125MN热模锻压力机拉杆测试研究
洛阳一拖参观实习报告(2012年——机械专业)

第一章前言“纸上得来终觉浅,绝知此事需躬行!”由于我们的专业实践性较强,所以生产实习是我们专业学习的重要组成部分。
此次,我们在老师的带领指导下去洛阳一拖进行生产实习,增长我们的见识,巩固课本知识,让我们了解工厂的一些基本运作过程,工艺流程以及机器设备的工作原理,这会突出我们的学习重点,为我们以后的工作奠定坚实的基础。
我校安排我们到洛阳中国一拖参观实习,开展生产实习历程,以及总结实习内容,实习感想。
通过我们自己的参观,产中相关技术人员的讲解和老师的指导,还查找各种图书资料以及到网上搜寻相关资料,使我们的的从实践中学得的知识得以巩固和完善,并能顺利完成本篇实习报告。
本次实习我们总共参观实习了五个隶属于一拖集团的分厂和农耕博物馆,下面具体谈谈本次实习的目的和历程。
一、实习目的生产实习是与今后工作生活最直接联系的,我们在生产实习过程中将完成学习到就业的过渡,作为我们材料专业,生产实习是我们知识结构中不可缺少的组成部分,并作为一个独立的项目列入专业教学计划中的。
通过生产实习,使我们学习和了解零件从原材料到成品批量生产的全过程以及生产组织管理等知识,培养学生树立理论联系实际的工作作风,以及生产现场中将科学的理论知识加以验证、深化、巩固和充实。
并培养学生进行调查、研究、分析和解决工程实际问题的能力,为后继专业课的学习、课程设计和毕业设计打下坚实的基础。
通过生产实习,拓宽我们的知识面,增加感性认识,把所学知识条理化系统化,学到从书本学不到的专业知识,并获得本专业国内、外科技发展现状的最新信息,激发学生向实践学习和探索的积极性,也是学生接触社会、了解产业状况、了解国情的一个重要途径,逐步实现由学生到社会的转变,培养我们初步担任技术工作的能力、初步了解企业管理的基本方法和技能;体验企业工作的内容和方法。
这些实际知识,为今后的学习和将从事的技术工作打下坚实的基础。
二、实习历程1、8月20日:上午一拖集团简介及安全教育下午一拖洛阳工程机械分公司2、8月21日:上午一拖股份有限公司锻造厂下午一拖股份有限公司热处理厂3、8月22日: 上午一拖股份有限公司齿轮厂下午一拖股份有限公司第一装配厂4、8月23日: 上午一拖股份有限公司农耕博物馆大学已过去四分之三,我们即将奔向社会,但是仅仅在书本学来的知识还不足以透彻的了解我们专业,。
热模锻压力机开发研究报告
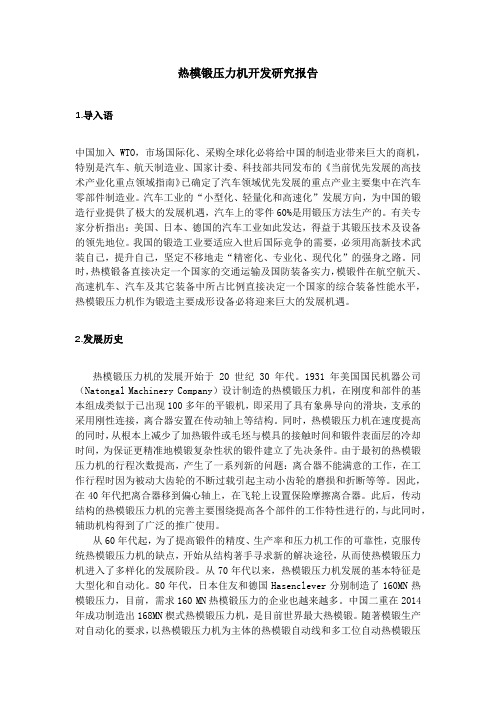
热模锻压力机开发研究报告1.导入语中国加入WTO,市场国际化、采购全球化必将给中国的制造业带来巨大的商机,特别是汽车、航天制造业、国家计委、科技部共同发布的《当前优先发展的高技术产业化重点领域指南》已确定了汽车领域优先发展的重点产业主要集中在汽车零部件制造业。
汽车工业的“小型化、轻量化和高速化”发展方向,为中国的锻造行业提供了极大的发展机遇,汽车上的零件60%是用锻压方法生产的。
有关专家分析指出:美国、日本、德国的汽车工业如此发达,得益于其锻压技术及设备的领先地位。
我国的锻造工业要适应入世后国际竞争的需要,必须用高新技术武装自己,提升自己,坚定不移地走“精密化、专业化、现代化”的强身之路。
同时,热模锻备直接决定一个国家的交通运输及国防装备实力,模锻件在航空航天、高速机车、汽车及其它装备中所占比例直接决定一个国家的综合装备性能水平,热模锻压力机作为锻造主要成形设备必将迎来巨大的发展机遇。
2.发展历史热模锻压力机的发展开始于20世纪30年代。
1931年美国国民机器公司(Natongal Machinery Company)设计制造的热模锻压力机,在刚度和部件的基本组成类似于已出现100多年的平锻机,即采用了具有象鼻导向的滑块,支承的采用刚性连接,离合器安置在传动轴上等结构。
同时,热模锻压力机在速度提高的同时,从根本上减少了加热锻件或毛坯与模具的接触时间和锻件表面层的冷却时间,为保证更精准地模锻复杂性状的锻件建立了先决条件。
由于最初的热模锻压力机的行程次数提高,产生了一系列新的问题:离合器不能满意的工作,在工作行程时因为被动大齿轮的不断过载引起主动小齿轮的磨损和折断等等。
因此,在40年代把离合器移到偏心轴上,在飞轮上设置保险摩擦离合器。
此后,传动结构的热模锻压力机的完善主要围绕提高各个部件的工作特性进行的,与此同时,辅助机构得到了广泛的推广使用。
从60年代起,为了提高锻件的精度、生产率和压力机工作的可靠性,克服传统热模锻压力机的缺点,开始从结构著手寻求新的解决途径,从而使热模锻压力机进入了多样化的发展阶段。
锻造液压机原理

天津大学2007届高职专科毕业设计论文题目:锻造液压机的原理姓名:年级:2007届院系:电气与自动化工程学院电气与自动化技术摘要液压机主机部分包括液压缸、横梁、立柱及充液装置等。
动力机构由油箱、高压泵、控制系统、电动机、压力阀、方向阀等组成。
液压机采用PLC控制系统,通过泵和油缸及各种液压阀实现能量的转换,调节和输送,完成各种工艺动作的循环。
该系列液压机具有独立的动力机构和电气系统,并采用按钮集中控制,可实现手动和自动两种操作方式。
该液压机结构紧凑,动作灵敏可靠,速度快,能耗小,噪音低,压力和行程可在规定的范围内任意调节,操作简单。
在本设计中,通过查阅大量文献资料,设计了液压缸的尺寸,拟定了液压原理图。
按压力和流量的大小选择了液压泵,电动机,控制阀,过滤器等液压元件和辅助元件。
关键词:锻造,液压系统,液压机, PLC目录目录 (Ⅰ)第1章国内外重型锻压设备的发展概况 (1)第2章锻造液压机系统 (4)2.1 锻造液压机的系统原理 (4)2.1.1液压系统工作原理 (4)2.2.液压系统分析 (5)第3章锻造液压机的改进设计方案及分析 (6)3.1 锻造液压机的该机方案 (6)3.2 液压机的改进方案分析 (7)第4章PLC在液压机控制系统改造中的应用 (7)4.1 工艺原理分析 (8)4.2 液压系统控制过程分析 (8)4.2.1 液压机执行部件动作过程分析 (8)4.3 PLC电控系统设计 (10)4.3.1 硬件设计与软件实现 (10)4.3.2 三地操作 (14)4.4 PLC可靠性保护措施 (15)4.4.1电动机组保护 (15)4.4.2机械设备的保护 (15)4.5 PLC程序设计 (16)第4章液压机电气控制系统 (18)4.1 液压机电气控制方案设计 (18)4.1.1液压机电气控制方案选择 (18)4.1.2电气控制要求与总体控制方案 (19)4.2 液压机电气控制电路设计 (20)4.2.1液压机主电路设计 (20)4.2.2液压机控制电路设计 (20)4.3 液压机电气控制系统分析 (22)参考文献 (23)附录 (24)致谢 (25)第一章绪论重型锻压设备是随着国民经济的发展,特别是随着汽车、航空、宇航、动力、造船、冶金、石油、化工、铁道、交通等工业部门对大型锻件、模锻件、冲压件日益增长的需要而迅速发展起来的。
21m长拉杆锻后热处理研究
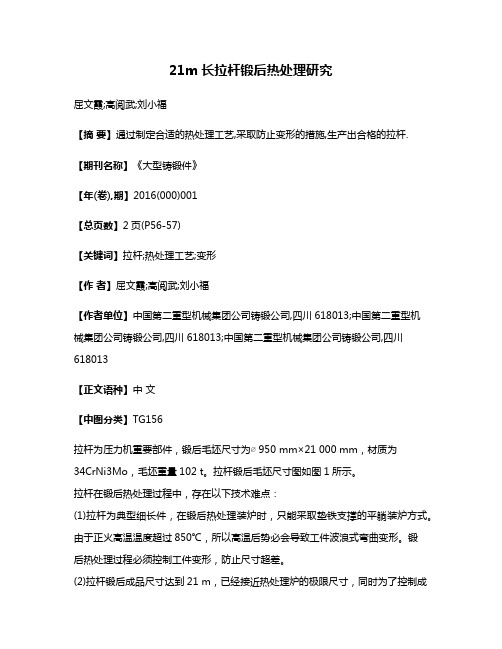
21m长拉杆锻后热处理研究屈文霞;高阅武;刘小福【摘要】通过制定合适的热处理工艺,采取防止变形的措施,生产出合格的拉杆.【期刊名称】《大型铸锻件》【年(卷),期】2016(000)001【总页数】2页(P56-57)【关键词】拉杆;热处理工艺;变形【作者】屈文霞;高阅武;刘小福【作者单位】中国第二重型机械集团公司铸锻公司,四川618013;中国第二重型机械集团公司铸锻公司,四川618013;中国第二重型机械集团公司铸锻公司,四川618013【正文语种】中文【中图分类】TG156拉杆为压力机重要部件,锻后毛坯尺寸为∅950 mm×21 000 mm,材质为34CrNi3Mo,毛坯重量102 t。
拉杆锻后毛坯尺寸图如图1所示。
拉杆在锻后热处理过程中,存在以下技术难点:(1)拉杆为典型细长件,在锻后热处理装炉时,只能采取垫铁支撑的平躺装炉方式。
由于正火高温温度超过850℃,所以高温后势必会导致工件波浪式弯曲变形。
锻后热处理过程必须控制工件变形,防止尺寸超差。
(2)拉杆锻后成品尺寸达到21 m,已经接近热处理炉的极限尺寸,同时为了控制成本,采取两件拉杆同炉处理,因此,锻后热处理过程中很难保证工件的均温效果,最终导致工件内部晶粒度不均匀,从而影响工件性能及UT可探性。
锻后热处理必须制定有效措施,保证工件的均匀性。
针对上述分析的技术难点,锻后热处理工艺采取了多项措施,主要措施如下:(1)工件变形措施拉杆装炉时,只能平躺在500 mm高的锥形垫铁上。
通常每5 m左右安置一根垫铁,考虑到拉杆属于细长件,应按每2 m~3 m安置一根垫铁,并且两端垫铁必须处于同一水平面,中部垫铁处于同一水平面,最终保证工件中心线与水平面平行。
装炉示意图(按比例)如图2所示。
减小垫铁间距,能有效控制工件在高温过程的扭曲变形,但并不能通过这唯一的措施控制拉杆的超差变形。
在锻后热处理过程中必须采取校直工序。
锻后热处理过程中,高温过程变形最大,所以有意在高温结束后,吊空冷过程中安排一次校直工序,目的是大大减小工件的高温变形。
热模锻压力机整机刚度估计与结构优化
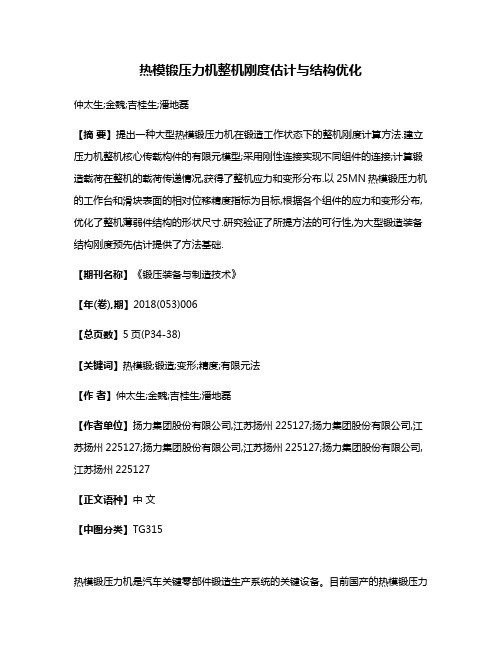
热模锻压力机整机刚度估计与结构优化仲太生;金魏;吉桂生;潘地磊【摘要】提出一种大型热模锻压力机在锻造工作状态下的整机刚度计算方法.建立压力机整机核心传载构件的有限元模型;采用刚性连接实现不同组件的连接;计算锻造载荷在整机的载荷传递情况,获得了整机应力和变形分布.以25MN热模锻压力机的工作台和滑块表面的相对位移精度指标为目标,根据各个组件的应力和变形分布,优化了整机薄弱件结构的形状尺寸.研究验证了所提方法的可行性,为大型锻造装备结构刚度预先估计提供了方法基础.【期刊名称】《锻压装备与制造技术》【年(卷),期】2018(053)006【总页数】5页(P34-38)【关键词】热模锻;锻造;变形;精度;有限元法【作者】仲太生;金魏;吉桂生;潘地磊【作者单位】扬力集团股份有限公司,江苏扬州225127;扬力集团股份有限公司,江苏扬州225127;扬力集团股份有限公司,江苏扬州225127;扬力集团股份有限公司,江苏扬州225127【正文语种】中文【中图分类】TG315热模锻压力机是汽车关键零部件锻造生产系统的关键设备。
目前国产的热模锻压力机基本沿用上世纪80年代引进的德国EUMUCO原有技术,很难满足汽车关键零件智能化精密锻造生产系统的需求。
压力机的整机刚度是沿压力机滑块方向工作载荷与主机在加载方向上变形量之比,是保证压力机锻造精度最重要的指标之一。
如果压力机的工作载荷一定,刚度越小,变形量也越大,对成形零件质量的影响也越大。
单纯从压力机抵抗弹性变形的能力来说,压力机的刚度参数应该越大越好,但压力机的制造成本也会越高。
文献[1]论述了热模锻压力机结构和载荷传递特点。
文献[2]从工程经验的角度指出了压力机刚度所需要的机身最大应力和静挠度值。
针对压力机结构刚度和振动问题,根据载荷传递特点,有限元法已用于多种吨位的压力机机身结构分析:竖直或水平分力被加载于机身有限元模型进行结构应力与变形计算[3]-[6];有限元模态分析揭示出了多种吨位压力机机身的振动特性[7][8]。
211165218_重型院研发的125MN预拉伸机组通过最终验收

马爱民,等:汽车前围内板铝合金冲压工艺设计工艺技术/信息报道Stamping process design of aluminum alloy for automobilefront inner panelMa Aimin,Xia Dewei,Duan Guangpo(Zhongwang Aluminum Co.,Ltd.,Beijing100020,China)Abstract:At present,the use of lightweight materials is an important way to realize the lightweight of automobile.Through the de⁃sign of stamping process program for the front inner panel of an all aluminum alloy automobile,the problems such as wrinkling,crack⁃ing,thinning and springback occurred in the stamping process of aluminum alloy automobile panel are discussed.By using the finite el⁃ement analysis software,the process plan of the front inner panel is simulated and analyzed.According to the analysis results,the pro⁃cess plan is optimized,and its feasibility is verified.The final processprogram is determined,which provides technical support and theo⁃retical basis for the development and trial production of aluminum alloy automobile panel.Key words:aluminum alloy;lightweight;front inner panel;stamping process重型院研发的125MN预拉伸机组通过最终验收125MN预拉伸机组作为宝武铝业年产600kt铝合金铸造及深加工项目(一期航天航空及汽车铝合金板项目)的核心设备,也是目前国内拉伸力最大的航空级铝合金板材拉伸机组,日前通过了最终考核验证。
洛阳一拖实习报告
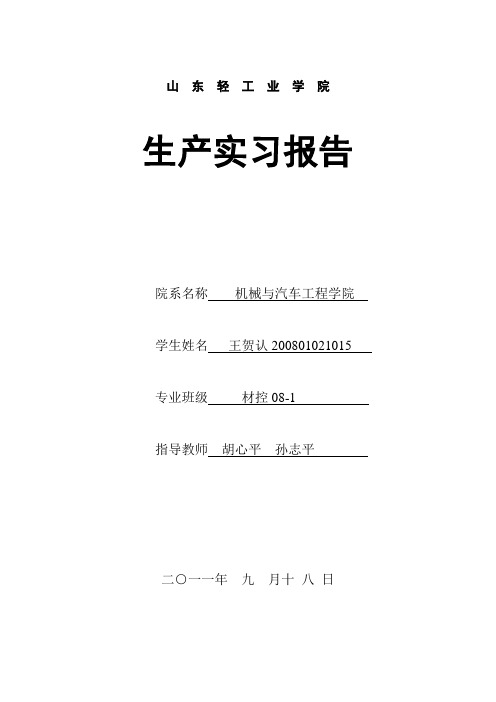
山东轻工业学院生产实习报告院系名称机械与汽车工程学院学生姓名王贺认200801021015 专业班级材控08-1指导教师胡心平孙志平二○一一年九月十八日实习情况一览表时间地点实习内容指导教师备注0830上午机电楼B125实习动员胡心平0831-0906山东轻工业学院实习预备知识学习0908上午一拖职教中心教室入厂安全教育以及一拖情况介绍0908下午一拖工程机械厂一拖热处理厂参观胡心平孙志平0909上午一拖锻造厂一拖齿轮厂参观胡心平孙志平0913-0915山东轻工业学院复习以及总结洛阳一拖实习报告2011年9月7日的早上我们山东轻工业学院材控专业的80多号人浩浩荡荡的向着洛阳出发,因为学校为我们安排了一周的实习,实习的地点就是洛阳一拖,因为这个是中国农机行业唯一的特大型企业,所以一拖的实习就成了我们的重中之重。
一、实习目的或研究目的(一)、安全教育我们是八号凌晨一点到达一拖的,然后上午工厂负责我们实习的老师给我们讲解了很重要的实习安全知识和一拖的发展历史,老师给我们看安全生产记录还有事故案例,一些注意事项加血淋淋的案例,这些血淋淋的案件给人们敲响了警钟。
老师给我们提了好多要求,我们都必须做到,毕竟事故发生了谁也负担不起。
厂内危害:1.机械性危害: 机械加工过程中(如机械转动时的刀削磨钻等)造成的伤害,居各类伤害之首。
2.化学物质危害: 如强酸、强碱、汞、铅、一氧化碳等使人中毒、窒息、烧伤等伤害。
3.燃烧爆炸危害:如钢水爆炸,化学物质爆炸等。
4.热危害:人与热件、热机直接接触 5.电器危害:灼伤、火灾等6.其他危害:如紫外线,辐射,低温等。
由于这些危害对人体的伤害很大,因此对我们着装要求然后第二天就开始了我们为期一周的实习。
(二)、一拖概况第一拖拉机股份有限公司是中国内地在香港上市的唯一农机制造与销售企业其前身第一拖拉机制造厂,创建于 1955年,是我国“一五”期间兴建的156个国家重点项目之一,是中国农机行业唯一的特大型企业,1990年被国务院企业管理委员会评为“国家一级企业”,1997年,中国一拖集团将与拖拉机相关的业务、资产、负债人员重组后进行股份制改造,依法设立了第一拖拉机股份有限公司。
800MN模锻压机用大拉杆热处理调质研究
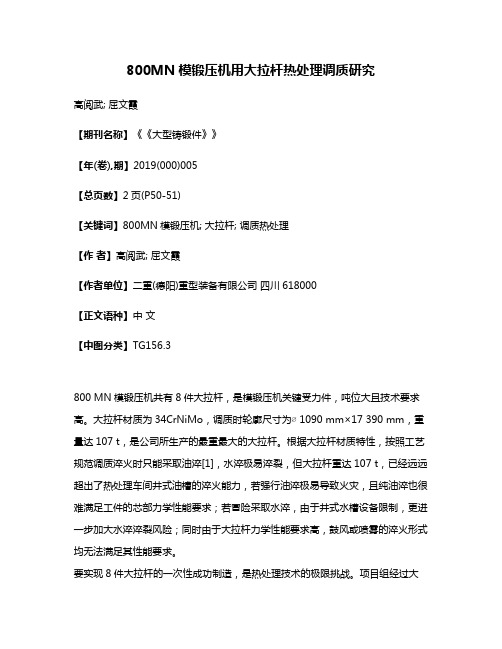
800MN模锻压机用大拉杆热处理调质研究高阅武; 屈文霞【期刊名称】《《大型铸锻件》》【年(卷),期】2019(000)005【总页数】2页(P50-51)【关键词】800MN模锻压机; 大拉杆; 调质热处理【作者】高阅武; 屈文霞【作者单位】二重(德阳)重型装备有限公司四川618000【正文语种】中文【中图分类】TG156.3800 MN模锻压机共有8件大拉杆,是模锻压机关键受力件,吨位大且技术要求高。
大拉杆材质为34CrNiMo,调质时轮廓尺寸为∅1090 mm×17 390 mm,重量达107 t,是公司所生产的最重最大的大拉杆。
根据大拉杆材质特性,按照工艺规范调质淬火时只能采取油淬[1],水淬极易淬裂,但大拉杆重达107 t,已经远远超出了热处理车间井式油槽的淬火能力,若强行油淬极易导致火灾,且纯油淬也很难满足工件的芯部力学性能要求;若冒险采取水淬,由于井式水槽设备限制,更进一步加大水淬淬裂风险;同时由于大拉杆力学性能要求高,鼓风或喷雾的淬火形式均无法满足其性能要求。
要实现8件大拉杆的一次性成功制造,是热处理技术的极限挑战。
项目组经过大量方案讨论,数据统计分析,在技术上进行大胆创新,在没增加任何设备、工装附具的情况下,利用现有设备,突破设备应用瓶颈,成功实现大拉杆的调质淬火,最终一次性成功制造,8件大拉杆的力学性能全部一次性满足技术要求。
1 大拉干调质前情况介绍1.1 化学成分要求大拉杆材质为34CrNiMo,化学成分要求如表1所示。
大拉杆长度达到17.39 m,冶炼过程中主要控制工件两端C偏析和合金聚集,同时将P、S含量控制在≤0.01%,提高钢水的纯净度,减少大拉杆后续的淬裂风险。
表1 34CrNiMo钢化学成分要求Table 1 Chemical composition requirements of 34CrNiMo steelCSiMnPSCrNiMo0.30~0.380.17~0.370.40~0.70≤0.035≤0.0351.40~1.70≤0.400.15~0.301.2 力学性能要求大拉杆力学性能要求为:Rm≥690 MPa,ReL≥490 MPa,A≥12%,Z≥32%,KU2≥31 J,根据制造技术规范JBT 5000.8—2007要求,大拉杆在工件两端的13半径处各套取一组试棒分别进行力学性能检验,两端力学性能均必须合格。
- 1、下载文档前请自行甄别文档内容的完整性,平台不提供额外的编辑、内容补充、找答案等附加服务。
- 2、"仅部分预览"的文档,不可在线预览部分如存在完整性等问题,可反馈申请退款(可完整预览的文档不适用该条件!)。
- 3、如文档侵犯您的权益,请联系客服反馈,我们会尽快为您处理(人工客服工作时间:9:00-18:30)。
125MN热模锻压力机拉杆测试研究摘要论述125mn热模锻压力机的检测方法和结果,并就实测数据和影响因数进行了分析。
125mn热模锻压力机是由左、右侧机架、上梁、下机架通过四根拉杆组合而成一个坚实的铸钢机架,拉杆的拉力是保证主体设备正常运行关键参数。
拉杆通过加热方法使其伸长并拧紧螺母,降温后拉杆收缩产生拉应力,本次测试主要测试拉杆加热预紧后的应变值,并以此计算拉杆预紧力。
关键词应力;应变;预紧力;检测
中图分类号th2 文献标识码a 文章编号
1674-6708(2012)64-0145-02
1 测量设备、元器件及计算公式
1.1 测量设备及元器件
1.1.1 测量设备
本次测试选定了主要的测量设备为江苏东华测试技术有限公司制造的dh3815静态应变测试系统。
1.1.2 测量元器件及主要参数
拉杆应变测量主要测量元件为应变片,采用中航工业电测仪器股份有限公司公司制造的高温应变片bb350-4bb。
该型号应变片电阻值350ω,灵敏系数:k=2.04,使用温度<250℃。
1.1.3 应变片传感器的工艺要求
在测试中应变片的粘贴要符合作为传感器的粘贴工艺。
为此,
选用北京化工厂生产的r-1型502高温胶作为粘胶,按照应变片传感器的标准工艺要求进行布置。
1.2 计算公式
1.2.1 应变仪读数到测试应变的换算
本次拉杆应变片采用半桥接法引入应变仪。
应变仪读数和测试应变的换算如下:
对半桥接法:
其中:为测试应变,i为应变仪读数,为材料泊松比。
1.2.2 应变到应力以及预紧力的计算
对于125mn模锻压机,拉杆为单向应力状态。
根据虎克定律,应力由测试应变表示为:式中,e为弹性模量(),为测试应变。
由于拉杆主要段为等截面杆,根据测试得到的应力,可计算出拉杆预紧力为:
式中:f0预紧力,为轴向应力,a为横截面积(a前=3 138cm2,a后=2 533cm2)。
2 拉杆应变测试及计算分析
2.1测点布置
此次应力测试我们采用了静态应变测量技术,选用二片应变片组成的应变花(90度角),根据设计要求,拉杆应力测点是在四根拉杆中部距二次灌浆面4 300mm处布置一组应变片组成半桥,每测点布二组接至静态应变仪。
如下图所示。
2.2测试过程
125mn热模锻压力机由左、右侧机架、上梁、下机架通过四根拉杆加热预紧组合而成一个坚实的铸钢机架,四根拉杆的预紧力参数测试尤为重要。
根据现场装配过程包含了拉杆的加热-降温过程。
在整个过程中对拉杆应变进行监控测试,应变值由应变测试系统自动记录。
现场通过加热方式使拉杆达到设计要求的伸长量,拧紧螺母后自然降温,利用拉杆收缩施加预紧力。
拉杆测点布置图
2.3 补偿及预置平衡
2.3.1 补偿
应变的测试主要考虑温度的补偿。
但对于拉杆应变片用半桥接法,拉杆应变片采用轴向和径向成90度的应变花接法,实现温度应变自补偿,温度应变不影响电桥平衡。
2.3.2 预置平衡与修正的考虑
根据安装工艺要求,为了消除接触面初始间隙,对拉杆螺母施加了一定的初始拧紧力矩,装配测试时以此作为测试初始状态,各测点可能有一定初始应变,所有测点预调平衡,应变仪读数归零。
2.4 测试结果及计算分析
为消除接触面间隙,在预紧前先给各螺母施加了初始力矩,该过程从11月15日开始,对四根拉杆同时加热(持续时间超过了14
个小时),伸长量达到要求后,拧紧螺母,自然冷却到常温,实现拉杆的预紧。
根据降温较稳定状态下的测点应变读数(取稳定时的值),应变实测数据见下表:
2.4.1 取值分析
从上表所测数据中,1号拉杆上的测点1与测点9,2号拉杆上的测点2与测点10的数据差距较大,3号拉杆上的测点3已损坏,4号拉杆上的测点4与测点12的数据相差较小,原因如下:由于本次加热的加热杆总功率不够、放置不均匀(偏心)和通风状态不好等,拉杆热量为此分布严重不均,造成出沙孔贴片处300mm直径范围内不同位置处温度差异很大,以致于有些位置温度过高造成应变片失效或部分失效,从而使得两组数据的差异也较大。
在测试当天晚上,测试人员经过通宵监测,用测温器测试,发现当加热快结束时,已加热14小时,在1号拉杆上的测点1的表面温度79℃,而测点9的温度就达到103℃;2号拉杆上的测点2的表面温度87℃,而测点10的温度就已达到105℃;3号拉杆上的测点3点处温度高达120℃,应变片已经失效,而测点11的温度是92℃;4号拉杆上的测点4点处温度71度,测点12的温度是78℃,这组数据就比较接近。
经过观察,在各高温区的应变片有的部分失效,有的已经损坏,而温度较低处的应变片是完全正常的。
故取采集数据为:1号拉杆测点1;2号拉杆测点2;3号拉杆测点11;4
号拉杆测点4。
2.4.2 测试数据及计算数据如下表所示
3主要测试结论及建议
1)前后拉杆预紧力最大分别为4 502t、3 324t。
根据前后拉杆预紧力要求分别为5 000t和3 900t,结合现场实际情况,根据计算结果,得知预紧力未达到设计要求。
2)按照拉杆加热预紧测试所采用的静态应变测试法的要求,拉杆预紧时贴片处表面温度不应超过80℃,加热预紧所需的加热棒功率应达到360kw,加热温度控制在450℃~470℃,加热时间应在9h左右即可达到要求的伸长量。
一般此类测试在每根拉杆上只需贴一组应变片,而为确保能采集到有效数据及通过两组数据进行相互验证,现场测试人员加贴了一组应变片;本次测试贴片严格按规范操作。
但本次加热总功率虽经技术人员的改进,也只有228kw,为达到加热预紧要求的伸长量,加热温度后来达到550℃~570℃,加热时间达14.5h,既没有满足加热温度控制在450℃,也没有满足加热时间这两个指标。
因此两组应变片中,有的完全失效,有的部分失效。
3)对于实测数据与设计要求偏小约10%~15%的情况,分析如下:根据现场安装情况,原定应在规定期间完成的预紧,由于加热杆等原因,经过多次加热,加热时去掉了热电偶,没有进行温度控制,致使加热棒在加热过程中就已经熔化,拉杆内部局部温度相当高,后两次加热温度也在550℃以上,多次超过450℃的高温加热,不排除可能造成拉杆组织
相变,使内应力发生变化,可能是造成预紧力偏小的主要原因。
参考文献
[1]吴宗岱,陶宝祺主编.应变电测试原理及技术.
[2]邵明亮,李文望主编.机械工程测试技术.
[3]刘鸿文主编.材料力学.。