棒材生产工艺简述
棒材车间生产工艺流程
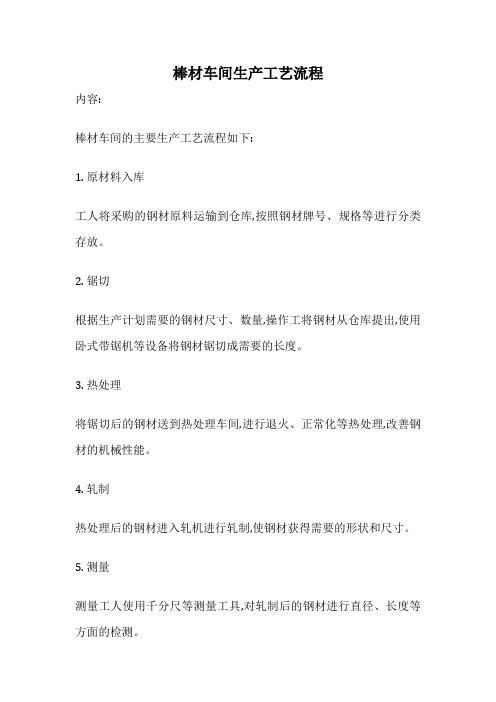
棒材车间生产工艺流程
内容:
棒材车间的主要生产工艺流程如下:
1. 原材料入库
工人将采购的钢材原料运输到仓库,按照钢材牌号、规格等进行分类存放。
2. 锯切
根据生产计划需要的钢材尺寸、数量,操作工将钢材从仓库提出,使用卧式带锯机等设备将钢材锯切成需要的长度。
3. 热处理
将锯切后的钢材送到热处理车间,进行退火、正常化等热处理,改善钢材的机械性能。
4. 轧制
热处理后的钢材进入轧机进行轧制,使钢材获得需要的形状和尺寸。
5. 测量
测量工人使用千分尺等测量工具,对轧制后的钢材进行直径、长度等方面的检测。
6. 标记
对检测合格的棒材进行打标,标明钢材牌号、规格、长度等信息。
7. 包装
工人使用牛皮纸等材料对标记完成的棒材进行包装。
8. 成品出库
按照产品编号、客户信息等对包装后的成品棒材进行堆放,然后使用叉车等设备运送到成品仓库。
以上是棒材车间从原材料入库到成品出库的主要生产工艺流程。
各环节的操作规范有利于保证棒材产品的质量。
棒线材生产工艺

一、棒线材生产现状1.2007年全国钢铁总产量达到4.9亿吨,其中棒线材的产量在总产量中比例接近40%,生产线近400条,钢铁生产明显过热;2.支撑棒线材生产的三大需求点:公路建设、住宅建设和城镇化建设随着今年下半年以来全球金融动荡,国家银根紧缩以上三个的领域投资速度明显下降,需求减弱,市场疲软;3.国际上游原料价格不断上涨,成本压力不断加大。
在这种情况下作为棒线材生产厂家,要生存下来必须开发新的产品品种,贴近市场客户需求,在生产中严格执行工艺要求提高产品质量,努力增加本厂产品的市场竞争力!棒线材的种类和用途棒材——一种简单断面型材,一般以条状交货,断面形状有圆形、方形和六角形,以及建筑用螺纹钢筋(周期断面)等;线材——是热轧产品中断面面积最小,长度最长而且以盘卷状态交货的产品,断面形状有圆形、方形、六角形和异型。
国外一般将棒材的直径定义为9~300毫米,线材的直径定义为5~40毫米,呈盘卷状态交货的产品最大直径规格为40 毫米(现在已突破60mm)。
国内一般定义为棒材直径为10~50毫米,线材一般为5~10 毫米。
棒线材的用途十分广泛,除了建筑用的螺纹钢筋和线材等被直接用作成品外,一般都要经过深加工才能制成产品。
表 1.1为棒、线的分类及其用途。
表1.1 棒、线材的产品分类和用途钢种用途一般机械零件、标准件钢筋混凝土建筑汽车零件、机械零件、标准件重要得汽车零件、机械零件、标准件汽车、机械用弹簧机械零件和标准件切削刀具、钻头、模具、手工工具轴承各种不锈钢制品冷拔各种丝材、钉子、金属网丝汽车轮胎用帘线焊条表1.2 市场对部分棒、线材产品的质量要求和生产对策冷加工材:硬线、轮胎用线材本厂产品种类及部分质量要求1.螺纹钢:(1)端部剪切正直,可以满足客户采用套筒机械联接得要求;(2)钢筋表面不准有裂纹、结疤和折叠;(3)国内要求螺纹钢表面不准存在回火马氏体。
2.碳结钢:(1)表面不得有裂纹、折叠、结疤和夹杂;(2)表面允许有局部发纹、拉裂、凹坑、麻点和刮痕,但不得超出允许得偏差;(3)表面缺陷允许清除,但是清除处应圆滑无棱角,不允许横向清除,清除宽度不得小于清除深度得 5倍,清除深度不得超过该尺寸圆钢的允许负偏差;(4)不得有分层和缩孔残余,不得有高度大于5毫米的毛刺,用压力剪切的条钢端部允许有局部变形。
棒线材生产工艺

直接用作钢筋的线材表面光洁程度影响不大, 而对螺钉、弹簧、镀层等所用线材要求较高。用于 冷镦的线材对划伤比较敏感,如冷镦用线材表面缺 陷深度不得大于0.15毫米,以防止锻裂。
横列式线材轧机生产工艺灵活,易于调整,投资少,见 效快,品种多,故为地方企业经常采用的一种类型。
用于生产棒线材的钢种非常广泛,有碳素结构钢、优质碳素结构钢, 弹簧钢、碳素工具钢、合金结构钢、轴承钢、合金工具钢、不锈钢,电 热合金钢等,
其中主要是普碳钢和低合金钢,凡是需要加工成丝的钢种大都经过热 轧线材轧机生产成盘条再拉拔成丝。
因为钢种、钢号繁多,在线材生产中通常将线材 分成以下四大类:
(1)软线 (2)硬线 (3)焊线 (4)合金钢线材
线材坯料主要有初轧坯和连铸坯。 为了保证终轧温度,适应小线径和大盘重的需要。 在供坯允许的前提下,其断面应尽可能小,以减少 轧制道次。因此坯料一般较长,目前最大坯料断面 边长为150mm,最大长度为22m。 由于线材成卷供应,不便于轧后探伤和清理,故 对坯料表面质量要求较严,一般可根据坯料表面缺 陷深度估算成品表面缺陷深度。
(1)软线 指普通低碳钢热轧圆盘条,现在的牌号主要是碳素结构钢标 准中所规定的Q195、Q215、Q235和优质碳素结构钢中所规定的 10、15、20号钢等。
(2)硬线 指优质碳素结构钢类的盘条,如制绳钢丝用盘条、针织布
钢丝用盘条、轮胎钢丝、琴钢丝等专用盘条。 硬线一般碳含量偏高,泛指45号以上的优质碳素结构钢、
建筑结构用线材 Q235
制品原料用高碳钢线材 60#~80#、82B
国内棒材生产工艺
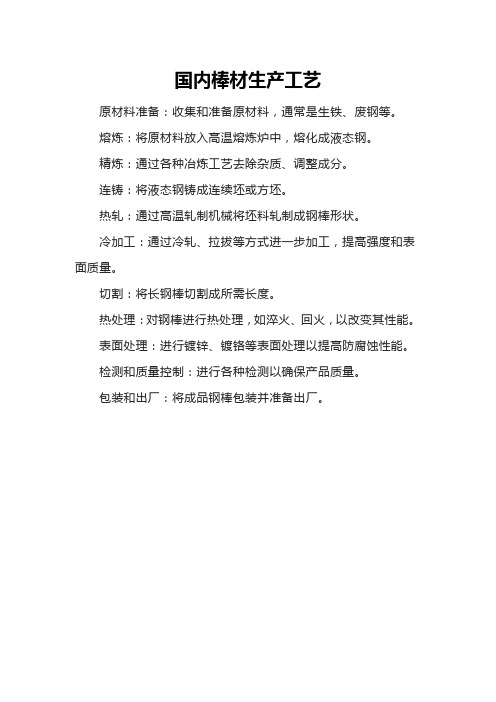
国内棒材生产工艺
原材料准备:收集和准备原材料,通常是生铁、废钢等。
熔炼:将原材料放入高温熔炼炉中,熔化成液态钢。
精炼:通过各种冶炼工艺去除杂质、调整成分。
连铸:将液态钢铸成连续坯或方坯。
热轧:通过高温轧制机械将坯料轧制成钢棒形状。
冷加工:通过冷轧、拉拔等方式进一步加工,提高强度和表面质量。
切割:将长钢棒切割成所需长度。
热处理:对钢棒进行热处理,如淬火、回火,以改变其性能。
表面处理:进行镀锌、镀铬等表面处理以提高防腐蚀性能。
检测和质量控制:进行各种检测以确保产品质量。
包装和出厂:将成品钢棒包装并准备出厂。
hrb500e带肋钢筋棒材及其生产 工艺

hrb500e带肋钢筋棒材及其生产工艺HRB500E带肋钢筋棒材是一种常用的建筑钢材,具有优异的力学性能和耐久性。
本文将介绍HRB500E带肋钢筋棒材的生产工艺及其特点。
一、HRB500E带肋钢筋棒材的生产工艺HRB500E带肋钢筋棒材主要通过以下几个步骤进行生产:1. 原材料准备:HRB500E带肋钢筋棒材的原材料是优质的碳素结构钢,通常采用轧钢厂提供的钢坯作为原材料。
钢坯经过预处理后,进入下一步的加工工艺。
2. 热轧加工:经过预处理的钢坯首先进入连铸机,通过连铸机将钢坯连续铸造成带有规定断面尺寸的钢坯。
然后将钢坯送入热轧机组,经过多道次的热轧,将钢坯轧制成带有纵向肋纹的钢筋棒材。
3. 冷却处理:热轧后的钢筋棒材需要经过冷却处理,以降低其温度并增强其力学性能。
冷却处理通常采用水冷方式,将热轧后的钢筋棒材浸入冷却水中进行快速冷却。
4. 调质处理:为了进一步提高钢筋棒材的强度和韧性,通常采用调质处理。
调质处理是通过加热和保温的方式,使钢筋棒材组织发生相变,得到细小的珠光体和贝氏体结构,从而提高其强度和韧性。
5. 表面处理:为了提高HRB500E带肋钢筋棒材的附着力和抗腐蚀性能,通常会对其表面进行处理。
常见的表面处理方法包括喷丸清理、酸洗处理、磷化处理等。
二、HRB500E带肋钢筋棒材的特点HRB500E带肋钢筋棒材具有以下几个特点:1. 高强度:HRB500E带肋钢筋棒材的强度远高于普通钢材,能够承受较大的拉力和压力。
这使得它在建筑结构中能够起到更好的支撑和抗震作用。
2. 良好的可焊性:HRB500E带肋钢筋棒材具有良好的可焊性,能够与其他钢材进行焊接,方便施工和连接。
3. 优异的韧性:HRB500E带肋钢筋棒材在受力时能够发生塑性变形,具有较好的韧性。
这使得它在抗震和抗风等极端环境下能够更好地保持结构的完整性和稳定性。
4. 良好的耐久性:HRB500E带肋钢筋棒材经过冷却处理和表面处理后,具有较好的耐腐蚀性能,能够在潮湿和腐蚀环境中长期使用。
钨钼棒材生产制造工艺

钨钼棒材生产制造工艺
钨钼棒材是一种重要的高温材料,广泛应用于航空航天、电子、化工、冶金等领域。
其生产制造工艺主要包括以下几个方面: 1. 材料选择:选择高纯度的钨、钼金属粉末作为原材料,并进行严格的质量控制,以确保产品的高质量。
2. 混合:将钨、钼金属粉末按一定比例混合,并加入一定量的流动剂和粘结剂,进行混合均匀。
3. 压制:将混合好的材料放入模具中,进行压制。
常用的压制方式包括等静压、热等静压、冷等静压等。
4. 烧结:将压制好的坯体进行烧结。
烧结过程中,需要控制温度、时间和气氛等参数,以确保产品的致密度和力学性能。
5. 加工:烧结后的钨钼棒材需要进行加工,包括车削、磨削、钻孔等,以满足客户的具体要求。
6. 检验:对生产出的钨钼棒材进行检验,包括外观质量、化学成分、机械性能等方面的检测。
以上是钨钼棒材生产制造工艺的主要内容,通过科学、严谨的制造工艺,可以确保钨钼棒材的高质量和稳定性能,满足客户的需求。
- 1 -。
钨钼棒材生产制造工艺
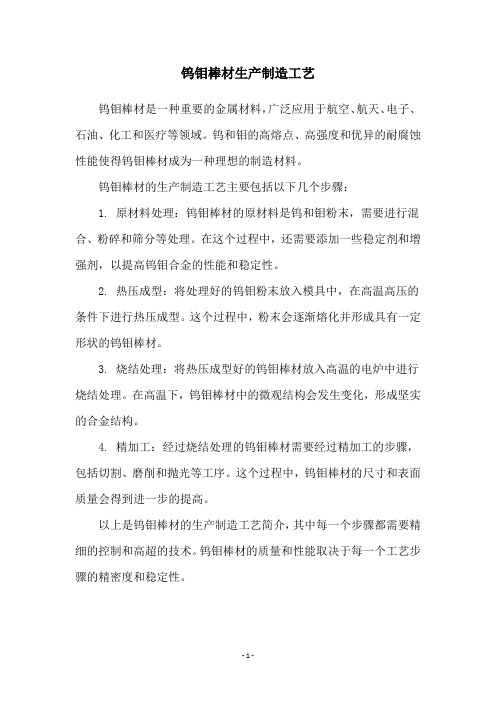
钨钼棒材生产制造工艺
钨钼棒材是一种重要的金属材料,广泛应用于航空、航天、电子、石油、化工和医疗等领域。
钨和钼的高熔点、高强度和优异的耐腐蚀性能使得钨钼棒材成为一种理想的制造材料。
钨钼棒材的生产制造工艺主要包括以下几个步骤:
1. 原材料处理:钨钼棒材的原材料是钨和钼粉末,需要进行混合、粉碎和筛分等处理。
在这个过程中,还需要添加一些稳定剂和增强剂,以提高钨钼合金的性能和稳定性。
2. 热压成型:将处理好的钨钼粉末放入模具中,在高温高压的条件下进行热压成型。
这个过程中,粉末会逐渐熔化并形成具有一定形状的钨钼棒材。
3. 烧结处理:将热压成型好的钨钼棒材放入高温的电炉中进行烧结处理。
在高温下,钨钼棒材中的微观结构会发生变化,形成坚实的合金结构。
4. 精加工:经过烧结处理的钨钼棒材需要经过精加工的步骤,包括切割、磨削和抛光等工序。
这个过程中,钨钼棒材的尺寸和表面质量会得到进一步的提高。
以上是钨钼棒材的生产制造工艺简介,其中每一个步骤都需要精细的控制和高超的技术。
钨钼棒材的质量和性能取决于每一个工艺步骤的精密度和稳定性。
- 1 -。
棒材直接轧制

棒材直接轧制摘要:1.棒材直接轧制的定义和特点2.棒材直接轧制的工艺流程3.棒材直接轧制的应用领域4.棒材直接轧制的优势和局限性正文:棒材直接轧制是一种将金属材料通过轧制设备直接加工成棒材的工艺方法。
这种工艺具有高效、节能、成本低等优点,广泛应用于金属加工领域。
下面将从棒材直接轧制的定义和特点、工艺流程、应用领域以及优势和局限性四个方面进行详细介绍。
一、棒材直接轧制的定义和特点棒材直接轧制是指将金属材料在轧制设备上直接轧制成棒材的加工方法。
这种工艺具有以下特点:1.高效:棒材直接轧制过程连续进行,生产效率高。
2.节能:与其他金属加工工艺相比,棒材直接轧制能耗较低。
3.成本低:棒材直接轧制工艺简化了生产流程,降低了生产成本。
二、棒材直接轧制的工艺流程棒材直接轧制的工艺流程主要包括以下几个步骤:1.准备:将待加工的金属材料进行预热处理,以保证其具有良好的塑性。
2.轧制:将预热后的金属材料送入轧制设备进行连续轧制,使其形状和尺寸发生变化。
3.冷却:轧制后的棒材进行冷却处理,以提高其力学性能。
4.成品:经过冷却处理后的棒材即为成品,可根据需求进行后续加工。
三、棒材直接轧制的应用领域棒材直接轧制广泛应用于以下领域:1.钢铁行业:生产各种规格和形状的钢材,如螺纹钢、圆钢等。
2.有色金属加工:生产铜、铝等有色金属的棒材。
3.矿山、冶金、建筑等领域:用于制作矿山支护材料、建筑钢筋等。
四、棒材直接轧制的优势和局限性棒材直接轧制的优势主要体现在高效、节能、成本低等方面。
但是,这种工艺也存在一定的局限性,如生产出的棒材尺寸和形状精度相对较低,对于高精度要求的产品可能不适用。
因此,在选择棒材直接轧制工艺时,需要综合考虑生产需求和工艺特点。
总之,棒材直接轧制作为一种高效、节能的金属加工工艺,在多个领域得到了广泛应用。
- 1、下载文档前请自行甄别文档内容的完整性,平台不提供额外的编辑、内容补充、找答案等附加服务。
- 2、"仅部分预览"的文档,不可在线预览部分如存在完整性等问题,可反馈申请退款(可完整预览的文档不适用该条件!)。
- 3、如文档侵犯您的权益,请联系客服反馈,我们会尽快为您处理(人工客服工作时间:9:00-18:30)。
棒材生产工艺简述:
一:产品方案
(1)产品及生产规模
产品规格:棒材:ф100~ф220mm
生产规模:年设计生产能力100×104t
(2)坯料
钢种:碳素结构钢、低合金结构钢、
坯料规格(连铸坯):
方坯:(220×220)~(320×340)×(~6000)mm
年需要坯料重量:105×104t
二:生产工艺
其主要工序由上料、坯料加热、粗轧、精轧、外形尺寸测量、冷床冷却、定尺锯切、检查、堆垛、打捆、标记、入库等组成。
(1)工艺流程框图:
↓↓
↓↓
↓↓
↓
(2)工艺流程简介
所有轧线设备均布置在+0.00m平台上,轧线标高为+1.40m。
当生产时,合格的连铸钢坯以单根方式从连铸热坯出坯台架送入输送辊道,输送辊道将坯料向前输送。
(坯料在输送辊道运输过程中经设在辊道中的坯料秤称重,自动显示纪录每根坯料的重量。
可不选)在输送辊道上不合格的坯料(人工右眼检查、表面缺陷、弯曲度过大和目测测长不符合要求的坯料),可由设在输送辊道侧面的剔除装置剔出。
合格的坯料输送到+2.00m 平台的辊道上,通过炉前顶钢机送入加热炉。
热送坯料进入加热炉的温度约为≈600°C左右。
当采用冷坯生产时,坯料以4~5根成组方式经输送辊道向前输送,(在输送过程中进行称重,)在辊道的另一侧设有不合格钢坯剔除装置,经人工检查表面缺陷和弯曲度达不到要求的坯料在此剔出。
坯料后经提升机构将坯料提升到+2.00m平台的辊道上,通过入炉辊道送入加热炉加热。
蓄热推钢式加热炉按不同钢种的加热制度,将坯料加热到980~1150°C。
加热好的钢坯在推钢机的推动下从炉前滑道滑出,出炉后的钢坯由输送辊道运送到粗轧机组第一架轧机中。
不合格的钢坯由钢坯剔除装置在此剔出。
钢坯首先进入粗轧机组(ф750x2)中轧制,最后送往一架两辊成品精轧机(ф650)轧制。
粗轧和中轧为往返式轧制。
合格钢坯经机前运输辊道送至第一架开坯ф750轧钢机,经机后升降台抬送与机前翻钢板翻钢,轧制4道次后,由机前移钢机送往ф750二架轧机,轧件经机后升降台抬送与机前翻钢板翻钢,轧制3道次后经二架轧机机后输送辊道,送至ф650二辊式成品精轧机,在经轧机前设有气动翻钢装置,当成品进入合金扭转导槽时,由设在机前的红外线检测仪检测到信号并发出指令,使气缸动作,完成精轧机前的翻钢,使平椭圆转为立椭圆,精轧机经过一道次轧制形成所需成品。
全部轧机为水平布置,最大轧制速度为3m∕s。
当轧线下游出现故障时,各道次轧孔钢由钢夹钳送至废钢车,等待运出。
成品轧件经成品输送辊道送至定尺锯切区。
由输送辊道输送的成品在辊道末端被红外线检测仪检测到后,信号指令为锯前夹紧,在汽缸的作用下夹紧成品钢,由信号传输给1800滑座式热锯机,热锯机在液压的(可用机械传动)推动下前行,完成锯切任务,由于限位开关的作用,热锯机自动退回。
此时夹紧装置已松开,由输送装置送往冷床冷却。
分段后的轧件由冷床输入辊道及下冷床装置送到9×30mm的锚链式冷床上,轧件在冷床上边前进边自然冷却。
下冷床前后由成品辊道输送到打包方向一端,(然后由链式移送机按一定间距和数量形成成排的钢材组,用卸钢装置成排送到自动打包台。
可不选)然后人工进行打包,捆扎,最后送到收集台架上进行钢材捆的称重、挂标牌和收集。
成品料捆由成品库内的双钩吊车吊到堆放区成“井”字形堆放。
三:金属平衡
金属平衡表
四:工作制度及年工作时间
生产线实行三班连续工作制,节假日及星期天不休息。
年工作时间见表
车间年工作时间分配表
五:轧制时间
以220*220*6000方坯轧100圆钢为例:(延伸系数不为准确依据)
全部时间如下:
每根重2.25T 由此可得:
(1): 2.25×3600×6080/55.58=886074T
(2): 2.25×3600×6080/36.58=1346310T
平均为: 886074T+1346310T=1116192T
即每年大约轧制成品圆钢吨位为100万吨以上。