典型铸铁件铸造工艺设计与实例
各种典型铸造技术的原理和方法
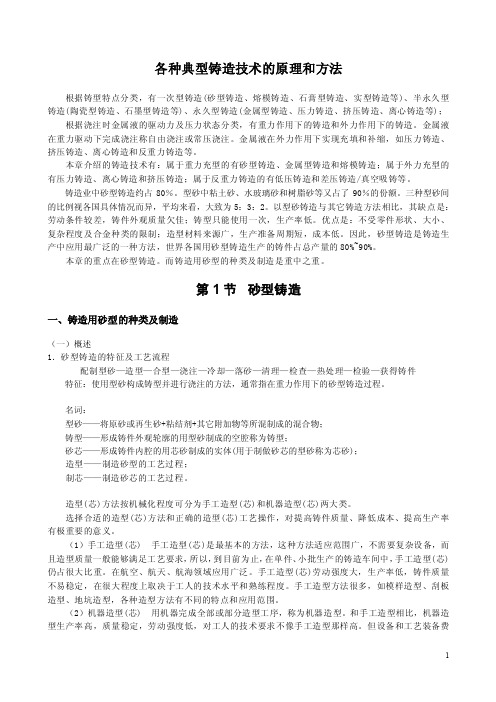
各种典型铸造技术的原理和方法根据铸型特点分类,有一次型铸造(砂型铸造、熔模铸造、石膏型铸造、实型铸造等)、半永久型铸造(陶瓷型铸造、石墨型铸造等)、永久型铸造(金属型铸造、压力铸造、挤压铸造、离心铸造等);根据浇注时金属液的驱动力及压力状态分类,有重力作用下的铸造和外力作用下的铸造。
金属液在重力驱动下完成浇注称自由浇注或常压浇注。
金属液在外力作用下实现充填和补缩,如压力铸造、挤压铸造、离心铸造和反重力铸造等。
本章介绍的铸造技术有:属于重力充型的有砂型铸造、金属型铸造和熔模铸造;属于外力充型的有压力铸造、离心铸造和挤压铸造;属于反重力铸造的有低压铸造和差压铸造/真空吸铸等。
铸造业中砂型铸造约占80%。
型砂中粘土砂、水玻璃砂和树脂砂等又占了90%的份额。
三种型砂间的比例视各国具体情况而异,平均来看,大致为5:3:2。
以型砂铸造与其它铸造方法相比,其缺点是:劳动条件较差,铸件外观质量欠佳;铸型只能使用一次,生产率低。
优点是:不受零件形状、大小、复杂程度及合金种类的限制;造型材料来源广,生产准备周期短,成本低。
因此,砂型铸造是铸造生产中应用最广泛的一种方法,世界各国用砂型铸造生产的铸件占总产量的80%~90%。
本章的重点在砂型铸造。
而铸造用砂型的种类及制造是重中之重。
第1节砂型铸造一、铸造用砂型的种类及制造(一)概述1.砂型铸造的特征及工艺流程配制型砂—造型—合型—浇注—冷却—落砂—清理—检查—热处理—检验—获得铸件特征:使用型砂构成铸型并进行浇注的方法,通常指在重力作用下的砂型铸造过程。
名词:型砂——将原砂或再生砂+粘结剂+其它附加物等所混制成的混合物;铸型——形成铸件外观轮廓的用型砂制成的空腔称为铸型;砂芯——形成铸件内腔的用芯砂制成的实体(用于制做砂芯的型砂称为芯砂);造型——制造砂型的工艺过程;制芯——制造砂芯的工艺过程。
造型(芯)方法按机械化程度可分为手工造型(芯)和机器造型(芯)两大类。
选择合适的造型(芯)方法和正确的造型(芯)工艺操作,对提高铸件质量、降低成本、提高生产率有极重要的意义。
铸造成形技术铸造工艺设计

①选择铸件的浇注位置及分型面 ②型芯的数量、形状及其固定方法 ③确定工艺参数(加工余量、起模
斜度、圆角、 收缩率) ④浇冒口、冷铁形状、尺寸及其布
置
铸造工艺图——在零件图上用各种工艺 符号表示出铸造工艺方案的图形
它是制造模样和铸型,进行生产准备 和铸件检验的依据——基本工艺文件。
使型腔和主要芯位于下箱,便于下 芯、合型和检查型腔尺寸。
3.铸造工艺参数的确定
铸造工艺参数包括收缩余量、 加工余量、起模斜度、铸造圆角、 芯头、芯座等。
①收缩余量:
为了补偿收缩,模样比铸件图纸尺寸 增大的数值称收缩余量。收缩余量的大小 与铸件尺寸大小、结构的复杂程度和铸造 合金的线收缩率有关,常常以铸件线收缩 率表示:
工艺 打箱、清理等工艺操作 根据批量大小填写必要条
卡片 过程及要求
件
⑨ 综合整个设计内容
实例分析:
以C6140车 床进给箱体 为例分析毛 坯的铸造工 艺方案如下: 质量约35Kg。
车床进给箱体零件图
该零件没有特殊质量要求的表面, 仅要求尽量保证基准面D不得有明显 铸造缺陷,以便进行定位。
材料:灰铸铁HT150,勿需考虑补缩。
为了便于采用机器造型、尽量 避免活块,故凸台和凹槽均应 用型芯来形成。
为了克服基准面朝上的缺点, 必须加大D面的加工余量。
单件、小批量生产,采用手 工造型,使用活块造型较型芯 更为方便。同时,因铸件的尺 寸允许偏差较大,九个轴孔不 必铸出。
此外,应尽量降低上型高度, 以便利用现有砂箱。
显然,在单件生产条件下,宜 采用方案II或方案III。
在制订铸造工艺方案时,主要应着 眼于工艺上的简化。
1.分型面
三个方案供选择: 方案I:分型面在轴孔 的中心线上。 方案II:从基准面D分 型,铸件绝大部分位于 下型。 方案III:从B面分型, 铸件全部置于下型。
铸造工艺学课程设计案例

成果报告需以PDF格式提交,同时附上所有相关数据和图表。
报告内容
报告需包含设计思路、工艺流程、数据分析及结论等部分,要求 内容详实、逻辑清晰。
成果展示形式和内容安排建议
展示形式
鼓励采用多媒体形式进行展示,如PPT、视频等。
内容安排
建议按照设计背景、设计思路、工艺流程、数据 分析、结论与展望等顺序进行展示。
时间安排
每个小组展示时间不超过20分钟,需提前做好时 间规划。
课程设计评价标准及成绩评定方法
01
评价标准
将从设计创新性、实用性、技术 难度、报告质量等方面进行综合 评价。
02
成绩评定方法
03
优秀作品选拔
采用百分制评分,其中设计创新 性占30%、实用性占20%、技术 难度占20%、报告质量占30%。
铸造材料选择
根据零件使用要求、生产批量和成本 等因素,选择合适的铸造合金,如铸 铁、铸钢、铝合金等。
性能要求
铸造合金应具有良好的流动性、收缩 性、偏析倾向小等性能,以保证铸件 质量。同时,合金成分和性能应符合 相关标准或技术条件的规定。
03
案例分析:典型铸件生产工艺设计
铸件结构分析与设计优化建议
根据评分结果,选拔出优秀作品 进行表彰和奖励。
THANKS
感谢观看
推广新技术和新材料
积极推广先进的铸造技术和新材料,如3D打印技术、高性能铸造合 金等,提高铸件的精度和性能。
加强人才培养
加强铸造领域的人才培养和引进,提高从业人员的专业素质和技能水 平,为铸造行业的发展提供有力的人才保障。
06
课程设计成果展示与评价标准
课程设计成果提交要求说明
提交时间
所有成果需在课程结束前一周内提交,逾期将不予受理。
典型铸铁件铸造工艺设计与实例

典型铸铁件铸造工艺设计与实例叙述铸造生产中典型铸铁件一一气缸类铸件、圆筒形铸件、环形铸件、球墨铸铁曲轴、盖类铸件、箱体及壳体类铸件、阀体及管件、轮形铸件、锅形铸件及平板类铸件的铸造实践。
内容涉及材质选用、铸造工艺过程的主要设计、常见主要铸造缺陷及对策等。
第1章气缸类铸件1.1低速柴油机气缸体1.1.1 一般结构及铸造工艺性分析1.1.2 主要技术要求1.1.3 铸造工艺过程的主要设计1.1.4 常见主要铸造缺陷及对策1.1.5 铸造缺陷的修复1.2中速柴油机气缸体1.2.1 一般结构及铸造工艺性分析1.2.2 主要技术要求1.2.3 铸造工艺过程的主要设计1.3空气压缩机气缸体1.3.1 主要技术要求1.3.2 铸造工艺过程的主要设计第2章圆筒形铸件2.1 气缸套2.1.1 一般结构及铸造工艺性分析2.1.2 工作条件2.1.3 主要技术要求2.1.4 铸造工艺过程的主要设计2.1.5 常见主要铸造缺陷及对策2.1.6 大型气缸套的低压铸造2.1.7 气缸套的离心铸造2.2冷却水套2.2.1 一般结构及铸造工艺性分析2.2.2 主要技术要求2.2.3 铸造工艺过程的主要设计2.2.4 常见主要铸造缺陷及对策2.3烘缸2.3.1 结构特点2.3.2 主要技术要求2.3.3 铸造工艺过程的主要设计2.4活塞2.4.1 结构特点2.4.2 主要技术要求2.4.3 铸造工艺过程的主要设计2.4.4 砂衬金属型铸造第3章环形铸件3.1活塞环3.1.1 概述3.1.2 材质3.1.3 铸造工艺过程的主要设计3.2 L形环3.2.1 L形环的单体铸造3.2.2 L形环的筒形铸造第4章球墨铸铁曲轴4.1 主要结构特点4.1.1曲臂与轴颈的连接结构4.1.2 组合式曲轴4.2主要技术要求4.2.1 材质4.2.2 铸造缺陷4.2.3 质量检验4.2.4 热处理4.3铸造工艺过程的主要设计4.3.1 浇注位置4.3.2 模样4.3.3 型砂及造型4.3.4 浇冒口系统4.3.5 冷却速度4.3.6 熔炼、球化处理及浇注4.4 热处理4.4.1 退火处理4.4.2 正火、回火处理4.4.3 调质(淬火与回火)处理4.4.4 等温淬火4.5常见主要铸造缺陷及对策4.5.1 球化不良及球化衰退4.5.2 缩孔及缩松4.5.3 夹渣4.5.4 石墨漂浮4.5.5 皮下气孔4.6大型球墨铸铁曲轴的低压铸造第5章盖类铸件5.1柴油机气缸盖5.1.1 一般结构及铸造工艺性分析5.1.2 主要技术要求5.1.3铸造工艺过程的主要设计5.2空气压缩机气缸盖5.2.1 一般结构及铸造工艺性分析5.2.2 主要技术要求5.2.3 铸造工艺过程的主要设计5.3其他形式气缸盖5.3.1 一般结构5.3.2 主要技术要求5.3.3铸造工艺过程的主要设计第6章箱体及壳体类铸件6.1大型链轮箱体6.2增压器进气涡壳体6.3排气阀壳体6.4球墨铸铁机端壳体6.5球墨铸铁水泵壳体6.6球墨铸铁分配器壳体第7章阀体及管件7.1灰铸铁大型阀体7.2灰铸铁大型阀盖7.3球墨铸铁阀体7.4管件7.5球墨铸铁螺纹管件7.6球墨铸铁管卡箍7.6.1 主要技术要求7.6.2 铸造工艺过程的主要设计7.6.3 常见主要铸造缺陷及对策第8章轮形铸件8.1 飞轮8.2调频轮8.3中小型轮形铸件8.4球墨铸铁轮盘第9章锅形铸件9.1大型碱锅9.2中小型锅形铸件第10章平板类铸件10.1大型龙门铳床落地工作台10.2大型立式车床工作台10.3大型床身中段10.4 大型底座中国机械工业出版社精装16开定价:299元。
高强度厚大断面球墨铸铁花盘的铸造工艺设计

\ \
。
铸钢件加工困难 ,缺陷多,所以选用 了高强度球 墨
铸 铁 材 质 ,铸 件 重 4 t 0 ,属 厚 大 断 面 球 墨 铸 铁 件 , 结 构 尺寸 如 附 图所 示 。铸 件特 点 及技 术 要 求如 下 。
—
/
/
() b
B
( )铸件材质QT o —3 1 6 0 ,机加工后硬度要求
台面 的 质 量 和 铸 件 尺 寸 精 度 ,方 便 下 芯 及 砂 芯 固
()铸件加工后需做静平衡试验 ,因而对砂芯 5
的尺 寸 一致性 、分度 和定 位尺 寸等 精 度要 求严 格 。
3_ 0
:
造 参 磊
工
机床铡造业技术专题
定 ,使 各 工序 操 作 方便 ,依 据 厚大 断 面 球 墨铸 铁 件
0. 5。
+ 11 ,主 轴 孔 及 卡爪 槽+1 m1。 起 模斜 度 1 T1 5 I3 T 5 I
5 mm ,砂 芯 间隙 2 mm ,分 型 负数 一4 m。铸 造 圆 a r 角R1 mm。设 计 了6 卡 板 ,测 量 砂 芯 的 尺 寸 精 5 个 度 、分 度 及定 位 尺 寸 。砂 箱 吃砂 量4 0 0 mm,合箱 后
t;
‘
上jI O 1 C 司
1。 5k 上 l 一
C
L ' n
一 《 {
0 0
卜
1 。 5,
L\ 工
I
7 7
拉 筋 共2 个
0
鲁 l 量 f ] } . 量
t / l /
I
缩松 、气 孔 、夹 渣 和 冷隔 等 缺 陷 。不 得有 尺 寸 、化
轮盘类铸铁件铸造工艺
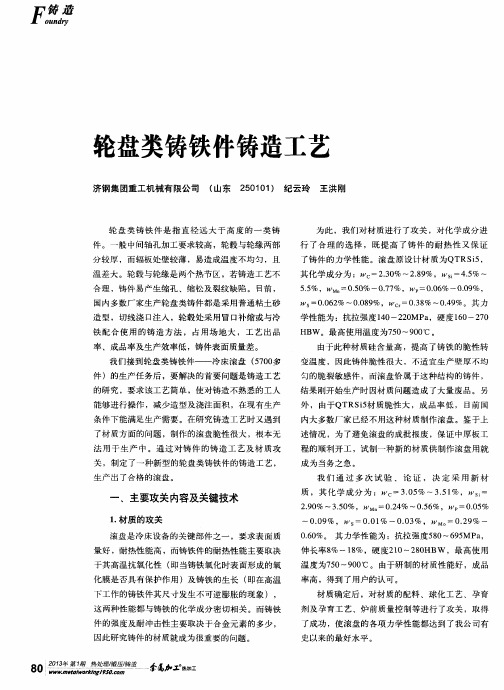
足 够 的 造 型及 浇 注 面 积 ,且 工 艺 复杂 ,对铸 造 不 熟 的工 人 无法 操 作 ,满 足 不 了生 产 要 求 。
为 此 ,我 们 通 过 比较 ,选 择 了金 属 型树 脂 砂 组
2 . 9 0 % ~3 . 5 0% , WM = 0 . 2 4% ~ 0 . 56 % , WP =0 . 0 5 %
、
主要攻关 内容及关键技术
1 . 材质 的攻关
滚盘 是 冷 床 设备 的关 键 部 件之 一 ,要 求表 面 质 量 好 ,耐 热 性 能 高 ,而铸 铁 件 的 耐热 性 能 主 要取 决
s =0 . 0 6 2 % ~0 . 0 8 9 %,Wc =0 . 3 8 %~0 . 4 9 %。其 力
学 性 能 为 :抗 拉 强度 1 4 0 ~2 2 0 MP a ,硬 度 1 6 0 ~2 7 0 H B W 。最 高使 用温 度为 7 5 0 ~9 0 0 C。 由于 此种 材 质 硅 含 量高 ,提 高 了铸 铁 的脆 性 转 变温 度 ,因此 铸 件 脆性 很 大 ,不适 宜 生 产 壁厚 不 均 匀 的脆 裂 敏感 件 ,而 滚盘 恰 属于 这 种 结 构 的铸 件 , 结 果 刚 开 始生 产 时 因材 质问 题造 成 了大 量废 品 。另 外 , 由于QT R S i 5 材 质 脆性 大 ,成 品率 低 , 目前 国 内 大 多数 厂 家 已经 不 用这 种 材 质制 作 滚 盘 。鉴 于 上
芯 叠浇 工 艺 ,即 采 用 金属 型 芯 盒树 脂砂 制 芯 ,然 后
大型球铁件的铸造工艺设计

大型灰铁铸件的铸造工艺

大型灰铁铸件的铸造工艺
大型灰铁铸件的铸造工艺可以分为以下几个步骤:
1. 模具准备:选择合适的灰铁模具,并进行准备工作,包括清洁、涂抹模脱剂等。
2. 铸型制备:将模具装配到铸造设备上,根据铸件的形状和尺寸,在模具中制备出与铸件相对应的空腔,可以采用砂型、金属型等不同的铸造方式。
3. 熔炼铁水:将铁矿石和其他合金原料放入熔炉中,通过高温熔炼,得到液态的铁水。
4. 铸注铁水:将熔融的铁水倒入预先准备好的铸型中,注意控制铁水的温度和流量,保证铁水充分填充整个铸型空腔。
5. 固化冷却:等到铁水完全填充整个铸型后,放置一段时间,让铁水逐渐固化和冷却,使铸件形成固态。
6. 脱模清理:待铁水完全固化后,拆卸模具,取出铸件。
对于有砂模的铸件,需要清理剩余砂粒和其他杂质。
7. 后处理:根据实际需要,对铸件进行修磨、去毛刺、清除氧化皮等后处理工
序,以提高铸件的精度和表面质量。
需要注意的是,大型灰铁铸件的铸造工艺还需要考虑铁水的浇注方式、冷却方式、铸型材料的选择等因素,以保证铸件的质量和性能。
- 1、下载文档前请自行甄别文档内容的完整性,平台不提供额外的编辑、内容补充、找答案等附加服务。
- 2、"仅部分预览"的文档,不可在线预览部分如存在完整性等问题,可反馈申请退款(可完整预览的文档不适用该条件!)。
- 3、如文档侵犯您的权益,请联系客服反馈,我们会尽快为您处理(人工客服工作时间:9:00-18:30)。
典型铸铁件铸造工艺设计与实例
叙述铸造生产中典型铸铁件一一气缸类铸件、圆筒形铸件、环形铸件、球墨铸铁曲轴、盖类铸件、箱体及壳体类铸件、阀体及管件、轮形铸件、锅形铸件及平板类铸件的铸造实践。
内容涉及材质选用、铸造工艺过程的主要设计、常见主要铸造缺陷及对策等。
第1章气缸类铸件
1.1低速柴油机气缸体
1.1.1 一般结构及铸造工艺性分析1.1.2 主要技术要求
1.1.3 铸造工艺过程的主要设计1.1.4 常见主要铸造缺陷及对策1.1.5 铸造缺陷的修复
1.2中速柴油机气缸体
1.2.1 一般结构及铸造工艺性分析1.2.2 主要技术要求
1.2.3 铸造工艺过程的主要设计1.3空气压缩机气缸体
1.3.1 主要技术要求
1.3.2 铸造工艺过程的主要设计第2章圆筒形铸件
2.1 气缸套
2.1.1 一般结构及铸造工艺性分析2.1.2 工作条件
2.1.3 主要技术要求
2.1.4 铸造工艺过程的主要设计2.1.5 常见主要铸造缺陷及对策2.1.6 大型气缸套的低压铸造
2.1.7 气缸套的离心铸造
2.2冷却水套
2.2.1 一般结构及铸造工艺性分析2.2.2 主要技术要求
2.2.3 铸造工艺过程的主要设计2.2.4 常见主要铸造缺陷及对策2.3烘缸
2.3.1 结构特点
2.3.2 主要技术要求2.3.3 铸造工艺过程的主要设计
2.4活塞
2.4.1 结构特点
2.4.2 主要技术要求
2.4.3 铸造工艺过程的主要设计
2.4.4 砂衬金属型铸造
第3章环形铸件
3.1活塞环
3.1.1 概述
3.1.2 材质
3.1.3 铸造工艺过程的主要设计
3.2 L形环
3.2.1 L形环的单体铸造
3.2.2 L形环的筒形铸造
第4章球墨铸铁曲轴
4.1 主要结构特点
4.1.1曲臂与轴颈的连接结构
4.1.2 组合式曲轴
4.2主要技术要求
4.2.1 材质
4.2.2 铸造缺陷
4.2.3 质量检验
4.2.4 热处理
4.3铸造工艺过程的主要设计
4.3.1 浇注位置
4.3.2 模样
4.3.3 型砂及造型
4.3.4 浇冒口系统
4.3.5 冷却速度
4.3.6 熔炼、球化处理及浇注
4.4 热处理
4.4.1 退火处理
4.4.2 正火、回火处理
4.4.3 调质(淬火与回火)处理
4.4.4 等温淬火
4.5常见主要铸造缺陷及对策
4.5.1 球化不良及球化衰退
4.5.2 缩孔及缩松
4.5.3 夹渣
4.5.4 石墨漂浮
4.5.5 皮下气孔
4.6大型球墨铸铁曲轴的低压铸造
第5章盖类铸件
5.1柴油机气缸盖
5.1.1 一般结构及铸造工艺性分析
5.1.2 主要技术要求
5.1.3铸造工艺过程的主要设计
5.2空气压缩机气缸盖
5.2.1 一般结构及铸造工艺性分析
5.2.2 主要技术要求
5.2.3 铸造工艺过程的主要设计
5.3其他形式气缸盖
5.3.1 一般结构
5.3.2 主要技术要求
5.3.3铸造工艺过程的主要设计
第6章箱体及壳体类铸件
6.1大型链轮箱体
6.2增压器进气涡壳体
6.3排气阀壳体
6.4球墨铸铁机端壳体
6.5球墨铸铁水泵壳体
6.6球墨铸铁分配器壳体
第7章阀体及管件7.1灰铸铁大型阀体7.2灰铸铁大型阀盖
7.3球墨铸铁阀体
7.4管件
7.5球墨铸铁螺纹管件
7.6球墨铸铁管卡箍
7.6.1 主要技术要求
7.6.2 铸造工艺过程的主要设计7.6.3 常见主要铸造缺陷及对策第8章轮形铸件
8.1 飞轮
8.2调频轮
8.3中小型轮形铸件
8.4球墨铸铁轮盘
第9章锅形铸件
9.1大型碱锅
9.2中小型锅形铸件
第10章平板类铸件
10.1大型龙门铳床落地工作台
10.2大型立式车床工作台
10.3大型床身中段
10.4 大型底座
中国机械工业出版社精装16开定价:299元。