选矿厂工艺流程设计
铁矿选矿厂工艺流程
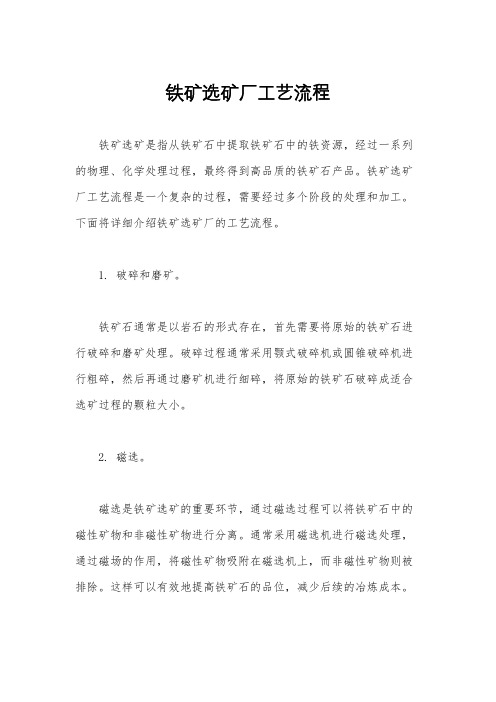
铁矿选矿厂工艺流程铁矿选矿是指从铁矿石中提取铁矿石中的铁资源,经过一系列的物理、化学处理过程,最终得到高品质的铁矿石产品。
铁矿选矿厂工艺流程是一个复杂的过程,需要经过多个阶段的处理和加工。
下面将详细介绍铁矿选矿厂的工艺流程。
1. 破碎和磨矿。
铁矿石通常是以岩石的形式存在,首先需要将原始的铁矿石进行破碎和磨矿处理。
破碎过程通常采用颚式破碎机或圆锥破碎机进行粗碎,然后再通过磨矿机进行细碎,将原始的铁矿石破碎成适合选矿过程的颗粒大小。
2. 磁选。
磁选是铁矿选矿的重要环节,通过磁选过程可以将铁矿石中的磁性矿物和非磁性矿物进行分离。
通常采用磁选机进行磁选处理,通过磁场的作用,将磁性矿物吸附在磁选机上,而非磁性矿物则被排除。
这样可以有效地提高铁矿石的品位,减少后续的冶炼成本。
3. 浮选。
在磁选之后,还需要进行浮选处理,将铁矿石中的硫化物进行分离。
通常采用浮选机进行浮选处理,通过向矿浆中加入药剂,使硫化物和其他矿物发生吸附作用,然后通过气泡的作用将其分离。
这样可以有效地提高铁矿石的品位,减少后续的冶炼成本。
4. 脱水。
经过磁选和浮选处理后,得到的铁矿石浆需要进行脱水处理,将其中的水分进行脱除。
通常采用压滤机或离心机进行脱水处理,将铁矿石浆中的水分进行脱除,得到干燥的铁矿石精矿。
5. 精矿处理。
经过脱水处理后,得到的铁矿石精矿还需要进行进一步的处理,通常包括磨矿、磁选和浮选等环节,以进一步提高铁矿石的品位和品质。
6. 成品铁矿石。
经过以上的一系列处理过程,最终可以得到高品质的成品铁矿石,可以直接用于冶炼生产高品质的铁制品。
以上就是铁矿选矿厂的工艺流程,通过破碎和磨矿、磁选、浮选、脱水和精矿处理等环节,可以将原始的铁矿石进行高效、高品质的提取和加工,为后续的冶炼生产提供优质的原料。
大孤山选矿厂工艺流程

大孤山选矿厂工艺流程下载温馨提示:该文档是我店铺精心编制而成,希望大家下载以后,能够帮助大家解决实际的问题。
文档下载后可定制随意修改,请根据实际需要进行相应的调整和使用,谢谢!并且,本店铺为大家提供各种各样类型的实用资料,如教育随笔、日记赏析、句子摘抄、古诗大全、经典美文、话题作文、工作总结、词语解析、文案摘录、其他资料等等,如想了解不同资料格式和写法,敬请关注!Download tips: This document is carefully compiled by theeditor. I hope that after you download them,they can help yousolve practical problems. The document can be customized andmodified after downloading,please adjust and use it according toactual needs, thank you!In addition, our shop provides you with various types ofpractical materials,such as educational essays, diaryappreciation,sentence excerpts,ancient poems,classic articles,topic composition,work summary,word parsing,copy excerpts,other materials and so on,want to know different data formats andwriting methods,please pay attention!大孤山选矿厂工艺流程。
大孤山选矿厂是一家大型的选矿企业,主要处理铁矿石。
选矿厂工艺流程

选矿厂工艺流程
选矿厂工艺流程是指将矿石中有用的矿物和有用的矿石分离出来的一系列工艺过程。
选矿厂工艺流程的主要目的是提高矿石的品位,降低生产成本,实现资源的有效利用。
下面我们将详细介绍选矿厂工艺流程的主要步骤。
首先,矿石的破碎和磨矿是选矿厂工艺流程的第一步。
矿石经过破碎设备的破碎和磨矿设备的磨矿,将矿石破碎成较小的颗粒,以便后续的选矿操作。
这一步是整个选矿过程的基础,破碎和磨矿的效果直接影响后续工艺的进行。
接下来是矿石的分类和分级。
经过破碎和磨矿后的矿石颗粒并不是均匀的,其中含有有用矿物的颗粒和废石的颗粒。
因此,需要通过分类设备将矿石进行分级,将有用矿物和废石进行分离,以便后续的选矿操作。
然后是矿石的浮选和重选。
浮选是利用有机物或无机物的表面活性剂,使有用矿物和废石在水中产生疏水性和亲水性的差异,从而达到分离的目的。
而重选是利用重力、离心力、阻力等原理,将矿石中的有用矿物和废石进行分离。
最后是矿石的脱水和干燥。
经过前面的工艺步骤,矿石中的有用矿物已经得到了分离,但其中还含有一定的水分。
因此,需要通过脱水和干燥设备将矿石中的水分去除,以便后续的运输和加工。
总的来说,选矿厂工艺流程是一个复杂的过程,需要经过多个步骤的精细操作才能达到预期的效果。
只有严格按照工艺流程进行操作,才能保证选矿厂的生产效率和产品质量。
希望本文对选矿厂工艺流程有所帮助,谢谢阅读!。
选矿厂工艺流程范文

选矿厂工艺流程范文矿厂是一种特殊的工业企业,用于处理含有矿物质的原材料并提取出有用的金属元素。
工艺流程是指在矿石处理过程中所采取的一系列技术步骤,用于将矿石转化为有用产品的过程。
下面是一份关于工艺流程的范文,供参考:一、概述选矿厂是矿产资源综合利用的工厂,主要用于对矿石进行加工,从中提取出有用的金属元素。
矿石的处理流程通常包括破碎、磨矿、选矿和精矿等环节。
通过对矿石进行加工处理,可以实现矿石中金属元素的分离和提取。
二、矿石破碎矿石破碎通常是将原始的矿石进行粉碎,使其达到适合进一步处理的细度。
常见的破碎设备包括颚式破碎机、圆锥破碎机、冲击破碎机等。
矿石破碎的目的是将矿石从大块状分解为较小的颗粒,以便提高后续步骤中的处理效果。
三、磨矿磨矿是将矿石进行进一步细化的过程,通常使用的磨矿设备包括球磨机、砂石磨机等。
磨矿的目的是将矿石中的金属矿物颗粒进一步细化,使其达到适合进行选矿操作的细度。
此外,磨矿还可以促使金属矿物与其他杂质的分离。
四、选矿选矿是将矿石中的有用金属矿物与其他无用杂质进行分离的过程。
选矿通常采用物理或化学方法来实现。
物理选矿通常是利用矿石中有用矿物和无用矿物在物理特性上的差异进行分离,常见的物理选矿方法包括重选、浮选等;化学选矿是通过物质的化学性质来实现分离,例如利用溶液中金属离子与特定化学试剂的反应来使金属矿物与杂质分离。
选矿工艺的选择取决于矿石的成分和性质,以及需要提取的金属元素。
五、精矿精矿是指通过选矿步骤分离出的含有较高金属含量的矿石。
精矿的处理通常包括砂浆搅拌、烘干、熔炼等过程,以提取出金属元素。
砂浆搅拌通常采用搅拌机将精矿与一定量的水混合,形成矿浆;烘干是将矿浆中的水分蒸发掉,使精矿达到熔点;熔炼是将矿石中的金属元素通过高温熔炼的方式分离出来,通常使用的设备有电炉、熔炉等。
六、尾砂处理尾砂是指经过精矿处理后所剩下的杂质和废料,其中包含了一定量的有用金属矿物。
尾砂处理可以将这些金属元素进一步提取出来,以实现矿石资源的综合利用。
铁矿选矿厂工艺流程

铁矿选矿厂工艺流程
铁矿是一种重要的矿石资源,铁矿选矿厂主要通过工艺流程将铁矿石分离出铁和杂质,以得到高纯度的铁矿产品。
下面将介绍一种常见的铁矿选矿厂工艺流程。
首先,铁矿石进入选矿厂后,经过初级破碎和细碎工序。
初级破碎设备将铁矿石压碎成较小的颗粒,然后细碎设备将颗粒更加细化,以便后续的分选工序。
接下来,经过物理分选工序对破碎后的铁矿石进行分选。
物理分选工序主要包括重介质选矿、磁选和重力选矿。
在重介质选矿中,通过将破碎后的铁矿石和重介质悬浮液混合,根据密度的差异使铁矿与杂质分离。
磁选则是利用铁矿石具有一定的磁性,通过磁性分离器将含铁矿物和非磁性杂质分离。
重力选矿是利用铁矿石和杂质的密度差异,通过重力分离设备将铁矿石和杂质分离。
在物理分选之后,还需进行化学分选以进一步提高铁矿的纯度。
化学分选主要是通过浸泡和浸泡浮选过程。
在浸泡过程中,将铁矿浸泡在一种化学药剂中,使得铁矿与某些杂质发生化学反应以分离开来。
而在浮选过程中,铁矿石与液体起泡剂反应,使得铁矿浮到液面上,然后被收集起来。
最后,对铁矿进行干燥和烧结处理。
干燥工序是将湿状的铁矿经过热处理,使其成为干燥的颗粒。
而烧结工序则是通过高温加热使铁矿颗粒间产生结合,形成固体块状。
这样的处理方式不仅可以提高铁矿的密度和强度,还方便后续的运输和储存。
总结起来,铁矿选矿厂的工艺流程包括初级破碎、物理分选、化学分选、干燥和烧结等几个主要工序。
通过这些工艺的组合,可以将铁矿石中的铁和杂质分离出来,得到高纯度的铁矿产品,为后续的钢铁生产提供了重要的原材料。
矿山采矿及选厂主要工艺描述及生产工艺流程图

矿山采矿及选厂主要工艺描述及生产工艺流程图一、矿石采矿主要工艺描述:1、凿岩工段掘孔是采矿的第一道工序,其作用内容是采用凿岩机在计划开采的范围内进行穿凿炮孔,为其后的爆破工作提供装药空间;严格按照当班爆破技术员的布孔要求进行掘眼,炮眼排间距误差控制在±0.2㎜,孔间距误差控制在±0.2m,孔深距误差控制在±0.2m。
2、爆破工段采用中深孔爆破,用压风管将炮眼内的杂物吹出,(爆破技术人员对爆区内的孔深、孔网进行验收,如炮孔不合格,不能实施爆破)。
对已掘好的炮眼进行装药,装药量按照炮眼孔径、最小抵抗线和炮孔周边的邻孔距离的计算公式填装,由爆破产生的爆破地震、爆破飞石、噪声等危害应控制在允许范围内。
3、铲装工段采用徐工X-992铲装王铲装,除了爆破质量因素外,掌子面不得随意抬高或挖低;不得装偏车,使车辆失重,如遇大块矿石(废石),应在工作面处理后铲装。
4、运输工段井下采用载重不超过12t的南骏汽车运输,在运输途中应注意保护井下各巷道的设施,应严格遵守井下的各项制度和运输制度。
二、选矿厂主要工艺描述:1、破碎工段磷矿由振动给矿机将矿石送入锤式破碎机,破碎后的矿石经筛选分后,粗颗粒再进入破碎,合格的矿石经圆盘给料机进入球磨工段。
含尘废气经袋收尘器处理后由15米高排气筒排放。
2、磨矿工段采用湿法磨矿,将磷矿石和水一起研磨成含一定水份的矿浆,矿石球磨后,将分级后粗颗粒的矿石送入回球机,合格的矿浆进入浮选工段。
3、浮选工段采用反浮选工艺选矿,矿浆在浮选机内加入硫酸、浮选剂、絮凝剂,PH控制在5.1—5.3,用罗茨鼓风机通入空气,经浮选后矿浆和尾矿分别进入精矿浓密机和尾矿浓密机。
4、过滤工段精矿和尾矿经浓密机沉降脱去大部分水份,精矿奖采用立式压滤机将压滤到含水为20%左右的精矿产品。
尾矿浆在中和槽内加入石灰,将PH调至8—9后经尾矿泵送至矿库堆存,尾矿渗滤液经库存底收集渗滤池,再用泵输送回选矿作补充水。
选矿厂工艺流程

选矿厂工艺流程选矿厂工艺流程是矿石经过一系列物理、化学和机械处理,以分离有用矿物和杂质的过程。
选矿厂工艺流程的设计和实施对于矿石的开采和利用具有重要意义,能够提高矿石的品位和回收率,降低生产成本,实现资源的高效利用。
本文将介绍选矿厂工艺流程的基本步骤和关键技术,以及其在矿石加工中的应用。
1. 破碎和磨矿矿石从矿山中采掘出来后,首先需要进行破碎和磨矿操作。
破碎是指将原始矿石通过破碎设备(如颚式破碎机、圆锥破碎机)进行初步破碎,将大块矿石破碎成适当大小的颗粒。
而磨矿则是将破碎后的矿石通过磨矿设备(如球磨机、磨矿机)进行细化,使得矿石颗粒达到所需的细度。
2. 分级和筛分经过破碎和磨矿处理后的矿石颗粒需要进行分级和筛分操作,以便进一步的处理。
分级是根据矿石颗粒的大小和密度将其分为不同的级别,以便后续的选矿操作。
而筛分则是利用筛分设备(如振动筛、旋振筛)对矿石颗粒进行筛分,将不同尺寸的颗粒进行分离。
3. 重选和浮选重选和浮选是选矿厂工艺流程中的关键步骤,通过这两个操作可以实现对有用矿物和杂质的有效分离。
重选是利用重选设备(如重选机、离心机)对矿石进行重选,根据矿石颗粒的密度差异进行分离,使得有用矿物得到提纯。
而浮选则是利用浮选剂和气泡将有用矿物和杂质进行分离,通过气泡在矿石颗粒表面的吸附作用实现浮选分离。
4. 脱水和干燥经过重选和浮选处理后的矿石颗粒需要进行脱水和干燥操作,以便进一步的处理和运输。
脱水是通过脱水设备(如脱水筛、脱水离心机)对矿石颗粒中的水分进行脱除,使得矿石颗粒达到适当的含水率。
而干燥则是利用干燥设备(如烘干机、旋转干燥机)对脱水后的矿石颗粒进行干燥,使得其达到适当的干燥度。
5. 精矿和尾矿处理经过上述步骤处理后,得到的产品可以分为精矿和尾矿两部分。
精矿是指含有有用矿物的产品,可以直接进行下一步的冶炼或加工。
而尾矿则是指含有较多杂质的产品,需要进行进一步的处理和回收。
尾矿处理可以采用再选、再浮选等方法,以提高有用矿物的回收率和降低对环境的影响。
铁矿选矿厂工艺流程

铁矿选矿厂工艺流程
《铁矿选矿厂工艺流程》
铁矿选矿厂是用来从原料中提取有用的矿物质的设备。
铁矿选矿过程是一个复杂的工艺流程,涉及到多种设备和技术的使用。
以下是一个典型的铁矿选矿厂工艺流程的简要描述:
1. 破碎:原料矿石首先要经过破碎过程,将大块的矿石破碎成小块,以便进一步的处理。
2. 磨矿:破碎后的矿石需要通过磨矿机进行细碎,以获得更细的颗粒度,为后续的选矿过程做准备。
3. 分级:磨矿后的矿石经过分级设备进行分级,将颗粒度不同的矿石进行分离,以便后续的浮选或磁选过程。
4. 浮选或磁选:根据矿石的性质,可以选择利用浮选设备或磁选设备对矿石进行提取,将有用的矿物质从废石中分离出来。
5. 浓缩:经过浮选或磁选后,需要对提取出来的有用矿物质进行浓缩处理,将其纯度提高到一定的水平。
6. 干燥:经过浓缩后的矿物质需要经过干燥设备进行干燥处理,以便存储和运输。
7. 尾矿处理:在整个选矿过程中,会产生一定量的废矿石,需要经过尾矿处理设备进行处理,以减少对环境的影响,同时可
以回收一部分有用的矿物质。
以上是一个简要的铁矿选矿厂工艺流程,实际的工艺流程会根据不同的矿石种类和质量要求而有所不同。
铁矿选矿厂的工艺流程是一个重要的环节,直接影响到选矿效率和产量,同时也对环境保护和资源利用具有重要意义。
- 1、下载文档前请自行甄别文档内容的完整性,平台不提供额外的编辑、内容补充、找答案等附加服务。
- 2、"仅部分预览"的文档,不可在线预览部分如存在完整性等问题,可反馈申请退款(可完整预览的文档不适用该条件!)。
- 3、如文档侵犯您的权益,请联系客服反馈,我们会尽快为您处理(人工客服工作时间:9:00-18:30)。
选矿厂工艺流程设计制定工艺流程是选矿厂设计的首要任务。
在设计前,工艺设计人员必须全面了解所设计的矿床赋存情况、矿石类型、矿石物理及化学性质、矿物组成及品位、嵌布粒度、共生关系等,并和地质、采矿人员共同研究商定采取矿样方案,以便进行选矿试验。
在试验中,要和试验人员研究试验方案,最后由试验部门提供试验报告作为设计的基础资料。
在制定设计工艺流程时要注意的若干原则问题,分述如下。
一、工艺流程的确定原则设计工艺流程及设备选择应遵循:(一)设计的工艺流程应根据试验报告并参考类似选矿厂成熟经验确定。
当选矿方法存在两个方案时,应在相同试验规模基础上进行全面技术经济比较,推荐最佳设计方案。
(二)可靠、高效和低耗是确定工艺流程的根本原则,在保证同等效益的前提下,工艺原则流程应力求简单以利于生产操作。
为适应采矿供矿条件和矿石性质的变化,在流程、设备选择和配置上要具有灵活性。
对于进厂原矿矿石性质及品位波动较大时,应设立配矿设施以混匀矿石,使能稳定生产,提高选矿回收率。
(三)不同矿石类型的分别处理或混合处理。
若各种类型矿石的可选性试验结果表明在磨矿细度及选别流程有明显差别时,则需分别处理,进行分别采选。
如白银厂铜矿矿石类型主要有块状含铜黄铁矿和细脉浸染型铜矿,由于其选别流程有明显差别,在选矿石中必须分别处理。
反之,虽然矿床中矿石类型多,但选别流程差异不明显,则可混合处理。
二、破碎段数及产品粒度的确定原则破碎段数主要取决于采矿场来矿的最大块度和选矿厂破碎产品最终粒度。
它与矿床赋存条件、矿山规模、采矿方法及装运设备等有关。
最终产品粒度视选矿厂磨矿流程而定。
采用常规碎磨流程时,露天开采和大型坑内矿山的来矿块度大,一般为三段破碎;小型坑内矿山常采用两段破碎。
如果矿石硬度大,根据最终破碎粒度要求也可以考虑四段破碎。
常规碎磨流程的破碎产品粒度的确定,由于破碎较磨矿效率高、费用低、能耗低、因此应遵循“多碎少磨”的原则,尽可能降低破碎产品粒度。
一般为-10~-15毫米。
最终一段破碎即细碎以闭距破碎为宜。
使用棒磨机为开路作业时,破碎产品粒度一般控制在15~20毫米;当破碎含泥量多的矿石时,产品粒度可适当放大到20~25毫米。
砾磨机一般用作研磨棒磨产品或球磨机、半自磨机的产品。
所需磨矿介质,一般从破碎流程分出40~100毫米粒级矿石供砾磨机使用。
采用自磨、半自磨流程时,矿石采用一段破碎到350毫米以下。
破碎产品直接供选别时,可根据矿石的解离度及不同工艺设备的入选粒度要求而定。
一般给入跳汰选矿为-20毫米;重介质选矿为-25,+3毫米,静态重介质选矿可到100毫米。
当要求破碎产品作为成品时,可根据用户要求来确定产品粒度。
三、洗矿作业的选定条件选矿厂考虑洗矿作业有如下条件:(一)矿石含泥量多、水分大时,必须考虑洗矿,以利破碎筛分作业的正常进行,防止破碎机及筛子的堵塞。
(二)矿石进行预选(如手选、光电选、重介质选矿)前需要洗矿。
手选、光电选是利用矿物和脉石、围岩颜色的不同进行选别的,所以必须预先洗除污泥,使矿石色泽清楚。
重介质选矿时,为降低矿浆粘度、提高选别效果,亦须预选洗矿。
(三)某些矿床,如沉积型铁锰矿床,洗矿是一种选别方法,通过洗矿脱泥使用有用矿物提高品位而获得合格产品。
又如天然硅砂,通常只需经洗矿、筛分(或分级)便可获得合格产品。
(四)有色金属、贵金属、稀有金属、金刚石的砂矿,大多数需要洗矿。
(五)有的太石含泥并有可溶性金属盐类,洗矿后可以回收溶解金属。
(六)特大型选矿厂,若采用洗矿作业导致工序复杂、难于管理,因此,往往在中碎前采用重型振动筛,筛出粉矿部分直接进入粉矿仓,以避免使用洗矿作业,从而简化了破碎流程。
如布干维尔(Bougainville)选矿厂用2.4×6米重型筛筛出泥矿直接运到粉矿仓,没有设置洗矿作业。
(七)对于难洗矿泥的矿石,可考虑采用半自磨(或自磨)流程来处理。
洗矿设置地点一般在粗碎后进行,但也有在粗碎前使用,少数设在细碎前。
设计时要根据具体情况来决定。
由于泥矿和砂矿性质不同,洗矿后的矿泥一般是单独进行处理,这样可以提高选别效果。
但对于规模较小的矿山且含泥量又不多时,也可考虑将泥矿保并到矿石中一起处理。
设计时应结合矿床赋存条件、矿物组成及矿石物理性质、含泥量多少、采矿方法、运输条件等因素,参考国内外有关实践合理选择洗矿方法和设备。
四、磨矿流程的选择原则磨矿流程有多种,主要有:(一)常规磨硫流程,主要有:1、球磨流程;2、棒磨-球磨流程;3、棒磨-砾磨流程。
(二)自磨流程,包括有:1、一段全自磨流程;2、自磨-砾磨流程;3、块磨磨矿流程;4、自磨-球磨流程;5、自磨-细破碎-球磨流程(A、B、C、流程);6、单段半自磨流程;7、半自磨-球磨流程;8、半自磨-砾磨流程。
此外,尚有其他多种组合。
在这些流程中生产实践常用的有:常规磨矿流程,块磨磨矿流程(北欧国家用),半自磨-球磨流程和自磨-细破碎-球磨流程。
我国目前普遍使用的是常规磨矿流程,少数矿山使用自磨流程。
设计欲采用自磨(半自磨)的工艺时,必须根据半工业试验结果与常规碎磨流程进行技术经济方案比较,推荐最佳的碎磨设计方案。
设计常规碎磨注程时,由于破碎效率远比磨矿效率高,所以要遵循尽量降低破碎粒度,提高球磨生产能力的“多碎少磨”的原则。
“多碎少磨”具有下述优点:1、提高磨矿生产能力降低单位能耗及成本;2、粉矿仓不会发生析离现象;3、磨矿给矿均匀,降低钢球消耗;4、降低噪音;5、减少维修工作量等。
在设计粗磨矿分级回路中使用水力旋流器时,为了减少砂泵及旋流器的磨损必须使用溢流型球磨机,球磨机排矿口需增加一定长度的轴颈筛(圆筒筛),砂泵槽也需采取隔离小球和大矿粒的措施。
在设计棒磨-砾磨流程时,对砾磨排出的顽石需有返回棒磨再磨的措施(如凤凰山选矿厂采用超声波自动控制气动返回棒磨措施)。
设计时注意吸收成熟的选进经验,对于新型磨机品种要进行试验后方可在设计中选用。
设计中研究采用新型衬板及材料如橡胶衬板、角螺旋衬板、磁性衬板等。
研究磨矿介质的形状、质量。
这些均需通过现场实践调查,或经过试验后采用。
选择采用合理先进的分析工艺及高效率分级设备。
一般采用水力旋流器或螺旋分级机分级。
生产实践中的两段分级,第一段磨矿使用直线筛,细磨使用高频细筛等以及其他高效率分级设备。
五、选别流程的确定选别流程是根据矿石组分,矿石及矿物的物理、化学性质、矿物及脉石嵌布粒度、共生关系等的研究,经过选矿试验而确定的。
有单一选矿流程,如浮选、重选、磁选等;也有联合选矿流程。
如重选-浮选-重选,浮选-磁选、浮选-磁选-重选等。
还有的矿石,为回收其中有益矿物,需要采用机械选矿与化学选矿联合的流程。
(一)浮选流程1、单金属矿浮选原则流程单金属矿浮选原则流程的选择,主要取决于矿石中有用矿物的嵌布粒度特性。
一般多为不均嵌布,由于有益矿物和脉石硬度不同,易于泥化,影响回收率,制定选别流程的原则是尽量使用矿物经粗选、扫选得粗精矿或中矿,然后再磨再选,对于嵌布不均的有益矿物在粗磨的条件下能产出部分合格精矿,粗选尾矿进行再磨再选或得粗精矿再磨再选,而得第二种合格精矿。
处理复杂不均嵌布矿石时,由于该类矿石有用矿物嵌布不均,连生体解离范围较广,有时要用三段磨矿三段选别的流程。
处理含大量原生泥和可溶性盐类矿石时,由于矿泥和矿砂选别工艺不一样,一般用泥砂分选流程。
2、多金属矿浮选原则流程金属矿浮选是指两种有益矿物以上的金属矿浮选,选别流程一般有优选浮选、混合浮选然后分离浮选和优先、混合浮选兼有的选别流程。
如铅锌矿一般有铅锌依次的优先浮选和铅锌混合浮选得混合精矿经再磨(或不再磨)后分离浮选得铅精矿和锌精矿。
又如铜、铅锌、硫化铁的多金属矿,其浮选流程一般为先优先浮选铜铅,进行铜铅分离,优先浮选铜铅的尾矿进行锌、硫混合浮选然后分离锌硫或依次优先浮选锌、硫得锌精矿、硫精矿。
某些矿石可利用矿物的可浮性使用选择性捕收剂优先选出已解离的部分矿物,然后再进行混合浮选、分离浮选。
流程中有否再磨工序,视矿物解离情况而定。
优先浮选和混合浮选的优缺点如下:(1)混合浮选磨矿细度较直接优先浮选为粗,可节省磨矿费用。
(2)混合浮选的浮选机用量少于优选浮选,浮选药剂也节省些。
(3)优先浮选生产操作较易,容易达到精矿品位,而混合浮选的分离浮选,生产操作较优先浮选困难些。
上述是一般的优缺点比较,多金属矿选别流程要进行试验,对优先、混合浮选的设计方案进行比较选定。
(二)重选流程重力选矿在国内外仍广为应用,我国钨、锡选矿广泛使用重选流程,铁矿石的选别也有采用。
制定重选流程应注意矿物性脆,易于过粉碎的特点,因此要尽量做到“早收多收、早丢多丢、细粒归队、阶段磨矿、分级选别”。
使用重选法进行洗矿、预先丢废,可以提高选矿厂的生产能力,从而降低磨选成本。
在磨矿方面一般采用棒磨,最好与筛子闭路。
进行多段磨矿、多段选别。
由于重选选别设备,对不同粒级适应性和分选效果不同,应注意严格分级,矿砂按粒度归队再分别给入不同选别设备。
应进行粗细分选、贫富分选、难易分选。
矿石用重选处理,一般都是泥砂分选,分别用不同设备处理。
泥矿重选处理是较复杂的。
钨锡矿的矿泥处理,现阶段仍以重选为主,必要时根据矿泥情况辅以浮选、磁选等方法。
细泥重选处于是使用离心选矿机、矿泥摇床、皮带溜槽、横流皮带溜槽等等。
有的联合使用。
(三)磁选流程磁选是一种有效的选矿方法,根据各种矿物的比磁化系数的差异,用不同磁场强度的磁选机进行磁选,一般大致分为三类:1、强磁性矿物,比磁化系数大3000×10-6厘米3/克,如磁铁矿、磁黄铁矿等,用弱磁选设备即能有效与脉石矿物分离。
2、中磁性矿物,比磁化系数为500~3000×10-6厘米3/克,如半假象赤铁矿及某些钛铁矿、铬铁矿等,用中磁场磁选设备进行分选。
3、弱磁性矿物,比磁化系数为15~500×10-6厘米3/克,如赤铁矿、褐铁矿、碳酸铁矿、铁锰矿、硬锰矿、菱锰矿、金红石及某些钛铁矿等,用强磁选及其他方法回收。
比磁化系数小于15×10-6厘米3/克为非磁性矿物,如石英、长石、荧石等。
磁选流程要通过试验来选定,对磁选矿石来说,一般大中型磁选厂,当磨矿粒度大于0.2毫米时,常用一段磨矿磁选;小于0.2毫米时,则采用两段磨矿磁选,若在粗磨条件能选出部分合格精矿,则采用阶段磨矿阶段选别的流程。
若在粗磨条件经粗选可以丢弃尾矿,则可用粗磨粗选,粗精矿再磨再选的流程。
矿石中含有弱磁性矿物和强磁性矿物时,可用弱磁-强磁联合流程。
当矿石在块度较大的条件下可以丢弃废石时,要以采用磁滑轮预选丢废部分尾矿。
缺水地区,则采用干式磨矿干式磁选。
磁化焙烧磁选主要是处理弱磁性铁矿石,矿石在焙烧炉中加热并在适宜的气氛中使弱磁性铁矿物变为强磁性铁矿物,然后进行磁选可得到较好的选别指标。