结构设计规范-射频模块结构设计流程
射频MEMS器件的研究与应用

射频MEMS器件的研究与应用射频MEMS(Micro-electro-mechanical-systems)器件是一种与射频信号处理有关的微小机电系统,它是由微纳加工技术制造而成的微小器件,目前已广泛应用于无线通信、卫星导航、雷达、太赫兹波等领域。
本文将从射频MEMS器件的制造工艺、结构设计与应用展开探讨。
一、射频MEMS器件的制造工艺射频MEMS器件是通过微电子加工技术制造而成的微小结构,其制造工艺和普通半导体芯片非常类似,主要包括以下几个步骤:1. 射频MEMS器件的设计:根据所需功能,设计器件的结构、形状和尺寸等参数。
2. 芯片的制备:选用高质量的硅衬底进行光刻、蒸镀、刻蚀等工艺加工,制备出射频MEMS器件的芯片。
3. 票面的制造:将芯片通过特殊的切割、翻转、引线等工艺,制备成具有功能的射频MEMS器件。
4. 成品检测与测试:使用专业的测试仪器对射频MEMS器件进行测试,测试其参数是否符合设计要求。
二、射频MEMS器件的结构设计射频MEMS器件的结构设计非常关键,它的结构不仅影响了其性能,还影响着其制造工艺和可靠性。
射频MEMS器件的结构设计需要考虑以下几个方面的因素:1. 结构的材料选择:对于射频MEMS器件来说,需要选择具有良好的射频性能、热稳定性和机械稳定性等特性的材料。
目前常用的材料有硅、氮化硅和铝等。
2. 结构的设计参数:射频MEMS器件的各项设计参数都直接影响了其性能,如膜的厚度、支撑梁的长度、宽度等等。
这些参数需要根据器件的功能和要求来进行优化设计。
3. 结构的可靠性设计:射频MEMS器件在使用过程中需要承受一定的力学和热力学应力,因此需要进行结构的可靠性设计。
例如:可以引入防抖动、降低振动等工艺处理。
三、射频MEMS器件的应用射频MEMS器件的应用范围非常广泛,既可以用于通讯行业,也可以用于雷达、太赫兹波等领域。
射频MEMS器件具有以下几个突出的应用优势:1. 小型化:射频MEMS器件的体积非常小,可以轻松实现芯片级集成,因此非常适合需求小型化的应用场景。
射频结环形器的设计流程与仿真

射频结环形器的设计流程与仿真环形器、射频环形器、微带环形器、小型环形器、射频结环形器、铁氧体环形器1 引言铁氧体是一种在微波频段具有旋磁性质的特殊磁材料,由于他具有一系列非互易特性,可以使用他构造出环形器等一系列微波非互易器件。
微波环形器已成为信息通讯、电子对抗、航天航空等领域不可缺少的关键性器件之一。
如今微波环形器的应用迅速向民用通讯、能源技术、工农医等领域扩展。
环形器具有单向传输特性,入射信号能顺利通过,反射信号由于被吸收电阻吸收而不能通过。
其工作原理就是利用中心结构在射频场和外加偏置磁场之间满足一定关系时产生的谐振效应,从而获得环行效果。
目前环形器大致上使用的是圆盘结,Y型结,双Y结,三角结的中心谐振导体。
本文研究的对象是用于基站中,中心导体为双Y结的带线铁氧体环形器。
根据设计,仿真结果在工作频带内满足隔离度大于26 dB,插损小于0.3 dB,回波损耗大于26 dB,电压驻波比小于1.14,中心导体外接半径尺寸约为5 mm,达到高性能与小型化兼顾,基本满足几乎所有GSM 基站对于环形器的要求。
同时本文通过把结环形器的场理论与路理论结合起来,推导出一些通用的设计公式,给出简明的设计流程,并结合计算机辅助设计给出仿真结果,对一般设计者起到一定指导意义。
2 设计过程图1为双Y带线结环形器结构示意图。
金属导体圆盘半径为R,小Y臂长度为R0,耦合角为φs宽为Ws,电长度为θs,大Y臂宽为W,耦合角为φ,铁氧体厚度为H,金属导体厚度为t。
环形器的核心是一个外加恒定磁场的铁氧体非互易结,中心导体一般可以是圆盘形、Y形、双Y形或三角形等各种形状。
通过网络理论分析可证明一个匹配的无耗对称三端结就是一个环形器,用散射矩阵表示为:如果此非互易结是无耗的,则通过圆盘结波动方程加以正负与同相本征激励推导出圆盘双Y结的同相与正负激励阻抗本征值:式中:其中Z0与Z±都是纯虚数。
若其归一化值在阻抗圆图上的分布以及其所对应的S本征值间的相角差互成120o,则此非互易结是环行的。
射频连接器的结构设计简述

射频连接器的结构设计简述1射频连接器简介射频连接器是一种同轴传输线,是一种通用性的互连元件,广泛应用于各类微波系统中。
作为基础元件,在微波系统中起电气和机械连接作用。
射频连接器一般分为三类。
(1)面板座:一端配接标准(或非标)界面连接器,一端配接微带、玻珠等,执行GJB976A-2009《同轴、带状线或微带传输线用射频同轴连接器通用规范》。
(2)转接器:两端配接标准(或非标)界面连接器,GJB680A-2009《射频连接器转接器通用规范》。
(3)接电缆连接器:一端配接标准(或非标)界面连接器,一端配接电缆,执行GJB681A-2002《射频连接器通用规范》。
射频连接器的内部结构分为三层,由外向内分别是外导体、绝缘介质和内导体。
外导体接地,绝缘介质起绝缘作用、支撑作用,内导体通电。
特性阻抗计算公式截止频率计算公式:a-内导体外径;b-外导体内径;-绝缘介质相对介电常数。
2射频连接器的界面结构标准界面的射频连接器,应符合GJB5246《射频连接器界面》。
其主要的插合形式包括:螺纹旋接(SMA、TNC);推入自锁(QMA);浮动盲插(BMA、SBMA);直插擒纵(SMP、SSMP);卡口连接(BNC)等。
(a)SMA型射频连接器(螺纹旋接式)(b)QMA型射频连接器(推入自锁式)(c)BMA型射频连接器(浮动盲插式)图1射频连接器的主要插合形式示意图以螺纹旋接形式为例:在插头和插座进行互连时,通过旋动螺套,带动插头外导体插入插座外导体中,直至两者的电气和机械基准面完全重合,在此过程中,实现内导体(插针和插孔)的插合接触。
可以明确的是,电气和机械基准面完全重合之前,内导体端面是不应该接触的,否则在外导体持续推进过程中,内导体会因此端面互顶,从而造成整个连接器内部结构的破坏。
但同时,内导体端面之间的缝隙使得此处存在一段高阻抗,造成反射增大。
因此,一些测试级转接器会控制插合完成后,内导体端面处的缝隙大小。
根据连接过程,界面设计时,插合部分的尺寸公差应满足界面手册的要求,内孔不能小于下限值,外圆不能大于上限值,以避免无法完成插合过程。
射频功放设计步骤(思路)

射频功放设计步骤(思路)本文将对射频功放电路的设计过程进行简要地介绍,以便初涉射频功放开发的同仁参考。
第一步,制定设计方案在进行射频功放设计时,我们首先要根据给定(或需要)的技术指标和功能指标制定设计方案。
制定设计方案的主要依据是指标要求中的增益、额定输出功率、线性度(ACPR/IMD)、载波数、功耗/效率等指标。
1.在GSM及LTE基站系统中,由于对线性度要求不是很高或者额定输出功率不是很大,且在单载波情况下工作,所以我们选择传统的射频功放设计方案——功率回退法(高功放HPA)。
构成HPA放大器一般有两种工作状态:A类及AB类工作状态。
A类放大器具有良好的线性放大性能,其三阶交调产物与输出功率的变化关系是:输出信号功率减小3dB(即减小一半功率),则三阶交调产物改善6dB。
一般来讲,A类放大器在1dB压缩点输出时,三阶交调系数约为-23.7dB (通常取-20dB)。
为了达到一定的线性,并考虑到工程问题,A类放大器需回退15dB,此时放大器的三阶交调抑制可以达到-45~-50dBc。
然而使用A类放大器的最大缺点是效率低及成本较高。
这是因为A类放大器在它的1dB压缩点输出功率时,其效率只有10%。
比如,完成一个30W平均输出功率的HPA,就需要至少有300W的耗电,并且工作电流随输出功率变化的值不大。
若考虑回退12dB,则需要有480W平均功率输出,需耗电4.8kW。
为了达到30W的输出功率需要用较多的功率管。
这样就加大了HPA的成本和体积,增大了研制成本和难度。
为了避免这个问题,建议在小功率放大器(平均功率输出≤5W)设计中使用A类放大器;在中大功率放大器(平均功率输出>5W)设计中使用AB类放大器。
AB类放大器的特点是效率高、成本低。
由于单管的输出功率高,仅需少量的功率管即可做到较高的输出功率,所以成本较低,且散热和结构设计可以简单化。
目前用在AB类的管子主要选LDMOS管,AB类放大器用最大包络功率PEP来描述其功率容量,类似A类的1dB压缩点。
射频功放设计指南

射频功率放大器的设计一般分为五个步骤,即制定设计方案、选择确定具体电路形式和关键器件、进行专项实验或单板实验、结构设计和PCB详细设计、可生产性和可测试性设计分析。
一.1
在设计射频功率放大器时,首先要根据给定的(或需要的)技术指标和功能指标做出设计方案。设计方案的主要依据是额定输出功率、线性度(ACPR/IMD)、载波数、功耗/效率等指标。
B=10log[1+10-A/10] (5)
方程式(5)可以表示为图1.6中的曲线。
图1.6级联放大器中驱动级互调系数对末级互调系数的影响曲线
通过相同的公式(5),可以获得不同A值的劣化值B,如表1.2所示。
表1.2和B的对应值
驱动级A优于最后一级的IMD3(dB)
末级交叉调制恶化值(dB)
0
三
五
1.2
一.5
在详细设计结构和PCB时,我们应该考虑可生产性和可测试性的设计。这时候生产线技术人员就可以提前介入,从产能和可测性方面指导我们的设计,让产能和可测性的问题在设计初期就得到解决,从而避免二板设计的大变动,尽可能避免三板设计的发生,节省人力、财力和时间,缩短研发周期,及时量产,抢占市场。
简而言之,射频功率放大器的设计步骤可以概括为:首先,根据给定(或要求)的技术和功能指标,制定设计方案;然后根据设计方案选择具体的电路形式和关键器件;具体电路形式和关键器件确定后,在仿真的基础上进行PCB设计(包括结构实验件的设计);在各单元板专项实验的基础上,进行各单元板的详细设计和结构件的详细设计(包括热设计和电磁屏蔽、产能和可测性设计);根据第一块板的调试情况和高低温的结果,进行第二块板的改进设计,解决第二块板的所有问题,尽量避免第三板设计的发生。
一.1.1
射频结环形器的设计流程与仿真
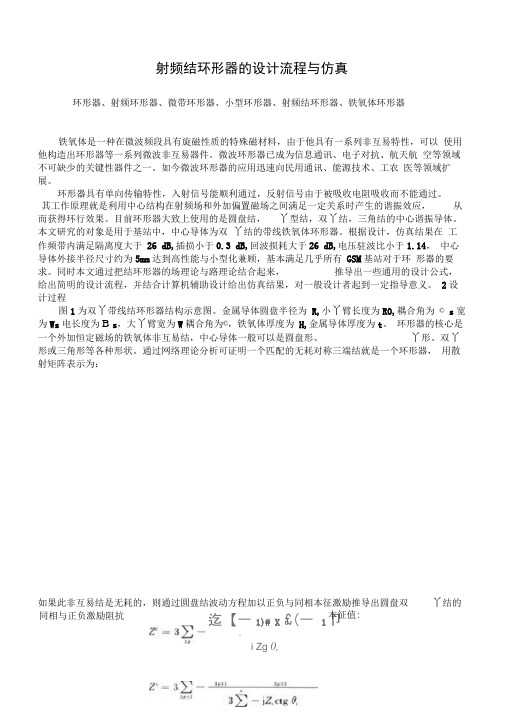
同相与正负激励阻抗迄【一1)# X £(一1卩本征值:lli Zg 0,射频结环形器的设计流程与仿真环形器、射频环形器、微带环形器、小型环形器、射频结环形器、铁氧体环形器铁氧体是一种在微波频段具有旋磁性质的特殊磁材料,由于他具有一系列非互易特性,可以使用他构造出环形器等一系列微波非互易器件。
微波环形器已成为信息通讯、电子对抗、航天航空等领域不可缺少的关键性器件之一。
如今微波环形器的应用迅速向民用通讯、能源技术、工农医等领域扩展。
环形器具有单向传输特性,入射信号能顺利通过,反射信号由于被吸收电阻吸收而不能通过。
其工作原理就是利用中心结构在射频场和外加偏置磁场之间满足一定关系时产生的谐振效应,从而获得环行效果。
目前环形器大致上使用的是圆盘结,丫型结,双丫结,三角结的中心谐振导体。
本文研究的对象是用于基站中,中心导体为双丫结的带线铁氧体环形器。
根据设计,仿真结果在工作频带内满足隔离度大于26 dB,插损小于0.3 dB,回波损耗大于26 dB,电压驻波比小于1.14,中心导体外接半径尺寸约为5mm达到高性能与小型化兼顾,基本满足几乎所有GSM基站对于环形器的要求。
同时本文通过把结环形器的场理论与路理论结合起来,推导出一些通用的设计公式,给出简明的设计流程,并结合计算机辅助设计给出仿真结果,对一般设计者起到一定指导意义。
2设计过程图1为双丫带线结环形器结构示意图。
金属导体圆盘半径为R,小丫臂长度为R0,耦合角为© s宽为Ws电长度为B s,大丫臂宽为W耦合角为©,铁氧体厚度为H,金属导体厚度为t。
环形器的核心是一个外加恒定磁场的铁氧体非互易结,中心导体一般可以是圆盘形、丫形、双丫形或三角形等各种形状。
通过网络理论分析可证明一个匹配的无耗对称三端结就是一个环形器,用散射矩阵表示为:如果此非互易结是无耗的,则通过圆盘结波动方程加以正负与同相本征激励推导出圆盘双丫结的”7/其中Z0与Z±都是纯虚数。
基站射频单元结构设计-定义说明解析
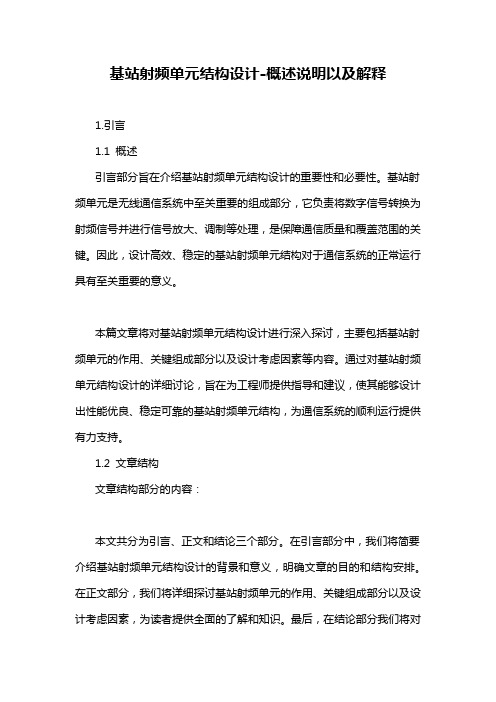
基站射频单元结构设计-概述说明以及解释1.引言1.1 概述引言部分旨在介绍基站射频单元结构设计的重要性和必要性。
基站射频单元是无线通信系统中至关重要的组成部分,它负责将数字信号转换为射频信号并进行信号放大、调制等处理,是保障通信质量和覆盖范围的关键。
因此,设计高效、稳定的基站射频单元结构对于通信系统的正常运行具有至关重要的意义。
本篇文章将对基站射频单元结构设计进行深入探讨,主要包括基站射频单元的作用、关键组成部分以及设计考虑因素等内容。
通过对基站射频单元结构设计的详细讨论,旨在为工程师提供指导和建议,使其能够设计出性能优良、稳定可靠的基站射频单元结构,为通信系统的顺利运行提供有力支持。
1.2 文章结构文章结构部分的内容:本文共分为引言、正文和结论三个部分。
在引言部分中,我们将简要介绍基站射频单元结构设计的背景和意义,明确文章的目的和结构安排。
在正文部分,我们将详细探讨基站射频单元的作用、关键组成部分以及设计考虑因素,为读者提供全面的了解和知识。
最后,在结论部分我们将对文章进行总结,并提出设计建议和展望未来的研究方向,以期推动基站射频单元结构设计领域的进一步发展。
1.3 目的本文旨在探讨基站射频单元结构设计的关键因素和考虑要点,以帮助读者更深入理解基站射频单元的重要性和复杂性。
通过深入分析基站射频单元的作用、关键组成部分和设计考虑因素,我们旨在提供一些设计建议和展望,以促进基站射频单元技术的发展和创新。
同时,通过本文的阐述,读者将能够更好地了解基站射频单元在通信系统中的作用,从而为相关领域的研究和实践提供一定的参考和指导。
2.正文2.1 基站射频单元的作用基站射频单元是无线通信系统中的重要组成部分,其主要作用包括以下几个方面:1. 信号处理:基站射频单元通过对收发信号的处理,将数字信号转换为射频信号或将射频信号转换为数字信号,实现信号的发送和接收功能。
2. 信号放大:基站射频单元能够对信号进行放大,以提高信号的传输功率和覆盖范围,确保通信质量和覆盖范围。
射频电路开发流程
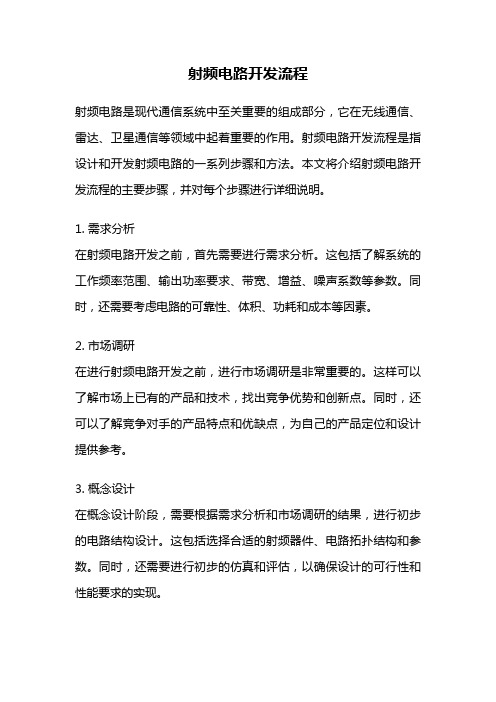
射频电路开发流程射频电路是现代通信系统中至关重要的组成部分,它在无线通信、雷达、卫星通信等领域中起着重要的作用。
射频电路开发流程是指设计和开发射频电路的一系列步骤和方法。
本文将介绍射频电路开发流程的主要步骤,并对每个步骤进行详细说明。
1. 需求分析在射频电路开发之前,首先需要进行需求分析。
这包括了解系统的工作频率范围、输出功率要求、带宽、增益、噪声系数等参数。
同时,还需要考虑电路的可靠性、体积、功耗和成本等因素。
2. 市场调研在进行射频电路开发之前,进行市场调研是非常重要的。
这样可以了解市场上已有的产品和技术,找出竞争优势和创新点。
同时,还可以了解竞争对手的产品特点和优缺点,为自己的产品定位和设计提供参考。
3. 概念设计在概念设计阶段,需要根据需求分析和市场调研的结果,进行初步的电路结构设计。
这包括选择合适的射频器件、电路拓扑结构和参数。
同时,还需要进行初步的仿真和评估,以确保设计的可行性和性能要求的实现。
4. 详细设计在详细设计阶段,需要进行更加具体和详细的电路设计。
这包括电路原理图设计、PCB布局和布线,以及射频器件的选型和参数调整。
同时,还需要进行电磁兼容性设计和射频信号完整性分析,以确保电路的稳定性和可靠性。
5. 原型制作在详细设计完成后,需要制作电路的原型进行验证。
这包括将设计好的电路板进行制作和组装,并进行初步的测试和调试。
通过测试和调试,可以评估电路的性能和功能是否符合设计要求,并进行必要的调整和优化。
6. 仿真和优化在原型制作完成后,可以进行更加精确和细致的仿真和优化。
通过使用射频仿真软件,可以模拟电路在不同工作条件下的性能和特性。
根据仿真结果,可以优化电路参数和结构,以提高电路的性能和稳定性。
7. 测试和验证在进行仿真和优化后,需要进行电路的测试和验证。
这包括使用测试仪器和设备对电路进行性能和功能的全面测试。
通过测试和验证,可以确保电路的性能和功能符合设计要求,并进行必要的修改和调整。
- 1、下载文档前请自行甄别文档内容的完整性,平台不提供额外的编辑、内容补充、找答案等附加服务。
- 2、"仅部分预览"的文档,不可在线预览部分如存在完整性等问题,可反馈申请退款(可完整预览的文档不适用该条件!)。
- 3、如文档侵犯您的权益,请联系客服反馈,我们会尽快为您处理(人工客服工作时间:9:00-18:30)。
武汉虹信通信技术有限责任公司 WRI_HX0 修改记录版本号 C/0武汉虹信通信技术有限责任公司管理文件文件编号 HX/QI/0363实施日期 2009.05.04 结构设计规范—射频模块结构设计流程页次: 1/11目 录0、修改记录1、 模块总体设计原则2、 模块机电交互设计原则3、模块结构设计原则之零件建模4、模块结构设计原则5、模块加工、包装编制 吴卫华 审核 甘洪文 批准 余勋林版本号 更改说明修订人日期审核 日期 批准 日期1 模块总体设计原则1.1模块总体设计原则之TOP-DOWN设计⏹总纲领:自顶向下的设计原则,是整机布局设计的后续任务;⏹现在做了哪些:列出设计原则,设计要点;⏹哪些还不完善:范例还不完善,技术还在发展;⏹后期怎么去做:完善范例,追踪技术发展方向。
1.1.1 在整机设计中考虑模块体量⏹长度和宽度由整机布局给出参考尺寸;⏹厚度由PCB堆叠的层数确定,堆叠的PCB间如果有电源,信号或射频的硬连接,此两PCB的板间距离由连接器的高度确定,合理选择较高器件的封装形式;⏹模块长度、宽度、以及安装孔的距离尺寸取到模数尺寸,优选为0或5结尾,次选为3和8结尾;⏹模块的安装厚度(既安装孔处的厚度)按照虹信公司紧固件规范选用。
1.1.2 在整机设计中考虑接口方式⏹电源的接口方式,有直接的插座引出,有和监控合并后的多PIN座转接或盲插;⏹监控的接口方式,有直接的DB9座引出,有和电源合并后的多PIN座转接或盲插;⏹射频的接口方式,方向上分有垂直向上和水平方向,按与外部电缆连接分有螺口和卡口,常用规格有SMA和SMB和N型,根据整机布局,整机的射频指标、频率和功率等合理选取;⏹其他接口方式,可以参考上述3点,合理选取。
1.1.3 在整机设计中考虑安装方式⏹模块的四个对角应有安装孔,大功率射频模块靠近放大管的部位需根据情况加一安装孔;⏹若模块安装在中蓝顶(或类似侧壁安装的情况),模块的安装孔平面不可相对模块顶部下沉;⏹规定M3,M4用在哪些地方(根据功率大小);⏹固定PCB用的M2、M2.5如何选用,材质确定(蓝白锌和不锈钢)。
1.1.4在整机设计中考虑模块的外部散热条件⏹由于整机的体积功率密度的限制,以及模块排列的日益紧凑化,应有整机散热方案;⏹射频模块由于布板和结构限制,从热源到热沉的传热通道存在哪些瓶颈;⏹分配到模块的结壳热阻会影响到模块的尺寸和PCB布局方式;⏹目前公司可行的方法是热测试和软件模拟,基本满足设计要求。
1.1.5 在整机设计中考虑模块运动检查⏹模块安装操作空间,插座接头操作安装空间;⏹模块的外部接口需要连接其他单板和模块;有一直线方向的运动距离;⏹射频电缆接头是否为直头或弯头或受指标限制必须为直头等因素决定接头的类型;⏹供电和监控是带导向的盲插还是软跳线决定插头型号和方向,在《模块结构设计输入文件表》中说明,见附件。
1.1.6输出格式:可以是2D 的工程图,含必要的投影视图;也可以是PROE的prt示例 1:单板的毛坯图示例2:模块整体的外形图1.2模块总体设计原则之标准化图例1.2.1 模块典型结构堆叠结构(依据堆叠设计原理,堆叠厚度确定,每层定高,凹凸利用);双面腔结构;⏹无盖板裸单板结构(局部屏蔽罩):屏蔽罩的系列化,标准化(结合典型电路);⏹单面腔+压条结构(考虑禁用);表1射频,数字,电源,监控的典型电路面积,板的层数,散热的要求,屏蔽的要求;(结构人员提供表格要求模块开发人员填写)对于无经验的模块,在预研时可以仿板,抄板,总结经验教训后给出典型电路,面积,屏蔽腔方案。
1.2.3 模块常用器件,接插件CAD封装图依据电子元器件优选库,建立结构关键器件(接口类,超高类,发热大类等等)封装库(画出第一脚,外形要准确),以及PROE的PRT(附电子档)。
1.2.4 设计间隙的留放原则射频接头离结构件间隙的考虑(EMC,结构加工精度);收集后出表格CHECKLIST规定;PCB外围轮廓相对盒体边缘的负公差值(防磕碰时PCB直接受力),PCB镀锡宽度相对压条宽度的正公差(良好电连接)。
1.3模块总体设计原则之堆叠设计:1.3.1 堆叠层数根据模块开发的并行化设计原理,根据射频,数字,选频,监控等不同部分,合理分层,有利于专业分工开发,提高开发质量和效率。
基本配置布在最底层板,选配的布在上层板,有利于结构件成本的最优化。
1.3.2 每层厚度每层厚度主要取决于PCB底部最高器件,PCB顶部最高器件,以及板间连接器高度3个因数。
部分封装高度较高的器件要给出低封装高度的备选方案(可能成本会上升),当它成为高度瓶颈时要综合取舍。
1.3.3 凹凸原则两层相邻的PCB,上层PCB背面和下层PCB顶面,较高的器件错位摆放。
可选择高度较低的板间连接器,同时减少模块厚度和结构件成本。
1.3.4 层间连接避免或减少装卸PCB需要动烙铁的情况。
模块装配调测工艺的考虑:较少紧固件,合理的EMC屏蔽,便于用简易工装夹具调测。
1.3.5 屏蔽腔选取射频、数字及电源之间相互隔离屏蔽良好。
1.3.6 模块长宽高精确尺寸确定(系列化的安装尺寸,标准化的安装高度)长度和宽度在整机布局中根据要求精确给出;高度根据层数,层间距离以及层间连接大致确定,然后根据虹信紧固件规范把模块高度或模块安装高度合理调整到符合规范数值。
1.3.7 层间散热的传导通道⏹堆叠各层间按从底层到顶层间热耗应遵循逐层递减规律确定;⏹一般底层PCB上的屏蔽不推荐采用导电胶形式,用压条面和PCB上的镀锡或镀金面直接接触,保证上层的热可以有一条低热阻通道导到下层;⏹PCB上的镀锡或镀金面要均布有金属化过孔,一是良好电连接,二是良好的散热通道可以把热从PCB正面导到背面的大面积接地覆铜层。
1.3.8 最小壁厚和最小间隙的检查摆放较高元件时,难免要掏槽避让,最薄壁厚不要低于1mm,最小间隙不要小于0.5mm。
1.3.9 模块散热的基本原则⏹查器件DATA Sheet,列出发热器件的封装,热阻和允许结温;(设计输入明确)⏹放在整机中散热仿真拿到放大管结温,PCB平均温度,和PCB上其他热敏感器件结温数据;⏹散热和隔热结合。
1.3.10 PCB背面器件高度确定PCB波峰焊,背面器件高度不许高于。
注:1.1和1.3条是一个交互的过程,如果堆叠设计后的模块体量超标,要返回到TOP-DOWN设计,修改整体方案或模块间的体量调整。
2 模块机电交互设计原则2.1 模块机电交互设计原则之毛坯图设计(关键)2.1.1 统一规定的PCB布板设计要点⏹外观、尺寸、孔径、限高、禁布区域、热过孔、过孔、热敏电阻探头位置、压条镀锡的宽度、内外R角、供电接口、监控接口、射频接口、PCB间射频连接、监控连接、供电连接等方式、背部器件高度的极限规定等;⏹TOP和BOTTOM规定:一个是相对PCB而言,一个是相对在模块中的可视方向而言,如果两者一致,可不做特别说明,如果相异,一定要加以说明。
2.1.2 毛坯图的规范格式毛坯图的参照基点;以及所有关键尺寸圆整到0.1。
2.1.3 ESD原理及ESD应对方案ESD原理是电子往低电压跑,即往地线上跑,不要让电子经过数据线走到地上,而是让电子直接走到地上即可。
ESD应对方案:1.封堵缝隙;2.本体接地(无功能pin);3.前段截电(有功能pin)。
前提是电子在布板的时候一定要多铺地,尤其是绕板边一圈和接插件的四周。
2.1.4 EMC下螺钉间距(考虑结构件刚性)的合理选取⏹屏蔽压条考虑用弹性导电体减少螺钉数量;⏹不同频率和屏蔽等级下的间距选取请参见虹信EMC设计规范;⏹螺钉间距不大于信号最高频率的1/4波长(主要指射频)。
2.2 模块机电交互设计原则之PCB输出⏹需要PCB的顶和底两层数据信息;⏹需要各类过孔的数据信息;⏹导出格式为DXF格式;⏹无法在PCB上看到的器件封装需特别说明;⏹关键器件的热特性。
3 模块结构设计原则之零件建模3.1 PCB建模步骤方法3.1.1层的简化提炼PCB顶和低层的毛坯图,简化图元,通过颜色区分,建PCB的标准PROE模型作为原始结构设计输入文件。
3.2装配模式设计⏹要求所有零件的特征基于PCB的导入DXF文档;⏹模块改版后导入新的DXF文档,对比修改相关特征图元的约束关系。
3.3 底板设计3.3.1底部需涂硅胶模块撬位的设计方法螺钉孔打在模块上,底部撬位在整机布局设计上考虑。
3.3.2底部沉头螺钉沉头孔的尺寸底部沉头螺钉沉头孔的尺寸见表2。
表2 单位:mm3.3.3.放大管处的加工要求,底板厚度⏹放大管处为减小接触热阻,一般要求粗糙度0.8,底板1.6,接合面1.6,未注3.2;⏹对应的底板厚度不宜太低(不低于4mm),以免过高的扩散热阻;⏹紧固的螺孔要取到可取的上限,保证最大的固定扭矩(按器件DATA SHEET推荐选用)。
3.4 中间结构层设计⏹下层PCB的屏蔽腔和上层PCB的安装面;⏹板间连接会在此结构层上形成很多通孔;⏹厚度由板间连接和高的器件确定。
3.5 上盖设计⏹上盖的屏蔽腔优选导电胶;⏹上盖的外表面为标识丝印层。
4 模块结构设计原则4.1 模块表面处理⏹导电氧化的颜色为本色;⏹喷砂和拉丝不推荐使用;⏹表面电阻的要求见HX/QI/03××表面处理规范。
4.2 丝印及激光蚀刻的适用范围详见HX/QI/03××标识规范。
4.3 一些关键面粗糙度要求⏹射频连接器和PCB安装面垂直度不大于0.5°;⏹模块底面的平行度和平面度要求不大于0.2;⏹放大管底部粗糙度不大于0.8;5 模块加工、包装5.1 模块加工5.1.1底板一般考虑材料缺陷、EMC、导热,侧重点考虑CNC加工的工艺性。
5.1.2 堆叠结构盖板考虑压铸生产趋势(增加脱模斜度,底部内圆角加大,肉厚均匀过度等)。
注:边缘一侧螺孔不要边宽逢中,要靠内侧一些,避免增加脱模斜度后肉太薄,决定本层厚度极限的高器件不要离侧壁太近。
5.1.3螺钉一般用M2和M2.5,用M2.5螺钉对模块材质的要求相应提高。
5.1.4 一些单向可以放宽的变形,比如模块底部的平面度,规定0.2,如果中部向上拱起不允许,向下可将尺度放宽。
5.2 模块包装5.2.1绝大多数的导电材料对硫敏感,纸中一般含硫,有导电胶的上盖内包装不可用纸包装。
5.2.2 PCB地面要求良好的接地性能,对应的盒体面贴膜防划伤、灰尘等等。
5.2.3丝印面贴膜防划伤。
其他要求详见物料包装规范。
6 附件。