磁控溅射、反应溅射与中频溅射
真空蒸发镀膜 1、真空蒸发镀膜原理 真空镀膜按其技术种类可分成以下
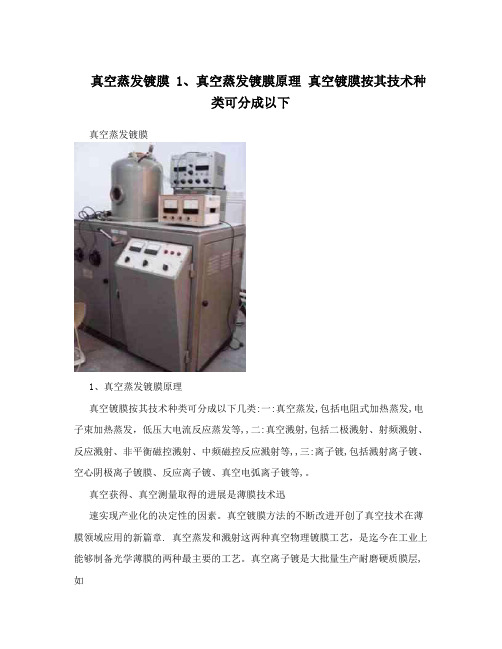
真空蒸发镀膜 1、真空蒸发镀膜原理真空镀膜按其技术种类可分成以下真空蒸发镀膜1、真空蒸发镀膜原理真空镀膜按其技术种类可分成以下几类:一:真空蒸发,包括电阻式加热蒸发,电子束加热蒸发,低压大电流反应蒸发等,,二:真空溅射,包括二极溅射、射频溅射、反应溅射、非平衡磁控溅射、中频磁控反应溅射等,,三:离子镀,包括溅射离子镀、空心阴极离子镀膜、反应离子镀、真空电弧离子镀等,。
真空获得、真空测量取得的进展是薄膜技术迅速实现产业化的决定性的因素。
真空镀膜方法的不断改进开创了真空技术在薄膜领域应用的新篇章. 真空蒸发和溅射这两种真空物理镀膜工艺,是迄今在工业上能够制备光学薄膜的两种最主要的工艺。
真空离子镀是大批量生产耐磨硬质膜层,如机械泵TiC,TiN等,的主要的工艺,在油扩散泵---抽气系统出现之后,它们才获得大规模地应用。
真空蒸发镀膜的原理是:先将镀膜室内的气体-2抽到10Pa以下的压强,通过加热蒸发源使臵于蒸发源中的物质蒸发,蒸汽的原子或分子从蒸发源表面逸出,沉积到基片上凝结后形成薄膜,它包括抽气,蒸发,沉积等基本过程。
真空环境是镀膜的首要条件:,1,可防止在高温下因空气分子和蒸发源发生反应,而使蒸发源劣化,,2,可防止蒸汽原子或分子在沉积到基片上的途中和空气分子碰撞而阻碍蒸汽原子或分子直接到达基片表面,以及由于蒸汽原子、分子间的相互碰撞而在到达基片表面前就凝聚,或在途中就生成其它化合物,,3,可防止在形成薄膜的过程中,空气分子作为杂质混入膜内或在膜中形成其它化合物。
真空蒸发镀膜常用的蒸发源有电阻式加热蒸发源、电子束加热蒸发源、激光加热蒸发源、空心热阴极等离子束加热蒸发源、感应式加热蒸发源等。
在高真空或超高真空下,用电阻、高频、电子束、激光等加热技术,在玻璃、塑料、和金属等基体上可蒸发沉积100多种金属、半导体、和化合物薄膜。
其中,电子束反应蒸发制备多层光学薄膜是一种方便有效的手段,在批量化生产中已被普遍采用,其优点是:电子束加热温度可达3500?左右,蒸发材料基本上不受限制,即使钨和钼也可蒸镀,蒸发速率高,100,750000 Å/s,,而且蒸发速率和电子束聚集调节方便,通过对蒸发材料的局部熔化或坩埚水冷,蒸发材料不与坩埚发生反应,保证了膜料的高纯度。
溅射

关于溅射发布时间:2010-4-28溅射一、溅射的基本内容:1、定义:所谓溅射,就是这充满腔室的工艺气体在高电压的作用下,形成气体等离子体(辉光放电),其中的阳离子在电场力作用下高速向靶材冲击,阳离子和靶材进行能量交换,使靶材原子获得足够的能量从靶材表面逸出(其中逸出的还可能包含靶材离子)。
这一整个的动力学过程,就叫做溅射。
入射离子轰击靶面时,将其部分能量传输给表层晶格原子,引起靶材中原子的运动。
有的原子获得能量后从晶格处移位,并克服了表面势垒直接发生溅射;有的不能脱离晶格的束缚,只能在原位做振动并波及周围原子,结果使靶的温度升高;而有的原子获得足够大的能量后产生一次反冲,将其临近的原子碰撞移位,反冲继续下去产生高次反冲,这一过程称为级联碰撞。
级联碰撞的结果是部分原子达到表面,克服势垒逸出,这就形成了级联溅射,这就是溅射机理。
当级联碰撞范围内反冲原子密度不高时,动态反冲原子彼此间的碰撞可以忽略,这就是线性级联碰撞2、溅射的四要素:①:靶材物质②:电磁场③:底物④:一整套完整配备的镀膜设备3、溅射收益:3.1、离子每一次撞击靶材时,靶材所释放出的靶材原子。
3.2、影响溅射收益的因素:①:等离子体中离子动能②:入射离子的入射角度3.3、最大溅射收益的决定因素:①:入射角度在45°-50°左右②:取决于靶材物质3.4、入射角度的影响因素①:由电场决定②:靶材表面于入射源的相对角度4、溅射率:4.1、定义:每单位时间内靶材物质所释放出的原子个数4.2、溅射率的影响因素①:离子动能(取决于电源电压和气体压力)②:等离子密度(取决于气体压力和电流)4.3、统计学公式:Rs(统计学)=d/t。
注:溅射原子溢出角度大部分在0~10度之间,因此在腔室内所有区域都可能被镀上一层膜,久之会产生污染。
所以真空溅射腔室内必须进行定期清洁。
二、溅射种类:1、反应溅射:氧化物,氮化物作为沉积物质现象:①:靶材分子分裂,其于工艺气体离子发生反应,形成化合物②:膜层性能改变③:靶材有可能中毒2、二极溅射(见下图):二极溅射是一种经典的标准溅射技术,其中等离子体和电子均只沿着电场方向运动。
磁控溅射技术及其应用

•
•
•
三、磁控溅射镀膜技术发展
3、反应磁控溅射技术
• 靶中毒:迟滞现象使反应气体与靶材作用生成的化合物覆盖在靶材表面,积 累大量的正电荷无法中和,在靶材表面建立越来越高的正电位,阴极位降区 的电位随之降低,最终阴极位降区电位降减小到零,放电熄灭,溅射停止, 这种现象称为靶中毒。 • 打弧:当靶材表面化合物层电位足够高时,进而发生击穿,巨大的电流流过 击穿点,形成弧光放电,导致局部靶面瞬间被加热到很高的温度,发生喷射
可以制备成靶材。磁控溅射镀膜在相互垂直的磁场和电场的双重作用
下,沉积速度快,膜层致密且与基片附着性好,非常适合于大批量且高 效率的工业化生产。
二、磁控溅射镀膜技术原理
2、磁控溅射技术
• 磁控溅射的工作原理是在辉光放电 的两极之间引入磁场,电子受电场 加速作用的同时受到磁场的束缚作 用,运动轨迹成摆线,增加了电子
三、磁控溅射镀膜技术发展
5、脉冲磁控溅射技术
• 脉冲磁控溅射是采用矩形波电压的脉冲电源
代替传统直流电源进行磁控溅射沉积。脉冲
磁控溅射技术可以有效的抑制电弧产生进而 消除由此产生的薄膜缺陷,同时可以提高溅 射沉积速率,降低沉积温度等一系列显著优
点。
• 脉冲可分为双向脉冲和单向脉冲。双向脉冲 在一个周期内存在正电压和负电压两个阶段 ,在负电压段,电源工作于靶材的溅射,正
射的同时,阳极靶完成表面清洁,
如此周期性地变换磁控靶极性,就 产生了“自清洁”效应。
四、磁控溅射镀膜技术的发展
6、磁控溅射新发展
•
高速溅射:高速溅射能够实现高速率沉积,可以缩短溅射镀膜的时间,提高 工业生产的效率;有可能替代目前对环境有污染的电镀工艺。
•
自溅射:当溅射率非常高,以至于在完全没有惰性气体的情况下也能维持放 电,即是仅用离化的被溅射材料的蒸汽来维持放电,这种磁控溅射被称为自 溅射。被溅射材料的离子化以及减少甚至取消惰性气体,会明显地影响薄膜 形成的机制,加强沉积薄膜过程中合金化和化合物形成中的化学反应。由此 可能制备出新的薄膜材料,发展新的溅射技术,例如在深孔底部自溅射沉积 薄膜。
薄膜的制备及其特性测试

图1 双靶反应磁控溅射原理图 如图,双靶法同时安装两块靶材互为阴阳极进行轮回溅射镀膜 如图,
1.4、射频反应磁控溅射 1.4、
在一定气压下,在阴阳极之间施加交流电压,当其频率 增高到射频频率时即可产生稳定的射频辉光放电。射频辉光 放电在辉光放电空间中电子震荡足以产生电离碰撞的能量, 所以减小了放电对二次电子的依赖,并且能有效降低击穿电 压。射频电压可以穿过任何种类的阻抗,所以电极就不再要 求是导电体,可以溅射任何材料,因此射频辉光放电广泛用 于介质的溅射。频率在5~30MHz都称为射频频率。
透光率是透明薄膜的一项非常重要的光学性能指标, 透光率是透明薄膜的一项非常重要的光学性能指标,透光 率是指以透过材料的光通量与入射的光通量之比的百分数表示, 率是指以透过材料的光通量与入射的光通量之比的百分数表示,在 测试中采用相对测量原理,将通过透明薄膜的光通量记为T2 T2, 测试中采用相对测量原理,将通过透明薄膜的光通量记为T2,在没 有放入透明薄膜的光通量记为T1 那么薄膜的透光率为: T1, 有放入透明薄膜的光通量记为T1,那么薄膜的透光率为: Tt =T2/T1⊆ 其中,T1,T2均为测量相对值 均为测量相对值) =T2/T1⊆100% (其中,T1,T2均为测量相对值) 一般用来测量透过率的仪器有透过率雾度测试仪和分光光 度计法, 度计法,其原理图分别如下
1.5、化学气相沉积(CVD)法 (CVD) 1.5、化学气相沉积(CVD)法
化学气相沉积是一种化学气相生长法,简称CVD(Chemical V apor Deposition)技术。这种技术是把含有构成薄膜元素的一种 或几种化合物质气体供给基片,利用加热等离子体、紫外光乃至 激光等能源,借助气体在基片表面的化学反应(热分解或化学合 成)生成要求的薄膜。例如下图是利用化学气相沉淀法制备ITO的 原理结构图
3.1磁控溅射

原理示意图
磁控溅射镀膜是指将涂层材料做为靶阴极,利用氩离子轰击靶材, 产生阴极溅射,把靶材原子溅射到工件上形成沉积层的一种镀膜技 术。
二、溅射装置
直流溅射(DC sputtering)
1.阴极(靶) 2.阳极(基片) 3.真空室 4.进气口 5.真空抽气系 统 6.高压电源 (DC)
距离与速度及附着力
• 为了得到最大的沉积速率并提高膜层的附着力,在保证不会破
坏辉光放电自身的前提下基片应当尽可能放置在离阴极最近的 地方。溅射粒子和气体分子(及离子)的平均自由程也会在其中发 挥作用。当增加基片与阴极之间的距离,碰撞的几率也会增加, 这样溅射粒子到达基片时所具有的能力就会减少。所以,为了 得到最大的沉积速率和最好的附着力,基片必须尽可能地放置 在靠近阴极的位置上
气体压强
将气体压强降低到某一点可以提高离子的平均自由程、进而使更 多的离子具有足够的能量去撞击阴极以便将粒子轰击出来,也就 是提高溅射速率。超过该点之后,由于参与碰撞的分子过少则会 导致离化量减少,使得溅射速率发生下降。如果气压过低,等离 子体就会熄灭同时溅射停止。提高气体压强可提高离化率,但是 也就降低了溅射原子的平均自由程,这也可以降低溅射速率。能 够得到最大沉积速率的气体压强范围非常狭窄。如果进行的是反 应溅射,由于它会不断消耗,所以为了维持均匀的沉积速率,必 须按照适当的速度补充新的反应气体。
系统参数
工艺会受到很多参数的影响。其中些是可以在工艺运行期间改变 和控制的;而另外一些则虽然是固定的,但是一般在工艺运行前 可以在一定范围内进行控制。两个重要的固定参数是:靶结构和 磁场。
靶结构
每个单独的靶都具有其自身的内部结构和颗粒方向。由于内部结构的不同,两 个看起来完全相同的靶材可能会出现迥然不同的溅射速率。在镀膜操作中,如 果采用了新的或不同的靶,应当特别注意这一点。如果所有的靶材块在加工期 间具有相似的结构,调节电源,根据需要提高或降低功率可以对它进行补偿。 在一套靶中,由于颗粒结构不同,也会产生不同的溅射速率。加工过程会造成 靶材内部结构的差异,所以即使是相同合金成分的靶材也会存在溅射速率的差 异因
磁控溅射
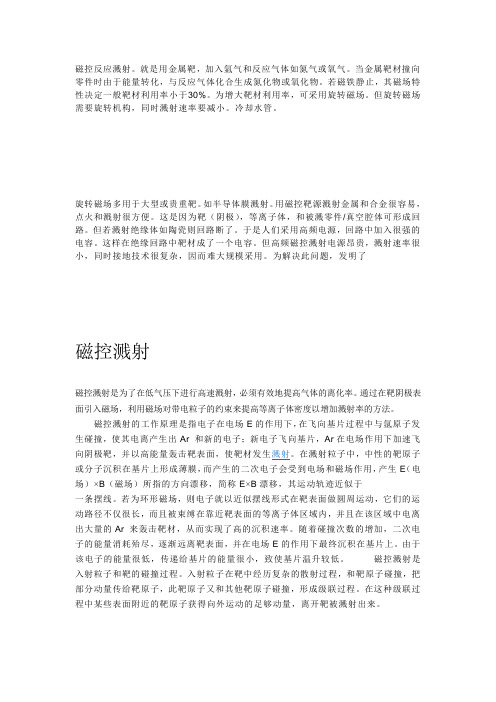
磁控反应溅射。
就是用金属靶,加入氩气和反应气体如氮气或氧气。
当金属靶材撞向零件时由于能量转化,与反应气体化合生成氮化物或氧化物。
若磁铁静止,其磁场特性决定一般靶材利用率小于30%。
为增大靶材利用率,可采用旋转磁场。
但旋转磁场需要旋转机构,同时溅射速率要减小。
冷却水管。
旋转磁场多用于大型或贵重靶。
如半导体膜溅射。
用磁控靶源溅射金属和合金很容易,点火和溅射很方便。
这是因为靶(阴极),等离子体,和被溅零件/真空腔体可形成回路。
但若溅射绝缘体如陶瓷则回路断了。
于是人们采用高频电源,回路中加入很强的电容。
这样在绝缘回路中靶材成了一个电容。
但高频磁控溅射电源昂贵,溅射速率很小,同时接地技术很复杂,因而难大规模采用。
为解决此问题,发明了磁控溅射磁控溅射是为了在低气压下进行高速溅射,必须有效地提高气体的离化率。
通过在靶阴极表面引入磁场,利用磁场对带电粒子的约束来提高等离子体密度以增加溅射率的方法。
磁控溅射的工作原理是指电子在电场E的作用下,在飞向基片过程中与氩原子发生碰撞,使其电离产生出Ar 和新的电子;新电子飞向基片,Ar在电场作用下加速飞向阴极靶,并以高能量轰击靶表面,使靶材发生溅射。
在溅射粒子中,中性的靶原子或分子沉积在基片上形成薄膜,而产生的二次电子会受到电场和磁场作用,产生E(电场)×B(磁场)所指的方向漂移,简称E×B漂移,其运动轨迹近似于一条摆线。
若为环形磁场,则电子就以近似摆线形式在靶表面做圆周运动,它们的运动路径不仅很长,而且被束缚在靠近靶表面的等离子体区域内,并且在该区域中电离出大量的Ar 来轰击靶材,从而实现了高的沉积速率。
随着碰撞次数的增加,二次电子的能量消耗殆尽,逐渐远离靶表面,并在电场E的作用下最终沉积在基片上。
由于该电子的能量很低,传递给基片的能量很小,致使基片温升较低。
磁控溅射是入射粒子和靶的碰撞过程。
入射粒子在靶中经历复杂的散射过程,和靶原子碰撞,把部分动量传给靶原子,此靶原子又和其他靶原子碰撞,形成级联过程。
磁控溅射镀膜原理及工艺

磁控溅射镀膜原理及工艺摘要:真空镀膜技术作为一种产生特定膜层的技术,在现实生产生活中有着广泛的应用。
真空镀膜技术有三种形式,即蒸发镀膜、溅射镀膜和离子镀。
这里主要讲一下山溅射镀膜技术发展来的磁控溅射镀膜的原理及相应工艺的研究。
关键i司:溅射;溅射变量;工作气压;沉积率。
绪论溅射现象于1870年开始用于镀膜技术,1930年以后山于提高了沉积速率而逐渐用于工业生产。
常用二极溅射设备如右图。
通常将欲沉积的材料制成板材一靶,固定在阴极上。
基片置于正对靶面的阳极上,距靶一定距离。
系统抽至高真空后充入(10~ 1 )帕的气体(通常为氨气),在阴极和阳极间加儿千伏电压,两极间即产生辉光放电。
放电产生的正离子在电场作用下飞向阴极,与靶表面原子碰撞,受碰撞从靶面逸出的靶原子称为溅射原子,其能量在1至儿十电子伏范用内。
溅射原子在基片表面沉积成膜。
其中磁控溅射可以被认为是镀膜技术中最突出的成就之一。
它以溅射率高、基片温升低、膜-基结合力好、装置性能稳定、操作控制方便等优点,成为镀膜工业应用领域(特别是建筑镀膜玻璃、透明导电膜玻璃、柔性基材卷绕镀等对大面积的均匀性有特别苛刻要求的连续镀膜场合)的首选方案。
1磁控溅射原理溅射属于PDV (物理气相沉积)三种基本方法:发、溅射、离子镀(空心阴极离子镀、热阴极离子镀、电弧离子镀、活性反应离子镀、射频离子镀、直流放电离子镀)中的一种。
磁控溅射的工作原理是指电子在电场E的作用下,在飞向基片过程中与氮原子发生碰撞,使其电离产生出Ar正离子和新的电子;新电子飞向基片,Ar正离子在电场作用下加速飞向阴极靶, 并以高能量轰击靶表面,使靶材发生溅射。
在溅射粒子中,中性的靶原子或分子沉积在基片上形成薄膜,而产生的二次电子会受到电场和磁场作用,产生E (电场)xB (磁场)所指的方向漂移,简称ExB漂移,其运动轨迹近似于一条摆线。
若为环形磁场,则电子就以近似摆线形式在靶表面做圆周运动,它们的运动路径不仅很长,而且被束缚在黑近靶表面的等离子体区域内,并且在该区域中电离出大量的A r 正离子来轰击靶材,从而实现了高的沉积速率。
磁控溅射技术
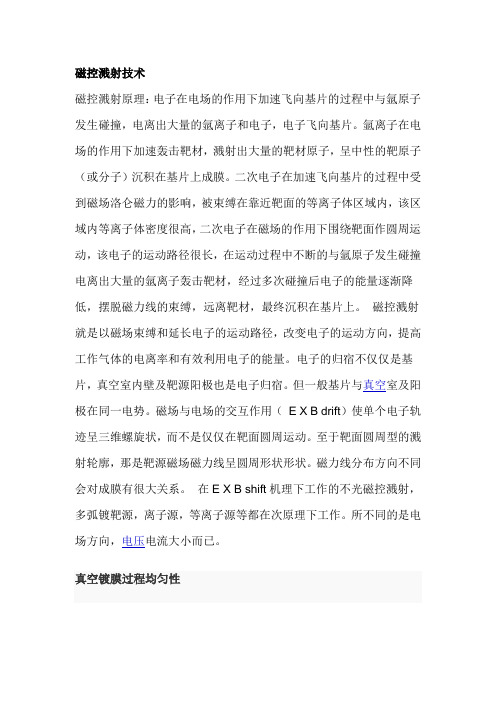
磁控溅射技术磁控溅射原理:电子在电场的作用下加速飞向基片的过程中与氩原子发生碰撞,电离出大量的氩离子和电子,电子飞向基片。
氩离子在电场的作用下加速轰击靶材,溅射出大量的靶材原子,呈中性的靶原子(或分子)沉积在基片上成膜。
二次电子在加速飞向基片的过程中受到磁场洛仑磁力的影响,被束缚在靠近靶面的等离子体区域内,该区域内等离子体密度很高,二次电子在磁场的作用下围绕靶面作圆周运动,该电子的运动路径很长,在运动过程中不断的与氩原子发生碰撞电离出大量的氩离子轰击靶材,经过多次碰撞后电子的能量逐渐降低,摆脱磁力线的束缚,远离靶材,最终沉积在基片上。
磁控溅射就是以磁场束缚和延长电子的运动路径,改变电子的运动方向,提高工作气体的电离率和有效利用电子的能量。
电子的归宿不仅仅是基片,真空室内壁及靶源阳极也是电子归宿。
但一般基片与真空室及阳极在同一电势。
磁场与电场的交互作用( E X B drift)使单个电子轨迹呈三维螺旋状,而不是仅仅在靶面圆周运动。
至于靶面圆周型的溅射轮廓,那是靶源磁场磁力线呈圆周形状形状。
磁力线分布方向不同会对成膜有很大关系。
在E X B shift机理下工作的不光磁控溅射,多弧镀靶源,离子源,等离子源等都在次原理下工作。
所不同的是电场方向,电压电流大小而已。
真空镀膜过程均匀性真空镀膜过程非常复杂,由于镀膜原理的不同分为很多种类,仅仅因为都需要高真空度而拥有统一名称。
所以对于不同原理的真空镀膜,影响均匀性的因素也不尽相同。
并且均匀性这个概念本身也会随着镀膜尺度和薄膜成分而有着不同的意义。
薄膜均匀性的概念:1.厚度上的均匀性,也可以理解为粗糙度,在光学薄膜的尺度上看(也就是1/10波长作为单位,约为100A),真空镀膜的均匀性已经相当好,可以轻松将粗糙度控制在可见光波长的1/10范围内,也就是说对于薄膜的光学特性来说,真空镀膜没有任何障碍。
但是如果是指原子层尺度上的均匀度,也就是说要实现10A甚至1A的表面平整,是现在真空镀膜中主要的技术含量与技术瓶颈所在,具体控制因素下面会根据不同镀膜给出详细解释。
- 1、下载文档前请自行甄别文档内容的完整性,平台不提供额外的编辑、内容补充、找答案等附加服务。
- 2、"仅部分预览"的文档,不可在线预览部分如存在完整性等问题,可反馈申请退款(可完整预览的文档不适用该条件!)。
- 3、如文档侵犯您的权益,请联系客服反馈,我们会尽快为您处理(人工客服工作时间:9:00-18:30)。
反应溅射原理
❖ 溅射过程中加入活性气体,制备成分与特性可 控的化合物薄膜
❖ 反应在哪里进行?
▪ 真空室空间?
▪ 能量守恒定律 能进行反应
化学反应能量释放 空间不可
▪ 反应在表面进行:基片表面、靶表面
反应溅射原理
❖ 优点
▪ 可使用高纯金属靶与高纯气体制备高纯度化合物薄膜, 避免制备化合物靶材带来的困难
1:4~1:8 ▪ 频率 10 kHz
直流反应溅射缺陷
❖ 靶面“中毒”与打火
▪ 靶面上形成了绝缘性的化合 物薄膜 绝缘膜上正电荷 积累 绝缘膜被击穿 溅射空间出现高电流低电 压的弧光放电 “打火” 镀膜过程不稳定和中断
▪ 打火 靶面局部熔化 喷射 薄膜缺陷增多 质量下降
▪ 靶面受损 使用寿命减少
❖ 阳极消失 ❖ 成膜速率低
❖电子漂移沿着同时垂 直 于 E⊥ 和 B 的 方 向 , 即E×B方向,电子加 速同时旋转
带电粒子在复合电磁场中的运动
❖ 静态开始运动的电子, 在均匀且相互垂直的E 和B场中运动轨迹为摆 线。
同轴圆柱面磁控溅射
同轴圆柱面磁控溅射平面磁控溅射来自平面磁控溅射目录
❖ 磁控溅射 ▪ 基本原理与特点 ▪ 磁控溅射类型
目录
❖ 磁控溅射 ▪ 基本原理与特点 ▪ 磁控溅射类型
❖ 反应溅射 ▪ 化合物薄膜 ▪ 反应溅射原理 ▪ 反应溅射工艺参数
❖ 中频溅射 ▪ 直流反应溅射的缺陷 ▪ 中频溅射原理 ▪ 中频溅射工艺参数
中频溅射
❖ 孪生靶磁控溅射(TwinMag) ❖ 双靶磁控溅射(Dual Magnetron Sputtering)
目录
❖ 磁控溅射 ▪ 基本原理与特点 ▪ 磁控溅射类型
❖ 反应溅射 ▪ 化合物薄膜 ▪ 反应溅射原理 ▪ 反应溅射工艺参数
❖ 中频溅射 ▪ 直流反应溅射的缺陷 ▪ 中频溅射原理 ▪ 中频溅射工艺参数
反应溅射工艺参数
❖ 沉积速率 ❖ 真空室气压 ❖ 溅射电压
反应溅射工艺参数
❖ 沉积速率
❖ 真空室气压 ❖ 溅射电压
❖ 反应溅射 ▪ 化合物薄膜 ▪ 反应溅射原理 ▪ 反应溅射工艺参数
❖ 中频溅射 ▪ 直流反应溅射的缺陷 ▪ 中频溅射原理 ▪ 中频溅射工艺参数
二极溅射缺点
❖ 成膜速率低 ❖ 基片温度高
二极溅射电子作用
❖ 碰撞放电空间的气体粒子,产生维持和增强放电所需 的电离(有利但较小)
❖ 到达阳极,撞击基片使之温度升高(不利但较大)
高速 低温
带电粒子在复合电磁场中的运动
❖ 电子在电场和磁场中受到的力
dv e (EvB) dt m
E×B 漂移
带电粒子在复合电磁场中的运动
❖ E=0,B为均匀磁场, 电子沿磁力线以速度vE 漂移,同时沿磁力线回 旋运动
❖ 回旋频率
e
eB m
❖ 回旋半径
rg
me e
( v B
)
带电粒子在复合电磁场中的运动
磁控模式
利用垂直于靶面的电场与平行于靶面的磁场形成二次 电子的捕集阱,电子运动方向受电磁场控制,沿着同 时垂直于电场和磁场的方向漂移,电子在运动过程中 不断与气体分子碰撞电离,直到二次电子能量耗尽。
二次电子运行路程大大增加,碰撞电离几率也 大大增加,离子数目增加使溅射速率相应增加
到达基片以及阳极的二次电子能量几乎耗尽, 基片温升明显下降
应用
A12O3
TaN
TiC
举例
In2O3
TiN
WC
SnO2
AlN
SiC
SiO2
Si3N4
Ta2O5
CNX
CdS CuS ZnS
TiCN
目录
❖ 磁控溅射 ▪ 基本原理与特点 ▪ 磁控溅射类型
❖ 反应溅射 ▪ 化合物薄膜 ▪ 反应溅射原理 ▪ 反应溅射工艺参数
❖ 中频溅射 ▪ 直流反应溅射的缺陷 ▪ 中频溅射原理 ▪ 中频溅射工艺参数
▪ 调节沉积工艺参数,可以制备不同配比的化合物薄膜 ▪ 无需射频电源,适合大面积生产 ▪ 基片不需要高温,对基片材料限制较少
❖ 二种模式
▪ 金属模式:靶面上溅射出来的金属原子或离子与活性气 体原子或离子在基片上反应,生成化合物薄膜
▪ 化合物模式:靶面上反应生成化合物,化合物再被溅射 到基片上形成化合物薄膜
Deposition rate versus oxygen partial pressure for an iron target in an Ar-O2 mixture.
反应溅射工艺参数
❖ 沉积速率
❖ 真空室气压 ❖ 溅射电压
反应溅射工艺参数
❖ 沉积速率
❖ 真空室气压
❖ 溅射电压
反应溅射工艺参数
磁控溅射特点
❖ 高速 ❖ 低温
磁控溅射特点
❖ 高速 如Al的成膜速率可达
1μm/min,接近电子 束蒸发,比二极溅射 高一个数量级 ❖ 低温
磁控溅射特点
❖ 高速 如Al的成膜速率可达
1μm/min,接近电子 束蒸发,比二极溅射 高一个数量级 ❖ 低温 同样条件下,二极溅射基 片温升可达 350~450℃,磁控溅 射仅250℃
磁控溅射、反应溅射与中 频溅射——原理与应用
复旦大学 材料科学系
沈杰
目录
❖ 磁控溅射 ▪ 基本原理与特点 ▪ 磁控溅射类型
❖ 反应溅射 ▪ 化合物薄膜 ▪ 反应溅射原理 ▪ 反应溅射工艺参数
❖ 中频溅射 ▪ 直流反应溅射的缺陷 ▪ 中频溅射原理 ▪ 中频溅射工艺参数
目录
❖ 磁控溅射 ▪ 基本原理与特点 ▪ 磁控溅射类型
❖ 沉积速率
❖ 真空室气压
❖ 溅射电压
反应溅射工艺参数
❖ 沉积速率 ❖ 真空室气压
❖ 溅射电压
目录
❖ 磁控溅射 ▪ 基本原理与特点 ▪ 磁控溅射类型
❖ 反应溅射 ▪ 化合物薄膜 ▪ 反应溅射原理 ▪ 反应溅射工艺参数
❖ 中频溅射 ▪ 直流反应溅射的缺陷 ▪ 中频溅射原理 ▪ 中频溅射工艺参数
中频溅射
❖ 直流反应溅射的缺陷 ▪ “积累电荷放电”——稳定工况 ▪ “靶中毒”——提高效率
弧光放电
❖1 高压击穿放电 ❖2 微弧放电 ❖3 极间放电
灭弧电源
❖ “灭弧”供电 ❖ A2K(Action Arc Killing)
电源
▪ 正脉冲平均电压 60~80 V ▪ 负脉冲平均电压 500~600 V ▪ 脉冲宽度比(放电/溅射)
❖ 反应溅射 ▪ 化合物薄膜 ▪ 反应溅射原理 ▪ 反应溅射工艺参数
❖ 中频溅射 ▪ 直流反应溅射的缺陷 ▪ 中频溅射原理 ▪ 中频溅射工艺参数
反应溅射——化合物薄膜
反应 气体
氧化 物薄 膜
O2
氮化 物薄 膜
N2 NH3
碳化 物薄 膜
CH4 C2H6
硫化 物薄 膜
H2S
碳氧化物 氮氧化物 碳氮化物