基于PLC的船用锅炉自动控制系统设计 -
基于PLC的锅炉电加热控制系统设计

基于PLC的锅炉电加热控制系统设计摘要本文针对锅炉电加热控制系统的实际需求,基于PLC,设计了一种可靠的电加热控制系统。
该系统通过PLC的控制,实现了对电加热器的开启、关闭、电流的调节等功能。
同时,系统还通过人机界面进行了参数设置和异常报警等功能。
实验结果表明,该系统具有高可靠性、稳定性,能够满足锅炉电加热的实际需求。
关键词:PLC、锅炉、电加热、控制系统一、引言锅炉是工业生产中常用的一种设备,其主要作用是将水加热为蒸汽,并通过蒸汽驱动液体或气体来完成工业生产流程。
而锅炉的加热方式一般有煤、油、气、电等多种方式,其中电加热由于其无污染、易控制等优点,被广泛应用于各种工业生产环节中。
然而,锅炉电加热控制系统的设计存在一些问题,如控制精度低、容易出现故障等。
这些问题给锅炉电加热操作带来了很大的不便,因此,需要设计一种基于PLC的锅炉电加热控制系统,以提高其可靠性和稳定性。
二、设计思路和方法1.设计思路基于以上问题,本文设计了一种基于PLC的锅炉电加热控制系统。
该系统采用西门子S7-200 PLC作为主控制器,通过PLC与电加热装置进行连接,实现对电加热装置的开关控制和电流调节。
同时,本文还设计了人机界面,以便进行参数设置和异常报警等功能。
通过该系统,可以实现对电加热的精确控制,从而提高锅炉的加热效率和生产稳定性。
2.设计方法(1)硬件部分设计系统硬件包含主要的PLC、电加热器、人机界面等几个部分。
PLC:采用西门子S7-200 PLC作为主控制器,通过该控制器,实现对电加热设备的精确控制。
电加热器:采用模块化的电加热器,可以根据实际需求进行扩展和修改。
人机界面:设计了触摸屏人机界面,以便进行电加热控制和参数设置等功能。
(2)软件部分设计软件部分主要包含PLC程序和人机界面程序两部分。
PLC程序:由于锅炉电加热主要是控制电加热的开关和电流调节,因此,PLC程序中主要包含电加热开关控制、电流调节等基本功能。
基于PLC锅炉控制系统设计开题报告

基于PLC锅炉控制系统设计开题报告题目基于PLC锅炉控制系统设计信息科学与工程学院,系,电气工程及其自动化专业班学生姓名学号指导教师开题日期: 年月日开题报告一、论文题目。
基于PLC锅炉控制系统设计二、课题研究的来源和实际意义。
随着工业的快速发展,自动化技术也随之占据着及其重要的地位。
无论是职工过万的大型企业还是百人的小型企业自动化无处不在。
而对于企业内的锅炉系统的自动控制是其中一项重要的课题。
因为这一控制不仅直接涉及到锅炉运行的效能,而且更关系到锅炉运行的安全性和可靠行。
锅炉按其用途分为:电站锅炉、工业锅炉、生活锅炉、机车船舶锅炉。
而按燃料分为:燃煤锅炉、燃油锅炉、燃气锅炉、原子能锅炉。
以继电—接触器为主的传统控制系统已不能满足现代船舶对其锅炉控制的越来越高、越来越复杂的要求,这一领域的计算机化已势在必行,而应用在当前工业过程控制领域中引人注目的可编程控制器(PLC)又是使其计算机化的最简便和可靠途径。
本文采用PLC控制器进行了对锅炉的控制设计。
锅炉微计算机控制,是近年来开发的一项新技术,它是微型计算机软、硬件、自动控制、锅炉节能等几项技术紧密结合的产物,我国现有中、小型锅炉30多万台,每年耗煤量占我国原煤产量的1/3,目前大多数工业锅炉仍处于能耗高、浪费大、环境污染等严重的生产状态。
提高热效率,降低耗煤量,用微机进行控制是一件具有深远意义的工作。
三、题目主要内容及预期达到的目标。
本设计针对机车船舶锅炉,锅炉所产生的蒸汽主要供主副机暖机,燃油加热,日常生活用汽,故对蒸汽品质要求不高,采用多位控制实现对锅炉蒸汽压力的控制。
设计内容包括:(1)应用可编程序控制器作为锅炉控制器,对锅炉给水,点火程序,风油调节和蒸汽压力进行自动控制。
(2) 根据船舶辅助锅炉的主要控制量蒸汽压力和锅炉汽包水位进行简单数学建摸,用计算机建立简单的锅炉模型。
(3)建立基于VB的锅炉模型与PLC控制器组成的控制系统,并验证锅炉控制器的可行性和有效性。
基于PLC系统的锅炉内胆水温控制系统设计
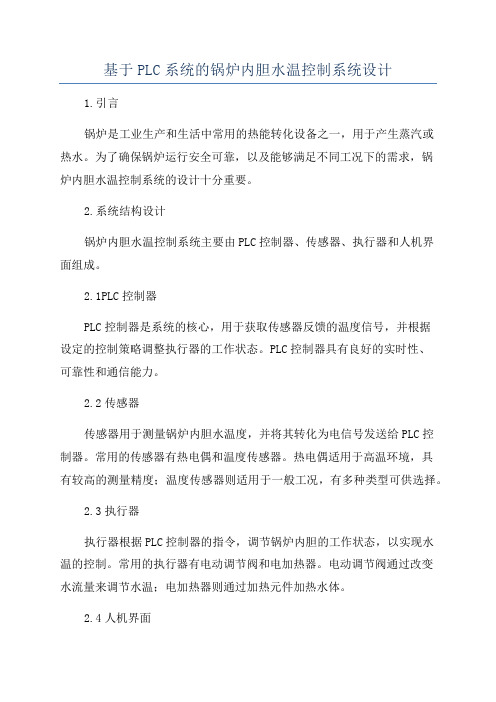
基于PLC系统的锅炉内胆水温控制系统设计1.引言锅炉是工业生产和生活中常用的热能转化设备之一,用于产生蒸汽或热水。
为了确保锅炉运行安全可靠,以及能够满足不同工况下的需求,锅炉内胆水温控制系统的设计十分重要。
2.系统结构设计锅炉内胆水温控制系统主要由PLC控制器、传感器、执行器和人机界面组成。
2.1PLC控制器PLC控制器是系统的核心,用于获取传感器反馈的温度信号,并根据设定的控制策略调整执行器的工作状态。
PLC控制器具有良好的实时性、可靠性和通信能力。
2.2传感器传感器用于测量锅炉内胆水温度,并将其转化为电信号发送给PLC控制器。
常用的传感器有热电偶和温度传感器。
热电偶适用于高温环境,具有较高的测量精度;温度传感器则适用于一般工况,有多种类型可供选择。
2.3执行器执行器根据PLC控制器的指令,调节锅炉内胆的工作状态,以实现水温的控制。
常用的执行器有电动调节阀和电加热器。
电动调节阀通过改变水流量来调节水温;电加热器则通过加热元件加热水体。
2.4人机界面人机界面用于人机交互操作,显示当前的水温、设定温度和控制状态,以及提供参数调整和报警信息等功能。
一般使用触摸屏作为人机界面,操作简单直观。
3.系统控制策略设计锅炉内胆水温控制系统的控制策略可以根据实际需求进行优化设计。
常用的控制策略有比例控制、比例积分控制和模糊控制等。
3.1比例控制比例控制根据当前的温度误差大小,调节执行器的开度。
开度与误差成正比,以获得较好的稳态和动态响应。
3.2比例积分控制比例积分控制在比例控制基础上加入积分项,用于补偿比例控制的静差。
通过积分项的积累,使负反馈控制系统具有零静差特性。
3.3模糊控制模糊控制可以根据实际的工作状态,自适应地调整控制策略。
通过建立模糊规则库,根据当前温度误差和变化率等信息,确定输出控制量。
4.系统硬件设计根据设计需求,选择合适的硬件设备进行系统实现。
主要包括PLC控制器、传感器、执行器和人机界面等。
基于PLC的锅炉温度控制系统设计方案

基于PLC的锅炉温度控制系统设计方案目录摘要 (1)第一章绪论 (3)1.1课题背景及研究目的和意义 (3)1.2国内外研究现状 (3)1.3项目研究内容 (4)第二章 PLC和组态软件基础 (5)2.1可编程控制器基础 (5)2.1.1可编程控制器的产生和应用 (5)2.1.2可编程控制器的组成和工作原理 ············错误!未定义书签。
2.1.3可编程控制器的分类及特点 (7)2.2组态软件的基础 (8)2.2.1组态的定义 (8)2.2.2组态王软件的特点 (8)2.2.3组态王软件仿真的基本方法 (8)第三章 PLC控制系统的硬件设计 (9)3.1 PLC控制系统设计的基本原则和步骤 (9)3.1.1 PLC控制系统设计的基本原则 (9)3.1.2 PLC控制系统设计的一般步骤 (9)3.1.3 PLC程序设计的一般步骤 (10)3.2 PLC的选型和硬件配置 (11)3.2.1 PLC型号的选择 (11)3.2.2 S7-200CPU的选择 (12)3.2.3 EM235模拟量输入/输出模块 (12)3.2.5 可控硅加热装置简介 (12)3.3 系统整体设计方案和电气连接图 (13)3.4 PLC控制器的设计 (14)3.4.1 控制系统数学模型的建立 (14)3.4.2 PID控制及参数整定 (14)第四章 PLC控制系统的软件设计 (16)4.1 PLC程序设计的方法 (16)4.2 编程软件STEP7--Micro/WIN 概述 (17)4.2.1 STEP7--Micro/WIN 简单介绍 (17)4.2.2 计算机与PLC的通信 (18)4.3 程序设计 (18)4.3.1程序设计思路 (18)4.3.2 PID指令向导 (19)4.3.3 控制程序及分析 (25)第五章组态画面的设计 (29)5.1组态变量的建立及设备连接 (29)5.1.1新建项目 (29)5.2创建组态画面 (33)5.2.1新建主画面 (33)5.2.2新建PID参数设定窗口 (34)5.2.3新建数据报表 (34)5.2.4新建实时曲线 (35)5.2.5新建历史曲线 (35)5.2.6新建报警窗口 (36)第六章系统测试 (37)6.1启动组态王 (37)6.2实时曲线观察 (38)6.3分析历史趋势曲线 (38)6.4查看数据报表 (40)结束语 (43)参考文献 (44)摘要从上世纪80年代至90年代中期,PLC得到了快速的发展,在这时期,PLC在处理模拟量能力、数字运算能力、人机接口能力和网络能力得到大幅度提高,PLC 逐渐进入过程控制领域,在某些应用上取代了在过程控制领域处于统治地位的DCS系统。
基于PLC锅炉温度控制系统的设计报告.doc
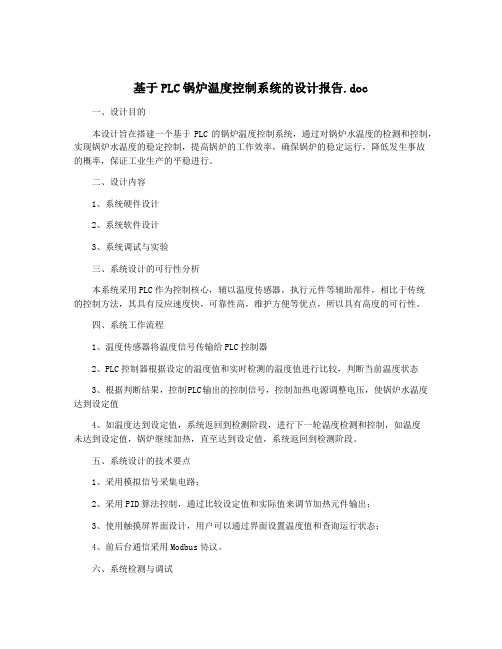
基于PLC锅炉温度控制系统的设计报告.doc一、设计目的本设计旨在搭建一个基于PLC的锅炉温度控制系统,通过对锅炉水温度的检测和控制,实现锅炉水温度的稳定控制,提高锅炉的工作效率,确保锅炉的稳定运行,降低发生事故的概率,保证工业生产的平稳进行。
二、设计内容1、系统硬件设计2、系统软件设计3、系统调试与实验三、系统设计的可行性分析本系统采用PLC作为控制核心,辅以温度传感器,执行元件等辅助部件,相比于传统的控制方法,其具有反应速度快,可靠性高,维护方便等优点,所以具有高度的可行性。
四、系统工作流程1、温度传感器将温度信号传输给PLC控制器2、PLC控制器根据设定的温度值和实时检测的温度值进行比较,判断当前温度状态3、根据判断结果,控制PLC输出的控制信号,控制加热电源调整电压,使锅炉水温度达到设定值4、如温度达到设定值,系统返回到检测阶段,进行下一轮温度检测和控制,如温度未达到设定值,锅炉继续加热,直至达到设定值,系统返回到检测阶段。
五、系统设计的技术要点1、采用模拟信号采集电路;2、采用PID算法控制,通过比较设定值和实际值来调节加热元件输出;3、使用触摸屏界面设计,用户可以通过界面设置温度值和查询运行状态;4、前后台通信采用Modbus协议。
六、系统检测与调试本系统设计完成后,需要进行硬件和软件的实现,并进行整体的调试测试,工程师需严格按照设计流程,全面检查各个部件的连接情况和参数设置,确保系统能够正常稳定地运行,运行过程中出现问题要及时解决。
七、总结与展望本设计成功地搭建了基于PLC的锅炉温度控制系统,系统具有实时性强,稳定性高,调节精度高等优点,提高了设备工作效率,大大降低了工业生产过程中锅炉事故的发生可能性。
在未来的研究中,可以通过结合智能算法等技术,进一步优化系统设计,提升锅炉温度控制系统的性能和应用范畴。
基于plc的锅炉控制系统的设计方案
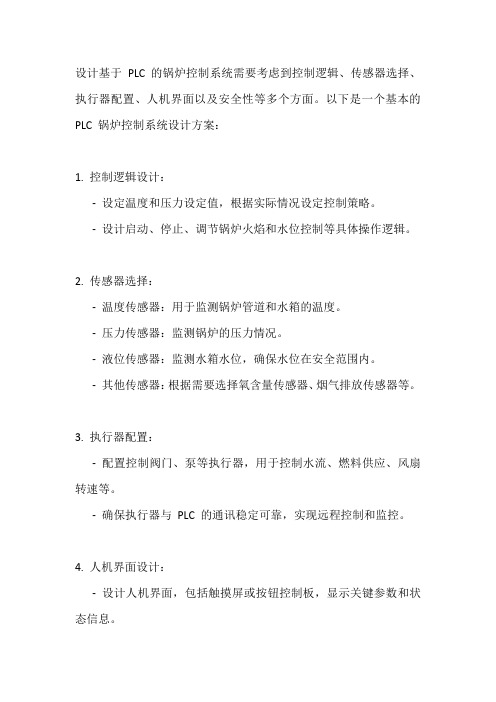
设计基于PLC 的锅炉控制系统需要考虑到控制逻辑、传感器选择、执行器配置、人机界面以及安全性等多个方面。
以下是一个基本的PLC 锅炉控制系统设计方案:1. 控制逻辑设计:-设定温度和压力设定值,根据实际情况设定控制策略。
-设计启动、停止、调节锅炉火焰和水位控制等具体操作逻辑。
2. 传感器选择:-温度传感器:用于监测锅炉管道和水箱的温度。
-压力传感器:监测锅炉的压力情况。
-液位传感器:监测水箱水位,确保水位在安全范围内。
-其他传感器:根据需要选择氧含量传感器、烟气排放传感器等。
3. 执行器配置:-配置控制阀门、泵等执行器,用于控制水流、燃料供应、风扇转速等。
-确保执行器与PLC 的通讯稳定可靠,实现远程控制和监控。
4. 人机界面设计:-设计人机界面,包括触摸屏或按钮控制板,显示关键参数和状态信息。
-提供操作界面,方便操作员设定参数、监控运行状态和进行故障诊断。
5. 安全性设计:-设计安全保护系统,包括过压保护、过温保护、水位保护等,确保锅炉运行安全。
-设置报警系统,当参数超出设定范围时及时警示操作员。
6. 通讯接口:-考虑与其他系统的通讯接口,如SCADA 系统、远程监控系统等,实现数据传输和远程控制。
7. 程序设计:-使用PLC 编程软件编写程序,包括控制逻辑、报警逻辑、自诊断等功能。
-测试程序逻辑,确保系统稳定可靠,符合设计要求。
以上是基于PLC 的锅炉控制系统设计方案的基本步骤,具体设计还需根据实际情况和需求进行调整和优化。
在设计过程中,还需遵循相关标准和规范,确保系统安全可靠、运行稳定。
基于PLC的锅炉供热控制系统的设计

基于PLC的锅炉供热控制系统的设计一、本文概述随着科技的不断发展,可编程逻辑控制器(PLC)在工业自动化领域的应用日益广泛。
作为一种高效、可靠的工业控制设备,PLC以其强大的编程能力和灵活的扩展性,成为现代工业控制系统的重要组成部分。
本文旨在探讨基于PLC的锅炉供热控制系统的设计,通过对锅炉供热系统的分析,结合PLC控制技术,实现对供热系统的智能化、自动化控制,提高供热效率,降低能耗,为工业生产和居民生活提供稳定、可靠的热源。
文章首先介绍了锅炉供热系统的基本构成和工作原理,分析了传统供热系统存在的问题和不足。
然后,详细阐述了PLC控制系统的基本原理和核心功能,包括输入/输出模块、中央处理单元、编程软件等。
在此基础上,文章提出了基于PLC的锅炉供热控制系统的总体设计方案,包括系统硬件选型、软件编程、系统调试等方面。
通过本文的研究,期望能够实现对锅炉供热控制系统的优化设计,提高供热系统的控制精度和稳定性,降低运行成本,促进节能减排,为工业生产和居民生活提供更加安全、高效的供热服务。
也为相关领域的研究人员和技术人员提供有价值的参考和借鉴。
二、锅炉供热系统基础知识锅炉供热系统是一种广泛应用的热能供应系统,其主要任务是将水或其他介质加热到一定的温度,然后通过管道系统输送到各个用户端,满足各种热需求,如工业生产、居民供暖等。
该系统主要由锅炉本体、燃烧器、热交换器、控制系统和辅助设备等几部分构成。
锅炉本体是供热系统的核心设备,负责将水或其他介质加热到预定温度。
其根据燃料类型可分为燃煤锅炉、燃油锅炉、燃气锅炉、电锅炉等。
锅炉的性能参数主要包括蒸发量、蒸汽压力、蒸汽温度等。
燃烧器是锅炉的重要组成部分,负责燃料的燃烧过程。
燃烧器的性能直接影响到锅炉的热效率和污染物排放。
燃烧器需要稳定、高效、低污染,同时要适应不同的燃料类型和负荷变化。
热交换器是锅炉供热系统中的关键设备,负责将锅炉产生的热能传递给水或其他介质。
热交换器的设计应保证高效、稳定、安全,同时要考虑到热能的充分利用和防止结垢、腐蚀等问题。
基于plc的锅炉供热控制系统的设计
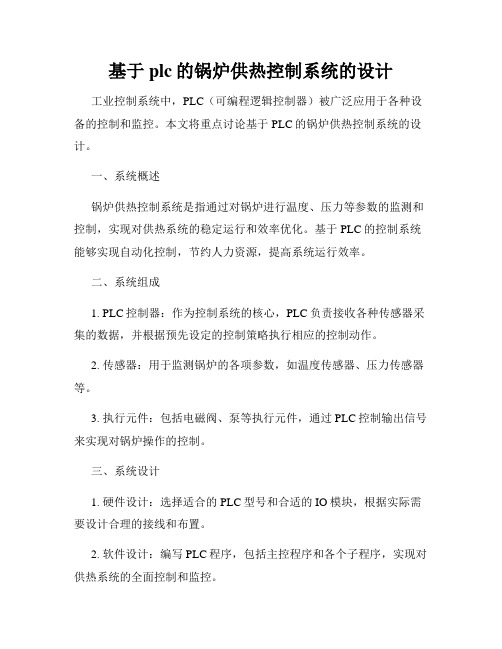
基于plc的锅炉供热控制系统的设计工业控制系统中,PLC(可编程逻辑控制器)被广泛应用于各种设备的控制和监控。
本文将重点讨论基于PLC的锅炉供热控制系统的设计。
一、系统概述锅炉供热控制系统是指通过对锅炉进行温度、压力等参数的监测和控制,实现对供热系统的稳定运行和效率优化。
基于PLC的控制系统能够实现自动化控制,节约人力资源,提高系统运行效率。
二、系统组成1. PLC控制器:作为控制系统的核心,PLC负责接收各种传感器采集的数据,并根据预先设定的控制策略执行相应的控制动作。
2. 传感器:用于监测锅炉的各项参数,如温度传感器、压力传感器等。
3. 执行元件:包括电磁阀、泵等执行元件,通过PLC控制输出信号来实现对锅炉操作的控制。
三、系统设计1. 硬件设计:选择适合的PLC型号和合适的IO模块,根据实际需要设计合理的接线和布置。
2. 软件设计:编写PLC程序,包括主控程序和各个子程序,实现对供热系统的全面控制和监控。
四、系统功能1. 温度控制:根据设定的温度范围,实现对锅炉加热的自动控制,确保供热系统温度稳定。
2. 压力保护:设定压力上下限,一旦超过范围即刻停止加热,确保系统安全运行。
3. 水位控制:通过水位传感器监测水位,保持恰当的水位以确保供热效果。
4. 故障诊断:PLC系统能够实时监测各个元件的运行状态,一旦有异常即可及时报警并进行故障诊断。
五、系统优势1. 自动化程度高:基于PLC的供热控制系统可以实现全自动化控制,减少人为干预,节约人力成本。
2. 稳定可靠:系统通过对各项参数的实时监测和控制,确保供热系统的稳定性和可靠性。
3. 灵活性强:PLC程序可以根据实际需要进行定制化设计,满足不同应用场景的需求。
六、总结基于PLC的锅炉供热控制系统的设计,能够实现对供热系统的智能化控制和监测,提高系统的稳定性和效率,减少运行成本,是目前工业控制领域的主流趋势。
希望本文的介绍能够对您有所帮助。
感谢阅读!。
- 1、下载文档前请自行甄别文档内容的完整性,平台不提供额外的编辑、内容补充、找答案等附加服务。
- 2、"仅部分预览"的文档,不可在线预览部分如存在完整性等问题,可反馈申请退款(可完整预览的文档不适用该条件!)。
- 3、如文档侵犯您的权益,请联系客服反馈,我们会尽快为您处理(人工客服工作时间:9:00-18:30)。
0 船舶PLC 锅炉培训仿真系统的功能
0.1 某柴油机货轮锅炉的主要特点
某柴油机货轮所配备的锅炉所产生的蒸汽主要用来加热主、辅柴油机所用燃油、厨房用汽,锅炉水位和汽压采用双位控制,燃烧采用单油头、定油量和定风量燃烧。
系统设有中途熄火、危险低水位和低风压等安全保护装置,详细的控制原理和过程见教材[5]。
为了更好对程序进行解读,结合船舶控制的安全保护需求,我们采用西门子公司的S7224CN 对控制系统进行了设计,并制作了该装置。
0.2 锅炉自动控制装置总体功能设计
系统包括点火自动/手动模式、水位自动/手动模式、风机、油泵自动/手动模式(简称风油自动/手动),水位和压力采用双位控制,另外系统设置有多个故障点(风压、水位、火焰)对锅炉的工作进行全程监控,具体如图1所示。
自动点火程序根据锅炉的点火特点,首先进行预扫风60秒,然后关小风门,打开点火变压器进行点火,10秒内点火成功,系统没有警报产生,则点火成功。
具体实现程序如图2所示,系统的I/O 点设计如表1所示,系统使用了14个输入点8个输出点,装置的实物如图3所示。
图1 PLC 锅炉总体功能设计框架图
表1 系统I/O 点的设计
I0.0 手动点火油头 I1.3 燃烧自动 I0.1 风压开关 I1.4 燃烧手动 I0.2 火焰开关 I1.5 风油手动 I0.3 蒸汽开关 Q0.0 水泵 I0.4 低水位 Q0.1 风机 I0.5 高水位 Q0.2 油泵 I0.6
水位自动 Q0.3 点火线圈 I0.7
危险水位 Q0.4 风门挡板 I1.0 风油自动 Q0.6 油头电磁阀 I1.1 手动点火 Q0.7 熄火保护 I1.2
复位开关
Q1.1
报警
手动点火水位控制压力控制故障设置 故障报警 故障处理 自动点火
执行自动点火程序
蒸汽压力双位控制(低汽压锅炉自动起动,高汽压锅炉自动停止)
水位双位控制 (低水位水泵自动起动,高水位水泵自动停止炉)
锅炉仿真系统
图2 自动点火流程图 图3 船舶PLC 锅炉装置实物图
1 PLC 锅炉的测试和使用方法
该船用锅炉模拟装置的控制功能包括:锅炉自动手动点火、水位控制、蒸汽压力控制,火焰检测,风油自动手动控制,熄火保护、报警等,输入状态由开关按钮控制,通过PLC 控制输出,并由指示灯指示。
1.1 自动点火
将PLC 控制器位于RUN 位置,燃烧控制、风油控制均置于自动状态(燃烧自动I1.4、风油自动I1.5),系统自动使风机Q0.1、油泵Q0.2指示灯点亮,开始进入预扫风阶段,并在此阶段建立风压(风压开关I0.1),经过60s 大风门预扫风自动关小风门,进行预点火,点火线圈指示灯、风门挡板指示灯点亮。
按下火焰模拟开关(I0.2),说明点火成功,首先熄灭点火变压器(Q0.3),2s 后风门挡板(Q0.4)指示灯熄灭,70s 内不报警则说明点火成功。
点火控制程序如图4所示。
a 手动模式
b 自动模式
图4 点火控制程序
1.2 手动点火模式
将燃烧控制、风油控制均置于手动位置(燃烧手动I1.3、风油手动I1.0),首先进行预扫风,60s 内建立风压(风压开关I0.1),60s 后手动点火I1.1,打开手动点火油头I0.0,按下火焰模拟开关,70s 内不报警则点火成功。
故障修复 系统复位
预扫风60s
预点火10s 点火2s 点火成功正常燃烧
风压、 水位、 火焰 故障报警
系统起动 电源
PLC
1.3水位控制
将水位控制置于自动位,先后闭合高水位I0.4,低水位I0.5,则水泵指示灯亮,关闭低水位,指示灯不熄灭,直到到达高水位,水泵停止供水,达到危险水位I0.7,系统将熄火报警。
水位控制如图5所示。
图5 水位自动控制图 6 系统复位功能程序
1.4蒸汽压力双位控制
运行中,蒸汽压力达到上限设定值(按下模拟开关,对应输入点为I0.3),系统将熄火停炉,并进行后扫风,可以实现自动停炉功能。
该控制功能分布在程序的各个控制点,用于控制风机、油泵、点火变压器、风门挡板以及油头电磁阀。
当蒸汽压力下降到设定的下限值(弹起模拟开关,对应输入点为I0.3),系统重新进行点火,具体分析和锅炉的点火过程相同。
1.5系统复位功能
本系统设计了系统复位功能(对应的输入点为I1.2),当出现故障后,待所有故障检测完毕,按下复位按钮,方可重新起动锅炉。
系统复位功能程序如图6所示
1.6运行中的模拟故障报警
运行中风机出现故障,导致无风压,系统熄火并报警,应检查故障;运行中弹起火焰开关,则系统将熄火并报警;危险水位报警,当水位低于危险水位时,系统将熄火并报警。
在点火过程,以及锅炉运转过程中,当出现故障时,所有这些报警都会触发。