大型甲醇合成塔选择探讨及SPC简介
甲醇合成塔正文
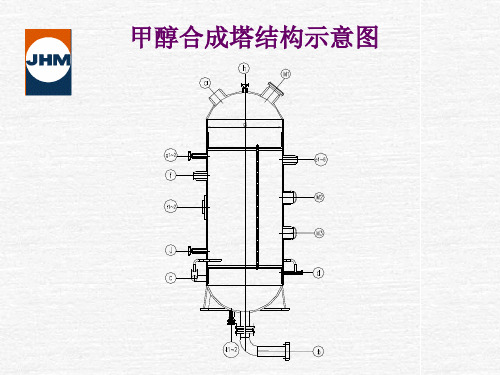
3.2.管板表面带极堆焊
甲醇合成塔的上、下管板管 程侧表面要求进行耐腐蚀材料堆 焊,堆焊焊接材料各不相同 : 过渡层309L+耐蚀层308L; 过渡层309L+耐蚀层347; 过渡层309L+耐蚀层2209; 过 渡 层 309L+ 耐 蚀 层 309LMo ; EQNiCrMo-3(Inconel 625);
甲醇合成塔制造过程工艺难点: 2205双相不锈钢材料的焊接 ; 管板表面带极堆焊 ; 中间管板与筒体焊接 ; 设备各部分的焊后热处理 。
3.1.2205双相不锈钢的焊接
对于2205型双相不锈钢材料, 焊接材料选用Ni含量比母材高一级 的ER2209氩弧焊丝,以获得较高比 例的奥氏体;焊接过程必须采用适 当的热输入保证焊接接头获得好的 奥氏体相变并防止金属间沉淀相的 析出,从而使焊接接头具有良好的 机械性能和耐腐蚀性能。
甲醇合成塔结构示意图
2.主体材料介绍
2.1 13MnNiMoNbR材料,交货状态 为正火加回火,材料焊接性能分析 : Ceq=C+Mn/6+(Cr+Mo+V)/5+(Cu+Ni)/15
2.2 SAF2205奥氏体-铁素体双相 不锈钢材料,耐点蚀系数: PRE=Cr+3.3Mo+16N
3.甲醇合成塔焊接制造工艺
3.3.中间管板与筒体焊接
甲醇合成塔产品结构最大特点是具 有中间管板,其与筒体焊接结构形式分 为以下三种: A. 管板与筒体T型全焊透角接; B. 加强筒体锻件与管板对接; C. 碗形管板锻件与两侧筒体对接;
中间管板筒体连接形式
3.4.设备各部分的焊后热处理
甲醇合成塔封头、壳体材质按照标 准要求,设备焊后必须进行消除应力热 处理,换热管材质为SAF2205不能经历主 体材料的焊后消除应力热处理过程,所 以必须对甲醇合成塔各部件分别进行热 处理,最终合拢焊缝采用电加热器进行 局部热处理。
大型甲醇合成塔技术实现产业化

大型甲醇合成塔技术实现产业化大型甲醇合成塔技术实现产业化是近年来甲醇工业发展的重要里程碑。
甲醇是一种广泛应用于化工、能源、交通等领域的重要化学原料,其产业化的发展对于改善环境、推动经济增长和提高能源效率具有重要意义。
本文将从技术实现、产业化优势以及未来发展等方面对大型甲醇合成塔技术的产业化进行分析。
大型甲醇合成塔技术的实现离不开工程设计和工艺流程的优化。
在大型甲醇合成塔的设计和建设过程中,需要考虑多方面因素,如反应过程的热力学、催化剂的选择和塔内的流体力学等。
通过合理的设计和流程优化,使甲醇合成塔能够在较低的温度和压力下实现高效的甲醇合成反应。
大型甲醇合成塔技术的产业化有以下几个优势。
首先,大型甲醇合成塔可以实现大规模生产,提高生产效率。
传统的小型合成塔规模较小,生产能力有限,而大型甲醇合成塔的产业化可以大幅度提高产能,满足市场的需求。
其次,大型甲醇合成塔技术对资源利用效率较高。
甲醇合成的过程中,可以采用多种原料,如天然气、煤等,有效利用资源。
此外,甲醇合成反应是一个副产物较多的过程,可以获取到一些其它有价值的化学品,增加经济效益。
再次,大型甲醇合成塔技术产业化可以提高环境友好性。
大型甲醇合成塔的工艺优化和尾气处理技术的改进可以降低CO2和其他有害气体的排放,减少对环境的影响。
未来,大型甲醇合成塔技术的产业化还有一些可改进的方面。
首先,需要进一步提高催化剂的选择和催化效率。
当前的催化剂仍然存在效率低和稳定性差的问题,进一步的研究和开发可以提高催化剂的效率和稳定性,降低生产成本。
其次,需要进一步优化工艺流程和降低能耗。
大型甲醇合成塔的能耗仍然较高,需要通过改进工艺流程和提高能源利用效率来降低能耗。
此外,还可以考虑将可再生能源应用于甲醇合成过程中,以进一步提高环保性。
综上所述,大型甲醇合成塔技术的实现产业化具有明显的技术优势和产业优势。
随着技术的不断进步和工艺的不断优化,大型甲醇合成塔的产业化将继续推动甲醇工业的发展,并为广大消费者提供更加优质的甲醇产品。
甲醇合成塔大型管板堆焊技术

甲醇合成塔大型管板带极堆焊技术摘要:通过对大直径20MnMo锻件管板带极堆焊309LMo的焊接及生产应用的研究,合理选择过渡层焊接材料及堆焊各层的工艺规范参数,减小堆焊层合金元素稀释率,控制铁素体含量,保证了堆焊质量,解决了管板堆焊变形的问题,成功用于产品制造。
关键词:管板;带极堆焊;20MnMo锻件;防变形引言化工装置的大型化,对容器的制造提出了更高要求,大型甲醇合成反应器的直径达到φ4000mm,为兼顾经济性和满足使用要求,越来越多地采用低合金管板作为基层,并在其与腐蚀介质接触一面堆焊一层或多层耐蚀合金。
埋弧带极自动堆焊具有熔敷率高,合金元素稀释率低,堆焊层表面光滑、平整、美观,堆焊层质量稳定等特点,被广泛应用于换热器管板的堆焊。
本文通过20万吨/年甲醇合成反应器20MnMo锻件管板堆焊309LMo的实例,介绍其焊接过程。
1堆焊技术要求1.1 管板及堆焊层主要指标管板基层采用20MnMo锻件,接触介质一侧单面堆焊不锈钢耐蚀层,堆焊加工后结构尺寸如图1,20MnMo的化学成分见表1,力学性能见表2。
表120MnMo锻件化学成分%表220MnMo锻件力学性能堆焊共二层,第一层为过渡层,第二层为面层。
堆焊材料:过渡层采用AWS ER309L,面层采用AWS ER309LMo。
堆焊方法:采用埋弧带极堆焊,手工堆焊(仅用局部)焊条为E309MoL。
焊带金属化学成分见表 3,熔敷金属化学成分见表4,堆焊层机械性能见表5。
金相组织:铁素体(10~20)%+奥氏体。
表3 焊带金属化学成分(%)表4 熔敷金属化学成分(%)表 5 堆焊层机械性能1.2 堆焊层合金元素的稀释率堆焊层的化学成分和金相组织在很大程度上取决于基层对堆焊层合金元素稀释率的大小、堆焊层厚度及熔深的大小。
高的稀释率不仅会降低堆焊层的耐腐蚀性能,而且会导致堆焊层焊接材料消耗量的增加,故要求基层对堆焊层稀释率尽量低,并需要通过试验来选择合理的工艺规范参数。
Lurgi甲醇合成塔制造质量控制要点探析
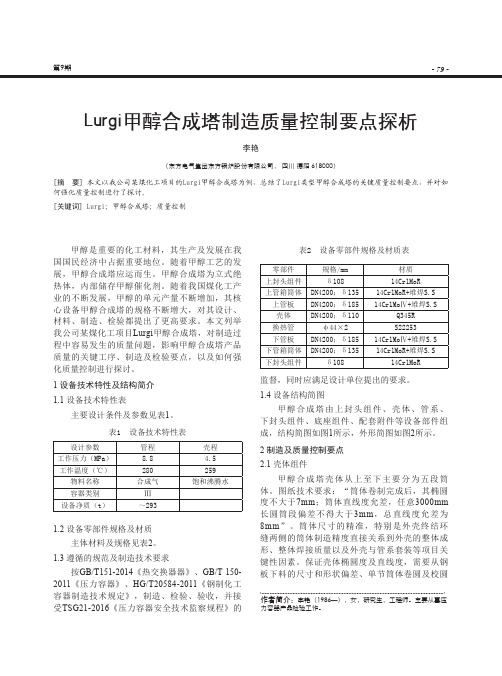
- 79 -第9期表1 设备技术特性表Lurgi甲醇合成塔制造质量控制要点探析李艳(东方电气集团东方锅炉股份有限公司, 四川 德阳 618000)[摘 要] 本文以我公司某煤化工项目的Lurgi甲醇合成塔为例,总结了Lurgi类型甲醇合成塔的关键质量控制要点,并对如何强化质量控制进行了探讨。
[关键词] Lurgi;甲醇合成塔;质量控制作者简介:李艳(1986—),女,研究生,工程师。
主要从事压力容器产品检验工作。
甲醇是重要的化工材料,其生产及发展在我国国民经济中占据重要地位。
随着甲醇工艺的发展,甲醇合成塔应运而生。
甲醇合成塔为立式绝热体,内部储存甲醇催化剂。
随着我国煤化工产业的不断发展,甲醇的单元产量不断增加,其核心设备甲醇合成塔的规格不断增大,对其设计、材料、制造、检验都提出了更高要求。
本文列举我公司某煤化工项目Lurgi 甲醇合成塔,对制造过程中容易发生的质量问题,影响甲醇合成塔产品质量的关键工序、制造及检验要点,以及如何强化质量控制进行探讨。
1 设备技术特性及结构简介1.1 设备技术特性表主要设计条件及参数见表1。
设计参数管程壳程工作压力(MPa)8.8 4.5工作温度(℃)280259物料名称合成气饱和沸腾水容器类别Ⅲ设备净质(t)~2931.2 设备零部件规格及材质主体材料及规格见表2。
1.3 遵循的规范及制造技术要求按GB/T151-2014《热交换器器》、GB/T 150-2011《压力容器》、HG/T20584-2011《钢制化工容器制造技术规定》,制造、检验、验收,并接受TSG21-2016《压力容器安全技术监察规程》的零部件规格/mm 材质上封头组件δ10814Cr1MoR 上管箱筒体DN4200;δ13514Cr1MoR+堆焊S.S 上管板DN4200;δ18514Cr1MoⅣ+堆焊S.S壳体DN4200;δ110Q345R 换热管φ44×2S22253下管板DN4200;δ18514Cr1MoⅣ+堆焊S.S 下管箱筒体DN4200;δ13514Cr1MoR+堆焊S.S下封头组件δ10814Cr1MoR表2 设备零部件规格及材质表监督,同时应满足设计单位提出的要求。
气冷甲醇合成塔

气冷甲醇合成塔
气冷甲醇合成塔是一种用于甲醇合成的设备。
在气冷甲醇合成塔中,通过气相催化合成,将原料气转化为甲醇。
该设备通常具有以下特点:
1.高效性:气冷甲醇合成塔采用先进的催化剂和反应技术,具有较高的转化率和选择性,能够将原料气高效地转化为甲醇。
2.稳定性:该设备采用稳定的气相催化反应,避免了液相反应可能出现的结垢、腐蚀等问题,确保了设备的长期稳定运行。
3.灵活性:气冷甲醇合成塔可以根据不同的原料气和产品要求,进行灵活的工艺调整,以满足不同的生产需求。
4.环保性:该设备采用清洁能源和环保技术,减少了废气、废水的排放,符合环保要求。
在气冷甲醇合成塔的设计和运行过程中,需要考虑到各种因素,如原料气的组成、温度、压力、流量等。
同时,还需要定期对设备进行维护和保养,以确保其正常运行和延长使用寿命。
甲醇合成塔介绍

来??源:百川资讯更新时间:2011-09-0116:17【打印】【收藏】
关键字:甲醇?合成塔
摘??要:甲醇合成塔设计的关键技术之一就是要高效移走和利用甲醇合成反应所放出的巨大热量。
甲醇合成塔设计的关键技术之一就是要高效移走和利用甲醇
热性和热稳定性较好,反应温度接近等温,易于控制,一氧化碳与二氧化碳的单程转化率和气相产物中的甲醇百分含量高于传统的气-固相催化法。
及时甲醇市场资讯,欢迎登陆百川资讯甲醇频道。
更多甲醇相关常识,欢迎进入百川资讯甲醇常识中心。
甲醇合成塔的设计

甲醇合成塔的设计公司标准化编码 [QQX96QT-XQQB89Q8-NQQJ6Q8-MQM9N]甲醇合成塔的设计Design of carbinol Synthetic Tower摘要:本文针对设备DN3400甲醇合成塔的设计要点进行了详细论述。
详细介绍了大直径不带法兰的立式列管固定床甲醇合成塔材料和加热方式的选择,以及各主要部件结构的设计特点。
Abstract: This text introduces the main point of designing de DN3400 carbinol synthetic tower, describes the section of material and heating method used to fabricate large diameter- non-flange, vertical pipe line carbinol synthetic tower. This text also explains the structure design character of the main components and parts.关键词:甲醇合成塔;工作原理;结构设计特点Key Words: Carbinol synthetic tower working theory structure design character1.引言甲醇工业始20世纪初,到20世纪60年代,甲醇工业取得重大进展。
1966年英国ICI公司首先推出了低压甲醇合成工艺—ICI工艺,此为低压法生产甲醇的开端。
所有中、低压法甲醇装置工艺过程类似,在压力为~、温度205℃~275℃操作。
各种工艺的主要区别在于反应器的设计、反应热的移走及回收利用方式的不同,另外,所用的催化剂亦有差异。
国内低压甲醇装置建设始于20世纪70年代,最早引进的是ICI公司的冷激型低压甲醇合成塔装置,数量不多。
甲醇合成塔介绍
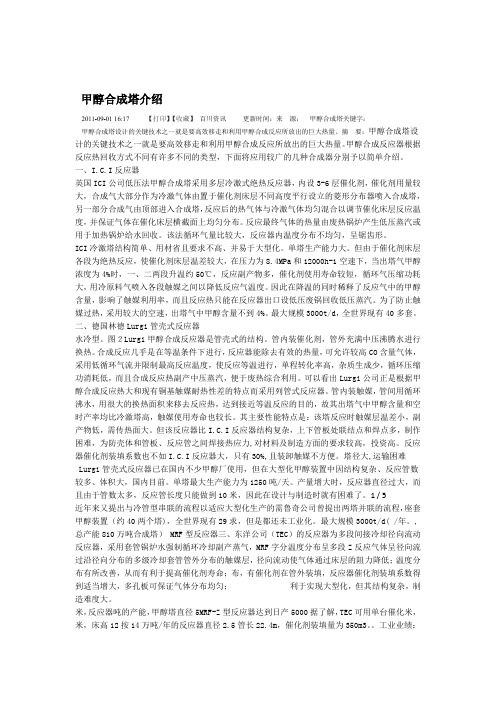
甲醇合成塔介绍2011-09-01 16:17 【打印】【收藏】百川资讯更新时间:来源:甲醇合成塔关键字:甲醇合成塔设计的关键技术之一就是要高效移走和利用甲醇合成反应所放出的巨大热量。
摘要:甲醇合成塔设计的关键技术之一就是要高效移走和利用甲醇合成反应所放出的巨大热量。
甲醇合成反应器根据反应热回收方式不同有许多不同的类型,下面将应用较广的几种合成器分别予以简单介绍。
一、I.C.I反应器英国ICI公司低压法甲醇合成塔采用多层冷激式绝热反应器,内设3-6层催化剂,催化剂用量较大,合成气大部分作为冷激气体由置于催化剂床层不同高度平行设立的菱形分布器喷入合成塔,另一部分合成气由顶部进入合成塔,反应后的热气体与冷激气体均匀混合以调节催化床层反应温度,并保证气体在催化床层横截面上均匀分布。
反应最终气体的热量由废热锅炉产生低压蒸汽或用于加热锅炉给水回收。
该法循环气量比较大,反应器内温度分布不均匀,呈锯齿形。
ICI冷激塔结构简单、用材省且要求不高、并易于大型化。
单塔生产能力大。
但由于催化剂床层各段为绝热反应,使催化剂床层温差较大,在压力为8.4MPa和12000h-1空速下,当出塔气甲醇浓度为4%时,一、二两段升温约50℃,反应副产物多,催化剂使用寿命较短,循环气压缩功耗大,用冷原料气喷入各段触媒之间以降低反应气温度。
因此在降温的同时稀释了反应气中的甲醇含量,影响了触媒利用率,而且反应热只能在反应器出口设低压废锅回收低压蒸汽。
为了防止触媒过热,采用较大的空速,出塔气中甲醇含量不到4%。
最大规模3000t/d,全世界现有40多套。
二、德国林德Lurgi管壳式反应器水冷型。
图2Lurgi甲醇合成反应器是管壳式的结构。
管内装催化剂,管外充满中压沸腾水进行换热。
合成反应几乎是在等温条件下进行,反应器能除去有效的热量,可允许较高CO含量气体,采用低循环气流并限制最高反应温度,使反应等温进行,单程转化率高,杂质生成少,循环压缩功消耗低,而且合成反应热副产中压蒸汽,便于废热综合利用。
- 1、下载文档前请自行甄别文档内容的完整性,平台不提供额外的编辑、内容补充、找答案等附加服务。
- 2、"仅部分预览"的文档,不可在线预览部分如存在完整性等问题,可反馈申请退款(可完整预览的文档不适用该条件!)。
- 3、如文档侵犯您的权益,请联系客服反馈,我们会尽快为您处理(人工客服工作时间:9:00-18:30)。
大型甲醇合成塔选择探讨及SPC简介日本高化学上海国际贸易有限公司张炳摘要:本文简要介绍了我国近年来甲醇项目建设的大型化趋势,并对国内外流行的几种合成塔进行了介绍和分析,并详细介绍了SPC甲醇合成塔的特点,以期对我国新上大型甲醇装置选择优良的合成塔有所帮助。
关键词:超级合成塔(超转化率合成塔);双套管;甲醇合成塔keywords : superconverter; double tube;methanol converter一、目前我国甲醇生产现状及甲醇装置大型化的必然性甲醇是重要的基础有机化工品和原料,又是极有前途的代用燃料。
甲醇的衍生物有100多种,近年来消费量增长迅速。
据统计,1991-1999年我国甲醇市场的需求量年平均增长率约为16%,2000年市场需求量为350万吨,2002年甲醇需求量为390万吨,预计到2005年将达到512万吨。
现在河南、北京、山西等省市正在大力推广“甲醇代油”工程,国内大型二甲醚工程也如火如荼的进展,甲醇市场在未来几年的需求将远远大于16%的年平均增长率。
虽然我国甲醇的年生产能力达到500万吨左右,但由于多种原因,实际开工率并不高,2001年装置开工率只有63%,2002年装置开工率只有55%。
国产甲醇远远不能满足国内市场的需求,目前我国甲醇大约40%需要进口。
近年来,我国甲醇工业取得了一定的发展,但与国外甲醇工业相比,还存在很大的差距。
目前,我国甲醇生产厂家超过150家,2003年实际开工的厂家大约120个,累计产能在578.3万吨。
工艺上,10万吨以上的装置还处于国外70年代的水平,产量低、能耗高、工艺落后导致装置经常停车,成本很高,无法与先进工艺竞争。
目前我国还没有单套大于30万吨的已投产甲醇装置。
其他大多为5万吨以下小型甲醇装置,采用的是国外已经淘汰的煤头高压法。
据统计,我国甲醇生产企业中,成本高的超过了1800元/吨,低的900多元/吨,大多数为1400元/吨左右。
由此,在甲醇生产领域,国内外存在明显差距,工艺落后、规模太小是阻碍甲醇生产节能的主要原因。
甲醇生产装置大型化可以明显降低产品投资和产品成本。
国外公司纷纷兴建80万吨以上的甲醇装置。
我国从02年起新起了新一轮甲醇扩产和新建的高潮,全国各个天然气及煤基地都在拟建30万吨以上甲醇项目。
据统计,国内拟建的60万吨以上甲醇项目至少有4-5个。
甲醇装置大型化已经成为我国甲醇工业发展的趋势。
二、甲醇合成塔甲醇合成的核心设备是合成塔。
选择稳定、节能、高产率、经济的合成塔对生产厂家至关重要。
从操作、结构、材料及维修等方面考虑,对甲醇合成塔的基本要求有:1、稳定性好,结构可靠;2、在操作上要求催化剂温度易于控制,调节灵活;合成反应器的转化率高;催化剂生产强度大,活性高而且稳定;能回收高位能的反应热;床层中气体分布均匀;压降低。
3、催化剂升温、还原操作方便、还原充分;4、气体能均匀地通过催化剂层,阻力小,甲醇产量高;5、操作稳定、调节方便,能适应各种操作条件的变化;6、装卸催化剂方便,制造、安装和维修容易;7、各个内件的连接与保温适当,使内件能在塔内自由移动,避免产生热应力。
甲醇合成塔设计的关键技术之一就是要有效的利用甲醇合成反应所放出的巨大热量。
甲醇合成反应器根据反应热回收方式不同有许多不同的类型,下面将分别予以简单介绍,并从以上几方面进行比较。
2.1 I.C.I反应器英国ICI公司低压法甲醇合成塔采用多层冷激式绝热反应器,催化剂用量较大,合成气大部分作为冷激气体由置于催化剂床层不同高度平行设立的菱形分布器喷入合成塔,另一部分合成气由顶部进入合成塔,反应后的热气体与冷激气体均匀混合以调节催化床层反应温度,并保证气体在催化床层横截面上均匀分布。
反应最终气体的热量由废热锅炉产生低压蒸汽或用于加热锅炉给水回收。
该法循环气量比较大,反应器内温度分布不均匀,呈锯齿形。
ICI冷激塔结构简单、用材省且要求不高、并易于大型化。
单塔生产能力大。
但由于催化剂床层各段为绝热反应,使催化剂床层温差较大,在压力为8.4MPa和12000h-1空速下,当出塔气甲醇浓度为4%时,一、二两段升温约50℃,反应副产物多,催化剂使用寿命较短,循环气压缩功耗大,用冷原料气喷入各段触媒之间以降低反应气温度。
因此在降温的同时稀释了反应气中的甲醇含量,影响了触媒利用率,而且反应热只能在反应器出口设低压废锅回收低压蒸汽。
为了防止触媒过热,采用较大的空速,出塔气中甲醇含量不到4%。
据笔者所知,可用四段ICI冷激型合成塔串达到日产甲醇3600吨的能力。
合成塔内径为6.1米,床层高度12.2米,催化剂装填量为283m3,合成压力为10.34MPa,出塔气中甲醇含量5.7%,催化剂空时产率0.53吨/m3·h。
这在国内加工和运输难度都较大。
其大致结构和床层温度分布见图1:图1. I.C.I冷激式绝热反应器图2.Lurgi 管壳式反应器2.2 Lurgi管壳式反应器图2Lurgi甲醇合成反应器是管壳式的结构。
管内装催化剂,管外充满中压沸腾水进行换热。
其主要性能特点是:该塔反应时触媒层温差小。
合成反应几乎是在等温条件下进行,反应器能除去有效的热量,可允许较高CO含量气体,采用低循环气流并限制最高反应温度,使反应等温进行,单程转化率高,杂质生成少,循环压缩功消耗低,而且合成反应热副产中压蒸汽,便于废热综合利用。
可以看出Lurgi公司正是根据甲醇合成反应热大和现有铜基触媒耐热性差的特点而采用列管式反应器。
管内装触媒,管间用循环沸水,用很大的换热面积来移去反应热,达到接近等温反应的目的,故其出塔气中甲醇含量和空时产率均比冷激塔高,触媒使用寿命也较长。
但该反应器比I.C.I反应器结构复杂,上下管板处联结点和焊点多,制作困难,对材料及制造方面的要求较高。
反应器催化剂装填系数也不如I.C.I反应器大,且装卸触媒不方便。
Lurgi管壳式反应器已在国内不少甲醇厂使用,但在大型化甲醇装置中因结构复杂、反应管数较多、体积大,国内目前。
单塔最大生产能力为1250吨/天。
产量增大时,反应器直径过大,而且由于管数太多,反应管长度只能做到10米,因此在设计与制造时就有困难了。
鲁奇公司曾提出两塔并联的流程,近年来又提出与冷管型串联的流程以适应大型化生产的需求,但是都还未工业化。
2.3东洋公司(TEC)的MRF型反应器图3东洋公司MRF反应器MRF反应器为多段间接冷却径向流动反应器,采用套管锅炉水强制循环冷却副产蒸气,反应气体呈径向流过沿径向分布的多级冷却套管管外分布的触媒层,温度分布呈多段Z字分布,温度分布有所改善,从而有利于提高催化剂寿命;径向流动使气体通过床层的阻力降低;多孔板可保证气体分布均匀;催化剂在管外装填,反应器催化剂装填系数得到适当增大,有利于实现大型化,但其结构复杂,制造难度大。
据了解,TEC可用单台MRF-Z型反应器达到日产5000吨的产能,甲醇塔直径5米,反应器管长22.4m,催化剂装填量为350M3。
按14万吨/年的反应器直径2.5米,床高12米,催化剂装填量43m3,合成压力5.82MPa,催化剂生产强度约0.4吨/ m3·h。
2.4 Linde螺旋管反应器Linde在催化反应层中设置螺旋管,用锅炉水移去管外催化剂层反应热。
使用螺旋冷管比Lurgi直管较好解决热应力问题,而且催化剂装填系数大,有利于大型化。
但设备加工难度进一步增加,据报道国内只有川维厂使用一套。
大型化困难。
2.5 国内管壳式反应器西南化工研究设计院、华东理工大学和鲁南化肥厂联合开发了结合I.C.I和Lurgi反应器特点的绝热等温混合型甲醇合成反应器,基本为列管式反应器,管板顶部装有300mm的绝热催化剂层,列管内装催化剂,管间沸腾水移去反应热。
催化剂层温差小,合成效率比冷激型高,并可副产蒸汽,热量回收利用合理。
不仅承继了I.C.I反应器催化剂装填系数大、Lurgi反应器床层温差小的优点,而且拥有自主知识产权,在鲁南化肥厂10万吨/年甲醇装置和上海焦化厂20万吨/年甲醇装置上使用都非常成功。
但其由于结构原因,只能在进出口设置温度计,不利于对轴向温差2.6杭州林达公司JW均温合成塔据报道,杭州林达公司JW性均温合成塔,其主要特点是在全部触媒床层中采用可自由伸缩活动装配。
催化剂装填系数为70~75%。
用管内冷气及时吸收管外反应热,管内冷气与触媒层中反应气有并流换热和逆流间接换热,可以在催化剂层内及塔内任何部位设置温度监测点。
用塔外设置废锅副产低压蒸汽或锅炉给水加热器回收热量。
该合成塔在国内小型的装置中应用较多,但还没有10万吨以上的工业化设备出现。
2.7三菱瓦斯超级合成塔(SPC)这是近年来在世界上广为使用的大型合成塔,为三菱瓦斯化学公司的工艺。
该塔为双套管式。
进塔气先预热到150-170℃,入塔后分布到各双套管的内管中,吸收管外套管间的反应热,预热至反应温度240℃后进入套管间的催化剂层反应,热点温度250℃左右,反应热同时被内管中冷气和外管外壳程间的沸腾水移走,出触媒层温度为205-230℃左右,出塔气中甲醇含量8.5%。
SPC有着比Lurgi等温反应器低的循环比和比Lurgi反应器更高的单程转化率,SPC双套管内径75mm比Lurgi列管反应器Ф24大得多,管数少得多,故装卸触媒容易,SPC外管受压壁厚,比列管式机械强度好,内管、挠管和隔板为不受压部件,作用在这些部分的触媒层压降最多为2-3kg/m2。
所以大型化容易,单套最高产图6 超级合成。