梯形多线螺纹的加工方法
梯形螺纹加工工艺分析
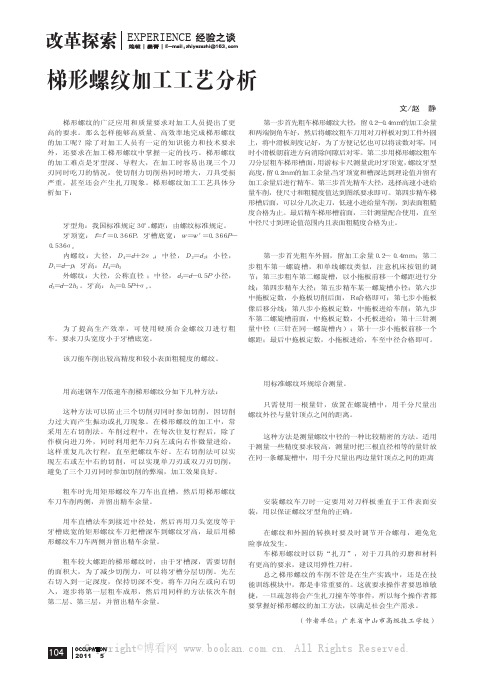
OCCUPATION2011 5104梯形螺纹加工工艺分析文/赵 静梯形螺纹的广泛应用和质量要求对加工人员提出了更高的要求。
那么怎样能够高质量、高效率地完成梯形螺纹的加工呢?除了对加工人员有一定的知识能力和技术要求外,还要求在加工梯形螺纹中掌握一定的技巧。
梯形螺纹的加工难点是牙型深、导程大,在加工时容易出现三个刀刃同时吃刀的情况,使切削力切削热同时增大,刀具受损严重,甚至还会产生扎刀现象。
梯形螺纹加工工艺具体分析如下:一、参数计算标准牙型角:我国标准规定30°。
螺距:由螺纹标准规定。
牙顶宽:f=f′=0.366P。
牙槽底宽:w=w′=0.366P-0.536αc内螺纹:大径,D4=d+2αc;中径,D2=d2;小径,D1=d-p;牙高:H4=h3外螺纹:大径,公称直径 ;中径,d2=d-0.5P 小径,d3=d-2h3 。
牙高:h3=0.5P+αc 。
二、刀具准备1.硬质合金梯形螺纹粗车刀为了提高生产效率,可使用硬质合金螺纹刀进行粗车。
要求刀头宽度小于牙槽底宽。
2.高速钢梯形螺纹精车刀该刀能车削出较高精度和较小表面粗糙度的螺纹。
三、加工方法用高速钢车刀低速车削梯形螺纹分如下几种方法:1.左右切入法 这种方法可以防止三个切削刃同时参加切削,因切削力过大而产生振动或扎刀现象。
在梯形螺纹的加工中,常采用左右切削法。
车削过程中,在每次往复行程后,除了作横向进刀外,同时利用把车刀向左或向右作微量进给,这样重复几次行程,直至把螺纹车好。
左右切削法可以实现左右或左中右的切削,可以实现单刀刃或双刀刃切削,避免了三个刀刃同时参加切削的弊端,加工效果良好。
2.车直槽法粗车时先用矩形螺纹车刀车出直槽,然后用梯形螺纹车刀车削两侧,并留出精车余量。
3.车台阶槽法用车直槽法车到接近中径处,然后再用刀头宽度等于牙槽底宽的矩形螺纹车刀把槽深车到螺纹牙高,最后用梯形螺纹车刀车两侧并留出精车余量。
4.分层切削法粗车较大螺距的梯形螺纹时,由于牙槽深,需要切削的面积大,为了减少切削力,可以将牙槽分层切削。
数控车床可换刀、换速加工梯形螺纹的操作技巧
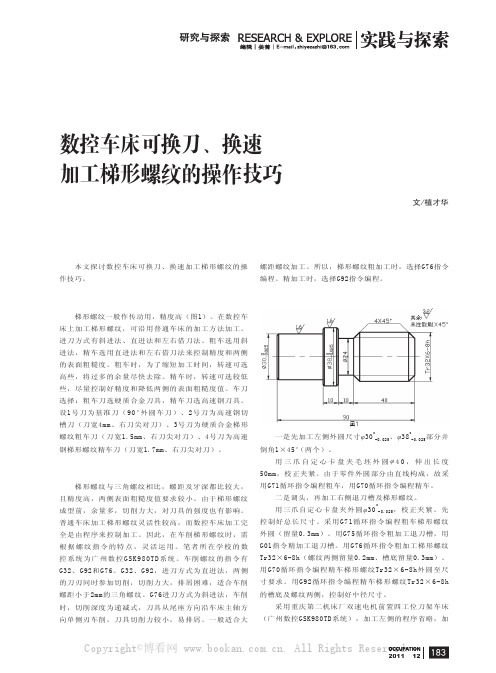
数控车床可换刀、换速加工梯形螺纹的操作技巧文/植才华本文探讨数控车床可换刀、换速加工梯形螺纹的操作技巧。
一、加工方法及刀具选择梯形螺纹一般作传动用,精度高(图1)。
在数控车床上加工梯形螺纹,可沿用普通车床的加工方法加工。
进刀方式有斜进法、直进法和左右借刀法。
粗车选用斜进法,精车选用直进法和左右借刀法来控制精度和两侧的表面粗糙度。
粗车时,为了缩短加工时间,转速可选高些,将过多的余量尽快去除。
精车时,转速可选较低些,尽量控制好精度和降低两侧的表面粗糙度值。
车刀选择:粗车刀选硬质合金刀具,精车刀选高速钢刀具。
设1号刀为基准刀(90°外圆车刀)、2号刀为高速钢切槽刀(刀宽4mm、右刀尖对刀)、3号刀为硬质合金梯形螺纹粗车刀(刀宽1.5mm、右刀尖对刀)、4号刀为高速钢梯形螺纹精车刀(刀宽1.7mm、右刀尖对刀)。
二、加工时选择的指令梯形螺纹与三角螺纹相比,螺距及牙深都比较大,且精度高,两侧表面粗糙度值要求较小。
由于梯形螺纹成型前,余量多,切削力大,对刀具的强度也有影响。
普通车床加工梯形螺纹灵活性较高,而数控车床加工完全是由程序来控制加工。
因此,在车削梯形螺纹时,需根据螺纹指令的特点,灵活运用。
笔者所在学校的数控系统为广州数控GSK980TD系统。
车削螺纹的指令有G32、G92和G76。
G32、G92,进刀方式为直进法,两侧的刀刃同时参加切削,切削力大,排屑困难,适合车削螺距小于2mm的三角螺纹。
G76进刀方式为斜进法,车削时,切削深度为递减式,刀具从尾座方向沿车床主轴方向单侧刃车削,刀具切削力较小,易排屑。
一般适合大螺距螺纹加工。
所以,梯形螺纹粗加工时,选择G76指令编程。
精加工时,选择G92指令编程。
三、装夹方案一是先加工左侧外圆尺寸φ300-0.025、φ380-0.025部分并倒角1×45°(两个)。
用三爪自定心卡盘夹毛坯外圆φ40,伸出长度50mm,校正夹紧。
由于零件外圆部分由直线构成,故采用G71循环指令编程粗车,用G70循环指令编程精车。
多线梯形螺纹的车削
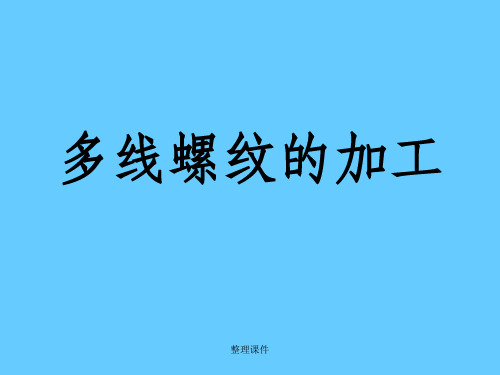
整理课件
七、加工步骤
1、车削工件端 面,车出即 可。
整理课件
2、打中心孔 φ3A。
整理课件
3、车螺纹外圆 φ控4制0 长0 0度.375至及 65。
整理课件
整理课件
4、按图纸要求
切出 3215
退刀槽(保证 螺纹外圆长
50),螺纹外 圆两边倒
角445。
5、按导程 (12mm)调整 走刀箱各手柄位 置。
• 导程L:同一螺旋 线上相邻两牙在中 径线上对应两点间 的轴向距离L。
• 导程L= 线数n×螺 距P。
整理课件
• 螺旋升角ψ : 由于多线螺纹的导程增
大一般应考虑其螺旋升角的 影响。螺纹升角对车刀工作 角度有较大的影响,即在车 右螺纹时左侧的后角等于工 作后角加上螺纹升角,而右 侧后角等于工作后角减去螺 纹升角。 tanψ=L/πd2=nP/πd2
多线螺纹的加工
整理课件
一、多线螺纹练习图
4×15°
I
4×15°
1.6
全部
Tr40×12(P6)-8e
32
12
I
6
15° ±15′ 15° ±15′ 2:1
50 65
40 -00.375
37 --00..519148
33 -00.649
练习内容 多线螺纹加工
材料 规格 5# φ45×150
件数 工时(min)
注意底径的的深度要 符合图
2)第一条螺旋线侧面 1(见图)加工完,将 车刀向前移动一个螺 距,加工第二条螺旋 线的同一侧面2(见 图)。注意小滑板向 前移动一个螺距,中 滑板刻线读数与前条 螺旋槽加工成一致。 这是为了保证第一条 螺纹深度与第二条的 螺纹深度一致。
数控车床上加工梯形螺纹

数控车床上加工梯形螺纹内容摘要:在数控车床上加工梯形螺纹是一个全新的课题,本文通过对梯形螺纹加工的工艺分析和加工方法的研讨,探索出一套可以在数控车床上加工出合格梯形螺纹的方法在普通车床的生产实习过程中,加工梯形螺纹课题是最基本的实习课题,但在数控车床实习过程中,常常由于加工工艺方面的原因,却很少进行梯形螺纹的加工练习,甚至有人提出在数控车床上不能加工梯形螺纹,显然这种提法是错误的.其实,只要工艺分析合理,使用的加工指令得当,完全可以在数控车床上加工出合格的梯形螺纹。
一、梯形螺纹加工的工艺分析1。
梯形螺纹的尺寸计算梯形螺纹的代号梯形螺纹的代号用字母“Tr”及公称直径×螺距表示,单位均为mm。
左旋螺纹需在尺寸规格之后加注“LH”,右旋则不用标注。
例如Tr36×6,Tr44×8LH等.国标规定,公制梯形螺纹的牙型角为30°。
梯形螺纹的牙型如图(1),各基本尺寸计算公式如表1—1。
图1 梯形螺纹的牙型2。
梯形螺纹在数控车床上的加工方法直进法螺纹车刀X向间歇进给至牙深处(如图2a)。
采用此种方法加工梯形螺纹时,螺纹车刀的三面都参加切削,导致加工排屑困难,切削力和切削热增加,刀尖磨损严重。
当进刀量过大时,还可能产生“扎刀”和“爆刀”现象。
这种方法数控车床可采用指令G92来实现,但是很显然,这种方法是不可取的。
斜进法螺纹车刀沿牙型角方向斜向间歇进给至牙深处(如图2b)。
采用此种方法加工梯形螺纹时,螺纹车刀始终只有一个侧刃参加切削,从而使排屑比较顺利,刀尖的受力和受热情况有所改善,在车削中不易引起“扎刀"现象。
该方法在数控车床上可采用G76指令来实现。
交错切削法螺纹车刀沿牙型角方向交错间隙进给至牙深(如图2c)。
该方法类同于斜进法,也可在数控车床上采用G76指令来实现.切槽刀粗切槽法该方法先用切槽刀粗切出螺纹槽((如图2d),再用梯形螺纹车刀加工螺纹两侧面。
这种方法的编程与加工在数控车床上较难实现。
数控车床中梯形螺纹(蜗杆)加工方法

数控车床中梯形螺纹(蜗杆)加工方法作者:李俊来源:《文理导航》2011年第20期通常车削梯形螺纹时,采用高速钢材料刀具进行低速车削,一般采用图1四种进刀方法:直进法、左右切削法、车直槽法和车阶梯槽法。
直进法适用于车削螺距较小(P4mm)的梯形螺纹常采用左右切削法、车直槽法和车阶梯槽法。
在这四种切削方法中,除直进法外,其他三种车削方法都能不同程度地减轻或避免三刃同时切削,使排屑较顺畅,刀尖受力、受热情况有所改善,从而不易出现振动和扎刀现象,还可提高切削用量,改善螺纹表面质量。
所以,左右切削法、车直槽法和车阶梯槽法获得了广泛的应用。
在数控车床上车削三角螺纹时一般可选用标准机夹刀具,利用螺纹循环指令完成加工。
但由于梯形螺纹较之三角螺纹,其螺距和牙型都大,而且精度高,牙型两侧面表面粗糙度值较小,致使梯形螺纹车削时,吃刀深,走刀快,切削余量大,切削抗力大,加之有些数控车床刚性较差,如果在切削过程中参数选择不合理就容易产生“扎刀”和“爆刀”现象。
采用斜进法对标准螺纹来说,由于有固定循环指令,较为方便,但对异型螺纹加工就不太方便。
下面介绍利用宏程序采用“分层法”切削加工梯形螺纹,该方法切削状况好,对刀具要求不高,尺寸由程序中相应数值保证,当牙顶宽和螺纹底径达到尺寸要求时,螺纹中径等其他各项尺寸也相应达到尺寸要求,尺寸精度易于控制,螺纹表面质量好,甚至蜗杆和其它异型螺纹的加工也可套用该方法的编程思路。
这里讲的“分层法”车削梯形螺纹实际上是直进法和左右切削法的综合应用。
在车削较大螺距的梯形螺纹时,“分层法”通常不是一次性就把梯形槽切出来,而是把牙槽分成若干层,每层深度根据实际机床情况可转化成若干个较浅的梯形槽来进行切削。
每一层的切削都采用左右交替车削的方法,背吃刀量很小,刀具只需沿左右牙型线切削,梯形螺纹车刀始终只有一个侧刃参加切削,从而使排屑比较顺利,刀尖的受力和受热情况有所改善,因此能加工出较高质量的梯形螺纹。
浅谈在数控车床上运用宏程序加工多线梯形螺纹轴的应用
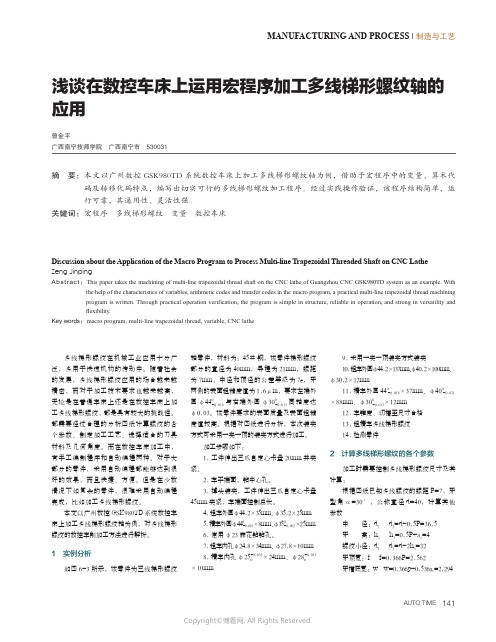
MANUFACTURING AND PROCESS | 制造与工艺浅谈在数控车床上运用宏程序加工多线梯形螺纹轴的应用曾金平广西南宁技师学院 广西南宁市 530031摘 要: 本文以广州数控GSK980TD系统数控车床上加工多线梯形螺纹轴为例,借助于宏程序中的变量、算术代码及转移代码特点,编写出切实可行的多线梯形螺纹加工程序。
经过实践操作验证,该程序结构简单,运行可靠,其通用性、灵活性强。
关键词:宏程序 多线梯形螺纹 变量 数控车床多线梯形螺纹在机械工业应用十分广泛,多用于快速机构的传动中。
随着社会的发展,多线梯形螺纹应用的场合越来越精密,而对于加工技术要求也越来越高,无论是在普通车床上还是在数控车床上加工多线梯形螺纹,都是具有较大的挑战性。
都需要经过合理的分析图纸计算螺纹的各个参数、制定加工工艺、选择适合的刀具材料及几何角度。
而在数控车床加工中,有手工编制程序和自动编程两种。
对于大部分的零件,采用自动编程都能够达到很好的效果,而且快捷、方便。
但是在少数情况下如复杂的零件,很难采用自动编程完成,比如加工多线梯形螺纹。
本文以广州数控GSK980TD系统数控车床上加工多线梯形螺纹轴为例,对多线梯形螺纹的数控车削加工方法进行解析。
1 实例分析如图6-3所示,该零件为三线梯形螺纹轴零件,材料为:45#钢,该零件梯形螺纹部分的直径为40mm,导程为21mm,螺距为7mm,中径和顶径的公差等级为7e,牙两侧的表面粗糙度值为1.6μm,要求左端外圆φ440-0.018与右端外圆φ300-0.013同轴度达φ0.03。
该零件要求的表面质量及表面粗糙度值较高。
根据对图纸进行分析,本次装夹方式可采用一夹一顶的装夹方式进行加工。
加工步骤如下:1.工件伸出三爪自定心卡盘20mm并夹紧。
2.车平端面,钻中心孔。
3.掉头装夹,工件伸出三爪自定心卡盘45mm夹紧,车端面控制总长。
4.粗车外圆φ44.2×35mm、φ35.2×25mm5.精车外圆φ440-0.018×8mm、φ350-0.062×25mm6.使用φ23麻花钻钻孔。
第六章 螺纹加工
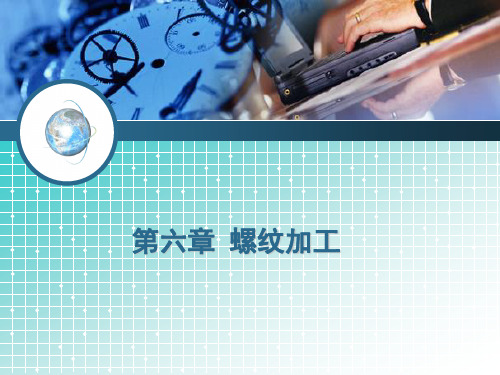
三、梯形螺纹车刀的装夹
螺纹车刀的刀尖应与工件轴线等高,两切削刃夹角的平分 线应垂直于工件轴线,装夹时用梯形螺纹对刀样板校正,以免 产生螺纹半角误差。
四、梯形螺纹车削注意事项
1. 加工梯形螺纹时应采用左右借刀法加工,避免刀具三刃 口同时切削,产生扎刀。 2. 螺纹的牙型角要正确,螺纹牙型两侧面的表面粗糙值要 小。 3. 螺纹加工过程中,应注意不得改变转速,否则会乱牙。
第六章 螺纹加工
在各种机电产品中,螺纹的应用十分广泛,如螺钉、螺 母、螺杆、丝杠等。 用途:它主要用于连接各种机件,也可用来传递运动和载 荷。 主要分类: 按螺纹的牙型——三角形、梯形、锯齿形、圆形等; 按螺纹的外廓形状——圆柱螺纹、圆锥螺纹。
螺纹轴套零件图
第一节 等距螺纹的加工 第二节 多线螺纹的加工 第三节 梯形螺纹的加工
二、运用子程序加工梯形螺纹
上例中的螺纹加工也可用左右切削法,可调用子程序重复 进刀切削。
(下一页续表)
续表
梯形螺纹的加工方法
一、梯形螺纹的一般技术要求
梯形螺纹的轴向剖面形状是等腰梯形。用作传动,精度要 求高,表面粗糙值小,车削梯形螺纹比车削三角螺纹困难。梯 形螺纹的一般技术要求如下: 1. 螺纹的中径必须与基准轴颈同轴,其大径尺寸应小于基 本尺寸。
毛坯为φ45mm×75mm的45钢,用G71、G92指令进行编程, 加工该零件。
实例零件图
一、工艺分析
1. 夹住毛坯φ45mm外圆,伸出大于40mm长→粗车 φ34mm外圆至φ34.5mm→粗车φ24mm外圆至φ24.5mm,精 车外轮廓至尺寸。 2. 换4mm车槽刀加工退刀槽。 3. 换外三角螺纹刀粗、精加工M24×3(1.5)-6g外 螺纹至尺寸。
k :螺纹的牙深。半径值,单位为μm。
多线内梯形螺纹的加工方法优化
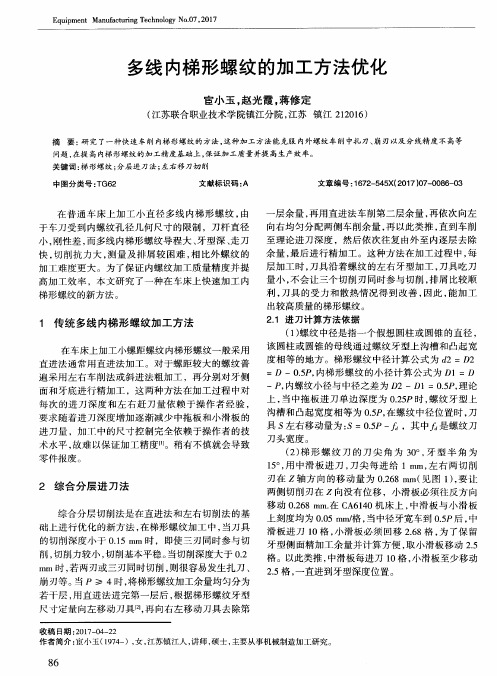
多线 内梯 形螺纹 的加工方法优化
宦小玉 。 赵 光霞 。 蒋修定
( 江 2 1 2 0 1 6 )
摘 要: 研 究 了一种快速 车削 内梯形螺纹 的方法 , 这种 加工方法能 克服 内外螺纹车 削中扎 刀、 崩 刃以及 分线精度 不高等
问题 , 在提 高 内梯 形 螺 纹 的 加 工精 度 基 础 上 , 保 证 加 工 质 量 并 提 高生 产 效 率 。
关键词 : 梯形螺纹 ; 分层 进刀法 ; 左 右移 刀切 削
中 图分 类 号 : T G6 2 文 献标 识 码 : A 文章编号 : 1 6 7 2 — 5 4 5 X ( 2 0 1 7 ) 0 7 — 0 0 8 6 — 0 3
层余量 , 再用直进法车削第二层余量 , 再依次 向左 向右均匀分配两侧车削余量 , 再 以此类推 , 直到车削 于车 刀 受 到 内螺 纹 孔径 几 何 尺 寸 的 限制 ,刀杆 直 径 小, 刚性 差 , 而多 线 内梯 形 螺 纹 导程 大 、 牙 型深 、 走 刀 至理 论 进 刀深 度 ,然后 依 次 往 复 由外 至 内逐 层 去 除 最后进行精加工 。这种方法在加工过程中 , 每 快, 切 削抗 力 大 , 测 量 及 排 屑 较 困难 , 相 比外 螺 纹 的 余量 , 刀 具 沿着 螺 纹 的左 右 牙 型 加工 , 刀具 吃刀 加 工难 度 更 大 。 为 了保证 内螺 纹 加工 质 量 精度 并 提 层加 工 时 , 量小 , 不 会 让 三 个切 削 刃 同时参 与 切 削 , 排 屑 比较 顺 高加 工 效 率 ,本 文 研 究 了一 种 在 车床 上 快 速 加工 内 利, 刀具 的受 力 和散 热 情 况 得 到 改 善 , 因此 , 能 加 工 梯 形 螺 纹 的新 方 法 。 出较高质量的梯形螺纹。 2 . 1 进 刀 计算 方 法依 据 1 传 统 多线 内梯 形螺纹/ J N T方 法 ( 1 ) 螺 纹 中径 是 指 一个 假 想 圆 柱或 圆锥 的直 径 , 该 圆柱 或 圆锥 的母 线 通 过螺 纹 牙 型 上 沟槽 和 凸起 宽 在车 床上 加 工小 螺距 螺纹 内梯形 螺 纹 一般 采用 度 相 等 的地 方 。梯 形 螺 纹 中径 计 算 公 式 为 d 2:D 2 直进 法通 常 用 直 进法 加 工 。对 于螺距 较 大 的螺 纹普 D 一0 . 5 P, 内梯 形 螺 纹 的 小 径 计 算公 式 为 D1=D 遍 采 用左 右 车 削 法或 斜 进 法粗 加 工 ,再 分 别 对 牙侧 P, 内螺 纹小 径 与 中径之 差 为 D 2一D1=0 . 5 P, 理论 面 和 牙底 进 行 精 加工 ,这 两 种方 法 在加 工 过 程 中对 上, 当 中拖 板 进 刀 单边 深 度 为 0 . 2 5 P时 , 螺纹 牙 型 上 每 次 的进 刀 深 度 和 左 右 赶 刀 量 依 赖 于操 作 者 经 验 , 沟槽 和凸起宽度相等为 0 . 5 P , 在螺纹 中径位置时 , 刀 要 求 随着 进 刀 深 度增 加 逐 渐 减少 中拖板 和小 滑 板 的 具| s 左 右 移 动量 为 : S=0 . 5 P一 ,其 中 是 螺 纹 刀 进 刀 量 ,加 T 中的 尺寸 控 制 完全 依 赖 于操 作 者 的技 刀 头宽 度 。 术水平 , 故难 以保 证 加工 精 度 I ” 。稍 有 不 慎 就会 导 致 ( 2 ) 梯 形螺 纹 刀 的刀 尖 角为 3 0 。 , 牙 型 半 角 为 零 件报 废 。 1 5 。 , 用 中滑 板 进 刀 , 刀尖 每进 给 1 m m, 左 右 两 切 削 刃 在 z轴 方 向 的移 动 量 为 0 . 2 6 8 a r m( 见图 1 ) , 要 让 2 综 合 分 层 进 刀 法 两 侧切 削 刃 在 z向没有 位 移 ,小 滑 板 必须 往 反 方 向 移动 0 . 2 6 8 m m. 在C A 6 1 4 0机 床 上 , 中 滑板 与小 滑 板 综 合 分层 切 削法 是 在直 进 法 和 左右 切 削 法 的基 上 刻度 均 为 0 . 0 5 m m/ 格, 当中径 牙宽 车 到 0 . 5 P后 , 中 础 上 进 行优 化 的新 方法 , 在梯 形 螺 纹加 工 中 , 当刀 具 滑板进刀 l 0格 , 小 滑 板 必 须 回移 2 . 6 8格 , 为 了保 留 的切 削 深 度小 于 0 . 1 5 m m 时 ,即使 三 刃 同 时参 与 切 牙型侧面精加工余量并计算方便 , 取小滑板移动 2 . 5 削, 切 削力 较 小 , 切 削基本 平稳 。 当切 削 深度 大 于 0 . 2 格 。以此类 推 , 中滑板 每进 刀 1 0格 , 小 滑板 至 少移 动 m m 时 , 若 两 刃或 三 刃 同 时切 削 , 则很 容 易发 生 扎 刀 、 2 . 5格 , 一 直进 到 牙型 深度 位置 。 崩刃等。 当 P≥ 4 时, 将梯形螺纹加工余量均匀分为 若干层 , 用 直 进 法进 完 第 一层 后 , 根据 梯 形 螺纹 牙 型
- 1、下载文档前请自行甄别文档内容的完整性,平台不提供额外的编辑、内容补充、找答案等附加服务。
- 2、"仅部分预览"的文档,不可在线预览部分如存在完整性等问题,可反馈申请退款(可完整预览的文档不适用该条件!)。
- 3、如文档侵犯您的权益,请联系客服反馈,我们会尽快为您处理(人工客服工作时间:9:00-18:30)。
梯形多线螺纹的加工方法梯形多线螺纹在车削加工中是一个较难的课题之一,它不仅要保证每条螺纹的尺寸精度和形状精度,而且还要保证几条螺纹的相对位置精度。
如果几条螺纹的位置精度(分线精度)出现较大误差,将会影响其配合精度,甚至造成无法安装,工件报废。
由此可见,多线螺纹分头精度是加工中的重点所在。
从理论上讲,不论是利用圆周分头法,还是轴线分头法都可以获得准确的分线精度。
但在实际操作中,没有一定的应变能力和一定的操作经验是难以加工出分线准确、精度较高的多线螺纹,甚至出现在粗加工中由于分头误差而产生工件报废。
在多年的工作实践中,我总结出了一套加工多线外螺纹的方法。
一、相关工艺知识
梯形螺纹车刀和几何角度及刃磨要求
梯形螺纹有英制和米制两种,米制牙型30°,英制牙型29°,我们常采用米制螺纹。
梯形螺纹车刀分粗车刀和精车刀两种。
1.梯形螺纹车刀角度
1)两刃夹角粗车刀应小于牙型角,精车刀应等于牙型角。
2)纵向前角粗车刀一般为15°左右,精车刀前角应等于0.
但实际时取5°--10°。
3)纵向后角一般为6°—8°。
4)两侧螺旋升角α1=(3—5)+Ψα2=(3—5)-Ψ
2.梯形螺纹车刀的刃磨要求
1)用样板校对刃磨两刀刃夹角。
2)车刀刃口要光滑、平直、无虚刃,两侧副刀刃必须对称刀头不能歪斜。
3)用油石研磨去各刀刃的毛刺。
二、梯形多线螺纹的车削方法(以Tr36×12 P6为例)
车削梯形螺纹与三角螺纹相比,螺距大、牙型角大、切削余量大、切削抗力大,而且精度要求高,加之工件一般都比较长,所以加工难度较大。
一般车削梯形螺纹我们用以下几种方法。
1.直进法
即每一刀都在X向进给,直至牙底处。
采用此方法加工梯形螺纹时,螺纹车刀的三个切削刃都要参与切削,导致加工排屑艰苦,切削力和切削热增长,刀头磨损严重,容易产生“扎刀”和“崩刃”现象,因此这种方法不合适大螺距螺纹的加工。
2.斜进法
螺纹车刀沿牙型一侧平行的方向斜向进刀,直至牙底处,用此方法加工梯形螺纹时,车刀始终只有一个侧刃参与切削,从而使排屑较顺利,刀尖的受热和受力情形有所改良,不易产生“扎刀”等现象。
3.交叉法
螺纹车刀分辨沿左、右牙型一侧的方向交叉进刀,直至牙底。
这种方法与斜进法较类似,利用此方法螺纹车刀的两刃都参与了切削。
以上三种方法加工时的刀具一般采用高速钢材料的刀具,粗、精车各一把刀。
在操作熟练情况下,选择提高主轴转速来进行加工,但
限制主轴转速不高于200转。
在临界螺纹终点距离时,可以用操纵压杆适度控制正转时的转速,但千万不能压得过位(以导致反转)。
粗加工时,为减小切削力,往往采用左右借刀切削法。
三、多线螺纹的分头
对车削螺纹较小的三角螺纹时可以采用导程分头或圆周分头一次完成。
原因是只有中拖板的径向进给,没有小拖板的轴向借刀,因而保证了轴向位置的精度。
而对加工较大螺距的螺纹,由于受切削力的影响,不能直接完成全部车削过程。
若采用斜进和左右进切削,就不可避免地会出现分头误差,具体措施如下:
1、多线螺纹的粗车分头
粗车时采用粗略分头。
刻线痕法;以TR36x12P6为例,用尖刀在螺纹表面对刀,后压下开合螺母在工件表面车出第一条螺旋线,然后使小滑板移动一个牙顶宽 2.2mm,再以第一刀为起点移动一个螺距,后再移动一个牙顶宽2.2mm, 刻线痕完毕。
粗车加工第一条螺旋槽时,只需把车刀移动到槽宽处,加工后的牙顶宽大于尺寸要求,同理开始粗车第二条螺旋槽,直至和第一条螺旋槽的尺寸基本相等。
2、多线螺纹的精车分头
在准备精车时,对先车某一个侧面应有所选择。
一般选择牙型较厚的开始精车,否则会对没有选择或选择错误而造成不必要的重复加工。
因此,在精车前,应对先车哪个侧面有所选择是非常必要的。
当精车好第一个牙型侧面后,要进行精确分头以保证工件螺距(或周节)的正确。
教材所讲的圆周分头和轴向分头都可以实施。
我在实操
中常采用百分表监视小拖板分头。
这样的优点是:直观、准确、操作方便,可以保证较高的分头精度。
在车第二个侧面时经过精确分头,车刀的轴向位置已确定,只要依次加深中拖板的进给深度至车削第一侧面的刻度(即螺纹小径),就获得了第二个牙型相同侧面的精度。
即通过精确分头,轴向位置确定,径向位置在第一侧面车削时的刻度不变就保证上述所谈。
不论是粗车,还是精车,首先应该选择一个侧面作为车削和测量基准,而另一侧面成为余量。
四、梯形螺纹的测量
在实操中我常用以下方法:
(1)齿轮卡尺测量法这种测量方法误差较大,适合精度较低的螺纹。
(2)三针测量法这种方法是测量外螺纹中经的一种比较精密的方法。
适用于测量一些精度要求较高、螺纹升角小于4º的螺纹工件。
测量时把三根直径相等的量针放在螺纹相对应的螺旋槽中,用千分尺量出两边量针顶点之间的距离。
例:车Tr32×12 P6梯形螺纹,用三针测量螺纹中径,求量针直径和千分尺读数值M?
量针直径dD=0.518P=3.018mm
千分尺读数值 M=d2+4.864dD-1.866P
=29+4.864×3.1-1.866×6
=29+15.08-11.20
=32.88mm
测量时应考虑公差,查表求得。
三针测量法采用的量针一般是专门制造的,在实际应用中,有时也用优质钢丝或新钻头的柄部来代替,但与计算出的量针直径尺寸往往不相符合,这就需要认真选择。
要求所代用的钢丝或钻柄直径尺寸,最大不能在放入螺旋槽时被顶在螺纹牙尖上,最小不能放入螺旋槽时和牙底相碰,可根据下表进行选用。
五、梯形多线螺纹加工注意事项:
1.车刀安装得应严格对准中心,过高或过低过高,会出现啃刀现象。
2. 调整小滑板松紧,防止车刀移动。
3.车刀两侧刀刃应平直,否则牙型不正,精车刀应保持锋利。
4.多头螺纹导程大,走刀速度快,车削时当心碰撞。
5.精车时要多次循环分头,第二次或第三次分头时,不准小滑板借刀。
由于梯形多线螺纹加工难度大,在教学中我采取老师反复讲解、多次演习的教学方法,以增加学生记忆,在实训中以学生多操作为主,加大训练力度,采取理实一体化教学,综合运用直观教学法、多媒体辅助教学,引导学生在做中学、学中做,使学生的动手能力增强,提高教学效果,达到教学目的。
现代制造技术飞跃发展,技工学校为现代制造技术提供大量的高技能人才;加强技工学校学生学习知识技能的全面性、系统性尤为重要。
参考文献:
[1]车工工艺与技能训练.中国劳动出版社.
[2]车工工艺学.中国劳动出版社.
[3]车工生产实习.劳动人民出版社.。