生产部门tpm全面生产性维护
TPM全面生产维护活动步骤
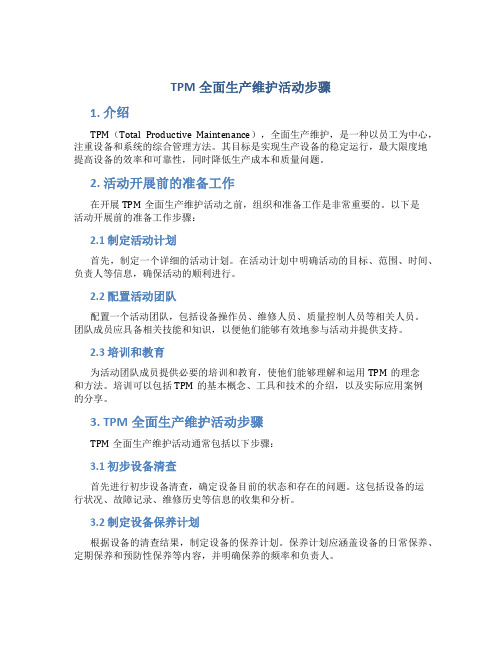
TPM全面生产维护活动步骤1. 介绍TPM(Total Productive Maintenance),全面生产维护,是一种以员工为中心,注重设备和系统的综合管理方法。
其目标是实现生产设备的稳定运行,最大限度地提高设备的效率和可靠性,同时降低生产成本和质量问题。
2. 活动开展前的准备工作在开展TPM全面生产维护活动之前,组织和准备工作是非常重要的。
以下是活动开展前的准备工作步骤:2.1 制定活动计划首先,制定一个详细的活动计划。
在活动计划中明确活动的目标、范围、时间、负责人等信息,确保活动的顺利进行。
2.2 配置活动团队配置一个活动团队,包括设备操作员、维修人员、质量控制人员等相关人员。
团队成员应具备相关技能和知识,以便他们能够有效地参与活动并提供支持。
2.3 培训和教育为活动团队成员提供必要的培训和教育,使他们能够理解和运用TPM的理念和方法。
培训可以包括TPM的基本概念、工具和技术的介绍,以及实际应用案例的分享。
3. TPM全面生产维护活动步骤TPM全面生产维护活动通常包括以下步骤:3.1 初步设备清查首先进行初步设备清查,确定设备目前的状态和存在的问题。
这包括设备的运行状况、故障记录、维修历史等信息的收集和分析。
3.2 制定设备保养计划根据设备的清查结果,制定设备的保养计划。
保养计划应涵盖设备的日常保养、定期保养和预防性保养等内容,并明确保养的频率和负责人。
3.3 建立保养标准和作业指导书针对设备的不同部位和组件,制定相应的保养标准和作业指导书。
保养标准应明确保养的具体内容、方法、工具和材料等,作业指导书应详细描述保养的步骤和注意事项。
3.4 实施设备保养根据设备保养计划和作业指导书,进行设备的保养工作。
保养工作可以包括设备的清洁、润滑、紧固、更换部件等内容。
保养过程中应严格按照标准和指导书进行操作,确保保养的质量和效果。
3.5 设备故障分析和改进在设备保养的过程中,如果发现设备存在故障或问题,应进行故障分析并寻找改进方案。
tpm全面生产维护

tpm全面生产维护TPM全面生产维护是一种重要的生产管理方法,它旨在通过最大程度地发挥设备和人力资源的潜能,提升生产效率和质量的同时降低成本。
本文将详细介绍TPM全面生产维护的原则、实施步骤以及它对企业生产的影响。
一、TPM全面生产维护的原则TPM全面生产维护的原则主要包括以下几个方面。
1. 以设备为中心:TPM强调设备是生产的核心,通过全面的管理和维护,保证设备的正常运行和寿命延长。
2. 全员参与:TPM要求所有员工从高层管理者到现场工人都要参与进来,形成全员合作的局面,共同努力实现生产效率和质量的提升。
3. 预防性维护:TPM强调预防胜于治疗,通过定期检查和保养设备,及时发现和解决问题,避免设备故障对生产造成的影响。
4. 持续改进:TPM鼓励员工不断学习和改进工作方式,积极参与问题解决和流程优化,提高生产效率和质量。
二、TPM全面生产维护的实施步骤1. 建立团队:首先要组建TPM团队,包括高层管理者、班组长和操作工等各个层级的员工。
团队成员要接受相关培训,了解TPM的原理和方法。
2. 制定计划:团队要制定全面生产维护的实施计划,包括设备评估、问题识别和改进措施等方面。
计划要有明确的目标和时间表。
3. 设备评估:通过对设备的评估,确定设备的状况和存在的问题。
可以采用故障分析、统计分析等方法,找出设备存在的问题和潜在的故障可能性。
4. 制定改进方案:根据设备评估的结果,制定改进方案和措施。
可以采用保养和修复计划、设备更新和升级等方式,解决设备存在的问题和提升生产效率。
5. 实施改进措施:按照制定的改进方案,组织员工进行改进工作。
包括定期的设备保养和检查、故障排除和设备更新等。
6. 监控和评估:实施改进措施后,要及时监控和评估效果。
可以通过数据统计和员工反馈等方式,了解改进措施的有效性和存在的问题,及时调整和优化。
7. 持续改进:TPM是一个持续改进的过程,需要团队成员的不断努力和参与。
要鼓励员工提出问题和改进建议,促进生产效率和质量的持续提升。
tpm全面生产维护

tpm全面生产维护TPM全面生产维护,即全面生产维护,是一种通过全员参与和团队合作来改善设备效率和生产过程的管理方法。
它的核心理念是以故障预防和事故预防为目标,在整个生产过程中实施持续改进和保养维护措施,以最大程度地提高设备的可靠性和生产效率。
TPM全面生产维护是源自日本的一种管理方法,它起源于20世纪60年代的日本制造业。
在当时,日本企业面临着严重的设备故障和生产事故问题,这严重影响了企业的生产效率和产品质量。
为了解决这些问题,日本企业开始思考如何通过全员参与和团队合作来改善设备效率和生产过程。
TPM全面生产维护的核心理念是通过设备保养维护和故障预防来提高设备的可靠性和生产效率。
它要求企业在生产过程中积极参与设备操作和保养,同时加强设备故障和事故的预防工作。
具体而言,TPM全面生产维护包括以下几个重要方面:1. 设备保养维护:企业要建立一套科学有效的设备保养维护体系,包括设备保养制度、保养计划和保养记录等。
通过定期检查、清洁、润滑和更换磨损部件等措施,保持设备的良好状态,提高设备的可靠性和寿命。
2. 故障预防:通过分析设备故障的根本原因,采取相应的措施,以预防故障的发生。
这包括加强设备操作和维护技能的培训,改进设备的设计和制造质量,加强设备的监控和预警等。
3. 全员参与:TPM全面生产维护要求企业的所有员工都积极参与到设备保养维护和故障预防工作中。
只有全员参与和团队合作,才能保证设备保养维护和故障预防的有效实施。
4. 持续改进:TPM全面生产维护是一个持续改进的过程,它要求企业不断地寻求改进和创新的机会。
通过不断地分析和评估设备的性能和生产过程,找出问题和改进的方向,推动企业的持续发展。
TPM全面生产维护的实施可以带来多方面的好处。
首先,它可以提高设备的可靠性和生产效率,减少设备故障和生产事故的发生。
其次,通过设备保养维护和故障预防,可以延长设备的使用寿命,降低设备的维修成本。
此外,TPM全面生产维护还可以促进员工的技能培训和团队合作,提高员工的满意度和工作积极性。
TPM全员生产维护管理

TPM中TOTAL的定义
全员参与 Total Members总体效率Total Effectiveness设备一生的维护 Total Maintenance System
重点说明教育 ONE POINT LESSON
QC 7大手法简介
手法
图形
用途
备注
特性要因图
分类清楚
1.管理.教育用2.改善.解析用3.源流管理用4.现场操作标准用
可以运用反转法,由找要因变换为找对策方法
柏拉图
重点把握 100%
1.决定改善目标2.明了改善的效果3.掌握重点分析
3
例 题
假设有一工厂某生产线每天工作时间为8小时,其中吃饭,休息时间为1小时; 每天作业中和下班之前的开会.点检5S需要30分钟;每天因突发故障而停机的时间为20分钟; 每天必须换模2次,每次15分钟;每天测模具1次,费时10分钟;生产单个产品额定周期为0.4分钟,但实际为0.5分钟;每天生产数量为600个产品,其中不良品为50个。 请计算设备总效率是多少.
目视管理基准书举例
【刻度板表示】适用于:管理值不变的场合 边缘能够拆下时 没有装甘油的地方
【边缘表示】适用于:管理值要变动的场合 边缘无法拆下时 装有甘油的地方
主题:小油杯的点检内容:安全.5S.自主保全.生产性.品质.技术说明:小油杯点检 1.查看有无杯盖:如果没有杯盖,则粉尘易掉入而引起动作不良 2.查看有无芯线:如果没有芯线,则油很容易一下子就流光
油量(油压罐.润滑油罐.齿轮油箱.三点一组
作业管理
TPM全面生产维护
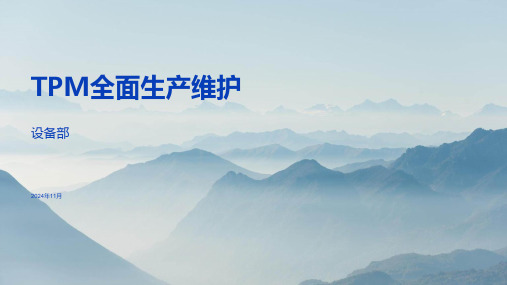
TPM的发展史
1 事后维修 (BM :Breakdown Maintenance)
故障后再维护 1950年以前
2 改良维修 (CM : Corrective Maintenance )
查找薄弱部位对其进行改良 1950年以后
3 预防维修 (PM :Preventive Maintenance)
对周期性故障提出的维护 1955年前后
6 全面生产维护 (TPM: Total Productive Maintenance)全员参加型的保养
1980年以后
5 生产维修 (PM: Productive Maintenance) 综合上述维护方法,系统的维护
方案 1960年前后
4 维修预防
(MP: Maintenance Prevention)
TPM的主要手段——OEE
• TPM使用的主要手段名为设备综合效率 (OEE: Overall Equipment Effectiveness )
• 这个数字与六大损失相关联:
• 1.故障/停机损失
(Equipment Failure / Breakdown Losses)
• 2.换装和调试损失 (Setup and Adjustment)
• 3.空闲和暂停损失 (Idling and Minor Stoppage Losses)
• 4.减速损失
(Reduced Speed Losses)
• 5.质量缺陷和返工 (Quality Defects and Rework)
ቤተ መጻሕፍቲ ባይዱ
• 6.启动损失
(Startup Losses)
• 三个可测量:时间开动率、性能开动率和合格品率。
• 质量缺陷和返工(Quality Defects and Rework)
TPM全生产性维护相关知识

TPM全生产性维护相关知识什么是TPM?•TPM,全称为Total Productive Maintenance,中文意为全生产性维护,是一种供应链管理技术,旨在提高设备可靠性和生产效率的一种方法。
•TPM源自于日本的制造业,最初由日产汽车公司引入,并在20世纪80年代由日本生产管理专家中村治郎提出。
•TPM的目标是通过消除故障、停机时间和生产过程中的浪费,实现设备的最大正常运行时间,从而达到高效的生产。
TPM的原则和目标原则TPM的原则基于以下几个核心概念:1.没有故障:设备保持良好的工作状态,并且不会发生任何故障。
2.零故障:通过预防性维护和故障预测来消除故障的可能性。
3.全面参与:全体员工都参与到设备的维护中,且设备操作人员也是维护专家。
4.持续改进:不断寻找和消除导致故障和浪费的根本原因,实现生产流程的不断改进。
目标TPM的目标主要包括以下几个方面:1.提高设备可靠性:通过预防性维护和故障预测,减少设备故障的发生和停机时间,提高设备的可靠性和稳定性。
2.提高设备使用效率:通过最大限度地减少设备故障和停机时间,实现设备的持续运行,提高生产效率。
3.减少浪费:通过分析生产过程中的各种浪费,如停机时间、材料损耗等,寻找并消除根本原因,从而提高整体生产效率。
4.培养员工技能:通过设备维护的培训和培养,提高员工的技能水平,使其成为设备维护和操作的专家。
TPM的基本步骤准备阶段1.召开启动大会:在这个会议上,公司领导向全体员工阐述TPM的原则、目标和重要性,并明确各个部门的责任。
2.设立TPM委员会:成立由各部门经理和代表组成的TPM委员会,负责制定和执行TPM计划。
3.建立TPM培训计划:制定培训计划,培养员工的技能和意识,以便他们能够有效地参与到设备的维护中。
4.记录设备现状:对所有设备进行评估和记录,包括设备的性能、运行状况和维护记录等。
故障消除阶段1.制定设备维护计划:根据设备的维护需求和生产计划,制定设备的维护计划,并明确各个维护任务的责任人和时间。
TPM生产维护概要及三要素

TPM生产维护概要及三要素概述TPM(全面生产维护)是一种旨在提高生产设备可靠性和效率的维护管理方法。
它强调员工参与和责任,旨在通过实施维护计划、维护培训和设备改进来消除生产过程中的故障和浪费。
TPM的目标是实现零故障、零事故、零损失的生产环境。
本文将重点介绍TPM生产维护的三要素:维护预防、维护改善和维护教育,并探讨如何有效地应用这些要素来提高生产设备的性能和效率。
维护预防维护预防是TPM的核心要素之一,它旨在通过定期检查、保养和维护生产设备来防止故障和损坏。
以下是一些维护预防的关键步骤:1.设备巡查:定期巡查生产设备,检查是否存在异常现象或潜在问题。
通过及时发现并解决问题,可以防止小问题演变为大问题。
2.保养计划:根据设备制造商提供的保养手册和经验,制定详细的保养计划。
保养计划应包括定期更换易损件、润滑设备、清洁设备等步骤,以确保设备的正常运行。
3.故障预测:通过监测设备性能指标、使用传感器和数据分析技术,可以预测设备可能出现的故障,并及时采取措施,以减少停机时间和生产损失。
4.操作规范:制定明确的操作规范,培训员工正确使用和操作设备。
规范化操作可以减少人为错误,延长设备寿命。
维护改善维护改善是TPM的第二个要素,它旨在通过持续改善生产设备和生产过程,提高效率和质量。
以下是一些维护改善的关键步骤:1.故障分析:对设备故障进行详细分析,找出故障的原因和根本问题。
通过分析故障模式,可以制定相应的改善措施,防止同样的故障再次发生。
2.设备改进:定期评估设备的性能和功能,并提出改进设备的建议。
改进可以包括增加自动化程度、提高设备稳定性、降低维护成本等。
3.持续改善:建立持续改进的文化,鼓励员工提出改善意见和建议,并提供相关培训和奖励机制。
持续改进是TPM成功的关键,它可以不断推动生产效率和质量的提高。
维护教育维护教育是TPM的第三个要素,它强调培训员工,使其具备维护设备的技能和知识。
以下是一些维护教育的关键步骤:1.技能培训:为员工提供必要的技能培训,使其能够进行设备操作、保养和故障排除。
TPM之全面质量管理
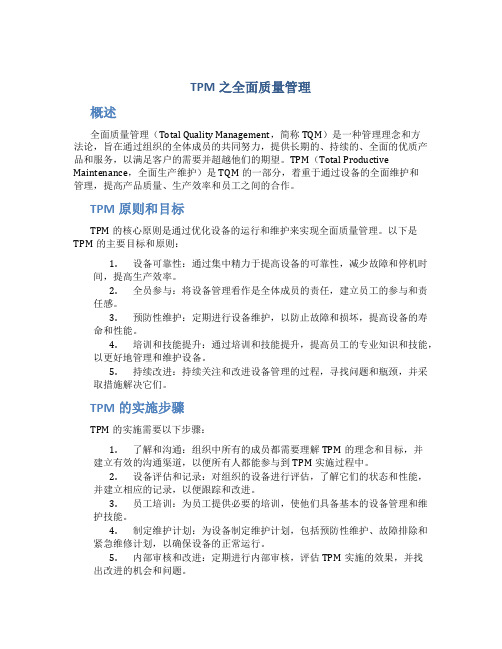
TPM之全面质量管理概述全面质量管理(Total Quality Management,简称TQM)是一种管理理念和方法论,旨在通过组织的全体成员的共同努力,提供长期的、持续的、全面的优质产品和服务,以满足客户的需要并超越他们的期望。
TPM(Total Productive Maintenance,全面生产维护)是TQM的一部分,着重于通过设备的全面维护和管理,提高产品质量、生产效率和员工之间的合作。
TPM原则和目标TPM的核心原则是通过优化设备的运行和维护来实现全面质量管理。
以下是TPM的主要目标和原则:1.设备可靠性:通过集中精力于提高设备的可靠性,减少故障和停机时间,提高生产效率。
2.全员参与:将设备管理看作是全体成员的责任,建立员工的参与和责任感。
3.预防性维护:定期进行设备维护,以防止故障和损坏,提高设备的寿命和性能。
4.培训和技能提升:通过培训和技能提升,提高员工的专业知识和技能,以更好地管理和维护设备。
5.持续改进:持续关注和改进设备管理的过程,寻找问题和瓶颈,并采取措施解决它们。
TPM的实施步骤TPM的实施需要以下步骤:1.了解和沟通:组织中所有的成员都需要理解TPM的理念和目标,并建立有效的沟通渠道,以便所有人都能参与到TPM实施过程中。
2.设备评估和记录:对组织的设备进行评估,了解它们的状态和性能,并建立相应的记录,以便跟踪和改进。
3.员工培训:为员工提供必要的培训,使他们具备基本的设备管理和维护技能。
4.制定维护计划:为设备制定维护计划,包括预防性维护、故障排除和紧急维修计划,以确保设备的正常运行。
5.内部审核和改进:定期进行内部审核,评估TPM实施的效果,并找出改进的机会和问题。
6.持续改进:通过持续改进,解决问题和挑战,进一步提高设备管理的效率和质量。
TPM的优势和挑战TPM的实施可以带来许多优势,包括:1.提高生产效率:TPM可以减少设备故障和停机时间,提高生产效率和产量。
- 1、下载文档前请自行甄别文档内容的完整性,平台不提供额外的编辑、内容补充、找答案等附加服务。
- 2、"仅部分预览"的文档,不可在线预览部分如存在完整性等问题,可反馈申请退款(可完整预览的文档不适用该条件!)。
- 3、如文档侵犯您的权益,请联系客服反馈,我们会尽快为您处理(人工客服工作时间:9:00-18:30)。
“我们所有人对我们的设备负责。”
5
Tip of the Iceberg 冰山的顶端
Failures 故障
Wear, play, slackness, leakage, dust, dirt, corrosion, deformation, adherence of raw
materials,surface damage, cracking, overheating, vibration, noise, and other
abnormalities. 磨损、松驰、泄露、灰尘、污垢、腐蚀 变形、原材料粘黏、表面磨损、裂缝、 过热、震动、噪音及其它不正常现象。
Hidden Defects 隐藏的问题
6
Typical Causes of Machine Breakdown 典型的机械故障原因
Contamination of sensors, contacts and Connectors
Process Certification
Quality Clinic Activity
Mistake Proofing
1
全面生产性维护 ACE 生产部门合格水平
6S
全面性生产 维护
质量诊断程序 图表
减少生产 准备
市场反馈 分析
标准化 作业
根本原因 修正行动
程序验证
质量诊断 行动
防误措施
2
TPM 全面生产性维护
• Enhanced safety 提高安全性
– Find exposed wires, open belts, missing guards, loose hardware
– 发现暴露在外的电线、松开的安全带、缺少防护、 松开的部件
• Reduced waste 减少浪费
– Prevents loss of lubricant, compressed air – 防止润滑油、压缩空气的浪费
Failure 组件失灵
Dirt and dust on cooling fan 冷却风扇上有 灰尘和污垢
7
TPM Techniques TPM技术
• Simplify and Document TPM Activities. • 简化并记录TPM行动
• Use visual techniques to indicate
TPM’s focus is to prevent problems before equipment breaks. TPM 的焦点是要在设备出
故障以前防止问题出现。
4
Total Productive Maintenance
is a New Way of Working 全面生产性维护是一种全新的工作方式
what’s right / what’s wrong. • 运用直观技术来演示什么是
对的/什么是错的。
– PM Completed? 生产性维护完成了吗? – Pressure gage 压力计 – Sight glass 视镜 – Arrows for motor rotation
and fluid circulation马达旋转和润油指示箭头 – markings for spare parts and fluids. – 备用零件和润滑油记号
Old Attitude:
过去的态度:
“I operate, you fix.” “我操作,你修理。”
“I fix, you design.” “我处理,你设计。”
“I design, you operate.” “我设计,你操作。”
TPM Attitude:
TPM态度:ຫໍສະໝຸດ “We are all responsible for our equipment.”
8
TPM Benefits TPM的益处
• Reduced maintenance costs
• 减少维护费用
– Breakdown maintenance is 10 times more costly than planned maintenance
– 故障维修费用是有计划进行维护费用的10倍以上
Total Productive Maintenance ACE Manufacturing Qualifying Level
TPM
6S
QCPC
Set-Up Reduction
Standard Work
Market Feedback Analysis
Root Cause / Corrective Action
Total Productive Maintenance is an equipment management strategy that improves equipment efficiency. 全面生产性维护是一种设备管理策略以提高设备效率。
Or, in other words... Treating the equipment like it is your own! 或者,换句话说……. 对待设备就象它是你自己的 一样!
3
TPM Key Concept TPM的重要概念
• Left neglected... Equipment Breaks Down • 如果不重视…设备很快就会坏
In the past, maintenance focused on fixing equipment after it broke. 过去,维护工作总是集中在设备坏了 以后对其进行修理。
Normal operating Range
正常操作范围
Danger!
危险!
Making PM devices more accessible. • 使生产性维护设备更容易获得
– Filters, fittings made more accessible 过滤器、各种装置 – Transparent panels to facilitate inspection 明了易读的仪表盘便于检查
传感器、触敏器、 连接器污染
Grit and chips
in revolving
or sliding parts 旋转或滑动零件 中的砂砾和碎片
I wonder what’s
going to fail next? 我在想下面还会出什么
问题呢?
Failure to
add oil. 没有加油
Component