铝合金电阻点焊的加工工艺研究
铝合金电阻点焊技术研究

车身制造工程BODY ENGINEERING46 ・2021年第03期铝合金电阻点焊技术研究基于轻量化的诉求,蔚来ES8车身铝材的使用率高达95%以上,这是全球量产的全铝车身中最高比例的铝材应用量。
同时为了确保车身强度刚性,ES8车身综合使用了3系、5系、6系和7系铝材成分的板材、挤出型材、高精密压铸件以及碳纤维复合材料,针对车身不同部位的强度和外观要求,突破传统钢车身单一材料的焊接工艺,实现了异性异种材料的连接。
ES8车身的连接工艺以结构胶粘接为核心,以SPR 自冲铆接和FDS 热熔直钻两种冷连接为主,辅助以铝点焊、激光焊和CMT 等热连接工艺。
铝点焊工艺规划1.铝点焊概念及特点铝点焊是电阻焊的一种,利用电流通过焊件及附近区域产生的电阻热作为热源将工件局部加热,同时加压使工件形成金属结合的一种方法。
由于铝合金材料有导热性好、导电率高、易与铜发生合金反应等特点,电阻点焊在铝合金材料结构件的连接中遇到能耗大、电极易失效、点焊质量不稳定等困难。
钢铝性能对比见表1。
基于车身轻量化连接技术的发展,本文重点介绍铝点焊工艺规划、质量评价及优化。
其中,工艺规划主要包含焊枪选择、电极帽选择和工装要求等。
质量评价及优化包含铝点焊检测标准及几种常见质量缺陷处理方法。
□ 安徽江淮集团汽车股份有限公司 吴卫枫 鲁厚国鉴于铝合金与碳钢性能的差异,铝点焊的主要特点如下:①铝材的电阻率是钢材的1/3,焊接相同厚度的铝材需要3~5倍的电流,铝合金分流损失比钢材分流严重;②铝合金具有高导热性(是钢材的4~5倍),焊接过程中热损失率较高,铝材焊接需要大电流和短时间;③铝合金焊核形成温度范围窄,铝点焊需要短焊接时间和快速的电流上升时间;④铝合金热膨胀系数高,在脆性温度区间内易产生热裂纹,铝点焊需要大的焊接压力和大的平面电极来控制焊接变形;⑤铝合金易氧化及合金化,氧化层焊接过程中易产生焊点气孔、泡群缺陷,铝点焊中铝、铜易生成合金,电极帽腐蚀快,需要频繁修磨,保持电极清洁,确保点焊质量;⑥连接强度相对低,常与结构胶配合使用;⑦不能连接异种材料,尤其是钢和铝;⑧无法做类似钢点焊的凿检,目视检查为主。
铝合金的点焊工艺

3.4 不等厚度和不同材料的点焊 熔核偏移:当进行不等厚度或不同材料的点焊时,熔核将不对称于其交界面, 而是向厚件或导电、导热性差的一边偏移。 偏移的结果将使薄件或导电、导热性好的工件焊透率减小,焊点强度降低。熔 核偏移是由两工件产热和散热条件不相同引起的。厚度不等时,厚件一边电阻大、 交界面离电极远,故产热多而散热少,致使熔核偏向厚件;材料不同时,导电、导 热性差的材料产热易而散热难,故熔核也偏向这种材料,见图5,图中p为电阻率。
图中2b表示用大接触面积的导电板做下电极,这样可以消除或减轻下面工 作的压痕,常用于装饰性面板的点焊。
图2c为,同时焊接两个或多个焊点的双面点焊,使用一个变压器而将各 电极并联。这时,所有电流通路的阻抗必须基本相等,而且每一焊接部 位的表面状态,材料厚度、电极压力都必须相同,才能保证通过各个焊 点的电流基本一致。
由于芯棒与工件的接触面远大于电极与工件的接触面,熔核将偏向与电极接触的 工件一侧。如果两工件的厚度不同,将厚件置于芯棒接触的一侧,则可减轻熔核 偏移程度。 当需要在封闭容器上焊接工件,而芯棒又无法伸入容器时,可以用Zn、Pb、 A1或其他较被焊金属熔点低的金属填满整个容器后进行焊接(图3f)。当容器壁厚 较大时,也可以用砂子或石蜡等不导电材料作为填料。焊接应采用强条件,以免 长时间加热使低熔点金属或石蜡熔化,导致电极压塌工件。 在大量生产中,单面多点点焊获得广泛应用。这时可采用由一个变压器供电, 各对电极轮流压住工件的形式(图4a),也可采用各对电极均由单独的变压器供电, 全部电极同时压住工件的形式(图4b)。后一形式具有较多优点,应用也较广泛。 其优点有:各变压器可以安置得离所连电极最近,因而其功率及尺寸能显著减速 小;各个焊点的工艺参数可以单独调节;全部焊点可能同时焊接,生产率高;全 部电极同时压住工件,可减少变形;多台变压器同时通电,能保证三相负载平衡。
铝合金电阻点焊的加工工艺研究

铝合金电阻点焊的加工工艺研究摘要随着时代的发展,社会的变迁,汽车,船舶,飞机,航天等重工业的不断发展,运用铝合金材料的地方也越来越多,吃饭离不开铝合金锅和盆,出行离不开汽车,汽车上很多零部件也是铝合金制造的,用的一些电气设备也会应用到铝合金,如手机啊,电脑啊,等等人们的生活已经离不开铝合金的这种工业材料,而优秀的铝合金铸造工艺也被人们越来越重视,越来越受到关注,本篇文章主要论述了铝合金电阻点焊的加工工艺的研究的必要性,铝合金电阻点焊的加工工艺的探究。
关键词铝合金;电阻点焊;必要性;加工工艺什么是电阻点焊,电阻点焊就是运用电阻点焊机进行交叉铝合金的焊接,可成型为铝合金网片或铝合金骨架。
电阻点焊是铝合金件加工的常用手段,如果电阻点焊的技术不过关,直接影响到加工件以后的日常使用。
所以功能可靠的电阻点焊机和好的点焊技术在铝合金件加工中是尤为重要的。
1 铝合金件加工中电阻点焊机的运用和缺陷1.1铝合金件加工中电阻点焊机的运用点焊机电阻焊重量检验是电阻焊生产中十分重要的一个环节,是保证产品质量、防止废品出厂的必不可少的手段。
在产品焊接钱和焊接过程中,通过检验工艺参数、试件和焊件的质量,及时发现焊接工艺参数。
时间和焊件的质量,及时发现焊接工艺参数和焊接条件的变化,以便采取相应的技术和管理上的措施来保证产品的焊接质量;在产品焊接之后,对焊件采用非破坏性检验方法,定性或定量地评定焊接接头或焊件的各中性能及冶金缺陷,从而鉴别焊件的质量等级与使用寿命。
为了保证产品的焊接质量,必须对焊机生产过程中的所有环节进行系统的检验,如焊件设计后的工艺审查、焊接有关各工序和焊接工序的工艺检验和质量评定、焊接工人技术水平的考试等。
焊接工序的工艺检验和质量评定。
点焊机焊接至俩个的检验十一电阻焊质量检验标准为一句的。
由于焊件的使用条件和采用的材料不同,因此质量检验的标准也不同,在国外和我国军工及重要宁用产品部门,以罕见的承载能力和受力状态、材料的焊接性能和焊件在系统中的主要性,将焊接接头分为一、二和三级。
6061铝合金低功率电阻点焊工艺优化

6061铝合金低功率电阻点焊工艺优化
6061铝合金低功率电阻点焊是一种重要的金属连接方式,在航空、航天、汽车等行业的应用十分广泛。
本文旨在通过对6061铝合金低功率电阻点焊工艺参数进行优化,提高点焊接头的力学性能和稳定性。
首先,本文在研究6061铝合金低功率电阻点焊工艺之前,对该材料的特性进行了分析。
6061铝合金具有良好的强度、耐腐蚀性和可焊性,但其导电性较差,容易产生氧化膜,导致接头焊接质量下降。
因此,在选用电极应力和电压时,需要注意保证电极与工件之间的
良好接触。
其次,本文选取了影响点焊品质的主要工艺参数,包括焊接电极压力、电极形状、电
极材料、焊接时间、焊接电流等进行研究。
针对不同工艺参数,分别设计实验方案,进行
实验研究,比较不同条件下焊接接头的力学性能和稳定性,分析不同参数对点焊质量的影响。
最后,通过分析实验数据,本文得出了6061铝合金低功率电阻点焊的优化工艺参数。
具体包括焊接电极压力为2kN、电极形状为平头、采用铜电极、焊接时间为100ms、焊接电流为4kA。
在这些优化参数下,点焊接头的强度得到了提高,并且焊接接头的质量稳定性
也得到了较好的保障。
总之,通过对6061铝合金低功率电阻点焊工艺参数的优化,可以进一步提高点焊品质,提高焊接接头的力学性能和稳定性,从而更好地满足实际工业生产需求。
铝电阻焊工艺
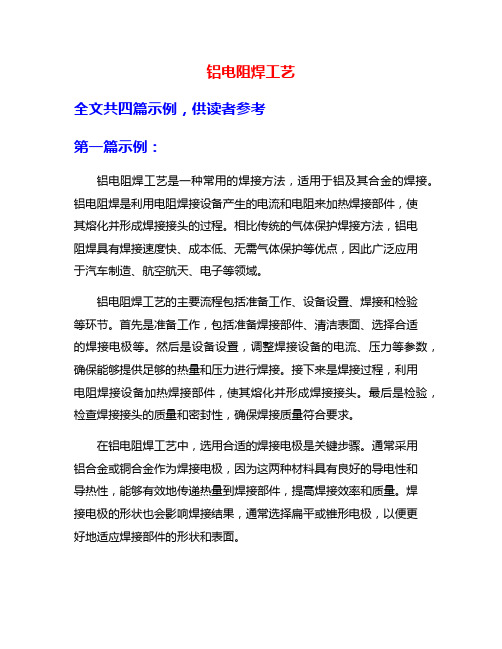
铝电阻焊工艺全文共四篇示例,供读者参考第一篇示例:铝电阻焊工艺是一种常用的焊接方法,适用于铝及其合金的焊接。
铝电阻焊是利用电阻焊接设备产生的电流和电阻来加热焊接部件,使其熔化并形成焊接接头的过程。
相比传统的气体保护焊接方法,铝电阻焊具有焊接速度快、成本低、无需气体保护等优点,因此广泛应用于汽车制造、航空航天、电子等领域。
铝电阻焊工艺的主要流程包括准备工作、设备设置、焊接和检验等环节。
首先是准备工作,包括准备焊接部件、清洁表面、选择合适的焊接电极等。
然后是设备设置,调整焊接设备的电流、压力等参数,确保能够提供足够的热量和压力进行焊接。
接下来是焊接过程,利用电阻焊接设备加热焊接部件,使其熔化并形成焊接接头。
最后是检验,检查焊接接头的质量和密封性,确保焊接质量符合要求。
在铝电阻焊工艺中,选用合适的焊接电极是关键步骤。
通常采用铝合金或铜合金作为焊接电极,因为这两种材料具有良好的导电性和导热性,能够有效地传递热量到焊接部件,提高焊接效率和质量。
焊接电极的形状也会影响焊接结果,通常选择扁平或锥形电极,以便更好地适应焊接部件的形状和表面。
在铝电阻焊工艺中,焊接部件的预处理对最终焊接质量起着至关重要的作用。
在进行铝电阻焊前,应先清洁焊接部件表面,除去油脂、污垢等杂质,以保证焊接接头的质量和密封性。
还需要对焊接部件进行对齐、夹紧等操作,确保焊接部件能够获得合适的加热和压力,从而完成焊接过程。
铝电阻焊工艺具有许多优点,但也存在一些注意事项。
首先是焊接温度控制,铝合金的熔点较低,易受热影响,因此在进行铝电阻焊时需要控制好焊接温度,避免焊接部件过热导致质量问题。
其次是焊接电流和压力的调节,应根据焊接部件的形状、大小和材质等因素调整焊接设备的电流和压力参数,以确保焊接接头均匀牢固。
最后是焊接部件的保护,铝合金易氧化,因此在焊接过程中需要采取相应的防护措施,例如采用氮气或惰性气体保护焊接部件,避免氧化对焊接质量的影响。
铝电阻焊工艺是一种快速、高效、低成本的焊接方法,适用于铝及其合金的焊接。
6061铝合金低功率电阻点焊工艺优化

6061铝合金低功率电阻点焊工艺优化【摘要】本文旨在探讨6061铝合金低功率电阻点焊工艺优化的相关问题。
在首先介绍了背景知识,指出6061铝合金在工业生产中的重要性,随后阐述了研究意义,即通过优化电阻点焊工艺参数,提高焊接质量和效率。
在重点分析了6061铝合金电阻点焊工艺参数的优化、影响因素的分析、优化方法的探讨以及试验设计与结果分析等内容。
在总结了文章的研究成果,展望了未来研究方向,指出进一步优化工艺将有助于提升焊接品质和效率。
通过本文的研究,可以为相关领域的工程技术人员提供一定的参考和指导,促进6061铝合金低功率电阻点焊工艺的进一步发展和提升。
【关键词】6061铝合金、低功率电阻点焊、工艺优化、影响因素、优化方法、试验设计、结果分析、优化效果评估、结论总结、未来研究方向1. 引言1.1 背景介绍6061铝合金是一种常用的铝合金材料,具有优良的机械性能和耐腐蚀性能。
在工业生产中,6061铝合金常常用于制造航空航天器件、汽车零部件、船舶结构等领域。
而电阻点焊是一种常见的连接技术,用于将金属部件焊接在一起。
由于6061铝合金的导热性较好,导致在电阻点焊过程中很容易出现热变形、焊接裂纹等质量问题。
对6061铝合金低功率电阻点焊工艺进行优化研究,对于提高焊接质量、降低成本具有重要意义。
通过优化工艺参数,合理控制焊接过程中的温度分布和热影响区,可以有效减少焊接变形和裂纹的发生。
优化工艺还可以提高工件的焊接强度和耐磨性,延长其使用寿命。
本文旨在通过对6061铝合金低功率电阻点焊工艺进行优化研究,探讨影响因素及优化方法,设计试验方案并分析结果,评估工艺优化效果,为进一步提高焊接质量和效率提供参考依据。
希望通过本文的研究,能够为相关行业的工程技术人员提供有益的参考和借鉴。
1.2 研究意义6061铝合金是一种常用的工业材料,在许多领域都有广泛的应用。
而在电子制造领域,6061铝合金低功率电阻点焊工艺的优化对于提高焊接质量、降低生产成本具有重要意义。
铝合金电阻点焊电极烧损机理的研究
铝合金电阻点焊电极烧损机理的研究 Ξ程方杰,廉金瑞,单 平,胡绳荪(天津大学材料学院,天津300072)摘 要:电极烧损是铝合金电阻点焊工艺当中存在的主要问题之一,它严重限制了该工艺的推广和应用,也是铝合金电阻点焊研究中的难点问题。
以实验为基础从多个角度探讨了铝合金电阻点焊时电极发生烧损的机理及其影响因素。
结果表明,铝合金点焊中电极的烧损是由于接触面上的局部高温熔化和铜铝之间的接触反应两方面因素共同作用的结果,电极烧损所形成的合金组织是以CuAl2为主的金属间化合物。
为进一步解决电极烧损问题提供了一些理论依据。
关键词:铝合金;电阻点焊;电极烧损中图分类号:TG44 文献标识码:A 文章编号:1004—244X(2003)02—0055—05 铝合金材料由于具有优良的耐腐蚀能力、高的比强度等特点,在诸如航空航天、船舶制造、汽车和机车制造等领域得到了广泛的应用。
而电阻点焊连接工艺在铝合金薄板结构件生产中的应用却远没有象在低碳钢薄板结构件生产中那样得到广泛的应用。
其中,铝合金电阻点焊中的电极烧损问题就是限制该工艺推广应用的主要原因之一。
电极发生烧损一方面使得电极的使用寿命变短,在生产过程中要频频修磨和更换电极,这既影响了生产效率又提高了生产成本;另一方面,电极烧损后表面粘有一层不均匀的合金组织,这使得在连续焊接的情况下接触情况变得不稳定而且接触电阻变大,这既影响了焊点质量的稳定性又容易导致飞溅的发生。
第三,由于电极烧损后表面会变得凹凸不平,这将导致焊点表面压痕变深、焊点表面不光滑等缺陷。
电极烧损问题是铝合金电阻点焊研究中的一个难点也是一个热点问题。
本文以实验为基础从多个角度探讨了铝合金电阻点焊时电极发生烧损的机理及其影响因素。
为进一步解决电极烧损问题提供了一些理论依据。
1 电极烧损的基本模式在铝合金的连续点焊过程中,铜电极与铝合金工件不断的发生粘连并形成合金组织,同时电极表面变得凹凸不平,这就是所谓的电极烧损。
铝合金电阻点焊和缝焊工艺
中华人民共和国航空工业部部标准HB/Z 77-84铝合金电阻点焊和缝焊工艺1 总则1.1 本标准适用于LF2、LF3、LF6、LF21、LY12、LY16、LC4、LC9变形铝合金电阻点焊及LF2、LF3、LF6、LF21变形铝合金电阻缝焊工艺。
1.2 焊工应有焊接航空产品的焊接操作证书。
2 设备2.1 焊机:点焊机、缝焊机。
2.1.1 焊接铝合金一般选用直流脉冲式、电容储能式、次级整流式等类型的焊机,缝焊机建议选用步进式的。
2.1.2 焊机最好具有三种加压方式:不变的压力、附加锻压力、附加予压和锻压力。
2.1.3 焊机电极臂应有足够的刚性,当施加最大额定压力时,臂长不大于500㎜,弹性挠度应不超过1.5㎜,臂长不大于1200㎜,挠度应不超过2㎜。
2.1.4 焊机在规定气压范围和额定焊接速度下工作时,电极压力的波动应不超过+8%。
上电极下降时应平稳无冲击现象。
2.1.5 焊机工作时,电源电压应在额定值的+5%范围内。
管道压缩空气压力应不低于5kg/cm2,室温应不低于15℃。
2.1.6 焊机的次级回路电阻,直流脉冲焊机应不大于60μΩ,交流焊机应不大于100μΩ,单个活动连结处电阻不大于20μΩ,单个固定结合处电阻不大于2μΩ。
焊机的次级回路电阻至少三个月测量一次,并记入设备档案中。
2.1.7 焊机应定期检修,活动导电部分应定期更换石墨润滑剂。
2.1.8 焊机应配备必要的专用工具。
2.1.9 焊机在安装、改装、大修或改变动力线路之后,由工厂主管部门组织进行鉴定,鉴定合格后才允许投入生产使用。
焊机鉴定内容如下:a.按附录A《焊机鉴定表》规定内容测量焊机的参数。
b.选用生产中常用的一种材料,取最薄和最厚的两种相同厚度的组合进行工艺稳定性试验,试验内容列于表1,试验结果应符合表1及HB5276--84《铝合金电阻点焊和缝焊质量检验》的规定。
在全部试验项目中有一项不合格,则应调整焊机重新试验,直到全部试验项目合格为止。
6061铝合金低功率电阻点焊工艺优化
6061铝合金低功率电阻点焊工艺优化6061铝合金是一种常用的工业铝合金材料,具有良好的可加工性、耐腐蚀性和强度,因此在汽车制造、航空航天和电子设备等领域得到广泛应用。
而在电子设备中,通常需要进行点焊工艺来连接不同部件,而低功率电阻点焊工艺则是其中一种常见的焊接方法。
本文将对6061铝合金低功率电阻点焊工艺进行优化研究,以提高焊接质量和效率。
6061铝合金是一种经典的热处理铝合金,具有优良的加工性能和焊接性能。
而在低功率电阻点焊工艺中,焊接过程中主要依靠电流通过两个不同材料间的接触面产生的热量,将两个材料点焊在一起。
低功率电阻点焊的优点在于焊接过程中对材料的热影响小,可以减少焊接区域的变形和金属组织的变化。
由于焊接过程中产生的热量较小,也可以减少对工件表面的损伤,保持工件的表面质量。
在6061铝合金低功率电阻点焊工艺中,通常需要考虑的参数包括焊接电流、焊接时间、电极压力等。
而选取合适的焊接参数并对焊接工艺进行优化,可以显著提高焊接质量,降低焊接成本,提高焊接生产效率。
1. 确定合适的焊接参数在确定焊接参数时,可以通过实验方法进行辅助。
首先选择一组初步的焊接参数,然后进行一系列的焊接实验,观察焊接接头的质量、焊接强度和焊接表面的状态,从而确定最佳的焊接参数。
2. 优化电极设计电极在低功率电阻点焊工艺中起到了传递电流和施加压力的作用。
合适的电极设计可以对焊接工艺的质量起到显著的影响。
在6061铝合金低功率电阻点焊工艺中,通常可以选择适当形状和尺寸的电极头来适应不同的焊接需求。
对于需要在较小的区域进行焊接的工件,可以选择较小的电极头来实现焊接。
还可以选择合适的电极材料,通常选取导电性好、耐磨性强的材料作为电极材料,以提高焊接质量和电极的使用寿命。
3. 控制焊接环境焊接环境的控制对于6061铝合金低功率电阻点焊工艺也是至关重要的。
在焊接过程中,需要保持焊接区域的清洁,并且控制好焊接环境的温度和湿度。
保持焊接区域的清洁可以有效地避免焊接接头表面的氧化和杂质的影响。
非等厚两板铝合金电阻点焊熔核偏移过程研究
10.试验与研究.焊接技术第42卷第5期2011生!旦文章编号:1002—025X(2013)05—0010—04非等厚两板铝合金电阻点焊熔核偏移过程研究颜福裕1’2,罗震1.一,白杨1.一,李洋1'2(1.天津大学材料科学与工程学院,天津300072;2.天津大学天津市现代连接技术重点实验室,天津300072)摘要:在非等厚板材的电阻点焊中,熔核的偏移对点焊质量有很大的影响。
本文通过M A T L A B建立非等厚两层板铝合金二维轴对称热传导模型.对厚度组合为1.0m m/2.0m m的5052铝合金电阻点焊温度场进行了模拟,得出熔核在非等厚板中的形核过程和偏移的本质原因.并利用高速摄影试验验证了模型的准确性。
结果表明:在点焊初期,薄板侧的高温区大于厚扳侧高温区;随着焊接时间的增加.高温区逐渐偏向厚板,并最终形成一个偏向厚板侧的熔核。
这是由于在点焊熔核形成前,散热作用的强弱是影响高温区域偏移的主导因素。
熔核开始形成后.析热作用的强弱成为主导熔核偏移的因素,熔核向具有大电阻、散热少的厚板一侧偏移。
因此,熔核偏移主要是由焊接区在加热过程中焊件析热和散热不均所致。
关键词:电阻点焊;熔核偏移;数值模拟;高速摄像中图分类号:TG453.9文献标志码:BO引言电阻点焊是现代汽车制造工业中重要的工艺方法,它具有生产效率高、易于实现自动化而被广泛地应用于汽车的焊装生产线上。
近年来,随着铝合金在汽车制造和结构部件中的广泛使用,有必要对铝合金电阻点焊进行更深入的了解。
目前.很多学者利用有限元理论.通过数值计算的方法来模拟电阻点焊过程,获得对该过程的定量认识(如焊接温度场、焊接变形和焊接应力场),并预测熔核尺寸与质量.如:B r ow ne等用建立的混合模型模拟了铝合金电阻点焊过程[i-2];上海交通大学的龙昕对镀锌钢板的电阻点焊建立了轴对称有限元模型来模拟温度场分布。
3j。
但是,目前点焊过程的数值模拟研究大多数限于2层等厚板的连接,较少有人涉及非等厚2层板点焊研究,这方面公开文献也非常少。
- 1、下载文档前请自行甄别文档内容的完整性,平台不提供额外的编辑、内容补充、找答案等附加服务。
- 2、"仅部分预览"的文档,不可在线预览部分如存在完整性等问题,可反馈申请退款(可完整预览的文档不适用该条件!)。
- 3、如文档侵犯您的权益,请联系客服反馈,我们会尽快为您处理(人工客服工作时间:9:00-18:30)。
湖北工业大学毕业设计(论文)
摘要
铝合金电阻点焊技术是一项即将在汽车制造中获得广泛应用的技术,其在各种焊接方法中,具有静强度高、可靠性好、性能稳定、产效率高和易于实现自动化等优点,对车身的轻量化有着重要的作用及研究意义,但铝合金电阻焊生本身也具有很大的焊接缺陷,包括铝合金的焊接性不好、焊点质量不稳定、电极烧损严重使用寿命短等,需要我们更好的试验研究,解决铝合金的焊接问题。
本文慨述了铝合金电阻点焊的工艺特点、点焊工艺中的问题,以及国内外在这方面的研究现状,进行了焊接接头的影响因素的试验,并指出了铝合金点焊时影响接头质量稳定性的因素及工艺缺陷。
对工艺焊接参数进行了正交分析实验,获得了最佳的工艺优化,完成了铝合金的加工工艺设计。
1。