棒材生产工艺
棒线材生产工艺

直接用作钢筋的线材表面光洁程度影响不大, 而对螺钉、弹簧、镀层等所用线材要求较高。用于 冷镦的线材对划伤比较敏感,如冷镦用线材表面缺 陷深度不得大于0.15毫米,以防止锻裂。
横列式线材轧机生产工艺灵活,易于调整,投资少,见 效快,品种多,故为地方企业经常采用的一种类型。
用于生产棒线材的钢种非常广泛,有碳素结构钢、优质碳素结构钢, 弹簧钢、碳素工具钢、合金结构钢、轴承钢、合金工具钢、不锈钢,电 热合金钢等,
其中主要是普碳钢和低合金钢,凡是需要加工成丝的钢种大都经过热 轧线材轧机生产成盘条再拉拔成丝。
因为钢种、钢号繁多,在线材生产中通常将线材 分成以下四大类:
(1)软线 (2)硬线 (3)焊线 (4)合金钢线材
线材坯料主要有初轧坯和连铸坯。 为了保证终轧温度,适应小线径和大盘重的需要。 在供坯允许的前提下,其断面应尽可能小,以减少 轧制道次。因此坯料一般较长,目前最大坯料断面 边长为150mm,最大长度为22m。 由于线材成卷供应,不便于轧后探伤和清理,故 对坯料表面质量要求较严,一般可根据坯料表面缺 陷深度估算成品表面缺陷深度。
(1)软线 指普通低碳钢热轧圆盘条,现在的牌号主要是碳素结构钢标 准中所规定的Q195、Q215、Q235和优质碳素结构钢中所规定的 10、15、20号钢等。
(2)硬线 指优质碳素结构钢类的盘条,如制绳钢丝用盘条、针织布
钢丝用盘条、轮胎钢丝、琴钢丝等专用盘条。 硬线一般碳含量偏高,泛指45号以上的优质碳素结构钢、
建筑结构用线材 Q235
制品原料用高碳钢线材 60#~80#、82B
国内棒材生产工艺
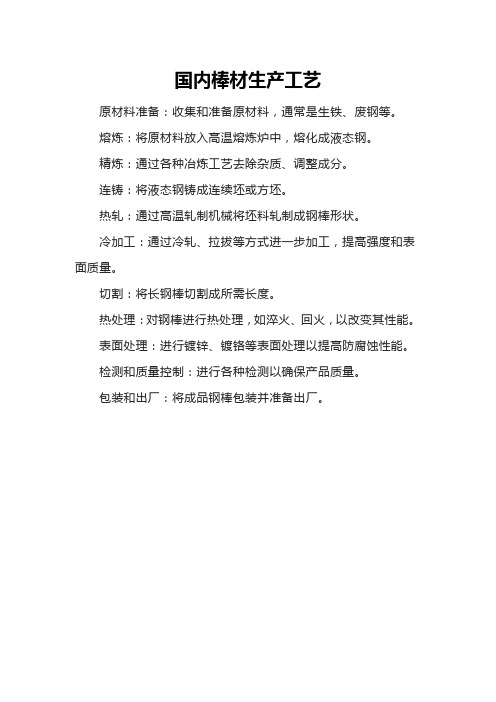
国内棒材生产工艺
原材料准备:收集和准备原材料,通常是生铁、废钢等。
熔炼:将原材料放入高温熔炼炉中,熔化成液态钢。
精炼:通过各种冶炼工艺去除杂质、调整成分。
连铸:将液态钢铸成连续坯或方坯。
热轧:通过高温轧制机械将坯料轧制成钢棒形状。
冷加工:通过冷轧、拉拔等方式进一步加工,提高强度和表面质量。
切割:将长钢棒切割成所需长度。
热处理:对钢棒进行热处理,如淬火、回火,以改变其性能。
表面处理:进行镀锌、镀铬等表面处理以提高防腐蚀性能。
检测和质量控制:进行各种检测以确保产品质量。
包装和出厂:将成品钢棒包装并准备出厂。
棒材生产工艺流程

棒材生产工艺流程
《棒材生产工艺流程》
棒材生产是一项复杂的工艺流程,包括原材料准备、锻造成型、热处理和表面处理等多个环节。
以下是典型的棒材生产工艺流程:
1. 原材料准备
棒材的原材料通常是金属材料,如钢、铜、铝等。
首先需要将原材料切割成适当的长度,然后进行加热处理,以确保材料的塑性和可锻性。
2. 锻造成型
在加热处理后,将原材料送入冲压机或锻造机进行成型。
通过锻造,原材料会逐渐变形成为所需的形状和尺寸,并去除材料表面的不良。
3. 热处理
锻造成形后的棒材需要进行热处理。
这一步骤是为了改善棒材的力学性能,包括硬度、韧性、强度等,以满足不同工程的要求。
4. 表面处理
最后一步是对棒材进行表面处理,包括酸洗、抛光、镀层等,以提高棒材的表面质量和耐蚀性。
总的来说,棒材生产工艺流程是一个繁复的过程,需要经过多
个环节的加工和处理,才能生产出高质量的棒材产品。
这一过程需要精密的设备和严格的工艺控制,以确保产品质量和工艺稳定性。
(完整版)棒材生产流程
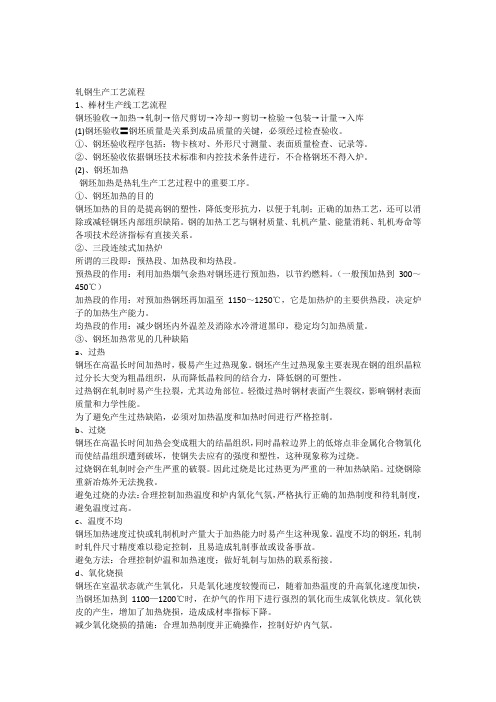
轧钢生产工艺流程1、棒材生产线工艺流程钢坯验收→加热→轧制→倍尺剪切→冷却→剪切→检验→包装→计量→入库(1)钢坯验收〓钢坯质量是关系到成品质量的关键,必须经过检查验收。
①、钢坯验收程序包括:物卡核对、外形尺寸测量、表面质量检查、记录等。
②、钢坯验收依据钢坯技术标准和内控技术条件进行,不合格钢坯不得入炉。
(2)、钢坯加热钢坯加热是热轧生产工艺过程中的重要工序。
①、钢坯加热的目的钢坯加热的目的是提高钢的塑性,降低变形抗力,以便于轧制;正确的加热工艺,还可以消除或减轻钢坯内部组织缺陷。
钢的加热工艺与钢材质量、轧机产量、能量消耗、轧机寿命等各项技术经济指标有直接关系。
②、三段连续式加热炉所谓的三段即:预热段、加热段和均热段。
预热段的作用:利用加热烟气余热对钢坯进行预加热,以节约燃料。
(一般预加热到300~450℃)加热段的作用:对预加热钢坯再加温至1150~1250℃,它是加热炉的主要供热段,决定炉子的加热生产能力。
均热段的作用:减少钢坯内外温差及消除水冷滑道黑印,稳定均匀加热质量。
③、钢坯加热常见的几种缺陷a、过热钢坯在高温长时间加热时,极易产生过热现象。
钢坯产生过热现象主要表现在钢的组织晶粒过分长大变为粗晶组织,从而降低晶粒间的结合力,降低钢的可塑性。
过热钢在轧制时易产生拉裂,尤其边角部位。
轻微过热时钢材表面产生裂纹,影响钢材表面质量和力学性能。
为了避免产生过热缺陷,必须对加热温度和加热时间进行严格控制。
b、过烧钢坯在高温长时间加热会变成粗大的结晶组织,同时晶粒边界上的低熔点非金属化合物氧化而使结晶组织遭到破坏,使钢失去应有的强度和塑性,这种现象称为过烧。
过烧钢在轧制时会产生严重的破裂。
因此过烧是比过热更为严重的一种加热缺陷。
过烧钢除重新冶炼外无法挽救。
避免过烧的办法:合理控制加热温度和炉内氧化气氛,严格执行正确的加热制度和待轧制度,避免温度过高。
c、温度不均钢坯加热速度过快或轧制机时产量大于加热能力时易产生这种现象。
棒材轧制(生产)工艺

目录热轧带肋钢筋的生产工艺及车间设计摘要:从工艺配置,设备选型,工艺控制,平面布置,设备等多方面介绍了热轧带肋钢筋的生产工艺及车间平面布置的情况,并提供了热轧线上主要机组的工艺技术参数。
关键词:热轧带肋钢筋,工艺,平面布置,设备。
Abstract: Focused on the process configuration, equipment selection, process control, layout, equipment, etc., and introduces the rolled ribbed bars production craft and workshop layout, and provides the hot line of main technical parameters.Key words:Rolled ribbed bars, craft, layout, equipment。
第一张热轧带肋钢筋国内外发展概况及建厂的必要性与可行性分析1.1螺纹钢筋市场分析与前景展望螺纹钢筋广泛应用于普通混凝土结构和预应力混凝土结构,是房屋、桥梁、隧道、水坝、桩基等建筑设施的重要材料,在国民经济中占有极其重要的地位,是我国重点发展和研究的钢材品种之一。
目前,我国有四十多个厂家生产螺纹钢筋,产量逐年上升,1982年全国总产量近166万吨,除了满足国内需要外,近年来出口钢筋数量迅速增加,1981年为18万吨,1982年约30万吨;1983年预计可达35万吨。
国内生产的螺纹钢筋,规格有小6一小40毫米,其中小40毫米规格主要供出口。
钢筋的强度级别主要为GB1499一79标准规定的1级和l级钢筋。
W级钢筋产量较低。
目前,各厂家生产螺纹钢筋的工艺,基本上为热轧、随后在冷床上空冷的传统流程。
控制轧制尚未应用于生产。
仅有少数厂家开展了轧后控制冷却工艺的试验生产。
螺纹钢筋的纹型,国内l、l 级钢筋大部分按首钢、唐钢和冶金部建筑研究总院共同制定的《热轧月牙纹钢筋技术条件》生产纵横筋不相交的月牙纹钢筋,少数仍采用国际规定的人字纹型;F级钢筋则采用不带纵筋的连续螺旋型。
棒材生产工艺简述
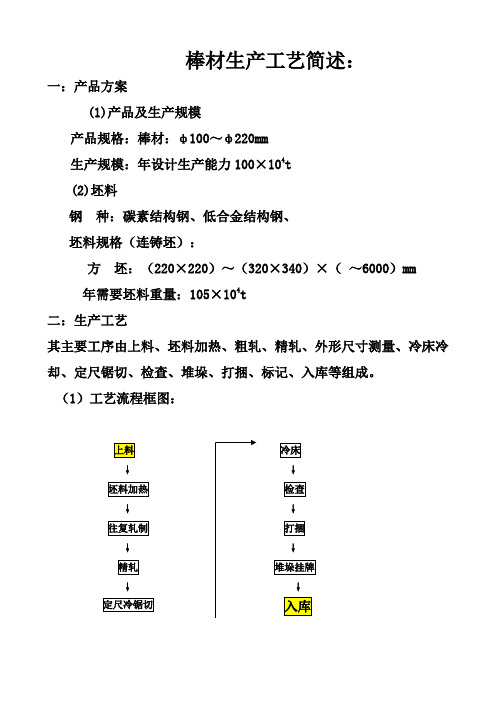
棒材生产工艺简述:一:产品方案(1)产品及生产规模产品规格:棒材:ф100~ф220mm生产规模:年设计生产能力100×104t(2)坯料钢种:碳素结构钢、低合金结构钢、坯料规格(连铸坯):方坯:(220×220)~(320×340)×(~6000)mm年需要坯料重量:105×104t二:生产工艺其主要工序由上料、坯料加热、粗轧、精轧、外形尺寸测量、冷床冷却、定尺锯切、检查、堆垛、打捆、标记、入库等组成。
(1)工艺流程框图:↓↓↓↓↓↓↓(2)工艺流程简介所有轧线设备均布置在+0.00m平台上,轧线标高为+1.40m。
当生产时,合格的连铸钢坯以单根方式从连铸热坯出坯台架送入输送辊道,输送辊道将坯料向前输送。
(坯料在输送辊道运输过程中经设在辊道中的坯料秤称重,自动显示纪录每根坯料的重量。
可不选)在输送辊道上不合格的坯料(人工右眼检查、表面缺陷、弯曲度过大和目测测长不符合要求的坯料),可由设在输送辊道侧面的剔除装置剔出。
合格的坯料输送到+2.00m 平台的辊道上,通过炉前顶钢机送入加热炉。
热送坯料进入加热炉的温度约为≈600°C左右。
当采用冷坯生产时,坯料以4~5根成组方式经输送辊道向前输送,(在输送过程中进行称重,)在辊道的另一侧设有不合格钢坯剔除装置,经人工检查表面缺陷和弯曲度达不到要求的坯料在此剔出。
坯料后经提升机构将坯料提升到+2.00m平台的辊道上,通过入炉辊道送入加热炉加热。
蓄热推钢式加热炉按不同钢种的加热制度,将坯料加热到980~1150°C。
加热好的钢坯在推钢机的推动下从炉前滑道滑出,出炉后的钢坯由输送辊道运送到粗轧机组第一架轧机中。
不合格的钢坯由钢坯剔除装置在此剔出。
钢坯首先进入粗轧机组(ф750x2)中轧制,最后送往一架两辊成品精轧机(ф650)轧制。
粗轧和中轧为往返式轧制。
合格钢坯经机前运输辊道送至第一架开坯ф750轧钢机,经机后升降台抬送与机前翻钢板翻钢,轧制4道次后,由机前移钢机送往ф750二架轧机,轧件经机后升降台抬送与机前翻钢板翻钢,轧制3道次后经二架轧机机后输送辊道,送至ф650二辊式成品精轧机,在经轧机前设有气动翻钢装置,当成品进入合金扭转导槽时,由设在机前的红外线检测仪检测到信号并发出指令,使气缸动作,完成精轧机前的翻钢,使平椭圆转为立椭圆,精轧机经过一道次轧制形成所需成品。
4032合金棒材生产工艺研究
探索 4032 合金棒材生产工艺的研究之路
4032 合金是一种高强度、高韧性的铝合金,具有良好的耐腐蚀性和机械性能,被广泛应用于航空、汽车、电子等领域。
然而,由于4032 合金具有较高的硬度和韧性,因此其生产工艺的研究一直是一个挑战。
材料的选用是生产 4032 合金棒材的第一步。
通常情况下,材料的选用需要考虑合金的化学成分、杂质含量、颗粒度等因素。
在熔炼过程中,需要对原材料进行加热和熔化,以便将其转化为液态合金。
在这个过程中,需要注意控制温度和气氛,以避免氧化和污染。
接下来是铸造环节,这个过程需要将液态合金倒入模具中,并使其凝固成所需形状的棒材。
在这个过程中,需要注意控制冷却速度和模具温度,以避免合金的变形和开裂。
最后是加工环节,这个过程包括切割、磨削、抛光等步骤,以便将棒材加工成所需尺寸和形状。
在这个过程中,需要注意选择合适的工具和工艺参数,以避免加工过程中的热变形和损耗。
除了上述环节外,还需要对生产工艺进行优化,以提高产品质量和生产效率。
例如,可以采用先进的熔炼技术,如真空熔炼、气体保护熔炼等,以减少杂质含量和氧化程度。
此外,还可以采用计算机模拟技术,模拟合金的凝固和变形过程,以预测和优化生产工艺。
棒材直接轧制
棒材直接轧制1. 引言棒材直接轧制是一种常见的金属加工方法,用于将金属坯料通过轧制工艺加工成具有特定形状和尺寸的棒材产品。
这种加工方法广泛应用于钢铁、铝合金、铜合金等金属材料的生产中,具有高效、经济、灵活等优点。
本文将对棒材直接轧制的工艺流程、设备和应用领域进行详细介绍。
2. 工艺流程棒材直接轧制的工艺流程通常包括原料准备、预轧制、精轧制、冷却和整形等步骤。
2.1 原料准备原料准备是棒材直接轧制的第一步,主要包括选择合适的金属材料、切割成适当的坯料尺寸和加热处理等操作。
金属材料的选择应根据产品的要求和生产成本进行综合考虑,常见的金属材料有碳钢、不锈钢、铝合金等。
切割成适当尺寸的坯料可以提高轧制效率和产品质量。
加热处理可以改善金属的塑性和可加工性。
2.2 预轧制预轧制是棒材直接轧制的第二步,主要目的是通过辊道的压力和摩擦力将坯料逐渐塑性变形成较小的截面尺寸。
预轧制可以提高轧制效率、减少轧制力和改善产品表面质量。
预轧制通常采用多道次的轧制,每道次的辊道间隙逐渐减小,使坯料逐渐变形。
2.3 精轧制精轧制是棒材直接轧制的第三步,主要目的是进一步减小截面尺寸、提高产品的表面质量和机械性能。
精轧制通常采用单道次的轧制,辊道间隙较小,轧制力较大。
精轧制过程中需要控制轧制温度、轧制速度和轧制力等参数,以保证产品的质量和尺寸精度。
2.4 冷却和整形冷却和整形是棒材直接轧制的最后一步,主要目的是通过冷却和整形工艺使产品获得所需的形状和尺寸。
冷却可以改善产品的力学性能和表面质量,通常采用水冷或空冷方式。
整形包括切割、修直、打标等操作,以满足产品的需求。
3. 设备棒材直接轧制需要使用一系列专用设备,包括轧机、辊道、传动系统、冷却系统和控制系统等。
3.1 轧机轧机是棒材直接轧制的核心设备,用于通过辊道的压力和摩擦力将金属坯料塑性变形成棒材产品。
轧机通常由上辊和下辊组成,辊道间隙可以调节,以适应不同的轧制需求。
轧机的类型和规格根据产品的要求和生产能力确定。
铜管棒材加工工艺简介资料
铜管棒材加工工艺简介资料精密铜镍合金节能降耗技术改造项目工艺计算说明产品方案及生产工艺简介根据产品方案及所选择的生产工艺,年产量60000 t。
其中:白铜管13000 t、紫铜和黄铜管材7000 t、型材4000 t、铜合金棒材和线材36000 t。
本项目4条生产工艺如下。
大规格管棒材生产线B10管材生产线冷凝管生产线直径小于Φ30mm 棒线材生产线工艺计算成材率合金棒线材生产线(拉一道出成品)一、B10为主的生产线:BFe10-1-1产量8000吨(直管Φ6~30×0.5~3 产量5000吨,盘管Φ6~20×0.5~3产量3000吨)工艺流程:铸锭设备流程:1、3.5吨白铜熔炼炉熔化率:3.5 t/h,有效容量:4吨,铸锭规格:Φ310×5500㎜单头牵引。
加料分析辅助时间20min,浇铸速度6m/h。
铸锭量12576吨,单台设备负荷142%,即本生产BFe10-1-1Φ310×5500㎜12576吨需要1.42台炉子。
2、锯切锯切规格按Φ310×750㎜计算,锯一次Φ310㎜时间8min 辅助时间0.5min。
一台锯床年锯切量17700吨是铸锭,Φ310×750㎜B10总需锭坯重量为12576吨,则设备负荷为71%(二班制109%)。
铸锭成材率90%算,锯切后合格锭坯量为11318吨。
3、加热炉每小时加热25节,Φ310×750㎜B实际需加热Φ310×750㎜B10锭为11318吨,占生产能力的15%(两班制为23%)。
4、50MN挤压机(Φ310×750→Φ110×12.5)挤压生产效率:25根/小时(针对BFe10-1-1 Φ310×750需挤压Φ310×750㎜B10锭为11318吨,占生产能力的15%(两班制为23%)。
综合成材率按85%计,成品量为9620吨压余按18㎜,去头尾共计400㎜,总几何废料重27㎏,铸锭Φ310×750㎜重量为504㎏,成品管重477㎏,挤压管Φ110×12.5mm长度为14000㎜。
棒材工艺操作规程(合订本)
目录第一章工艺技术概述一、生产工艺流程 (3)二、原料技术条件 (3)三、成品技术条件 (3)四、温度制度 (4)五、成品捆扎包装规定 (4)第二章加热区工艺技术操作规程一、加热区工艺操作设备性能 (5)二、钢坯验收与堆放操作规程 (6)三、钢坯装炉操作规程 (6)四、加热炉布料操作规程 (6)五、钢坯出炉操作规程 (7)六、重油点火操作规程 (7)七、提温操作规程 (7)八、加热操作规程 (8)九、待轧保温操作规程 (8)十、停炉降温操作规程 (9)十一、烘炉操作规程 (9)十二、吹扫操作规程 (9)十三、汽化冷却技术操作规程 (10)十四、CS1操作台操作规程 (10)十五、CS2操作台操作规程 (12)第三章轧制区工艺技术操作规程一、轧制区主要工艺设备性能参数轧制区主要工艺设备性能参数 (15)二、轧制压下制度 (15)三、3CS中心操作室技术操作规程 (16)四、粗中轧机组技术操作规程 (18)五、精轧机组技术操作规程 (18)六、1#飞剪技术操作规程 (19)七、2#飞剪技术操作规程 (20)八、倍尺剪夹送辊技术操作规程 (22)九、倍尺剪技术操作规程 (22)十、热处理(水冷段)技术操作过程 (23)十一、换辊技术操作规程 (25)十二、轧制区机旁操作箱操作规程 (27)十三、轧辊装配技术操作规程 (33)第四章精整区工艺技术操作规程一、概述 (35)二、冷床技术操作规程 (36)三、冷床上钢装置技术操作规程 (37)四、冷剪机技术操作规程 (37)五、冷剪后卸钢小车技术操作规程 (39)六、打捆操作规程 (39)七、成品称重技术操作规程 (39)八、成品收集、堆放、挂吊操作规程 (40)九、打牌记录技术操作规程 (40)十、4CS操作台(4AOS)操作规程 (40)十一、5CS操作台(5AOS)和6CS操作台(6AOS)操作规程 (41)第一章 工艺技术概述一、生产工艺流程二、原料技术条件连铸方坯的检查验收应符合YB/T2011的规定。
- 1、下载文档前请自行甄别文档内容的完整性,平台不提供额外的编辑、内容补充、找答案等附加服务。
- 2、"仅部分预览"的文档,不可在线预览部分如存在完整性等问题,可反馈申请退款(可完整预览的文档不适用该条件!)。
- 3、如文档侵犯您的权益,请联系客服反馈,我们会尽快为您处理(人工客服工作时间:9:00-18:30)。
其性能见表2—8
吐丝机主要性能 表2—8
项目
单位
技术性能机参数
型式
卧式
线圈直径
mm
~1050
倾角
(°)
10
最大吐线速度
m/s
150
电机功率
kw
200
电机转数
Rpm
850/1850
(7)风冷段
风冷段主要性能 表2—9
项目
单位
技术性能机参数
型式
带有佳灵系统的斯太尔摩标准型
总长度
m
~96
冷却段数
悬臂辊环式立式二辊轧机
1
Φ254/221
65
交流
550
600/1300
精
轧
机
组
19~22
45°摩根型轧机
4
Φ208/187
62
交流
5000
750/1500
23~26
4
Φ159/143
62
27~28
引进减径机
2
Φ230/210
交流
3000
850/1850
29~30
引进定径机
2
Φ160/150
飞剪技术性能表2—7
段
14
冷却速度
°C
0.3~17°C
各段间台阶高度
mm
~45
冷却段传动方式
分段集体传动
风机型式
离心式
风机数量
台
14
风机风量
M3/h
157400
(8)集卷筒
集卷筒主要性能表2—10
项目
单位
技术性能机参数
型式
双芯棒
集卷筒内径
mm
1200
定位锥竖直行程
mm
250
传动方式
液压
形成盘卷(外径/内径)
mm
1250/850
在精轧机前后设有穿水冷却装置, 精轧机前水冷线长42米
2个水箱,精轧后水冷线4个水箱通过控制水压、水量、水箱数及每个水箱的冷却喷嘴数来控制精轧和减径定径机入口处轧件温度及线材吐丝温度。
轧件经夹送辊和吐丝机形成螺旋状线圈,并落在风冷辊道上,根据处理的钢种和规格,可以调节辊道速度、风量等,以控制线材冷却速度。
2
主轧跨
24×2
360
17280
13.800
3
轧辊机修间
18
192
3456
10
立式二辊轧机Φ430
1
Φ430/370
650
交流
550
600/1300
11
水平二辊轧机Φ430
1
Φ430/370
650
交流
600
600/1300
12
立式二辊轧机Φ430
1
Φ430/370
650
交流
550
600/1300
预
精轧机组
13
水平二辊轧机Φ370
1
Φ370/305
650
交流
600
600/1300
轧机主要性能参数见表2—6。
(4)飞剪
轧线上设有粗轧前卡断剪,3台切头和事故碎断剪、1台碎断剪,
精轧机前卡断剪,其性能见表2—7。
轧机主要性能参数表2—6
名称
序号
轧机规格
数量
轧辊尺寸(mm)
电机参数
最大直径/最小直径
辊身长度
型式
功率(kw)
数(r/min)
粗轧机组
1
水平二辊轧机Φ610
1
Φ610/520
1
普通碳素结构钢
Q235
400000
25
2
优质碳素结构钢
45#80#
480000
30
3
焊条钢
320000
20
4
弹簧钢
60Mn 60Si2Mn64000ຫໍສະໝຸດ 45合金结构钢
40Gr
160000
10
6
冷镦优质钢
ML25—ML45
80000
10
7
不锈钢
8000
0.5
8
轴承钢
8000
0.5
7
合计(t)
1600000
2、轧钢工艺
2.1产品大纲及金属平衡
2.1.1产品大纲
本车间设计为2条年产量80万吨的高速线材生产线。
主要产品规格为:
圆钢: Φ5.0—Φ20mm光面线材
螺纹钢: Φ6.0—Φ18mm螺纹钢筋
生产钢种为:普通碳素结构钢、优质碳素结构钢、锚螺钢、合金钢、不锈钢、轴承钢等。
序号
钢种
代表钢号
年产量(t)
比例(%)
2.1.2产品质量及标准
(1)产品交货状态:
均以盘卷状态交货
(2)产品执行标准
—GB/T14981-94热轧盘条尺寸、外形、重量及允许偏差
—GB700-88碳素结构钢
—GB/T699-1999优质碳素结构钢技术条件
—GB6478-86冷镦钢技术条件
—GB/T3077-1999合金结构钢技术条件
—GB1222-84弹簧钢
成品跨、轧辊机修间和主电室与主轧跨平行布置。原料跨与主轧垮成丁字布置。厂区公路接通到成品跨门外运输成品,厂房的相关位置留有通道和大门。
车间组成及厂房参数见表2—13。
车间组成及厂房参数表2—13
序号
跨间名称
跨度(m)
长度(m)
厂房占地面积(m2)
吊车轨面标高(m)
1
原料跨
24
102
2448
12.000
2.1.3原料
车间所用原料为连铸坯,全部由潍钢炼钢供给,钢坯规格尺寸为:150×150×12000mm,净重为2075kg,最小坯料长度为8000mm。
坯料应满足国家标准YB2011—83中规定和YB/T004—91中规定的内容。
连铸坯年需要量为166.4万吨。
2.1.4金属平衡
车间原料用量为166.4万吨,成品量为160万吨,成材率为96%,金属平衡见表2—2。
轧制过程中产生的废料被收集在废料筐内先由叉车运至成品库,再被汽运到炼钢的废钢场。
2.3车间年工作制度和年工作时间
车间采用四班三运转连续工作制,节假日及公休日不休息,年有效工作时间为7000小时。车间年工作时间见表2—4。
车间年工作时间表2—4
工作制度
日历数(天)
计划停工时间(h)
规定工作时间(h)
停工时间(h)
轧机生产能力计算见表2—5。
轧机生产能力计算表表2—5
序号
代表规格(mm)
年计划产量(t)
终轧速度(m/s)
轧制周期(s)
理论小时产量(t/h)
年轧制时间(h)
备注
纯轧时间
间隙时间
轧制周期
1
Φ5
40000
105
131
6.0
137
54
741
2
Φ5.5
40000
105
108
6.0
114
65
615
3
Φ8
200000
100
8
比例(%)
100
按品种规格和钢种分类的产品大纲见表2—1、2—2。
产品大纲表2—1
产品大纲表2—2
序号
产品规格范围
年产量(t)
比例(%)
1
ф5-ф5.5
160000
10
2
ф6.0—ф9
400000
25
3
ф10—ф13
720000
45
4
ф14—ф18
240000
15
5
ф20
80000
5
合计
100
线材在运输机尾部落入集卷筒,然后由收集装置收集成卷。当一卷线材收集完了后,收集装置芯棒旋转,盘卷运输小车接受盘卷。然后小车移出,将盘卷送到处于等待状态的P&F线的钩子上。盘卷挂好后,运输小车返回,载有盘卷的钩子则由运输机带动沿轨道向前运行,继续进行冷却。经压紧打捆、称重、挂标、进入卸卷站卸卷,最后由电磁吊车运到成品库堆存。
(9)打捆机
打捆机引进瑞典森德斯公司打捆机两台。
型号:PCH-4KNA/4600
(10) P&F线
运输系统设备主要性能表2—11
项目
单位
技术性能机参数
型式
积放悬挂式
运输线全长
m
520
钩子总数
个
120
小车运输速度
0.25
(11)卸卷站
卸卷装置主要性能表2—12
项目
单位
技术性能机参数
储卷能力
t
6
卸卷时间
600/1300
6
立式二辊轧机Φ610
1
Φ610/520
750
交流
550
600/1300
中轧机组
7
水平二辊轧机Φ430
1
Φ430/370
750
交流
600
600/1300
8
立式二辊轧机Φ430
1
Φ430/370
750
交流
550
600/1300
9
水平二辊轧机Φ430
1
Φ430/370
650
交流
600
600/1300
连铸坯供料为热坯供料方式。
钢坯在加热炉内加热1050至1150℃后,由炉内输出辊道送出炉外。
出炉后的钢坯由保温辊道送入轧机进行全连续轧制。轧机全部呈平—立交替布置,共有30机架,分为粗、中、预精轧、精轧、减定径机五个机组,1#-18#轧机为平立交替布置,精轧机各机架轧辊轴线与水平面称45°倾角,相邻两机架间轧辊轴线90°交替布置。各架轧机均由交流变频电机单独传动,轧件在第1到第12机架之间采用微张力轧制;从12号机架至精轧机前设置量2个侧活套,8个立活套,采用无张力轧制。。