达涅利新一代棒材生产线经济效益显著
棒材连轧生产工艺最佳轧制节奏控制的研究

生产线主要 由双蓄热 步进梁式加热炉、8架 连续轧制两支 钢 的间隔 时间。根据 工艺设计商 l 平立交替布置的轧机 、 剪切设备、 冷床及精整打包 D IL 公司的规定 , NE I 间隙时问最短为 5 。当间隔 s
经济效益计算如下:
H =0
S= 。 烧结机艺设备故障停机率降低, 提高产
参考文献 [] 1 吕和平 . 重钢 2× 0m 烧 结混合机使用 新型衬板 15 的效果浅析. 烧结球团 , 0 , ( )5 — 9 2 02 1 ; 5. 0 5 8
设备故 障停机率降低数 ×日 历天数 × 4小时 × 2 每
小时产量 × 吨矿加工 费
=2 1 o×3 5 ×2 ×5 × 1 5 1 +1 8 .% 6 4 5 6 .6 . ‰ × 3 5×2 ×7 6 4 5×l O 1 l .O
O一2
=6 9 ×3 5 ×2 ×7 0×1 9 7 .% 6 4 5 0 .8
:
476 9 . 7万元
=4 . 5 54万元
S= : 球团( 包括竖炉 和回转窑 ) 工艺设备故障 停机率降低 , 提高产量 , 节约球团矿 加工费 = 工艺
经过近几年的生产实践和不断的摸索 , 在工艺
经统计 20 04年间隙时间平均控制在 l 秒 , 2 其不但
厂全线共有 8 活套 , 个 当轧制 间隙太小 , 快于活套 起落套反应时间, 轧件就容易顶在起套辊上而被打
飞, 出现废钢。 严藿影响平均机 时产量 ( 仅为 10 h , 2 t ) 而且 因控 2 4 l剪切头尾对轧制节奏的影响 / . #
= 97 2 .3万元
S= 每年节省 的检修费用约 3 O万元 ; S= 每年减少“ 漏料 、 清料、 运料” 的费用约 l O
棒线材MI.DA.无头轧制技术介绍

棒线材MI.DA.无头轧制技术介绍赵辉1,2①(1:北京首钢国际工程技术有限公司 北京100043;2:北京市冶金三维仿真设计工程技术研究中心 北京100043)摘 要 本文主要介绍MI.DA.无头轧制技术以及国内应用现状。
以山西建邦MI.DA.生产线为例,详细介绍了MI.DA.无头轧制的生产工艺和装备,总结了MI.DA.无头轧制技术的优缺点,为今后国内新建类似项目给出建议。
关键词 无头轧制 棒材 线材 MI.DA.中图法分类号 TG333 TG335.1 文献标识码 BDoi:10 3969/j issn 1001-1269 2023 06 025IntroductiontoMI.DA.HeadlessRollingTechnologyofBarandWireZhaoHui1,2(1:BeijingShougangInternationalEngineeringTechnologyCo.,Ltd.,Beijing100043;2:MetallurgicalEngineering3-DSimulationDesignEngineeringTechnologyResearchCenterofBeijing,Beijing100043)ABSTRACT MI.DA.headlessrollingtechnologyanditsdomesticapplicationstatusareintroduced.TakingShanxiJianbangMI.DAproductionlineasanexample,theproductionprocessandequipmentofMI.DAheadlessrollingareintroducedindetail,theadvantagesanddisdvantagesofMI.DAheadlessrollingtechnologyaresummarized,andsuggestionsaregivenfornewsimilarprojectsinChinainthefuture.KEYWORDS Headlessrolling Rod Wire MI.DA.1 前言节能降本一直是我国钢铁企业追求的目标,如何在保证产量的同时,降低生产成本,无头轧制工艺是一个很好的选择。
特殊钢棒线材扎制工艺技术的发展
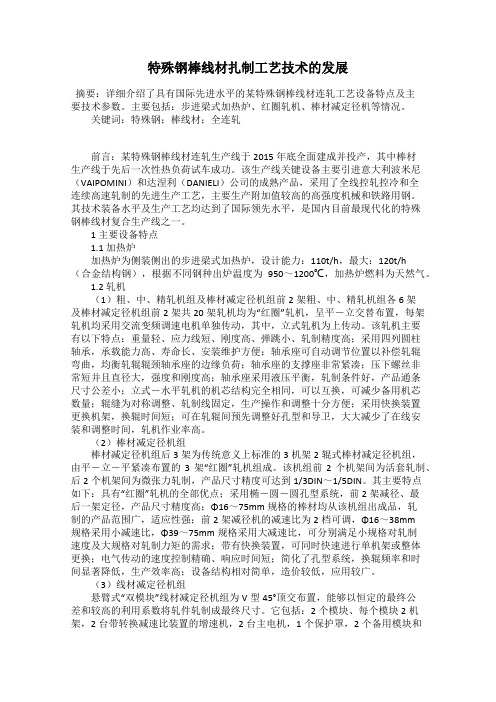
特殊钢棒线材扎制工艺技术的发展摘要:详细介绍了具有国际先进水平的某特殊钢棒线材连轧工艺设备特点及主要技术参数。
主要包括:步进梁式加热炉、红圈轧机、棒材减定径机等情况。
关键词:特殊钢;棒线材;全连轧前言:某特殊钢棒线材连轧生产线于2015年底全面建成并投产,其中棒材生产线于先后一次性热负荷试车成功。
该生产线关键设备主要引进意大利波米尼(VAIPOMINI)和达涅利(DANIELI)公司的成熟产品,采用了全线控轧控冷和全连续高速轧制的先进生产工艺,主要生产附加值较高的高强度机械和铁路用钢。
其技术装备水平及生产工艺均达到了国际领先水平,是国内目前最现代化的特殊钢棒线材复合生产线之一。
1 主要设备特点1.1 加热炉加热炉为侧装侧出的步进梁式加热炉,设计能力:110t/h,最大:120t/h(合金结构钢),根据不同钢种出炉温度为950~1200℃,加热炉燃料为天然气。
1.2 轧机(1)粗、中、精轧机组及棒材减定径机组前2架粗、中、精轧机组各6架及棒材减定径机组前2架共20架轧机均为“红圈”轧机,呈平-立交替布置,每架轧机均采用交流变频调速电机单独传动,其中,立式轧机为上传动。
该轧机主要有以下特点:重量轻、应力线短、刚度高、弹跳小、轧制精度高;采用四列圆柱轴承,承载能力高、寿命长、安装维护方便;轴承座可自动调节位置以补偿轧辊弯曲,均衡轧辊辊颈轴承座的边缘负荷;轴承座的支撑座非常紧凑;压下螺丝非常短并且直径大,强度和刚度高;轴承座采用液压平衡,轧制条件好,产品通条尺寸公差小;立式-水平轧机的机芯结构完全相同,可以互换,可减少备用机芯数量;辊缝为对称调整、轧制线固定,生产操作和调整十分方便;采用快换装置更换机架,换辊时间短;可在轧辊间预先调整好孔型和导卫,大大减少了在线安装和调整时间,轧机作业率高。
(2)棒材减定径机组棒材减定径机组后3架为传统意义上标准的3机架2辊式棒材减定径机组,由平-立-平紧凑布置的3架“红圈”轧机组成。
线棒材生产现状及发展趋势

线棒材生产现状及发展趋势线棒材是一种广泛应用于建筑、制造和交通等领域的材料,其生产现状和发展趋势备受关注。
本文将从产业规模、技术创新、市场需求和可持续发展等方面探讨线棒材生产的现状和未来发展趋势。
一、产业规模线棒材生产是一个庞大的产业,涉及到钢铁、金属加工和建筑等多个领域。
目前,全球线棒材生产规模不断扩大,年产量持续增长。
中国是世界上最大的线棒材生产国家,其产能和产量居全球领先地位。
此外,亚洲、欧洲和北美地区也是线棒材生产的重要地区。
二、技术创新线棒材生产技术在不断创新和改进。
传统的生产工艺主要包括连铸、轧制和拉拔等步骤,但随着科技进步和自动化技术的应用,线棒材生产过程越来越智能化和高效化。
例如,引入先进的连铸机和轧机,可以实现连续生产和高速轧制,提高生产效率和产品质量。
此外,一些新材料和新工艺的应用也为线棒材生产带来了新的发展机遇。
三、市场需求线棒材是建筑和制造业中不可或缺的材料,其市场需求受到经济发展和基础设施建设的影响。
随着全球城市化进程的加速和工业化水平的提高,线棒材的市场需求将继续保持增长。
此外,新兴行业如新能源、电动汽车和航空航天等对线棒材的需求也在不断增加。
因此,线棒材生产企业需要根据市场需求调整产品结构和提高产品质量,以满足不同行业的需求。
四、可持续发展随着全球环境问题的日益突出,线棒材生产也面临着可持续发展的压力和挑战。
传统的线棒材生产过程会产生大量的废气、废水和固体废弃物,对环境造成污染。
因此,线棒材生产企业需要加大环保投入,采用清洁生产技术和循环经济模式,减少和回收废弃物。
此外,提高能源利用效率和降低碳排放也是可持续发展的重要任务。
线棒材生产在全球范围内具有巨大的规模和潜力。
随着技术创新和市场需求的推动,线棒材生产将不断发展壮大。
然而,可持续发展问题也需要引起重视,产业需要加强环保意识,采用清洁生产技术,实现资源的高效利用和循环利用。
只有在技术创新、市场需求和可持续发展的支撑下,线棒材生产才能持续发展,并为社会经济发展做出更大贡献。
小型棒材轧制技术的发展

小型棒材生产线技术发展1.小型棒材生产线概述 (2)2.生产线布置形式及主要技术 (2)2.1.布置形式 (2)2.2.目前应用的主要技术 (6)3.国内其它主要生产线简介: (8)3.1.河北唐钢 (8)3.2.安徽马钢 (9)3.3.河北承钢 (10)4.棒材发展的新技术 (11)5.参考文献 (13)1.小型棒材生产线概述棒材是热轧条状钢材中的一种。
根据它的断面形状,一般分为圆钢、方钢、扁钢、六角钢、八角钢等,也有周期断面型钢如螺纹钢。
特殊情况下,也有卷状棒材,而不是直条形式。
棒材广泛用于机械、汽车、船舶、建筑等工业领域,是现代经济生活中不可缺少的品种。
近20年来,小型棒材产量占钢材的总产量的23.5%~27.7%。
棒材生产线主要是以连续铸钢坯或轧制坯为原料,经加热、轧制、精整等工序,生产各类小型型钢钢材。
据说在14 世纪欧洲就有轧机。
1728年,英国设计出了第一台的生产圆棒材用的轧机。
1761年英国建造了第一套小型横列式轧机。
1882年欧洲建设了第一套半连续式小型轧机。
1945年以后,随着连铸技术的出现,在全世界范围发展了半连续式和连续式小型轧机。
中国于1871年在福州船政局所属拉铁厂(轧钢厂)建设了第一套横列式小型轧机。
20世纪50年代和60年代先后在石景山钢铁公司建设了一套普通碳素钢连续式小型轧机和在济南钢铁厂建设了一套可生产合金钢的半连续式小型轧机。
80年代又在上海第五钢铁厂和安阳钢铁厂建设了半连续式小型轧机。
90年代初在广州钢铁厂建设了平立交替布置的连续式小型轧机。
2.生产线布置形式及主要技术2.1. 布置形式小型轧机的种类较多,轧机的类型和布置方式多种多样,主要运行的有:连续式、半连续式和横列式小型轧机,其他如布棋式、串列式、跟踪式小型轧机等已比较少见,下面主要介绍几种比较典型的小型轧机。
2.1.1连续式小型轧机。
连续式小型轧机是当今世界上最为流行、用得最多的一种小型轧机。
它所采用的坯料规格为130mm*130mm,150mm*150mm,甚至180mm*180mm,坯料单重1.5-2.5t。
达涅利倍尺飞剪在高强度棒材生产线的应用

达涅利倍尺飞剪在高强度棒材生产线的应用作者:于洋来源:《科技风》2017年第11期摘要:介绍了宣钢棒材生产线倍尺飞剪控制系统原理,阐述了倍尺飞剪控制系统获得脉冲当量两种方法,达到对倍尺飞剪剪切长度及精度的调整目的。
改造完成后认真做好在线使用运行状态的跟踪反馈,对一些不成熟的改造项目及时制定优化方案借机进行完善,以达到设备最佳运行状态。
关键词:倍尺飞剪;编码器;脉冲当量;辊径优先;测量优先宣钢高强度棒材生产线是宣钢第二次跨越发展的生产线,该生产线设计由中冶京诚负责,由意大利达涅利公司提供先进的技术,并由该公司设计制造全线的设备。
该生产线设计年产量90万吨,全线设有3台飞剪,1#飞剪位于粗轧机组后,用于轧件的剪头剪尾和事故碎断,2#飞剪位于中轧机组后,用于轧件的剪头剪尾和事故碎断,3#飞剪即倍尺飞剪位于QTB(轧后余热处理装置)水冷线之后,用于倍尺剪切。
飞剪控制系统完成对剪刃的位置和剪切起动、停止及回位等动作周期的控制,位置检测信号取自电机轴端编码器PG。
系统用一个热金属检测器及一个预设定计数器来检测轧件头部位置,计数脉冲取自出口机架电动机轴端脉冲发生器。
热金属检测器检测到轧件头部时起动计数器,当计数值达到预设定值时发出剪切起动信号。
轧件长度测量及飞剪剪切与位置控制由西门子高速工艺控制板T400完成。
1 倍尺飞剪的控制系统参数设置1.1 速度设定切头/分断速度超前率:取值范围1~1.1。
切尾速度滞后率:取值范围0.8~0.9。
碎断速度超前率:取值范围:一般等同切头分段超前率。
取较大的值可以减小。
1.2 长度设定成品长度:按实际冷剪定尺长度设定倍尺根数:上冷床的倍尺长度包含的定尺数附加长度:按冷剪切头/切尾长度、飞剪剪切误差和HMD1~2 距离测量误差等因素设定冷缩率:轧件冷态与热态长度的比值,一般为 0.98~09定采样长度:对于分断剪,选择采样功能后,采样时比倍尺长度多切的长度1.3 测量系统设置轧件长度测量系统中有两种设置方法,一种为测量模式,选择为测量优先方式,不用修改工作辊径;此时若换辊,则启车时飞剪画面的轧件速度与轧机计算机画面的对应轧机速度可能不匹配,直到热检检测到钢,计算出新辊的辊径,速度才显示正确的值。
国内棒材生产线生产工艺及设备综述
国内棒材生产线生产工艺及设备综述《重型机械科技}2004年第1期国内棒材生产线生产工艺及设备综述崔艳(重钢股份公司钢研所.重庆100084)摘要综述了我国多家捧材生产厂宋的生产工艺及设备状况,各俸材生产线的特点及生产能了J.分析了我国棒材生产的需求和发展趋势关键词棒材生产l艺设备TheProcessandEquipmentDescriptionoftheDomesticBarProductionLineCuiY anAbstractThisarticlesummal'izedthepiocessandtheequipmentstatusofdomestic.'sere1aIhl [acturersaswel1asthechalactel'isticofthebaI1)loductiol1lineandtheploductioncapacity.I htIm1tionrequilementandthe(1e,elopinenitcndenc>inChinahasbeenanal}zed KeyWordsBa1.P1'()cess.Equipment.1引言小型棒材一直是我国消费量最大的钢材品种,并且一直以较高速度增长,近20年来,小型棒材产量占钢材的总产量的23.50~27.7.本文综述了我国多家棒材生产厂家的生产T艺及设备状况.介绍了各棒材生产线的特点,支生产能力.分析了我国棒材生产的需求和发展趋势.以下介绍我国主要棒材生产厂家的情况.2河北唐钢2.1概述唐山钢铁股份有限公司l994年由意大利达涅利公司引进了具有90年代先进水平的全连续式棒材生产线.设计年产量6O万吨.其中精整设备除了冷剪,打包机为达涅利制造外.余均为国内配套制造,电气及自动化控制系统由美通用电气公司提供.该生产线l996年6月热负荷试车,同年9月试生产.从热试开始算.不到?年时间即超过了设计生产能力.而且产量逐年提高,各项技术经济指标在国内名列前茅.361.2生产工艺简介2.2.1原料及产品大纲坯料:l65ram×l65ram×l2m连铸方坯.产品规格:l2~40ram带肋钢筋,l4~50ram圆钢;直条供货.成品交货定尺6~l2m:产品精度要求达到DINl0l3际准要求的】/2钢仲:普碳钢,优质碳素结掏钢,低台金钢,铆螺钢,弹簧钢.最高轧速:l8m/s.2.2.2平面布置主厂房由原料跨,主轧跨,成品跨组成.原料跨距为30m.与主轧跨呈丁字形布置.主轧跨跨度为97m.长396m.轧面标高一15n1.设有5m平台.成品跨跨度为36m.长288m.轧而标高一12.6mj二问平面布置如图1所爪2.2.3生产工艺流程生产工艺流程如图2所示.2.3工艺设备特点2.3.1加热炉加热炉为全梁步进式加热炉.量为J50t,‰芸.霹护~述一洮洮{耄一综一基h.步进周期为45s,燃料为重油和煤气.加热炉使用部分热送热装连铸坯.而转炉煤气与重油混烧技术的采用使唐钢首次:转炉煤气全部回收《重型机械科技~2004年第1期利用.2.3.2轧机粗,中,精轧机组分别设置6轧机.实现全连[=l_II2l3王一8-7JI65图1唐钢全连续棒材车间平面布置简图1一上料台架2一步进式加热炉3一高压水除鳞箱4一夹送辊5一悬臂式粗轧机6架6—1号飞剪7一中轧机6架8—2号飞剪9—7组立活套l《1一精轧机6架11一淬水小车12—3号倍尺飞剪13一冷床14一冷剪1一收集台架2唐钢棒材生产工艺流程37--.■■■■■■L《重型机械科技))2004年第l期续无扭轧制.粗轧机为悬臂式BSS轧机.规格为685×4,j2『510×2;中,精轧机为短应力线整体更换轧机,规格为460×6,430×2,365×4.l4",l6"和l8"轧机均为平一立可转换轧机.全线轧机呈平一立交替布置.1~l0轧机采嗣电流记忆法微张力轧制.1l~l8轧机采H了7个立活套实现无张力轧制.轧线采用计算机自动控制.实现单线全连轧.同时,该厂采用低温轧制技术,钢坯开轧温度仅为950C.另外,用165mm×l65ram方坯轧制l2mm和14mm带肋钢筋时采嗣3线切分.生产l6mm带肋钢筋时采用2线切分.2003年6月.应用德国巴登钢铁I程公司(BSE)的四切分轧制技术的唐钢棒材J一【几1c』J分轧制生产线顺利投产.陔生产线轧制0l×l2mm棒材的速度为l2.2m/s.生产能为l40t/h.可在现有设备和投资少的条件下使小规格钢筋生产获取极高生产率.2.3.3轧线其它设备热轧带肋钢筋水冷淬火线由计算机,温瞍检测仪及各类控制阀等组成通过淬火披水.【1J'使钢筋达到Ⅲ级钢筋水平.同时减少r玖氧比铁皮生成量.步进式冷床长l32m.宽l2.5m.勾适调整,大坯重,长轧件轧制以及提高钢材外形质量.唐钢采用长尺冷却技术.同时,在冷床入口端的齿条排列较密.出口端的齿条排列较稀.使该冷床同时具有了矫直功能根据引进设备的具体条件.唐钢自行设汁了最佳优化剪切方案.编制了自动控制软件.f允比剪切工艺的采用使定尺率和成材率日I{提高. l999年唐钢生产棒材77.018万吨.成材宰为9607.定尺率为9820/.其中.2()卡Ⅱ22mm两个单线轧制的规格.基本实现r垣尺自动剔除操作.精整工序实现了机械化,自动化.生产线可自动计算棒材根数,自动打捆,自动称重,自动记录等.自动计数"标准捆"交货技术的误差率仅为0.7%.2.4小结为进一步提高该厂的经济效益.害钢仍在不断开发和应用新技术.目前.热装热送,连铸坯感应加热直接轧制,高频焊接无头轧制等创新技术38正在开发和应用中.3安徽马钢3.1慨述屿钢公司新建的60万吨全连续俸材生线于l998年l2月正式投产.至l999年3月底已生产近8万吨圆钢和带肋钢筋.生产线的主要工艺技术及关键设备由意大利POMINI公司提供.电控技术及主要电控设备由瑞典ABB电气公司提供,加热炉及其前后辅助设施由马鞍山钢铁设计院自行设计.轧机具有2O世9O年代国际先进水平.3.2生产工艺简介3.2.1原料产线所需坯料如表l所示表1棒材生产原料长度范围2…l32.2产品火纲产品大纲见表2.产品精度要求达到DIN标准要求的l/2.产品定尺打捆交货.定长度为6 ~l5m.最大终轧速度为18m/s:表2棒材产品大纲品种标准产品规格l2~lj1~2n2l~22矗~3(31~4【)4l~6(1年产量万吨I3.(】圆钢GB7f)286tIjI3【1l91螺纹铺.22~2512.28~32I1.'36~508j(B70286l4lllf;×l6方钢l8l8:索结构钢j亡;最碳素绐陶钢骶金结构钢鄙螺钢弹簧钢轴承钢S(150扁钢:GB7'488356l_】025一.一3.2.3平面布置车间由原料跨,主轧跨,成品跨等布置组成.轧机所有设备均布置在±0.000m地平上.主电室设在主轧跨内.车间厂房主要尺寸见表3.车间平面布置如图3所示.表3棒材车间厂房尺寸跨度长度轨面标高名称m原料跨302889主轧跨36384成品跨30276饥修间152523.2.4工艺流程工艺流程是:原料准备一称重,测长一加热一粗轧机组一倍尺剪一穿水冷却一中轧机组一精轧机组一冷床冷却一定尺剪一棒材打捆一成3.3工艺设备特点3.3.1加热炉侧进侧出梁底步进式加热炉为双框架结构.内部尺寸为23.8m×l6.8m.额定产量l50t/h.最高产量170t/h,燃料为高,焦炉混合煤气.3.3.2轧机《重型机械科技}~2004年第1期全线共18架轧机.粗,中,精轧机组各6架.均为无牌坊,短应力线,高刚度"红圈"轧机.呈平一立交替布置.轧机主要参数见表4.1~l0轧机间实现微张力轧制.10~l8轧机间采用立式可控活套.实现无张力轧制.从而全线实现了无扭,微张力或无张力轧制.第14架和第l6架轧机为平/立可转换轧机.该轧机采用大断面连铸坯"一火成材".开轧温度仅为950C.并且1~4架轧机在国内首次采用了平辊轧制,选用的两种规格方坯.只需调整1~4架的辊缝在第5架即可实现孔型共用. 生产j2『l2mm,14mm,j2『16mm螺纹钢筋时采用2线切分轧制技术.轧制j2『l2mm规格也可采用3线切分.3.3,3轧线其它设备精轧机组后设有穿水冷却装置.热轧件按Thermex工艺冷却.轧件经穿水冷却后可获得高屈服强度和高延展性的组织结构(屈服强度约可提高l50~230MPa).能使I级钢筋达到Ⅲ级钢筋水平.倍尺飞剪提高丁冷床利用率.冷定R飞剪保证了剪切精度和成品的定尺率.自动计数.自动图3马钢全连续棒材车间工艺平面布置简图1一梁底组台式步进加热炉(15【)tl/l1):2一粗轧机组(6架);3中轧饥组(6架):4一精轧饥组(6架);5穿水冷却装置6倍尺飞剪:7短尺(3.5~12m)收集系统;8一冷床:9冷定尺飞剪:10一自动收集打捆装置表4轧机主要参数最大辊径最小辊径辊身长最大轧辊中心距最小轧辊中心距最大轧辊负荷主电机功率饥架号轧机型号MNkW1,2RR464HSS()()41【】76l】62o5202.74;5(13,4RR一464一HS61(152(17()62052(12.7405o5,6RR一464一HS56【)47f176l1S7o47()2.7495o7~12RR一445一HS42()36()65o43036()1,47950'13~18RR~445一HS36(131()65()37(13101,47950:39《重型机械科技>>2004年第l期打捆.全线采用瑞典ABB公司专为棒材生产线开发的ABBasterRNS分级控制系统.具有完备的数据采集,控制,监视,跟踪和通讯功能.3.4小结该条生产线的建成投产对改善马钢产品结构?增强市场竞争力发挥了重要作用.但这条无论工艺还是设备都1t;较先进的棒材生产线仍存在着一些问题:(1)在建设初期为节省投资.生产线全部放在±0?OOm的平台上.在生产过程中.这一原因造成车间环境较差.设备维护比较困难的情况.(2)钢材的打包采用了圆钢捆扎的方式.打捆效果不理想.(3)这条生产线虽已基本达产,但目前的主要产品是精度要求不高的螺纹钢.高精度短应力线轧机的优势还没有充分发挥出来.(4)目前生产的螺纹钢是二级螺纹钢筋,即使生产三级螺纹钢筋也只是采用加合金元素的方法,而没有采用控冷的方法生产.THERMEX 工艺还没有起作用4吉林通钢4.1慨述通化钢铁公司35万吨小型棒材连轧厂是在原初轧厂基础上改造而成的.由通钢冶金设计院负责生产线设计,设备以国内设计和制造为主. 仅3飞剪,自动打包机和控制系统由国外引进. l999年11月底一次试车成功.2000年4月产量已达2.75万吨.基本上达到设计水平.4.2生产工艺简介4.2.1原料及产品大纲坯料:120ram×120ram×95000mm和150mm×l50ram×95000mm连铸坯.产品规格:l2~40mm圆钢和带肋钢筋?2.O~12.5m无级定尺,直条交货.钢种:碳素结构钢,优质结构钢,优质合金钢,低合金结构钢等.最高轧速:l7m/s.4.2.2平面布置车间平面布置图如图4.夕j./-8nn^/5\一,,…一\.n..1ln图4通钢小型j=L轧生:线f【fI=『布置图1一步进梁式加热炉z一9550mm4+450mn13粗轧机组31n飞剪4~38Omm4中轧饥组5—2飞剪6~水平活套7—380ramX2+32()mm×4(H/V)精轧机组8立式活套9水冷装置lO一倍尺飞剪11一变颇辊道12~齿条步进冷床13—49OOkN冷剪14定尺机15~检查台架16一打捆机l7一辊道电子称18集捆台架19一短尺剔除辊道2O~分级定尺冷剪4.3工艺设备特点4.3.1加热炉侧进,侧出3段步进梁式加热炉.烧高,焦炉混合煤气,小时产量为70t.4.3.2轧机共17架轧机,其中,粗轧机组规格为550mmx4+450mm×3.中轧机组规格为380mm×4,精轧机组规格为380mm×2+3.20mm×4.中轧机均为水平布置,采用微张力轧制中轧与精轧机组之间设有1个侧活套.精轧机组各架之间设有5个立活套.精轧机组各架之间可实现无张力无扭轧制.4.3.3轧线其它设备精轧机组后设有可移动控制水冷线,可根据钢种需要决定是否选择水冷.齿条步进式冷床尺寸为8.15m×78m.,轧件最大长度为72m.生产线设有2KNSB--8/6500型自动打捆机.4.4小结由于该生产线是由原初轧厂改造而成,所以存在一些设计上的问题.原料存放场地过小.只能存放3000t左右钢材;3倍尺飞剪没有切头尾功能.增加了成品定尺剪的切头量;由于仅设计了2套孔型.用120mm×l20mm连铸坯尚不能生产12mm和14mm产品等.所以该条生产线还需进一步改造.5湖南涟钢5.1概述涟钢新建的年产40万吨全连续棒材生产线于2001年4月12日正式投产.其主要工艺技术,机械设备,电气及自动控制装置由国外提供, 加热炉及其前后辅助设施由重庆钢铁设计院设计.轧机具有20世纪90年代国际先进水平. 5.2生产工艺简介5,2.1原料及产品大纲坯料:150mm×150mm×l2000mm连铸坯.坯重2505kg.产品规格:12~t0mm圆钢(15万吨/年),l0~40mm螺纹钢(25万吨/年).定尺交货.钢种:普通碳素结构钢,优质碳素结构钢,低合金结构钢,铆螺钢,弹簧钢,齿轮钢等.代表钢号:Q235,10#~45#,20MnSiV,20Cr~40Cr,60Si2Mn,20CrMnTi,ML20Mn等.最高轧速:18m/s.5.2.2平面布置车间原料跨跨度为33m.长108m;主轧跨跨度为27m,长409.2m;成品跨跨度为33m.长《重型机械科技)2004年第l期252m;主电室设在主轧跨外.轧线主设备均布置在+5,000m平台上.主厂房轨面际高为一l5m. 车间平面布置见图5.5.2.3生产工艺流程生产工艺流程是:坯料一上料一称重,测长一(剔除)一加热一夹送一粗轧一切头一中轧一切头一精轧一(水冷)一倍尺分段一冷床冷却一冷剪定尺一检查移送一打捆一称重标志一入库5.3工艺设备特点5.3.1加热炉采用炉内悬壁辊侧进侧出步进梁式加热炉.有效尺寸为l9.04m×l2.76m.步进周期40s.采用煤气加热.额定产量为l30t/h(冷装),l50t/h (热装).5.3.2轧机全线共20架轧机,呈平一立交替布置.初轧机为550mm×4,450mm×2闭式轧机.中轧机(7~l2)为450mm×2闭式轧机和450mm×4高刚度轧机.精轧机(13~20)为350mm×8高刚度轧机.l~ll轧机间实现微张力轧制,ll~20轧机间采用立式可控活套,实现无张力轧制.16,18为平立可转换式机架.该精轧机组的技术参数见表5.该生产线采用了低温轧制技术,切分轧制技术和无头轧制技术.开轧温度仅为950C.轧制14mm和l6mm带肋钢筋时.采用2切分.轧制l2mm规格时采用3切分.另外在第一道轧制前设置了由意大利达利涅公司引进的无头轧制技术.焊接机运行速度与第一道同步.焊接周期为45s.同时可完成去毛刺任务.焊接处材质与母材性能完全一致.图5涟钢全连续棒材车间平面布置简图1一原料跨2一加热炉(13or/h冷坯)3一粗轧机组(6架)4—1飞剪5一中轧机组(6架)6—2飞剪7一精轧机组(8架)8一倍尺飞剪9一冷床l【)一冷剪11一定尺机12一俭查台13一打包机l4一称量收集台l5一短尺台4l《重型机械科技))2004年第1期表5精轧区轧机机列技术参数彩350mm短应力线轧机设备13H14V15H16H/V17H18H/V19H2(1V轧辊直径.mm彩315~37()辊长度,mm650减速机速比l_811.7561.56Sl_3571.1()7111f】417表6热轧棒材品种产量及规格121416182【]1125324()台计低台金高强度螺纹钢19.2螺纹钢2.()4.()4.()4.()03()2.()1.(1().524.0低台金螺纹钢4,8碳结圆钢1.2圆钢().51.01,5l_51,S(1.5Cn普碳圆钢42合计2.54.()S.()4.()1,S{.03,52.51()3(J()5.3.3轧线其它设备全线共4台飞剪,倍尺飞剪由计算机控制.以保证入冷床的倍尺不至于过短.提高了冷床利用率定尺剪为精度较高的冷定尺剪.包装阶段采用了自动计数装置.5.4小结本套机组至2001年l2月底已生产近3O万吨圆钢和带肋钢筋.定R率达98.4..成材率为94.48.工序能耗为84.82kg/t.这条生产线的建成投产.使涟钢圆钢和螺纹钢的产量增加. 轧材能力突破300万吨/年.'6河北承钢6.1概述承钢1986年从原西德PEINE公司购入一套二手小型半连轧生产线.并靠自身技术力量.对原生产线进行了改造.自行完成了车间设计和设备的安装调试.其中.除加热炉系统,2台飞剪和检验台架由国内配套外.其余设备均为引进.该生产线1990年6月试车.1997年达到30 万吨的设计能力.6.2生产工艺简介6.2.1原料及产品大纲坯料:120mm×120mm×6000mm连铸坯.单重67lkg(投产初期为l30mm×l30ram×2900mm方坯,单重374kg).42最高终轧速度:12m/s.产品规格:产品定尺6~l2m.产品大纲如表6所示.6.2.2生产工艺流程承钢小型半连轧生产工艺流程为:加热炉一翻钢机一开坯机组一双摆动剪一粗轧机组一l. 飞剪一中轧机组一2.飞剪一精轧机组一3飞剪,冷床一冷剪一打捆,包装,称重,入库.坯料经开坯后在粗轧,中轧,精轧机组进行连续轧制.开坯机组与粗轧机组间不连轧为脱尾轧制.2号辊道上设有钢坯分配器.当生产j2『l6mm以下的产品时.钢坯由此分为两路.进入粗轧机组.其余规格为单线轧制.6.3工艺设备特点6.3.1加热炉三段连续式端进侧出推钢武l儿1热炉.炉瞠有效长度26.68m.产量为80t/h.燃料为渣油.6.3.2轧机全轧线共26架轧机,立一平交替布置.均为二辊闭口式连轧机.开坯机组为4架j2『420mm ×850mm轧机.粗轧机组为6架0380mm×850mm轧机.I中轧机组(7~l0架)为4架轧机,I中轧机组(1l~l4架>为I架0330mm×600mm轧机.精轧机组分南北两线布置备4架轧机.6.4小结《重型机械科技))2004年第l期由于引进设备为西德50年代产品,所以承钢对该条生产线进行了系统改造.l993~l994年对全线电控系统进行了改造,l996~l997年对粗,中,精轧机组进行了改造.切分轧制技术, 高刚度短应力轧机和轴承轧机的应用使承钢的棒材产量于l997年首次达到32.3万吨.并且成材率达到93.5.合格率达到98.5.2000年四季度.承钢又投资近5000万元.对该生产线及配套设备进行了60万吨设计改造,使装备水平达到国内先进水平和国际90年代初水平.并于2002年实现70万吨的产量.今年年底.承钢又计划投产一条产能为80万吨/年的新棒材生产线.其主要设备由达涅利提供.生产l2~60ram 的棒材.新线投产后,该公司的钢材产量将达到l50~230万吨/年.7河北石钢7.1概述石钢公司引进的60万吨棒材连轧生产线. 2000年3月18日进行热负荷试车.同年5月开始试生产.该生产线的工艺设计,轧线的机械设备没计由意大利TECHINTPOMINI公司负责.电气控制系统由德国SIEMENS公司完成. 加热炉设计由法国STEINHEURTEY公司完成.生产线的工厂设计由北京钢铁设计研究总院完成.整条生产线具有90年代末期国际先进水平,并为将来实现热送热装,高线大盘卷生产,型材生产,无头轧制,在线测径等工艺和技术预留了足够的位置.7.2生产工艺简介7.2.1原料及产品大纲坯料:l50mm×l50ram×l2000mm连铸坯,重2.05t.产品规格:主导产品为j2『l4~50mm圆钢,l0~50mm带肋钢筋,45~l00×5~12mm扁钢.产品定尺长度6~l2m.钢种:碳结钢,优碳钢,合金结构钢,低合金钢及弹簧钢.最高终轧速度:18m/s.7.2.2生产工艺流程石钢棒材生产工艺流程图见图6.7.3工艺设备特点7.3.1加热炉单排装料侧进侧出加热炉.有效面积为24m×l2.8m,燃烧高,焦炉混合煤气.额定加热能力l50t/h.最大产量为l70t/h.入炉辊道中设有坯料称重测长装置.加热炉装配有汽化冷却系统和二级燃控系统.7.3.2轧机全线l8架轧机,全部为二辊短应力线轧机.即P0MINI的"红圈"轧机.分别为RR464,RR455,RR445型.粗轧机组为580/480mm×760mm×4+600/500mm×760mm×2.中轧机组为520/450mm×750mm×3十440/370mm×750mm×3.精轧机组为365/310mm ×650mm×6.精轧机组的l4,l6和l8#轧机为平立可转换轧机.全线轧机呈平立交替布置.可实现棒材的连续无扭轧制.l"~l0.架轧机为微张力轧制,l0~l8架为立活套控制无张力轧制.l8轧机后安装了德国BRUNORICHTER公司的移动式在线测径仪.产品尺寸偏差可达到1/3DIN标准公差范围的水平.该轧线还留有备用机架:粗轧2架,中轧6 架,精轧6架.该轧线具备了低温轧制的条件.石钢棒材生产线的大部分钢种可在950C~l020C范围内开轧.小规格带肋钢筋(j2『10~16ram)采用切分轧制.其中j2『10~j2『12mm的带肋钢筋采用3 线切分.l4~16ram规格的采用2线切分.7.3.3轧线其它设备水冷线采用THERMEX专利技术.闭环控制.可将轧件表层由950C剧冷到250C.在轧件表层一定深度内马氏体组织.具进齿条式冷床.床面尺寸为120m×l2.5m.由意大利0MV公司提供的自动打捆机可打单道也可打双道.对扁钢和大规格圆钢还可打方捆.全轧线的自动化控制系统由德国SIMENS公司设计制造.一级系统为基础自动化控制系统.二级系统为过程控制系统.7.4小结这条生产线的建成投产为石钢改变品种结构,提高产品质量,增强企业的市场竞争力打下了坚实的基础.但该生产线仍存在成品跨存放场地面积较小.车间±0.00m面上的各类介质站布置略显凌乱以及设备故障及控制问题.43《重型机械科技}2004年第1期8江苏沙钢图6石钢棒材生产工艺流程图8.1概述沙钢1999年4月建成一条具有90年代国内领先水平的小规格全连续棒材生产线,年设计能力4O万吨.1999年5月试生产后.用切分轧制生产1O~12mm带肋钢筋.共生产l0.5个月,总产量为27.1429万吨.产品合格率达99.29/6成材率(不含负偏差)为95.81.定R44预留线材一…:'卷取一一0.-r一一Ir...』一一-'一lL苣输::蔓]r一葡]_一_上L.…一-J.一』一一曼一j—.』—.lLlLr-mi----j~L..…—..J.一』一一lL率达99.72.8.2生产工艺简介.8.2.1原料及产品大纲坯料:130ram×130mm~l5Omm×150mm方坯,单根坯重1570~218okg.产品规格:10~25ram带肋钢筋和14~25mm光面圆钢.预留了生产5.5~16mm光面圆钢盘条的位置.最高终轧速度:15m/s.《重型机械科技))2004年第l期8.2.2生产工艺流程工艺流程为:方坯一加热炉一粗轧机组一l飞剪一中轧机组一2飞剪一精轧机组一3倍尺飞剪一步进冷床一4900kN定尺冷剪机一成品打捆.8.3工艺设备特点8.3.1加热炉侧进侧出推钢式加热炉.有效尺寸为l6.0m×l2.8m,燃重油或渣油.额定产量85t/h.最大产量lOOt/h.烟气余热用于激化冷,空气换热器及蒸汽过热器.8.3.2轧机全线共l8架轧机.各由6架平一立二辊轧机组成.粗轧机组为560/480mm×600mm×4+410/350mm×600mm×2,中轧机组为41O/350mm×600mm×6.精轧机组为335/285mm×600mm×4+335/285mm×500mm×2,第l6#精轧机架为平立可转换轧机.轧线为全连续无扭轧制.采用切分轧制技术生产l0 ~l2mm小规格带肋钢筋.8.3.3轧线辅助设备全轧线采用计算机自动控制.产品在冷床由人工点数,用气动钢带打捆机捆扎.8.4小结沙钢在该条生产线投产后,对其进行了多次小改小革,使其轧制速度达到最高设计速度15m/s,作业超过85.产量,成材率,产品合格率等主要技术经济指标均超过设计水平.在此基础上.2001年4月.通过增加成品机架轧辊辊径,设置沿未剪成倍尺轧件的头部拨料装置相增设快速制动压料装置等措旎.沙钢再次提高各项指标.并将轧制速度提高至l7m/s.与此同时.在生产线刚建成一个月时,沙钢就开始试验在平立交替布置的轧线上进行小规格棒材二切分轧制. 并且一次调试成功.2001年6月又开始试验三切分轧制,并于2002年2月攻关成功.目前.沙钢三切分的钢坯产品合格率已达到98.53.成材率达到96.44.9广东韶钢9.1概述韶关钢铁公司l995年从意大利达涅利公司引进了一条年产50万吨具有90年代先进水平的棒材生产线,由马鞍山钢铁设计研究院进行总体设计和工厂设计.1996年12月建成投产. 9.2生产工艺简介9.2.1原料及产品大纲坯料:l50mm×l50mm×lO000mm和200mm×200mm×lO000mm连铸坯或轧坯.单根坯分别重l730~3o7Okg.短尺坯长度8000mm.产品规格:l2~40mm光面圆钢和螺纹钢筋.定尺6~18m.钢种:碳素结构钢,优质碳素结构钢,铆螺钢,低合金钢和少量一般结构钢等保证轧制速度:24m/s.最大轧制速度:33m/So9.2,2生产工艺流程该轧钢厂采用全连轧方式组织生产.主轧线设置20架轧机,平立交替布置.出炉钢坯在连轧机组上经20~l2道次轧制成各种规格产品. 9.3工艺设备特点主轧线设置20架轧机.采用全连轧方式组织生产.使用大断面钢坯一火成材.全线轧机平立交替布置,粗中轧机组采用无扭,小张力控制轧制.精轧机组采用无扭,无张力轧制.l~8轧机(粗轧机组)采用双支撑无牌坊单孔短应力线轧机.9~l8轧机采用双支撑无牌坊多孔槽短应力线轧机.19~20轧机采用悬臂辊环BLOCK机组.轧线主辅设备采用二级计算机控制.9.4小结随着连铸连轧工程的建设和投产.捧材生产线产量将达到65~70万吨/年.为此韶钢对生产线的粗轧机组和精整区等部分进行了改造以更好地满足生产需要.lO广东广钢l0.1概述l991年广州钢铁公司新建了一条40万吨棒材生产线.该生产线全部技术和轧线设计由达涅利公司负责.电控设备,l8台轧机,分段飞剪, 带裙板冷床输入辊道,钢材计数装置,钢材自动打捆机和相应配套的润滑液压装置等关键设备由达涅利提供.轧线其它设备由国内转化达涅利公司图纸制造,加热炉区设备由武汉冶金设备制45《重型机械科技~2004年第l期造公司承制.1994年3月全线热负荷试车.同年6月投产.l0.2生产工艺简介lO.2.1原料及产品大纲坯料:150mm×150mm×10000mm钢坯.单根坯重1.7t.(生产l2光面圆钢时喟ll5ram×1l5mm方坯).产品规格:l2~40ram圆钢和螺纹钢.钢种:热轧普通碳素钢,普通铆螺钢,普通低合金钢和优质碳素钢等.最大轧制速度:33m/s.l0.2.2平面布置连轧生产线平面示意图见图7图7广钢连轧生产线平面布置图l一上料台架2一坯料电子称3一入炉辊道4一推出机5一组合式步进炉6一夹送辊7一悬臂式组轧饥组8一l#飞剪9一悬臂式中轧机组l0一立式活套器11—2#飞剪机l2一水平精轧机l3一平立可转变情轧帆l4一水冷线l5一倍R飞剪(3#)16一碎断剪l7一带裙板岭床输入辊道l8~步进式冷床lL】冷翦饥2()一成品收集槽211?一成品电子称22__1十数器23一自动打捆机24一定R挡板2s一非定只包扎亩l0.2.3生产工艺流程钢坯由电磁盘吊车吊上上料台.步进式料台将钢坯逐根移到入炉辊道上.钢坯经电子称自动称量后,被送入步进式加热炉.钢坯加热到11o0~ll50C.由推钢机推出炉口经平送辊送入第一机架进行连续轧制.轧件经l号飞剪机切头后进入中轧机,经2号飞剪机再切头切尾后进入精轧机,此时活套自动投入运行实现无张轧制.成品钢材从精轧机出来空过水冷却装置经3号飞剪机剪成倍尺长度经裙板辊道拨入步进式冷床.冷床中部的齐头辊道将钢材往冷剪机方向靠齐,并自动编组送上冷剪输入辊道.冷剪机将倍尺钢材剪成定尺长度送入计数站.计数站一方面调整计算每一组钢材.另一方面将短尺钢材分离出来送去短尺包扎台.定尺钢材由自动扪捆捆轧后,由辊道移送到电子称称量入库.lO.3工艺设备特点l0.3.1轧机全轧线l8台轧机.平立.6台粗轧机和6台。
攀钢110万吨棒线材生产线建设与发展
攀钢110万吨棒线材生产线建设与发展宋建国;陈文灶【摘要】攀钢抓住市场机遇,在攀枝花本部搬迁建设一条110万吨的棒线材生产线,本文对该生产线的工艺布局、主要装备特点、产品定位及后期发展等进行了介绍.【期刊名称】《四川冶金》【年(卷),期】2018(040)005【总页数】3页(P38-40)【关键词】棒材;高线;生产工艺;技术改造【作者】宋建国;陈文灶【作者单位】攀钢集团攀枝花金属制品有限公司,四川攀枝花617023;攀钢集团攀枝花金属制品有限公司,四川攀枝花617023【正文语种】中文【中图分类】TG33根据攀钢产线结构调整需求,攀钢集团利旧搬迁攀成钢闲置设备,在攀枝化本部建设一条年产50万吨高速线材生产线和60万吨的棒材生产线。
棒材于2017年3月1日热负荷试车,高线于2017年5月9 日热负荷试车。
在一年的时间内,完成项目的搬迁建设与达产达效,实现当年投资、当年建成、当年赢利的任务,成为攀钢新的利润增长点。
截止2017年12月底,全年累计生产建筑用钢40.8万吨,棒材实现了Φ14~40mm规格、高线实现了Φ6.5~12 mm规格的螺纹钢、圆钢生产。
现今,高速线材生产线正致力于高端金属制品用线材的开发,逐步打造西南地区最具竞争力的建材生产基地和金属制品材生产基地。
1 平面布置根据地理位置条件,为有效节约占地和工程投资,尽可能利旧闲置设备及设施,高速线材与棒材车间平行相邻布置,依次布置线材主轧跨(231.0 m×24.0 m+135.0 m×21.0 m)、棒材主轧跨(428.5 m×24.5 m)、原料跨(440.5 m×33.0 m)、成品跨(256.5 m×18.5 m,预留184.0 m×18.5 m)。
车间最大长度440.5 m,最大宽度100 m,线材主轧线设备布置在+5.0 m平台上。
工艺平面布置示意图如图1所示。
2 主要装备2.1 棒材生产线主要由1台蓄热推钢式加热炉、18架轧机、3台飞剪、1台冷剪机、1台步进齿式冷床、检查收集设备等组成。
小规格圆钢生产工艺改进
小规格圆钢生产工艺改进王新奎【摘要】针对小规格圆钢轧制道次多,工艺控制点复杂、易出现折叠等缺陷,通过对孔型进行优化、轧辊材质进行调整、导卫轮进行改造,提高了小规格圆钢的产量、质量和成材率,降低了生产成本,取得了较好的经济效益.【期刊名称】《天津冶金》【年(卷),期】2017(000)004【总页数】3页(P32-34)【关键词】小规格圆钢;孔型;导卫;折叠【作者】王新奎【作者单位】天津钢铁集团有限公司,天津300301【正文语种】中文天津钢铁集团有限公司双棒材厂引进的两条意大利达涅利公司生产线,于2006年投入生产,其中一线主要轧制螺纹钢,二线主要轧制圆钢。
主要产品规格为Φ10 mm~Φ50 mm热轧带肋钢筋,Φ16 mm~Φ75 mm的光面圆钢,主要品种有碳素结构钢、合金结构钢、弹簧钢、齿轮钢等。
生产流程如下:合格的连铸方坯→上料台架→链式提升机→步进式加热炉→高压水除鳞→6架粗轧机组→1#曲柄剪→8架中轧机组→2#回转剪→4架精轧机组→测径仪→3#组合倍尺剪→裙板辊道→120 m冷床自然冷却→4#定尺摆剪→双辊道横移台架→三段链收集→打捆入库[1]。
目前国内钢铁行业产能过剩,市场形势严峻,下游制造商对钢铁生产企业的产品种类、钢种、质量需求日益提高。
天钢为开拓市场,积极开发新规格、新钢种,并在此基础上降低成本、优化产品质量,力求提高市场竞争力。
长期以来,由于小规格圆钢轧制道次多,工艺控制点复杂,实际生产中Φ16 mm~Φ25 mm规格问题突出,容易发生堆钢,成品尺寸超标,且极易出现折叠缺陷。
这些问题直接导致切废率上升,作业率和成材率下降,造成成本增加,天钢决定对小规格圆钢生产工艺进行优化。
天钢结合现有设备水平和自身技术特点,通过对孔型的优化、轧辊材质的调整、导卫轮的改造等措施,提高小规格圆钢的产量、作业率和成材率等指标;通过对折叠缺陷的案例的分析,总结经验,严格控制折叠缺陷的产生,改善圆钢的表面质量。
2024年特钢棒材制造市场发展现状
2024年特钢棒材制造市场发展现状引言特钢棒材是一种高强度、耐磨性好、耐蚀性强的金属材料,在建筑、汽车、能源等领域有广泛应用。
随着全球工业化进程的加速,特钢棒材制造市场也呈现出快速发展的趋势。
本文将对2024年特钢棒材制造市场发展现状进行分析和探讨。
市场规模与需求特钢棒材制造市场近年来呈现出稳步增长的态势。
据行业数据统计,特钢棒材的年产量从2016年的2000万吨增长到2020年的2500万吨,复合年增长率达到5%。
市场需求主要来自建筑、汽车、能源等行业,这些行业对特钢棒材的需求量持续增加。
市场竞争格局特钢棒材制造市场存在着较为激烈的竞争格局。
全球特钢棒材制造商众多,包括国际知名企业和地区性企业。
在全球市场中,主要特钢棒材生产国家有中国、美国、德国、日本等。
这些国家的企业凭借技术实力和规模优势,竞争力较强。
此外,新兴市场如印度、巴西等国家也开始崛起,呈现出快速发展的态势。
技术进步与创新在特钢棒材制造领域,技术进步和创新是推动市场发展的重要因素。
近年来,随着科技的不断进步,特钢棒材制造技术也在不断改善和创新。
比如,采用先进的连铸连轧技术可以提高生产效率和产品质量;应用新型合金材料可以满足不同行业对特定性能的要求。
技术进步和创新的推动,为特钢棒材制造市场的发展注入了新的动力。
市场挑战与机遇特钢棒材制造市场面临着一些挑战,但也有着发展的机遇。
首先,环保问题是特钢棒材制造面临的重要挑战之一。
特钢棒材的制造过程涉及大量的能源消耗和环境污染,因此提高生产过程的环保性和可持续性是当前亟待解决的问题。
其次,市场竞争激烈,企业需要通过技术创新和提高产品质量来保持竞争力。
同时,市场的快速发展也为企业带来了机遇,适应市场需求和扩大市场份额是企业的发展方向。
发展趋势与前景展望特钢棒材制造市场将继续保持快速发展的态势。
未来,市场需求将持续增加,特钢棒材的应用领域也将进一步拓展。
与此同时,技术进步和创新将不断推动市场发展,新型材料和新工艺的应用将提高特钢棒材的性能和品质。
- 1、下载文档前请自行甄别文档内容的完整性,平台不提供额外的编辑、内容补充、找答案等附加服务。
- 2、"仅部分预览"的文档,不可在线预览部分如存在完整性等问题,可反馈申请退款(可完整预览的文档不适用该条件!)。
- 3、如文档侵犯您的权益,请联系客服反馈,我们会尽快为您处理(人工客服工作时间:9:00-18:30)。
达涅利新一代棒材生产线经济效益显著
意大利AcciaierieBertoliSafau(ABS)工厂
以很高的生产率生产小规格棒材产品,以充分发挥加热炉生产能力,一直是全世界棒材生产商共同追求的一个目标。
对于中国市场来说,为实现这一目标,最常用的方式就是众所周知的多线切分轧制系统。
它采用专用轧辊孔型设计和特殊的导卫设备,以使轧件成形,并纵向切分为2线、3线或4线棒材。
然后,同时将各线棒材轧制到最终产品尺寸规格。
能够在中国的棒材轧机上应用的具有革命性创新意义的一项可选技术,将是超高速棒材精轧和通过达涅利HTC(High-speed Twin Channel )“高速双通道”输送系统,将精轧后的棒材高速送上冷床。
高速双通道输送系统最初由达涅利早在20世纪70年代初期研制开发,并申请专利,此后在全世界获得广泛应用。
它将棒材输送到冷床上的速度也由最初几年的20m/s最大速度,逐渐发展到今天创纪录的50m/s。
HTC高速双通道输送系统非常适用于最新一代高效棒材轧机。
高效棒材轧机在生产小规格棒材时,可在连续式预精轧机上进行切分轧制,然后在两个独立的Delta高速线材轧制机组,同时完成双线精轧。
本文将介绍超高速棒材精轧机组和高速输送系统的主要技术特点,它们的主要亮点和给用户带来的好处(其中最显著的特点是可以极高的生产效率,生产最小直径为?6mm的小规格螺纹钢棒材)。
高效生产小规格棒材
现代棒材轧机追求的主要目标之一,是能够以很高的生产率,生产符合市场需要的小规格棒材和钢筋。
小规格棒材和钢筋通常占轧机设备总产量的一半以上。
要实现这一目标,就意味着要充分发挥加热炉加热小规格坯料的生产能力,从而能够很好地平衡轧机的生产能力,充分发挥它的生产潜力。
要实现这一目标,可通过以下两种途径:
1)MSR多线切分轧制
该系统目前在中国使用最多,主要目的是用于实现上述目标。
多线切分轧制系统利用同一根直方坯,通过两线或多线切分轧制,生产小规格棒材。
其特点是,与单线轧制相比,可以减少轧制道次。
切分轧制技术采用特殊的轧辊孔型设计和专用导卫设备,以使轧件成形,并将来坯纵向切分为2线、3线、4线或5线棒材。
然后由精轧机架将各线棒材,轧制到最终产品尺寸规格,并同时完成倍尺剪切。
然后,通过传统“挡板式”入口输送辊道,以18~20m/s(用于2线切分轧制)或13~15m/s(用于3线或4线切分轧制)的最大速度,将这些棒材一起输送到冷床上。
这项工艺必然要涉及将两根或多根棒材送到冷床齿槽内(输送根数取决于轧机切分轧制线数)。
随之而来的问题是,有可能使棒材在对中辊道区内头部对齐作业变得困难。
当采用4线切分轧制时,这个问题可能容易解决一些。
这应该归功于双挡板式冷床入口输送辊道。
由于配备了这种输送辊道,只需将两根棒材送入冷床上的每个齿槽内,从而使棒材头部对齐和料层成形变得容易一些。
切分轧制工艺可用于生产?8~22mm圆钢和钢筋。
2)高速精轧和双通道输送系统
将高速精轧与达涅利双通道棒材输送系统结合在一起,与上述切分轧制系统相比,在高效生产小规格棒材方面,具有许多明显的优势,可为用户带来许多好处。
这项技术可以追溯到上世纪70年代初期。
当时达涅利发明了它的双通道输送系统,并申请了专利。
双通道输送系统可实现自动作业,可对来自精轧机组的多根高速棒材进行平稳制动,然后将这些棒材平稳地直接输送到冷床齿槽上。
从那以后,双通道输送系统在全世界获得广泛应用:不仅用于新建设备,而且用于现有轧机升级改造和扩建项目。
它将棒材输送到冷床上的速度也由最初几年的20m/s最大速度,逐渐发展到今天创纪录的50m/s。
双通道输送系统可实现平稳制动,可将?6~40mm棒材,以高达50 m/s的精轧速度平稳地输出,既适用于单线轧制,也适用于双线切分轧制。
该系统采用这样的设计概念,要将多线棒材,以每个齿槽一根棒材的方式送上冷床,以满足单线轧制或双线切分轧制生产需要(分别配备一台或两台双通道输送装置)。
它主要由交替打开,让棒材依次落下的一系列通道和安装在来料侧的夹送辊/尾部制动装置组成。
双通道输送系统特别适用于最新一代高效棒材轧机,在预精轧机架完成小规格棒材切分轧制后,在分别独立设置的两个4道次或6道次Delta轧制机组上,实现两个独立轧线的高速精轧。
通过这种方式,可大幅度提高设备生产能力,即使在轧制?8mm小规格棒材时,仍可确保小时生产能力超过100 t/h。
双通道系统与MSR多线切分轧制可为用户带来的主要好处:
拓展产品生产规格范围——可生产最小直径为?6mm小规格棒材。
提高金属材料收得率——由于冷床每个齿槽上仅放一根棒材,因此可确保棒材头部准确对齐,从而可提高棒材成层质量,最大限度地减少冷剪切头切尾量;由于可实现单线无扭轧制,因此能够尽可能减少废品。
改善产品质量——由于DWB-Delta轧制机组可实现单线无扭轧制,因此可提高棒材精整质量:钢筋棒材单位长度重量和圆钢尺寸公差绝对满足标准要求(参照非切分轧制棒材生产标准)可提高棒材平直度(冷床上每个齿槽放置一根棒材冷却),从而改善棒材成捆质量。
提高设备MUF(轧机利用系数)——设备调整更方便、更快捷:利用碳化物辊环实现单线/无扭精轧,可延长轧槽使用寿命,尽可能缩短设备更换时间;减少导向装置数量;单线QTB水淬火和自回火热处理线;减小产生废品的可能性,进而缩短设备重新设定时间。
降低原材料消耗——使用“长寿命”碳化物辊环;减少辊式导卫装置数量,从而减少相应的备件/消耗件用量。
双通道输送系统的主要技术亮点:
棒材可通过打开的通道平稳而有规律地落到冷床齿槽内(下落高度只有170mm,矮于其他任何现有系统)。
配备具有良好减速性能的超紧凑式棒材制动器,可确保产品表面无缺陷,棒材在冷床上排列整齐,并保持在它们的“卸料”位置。
整个双通道系统在不工作时,或为设备检修目的,可在离线/备用泊放位实现自动翻转。
可分离式驱动系统能够尽可能减小驱动轴扭转。
与其他同类系统相比,可缩短工作周期。
较短的工作周期使它能够将很高的精轧速度与超短冷床长度完善地结合起来,从而降低设备投资费用。
高速精整系统轧机配置是十分理想的,预留将来设备扩建的可能性,可在将来增加线材轧制和工字轮卷取生产线。
双通道输送系统是一种理想的工具,既适用于新建棒材轧机,也可以方便地用于现有轧机改造和扩建(因为它安装在传统冷床输入辊道的一侧)。
双通道技术和生产工艺过程
在最新一代高效棒材轧机系统中,经过DWB-Delta精轧机组轧制后的棒材,通过HTC -高速双通道输送系统,以很高的速度输送到冷床上。
双通道输送系统主要由按“双线”布置的“C”形输送器组成。
C形输送器布置在冷床第一部分(矫直格栅区)的上方,高出冷床台面不超过170mm。
来自精轧机组的棒材,输送到QTB水淬火和自回火热处理线和剪切机。
剪切机将根据冷床长度,将棒材剪切成相应的倍尺长度。
在每台剪切机后面,作业线变成双线。
每根切成倍尺的棒材,通过一台专用偏转装置,或者输送到第一条,或者输送到第二条双通道输送线上。
专门设计的紧凑式棒材制动器,布置在非常靠近冷床的地方。
它的作用是降低棒材速度,使棒材到达所需要的输出位置,并尽可能使棒材头部对齐。
交替打开双通道输送系统“C”形输送器,让棒材依次落到冷床矫直格栅上,使每个齿槽上放置一根棒材,以确保棒材平直度。
这种方式既适用于单线轧制,也适用于双线切分轧制。
专门设计的自动控制系统可驱动和控制整条生产线,以最大限度地提高作业精度,确保棒材在冷床上准确定位,使棒材产品获得最好的表面质量。
最新设备安装和供货业绩
达涅利摩根沙玛拥有显赫的业绩,自1970年以来共为世界各地提供和安装过106套HTC高速双通道输送系统,在小规格钢筋和圆钢棒材高速精轧方面居世界领先地位。
自2002年以来,达涅利已为南美洲、中东、远东、欧洲、印度和北非,提供(或正在供货)和已经投入生产运行的完整的最新一代高效棒材轧机(配备两套DWB高速精轧机组和两套双通道输送系统),总共达到12套。
截止到目前为止,葡萄牙SN Longo厂在生产?8mm小规格钢筋时,已经达到的最大速度为47 m/s,并可在生产过程中长期保持稳定。
不久前,在同一钢厂组织了进一步的生产试验,设备最大速度进一步达到50 m/s这一具有挑战性的目标。
结论
由于本文上面提到的许多优点(技术亮点和良好的经济效益),采用高速精轧技术可使中国庞大的建筑用钢筋市场得到进一步发展,并将建立在传统切分轧制基础上的棒材轧制技术向前推进一步。