6铸造工艺基础
铸造工艺基础知识及理论

铸造工艺基础知识及理论目录一、基础概念 (2)1.1 铸造的定义与意义 (3)1.2 铸造工艺的种类与应用 (4)二、铸造材料 (6)三、铸造设备 (7)3.1 熔炼设备 (9)3.2 锻造设备 (10)3.3 后处理设备 (11)四、铸造工艺过程 (12)五、铸造工艺设计 (13)5.1 工艺方案的确定 (15)5.2 工艺参数的选择 (16)5.3 工艺文件的编制 (18)六、铸造质量与控制 (20)6.1 铸造缺陷的产生原因及防止措施 (22)6.2 铸造质量检测方法与标准 (23)七、铸造生产与环境 (24)7.1 铸造生产的环保要求 (26)7.2 环保设备的应用与管理 (27)八、现代铸造技术的发展趋势 (28)8.1 快速凝固与近净形铸造技术 (30)8.2 数字化与智能化铸造技术 (31)8.3 生物铸造与绿色铸造技术 (33)一、基础概念铸造工艺是指将熔炼好的液态金属浇入铸型,待其凝固后获得所需形状和性能的金属制品的过程。
它是制造业中非常重要的工艺之一,广泛应用于汽车、航空、建筑、电子等领域。
铸造工艺的基础知识主要包括液态金属的性质、铸型(即模具)的设计与制造、浇注系统、凝固过程以及后处理等。
这些知识是理解和掌握铸造工艺的基本前提。
液态金属的性质:液态金属在铸造过程中的流动性、填充能力、冷却速度等对其最终的产品质量有着决定性的影响。
了解液态金属的成分、温度、粘度等基本性质对于铸造工艺的设计和实践都是非常重要的。
铸型的设计与制造:铸型是形成金属制品形状和内部结构的重要工具。
铸型的设计需要考虑到金属液的流动性和凝固特性,以及制品的精度和表面质量要求。
铸型的制造也需要选用合适的材料,并经过精密加工才能达到设计要求。
浇注系统:浇注系统是连接铸型和液态金属的通道,包括浇口杯、直浇道、横浇道和内浇道等部分。
合理的浇注系统设计可以确保金属液均匀地注入铸型,并有利于热量和气体的排出,从而提高制品的质量和生产效率。
铸造工艺基础

• a 结晶温度范围(钢、可铁、铸铝易产生) • b 合金中的S形成低熔点共晶体。 • c 铸型的退让性。(采用有机粘结剂、加锯末等)。
② 冷裂 • 特征:直、细、连续、表面干净。 • 产生:在弹性阶段→内应力→裂纹。 • 影响因素。
• c 钢铁中的含磷量。钢>0.1%,铸铁>0.5%。
铸件以糊状凝固方式凝固或在缩孔下方
• 特点
细小、分散,表面氧化。
• 对铸件质量的影响:渗漏、物理化学性能下降
2 缩孔和缩松的防止 ① 缩孔的防止 顺序凝固的原则:在铸件上可能出现缩孔的厚大部位安放
冒口等措施,使铸件上远离冒口的部位先凝固,尔后是靠 近冒口的部位凝固,最后才是冒口凝固,铸件上最后凝固 部位的收缩由冒口补充。 实现顺序凝固的工艺措施:冒口、冷铁、补贴等。
80
60
40
20
0
Pb
20
40
60
80 Sb
② 浇注条件
② 浇注温度 ② 充型压力 ② 浇注系统
③ 铸型的充填条件
③ 铸型材料 ③ 铸型温度 ③ 铸型中的气体
④ 铸件结构
9.2 铸件的凝固与收缩特性 9.2.1 铸件的凝固方式 • 铸件凝固断面上的三个区域:固相区、凝固区、液相区。
• 凝固方式的划分原则:按凝固区的宽窄。 • 三种凝固方式
• a 逐层凝固 • b 糊状凝固 • c 中间凝固
• 影响凝固方式的因素
• a 合金的凝固温度范围 • b 铸件断面的温度梯度
凝固方式对铸件质量的影响: - 充型、补缩
9.2.2 铸造合金的收缩
• 收缩: • 收缩的三个阶段:
• a 液态收缩 • b 凝固收缩 • c 固态收缩
铸造工艺基础教学培训PPT

二、铸造成形基础
逐层凝固:液固金属间轮廓线清 晰。4.3%的铁碳合金,结晶在恒 温下进行,结晶过程有表及里,逐 层推进,凝固层的内表面比较光滑, 对尚未凝固合金流动阻力小,有利 于合金的充型,所以流动性好。 糊状凝固:先结晶的固态金属广泛 分布在没有结晶的液态金属中,液 固金属间没有明显的轮廓线。
二、铸造成形基础
• 2.合金的收缩
(4)铸造内应力、变形和裂纹
◆ 消除或减小铸造内应力的方法: ① 采用同时凝固的原则,通过设置冷铁、布置浇 冒口位置等工艺措施,使铸件各部分在凝固过程中 温差尽可能小;(不管壁厚如何,同时一起收缩, 可避免热应力的产生) ② 提高铸型温度,使整个铸件缓冷,以减小铸型 各部分温差; ③ 改善铸型与铸芯的退让性; ④ 进行去应力退火,这是消除铸造应力最彻底的 方法。
二、铸造成形基础
• 2.合金的收缩
(4)铸造内应力、变形和裂纹
◆ 变形: 当铸件中的内应力若超过合金的屈服强度,将使铸件产生变形。为防止变形,在铸件设计
时,应力求壁厚均匀、形状简单而对称。 ◆ 变形:
当铸件的内应力超过合金的抗拉强度时,铸件便会产生裂纹。裂纹是铸件严重的缺陷。 防止裂纹的主要措施: 合理的设计铸件结构;合理选用型砂和芯砂的粘结剂与添加剂,以改善其退让性;大的型 芯可制成中空的或内部填以焦炭;严格限制钢与铸铁中的硫含量;选用收缩量小的合金。
二、铸造成形基础
• 2.合金的收缩
• (2)缩松:液态合金在凝固过程中,若凝固时的收缩得不到及时补充,就会形成缩
孔,若缩孔是分散的,即为缩松。
又称分散缩孔) 形状:宏观缩松—肉眼可见的微小孔洞;
铸造工艺基础

铸造工艺基础
1.3 铸造应力、变形和裂纹
热应力形成过程示意图
铸造工艺基础
1.3 铸造应力、变形和裂纹
1)热裂 热裂的形状特征是裂纹短,缝隙 宽,形状曲折,缝内呈氧化色。热裂 是铸钢和铝合金铸件的常见缺陷。
14
铸造工艺基础
1.3 铸造应力、变形和裂纹
2)冷裂 铸件所产生的热应力和收缩应力 的总和,若,大于该温度下合金的强 度,则产生冷裂。
铸造工艺基础
1.3 铸造应力、变形和裂纹
收缩应力是由于铸件在固态收缩时受 到铸型和型芯的阻碍而产生的。
铸造工艺基础
1.3 铸造应力、变形和裂纹
铸件产生收缩应力示意图
铸造工艺基础
1.3 铸造应力、变形和裂纹
热应力是由于铸件各部分壁厚不同、冷却 速度不同、固态收缩不一致而产生的。
预防热应力、减小铸件变形的基本途径是 尽量减小铸件各部分的温度差,使得其均匀冷 却。
1.1 液态合金的充型
铸造工艺基础
流动性是熔融金属的流动能力,它是影响充型 能力的主要因素之一。流动性仅与金属本身的化学 成分、温度、杂质含量以及物理性质有关,其中以 化学成分的影响最为显著。它是熔融金属本身固有 的属性。
液态金属充满铸型的能力即为:充型能力。充 型能力是考虑铸型及工艺因素影响的熔融金属流动 性。
1.2 铸件的收缩
铸造工艺基础
(1)
化学成分
(2)
浇注温度
(3)
铸件结构与铸 型条件
1.2 铸件的收缩
铸造工艺基础
1)缩孔的形成
圆柱体铸件Байду номын сангаас缩孔形成示意图
铸造工艺基础
1.2 铸件的收缩
2)缩松的形成
圆柱体铸件中缩松形成示意图
6铸造工艺基础.pptx

铸件的凝固过程:
在铸件的凝固过程中, 其截面一般存在三个区 域,即液相区、凝固区、 固相区。对铸件质量影 响较大的主要是液相和 固相并存的凝固区的宽 窄。铸件的凝固方式就 是依据凝固区的宽窄来 划分的。
凝固方式有:
2.1 铸造工艺基础
什么是金属的液态成形:
即将液态金属浇入与零件形状相适应的铸型空腔中,待其冷却凝固, 以获得毛坯或零件的工艺方法,亦称铸造.
金属的液态成形的作用:
金属的液态成形是制造毛坯、零件的重要方法之一。按铸型材料的 不同,金属液态成形可分为砂型铸造和特种铸造(包括压力铸造、金属型 铸造等).其中砂型铸造是最基本的液态成形方法,所生产的铸件要占铸 件总量的80%以上.
合金的收缩
合金的收缩的过程:
合金从液态冷却至室温的过程中,其体积或尺寸缩减的 现象。合金的收缩给液态成形工艺带来许多困难,会造成许 多铸造缺陷。(如:缩孔、缩松、裂纹、变形等)。
合金收缩的三个阶段
缩孔与缩松的形成
液态合金在冷凝过程中,若其液态收缩和凝固收缩所减少的体积得不到有效补 充,则铸件最后凝固的部位形成空洞,按空洞大小、分布,可分为缩孔和缩松。
缩孔与缩松的形成演示
判断缩孔出现的方法
A等温线法
B内截圆法
消除缩孔和缩松的方法
原理
定向凝固原则
是铸件让远离冒口的地方先凝 固,靠近冒口的地方次凝固, 最后才是冒口本身凝固。实现 以厚补薄,将缩孔转移到冒口 中去。
方法
合理布置内浇道及确定浇铸工艺。 合理应用冒口、冷铁和补贴等工艺措施。
解决缩孔的方法演示: 冒口和冷铁
缩孔的形成: 纯金属、共晶成分和凝固温度范围窄的合金,浇注后在型腔内是由表
铸造工艺基础(1)
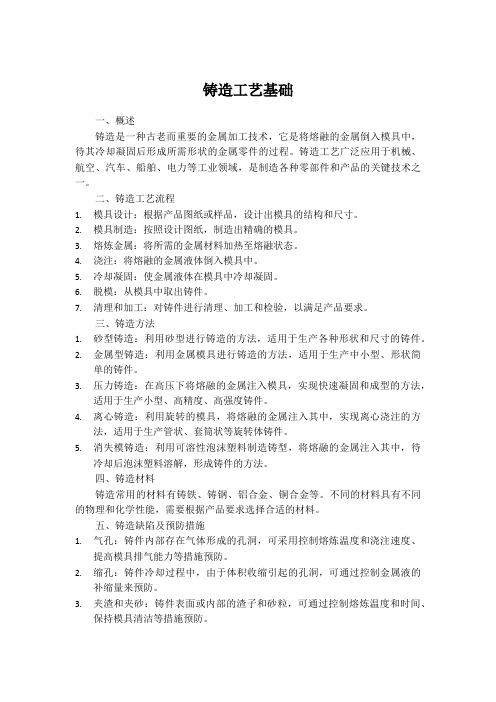
铸造工艺基础一、概述铸造是一种古老而重要的金属加工技术,它是将熔融的金属倒入模具中,待其冷却凝固后形成所需形状的金属零件的过程。
铸造工艺广泛应用于机械、航空、汽车、船舶、电力等工业领域,是制造各种零部件和产品的关键技术之一。
二、铸造工艺流程1.模具设计:根据产品图纸或样品,设计出模具的结构和尺寸。
2.模具制造:按照设计图纸,制造出精确的模具。
3.熔炼金属:将所需的金属材料加热至熔融状态。
4.浇注:将熔融的金属液体倒入模具中。
5.冷却凝固:使金属液体在模具中冷却凝固。
6.脱模:从模具中取出铸件。
7.清理和加工:对铸件进行清理、加工和检验,以满足产品要求。
三、铸造方法1.砂型铸造:利用砂型进行铸造的方法,适用于生产各种形状和尺寸的铸件。
2.金属型铸造:利用金属模具进行铸造的方法,适用于生产中小型、形状简单的铸件。
3.压力铸造:在高压下将熔融的金属注入模具,实现快速凝固和成型的方法,适用于生产小型、高精度、高强度铸件。
4.离心铸造:利用旋转的模具,将熔融的金属注入其中,实现离心浇注的方法,适用于生产管状、套筒状等旋转体铸件。
5.消失模铸造:利用可溶性泡沫塑料制造铸型,将熔融的金属注入其中,待冷却后泡沫塑料溶解,形成铸件的方法。
四、铸造材料铸造常用的材料有铸铁、铸钢、铝合金、铜合金等。
不同的材料具有不同的物理和化学性能,需要根据产品要求选择合适的材料。
五、铸造缺陷及预防措施1.气孔:铸件内部存在气体形成的孔洞,可采用控制熔炼温度和浇注速度、提高模具排气能力等措施预防。
2.缩孔:铸件冷却过程中,由于体积收缩引起的孔洞,可通过控制金属液的补缩量来预防。
3.夹渣和夹砂:铸件表面或内部的渣子和砂粒,可通过控制熔炼温度和时间、保持模具清洁等措施预防。
4.裂纹:铸件冷却过程中产生的裂纹,可通过优化模具设计和制造工艺、控制铸件壁厚等措施预防。
5.组织疏松:铸件内部组织不紧密,可通过控制熔炼温度和浇注温度等措施预防。
《铸造工艺基础》PPT课件
上一页 下一页 后 退 退 出
19
ppt课件
三、影响充型能力的因素
1.合金性质——合金流动性:决定于合金种类 与化学成分。
合金种类
根据“螺旋型试样长度”实验: 灰铸铁和硅黄铜的流动性和充型能力最好; 铝硅合金其次; 铸钢最差。
上一页 下一页 后 退 退 出
21
ppt课件
化学成分
同一种合金,化学成分不同,合金流动性也有不同。 因为化学成分不同,合金的结晶温度范围和结晶特性 不同。
❖ 根 据 生 产 经 验 , 常 用 铸 造 合 金 的 浇 注 温 度 为 : 铸 铁 1230 ~ 1450C;铸钢1520~1620C;铝合金680~780C。对薄壁及复 杂铸件取浇注温度的上限,对于厚大铸件可以取其下限。
上一页 下一页 后 退 退 出
23
ppt课件
充型压力
❖ 浇注时,金属所受的充型压力越大,充型能力就越 强。
❖ 非共晶成分的合金的结晶过程是在一定的温度范围之内进行, 凝固时铸件存在两相区,其中既有没有凝固的液态金属,还有 已经凝固的小的树枝状结晶体,称为糊状凝固,树枝状的小晶 体和粗糙不平的凝固层的内表面使得液态金属的流动阻力增大, 因此这种合金的流动性较差。合金的结晶范围越宽,则两相区 越宽,合金的流动性也就越差。
合金种类
根据“螺旋型试样长度”实验: 灰铸铁和硅黄铜的流动性和充型能力最好; 铝硅合金其次; 铸钢最差。
上一页 下一页 后 退 退 出
18
ppt课件
化学成分
同一种合金,化学成分不同,合金流动性也有不同。 因为化学成分不同,合金的结晶温度范围和结晶特性 不同。
❖ 纯金属和共晶成分的合金,结晶是在恒温之下进行,此时金属 液的凝固是从金属件的表面开始向中心逐层推进,称为逐层凝 固,凝固层的内表面比较平滑,对还没有凝固的液态金属阻力 较小,合金的流动性较好;
铸造工艺基础资料
铸造工艺基础资料§1 液态合金的充型充型: 液态合金填充铸型的过程.充型能力: 液态合金充满铸型型腔,获得形状完整,轮廓清晰的铸件的能力充型能力不足:易产生: 浇不足: 不能得到完整的零件.冷隔:没完整融合缝隙或凹坑, 机械性能下降.一合金的流淌性液态金属本身的流淌性----合金流淌性1 流淌性对铸件质量阻碍1) 流淌性好,易于浇出轮廓清晰,薄而复杂的铸件.2) 流淌性好,有利于液态金属中的非金属夹杂物和气体上浮,排除.3) 流淌性好,易于对液态金属在凝固中产生的收缩进行补缩.2 测定流淌性的方法:以螺旋形试件的长度来测定: 如灰口铁:浇铸温度1300℃试件长1800mm.铸钢: 1600℃100mm3 阻碍流淌性的因素要紧是化学成分:1) 纯金属流淌性好:一定温度下结晶,凝固层表面平滑,对液流阻力小2) 共晶成分流淌性好:恒温凝固,固体层表面光滑,且熔点低,过热度大.3) 非共晶成分流淌性差: 结晶在一定温度范畴内进行,初生数枝状晶阻碍液流二浇注条件1 浇注温度: t↑ 合金粘度下降,过热度高. 合金在铸件中保持流淌的时刻长,∴t↑ 提高充型能力. 但过高,易产生缩孔,粘砂,气孔等,故不宜过高2 充型压力: 液态合金在流淌方向上所受的压力↑ 充型能力↑如砂形铸造---直浇道,静压力. 压力铸造,离心铸造等充型压力高.三铸型条件1 铸型结构: 若不合理,如壁厚小, 直浇口低, 浇口小等充↓2 铸型导热能力: 导热↑ 金属降温快,充↓如金属型3 铸型温度: t↑ 充↑如金属型预热4 铸型中气体: 排气能力↑ 充↑ 减少气体来源,提高透气性, 少量气体在铸型与金属液之间形成一层气膜,减少流淌阻力,有利于充型.§2 铸件的凝固和收缩铸件的凝固过程假如没有合理的操纵,铸件易产生缩孔,缩松一铸件的凝固1 凝固方式:铸件凝固过程中,其断面上一样分为三个区: 1—固相区2—凝固区3—液相区对凝固区阻碍较大的是凝固区的宽窄,依此划分凝固方式.1) 逐层凝固:纯金属,共晶成分合金在凝固过程中没有凝固区,断面液,固两相由一条界限清晰分开,随温度下降,固相层不断增加,液相层不断减少,直达中心.2) 糊状凝固合金结晶温度范畴专门宽,在凝固某段时刻内,铸件表面不存在固体层,凝固区贯穿整个断面,先糊状,后固化.故---3) 中间凝固大多数合金的凝固介于逐层凝固和糊状凝固之间.2 阻碍铸件凝固方式的因素1) 合金的结晶温度范畴范畴小: 凝固区窄,愈倾向于逐层凝固如: 砂型铸造, 低碳钢逐层凝固, 高碳钢糊状凝固2) 铸件的温度梯度合金结晶温度范畴一定时,凝固区宽度取决于铸件内外层的温度梯度.温度梯度愈小,凝固区愈宽.(内外温差大,冷却快,凝固区窄)二合金的收缩液态合金从浇注温度至凝固冷却到室温的过程中,体积和尺寸减少的现象---.是铸件许多缺陷(缩孔,缩松,裂纹,变形,残余应力)产生的差不多缘故.1 收缩的几个时期1) 液态收缩: 从金属液浇入铸型到开始凝固之前. 液态收缩减少的体积与浇注温度质开始凝固的温度的温差成正比.2) 凝固收缩: 从凝固开始到凝固完毕. 同一类合金,凝固温度范畴大者,凝固体积收缩率大.如: 35钢,体积收缩率3.0%, 45钢4.3%3) 固态收缩: 凝固以后到常温. 固态收缩阻碍铸件尺寸,故用线收缩表示.2 阻碍收缩的因素1) 化学成分: 铸铁中促进石墨形成的元素增加,收缩减少. 如: 灰口铁C, Si↑,收↓,S↑ 收↑.因石墨比容大,体积膨胀,抵销部分凝固收缩.2) 浇注温度: 温度↑ 液态收缩↑3) 铸件结构与铸型条件铸件在铸型中收缩会受铸型和型芯的阻碍.实际收缩小于自由收缩.∴铸型要有好的退让性.3 缩孔形成在铸件最后凝固的地点显现一些空泛,集中—缩孔. 纯金属,共晶成分易产生缩孔*产生缩孔的差不多缘故: 铸件在凝固冷却期间,金属的液态及凝固受缩之和远远大于固态收缩.4 阻碍缩孔容积的因素(补充)1) 液态收缩,凝固收缩↑ 缩孔容积↑2) 凝固期间,固态收缩↑,缩孔容积↓3) 浇注速度↓缩孔容积↓4) 浇注速度↑液态收缩↑ 易产生缩孔5 缩松的形成由于铸件最后凝固区域的收缩未能得到补足,或者,因合金呈糊状凝固,被树枝状晶体分隔开的小液体区难以得到补缩所至.1) 宏观缩松肉眼可见,往往显现在缩孔邻近,或铸件截面的中心.非共晶成分,结晶范畴愈宽,愈易形成缩松.2) 微观缩松凝固过程中,晶粒之间形成微小孔洞---凝固区,先形成的枝晶把金属液分割成许多微小孤立部分,冷凝时收缩,形成晶间微小孔洞. 凝固区愈宽,愈易形成微观缩松,对铸件危害不大,故不列为缺陷,但对气密性,机械性能等要求较高的铸件,则必须设法减少.(先凝固的收缩比后凝固的小,因后凝固的有液,凝,固三个收缩,先凝固的有凝,固二个收缩区----这也是形成微观缩松的差不多缘故.与缩孔形成差不多缘故类似)6 缩孔,缩松的防止方法差不多原则: 制定合理工艺—补缩, 缩松转化成缩孔.顺序凝固: 冒口—补缩同时凝固: 冷铁—厚处. 减小热应力,但心部缩松,故用于收缩小的合金.l 安置冒口,实行顺序凝固,可有效的防止缩孔,但冒口白费金属,白费工时,是铸件成本增加.而且,铸件内应力加大,易于产生变形和裂纹.∴要紧用于凝固收缩大,结晶间隔小的合金.l 非共晶成分合金,先结晶树枝晶,阻碍金属流淌,冒口作用甚小.l 关于结晶温度范畴甚宽的合金,由于倾向于糊状凝固,结晶开始之后,发达的树枝状骨状布满整个截面,使冒口补缩道路受阻,因而难幸免显微缩松的产生.明显,选用近共晶成分和结晶范畴较窄的合金生产铸件是适宜的.§3 铸造内应力,变形和裂纹凝固之后的连续冷却过程中,其固态收缩若受到阻碍,铸件内部就发生内应力,内应力是铸件产生变形和裂纹的差不多缘故.(有时相变膨胀受阻,负收缩)一内应力形成1 热应力: 铸件厚度不均,冷速不同,收缩不一致产生.塑性状态: 金属在高于再结晶温度以上的固态冷却时期,受力变形,产生加工硬化,同时发生的再结晶降硬化抵消,内应力自行消逝.(简单说,处于屈服状态,受力—变形无应力)弹性状态: 低于再结晶温度,外力作用下,金属发生弹性变形,变形后应力连续存在.举例: a) 凝固开始,粗细处都为塑性状态,无内应力∵两杆冷速不同,细杆快,收缩大,∵受粗杆限制,不能自由收缩,相对被拉长,粗杆相对被压缩,结果两杆等量收缩.b) 细杆冷速大,先进如弹性时期,而粗杆仍为塑性时期,随细杆收缩发生塑性收缩,无应力.c) 细杆收缩先停止,粗杆连续收缩,压迫细杆,而细杆又阻止粗杆的收缩,至室温, 粗杆受拉应力(+),(-)由此可见,各部分的温差越大,热应力也越大,冷却较慢的部分形成拉应力,冷却较快的部分形成压应力.预防方法: 1 壁厚平均2 同时凝固—薄处设浇口,厚处放冷铁优点: 省冒口,省工,省料缺点: 心部易显现缩孔或缩松,应用于灰铁锡青铜,因灰铁缩孔、缩松倾向小,锡青铜糊状凝固,用顺序凝固也难以有效地排除其显微缩松。
铸造工艺基础知识
铸造1.铸造是人类掌握比较早的一种金属热加工工艺,已有约6000年的历史。
铸造是将液体金属浇铸到与零件形状相适应的铸造空腔中,待其冷却凝固后,以获得零件或毛坯的方法。
[1]被铸物质多为原为固态但加热至液态的金属(例:铜、铁、铝、锡、铅等),而铸模的材料可以是砂、金属甚至陶瓷。
因应不同要求,使用的方法也会有所不同。
中国商朝的重875公斤的司母戊方鼎,战国时期的曾侯乙尊盘,西汉的透光镜,都是古代铸造的代表产品。
早期的铸件大多是农业生产、宗教、生活等方面的工具或用具,艺术色彩浓厚。
那时的铸造工艺是与制陶工艺并行发展的,受陶器的影响很大。
中国在公元前513年,铸出了世界上最早见于文字记载的铸铁件-晋国铸型鼎,重约270公斤。
2.铸造定义是:熔炼金属,制造铸型,并将熔融金属浇入铸型,凝固后获得具有一定形状、尺寸和性能金属零件毛坯的成型方法,铸造是将金属熔炼成符合一定要求的液体并浇进铸型里,经冷却凝固、清整处理后得到有预定形状、尺寸和性能的铸件的工艺过程。
铸造毛坯因近乎成形,而达到免机械加工或少量加工的目的降低了成本并在一定程度上减少了制作时间.3.铸造主要有砂型铸造和特种铸造2大类。
1) 普通砂型铸造,利用砂作为铸模材料,又称砂铸,翻砂,包括湿砂型、干砂型和化学硬化砂型3类,但并非所有砂均可用以铸造。
好处是成本较低,因为铸模所使用的沙可重复使用;缺点是铸模制作耗时,铸模本身不能被重复使用,须破坏后才能取得成品。
砂型(芯)铸造方法:湿型砂型、树脂自硬砂型、水玻璃砂型、干型和表干型、实型铸造、负压造型。
砂芯制造方法:是根据砂芯尺寸、形状、生产批量及具体生产条件进行选择的。
在生产中,从总体上可分为手工制芯和机器制芯。
2) 特种铸造,按造型材料又可分为以天然矿产砂石为主要造型材料的特种铸造(如熔模铸造、泥型铸造、壳型铸造、负压铸造、实型铸造、陶瓷型铸造等)和以金属为主要铸型材料的特种铸造(如金属型铸造、压力铸造、连续铸造、低压铸造、离心铸造等)两类。
铸造工艺基础
熔剂主要是石灰石(CaCO3), 必要时也可加入氟石(CaF2 )。
19
⒉ 电炉
冶炼设备:电弧炉、平炉和感应电炉等。
电弧炉用得最多,平炉仅用于重型铸钢件,感应电炉主要用于合金钢中、小型 铸件的生产。
A、电弧炉炼钢
利用电极与金属炉料间电弧 产生的热量来熔炼金属,如 图所示。炉子容量从 1 ~ 15吨。钢液质量较高,熔 炼速度快,一般为2 ~ 3 小时一炉,温度容易控制。 炼钢的金属材料主要是废钢、 生铁和铁合金等。其它材料 有造渣材料、氧化剂、还原 剂和增碳剂等。
铸造生产中常用的金属液有:铸铁、铸钢、铸造非 铁合金。
16
1、 铸铁的熔炼
铸造生产中用量最多的合金:铸铁
熔炼铸铁的炉子有:冲天炉、电炉
一般情况: 灰铁一般采用冲天炉熔炼 球墨铸铁一般采用电炉熔炼。为了提高熔炼速度,采用
冲天炉熔炼,倒入电炉进行孕育处理。
冲天炉的大小是以每小时熔化金属液的多少来定的,一 般厂家都用每小时熔化1.5~10t金属液的冲天炉。
7
二: 型(芯)砂的分类
(1) 按粘结剂的不同可分为、粘土砂、 水玻璃砂和树脂砂等。
1. 粘土砂:适用于机器造型型腔 2. 覆模砂:适用于做型芯 3. 树脂砂:适用于手工造型型腔
8
黏土 砂 覆 模 砂
黏土砂、覆模砂
树脂砂
9
三、砂型铸造
(一)砂型铸造简介
砂型铸造是最常用的造型方法,砂型铸造 按造型方法的不同可分为手工造型和机器造型 两大类。
致密的健全铸件,必须对收缩加以控制。
合金的收缩量通常用体收缩率或线收缩率来表示。
金
属从浇注温度冷却到室温要经历三个互相联系的收缩阶段:
- 1、下载文档前请自行甄别文档内容的完整性,平台不提供额外的编辑、内容补充、找答案等附加服务。
- 2、"仅部分预览"的文档,不可在线预览部分如存在完整性等问题,可反馈申请退款(可完整预览的文档不适用该条件!)。
- 3、如文档侵犯您的权益,请联系客服反馈,我们会尽快为您处理(人工客服工作时间:9:00-18:30)。
铸型充填条件对充型能力的影响
铸型蓄热系数: 即从金属中吸取热量
并储存的能力
铸型温度(不能过高)
铸型的发气和 透气能力:
浇铸时产生气体 能在金属液与铸型间形成气膜,
减小摩擦阻力,有利于充型。 但发气能力过强,透气能力又差时,
若浇铸速度太快, 则型腔中的气体压力增大,
铸件在固态收缩时,因受到铸型、型 芯、浇冒口、砂箱等外力阻碍而产生 的应力。
变形
残余热应力的存在,使铸件处在一种非稳定 状态,将自发地通过铸件的变形来缓解其应 力,以回到稳定的平衡状态。
裂纹
当热应力大到一定程度会导致出现裂纹。
热应力的消除方法
铸件的结构:
铸件的结构尽可能对称 铸件的壁厚尽可能均匀
工艺方面:采用同时凝固原则
逐层凝固,糊状凝固, 中间凝固.
影响凝固的主要因素
*合金的结晶温度范围: 合金的结晶温度范围越小,凝固区域越
窄,越趋向于逐层凝固。在铁碳合金中普通 灰铸铁为逐层凝固,高碳钢为糊状凝固。 *铸件的温度梯度:
在合金结晶温度范围已定的前提下,凝 固区的宽窄取决于铸件内外层之间的温度差。 若铸件内外层之间的温度差由小变大,则其 凝固区相应由宽变窄。
金属液在冷凝过程中,其液态收缩和凝固过程若得不到有效补充,铸件将 产生缩孔或松动缺陷。
铸件的凝固过程:
在铸件的凝固过程中, 其截面一般存在三个区 域,即液相区、凝固区、 固相区。对铸件质量影 响较大的主要是液相和 固相并存的凝固区的宽 窄。铸件的凝固方式就 是依据凝固区的宽窄来 划分的。
凝固方式有:
浇不足缺陷
气孔缺陷
夹砂缺陷
合金的充型能力
合金的流动性愈好,冲型能力愈强,愈便于浇铸出轮廓清晰、薄而复杂的 铸件。同时有利于非金属夹杂物和气体的上浮和排除。
测试合金充型能 力的方法:
如右图,将合金 液浇入铸型中,冷 凝后测出充满型腔 的式样长度。浇出 的试样越长,合金 的流动性越好,合金 充型能力越好.
3液态成形内应力、变形与裂纹
铸件在凝固之后的继续冷却过程中,其固态收缩若受到阻碍,铸件内部将产生
内应力,这些内应力有时是在冷却过程中暂存的,有时一直保持到室温,成为残余 应力,其是铸件产生变形的基本原因。
内应力
热应力 机械应力
铸件在凝固和冷却的过程中,由于铸件 的壁厚不均匀,导致不同部位不均衡的 收缩而引起的应力。
充型能力减弱。
铸件结构对充型能力的影响
折算厚度:
复杂程度:
折算厚度也叫当量厚度 或模数,是铸件体积与铸件 表面积之比。折算厚度越大, 热量散失越慢,充型能力就 越好。铸件壁厚相同时,垂 直壁比水平壁更容易充 填.(大平面铸件不易成形)
铸件结构越复杂,流 动阻力就越大,铸型的 充填就越困难。
2铸件的凝固与收缩
液态成形零件内部组织的均匀性、 致密性一般较差
液态成形零件易出现缩孔、缩松、 气孔、砂眼、夹渣、夹砂、裂纹等 缺陷,产品 质量不够稳定
由于铸件内部晶粒粗大,组织不均 匀,且常伴 有缺陷,其力学性能 比同类材料的塑性成形低
液态合金的工艺性能
液态合金的工艺性能表征为液态合金的 铸造性能:指合金在铸造成形时获得外形准确、内 部健全铸件的能力。
合金的收缩
合金的收缩的过程:
合金从液态冷却至室温的过程中,其体积或尺寸缩减的 现象。合金的收缩给液态成形工艺带来许多困难,会造成许 多铸造缺陷。(如:缩孔、缩松、裂纹、变形等)。
合金收缩的三个阶段
缩孔与缩松的形成
液态合金在冷凝过程中,若其液态收缩和凝固收缩所减少的体积得不到有效补 充,则铸件最后凝固的部位形成空洞,按空洞大小、分布,可分为缩孔和缩松。
砂型铸造过程
液态成型的特点
液态成型 优点
适于做复杂外形,特别是 复杂内腔的毛坯
对材料的适应性广,铸件 的大小 几乎不受限制
成本低,原材料来源广泛, 价格低廉,一般不需要昂 贵的设备
是某些塑性很差的材料 (如铸铁等)制造其毛坯或 零件的唯一成型工艺
液态成型的特点
液态成型 缺点
工艺过程比较复杂,一些工艺 过程还难以控制
通常是指合金的流动性、收缩性 吸气性及偏析等性能
合金铸造性能是选择铸造金属材料,确定铸件的 铸造工艺方案及进行铸件结构设计的依据
1合金的充型能力
充型能力的概念: 液态金属充满铸型型腔,获得尺寸精确、轮廓清晰 的成型件的能力
充型能力不足
浇不足
冷隔
夹砂
气孔
夹渣
充型能力的决定因数
合金的流动性 铸型性质 浇注条件 铸件结构等
几种不同合金流动性的比较
比较下面几种合金流动性能 *铸钢的流动性
*铸铁的流动性
实验证明铸铁的流动性好,铸钢的流动性差。
浇注条件度越高,液态金属的粘度越小, 过热度高,金属液内含热 量多,保持 液态的时间长,充型 能力强。
充型压力 浇注系统
液态金属在流动方向上所受的压力称为 充型压力。充型压力越大, 充型能力越 强。
2.1 铸造工艺基础
什么是金属的液态成形:
即将液态金属浇入与零件形状相适应的铸型空腔中,待其冷却凝固, 以获得毛坯或零件的工艺方法,亦称铸造.
金属的液态成形的作用:
金属的液态成形是制造毛坯、零件的重要方法之一。按铸型材料的 不同,金属液态成形可分为砂型铸造和特种铸造(包括压力铸造、金属型 铸造等).其中砂型铸造是最基本的液态成形方法,所生产的铸件要占铸 件总量的80%以上.
缩孔与缩松的形成演示
判断缩孔出现的方法
A等温线法
B内截圆法
消除缩孔和缩松的方法
原理
定向凝固原则
是铸件让远离冒口的地方先凝 固,靠近冒口的地方次凝固, 最后才是冒口本身凝固。实现 以厚补薄,将缩孔转移到冒口 中去。
方法
合理布置内浇道及确定浇铸工艺。 合理应用冒口、冷铁和补贴等工艺措施。
解决缩孔的方法演示: 冒口和冷铁
缩孔的形成: 纯金属、共晶成分和凝固温度范围窄的合金,浇注后在型腔内是由表
及里的逐层凝固。在凝固过程中,如得不到合金液的补充,在铸件最后 凝固的地方就会产生缩孔.
缩松的形成原因:
铸件最后凝固的收缩未能得到补足,或者结晶 温度范围宽的合金呈糊状凝固,凝固区域较宽,液、 固两相共存,树枝晶发达,枝晶骨架将合金液分割 开的小液体区难以得到补缩所致。
时效处理:人工时效;自然时效
铸件的变形的消除方法