的比表面积和特殊的物理、化学性质,使得其在光电、能源、生物医学等领域具有广泛的应用前景。
薄膜材料的制备方法薄膜材料的制备方法多种多样,常见的制备方法包括:1.物理气相沉积(PVD):通过热蒸发、电子束蒸发、激光蒸发等方法将材料蒸发在基底上,形成薄膜。
2.化学气相沉积(CVD):将气相前体分子引入反应室中,经过热分解或化学反应,在基底表面生成薄膜。
3.溶液法:将溶解了材料的溶液涂覆在基底上,通过溶剂蒸发或化学反应,将材料转变为薄膜。
常见的溶液法包括旋涂法、浸渍法等。
4.声波法:利用声波的能量使材料溶解或悬浮在溶剂中,然后将溶液通过超声波定向沉积在基底上。
5.离子束辅助沉积(IBAD):通过将离子束轰击基底表面,促使薄膜材料原子结晶或沉积在基底上。
薄膜材料的应用领域薄膜材料在多个领域中发挥着重要作用,以下是几个常见的应用领域:1.光学领域:薄膜材料在光学镀膜中广泛应用,用于改善光学元件的透射和反射特性。
例如,透明导电薄膜可用于制造触摸屏、光伏电池和显示器件。
2.电子领域:薄膜材料可用于制造半导体器件,如晶体管、薄膜电阻器和电容器。
此外,薄膜材料还可用于制造柔性电子产品和纳米电子元件。
3.能源领域:薄膜太阳能电池是一种高效能源转换设备,薄膜材料在其制备过程中起到关键作用。
此外,薄膜材料还可用于燃料电池、锂离子电池等能源存储和转换装置中。
4.生物医学领域:薄膜材料在生物医学传感器、生物芯片、医用导管等方面有广泛应用。
例如,聚合物薄膜可用于修复组织缺损,金属薄膜可用于制造仿生传感器。
吹塑法和流延法比较
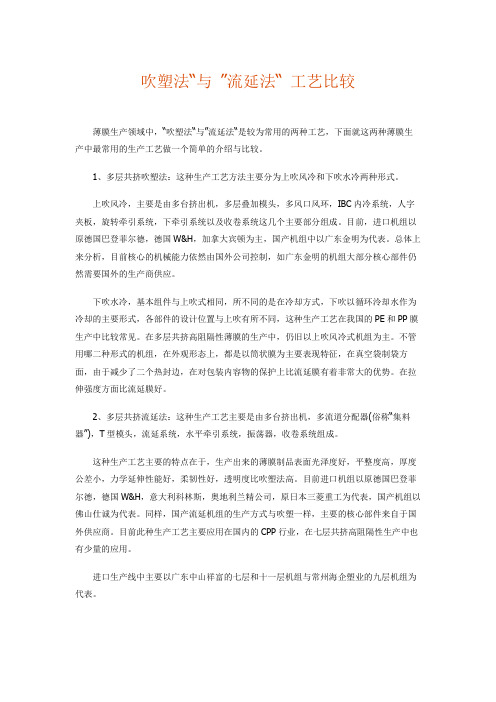
吹塑法“与”流延法“ 工艺比较薄膜生产领域中,“吹塑法“与”流延法“是较为常用的两种工艺,下面就这两种薄膜生产中最常用的生产工艺做一个简单的介绍与比较。
1、多层共挤吹塑法:这种生产工艺方法主要分为上吹风冷和下吹水冷两种形式。
上吹风冷,主要是由多台挤出机,多层叠加模头,多风口风环,IBC内冷系统,人字夹板,旋转牵引系统,下牵引系统以及收卷系统这几个主要部分组成。
目前,进口机组以原德国巴登菲尔德,德国W&H,加拿大宾顿为主,国产机组中以广东金明为代表。
总体上来分析,目前核心的机械能力依然由国外公司控制,如广东金明的机组大部分核心部件仍然需要国外的生产商供应。
下吹水冷,基本组件与上吹式相同,所不同的是在冷却方式,下吹以循环泠却水作为冷却的主要形式,各部件的设计位置与上吹有所不同,这种生产工艺在我国的PE和PP膜生产中比较常见。
在多层共挤高阻隔性薄膜的生产中,仍旧以上吹风冷式机组为主。
不管用哪二种形式的机组,在外观形态上,都是以筒状膜为主要表现特征,在真空袋制袋方面,由于减少了二个热封边,在对包装内容物的保护上比流延膜有着非常大的优势。
在拉伸强度方面比流延膜好。
2、多层共挤流延法:这种生产工艺主要是由多台挤出机,多流道分配器(俗称“集料器”),T型模头,流延系统,水平牵引系统,振荡器,收卷系统组成。
这种生产工艺主要的特点在于,生产出来的薄膜制品表面光泽度好,平整度高,厚度公差小,力学延伸性能好,柔韧性好,透明度比吹塑法高。
目前进口机组以原德国巴登菲尔德,德国W&H,意大利科林斯,奥地利兰精公司,原日本三菱重工为代表,国产机组以佛山仕诚为代表。
同样,国产流延机组的生产方式与吹塑一样,主要的核心部件来自于国外供应商。
目前此种生产工艺主要应用在国内的CPP行业,在七层共挤高阻隔性生产中也有少量的应用。
进口生产线中主要以广东中山祥富的七层和十一层机组与常州海企塑业的九层机组为代表。
这两种生产工艺在我国是最为常见的,由于吹塑工艺在产品平整度以及透明度方面不能与流延膜相比,但是其生产的高效率,设备投入低,低材料损耗量是流延工艺无法比拟的。
- 1、下载文档前请自行甄别文档内容的完整性,平台不提供额外的编辑、内容补充、找答案等附加服务。
- 2、"仅部分预览"的文档,不可在线预览部分如存在完整性等问题,可反馈申请退款(可完整预览的文档不适用该条件!)。
- 3、如文档侵犯您的权益,请联系客服反馈,我们会尽快为您处理(人工客服工作时间:9:00-18:30)。
单风环
• 主要由进气管、风环体、风口等部分组成。只有 一个风口,冷却效果较差。迷式单风口风环多孔分流式风环
双风口风环
• 具有两个风口,冷却效果较好。
型坯机头进料速度的控制
在制坯成型过程中,型坯机头的进料速度,可通过挤出机加 料量及挤出速度印证。可以进行一项挤出量测定试验:在 挤出机与机头不连接的情况下,采用相同的工艺条件,变 换挤出机挤出速度,测定同一种材料在不同挤出机的挤出 量,并作好记录。根据测试数据的整理,可以粗略地推算: 在不同速度下,各台挤出机的挤出量;在相同速度下,各 台挤出机的挤出量之比率,以此来确定多层制品的复合结 构中,各层次壁厚比(层次比)。
膜泡内冷却控制
由膜泡测量仪(绕膜泡旋转)对膜泡的直径大小 进行测量,并把信号传送到自动控制系统2进行 放大比较,再输出信号控制比例阀3的开度,从 而控制鼓风机4的鼓风量,气体由抽气机5抽出, 同时利用进气量与排气量之差保持一定的气压实 现对膜泡的吹胀,吹胀同时又对膜泡进行冷却。 整套系统均由计算机控制,保证吹膜的稳定性与 连续性,除了全自动控制外,该系统还设有手动 调整控制方式,用于引膜初始阶段。 (如下页图所示)
轴向调节厚度
齿轮传动机构
• 采用齿轮传动机 构的驱动,来调 节部分复合熔体 层的流动大小。
轴向调节复合层熔体的流动 1,2为齿轮的传动
转动套轴向移动
• 该方法适用于管套式 共挤机头,调节内外 层流道出口间隙。调 节时,先拆去芯棒与 口模,转动套1、2使 之轴向移动,分别调 节外层与内层流道的 出口间隙与熔体流动。
储料式共挤出机头
多头型坯共挤出机头
多层型坯的控制
• 多层型坯的控制 • 型坯机头温度的控制 • 型坯机头进料速度的控制
多层型坯的控制
• 重点是保证多层型坯壁厚的控制:单层壁厚和型坯总壁厚 的控制。 • 型坯总壁厚可采用挤出单层型坯的壁厚控制方法; • 多层型坯中的各层壁厚控制: a、径向调节 b、轴向调节 c、齿轮传动机构 d、转动套轴向移动
适用于印刷或 复合的外层、防 热层、力学性能 粘合层
阻气、阻味层 粘合层 热封层
阻气层 (如 EVOH, Nylon, ...)
黏合剂
可热封层, 具有剥离性能, 摩擦性能, 阻湿
共挤出吹塑设备
• • • • 挤出机(两台以上) 机头 锁模装置 模具
• 与单层挤出吹塑成型设备相近, 主要差别在于共挤出系统及共挤出机头。
出风温度可控风环
型坯机头温度的控制
• 常用的控制型坯机头温度的方法有如下几种: • a、在每个定型组块之间,设置隔热套筒或空气隔热间隙; • b、在每个定型组块的外侧加热器与模体之间,设置特殊 铜气体,加强加热器向机头内的热输送。 • c、在型坯机头内部,设置冷冻介质循环通道,它与模体 外侧的加热器结合,使型坯机头能适应熔体温差大的不同 材料。 • 在实际生产操作时,先按基层材料的要求,设定型坯机头 的加热温度;再根据功能层和黏结层的熔体性能,进行适 当的温度调节。从型坯机头总体来说,提高型坯机头的加 热温度,有利于改善型坯各层熔体的熔接缝强度。
径向调节
• 在定型组块式共挤型 坯机头结构中,可在 各层流道出口处的圆 周上,通过机头外拧 动调节螺栓,从径向 调节各层流产间隙与 熔体流量。
轴向调节
• 在定型组块式 共挤型坯机头 结构中,可在 芯轴上对应每 层流道的出口 处,设置一个 节流环,轴向 移动芯轴,调 节每层流道出 口的间隙,来 控制各流道的 熔体流动。
• 连续式共挤出机头:连续式共挤出机头能连续挤出多层型 坯; • 储料式共挤出机头:在短时间可挤出大量熔体,适用于较 大型制品吹塑; • 多头型坯共挤出机头:机头可以一次挤出2~4只型坯,有 利于提高多层容器的产量,适于大批量、小容量、多层容 器的成型加工。
连续式共挤出型坯机头
固定式连接器型多层共挤出复合平膜模头
管套式共挤型坯机头中熔体流动的调节 1,2—转动套
薄膜厚度调整
由膜泡测量仪测厚仪测 得薄膜圆周上的厚度 分布与设定值进行比 较,如某点处薄膜厚 了,则对应模处的加 热器(见图中的加热 元件)通电使该处温 度升高一些,从而使该 处熔体粘度减少一些, 吹胀后该处薄膜的厚 度相应薄些。
薄膜厚度调整
除了在模头处安装加热 元件外,也有的在风 环出风口附近安装加 热元件(如图是出风 温度可控风环)其对 薄膜厚度的调整原理 与模头加热元件相似。 如薄膜某处厚了,对 应的加热器通电使该 处出风的温度升高些, 薄膜经吹胀拉伸后 的 厚度自然也薄些。
膜泡内冷却控制图
共挤出吹塑薄膜生产线的冷却
• 冷却风环 风环以风机送出的压力空气为冷却介质,对膜泡吹胀(即口 模到冷凝线之间)进行冷却,当冷却空气通过风环以一定 角度和速度吹向从机头挤出的膜泡时,高温的膜泡与冷却 空气相接触,膜泡上大量的热量传递给空气并被带走,使 膜泡得到冷却。 冷却风环先后从单风环、双风环到自然风环不断改进与完善。
多层薄膜生产工艺
• 共挤出优点 • 生产工艺设备 • 生产工艺控制
多层共挤的优点
•多层共挤膜可同时拥有多种包装物理性能
•阻隔性能 •高强度 •热封性能好 •降低费用 •降低昂贵树脂的用量 •尽量使用价格便宜的树脂的用量
多层共挤的优点
多层共挤可以将不同的树脂所拥有的不同性能一次性地柔和在一起,从而能很 好地满足对包装薄膜日益增加的要求。例如:
• 塑料原料1→挤出1→共挤出模头→冷却→牵引
挤出机2 塑料原料2 复 合 薄 膜 成 品 收 卷
以两层共挤出复合为例的共挤出工艺过程
挤出系统
• 挤出机、输料管 • 在共挤出时,挤出机必须同时向机头输送几股相同或不同 材料的熔融料流 • 挤出系统最重要的是保证每层熔体流的稳定性和均匀性
共挤出机头
吹膜机结构
加紧辊
人字架
N ip R o lls C o lla p s e d Tube
筒膜
C o lla p s in g F r a m e
剖刀 膜泡
S lit te r s B u b b le
冷冻线 挤出机
F ro s t L in e
收卷
W in d e r
膜头 D i e
E x tru d e rs
表面构造 / 可印刷性 / 黏合剂 坚强, 不透光性, 韧性, 黏性 热封性, 剥离性, 摩擦性
• 用少量昂贵的树脂取得必要的物理性能。 • 黏合剂可根据需要置于合适的层上。
适用于印刷或 复合的外层
中心层
热封层
五层共挤阻隔薄膜
阻气、阻湿的组合
可印刷性 / 黏合剂 , 耐热, 耐摩擦、阻湿、挺性 黏合剂