加氢裂化装置简介教材
第一篇_第八章_加氢裂化装置

第八章加氢裂化装置第一节概述加氢裂化装置是炼油厂中重要的二次加工手段,可获得高质量的轻质燃料油.本章是以加氢裂化装置过去所遇到的腐蚀事例和目前实际采用的防护措施为依据,对设备的防护设计提出的要求.适用于加氢裂化装置工艺设备的防抑和材料选用,也可作为炼油厂维护管理和改造设计参考。
第二节原理、流程及特点加氢裂化装置的目的是将重质油转化为轻油的一种加工手段。
其特点是对原料油的适应性强,可加工直馏重柴油、催化裂化循环油,焦化馏出油,甚至可用脱沥青重残油生产汽油、航煤和低凝固点柴油。
其次是生产方案灵活,可根据不同季节要求来改变生产方案。
再就是产品质量好,产品收率高。
加氢裂化装置的工艺流程,主要有三种类型方法:(1)一次通过法:所产尾油不循坏(图2-8-1)。
图2-8-1 加氢裂化装置流程示意图(一次通过)( 2 )部分循环法:所产尾油一部分循环,一部分排出装置,( 3 )全循环法:尾油全部循环,不排尾油(图2-8-2)。
加氢裂化装置流程简述如下:原料油经过滤、脱水后进入缓冲罐,由高压泵升压后与氢气(包括循环氢与新氢气)混合后一起进入换热器与反应生成物换热至300 ℃左右,然后进加热炉预热(另一种流程是原料油不进加热炉而只有循环氢进加热炉预热,在炉出口与换热后的原料油混合,这种流程可以减少炉管结焦),预热后从反应器顶部进入,在反应器内反应后由底部排出,经与新鲜原料、循环氢换热后再进入空冷器冷却,冷凝下来的油和不冷凝的油气和氢气进入高压分离器,油气分离,氢气从高压分离器顶部排出大部分进循环氢压缩机,反应生成油由底部排出降压后送至低压分离器,油、气再次分离,气体送燃料气管网,生成油送至分馏系统经分馏塔、汽提塔、脱丁烷塔等分馏后得到汽油、航煤、柴油等产品。
第三种流程中分馏塔底的尾油再全部循环回到加氢裂化反应器进行裂化反应。
图2-8-2 加氢裂化装置流程简图〔带循环尾油)加氢裂化装置的操作范围如下:操作温度380~450℃,操作压力8~20MPa(80~200kgf/cm),采用的催化剂含有Pt、Pd、W、Mo、Ni、Co 等金属氧化物作为加氢组分,以硅酸铝、氟化氧化铝或结晶硅铝酸盐为担体。
290万加氢裂化装置简介PPT课件

,操作岗位定员36人
10
中国石油华北石化公司
二、原料及主要产品性质
11
中国石油华北石化公司
装置原料
• 原料油:1#和2#常减压装置的直馏热蜡油以及罐 区来冷蜡油
设计冷热进料比为2:8
• 新氢:制氢装置来纯度99.9%(V)新氢
12
中国石油华北石化公司
装置产品
• 轻石脑油:至罐区作汽油调合组分 • 重石脑油:至连续重整装置作原料 • 航煤:产品送至罐区 • 精制柴油:至罐区作柴油产品调合组份 • 未转化油:至重油催化裂化装置作为原料 • 低分气:和柴油加氢精制装置、渣油加氢脱硫装
置来的低分气一起脱硫后去PSA装置进行氢气提 浓 • 含硫干气及汽提塔顶液:送至轻烃回收装置统一 处理
13
中国石油华北石化公司
原料油性质
原料名称 密度(20℃),kg/m3
硫,wt% 氮, g/g 残炭,wt% 氯, g/g Ni+V, g/g Na, g/g Fe, g/g Cu+Pb+Ca+Mg, g/g
馏程(ASTM-D1160),℃ IBP/5% 10%/30% 50%/70% 90%/95%
7
中国石油华北石化公司
装置概述
• 设计规模:290×104t/a
• 实际加工量:276.67×104t/a
• 操作弹性:60%~110%
• 年开工时数:8400小时
8
中国石油华北石化公司
装置组成
• 反应部分(包括新氢压缩机、循环氢压缩 机和循环氢脱硫设施)
• 分馏部分
• 公用工程部分
9
中国石油华北石化公司
加氢裂化说明书
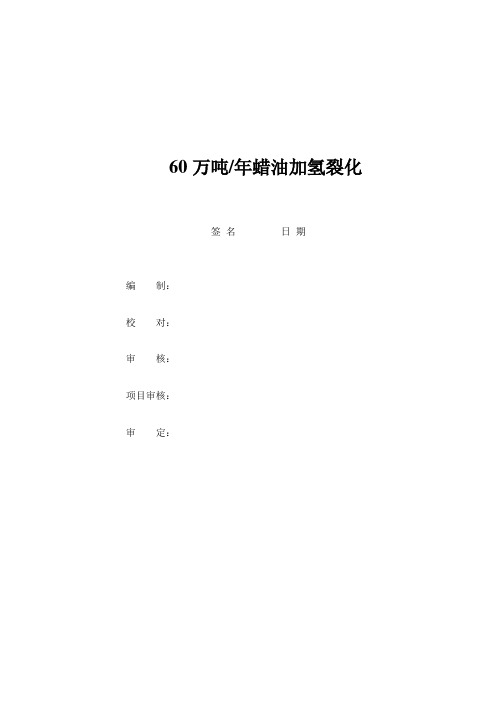
60万吨/年蜡油加氢裂化签名日期编制:校对:审核:项目审核:审定:目录1. 概述 (3)2.工艺设计技术方案 (4)3.原料、产品、催化剂和化学药剂 (5)4.物料平衡 (13)5.工艺流程简述 (15)6.主要设备选型 (20)7.消耗指标及能效 (29)8.生产控制分析 (34)9.装置定员 (37)10.环境保护 (38)11.职业安全卫生 (40)12.对外协作关系 (47)13.设计执行的主要标准目录 (49)1. 概述本项目工程内容包括厂区内新建50万吨/年润滑油基础油改质装置界区内所有工程。
1.1装置概况本装置是河北鑫海化工集团有限公司50万吨/年润滑油基础油改质装置,本装置以直馏蜡油和焦化蜡油为原料生产石脑油、柴油和尾油。
以直馏蜡油和焦化蜡油为原料生产石脑油、柴油和尾油。
装置设计兼顾全循环和一次通过两种操作方案。
1.1.1 装置规模方案一:50万吨/年,部分循环(按5%尾油);方案二:一次通过60万吨/年;操作弹性:60%~110%。
1.1.2 年开工时数本装置年开工时数为8000小时。
1.2 装置组成加氢裂化装置由反应部分(包括压缩机)、分馏部分、吸收稳定部分及公用工程部分构成。
2. 工艺设计技术方案2.1工艺技术方案采用一段串联全循环流程,兼顾一次通过生产乙烯料流程。
反应部分采用热分流程,炉前混氢工艺,设置双反应器,尾油循环至精制反应器入口。
分馏部分采用了“脱丁烷塔+分馏塔”方案,同时设置了轻烃回收设施。
这些工艺技术的优点是对原料油的适应性较强,具有较高的生产灵活性,其主产品煤油、柴油、石脑油以及尾油的产率均可进行较大幅度的调整。
该设计充分考虑了生产的灵活性,在流程设置上不仅考虑了全循环及一次通过两种工况下操作的可能性,而且进一步优化产品分馏系统的设计,提高反应产物中高价值组分的回收速率,清晰分割产品,增加经济效益。
2.2工艺技术特点(一)反应部分流程特点1)为获得低固体含量的进料,防止因系统压强过大而造成的非正常停工,原料油在进装置前应滤去直径大于50μm的颗粒。
加氢裂化装置概述
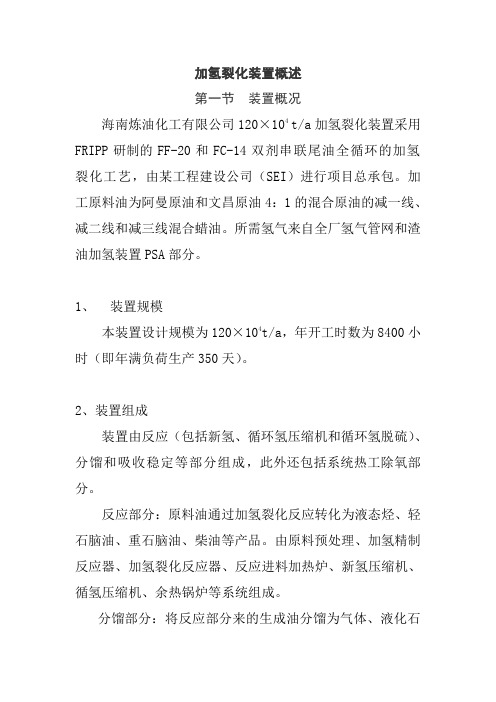
加氢裂化装置概述第一节装置概况海南炼油化工有限公司120×104 t/a加氢裂化装置采用FRIPP研制的FF-20和FC-14双剂串联尾油全循环的加氢裂化工艺,由某工程建设公司(SEI)进行项目总承包。
加工原料油为阿曼原油和文昌原油4:1的混合原油的减一线、减二线和减三线混合蜡油。
所需氢气来自全厂氢气管网和渣油加氢装置PSA部分。
1、装置规模本装置设计规模为120×104t/a,年开工时数为8400小时(即年满负荷生产350天)。
2、装置组成装置由反应(包括新氢、循环氢压缩机和循环氢脱硫)、分馏和吸收稳定等部分组成,此外还包括系统热工除氧部分。
反应部分:原料油通过加氢裂化反应转化为液态烃、轻石脑油、重石脑油、柴油等产品。
由原料预处理、加氢精制反应器、加氢裂化反应器、反应进料加热炉、新氢压缩机、循氢压缩机、余热锅炉等系统组成。
分馏部分:将反应部分来的生成油分馏为气体、液化石油气、轻石脑油、重石脑油、柴油及尾油(未转化油)等产品。
由脱硫化氢塔、产品分馏塔、柴油汽提塔、石脑油分馏塔、吸收脱吸塔和石脑油稳定塔等组成。
3、装置技术特点本装置采用双剂串联尾油全循环的加氢裂化工艺。
反应部分采用国内成熟的炉前混氢方案;分馏部分采用脱硫化氢塔+常压塔出柴油方案,采用分馏进料加热炉;吸收稳定部分采用重石脑油作吸收剂的方案;循环氢脱硫部分采用MDEA作脱硫剂的方案;催化剂的硫化采用干法硫化;催化剂的钝化采用低氮油注氨的钝化方案;催化剂再生采用器外再生方案。
4、装置主要设备本装置共有设备约166台(套),其中:反应器2台加热炉3座塔器7台容器23台换热器24台空冷器34片压缩机4台泵38台过滤器1套其它小型设备30台装置主要设备一览表见规程后附表。
5、装置占地加氢裂化装置的总面积为11016.75m2。
装置内除生产设备外,还设有高、低压配电室。
DCS、ITCC 和SIS机柜室与渣油加氢装置共用。
第二节原料和产品一、原料加工的原料油为阿曼油和文昌油4:1的混合原油的减一线(355~390℃)、减二线(390~440℃)和减三线(440~520℃)混合而成。
培训竞赛优秀课件13-4:加氢裂化装置__中化泉州项目部

图5 循环氢压缩机
北京华夏石化工程监理有限公司
BEIJING HUAXIA SUPERVISION CO., LTD
图6
新氢压缩机
北京华夏石化工程监理有限公司
BEIJING HUAXIA SUPERVISION CO., LTD
图7
反应进料泵(带液力透平日产)
北京华夏石化工程监理有限公司
BEIJING HUAXIA SUPERVISION CO., LTD
图8
高压注水泵(美国产)
北京华夏石化工程监理有限公司
BEIJING HUAXIA SUPERVISION CO., LTD
3.安装中应注意的问题 1) 高温管道和管件必须采用合金钢或不锈钢材质,其管材、管件、阀门 、法兰和螺栓等必须做好标示,以免用错。安装后要求做符合性检验 。 2)检查高压设备和管道的法兰密封槽和八角垫外观检查和接触面积检查 ,安装后(新氢压缩机试运合格后)用氮气和氢气进行严密性试验。 如发现问题要由厂家解决。 3)新氢压缩机是现场组装设备,功率大,振动大;循环氢压缩机和汽轮 机是高速转动机械。其水平度和同轴度等安装精度要求高,尤其是轴 对中要求采用三表找正法,并且应按照厂家提供的冷态找正曲线进行 找正。
北京华夏石化工程监理有限公司
BEIJING HUAXIA SUPERVISION CO., LTD
4)新氢压缩机采用干气密封, 由厂家负责安装,安装前由施 工单位负责将轴头和压缩机各 通气孔和管路用丙酮脱脂处理 干净。
图12 干气密封安装前要求脱脂处理
图13
干气密封安装完成
北京华夏石化工程监理有限公司
北京华夏石化工程监理有限公司
BEIJING HUAXIA SUPERVISION CO., LTD
第八章加氢裂化装置
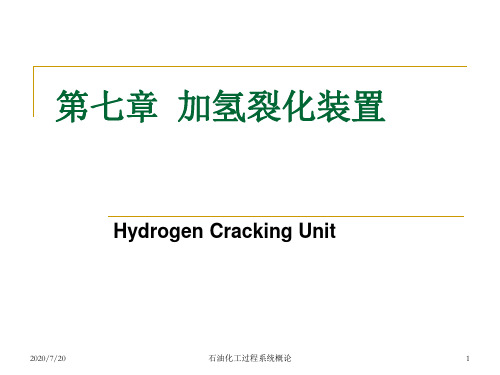
2020/7/20
3
石油化工过程系统概论
第一节 工作原理、工艺流程及特点
2020/7/20
4
石油化工过程系统概论
一、加氢裂化装置的特点 1.对原料油的适应性强,可加工直馏重柴油、催化
裂化循环油,焦化馏出油,甚至可用脱沥青重残 油生产汽油、航空煤油和低凝固点柴油; 2.生产方案灵活,可根据不同季节要求来改变生产 方案; 3.产品质量好,轻质油收率高。
2020/7/20
17
石油化工过程系统概论
(二)沸腾床加氢裂化
沸腾床(又称膨胀床)工艺是借助于流体流速带动具 有一定颗粒度的催化剂运动,形成气、液、固三相床 层,从而使氢气、原料油和催化剂充分接触而完成加 氢反应过程。
沸腾床工艺可以处理金属含量和残炭值较高的原 料(如减压渣油),并可使重油深度转化;但反应温度 较高,一般在400~450℃范围内。
2020/7/20
14
石油化工过程系统概论
图1-7-1 加氢裂化装置流程示意图
此流程属于什么加氢裂化工艺流程?
简述其工艺流程
2020/7/20
15
石油化工过程系统概论
图1-7-2 加氢裂化装置流程简图
2020/7/20
16
石油化工过程系统概论
加氢裂化装置的工艺流程
原料油经过滤、脱水后进入缓冲罐,由高压泵升压后与氢气(包括 循环氢与新氢气)混合后一起进入换热器与反应生成物换热至 300℃左右,然后进加热炉预热(另一种流程是原料油不进加热炉 而只有循环氢进加热炉预热,在炉出口与换热后的原料油混合, 这种流程可以减少炉管结焦),预热后从反应器顶部进入,在反应 器内反应后由底部排出,经与新鲜原料、循环氢换热后再进入空 冷器冷却,冷凝下来的油和不冷凝的油气和氢气进入高压分离器, 油气分离,氢气从高压分离器顶部排出,大部分进循环氢压缩机, 反应生成油由底部排出,降压后送至低压分离器,油、气再次分 离,气体送燃料气管网,生成油送至分馏系统经分馏塔、汽提塔、 脱丁烷塔等分馏后得到汽油、航空煤油、柴油等产品。第三种流 程中分馏塔底的尾油再全部循环回到加氢裂化反应器进行裂化反 应。
加氢裂化设备基础知识ppt课件
设计方法 过去一般采用的“规则设 计”即“常规设计”的方法(GB150等) ,它是以弹性失效准则为理论基础,采用第 一强度理论,用第一主应力为控制应力。 现在逐步发展到采用以“应力分析为基础 的设计”,即“分析设计”的方法,采用 最大剪应力为控制作用的第三强度理论, 按照JB4732-95《钢制压力容器-分析设计 标准》进行设计。 “分析设计”要求对容 器的有关部位
19
20
◆反应器支撑结构
为了改善反应器裙座支撑部位的应力状 况和为使裙座连接处焊缝在制造与使用过程 检修时能够进行超声和射线检测,将此处的 结构由过去的图-3(a)的形式改进为图-3( b)的形式。
21
( 过去的结构
( 新的结构
图-3 催化剂支持结构的改进
22
◆改善裙座连接处应力水平的结构 设计
42
2.氢的来源
金属在冶炼、焊接、酸洗、电镀等生 产加工过程中都会吸收氢,因此都要加以严 格控制,但这不属于本文讨论的范畴。本文 所关心的是金属设备在使用过程中与含氢介 质相接触时所吸收的氢。氢必须首先在金属 表面成为活性氢原子,然后才能扩散进入金 属。活性氢原子的来源主要是通过以下三种 途径:
43
9
的应力进行详细计算及按应力的性质进 行分类,并对各类应力及其组合进行评 价,同时对材料、制造、检验也提出了 比“常规设计”更高的要求,该设计方 法先进、严格,从而提高了设计的准确 性与使用的可靠性,设备重量减轻,投 资节省,它是容器设计观点和方法的一 个飞跃。
10
结构型式 反应器本体经历了由单层到 多层的阶段,后来由于冶金、锻造等技术的 进步,单层锻造结构或厚板卷焊结构的反应 器又逐渐占了统治地位。从使用状态下其高 温介质是否直接与器壁接触来看,又分为热 壁结构和冷壁结构。为了易于解决反应器用 材的耐氢腐蚀和硫化氢腐蚀等问题,在反应 器内表面衬非金属隔热衬里结构或通以温度 不高的氢气以达到保护反应器不直接受高温 高压氢腐蚀的另一种带“瓶衬”的结构称为 冷壁结构;反之称为热壁结构。
第八章__加氢裂化装置课件
2019/11/20
炼油装备技术
6
西南石油大学
按反应器中催化剂所处的状态不同,可分为固定 床、沸腾床和悬浮床等几种型式。 根据原料和产品目的不同,还可细分出很多种型 式,如:馏分油加氢裂化、渣油加氢裂化以及单 段流程、一段串联流程和两段流程加氢裂化等等。 按尾油循环方式不同可分为一次通过法、部分循 环法和全循环法。
2019/11/20
炼油装备技术
3
西南石油大学
第一节 工作原理、工艺 流程及特点
2019/11/20
炼油装备技术
4
西南石油大学
一、加氢裂化装置的特点
加氢裂化装置是将重质油转化为轻质油的一 种加工手段,其特点是: 1.对原料油的适应性强,可加工直馏重柴油、催化 裂化循环油,焦化馏出油,甚至可用脱沥青重残 油生产汽油、航空煤油和低凝固点柴油; 2.生产方案灵活,可根据不同季节要求来改变生产 方案; 3.产品质量好,轻质油收率高。
2019/11/20
炼油装备技术
27
西南石油大学
3.去垢篮筐
在加氢反应器的顶部催 化剂床层上有时设有去垢篮 筐,与床层上的磁球一起对 进入反应器的介质进行过滤。
去垢篮一般均匀地布置 在床层上表面,篮筐周围充 填适量的大颗粒瓷球,以增 加透气性。
2019/11/20
炼油装备技术
28
西南石油大学
4.催化剂支撑盘
反应器筒体分为冷壁筒 和热壁筒两种。
2019/11/20
炼油装备技术
23
西南石油大学
(二)加氢反应器内件
加氢反应是在高温高压及有腐蚀介质(H2、H2S) 的条件下操作,除了在材质上要注意防止氢腐蚀及其 他介质的腐蚀以外,加氢反应器还应保证: 反应物(油气和氢)在反应器中分布均匀,保证反应物 与催化剂有良好的接触; 及时排除反应热,避免反应温度过高和催化剂过 热.以保证最佳反应条件和延长催化剂寿命; 在反应物均匀分布的前提下,反应器内部的压力降不 致过大,以减少循环压缩机的负荷,节省能源。
加氢裂化装置课件
10/22/2023
8
石油化工过程系统概论
根据原料及目的产品的不同,固定床加氢裂 化大致分为下列几种流程。
1.单段加氢裂化流程 单段加氢裂化流程中只有一个反应器,原料油
加氢精制和加氢裂化在同一反应器内进行。反应 器上部为精制段,下部为裂化段。
10/22/2023
29
石油化工过程系统概论
有些设计自催化剂支持盘到 再分配盘之间设置几个连通 管,卸催化剂只要打开底封 头上的卸料口,就可以卸出 全部催化剂。
10/22/2023
30
石油化工过程系统概论
本章重点
1.加氢裂化的作用是什么? 2.加氢裂化有哪些特点? 3.加氢裂化如何分类? 4.根据介质是否直接接触金属器壁,高压加氢
10/22/2023
11
石油化工过程系统概论
2.两段加氢裂化流程 两段加氢裂化流程中有两个反应器,分别装
有不同性能的催化剂。
第一个反应器中主要进行原料油的精制; 第二个反应器中主要进行加氢裂化反应,形成 独立的两段流程体系。
10/22/2023
12
石油化工过程系统概论
汽提塔的作用:脱去NH3和H2S以及残留在油 中的气体。
10/22/2023
7
石油化工过程系统概论
(一)固定床加氢裂化 固定床是指将颗粒状的催化剂放置在反应器内,
形成静态催化剂床层。原料油和氢气经升温、升 压达到反应条件后进入反应系统,先进行加氢精 制以除去硫、氮、氧杂质和二烯烃,再进行加氢 裂化反应。反应产物经降温、分离、降压和分馏 后,目的产品送出装置,分离出含氢较高(80%、 90%)的气体,作为循环氢使用。
加氢裂化装置说明、危险因素及防范措施实用版
YF-ED-J1551可按资料类型定义编号加氢裂化装置说明、危险因素及防范措施实用版In Order To Ensure The Effective And Safe Operation Of The Department Work Or Production, Relevant Personnel Shall Follow The Procedures In Handling Business Or Operating Equipment.(示范文稿)二零XX年XX月XX日加氢裂化装置说明、危险因素及防范措施实用版提示:该解决方案文档适合使用于从目的、要求、方式、方法、进度等都部署具体、周密,并有很强可操作性的计划,在进行中紧扣进度,实现最大程度完成与接近最初目标。
下载后可以对文件进行定制修改,请根据实际需要调整使用。
一、装置简介(一)装置的发展及类型1.加氢装置的发展加氢是指石油馏分在氢气及催化剂作用下发生化学反应的加工过程,加氢过程可分为加氢精制、加氢裂化、临氢降凝、加氢异构化等,下面重点介绍加氢裂化加工过程。
加氢技术最早起源于20世纪20年代德国的煤和煤焦油加氢技术,第二次世界大战以后,随着对轻质油数量及质量的要求增加和提高,重质馏分油的加氢裂化技术得到了迅速发展。
1959年美国谢夫隆公司开发出了Isocrosking加氢裂化技术,其后不久环球油品公司开发出了Lomax加氢裂化技术,联合油公司开发出了Uicraking加氢裂化技术。
加氢裂化技术在世界范围内得到了迅速发展。
早在20世纪50年代,我国就已经对加氢技术进行了研究和开发,早期主要进行页岩油的加氢技术开发,60年代以后,随着大庆、胜利油田的相继发现,石油馏分油的加氢技术得到了迅速发展,1966年我国建成了第一套4000kt/a的加氢裂化装置。
进入20世纪90年代以后,国内开发的中压加氢裂化及中压加氢改质技术也得到了应用和发展。
2.装置的主要类型加氢装置按加工目的可分为:加氢精制、加氢裂化、渣油加氢处理等类型,这里主要介绍加氢裂化装置。
- 1、下载文档前请自行甄别文档内容的完整性,平台不提供额外的编辑、内容补充、找答案等附加服务。
- 2、"仅部分预览"的文档,不可在线预览部分如存在完整性等问题,可反馈申请退款(可完整预览的文档不适用该条件!)。
- 3、如文档侵犯您的权益,请联系客服反馈,我们会尽快为您处理(人工客服工作时间:9:00-18:30)。
加氢裂化主催化剂性质
物化性质 孔容/mL/g 表面积/m2/g 堆密度/ g/100ml 压碎强度/ N/mm 烧减,mt% 磨耗,mt% 形状 条长/mm 直径/mm
3936 0.32-0.38 >160 88-94 >25 <2.0 <1.0 三叶草 3-8 1.2-1.4
ZHC-01 0.30-0.35 ≥240 96-102 >14.7 <3.0 柱状 3-8 1.5-1.7
加氢裂化装置概述 设计的原料组成为131.2万t/a中东高硫蜡油和8.8万t/a胜利 焦化蜡油,中试评价采用沙轻VGO:沙中VGO:科威特 VGO=46:8:46的混合油。所需H2 为联合布局的连续重整装 置和乙烯裂解装置产生的氢气经本装置PSA部分提纯至纯度 99.9% ,不足部分由制氢装置补充。2001年4月氢气流程动改 后,在连续重整装置停工的情况下,可由第二化肥厂天然气制 氢供给氢气。装置建设规模为140万t/a(175t/h),装置设计 运转周期为8000h(11个月)。 装置由反应、分馏、吸收稳定、气体脱硫、溶剂再生和氢 气提纯(PSA)等部分组成。 主要产品是液化气、石脑油、航煤、柴油和尾油,同时副 产部分气体。设计的转化率为60%,其中尾油做乙烯裂解的原 料。
加氢裂化装置主要影响因素
• 反应压力 反应压力是通过冷高分压力来控制的, 为使反应向有利于加氢裂化的方向进行, 应使反应系统维持尽可能高的氢分压,因 此冷高分应在尽可能高的压力下操作。考 虑到冷高分的设计压力,冷高分操作压力 不能超过16.3MPa。
加氢裂化装置流程说明
1.反应部分 2.分馏部分 3.吸收稳定部分 4.脱硫部分
2.加氢裂化反应器(R-402)共有四个床层,催化剂 装填数据见附表。ZHC-01为加氢裂化主催化剂,属 无定型类催化剂,含有一定量的分子筛。因此,其裂 化活性没有分子筛型的强,反应缓和,起始温度较高。 ZTS-3是后精制催化剂,用来饱和裂化反应产生的少 量不饱和烃。
加氢裂化装置催化剂装填数据
• 反应器R401共计装入抚顺研究院产的精制催化剂 3936 167.55吨,保护剂CEN-2 4.675吨,保护剂 FZC-16 7.8吨。3936设计装填密度0.8 t/m3,实 际装填密度0.78 t/m3,FZC-16装填密度0.69 t/m3, CEN-02装填密度0.42 t/m3。具体装填数据见附 表。 • 反应器R402共计装入齐鲁第一化肥厂生产的抚顺 研究院研制的裂化催化剂ZHC-01 162.96吨,后 精制催化剂ZTS-03 12.99吨。ZHC-01设计装填 密度0.88 t/m3,实际装填密度0.89 t/m3,ZTS03设计装填密度0.82 t/m3,实际装填密度0.88 t/m3。
加氢裂化装置主要影响因素
•原料性质的影响 不同的原料性质对加氢裂化操作有显著的影响,原料的馏 程、氮含量、硫含量、沥青质和金属含量、多环指数等都会 影响到反应转化率、催化剂的活性及产品质量。 •氢气的影响 补充氢的纯度、系统氢分压、循环气流量、循环气氢纯度 等都会对加氢裂化的操作产生显著的影响。 •反应温度 通过调整反应温度,可以达到所要求的产品转化率、脱 硫率和脱氮率。反应温度也会影响到航煤和柴油产品的质量, 在相同的转化率时,高的催化剂温度将导致航煤烟点下降和 柴油十六烷值降低。催化剂温度由调节反应器入口温度,以 及在床层间注入的冷氢量来控制,以达到所有催化剂床层有 基本相同的平均温度。
加氢裂化主催化剂性质
物化性质
MoO3
NiO P WO3
3936
21.73
4.02 2.55
ZHC-01
m%
m% m% m%
8.5~9.5
21.5~23.5
加氢裂化装置保护剂性质 物化性质
孔容/mL/g 表面积/m2/g
CEN-2
1.05-1.35 110 - 165
FZC-16
>0.48 140-180
140万吨加氢裂化装置简介
二00七年八月
加氢裂化装置概述
140万t/a加氢裂化装置,是齐鲁石化公司加工 进口原油改扩建工程的重点项目,本装置与60万t/a 连续重整装置联合布局,由抚顺石油化工科学研究 院提供工艺试验中试报告,由中国石化北京设计院 设计,齐鲁胜利炼油设计院负责系统配套,大部分 设备由国内制造,中石化集团公司第十建设工程公 司负责施工安装。装置于1998年3月31日开工建设, 2000年11月23日实现中间交接,2001年3月5日产 品合格,实现装置一次开汽成功。
加氢裂化装置设计特点
• • • 采用抚顺石油化工研究院开发的3936和ZHC-01催化剂两 段串联一次通过加氢裂化工艺。 反应部分采用国内外成熟的炉前混氢流程,操作方便,流 程简化,传热效率高。 精制反应器与裂化反应器之间设置混氢油与精制反应产物 换热器,回收热量,减少冷氢用量。 采用热进料热高分流程,既降低能耗,又节省换热面积。 选用了PALL自动气体反吹原料过滤器。 对催化剂预硫化采用干法预硫化流程,催化剂活性高,预 硫化期间加热炉负荷少,预硫化所需时间短。 对催化剂钝化选用低氮油注氨的钝化方案。 大机组、高压泵、高压设备大部分国产化。
• • •
• •
加氢油化工科学研究院开发的 两段双剂串联一次通过固定床的加氢裂化工艺。本装 置以二常、三常切出的减压瓦斯油和焦化蜡油为原料, 在催化剂作用下进行加氢脱蜡、脱氮、裂解、烯烃和 芳烃饱和、脱除氧化物和金属等反应。所用的加氢精 制催化剂为3936,加氢裂化催化剂为ZHC-01。原料 油经加氢反应后有60%(w)转化为轻质油品。加氢 生成油经常压分馏切割出石脑油、航煤、柴油和未转 化油(尾油)。
堆密度/ g/ml 压碎强度/ N/mm 磨耗,mt% 形状 直径/mm NiO Wt% K Wt/%
0.41-0.46 >30 <0.8 椭球 长轴4.3-5.5,短 轴
1.9-2.9
0.70-0.80 >30 <0.8 球形 2.2-3.2 0.2
加氢裂化装置催化剂作用 1.加氢精制反应器(R-401)共有四个床层,催化剂 装填数据见附表。其中CEN-2、FZC-16为保护催化 剂,其颗粒和微孔较大,容垢能力强,具有良好的脱 金属能力,从而保护主催化剂的活性和稳定性。3936 为加氢精制主催化剂,具有较强的脱硫脱氮能力。