铝合金电阻点焊的加工工艺研究
电阻点焊质量控制技术的方法与研究现状

电阻点焊质量控制技术的方法与研究航空制造工程学院080142 05 韦谨宗0 前言电阻点焊是一种高效的焊接方法,具有能量集中、变形小、辅助工序少、无须填加焊接材料、生产效率高、操作简便和易于实现自动化等特点,广泛应用于航空、航天、汽车制造等行业生产中,但是由于点焊过程以电流通过焊接区产生的电阻热为热源,是一个高度非线性、多变量藕合作用并伴随着大量随机不确定因素的过程,焊点接头质量受各种不可测因素的影响;并且焊点熔核处于封闭状态,使形核过程无论是在焊接期间还是在焊后都无法直接观测到,质量信息的提取比较困难;焊点形核凝固时间短暂,同时要求特定、精确的温度场分布,环境的瞬时改变可能造成严重后果,出现裂纹、缩孔、疏松、偏析、深度压痕、喷溅乃至虚焊、漏焊、弱焊、烧穿等缺陷,造成焊点质量不稳定和难以控制,严重限制和影响了点焊技术在重要结构上的广泛使用[1].。
传统生产中,焊接质量是通过稳定焊接工艺参数和焊后检验来保证的。
由于焊点接头质量受大量随机因素的影响,仅通过稳定工艺参数不可能全面保证焊点质接缺陷、实现焊接质量在线监控,因此发展一种在线、非破坏性、低成本、诊断可靠性高的质量评判系统对于现实生产及点焊方法的广泛使用是非常有意义的。
现代信号分析处理、人工智能、模式识别、数据挖掘等信息处理方法凭借其明确的问题定义、严格的数学基础、坚实的理论框架和广泛的应用价值,为处理点焊过程监测特征参量与焊点质量评价指标之间复杂的多元非线性相关关系提供了丰富的方法。
1电阻点焊质量监测技术的方法点焊过程通常由预压、焊接、锻压三个阶段构成[2],是一个电场、热场、力场等各种场祸合作用的过程,因此产生焊接缺陷的原因必然隐含于各种场监测参量的动态变化之中。
点焊过程的工艺参数主要有焊接电流、焊接时间、预紧力、顶锻力等。
接头形式和焊接规范一定时,焊点质量主要取决于电极、工件表面、接触面的微观状态、动态变化,它们影响点焊过程中能量的输入与分配、局部热积累速度和热量的分布。
铝合金焊接技术研究现状及进展
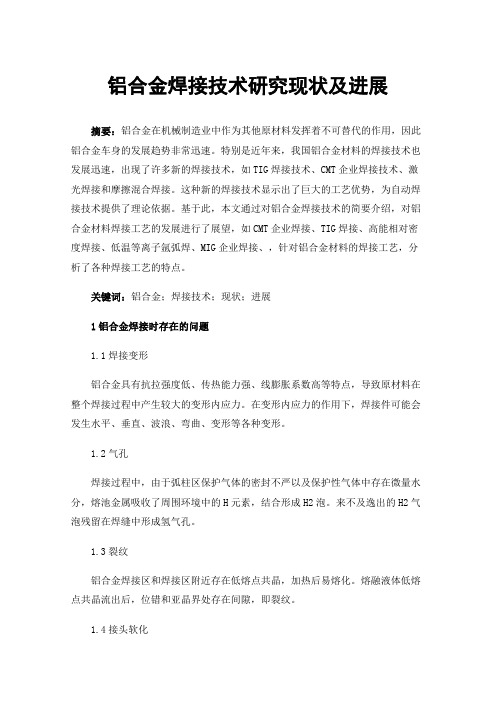
铝合金焊接技术研究现状及进展摘要:铝合金在机械制造业中作为其他原材料发挥着不可替代的作用,因此铝合金车身的发展趋势非常迅速。
特别是近年来,我国铝合金材料的焊接技术也发展迅速,出现了许多新的焊接技术,如TIG焊接技术、CMT企业焊接技术、激光焊接和摩擦混合焊接。
这种新的焊接技术显示出了巨大的工艺优势,为自动焊接技术提供了理论依据。
基于此,本文通过对铝合金焊接技术的简要介绍,对铝合金材料焊接工艺的发展进行了展望,如CMT企业焊接、TIG焊接、高能相对密度焊接、低温等离子氩弧焊、MIG企业焊接、,针对铝合金材料的焊接工艺,分析了各种焊接工艺的特点。
关键词:铝合金;焊接技术;现状;进展1铝合金焊接时存在的问题1.1焊接变形铝合金具有抗拉强度低、传热能力强、线膨胀系数高等特点,导致原材料在整个焊接过程中产生较大的变形内应力。
在变形内应力的作用下,焊接件可能会发生水平、垂直、波浪、弯曲、变形等各种变形。
1.2气孔焊接过程中,由于弧柱区保护气体的密封不严以及保护性气体中存在微量水分,熔池金属吸收了周围环境中的H元素,结合形成H2泡。
来不及逸出的H2气泡残留在焊缝中形成氢气孔。
1.3裂纹铝合金焊接区和焊接区附近存在低熔点共晶,加热后易熔化。
熔融液体低熔点共晶流出后,位错和亚晶界处存在间隙,即裂纹。
1.4接头软化在铝合金的整个焊接过程中,熔化的形状记忆合金冷却速度更快,并且很容易冷凝。
凝固后,α离子晶体和非平衡碳化物相,随着制冷效率的进一步扩大,位错处产生的网状碳化物机制降低了接头的抗压强度和塑性,导致接头软化。
2铝合金焊接技术策略2.1点链接技术现状在某些情况下,一般的焊接工艺无法进行焊接过程,因此必须调整焊接方式。
例如,在车辆加工制造行业,点焊已得到广泛应用。
因此,针对铝合金点焊技术的发展趋势,对铝合金点焊技术在加工制造行业的推广应用具有重要的现实意义。
铝合金点焊的关键加工技术包括电阻点焊、混合摩擦点焊、激光点焊等。
铝合金的点焊
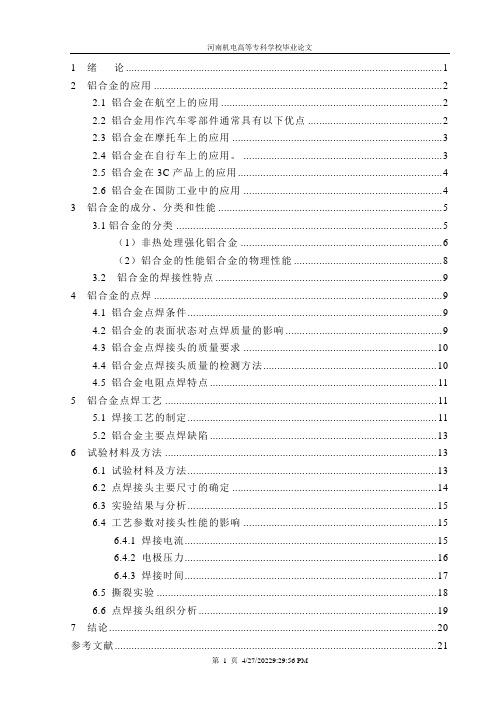
1 绪论 (1)2 铝合金的应用 (2)2.1 铝合金在航空上的应用 (2)2.2 铝合金用作汽车零部件通常具有以下优点 (2)2.3 铝合金在摩托车上的应用 (3)2.4 铝合金在自行车上的应用。
(3)2.5 铝合金在3C产品上的应用 (4)2.6 铝合金在国防工业中的应用 (4)3 铝合金的成分、分类和性能 (5)3.1铝合金的分类 (5)(1)非热处理强化铝合金 (6)(2)铝合金的性能铝合金的物理性能 (8)3.2铝合金的焊接性特点 (9)4 铝合金的点焊 (9)4.1 铝合金点焊条件 (9)4.2 铝合金的表面状态对点焊质量的影响 (9)4.3 铝合金点焊接头的质量要求 (10)4.4 铝合金点焊接头质量的检测方法 (10)4.5 铝合金电阻点焊特点 (11)5 铝合金点焊工艺 (11)5.1 焊接工艺的制定 (11)5.2 铝合金主要点焊缺陷 (13)6 试验材料及方法 (13)6.1 试验材料及方法 (13)6.2 点焊接头主要尺寸的确定 (14)6.3 实验结果与分析 (15)6.4 工艺参数对接头性能的影响 (15)6.4.1 焊接电流 (15)6.4.2 电极压力 (16)6.4.3 焊接时间 (17)6.5 撕裂实验 (18)6.6 点焊接头组织分析 (19)7 结论 (20)参考文献 (21)1 绪论随着现代工业的发展,对工业材料的要求越来越向着质量轻﹑强度高、易加工的方向发展。
由于铝及铝合金材料具有一系列的优良特性,已广泛应用于国民经济的各个领域,成为发展国民经济与提高人民物质生活和文化生活水平的重要基础材料。
近二十年来,我国的铝加工业发展十分迅速,其产量已从1980年不到30万吨,发展到2005年的583.7万吨。
同时,出现了许多的新材料、新技术、新工艺及新设备。
我国已经成为名副其实的铝业大国。
铝和铝合金具有优异的物理性能和力学性能,其密度低、比强度高、热导率高、电导率高,耐蚀能力强,已广泛应用于机械、电力、化工、轻工、航空、航天、铁道、舰船、车辆等工业内的焊接结构产品上,例如飞机、飞船、火箭、导弹、高速铁道机车和车辆、鱼雷和鱼雷快艇、轻型汽车、自行车和赛车、大小化工容器、空调器、热交换器、雷达天线、微波器件等,都采用了铝和铝合金材料,制成各种熔焊、电阻焊、钎焊结构。
铝及铝合金焊接工艺的研究 毕业论文

毕业论文毕业论文题目:铝及铝合金焊接工艺的研究系部船舶工程系专业焊接技术及自动化班级09级焊接1班学生姓名学号指导教师2011年10 月19日摘要铝及铝合金是工业中应用最广泛的一类有色金属结构材料,在航空、航天、汽车、机械制造、船舶及化学工业中已大量应用。
随着近年来科学技术以及工业经济的飞速发展,对铝合金焊接结构件的需求日益增多,使铝合金的焊接性研究也随之深入。
铝合金的广泛应用促进了铝合金焊接技术的发展,同时焊接技术的发展又拓展了铝合金的应用领域,因此铝合金的焊接技术正成为研究的热点之一。
关键词:铝及铝合金手工氩弧焊焊接特点AbstractAluminum and aluminum alloy is the most widely used in industry of a class of non-ferrous metal structure material, in aviation, aerospace, automotive, machinery manufacturing, shipping and the chemical industry has a large application.Recent years, with science and technology and industrial economic development, to the aluminum alloy welding structure of the increasing demand, the aluminum alloy welding sex research will be further. The wide application of aluminum alloy aluminum alloy welding technology promoted thedevelopment, and welding technology development and expand the application field of aluminum alloy, aluminum alloy welding technology is therefore become one of the hot spot in the research.Keywords:Aluminum and Aluminum alloy、Handmade Argon Arc Welding、Welding characteristics•目录摘要 (1)英文摘要 (2)第一章绪论 (4)第二章从应用的角度掌握有色金属的分类 (5)2-1 什么是金属盒非金属,什么是黑色金属和有色金属,什么事合金 (5)2-2 有色金属的分类 (5)第三章铝及铝合金的性能分析其特点及焊接性 (6)3-1 铝合金的分类、成分和性能 (6)3-2 铝合金的焊接性特点 (10)第四章铝及铝合金的焊接工艺方法 (12)4-1 铝合金的焊接方法 (12)4-2 铝用焊接材料 (14)4-3 铝及铝合金的焊接工艺方法 (17)第五章铝及铝合金的焊接实例 (30)5-1 铝合金汽车油箱的焊接实例 (30)5-2 海外铝合金机器人的焊接实例 (32)第六章总结 (34)参考文献 (35)致谢 (36)第一章绪论有色金属non-ferrous metal,狭义的有色金属又称为非铁金属,是铁、锰、铬以外的所有金属的统称。
【连接技术】汽车铝合金电阻点焊的改进

【连接技术】汽车铝合金电阻点焊的改进大多数汽车车身都采用电阻点焊(PSW)焊接,因为它成本低,速度快。
随着铝合金在汽车中的应用,汽车制造商期望能继续采用电阻点焊对铝合金进行连接。
然而,铝合金材料表面存在绝缘氧化层,若采用同样点焊工艺进行焊接将存在重大问题。
2014款雪佛兰克尔维特跑车的制造采用了通用汽车公司(GM)多环圆顶电极专利技术。
A-正在焊接的克尔维特跑车的空间架构;B-空间架构上的焊点;C-空间架构和D车体结构(照片由通用汽车公司授权)。
通用汽车公司(GM)发明的多环圆顶(MRD)电极专利解决了这一问题。
目前,该项关键技术被应用于汽车构架制造上,比如2014款雪佛兰克尔维特跑车—如上图所示。
新电极在焊接面上设计了几个凸起的同心环,焊接时使相接触的铝合金表面产生变形,从而刺破铝合金表面的氧化层,这个过程对铝合金点焊工艺的稳固性至关重要。
新开发的涂层刀片能够切掉电极焊接面上的凸起环,进一步推动了其在通用工厂的应用。
焊接面的重要性为了保证一致、高质量的焊接工艺,电极的焊接面不能出现严重退化。
同时,焊接面还需定期涂层进行维护。
最关键的是,涂层频率和切削深度必须足够,确保电极焊接面的几何形状。
然而,这两者都需要去除掉大量电极材料,造成电极更换频繁,制造成本升高。
铝合金点焊时,传统电极焊接面的磨损主要是由于铜电极和铝合金发生冶金反应,导致在电极焊接面上形成蚀坑。
一旦电极焊接面形成点蚀,要完全去除掉这些蚀坑就需要增加涂层,这会大大缩短电极寿命。
如果涂层也不能完全去除这些蚀坑,则致使电极表面更迅速地恶化,反过来导致形成不合格焊点。
电极的宏观变形一般发生在钢铁材料点焊中,而不会发生在铝合金点焊工艺上,因为后者的熔核温度要低得多。
然而,MRD电极上的截面小,因此使用中很容易产生变形或压扁。
确定电极关键因素该研究的目的是探求铝合金点焊时MRD焊接电极的磨损情况及其磨损机理。
针对铜电极和铝合金间的冶金反应产生的机械变形和焊接面腐蚀两部分内容进行研究。
点焊铝合金的一般工艺
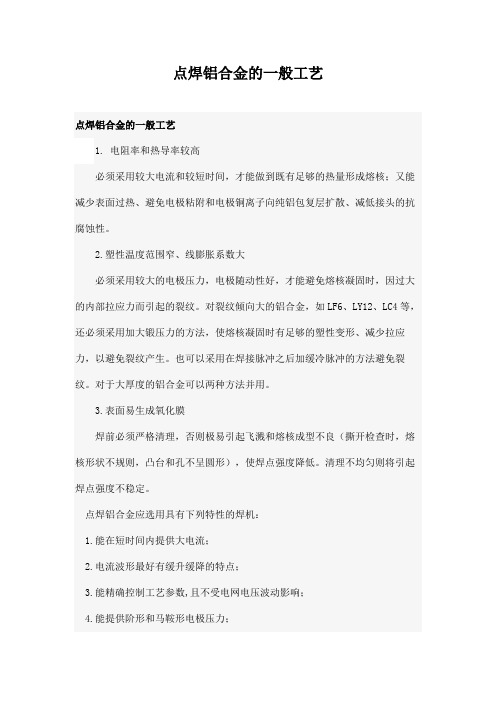
点焊铝合金的一般工艺点焊铝合金的一般工艺1.电阻率和热导率较高必须采用较大电流和较短时间,才能做到既有足够的热量形成熔核;又能减少表面过热、避免电极粘附和电极铜离子向纯铝包复层扩散、减低接头的抗腐蚀性。
2.塑性温度范围窄、线膨胀系数大必须采用较大的电极压力,电极随动性好,才能避免熔核凝固时,因过大的内部拉应力而引起的裂纹。
对裂纹倾向大的铝合金,如LF6、LY12、LC4等,还必须采用加大锻压力的方法,使熔核凝固时有足够的塑性变形、减少拉应力,以避免裂纹产生。
也可以采用在焊接脉冲之后加缓冷脉冲的方法避免裂纹。
对于大厚度的铝合金可以两种方法并用。
3.表面易生成氧化膜焊前必须严格清理,否则极易引起飞溅和熔核成型不良(撕开检查时,熔核形状不规则,凸台和孔不呈圆形),使焊点强度降低。
清理不均匀则将引起焊点强度不稳定。
点焊铝合金应选用具有下列特性的焊机:1.能在短时间内提供大电流;2.电流波形最好有缓升缓降的特点;3.能精确控制工艺参数,且不受电网电压波动影响;4.能提供阶形和马鞍形电极压力;5.机头的惯性和摩擦力小,电极随动性好.当前国内使用的多为300~600kVA的直流脉冲、三相低频和次极整流焊机,个别的达1000kVA,均具有上述特征。
也有采用单相交流焊机的但仅限于不重要工件。
点焊铝合金的电极点焊铝合金的电极应采用1类电极合金,球形端面,以利于压固熔核和散热。
点焊铝合金电极为何容易粘着?由于电流密度大和氧化膜的存在,铝合金点焊时,很容易产生电极粘着,电极粘着不仅影响外观质量,还会因电流减小而降低接头强度。
为此需经常修整电极。
电极每修整一次后可焊的焊点数与焊接条件、被焊金属型号、清理情况、有无电流波形调制,电极材料及其冷却情况等因素有关。
通常点焊纯铝为5~10点,点焊LF6、LY12时为避免5~30点。
防锈铝LF21的特性?其焊接规范?防锈铝LF21强度底,延性好,有较好的焊接性,不产生裂纹,通常采用固定不变的电极压力。
电阻点焊方法和工艺
电阻点焊方法和工艺点焊方法和工艺一、点焊方法:点焊通常分为双面点焊和单面点焊两大类。
双面点焊时,电极由工件的两侧向焊接处馈电。
典型的面点焊方式如图11-5所示。
图中a是最常用的方式,这时工件的两侧均有电极压痕。
图中b表示用大焊接面积的导电板做下电极,这样可以消除或减轻下面工件的压痕。
常用于装饰性面板的点焊。
图中c为同时焊接两个或多个点焊的双面点焊,使用一个变压器而将各电极并联,这时,所有电流通路的阻抗必须基本相等,而且每一焊接部位的表面状态、材料厚度、电极压力都需相同,才能保证通过各个焊点的电流基本一致。
图中d为采用多个变压器的双面多点点焊,这样可以避免c的不足。
单面点焊时,电极从工件的同一侧送入焊接位置。
典型的单面点焊方法如图11-6所示。
图中a为单面单点点焊。
不形成焊点的焊条采用大直径、大接触面,以降低电流密度。
图中B为单面双点点焊,无分流。
此时,所有焊接电流流过焊接区域。
在图C中,有一个单面双点点焊,流过上部工件的电流没有通过焊接区域形成气流。
为了为焊接电流提供低电阻路径,在工件下方垫一块铜垫板。
图中D显示,当两个焊接点之间的距离L较大时,例如,在焊接骨架构件和复合板时,为了避免因加热不当导致复合板翘曲,降低两电极之间的电阻,采用了特殊的铜桥a,它与电极同时压在工件上。
在大量生产中,单面多点点焊获得广泛应用。
这时可采用由一个变压器供电,各对电极轮流压住工的型式(图11-7a),也可采用各对电极均由单独的变压器供电,全部电极同时压住工件的型式(图11-7b).后一型式具有较多优点,应用也较广泛。
其优点有:各变压器可以安置得离所联电极最近,因而。
其功率及尺寸能显著减小;各个焊点的工艺参数可以单独调节;全部焊点可以同时焊接、生产率高;全部电极同时压住工件,可减少变形;多台变压器同时通电,能保证三相负荷平衡。
二、点焊工艺参数选择通常,电极端面的形状和尺寸根据工件的材料和厚度以及材料的焊接条件表确定。
非等厚两板铝合金电阻点焊熔核偏移过程研究
10.试验与研究.焊接技术第42卷第5期2011生!旦文章编号:1002—025X(2013)05—0010—04非等厚两板铝合金电阻点焊熔核偏移过程研究颜福裕1’2,罗震1.一,白杨1.一,李洋1'2(1.天津大学材料科学与工程学院,天津300072;2.天津大学天津市现代连接技术重点实验室,天津300072)摘要:在非等厚板材的电阻点焊中,熔核的偏移对点焊质量有很大的影响。
本文通过M A T L A B建立非等厚两层板铝合金二维轴对称热传导模型.对厚度组合为1.0m m/2.0m m的5052铝合金电阻点焊温度场进行了模拟,得出熔核在非等厚板中的形核过程和偏移的本质原因.并利用高速摄影试验验证了模型的准确性。
结果表明:在点焊初期,薄板侧的高温区大于厚扳侧高温区;随着焊接时间的增加.高温区逐渐偏向厚板,并最终形成一个偏向厚板侧的熔核。
这是由于在点焊熔核形成前,散热作用的强弱是影响高温区域偏移的主导因素。
熔核开始形成后.析热作用的强弱成为主导熔核偏移的因素,熔核向具有大电阻、散热少的厚板一侧偏移。
因此,熔核偏移主要是由焊接区在加热过程中焊件析热和散热不均所致。
关键词:电阻点焊;熔核偏移;数值模拟;高速摄像中图分类号:TG453.9文献标志码:BO引言电阻点焊是现代汽车制造工业中重要的工艺方法,它具有生产效率高、易于实现自动化而被广泛地应用于汽车的焊装生产线上。
近年来,随着铝合金在汽车制造和结构部件中的广泛使用,有必要对铝合金电阻点焊进行更深入的了解。
目前.很多学者利用有限元理论.通过数值计算的方法来模拟电阻点焊过程,获得对该过程的定量认识(如焊接温度场、焊接变形和焊接应力场),并预测熔核尺寸与质量.如:B r ow ne等用建立的混合模型模拟了铝合金电阻点焊过程[i-2];上海交通大学的龙昕对镀锌钢板的电阻点焊建立了轴对称有限元模型来模拟温度场分布。
3j。
但是,目前点焊过程的数值模拟研究大多数限于2层等厚板的连接,较少有人涉及非等厚2层板点焊研究,这方面公开文献也非常少。
铝合金点焊工艺标准
铝合金点焊工艺标准1.材料选择在铝合金点焊过程中,需要选择符合要求的铝合金材料。
通常,母材应为5系或6系铝合金,其质量等级应为优质的1级或2级铝合金。
另外,为了确保焊接质量,应选择具有良好抗氧化性能、高导热系数和高电阻率的铝合金材料。
2.焊接前准备在进行点焊前,需要对铝合金材料进行表面清洁处理。
首先,应使用砂纸或磨光机将表面氧化膜打毛,并用水清洗干净。
同时,需要去除铝合金材料表面的油污、杂质等,以防止焊接时产生气孔、裂纹等问题。
3.焊接参数设定在铝合金点焊过程中,需要设置的焊接参数包括电流、电压、焊接速度和保护气体等。
电流和电压是影响焊接质量的主要因素,应根据母材的材质、厚度等因素进行选择。
焊接速度应保持均匀,以防止出现过热或未熔合现象。
保护气体应选择高纯度氩气或氦气,以防止氧化和污染。
4.点焊操作点焊操作是铝合金点焊工艺的核心环节,包括定位焊点、点焊顺序和移动轨迹等步骤。
在定位焊点时,应准确确定焊接位置,并保证足够的搭接量。
点焊顺序应遵循先下后上、先中间后两边的原则,以保证焊接质量和效率。
移动轨迹应保持稳定,以防止出现偏移和重叠等问题。
5.质量检查铝合金点焊完成后,需要对焊接质量进行检查。
首先,应检查焊点的牢固性和稳定性,以防止出现脱落和断裂等现象。
其次,应检查焊点的外观质量,包括是否平整、光滑、无气孔等。
最后,应对焊接接头的力学性能进行检测,包括抗拉强度、屈服强度和伸长率等。
6.焊后处理铝合金点焊完成后,需要进行焊后处理。
首先,应去除飞溅物和熔渣,以防止影响后续加工和使用。
其次,应对焊点进行打磨和修整,以使表面更加平整和光滑。
最后,应对焊接区域进行清洗和防护处理,以防止氧化和腐蚀等问题。
7.安全措施在铝合金点焊过程中,需要注意安全操作。
首先,应穿戴防护服、手套等安全用品,以防止烫伤、割伤等危险。
其次,应正确处理危险废弃物,如废渣、废气等,以防止污染环境和危害健康。
同时,应定期对焊接设备进行检查和维护,以确保其正常运转和使用安全。
铝合金电阻焊接方法
铝合金电阻焊接方法铝合金电阻焊接方法铝合金电阻焊接是一种常用的焊接方法,广泛应用于铝合金制品的生产和加工过程中。
它具有焊接速度快、焊缝质量好、适用于大批量生产等优点,因此备受青睐。
下面将介绍铝合金电阻焊接的具体方法,以供参考。
首先,铝合金电阻焊接的准备工作至关重要。
首先要确保焊接设备的正常工作状态以及相关工具的可用性。
检查电阻焊机的电源接线和控制面板,确保各项指示灯和开关正常。
同时,检查焊接钳、焊具等工具是否完好无损,确保其能够正常使用。
其次,准备焊件和焊接区域。
清理铝合金表面的氧化层和污染物,以保证焊接时焊缝的质量和强度。
可通过去氧除污剂进行清洗,或者使用机械方法研磨、擦拭来清理。
在焊接区域周围先进行遮挡和防护措施,以保护周围不需要焊接的区域。
然后,进行焊接参数的调整。
铝合金具有导电率高、热传导量大,因此焊接时需要加大电流和加热时间,以达到合适的焊接温度。
根据焊接材料的种类和厚度,调整焊机的电流和时间设置,确保焊接区域能够达到预定的温度。
此外,还要根据具体情况确定焊接压力和焊接距离的大小,以保证焊接效果。
接下来,进行实际的焊接操作。
将焊机的电极夹住铝合金焊件,确保夹紧力均匀分布,避免出现过大或过小的压力。
按下启动按钮,电流开始流过焊接区域,产生热量,将焊接区域加热至熔点。
在合适的时间内保持加热,然后松开电极,焊接完成。
过程中注意观察焊接区域的状态,如有需要可以进行调整。
最后,进行焊后处理。
焊接完成后,要及时对焊缝进行清理和处理。
清除残留的焊接渣和污垢,可以使用焊后清洁剂进行清洗,确保焊缝的外观和质量。
焊接后还可以进行表面处理,如涂上保护剂,提高焊接区域的抗氧化能力。
综上所述,铝合金电阻焊接是一种重要的焊接方法,其准备工作、焊接参数的调整、实际操作和焊后处理等步骤的正确与否,直接影响焊接效果和产品的质量。
因此,在进行铝合金电阻焊接时,务必仔细操作,确保每一步都正确无误。
只有这样,才能实现铝合金焊接的高质量和高效率。
- 1、下载文档前请自行甄别文档内容的完整性,平台不提供额外的编辑、内容补充、找答案等附加服务。
- 2、"仅部分预览"的文档,不可在线预览部分如存在完整性等问题,可反馈申请退款(可完整预览的文档不适用该条件!)。
- 3、如文档侵犯您的权益,请联系客服反馈,我们会尽快为您处理(人工客服工作时间:9:00-18:30)。
摘要 铝合金电阻点焊技术是一项即将在汽车制造中获得广泛应用的技术,其在各种焊接方法中,具有静强度高、可靠性好、性能稳定、产效率高和易于实现自动化等优点,对车身的轻量化有着重要的作用及研究意义,但铝合金电阻焊生本身也具有很大的焊接缺陷,包括铝合金的焊接性不好、焊点质量不稳定、电极烧损严重使用寿命短等,需要我们更好的试验研究,解决铝合金的焊接问题。本文慨述了铝合金电阻点焊的工艺特点、点焊工艺中的问题,以及国内外在这方面的研究现状,进行了焊接接头的影响因素的试验,并指出了铝合金点焊时影响接头质量稳定性的因素及工艺缺陷。对工艺焊接参数进行了正交分析实验,获得了最佳的工艺优化,完成了铝合金的加工工艺设计。 Abstract Resistance spot technology of Aluminum is applied widely in automobile manufacturing. In Itsvarious welding method, with the advantages of static strength, high reliability, performance stability,high production efficiency and easy to realize automation.It`s play a important role in the lightweight of car and have a great research significance. But aluminum alloy resistance we- lding itself also has great welding defects. Including the bad of aluminum alloy welding sex, anstable of solder qualityand so on . Then we need to solve the experimental research of alum-inumwelding problembetter.This paper describes the process characteristicsof aluminium alloy resistance spot. the problem of welding process and the research status in this respect at home andabroad.we have a experiment of the factors in welding joint .Pointed out the majorfactors which affect of the quality of welding joints in aluminum alloy spot. And we have a orthogonal analysis experiment of the process of welding parameters.The last ,Acquired optimal processoptimization and pleted the design of aluminum alloy processing. 目录摘要 Abstract 目录 第一章绪论1 1.1 前言1 1.2 铝合金电阻点焊研究的必要性1 1.3 铝合金点焊所存在的问题及现状研究3 1.3.1 所存在的问题3 1.3.2 问题的研究6 1.4 本文研究的内容以及方案7 第二章铝合金电阻点焊工艺特点分析8 2.1 电阻点焊的原理及特点8 2.1.1 焊点的形成8 2.1.2 点焊的工艺参数9 2.1.3 点焊的焊接循环10 2.1.4 点焊的应用10 2.2 铝合金电阻点焊的工艺特点11 2.2.1 焊接性能分析11 2.2.2 工艺特点及分析12 2.2.3 工艺措施及焊机的选择13 2.3 微量元素在铝合金电阻焊中的作用13 2.4 焊前的工件清理14 2.5电阻点焊的焊接工艺参数15 2.6 本章小结17 第三章铝合金点焊的试验设计及其分析18 3.1 实验材料及设备18 3.1.1 实验材料18 3.1.2 试验设备18 3.2 试验方法19 3.2.1 加压方式20 3.2.2 实验参数20 3.2.3 试验结果21 3.3 实验结果分析24 3.3.1 焊接电流不同对工艺的影响24 3.3.2 焊接时间不同对接头的影响25 3.3.3 电极压力对接头性能的影响26 3.4 点焊缺陷及其影响27 3.4.1 未熔合与未完全熔合27 3.4.2 缩孔、裂纹与结合线伸入28 3.4.3 表面烧伤、烧穿和喷溅29 3.4.4 过烧和晶间腐蚀29 3.5 本章小结30 第四章铝合金电阻焊的加工参数优化设计31 4.1 引言31 4.2 点焊工艺参数优化的理论基础31 4.2.1 正交实验法的基本思路31 4.2.2 正交试验的理论基础31 4.3 铝合金电阻点焊的正交实验设计34 4.4 实验数据分析35 4.5 实验结论36 4.6 本章小结36 致谢38 参考文献39 第一章 绪论 1.1 前言 随着我国工业的迅猛发展,对工业产品(特别是汽车)外壳用材的性能提出了更高的要求,并促进了产品钢材的更新换代。例如:为了减轻车身总体质量,节省能源消耗,世界各大汽车公司正在开发铝合金或高强钢车身的汽车.铝合金的应用和铝合金焊接技术的发展是相辅相成的,汽车上的铝合金结构件多数要求焊接.并要求焊缝有良好机械性能。在汽车制造业长期以来广泛应用的电阻点焊工艺方法,具有机械化、自动化程度高、生产率高、焊接质量可靠的特点。将单个零件拼接成车身结构的工作属于汽车制造商的核心技术。为保证焊接质量,研究铝合金等新材料的电阻点焊性能已成了非常迫切的任务。近年来,各国焊接工作者就此做了大量的理论及实际研究工作,并取得了一定的成绩。铝及其合金是汽车轻量化的最重要材料,同时铝的消费指标及生产能力也是衡量一个国家和地区工业发展基础和技术进步程度的重要标志—[1]。 铝合金电阻焊连接技术在汽车车体组装过程中占有重要地位,是汽车车体生产的关键技术。近年来,汽车工业发达国家都有铝制车体的概念车或批量生产的车型问世,而我国在汽车车体轻量化应用研究方面基本属于空白。在国产化的铝合金汽车车体研究中,采用传统的电阻点焊技术,遇到许多困难:如设备投资巨大、电力消耗严重、焊接质量不稳定及需要进行大量铝合金电阻点焊工艺研究开发等(目前,国内在铝合金电阻点焊方面仍存在许多有待解决的问题)。因此,为了推广铝合金在汽车、家电等行业中的应用,必须对铝合金的点焊性能作进一步深入细致的研究。 在各种焊接方法中,点焊具有静强度高、可靠性好、性能稳定、生产效率高和易于实现自动化等优点,因此目前在汽车车身结构上被广泛采用。
1.2 铝合金电阻点焊研究的必要性
能源短缺和环境污染已经成为目前制约全球经济,社会发展的两大问题。交通运输业是导致能源短缺和环境污染尤其是空气污染的一个主要因素,在美国该行业的石油消耗占到了石油消耗的三分之二,其中汽车燃油的比例为75%。在我国,汽车燃油的比例高达85%,据国际制造商协会统计,2011年全世界汽车生产总量为5754万辆,我国汽车产量也达到万辆,已居世界第8位,居估算,燃油汽车给城市造成了至少30%以上的空气污染,汽车排放所造成的污染已成为当今社会的一大公害,从80来年代世界各国尤其是发达国家就开始研究采取各种措施来减少汽车能源的消耗和排放污染。为此,美国制定了PNGV计划德国制定了3升汽车计划,汽车的轻量化是其中非常重要的一个途径,轻量化已经成为汽车发展的主要方向,对降低汽车能源消耗和减少环境污染是至关重要的。 铝合金材料是实现汽车轻量化得理想材料,铝合金的比重是碳钢的1/3,采用铝合金材料制造汽车车身,在保证具有与钢同样强度和刚度的前提下,车身重量可减少50%,整车重量可减少10%,同时可以减少相同数量的燃油消耗和环境污染。铝合金材料还被称为“绿色材料”,可反复回收利用,回收重熔铝合金所需能量仅是生产新铝合金所需能量的5%,而再生铝合金材料能够保持原有材料的性能,而不像一般碳钢具有良好的防腐性能,其表面只需稍加处理就可获得满意的防腐性能,而电镀,镀锌等处理不仅工艺复杂,成本高,而且环境污染严重。目前经济发达国家已开始进行铝合金汽车的研制,一些公司现已推出了铝合金汽车,如美国通用公司推出的“Precept”,福特公司推出的“合成-210”,德国宝马公司推出的“528”,德国大众推出的“奥迪A8”及推出的“奥迪A2”,现已都批量生产。 由于电阻点焊具有焊接质量可靠,生产效率高且易实现机械化和自动化等优点,在汽车工业领域获得了广泛应用,现在它已成为汽车制造领域中的主导加工工艺。但是,铝合金点焊所存在的问题限制了点焊在铝合金汽车生产中的应用。目前国外推出的铝合金汽车很少单独采用电阻点焊工艺,而大多采用气保焊,激光焊,胶焊等连接工艺。如新近推出的采用第二代铝合金空间架构(ASF)的“奥迪A2”就采用了MIG焊工艺和激光焊,但这些工艺并不适合汽车的规模化和连续化生产。为实现铝合金汽车的大规模化生产,就必须开展铝合金材料电阻点焊的研究。 在航空航天领域,为减轻飞行器的重量,大量的薄板结构采用了铝合金材料。电阻点焊是薄板结构最理想的连接工艺,铝合金点焊所存在的问题使得这些板筋结构目前的连接工艺还是铆接。与点焊相比,其具有刚性差,重量大等缺点。若解决了铝合金电阻点焊问题,大量采用点焊工艺,飞行器的重量将会进一步降低,动力学性能也会得到进一步的提高。