基于ANSYSworkbench的汽车发动机连杆力学性能分析
CAE(ansys)汽车发动机连杆课程设计论文

连杆简化模型的有限元分析一.个人任务1.连杆简化模型的静力学分析2.参数化研究与目标驱动优化设计二.分析所需数据见《汽车设计课程设计指导书》P6 明细三.连杆的实体模型和网络模型连杆简化实体模型连杆简化网络模型四.连杆原设计在各种接触条件下进行有限元分析后得到的变形图和应力图方案一:连杆小头里铜环内壁施加均匀压强 P=52MPa载荷施加图小铜环与连杆小头在不同接触条件下的接触分析:1.bonded2. frictionless3.rough4. frictional_0.15 摩擦系数0.15最大值TotalDeformationEquivalentStressNormalStressTotalDeformation2TotalDeformation3均匀载荷0.084824mm 312.83MPa 246.05MPa 0.084447mm 0.080688mm轴承载荷0.083415 311.31 260.34在方案一的载荷情况下:在DS中进行拓扑优化方案二:连杆小头里铜环内壁施加轴承载荷 X方向的力F=5*sqrt2*3*e-6*52*e6=1102.92N Bonded - Solid To Solid在方案二的载荷情况下:在DS中进行拓扑优化五.局部网格细化的研究方案一在施加均匀压力的条件下:方案二在施加轴承载荷的条件下:最大Total Equivalent Normal Total Total值Deformation Stress Stress Deformation2 Deformation3 均匀0.084824mm 312.83MPa 246.05MPa 0.084447mm 0.080688mm 载荷0.083415 311.31 260.34轴承载荷六.参数化研究和目标驱动的优化设计(在DS中进行优化设计)在DS仿真后建立DX模型进行测试,测试出在既定的形状下模型的最理想受载情况在进行目标驱动优化前,利用响应图查看整个系统的特性七.对设计结构进行修改取变量有铜环直径,连杆小头直径,连杆大头到连杆小头之间的距离优化后的受载情况:. ..八.具体分析操作中遇到的问题汇总1.建模过程中(DM 模型),要考虑在DS 模型中的成角度曲面的约束和施加载荷对连杆大头和小头进行扇形建模2.在建模的过程中为了构造用于施加约束和载荷的扇形曲面,在构造扇形的过程中要一个扇形一个扇形的建模,建模完一个扇形后,在准备建立下一个扇形以前,记得对已经建立的扇形模型进行冻结操作3.网格划分过程中,首先用的是整体自动网格划分,后来进行了局部细化网格分析,而细化网格的方法大致有两种,一个用的是Contact Sizing ,一个是Part Relevance ,自己对比分析两种方法4.在施加边界条件时发现,连杆小头里的铜环和连杆小头在不同的接触条件下仿真分析出来的结果很不相同,本人分别用了bounded, frictionless, rough, fritional (摩擦系数0.15)进行了对比分析5.对连杆小头里面铜环内壁90°曲面的载荷施加,采取了两种对比分析,一是均匀压强载荷分析,一是轴承载荷分析,即在连杆轴线方向,离连杆小头轴心距离越远,受到的轴线方向的载荷越大,根据圆曲面的对称性求出了轴线方向,即X 方向的力F=1102.92N6.目标驱动优化分析(DOE )中八.课程设计总结CAE 技术在汽车的设计和改善技术中的应用越来越多,仿真的方法越来越接近汽车在实际使用中的运行工况,从而改善了汽车的设计和完善水平,减少了实车实验的成本,缩短了整车开发的周期,能更快,更好的解决汽车在实际使用中的问题。
基于ANSYS的发动机连杆分析设计
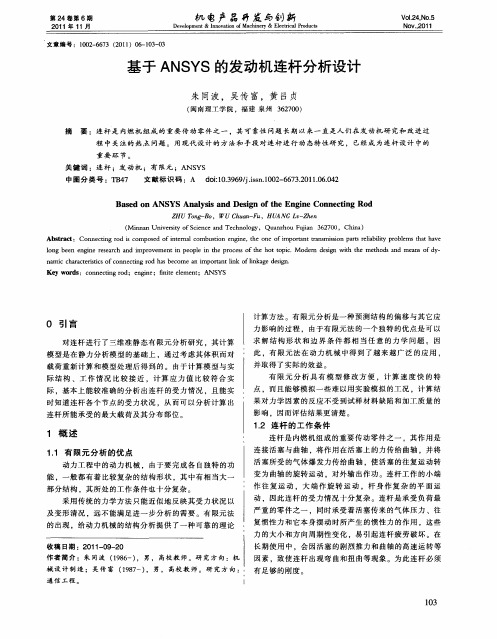
21 0 1年 1 1月
De eo me t& I n v t no c i ey& E e t c lP o u t v lp n n o ai f o Ma hn r lcr a r d cs i
机 电 产 品 开 发 与 新
VO.4, . I NO5 2
约 为 27 5 162N;② 活 塞组 的惯 性力 包 括 活塞 、活 塞环 、
活 塞 销 、活 塞 销 卡 环 ,其 总质 量 记 为 M ,以活 塞 加 速 度 i作 变 速 直 线 运 动 , 则 活 塞 组 的 惯 性 力 为 一
收 稿 日期 :2 1 — 9 2 0 10 — 0 作 者 简 介 :朱 同 波 (9 6 ) 男 , 高校 教 师 。 研 究 方 向 :机 18- , 械 设 计 制 造 ; 吴 传 富 (9 7 ,男 , 高校 教 师 。研 究 方 向 : 18 -)
通信工程 。
长期 使 用 中 。会 因活塞 的剧 烈推 力 和曲轴 的 高速运 转 等 因素 ,致 使 连杆 出现 弯 曲和 扭 曲等现 象 。为此 连杆 必 须 有足 够 的刚度 。
此 ,有 限 元 法 在 动 力 机 械 中得 到 了 越 来 越 广 泛 的 应 用 ,
模 型是 在 静力 分析 模 型的基 础上 ,通 过 考虑 其 体积 而对
载 荷重 新计 算 和模 型处 理后 得 到 的。 由于计 算模 型 与实
并 取 得 了实际 的效益 。
际 结 构 、工 作 情 况 比较 接 近 .计 算 应 力 值 比较 符 合 实
22 连杆 几何 实体模 型 的建 立 .
本 文所 研 究 的汽 车连杆 如 图 1 示 ,连 杆 的厚度 为 所 05n,图 中标 注尺 寸 的单位 均 为英制 。在 小 头孔 的 内测 .i 9 。 罔 内承 受 P 10 p i 面 载 荷 作 用 ,利 用 有 限 元 0范 = 00s 的 分 析 该连 杆 的 受 力状 态 。连 杆 的材料 属 性 为杨 氏模 量 . E干2 O Pa泊 松 比为 03 0G I。 由于 连杆 的 结 构 和 载 荷 均 对 称 . 因此 在 分 析 时 只 需 采用 一 半 进行 分 析 。在 A S S中采 用 由底 向 上 的建 NY 模 方式 .用 2 0节点 的 S LD 5单 元 划 分 网格 并 用 P G O I9 C 求 解 器求 解 。图 2用 A S S软 件 直接 建 立 的连 杆 实 体 NY
基于ANSYS Workbench车用柴油发动机曲轴强度有限元分析

曲轴建模参数如下:
曲轴受热胀 冷缩 的影 响, 所 以 对 曲 轴 大 端 进 行 X㊁ Y 方 向 的 约束㊂
( 1) 主轴径直径 D j = 100 mm; ( 2) 连杆轴颈直径 r = 82 mm; ( 3) 活塞直径 D p = 126 mm; ( 4) 爆发压 p max = 13������ 5 MPa; ( 5) 连杆质量 m r = 3������ 639 kg; ( 7) 连杆中心距 L = 153 mm;
26.539
2
28.745
3
7.799 7
152.00
4
表 2㊀ 固有频率计算结果
174.58 5 308.94 6
9.135 0 7.760 5
9.389 0 8.399 9
404.45
7
442.99
8
9.592 9
578.53
9
740.07 13.426
10
7.768 7
841.63
11
922.88 10.579
钢, 参数如表 1 所 示㊂ 采 用 Solid186 单 元对 曲 轴 进 行 网 格 划 分 , 连杆轴颈与曲柄壁的连接处和主轴径与曲柄壁过渡圆角 连接处均采用单元长度为 3 mm 的四面体网格 ; 主轴径和连杆 轴颈处采用单元长度为 5 mm 的四面体网格 ; 曲柄臂处采用单 元长度为 8 mm 的四面体网格 ; 模拟轴承支座采用单元长度为
建立曲轴有限元模型, 如图 2 所示㊂ 曲轴材料采用 45 号
1������ 5㊀ 模态结果及分析
型, 表 2 为固有频率计算结果, 图 3 为典型的振型图㊂
通过分析计算, 得到了曲轴前 12 阶的固有频率和固有振
基于Workbench的航空发动机连杆有限元分析

基于Workbench的航空发动机连杆有限元分析作者:付贵郭湘川来源:《科技风》2018年第10期摘要:连杆是航空发动机中一个重要的传力零件,由于它承受的是变载荷,容易疲劳损坏,所以对其强度有很高的要求。
本文以某型发动机连杆为研究对象,首先对连杆进行了受力分析,确定了连杆两种极限受力状态。
文章通过Solidworks对连杆进行三维建模,然后再导入Ansys Workbench 有限元分析软件进行分析,得到应力分布云图,找出的危险位置,为连杆强度设计分析提供理论依据。
关键词:航空发动机;Workbench;连杆;应力分析连杆是航空活塞发动机中一个重要的传力零件,它用于连接活塞与曲轴,将活塞的往复直线运动转化成曲轴的旋转运动。
发动机工作时连杆承受混合气体的爆发力、摆动惯性力和往复惯性力的作用,这些受力不仅有大小的变化,而且还有方向的变化[1]。
由于连杆承受了变载荷,连杆就容易产生疲劳断裂。
本文首先对连杆进行了受力分析,找出了连杆所受最大拉力和压力的位置并确定了最大拉伸和压缩两种有限元模型。
利用Solidworks对连杆进行三维建模,再导入Ansys Workbench中进行有限元分析,最终得到应力分布云图,找出的危险位置,为连杆强度设计分析提供理论依据。
1 连杆载荷受力分析连杆的运动机构是一个曲柄滑块机构,活塞直线运动通过连杆带动曲轴的旋转运动,连杆运动简图如图1所示。
图中:l—连杆长度,x—活塞位移,S—活塞行程,a—曲柄转角,β—连杆摆角,r—曲柄半径。
连杆在工作过程中需要承受通过活塞传递的燃气爆发力、往复运动质量的惯性力以及由于自身摆动所产生的惯性力[2]。
燃气爆发力Fg为:Fg=(Pg-Pa)×πd24(1)式中:Pg为气体压力,d为气缸直径。
活塞的往复惯性力为:Fj=mjrw2(cosa+λcos2a)(2)则作用在连杆上的力FL为:FL=(Fg+Fj)/cosβ(3)经过以上分析可知连杆连杆在运动过程中主要受爆发力和惯性力作用,当爆发力和惯性力分别最大的时候会出现两种工况,即最大压缩和拉伸。
基于Workbench仿真的内燃机曲柄连杆机构动力学分析
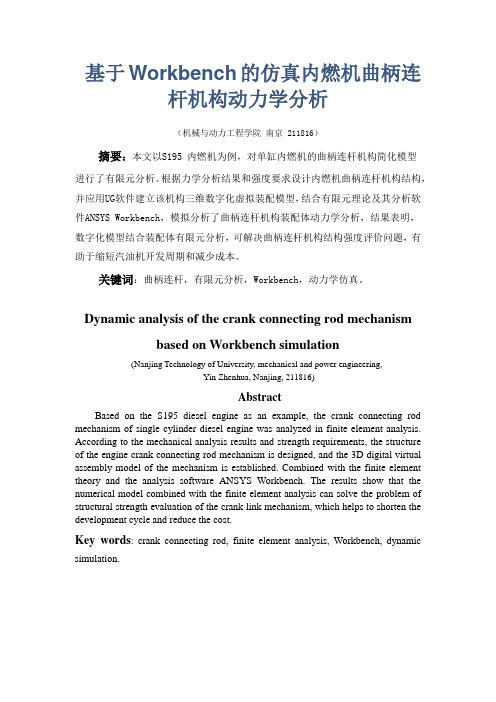
基于Workbench的仿真内燃机曲柄连杆机构动力学分析(机械与动力工程学院南京 211816)摘要:本文以S195 内燃机为例,对单缸内燃机的曲柄连杆机构简化模型进行了有限元分析。
根据力学分析结果和强度要求设计内燃机曲柄连杆机构结构,并应用UG软件建立该机构三维数字化虚拟装配模型,结合有限元理论及其分析软件ANSYS Workbench,模拟分析了曲柄连杆机构装配体动力学分析,结果表明,数字化模型结合装配体有限元分析,可解决曲柄连杆机构结构强度评价问题,有助于缩短汽油机开发周期和减少成本。
关键词:曲柄连杆,有限元分析,Workbench,动力学仿真。
Dynamic analysis of the crank connecting rod mechanismbased on Workbench simulation(Nanjing Technology of University, mechanical and power engineering,Yin Zhenhua, Nanjing, 211816)AbstractBased on the S195 diesel engine as an example, the crank connecting rod mechanism of single cylinder diesel engine was analyzed in finite element analysis. According to the mechanical analysis results and strength requirements, the structure of the engine crank connecting rod mechanism is designed, and the 3D digital virtual assembly model of the mechanism is established. Combined with the finite element theory and the analysis software ANSYS Workbench. The results show that the numerical model combined with the finite element analysis can solve the problem of structural strength evaluation of the crank link mechanism, which helps to shorten the development cycle and reduce the cost.Key words: crank connecting rod, finite element analysis, Workbench, dynamic simulation.0.引言随着发动机强化指标的不断提高,曲柄连杆机构的工作条件更加复杂[1-2]。
ansys汽车连杆

姓名:学号:班级:一,分析目的:连杆链接活塞和曲轴,活塞上的力传送给曲轴以输出功率。
连杆在工作中,除承受燃烧室燃气产生的压力外,还承受纵向和横向的惯性力。
因此,连杆在一个很复杂的盈利状态下工作。
它即受交变的拉件要求连杆具有较高的强度和抗疲劳性能,又要求具有足够的刚性和韧性。
所以,在连杆外形、过度圆角等方面需严格要求,还应注意表面加工质量以提高疲劳强度。
二,材料参数:图中标注均为英寸作为单位,杨氏模量为E=30E6psi,泊松比为0.3。
连杆材料一般采用45钢、40Cr、20CrMnMo或者40MnB等调质刚。
三,结构参数:图1- 1汽车连杆的有限元分析,为骑车连杆几何模型,连杆的厚度为0.5in,中间部分轮廓为6个点形成的样条曲线,其他长度均在草图中有所表示。
图1- 1汽车连杆的有限元分析四,边界条件:力、位移高强度合金钢的应用并不能达到预期效果连杆是汽车发动机中的主要传动部件之一,它在柴油机中,把作用于活塞顶面的膨胀的压力传递给曲轴,又受曲轴的驱动而带动活塞压缩气缸中的气体。
连杆在工作中承受着急剧变化的动载荷。
连杆由连杆体及连杆盖两部分组成。
连杆体及连杆盖上的大头孔用螺栓和螺母与曲轴装在一起。
为了减少磨损和便于维修,连杆的大头孔内装有薄壁金属轴瓦。
轴瓦有钢质的底,底的内表面浇有一层耐磨巴氏合金轴瓦金属。
在连杆体大头和连杆盖之间有一组垫片,可以用来补偿轴瓦的磨损。
连杆小头用活塞销与活塞连接。
小头孔内压入青铜衬套,以减少小头孔与活塞销的磨损,同时便于在磨损后进行修理和更换。
五,具体流程:命令流:Finish $ /Clear/PREP7 !*入前处理器PCIRC,1.4,1,0,180, $ PCIRC,1.4,1,45,180, !*创建两个圆面/REPLOT,RESIZE/PNUM,KP,0 $/PNUM,LINE,0 $/PNUM,AREA,1 $/PNUM,VOLU,0 $/PNUM,NODE,0/PNUM,TABN,0 $ /PNUM,SV AL,0 $/NUMBER,0 $/PNUM,ELEM,0/REPLOTRECTNG,-0.3,0.3,1.2,1.8, $RECTNG,-1.8,-1.2,0,0.3, !* 创建两个矩形面FLST,2,1,8FITEM,2,6.5,0,0WPA VE,P51XCSYS,4PCIRC,0.7,0.4,0,180, $PCIRC,0.7,0.4,0,135, !*创建另两个圆面FLST,2,4,5,ORDE,2FITEM,2,1 $FITEM,2,-4AOVLAP,P51XFLST,2,2,5,ORDE,2FITEM,2,5 $FITEM,2,-6AOVLAP,P51XCSYS,0K, ,2.5,0.5,, $K, ,3.25,0.4,, $K, ,4,0.33,, $ K, ,4.75,0.28,, !*创建关键点CSYS,1FLST,3,6,3FITEM,3,5 $FITEM,3,6 $FITEM,3,7 $FITEM,3,21 $FITEM,3,24 $FITEM,3,22BSPLIN, ,P51X, , , , ,1,135,,1,45,, !*创建多义线LSTR,1,18 !*创建1和18之间的直线/PNUM,KP,0/PNUM,LINE,1 $/PNUM,AREA,1 $ /PNUM,VOLU,0 $ /PNUM,NODE,0/PNUM,TABN,0 $/PNUM,SV AL,0 $/NUMBER,0 $/PNUM,ELEM,0/REPLOT $LPLOTFLST,2,4,4FITEM,2,6 $FITEM,2,1 $FITEM,2,7 $FITEM,2,25AL,P51XLFILLT,36,40,0.25, , $LFILLT,40,31,0.25, , $LFILLT,30,39,0.25, , !*创建三个线倒角LPLOTFLST,2,3,4FITEM,2,10 $FITEM,2,12 $FITEM,2,13 !*由三个线倒角创建新的面AL,P51XFLST,2,3,4FITEM,2,15 $FITEM,2,17 $FITEM,2,19AL,P51XFLST,2,3,4FITEM,2,23 $FITEM,2,21 $FITEM,2,24AL,P51XAPLOTFLST,2,12,5,ORDE,2FITEM,2,1 $ FITEM,2,-12AADD,P51X/AUTO, 1/REP/PNUM,KP,0 $/PNUM,LINE,0 $/PNUM,AREA,0 $/PNUM,VOLU,0/PNUM,NODE,0 $/PNUM,TABN,0 $/PNUM,SV AL,0 $/PNUM,ELEM,0/REPLOTAPLOTCSYS,0FLST,3,1,5,ORDE,1FITEM,3,13ARSYM,Y,P51X, , , ,0,0FLST,2,2,5,ORDE,2FITEM,2,1 $FITEM,2,13AADD,P51XWPSTYLE,,,,,,,,0ET,1,SOLID45 !*材料MPTEMP,,,,,,,, $MPTEMP,1,0 $MPDA TA,DENS,1,,8000MPTEMP,,,,,,,, $MPTEMP,1,0MPDATA,EX,1,,2.1e11 $MPDATA,PRXY,1,,0.3 !*弹性模量FLST,2,1,5,ORDE,1 !*拉伸体VEXT,2, , ,0,0,0.5,,,,MSHAPE,1,3D $MSHKEY,0 $CM,_Y,VOLU $VSEL, , , ,1 !*网格CM,_Y1,VOLU $CHKMSH,'VOLU' $CMSEL,S,_Y $VMESH,_Y1CMDELE,_Y $ CMDELE,_Y1 $ CMDELE,_Y2 $ /UI,MESH,OFFFINISH $ /SOL $ FLST, 2,4,5,ORDE,2 $ FITEM,2,27 !*对大圆内孔施加全约束FITEM,2,-30 $DA,p51x,ALL,FLST,2,2,5,ORDE,2 $FITEM,2,31 $ FITEM,2,-32 $ SFA,P51X,1,PRES,1000 !*对小圆内孔施加均布荷载1000/STA TUS,SOLU $SOLVE !*求解六,查看结果:图1- 2变形七,用新的知识,建立一条路径,让力和变形都映射在路径上。
基于CATIA和ANSYS的连杆疲劳分析
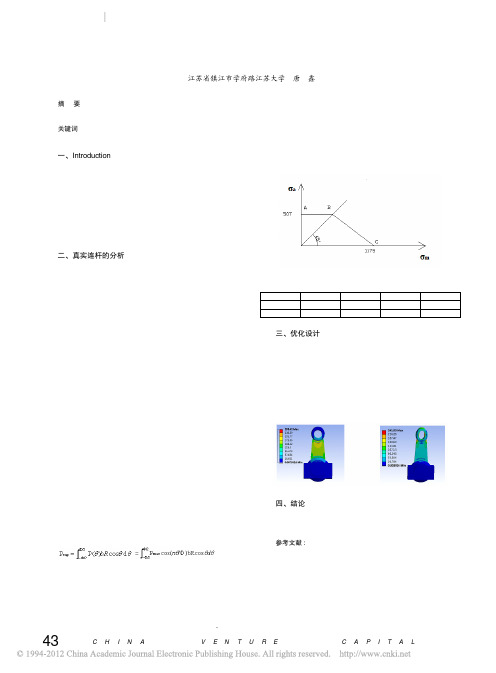
York: Addison-Wesley Publishing Company, 1998.
43
C H I N A
V E N T U R E
C A P I T A L
科技技术应用|TECHNOLOGY APPLICATION
基于 CATIA 和 ANSYS 的连杆疲劳分析
江苏省镇江市学府路江苏大学 唐 鑫
摘 要:本文中应用ANSYS软件对连杆进行有限元分析以得到应力及其分布图。首先连杆的三维模型由CATIA建立并导入ANSYS。根据 ANSYS处理结果,得到应力分布图。通过有限元分析可以针对应力分布情况对连杆的疲劳失效情况进行分析。针对分析结果,最终达到对连杆结 构进行优化的目的。
4. 分析结果 (1) 连杆应力分布是合理的。应力分布平均且正常,几乎 没有应力集中现象出现。 (2) 工作中的极限应力条件下 , 最大应力区域应力符合材料 的极限应力和屈服强度。 所有危险工作区域均符合强度准则。 根 据 连 杆 材 料 的 各 种 参 数 , 18Cr2Ni4WA 极 限 应 力 为 1175MPa 双侧疲劳强度为 507MPa。所以 , 定义 σa=(σ max-
很明显,连杆出于安全状态。 三、优化设计 燃油的减少使得汽车发动机的燃油经济性越来越受到重 视,连杆作为重要的回转件,它的轻量化设计对减少燃油消 耗有着重要的作用。受限于结构和其它因素设定最大厚度为 20mm 最小厚度为 7mm. 所受应力随厚度变化而变化。 优化目标是在符合应力条件的基础上寻找最佳厚度值,如 图 1 所示。优化后得到两个优化候选点,选取一个插入设计点。 从图中可以看到最佳厚度为 10mm. 根据结果建立模型并对模 型进行网格划分和应力分析,如图 2 所示。
σmin)/2 ,σm=(σmax+σmin)/2. 分别以其为横纵坐标做出图 表。图中 ABC 区域即为安全区域。
毕业论文参考-基于ANSYS的连杆应力有限元分析及结构优化
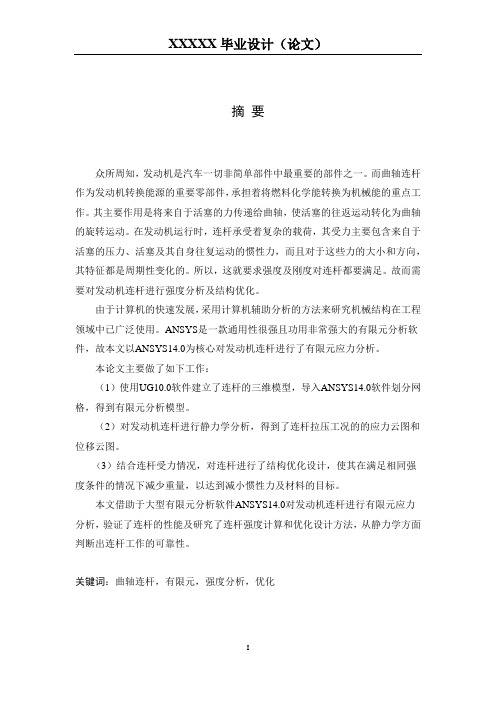
XXXXX毕业设计(论文)摘要众所周知,发动机是汽车一切非简单部件中最重要的部件之一。
而曲轴连杆作为发动机转换能源的重要零部件,承担着将燃料化学能转换为机械能的重点工作。
其主要作用是将来自于活塞的力传递给曲轴,使活塞的往返运动转化为曲轴的旋转运动。
在发动机运行时,连杆承受着复杂的载荷,其受力主要包含来自于活塞的压力、活塞及其自身往复运动的惯性力,而且对于这些力的大小和方向,其特征都是周期性变化的。
所以,这就要求强度及刚度对连杆都要满足。
故而需要对发动机连杆进行强度分析及结构优化。
由于计算机的快速发展,采用计算机辅助分析的方法来研究机械结构在工程领域中已广泛使用。
ANSYS是一款通用性很强且功用非常强大的有限元分析软件,故本文以ANSYS14.0为核心对发动机连杆进行了有限元应力分析。
本论文主要做了如下工作:(1)使用UG10.0软件建立了连杆的三维模型,导入ANSYS14.0软件划分网格,得到有限元分析模型。
(2)对发动机连杆进行静力学分析,得到了连杆拉压工况的的应力云图和位移云图。
(3)结合连杆受力情况,对连杆进行了结构优化设计,使其在满足相同强度条件的情况下减少重量,以达到减小惯性力及材料的目标。
本文借助于大型有限元分析软件ANSYS14.0对发动机连杆进行有限元应力分析,验证了连杆的性能及研究了连杆强度计算和优化设计方法,从静力学方面判断出连杆工作的可靠性。
关键词:曲轴连杆,有限元,强度分析,优化IXXXXX毕业设计(论文)ABSTRACTAs we all know, engine is one of the most important parts of all the complex parts of automobile. Crankshaft connecting rod, as an important part of engine power conversion, undertakes the core task of converting fuel chemical energy into mechanical energy.Its main function is to transfer the force from the piston to the crankshaft, so that the reciprocating motion of the piston can be transformed into the rotating motion of the crankshaft. When the engine works, the connecting rod bears harsh working conditions and complex loads. The force mainly comes from the gas force of the piston, the inertia force of the piston and its reciprocating motion, and the magnitude and direction of these forces show periodic changes. Therefore, it requires the connecting rod to have enough strength and stiffness. Therefore, it is necessary to analyze the strength and optimize the structure of the engine connecting rod.Because of the rapid development of computer, the method of computer aided analysis has been widely used in the field of engineering. ANSYS is a very versatile and powerful finite element analysis software, so this paper takes ANSYS14.0 as the core to carry out finite element stress analysis of engine connecting rod.The main work of this paper is as follows:(1) The three-dimensional model of the connecting rod is established by UG10.0 software, and meshed by ANSYS14.0 software, the finite element analysis model is obtained.(2) Static analysis of engine connecting rod is carried out to check the correctness of finite element model and boundary conditions, and stress nephogram which is in accordance with actual working conditions is obtained.(3) Optimized design of the connecting rod in combination with the force of the connecting rod, so that the weight of the connecting rod can be reduced under theIIXXXXX毕业设计(论文)same strength condition, in order to achieve the purpose of reducing inertial force and material.In this paper, the finite element stress analysis of engine connecting rod is carried out by means of the large-scale finite element analysis software ANSYS14.0. The performance of the connecting rod is verified, the strength calculation and the optimization design method of the connecting rod are studied, and the reliability of the connecting rod is judged from the static aspect.KEY WORDS:crankshaft connecting rod, finite element, strength analysis, optimizationIIIXXXXX毕业设计(论文)目录摘要 (I)ABSTRACT ......................................................................................................................I I 目录 . (IV)第一章绪论 (1)1.1论文研究背景和意义 (1)1.2有限元法研究现状 (1)1.3发动机连杆有限元分析研究现状 (2)1.4本章小结 (3)第二章有限元分析基础 (4)2.1有限元法介绍 (4)2.1.1有限元法发展历史 (4)2.1.2有限元法基本理论 (5)2.1.3有限元法分析步骤 (7)2.2ANSYS软件介绍 (9)2.3本章小结 (9)第三章连杆的受力分析 (10)3.1连杆受载情况及参数 (10)3.1.1连杆受力分析 (10)3.1.2已知参数 (11)3.2燃气压力计算 (11)3.3惯性力计算 (12)IVXXXXX毕业设计(论文)3.5连杆最大压应力工况受力分析 (15)3.6本章小结 (16)第四章连杆应力有限元分析与结构优化 (17)4.1连杆三维模型的建立 (17)4.1.1 UG10.0软件介绍 (17)4.1.2建立连杆三维模型 (18)4.1.3三维模型的简化 (19)4.2有限元模型前处理 (22)4.2.1三维模型的导入 (22)4.2.2材料参数的设定 (24)4.2.2单元类型的选择及网格划分 (25)4.3连杆载荷施加及边界条件 (28)4.3.1连杆载荷处理与分布 (28)4.3.1.1载荷处理 (28)4.3.1.2连杆大小端拉应力加载 (29)4.3.1.3连杆大小端压应力加载 (31)4.3.2连杆位移边界条件的确定 (34)4.4运算及结果分析 (35)4.5连杆结构优化分析 (37)4.6.1连杆优化概述 (37)4.6.2连杆优化分析 (38)4.6本章小结 (40)第五章总结与展望 (41)5.1工作总结 (41)5.2工作展望 (42)参考文献 (44)VXXXXX毕业设计(论文)致谢 (46)毕业设计小结 (47)VIXXXXX毕业设计(论文)第一章绪论1.1论文研究背景和意义以往对发动机的主要组成部件的受力分析,只能靠传统力学计算方法,大致反映这些零件受力状态,因为这些零件受力复杂且形状不规则,比如活塞、连杆、气缸、曲轴等。
- 1、下载文档前请自行甄别文档内容的完整性,平台不提供额外的编辑、内容补充、找答案等附加服务。
- 2、"仅部分预览"的文档,不可在线预览部分如存在完整性等问题,可反馈申请退款(可完整预览的文档不适用该条件!)。
- 3、如文档侵犯您的权益,请联系客服反馈,我们会尽快为您处理(人工客服工作时间:9:00-18:30)。
第36卷 第2期 2014-02(下) 【107】收稿日期:2013-11-22作者简介:胡小青(1980 -),女,四川德阳人,讲师,硕士,研究方向为机械设计制造及其自动化。
基于ANSYS workbench 的汽车发动机连杆力学性能分析Mechanical properties analysis of motocar engine connecting rodbased on ANSYS Workbench胡小青HU Xiao-qing(四川工程职业技术学院,德阳 618000)摘 要:以汽车发动机用连杆为研究对象,建立了发动机连杆力学性能分析简化模型。
采用Ansysworkbench软件static structure模块,利用有限元分析法对发动机连杆模型进行模拟分析,得出了发动机连杆模型总变形、等效应力以及等效弹性应变分布。
结果显示,发动机连杆模型最大变形位于发动机小头顶部,最大等效应力位于发动机连杆与大头交接顶角处,为4.09×109Pa ,最大等效弹性应变与等效应力所处位置相同为0.02。
关键词:发动机连杆;Ansys workbench;有限元法;模拟分析;力学性能中图分类号:TG213 文献标识码:A 文章编号:1009-0134(2014)02(下)-0107-02Doi:10.3969/j.issn.1009-0134.2014.02(下).300 引言汽车发动机连杆是内燃机中的一个重要的结构零件,其作用是连接活塞和曲轴,将作用在活塞上的力传递给曲轴,使活塞的往复运动转变为曲轴的旋转运动,对外输出做功[1]。
连杆小头与活塞销相连接,与活塞一起做往复运动,连杆大头与曲柄销相连和曲轴一起做旋转运动[2,3]。
因此,连杆体除了上下运动外,还左右摆动,做复杂的平面运动[4]。
所以,连杆的受力情况也十分复杂,工作中经常受到拉伸、压缩和弯曲等交变载荷的作用[5]。
这种复杂的载荷容易引起连杆的疲劳破坏,甚至直接关系到操作人员的安全,从而造成严重的后果[6]。
因而,对于汽车发动机连杆运动过程中的力学分析非常重要。
通常,大多数工程实际问题很难单独的通过经典的弹性力学通过求解微分方程而得到其解析解[7,8]。
而有限元方法则避免了求解微分方程,因此,通过计算机采用有限元分析方法分析汽车发动机连杆在使用过程中的力学性能,可以为汽车发动机行业的发展提供一个有力的参考[9~11]。
基于此,本文对汽车发动机连杆建立了相应的模型,采用有限元法,利用Ansys Workbench 软件分析了发动机连杆的力学性能,包括连杆的变形、等效应力与等效弹性应变。
为发动机连杆的应用提供一定的参考。
1 实验建立合适的有限元模型和进行合适的网格划分对发动机连杆分析至关重要。
实验中采用Pro/E 软件建立发动机连杆的简化模型,在建立模型时,对连杆总体应力影响不大地过渡圆角、润滑小油孔等均被忽略。
采用Ansys Workbench 软件进行网格划分和模拟分析。
实验所建立的实体模型和网格模型如图1所示,图1(a)为实体模型,图1(b)为网格模型。
划分网格时,发动机小头和大头内表面均采用加密网格。
网格划分后,连杆节点数为292598个,单元数为191590个。
在发动机工作过程中,连杆只承受轴向力作用,该力的最大值是由发动机活塞面爆燃气体压力和活塞与连杆小头的惯性力引起的。
通过分析汽车发动机的做功情况以及燃气压力和连杆惯性力的影响,得到连杆在发动机燃气压力下的压力约为4.5MPa ,对应的最大轴向力约为11500N 。
将其均布在连杆小头下半圆面上。
对模型进行材料实验初始值特性定义过程中,采用连杆采用40Cr 钢,其主要性能参数如下:弹性模量E=2×1011Pa ,泊松比μ=0.28,ρ=7.9×103kg/m 3。
实验中采用Ansys workbench 中Static Structural 模块对发动机连杆进行模拟分析。
【108】 第36卷 第2期 2014-02(下)(a) 实体模型 (b) 网络模型图1 发动机连杆实体和网格模型2 结果分析与讨论2.1 连杆总变形分析图2(a)是发动机连杆模型整体变形结果分布,从图中可以发现,发动机连杆最大变形处位于连杆小头处,变形呈梯度分布,并呈逐渐减小趋势,最小变形处位于连杆大头处。
同时还可发现,发动机连杆在工作过程中,在燃气压力推动活塞面加压到小头内表面时,小头处于最大变形,如图2(a)所示。
发动机连杆中部由于压力的作用也产生了横向的变形,如图2(b)所示。
(a) (b)图2 发动机连杆模型整体变形分布2.2 发动机连杆等效应力分析图3是发动机连杆整体Miss 等效应力模拟结果,从图中可以发现,发动机连杆模型等效应力沿小头至大头方向呈非线性变化,最大应力如图4所示,位于发动机靠近大头方向的加强槽顶角处,应力为4.09×109Pa ,最小应力位于发动机连杆大头和小头顶部,应力为23.09Pa 。
结合图3和图4可发现,发动机连杆整体应力分布均匀,发动机连杆中应力集中部位均在连杆肋避表面处,且不是很明显。
同时,在肋避处存在的部分应力集中现象可以起到应力-力增强的作用。
当发动机连杆在工作过程中,这样的布置,可有效减小应力在连杆大头和小头上的集中,从而可增加连杆使用的可靠性和稳定性能。
图3 发动机连杆等效应力分布 图4 发动机连杆最大应力分布2.3 发动机连杆等效弹性应变分析图5是发动机连杆模型的整体等效弹性应变分布,图6是发动机连杆最大等效弹性应变分布,从图中可以发现,模型的最大等效弹性应变位于靠近大头肋壁与大头结合的顶角处,为0.02。
从图5中可以发现最小等效弹性应变位于发动机连杆大头和小头的顶角处为1.15×10-10。
从最大等效弹性应变所处的位置可以发现,发动机连杆在工作过程中,最容易产生弹性应变的地方处于发动机连杆靠近大头处的连杆肋顶角处。
结合图5和图6分析可知,发动机连杆等效弹性应变分布均匀。
发动机机连杆等效弹性应变的分布位置与等效应力集中部位具有位置同步性,这说明在发动机连杆上Miss 等效应力的集中会导致与之对应的连杆处产生较大弹性应变,但是,由于发动机连杆采用了工字型加强结构,使得连杆在工作过程中可以承受较大的惯性扭矩和压力,从而保证了发动机连杆经历上万次的使用而不受到破坏。
图5 发动机连杆等效 图6 发动机连杆最大 弹性应变分布 等效弹性应变分布3 结论1)采用有限元分析方法,利用A n s y s Workbench 软件中Static Structural 模块对发动机连杆建立简化实体模型和网格模型,并对其进行工作状态下力学性能进行模拟分析,得出了连杆总变形、等效应力以及等效弹性应变分布。
2)模拟结果显示,发动机连杆模型最大变形位于连杆小头顶部,最大Miss 等效应力为4.09×109Pa ,最小应力为23.09Pa ,最大等效弹性第36卷 第2期 2014-02(下) 【109】应变为0.02,最小等效弹性应变为1.15×10-10。
3)应力部分集中于发动机连杆肋避顶角处,在发动机工作过程中可以起到应力-力增强的作用,使得整体等效弹性应变均匀分布,从而提高发动机连杆在工作时的可靠性和稳定性能。
参考文献:[1] 柴油机设计手册编辑委员会.柴油机设计手册(上册)第一版[M].北京:中国农业出版社,1984:523-553.[2] Q.Wang, F.He.A view of developments in the forgingof connecting rod in China[J].Journal of Materials of Processing Technology,2004,151(1):192.[3] 王银燕,张鹏奇,王善.内燃机连杆杆身疲劳强度可靠性分析[J].哈尔滨工程大学学报,2001, 22(1):67-71.[4] 张勇,王有喜,张春明.发动机连杆的渗流铸造工艺参数研究[J].铸造技术,2010, 31(6):720-722.[5] 王林军.LR4105柴油机曲轴、连杆动应力分析研究[J].车用发动机,2008,6:140-145.[6] 潘琼瑶,陈凯.车用发动机连杆强度分析与结构改进[J].车用发动机,2008,6:140-145.[7] 谈卓君,左正兴,张儒华.内燃机连杆有限元分析进展[J].中国机械工程,2004,15(4), 365-369.[8] 马军彦.柴油机连杆应力和变形的计算与实验研究[D].哈尔滨:哈尔滨工程大学,2010.[9] 赵丕欢,樊文欣,张保成,等.基于虚拟样机技术的柴油机曲柄连杆机构动力学仿真研究[J].柴油机设计与制造, 2008,4:21-23.[10] 郭涛,杨晓.基于ABAQUS 的连杆有限元分析[J].装备制造技术,2010,2(7):45-47.[11] 王克武.基于有限元的汽车发动机连杆锻坯塑性成形新工艺研究[J].制造业自动化,2013,(14):154-156.fidtl=fopen('C:\Users\Administrator\Desktop\data\ug.dat','wt');fprintf(fidtl,'%12.4f %12.4f %12.4f\n',XYTL);fclose(fidtl);4 三维凸轮生成运行U G 软件并新建文件,通过菜单栏的【insert 】/【curve 】/【spline 】/【through points 】,在弹出的对话框中Curve type 选择Multiple Segments ,Curve Degree 选项选择3,并勾选Closed Curve 选项,点击“Points from File ”按钮进入查找凸轮轮廓曲线点的数据存放文件ug.dat 文件,找到文件后点击确定退出数据文件查找界面,在spline through points 窗口界面点击OK 按钮即可生成封闭的凸轮轮廓曲线[3],如图3所示。
图3 高次多项式凸轮轮廓曲线进行凸轮三维实体生成时,选择Extrude 命令,选中生成的凸轮轮廓曲线,设定凸轮厚度后点击确认后得到凸轮三维实体模型,然后进行凸轮安装轴孔的拉伸切除操作就完成了凸轮的三维设计,凸轮三维实体模型如图4所示。
图4 凸轮三维实体模型5 结束语通过对凸轮从动件的高次多项式及其约束方程进行Matlab 编程求解,获取了从动件的运动规律曲线,实现了高次多项式凸轮轮廓曲线的求解。
同时,获取了高次多项式凸轮轮廓曲线点的数据文件。
然后通过UG 软件的曲线功能及实体操作功能实现了高精度高次多项式凸轮的三维实体建模。