切削参数的合理选择
0.8mm钻头加工中心切削参数
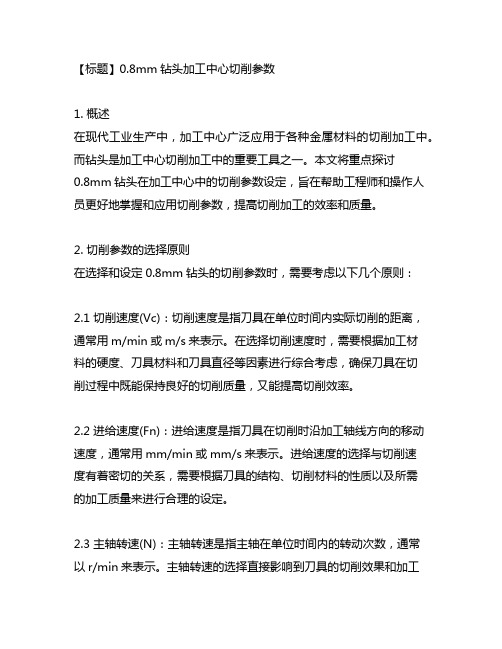
【标题】0.8mm钻头加工中心切削参数1. 概述在现代工业生产中,加工中心广泛应用于各种金属材料的切削加工中。
而钻头是加工中心切削加工中的重要工具之一。
本文将重点探讨0.8mm钻头在加工中心中的切削参数设定,旨在帮助工程师和操作人员更好地掌握和应用切削参数,提高切削加工的效率和质量。
2. 切削参数的选择原则在选择和设定0.8mm钻头的切削参数时,需要考虑以下几个原则:2.1 切削速度(Vc):切削速度是指刀具在单位时间内实际切削的距离,通常用m/min或m/s来表示。
在选择切削速度时,需要根据加工材料的硬度、刀具材料和刀具直径等因素进行综合考虑,确保刀具在切削过程中既能保持良好的切削质量,又能提高切削效率。
2.2 进给速度(Fn):进给速度是指刀具在切削时沿加工轴线方向的移动速度,通常用mm/min或mm/s来表示。
进给速度的选择与切削速度有着密切的关系,需要根据刀具的结构、切削材料的性质以及所需的加工质量来进行合理的设定。
2.3 主轴转速(N):主轴转速是指主轴在单位时间内的转动次数,通常以r/min来表示。
主轴转速的选择直接影响到刀具的切削效果和加工质量,需要根据刀具的直径、切削材料的硬度和刀具的耐磨性等因素进行合理的设定。
3. 0.8mm钻头切削参数的设定基于以上切削参数选择原则,我们可以为0.8mm钻头在加工中心中的切削参数进行如下设定:3.1 切削速度(Vc):根据不同的加工材料硬度和刀具材料,0.8mm钻头的切削速度通常在10m/min至30m/min之间。
需要根据具体情况进行调整和优化。
3.2 进给速度(Fn):0.8mm钻头的进给速度通常在100mm/min至300mm/min之间,具体数值也需根据具体加工需求和刀具性能进行合理的选择。
3.3 主轴转速(N):0.8mm钻头的主轴转速通常在xxxr/min至xxxr/min之间,需要根据刀具和加工材料的情况进行合理的设定。
4. 切削参数的优化与调整在实际应用中,切削参数的设定并非一成不变的,需要根据加工材料、刀具磨损情况和加工效果进行定期检查与调整。
切削参数选择

3/57
工程实训中心
2.进给速度 2.进给速度F (mm/min) 进给速度F (1)工件材料的强度和硬度越高,每齿进给量越小。 工件材料的强度和硬度越高,每齿进给量越小。 (2)工件表面粗糙度要求越高,每齿进给量越小。 工件表面粗糙度要求越高,每齿进给量越小。
加工中心综合实训
切 削 参 数 选 择
主讲:王 飞 主讲:
1/57
工程实训中心
讲授内容:
一、主轴转速 二、进给速度 三、切削参数参考表 四、零件加工顺序
Байду номын сангаас
2/57
工程实训中心
1.主轴转速 1.主轴转速n(r/min) 主轴转速n r/min)
1000v 主轴转速一般根据切削速度V来选定。 主轴转速一般根据切削速度V来选定。 n = πd
6/57
工程实训中心
(13)调头装夹,用平行垫铁保证上下表面的平行度 13)调头装夹, 14) (14)确定工件坐标系 15)铣平面, (15)铣平面,保证工件厚度尺寸 16) (16)确定所用刀具的长度补偿 17)去除余量,利用以加工完毕的外表面, (17)去除余量,利用以加工完毕的外表面,精确确定工件坐标系 18) (18)按要求加工各轮廓
7/57
工程实训中心
8/57
工程实训中心
F = f ⋅Z ⋅n
Z
常用进给速度参考表: 常用进给速度参考表:
4/57
工程实训中心
3.高速钢立铣刀加工铝材切削参数参考表: 3.高速钢立铣刀加工铝材切削参数参考表: 高速钢立铣刀加工铝材切削参数参考表
5/57
工程实训中心
3.零件加工步骤: 3.零件加工步骤: 零件加工步骤
切削参数选择
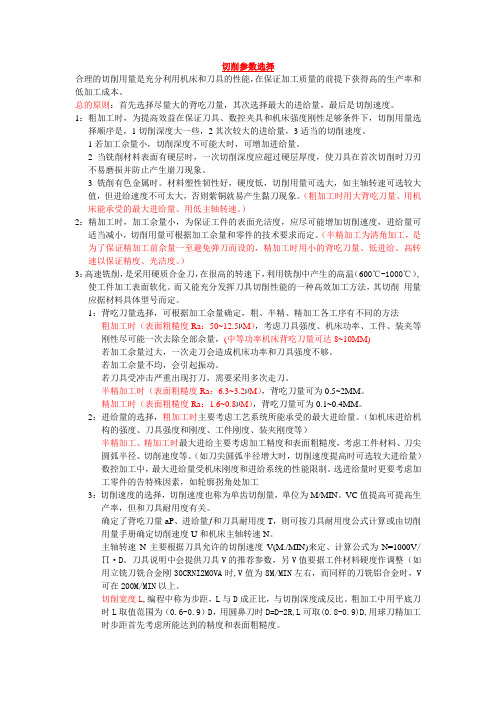
切削参数选择合理的切削用量是充分利用机床和刀具的性能,在保证加工质量的前提下获得高的生产率和低加工成本。
总的原则:首先选择尽量大的背吃刀量,其次选择最大的进给量,最后是切削速度。
1:粗加工时,为提高效益在保证刀具、数控夹具和机床强度刚性足够条件下,切削用量选择顺序是,1切削深度大一些,2其次较大的进给量,3适当的切削速度。
1若加工佘量小,切削深度不可能大时,可增加进给量。
2当铣削材料表面有硬层时,一次切削深度应超过硬层厚度,使刀具在首次切削时刀刃不易磨损并防止产生崩刀现象。
3铣削有色金属时。
材料塑性韧性好,硬度低,切削用量可选大,如主轴转速可选较大值,但进给速度不可太大,否则紫铜就易产生黏刀现象。
(粗加工时用大背吃刀量、用机床能承受的最大进给量、用低主轴转速。
)2:精加工时,加工佘量小,为保证工件的表面光洁度,应尽可能增加切削速度,进给量可适当减小,切削用量可根据加工佘量和零件的技术要求而定。
(半精加工为清角加工,是为了保证精加工前佘量一至避免弹刀而设的,精加工时用小的背吃刀量、低进给、高转速以保证精度、光洁度。
)3:高速铣削,是采用硬质合金刀,在很高的转速下,利用铣削中产生的高温(600℃-1000℃),使工件加工表面软化。
而又能充分发挥刀具切削性能的一种高效加工方法,其切削用量应据材料具体型号而定。
1:背吃刀量选择,可根据加工佘量确定,粗、半精、精加工各工序有不同的方法粗加工时(表面粗糙度Ra:50~12.5µM),考虑刀具强度、机床功率、工件、装夹等刚性尽可能一次去除全部佘量,(中等功率机床背吃刀量可达8~10MM)若加工佘量过大,一次走刀会造成机床功率和刀具强度不够。
若加工佘量不均,会引起振动。
若刀具受冲击严重出现打刀,需要采用多次走刀。
半精加工时(表面粗糙度Ra:6.3~3.2µM),背吃刀量可为0.5~2MM。
精加工时(表面粗糙度Ra:1.6~0.8µM),背吃刀量可为0.1~0.4MM。
刀具几何参数和切削用量的合理选择

加工条件:工艺系统刚性差时,易出现振
动,应选取较小的后角αo;加工表面质量要求 较高时,为减轻刀具与工件之间的摩擦,应选
取较大的后角αo;尺寸精度要求较高时,应选 取较小的后角αo,以减小刀具的径向磨损值NB 值,如下图所示。
硬质合金车刀合理后角的参考值如下表所示。
② 后角αo的选择
切削厚度hD:粗加工时,切削厚度hD较大,要 求切削刃坚固,应选取较小的后角αo。精加工时, 切削厚度hD较小,磨损主要发生在后刀面上,为降 低磨损,应选取较大的后角αo。
工件材料:工件材料强度和硬度较高时,为提
高切削刃强度,应选取较小的后角αo;工件材料软、 塑性大时,后刀面磨损严重,应选取较大的后角αo; 工件材料脆性较大时,载荷集中在切削刃处,为提
负前角双面型:该形式的刀具使刀具的重磨次数 增加,最大程度地减少了前刀面和后刀面的磨损。同 时负前角的倒棱应有足够的宽度,以确保切屑沿该棱 面流出。
(3)倒棱
倒棱是增强切削刃强度的一种措施。在用脆性大 的刀具材料粗加工或断续切削时,磨倒棱能够减小刀 具崩刃,显著提高刀具耐用度(可提高1~5倍)。
倒棱宽度br1不可太大,以便切屑能沿前刀面 流出。br1的取值与进给量f有关,常取br1≈ (0.3~0.8)f。其中,精加工时取小值,粗加工
② 前角γo的选择
工件材料:工件材料的强度、硬度较低,塑
性较好时,应选取较大的前角γo;工件材料脆性较 大时应选取较小的前角γo;工件材料强度、硬度较 高时,应选取较小的前角γo,甚至负前角。
刀具材料:刀具材料的强度和韧度高时,如高 速钢,可选取较大的前角γo;反之,刀具材料的强度 和韧度差时,如硬质合金,应选取较小的前角γo。
数控机床加工塑料材料的最佳切削参数选择方法
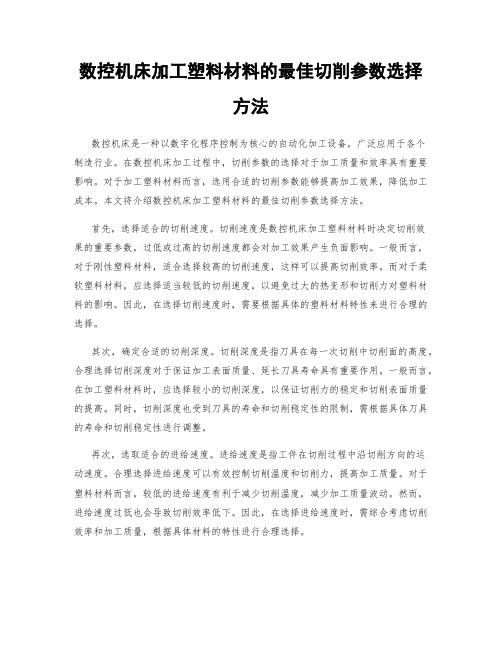
数控机床加工塑料材料的最佳切削参数选择方法数控机床是一种以数字化程序控制为核心的自动化加工设备,广泛应用于各个制造行业。
在数控机床加工过程中,切削参数的选择对于加工质量和效率具有重要影响。
对于加工塑料材料而言,选用合适的切削参数能够提高加工效果,降低加工成本。
本文将介绍数控机床加工塑料材料的最佳切削参数选择方法。
首先,选择适合的切削速度。
切削速度是数控机床加工塑料材料时决定切削效果的重要参数,过低或过高的切削速度都会对加工效果产生负面影响。
一般而言,对于刚性塑料材料,适合选择较高的切削速度,这样可以提高切削效率。
而对于柔软塑料材料,应选择适当较低的切削速度,以避免过大的热变形和切削力对塑料材料的影响。
因此,在选择切削速度时,需要根据具体的塑料材料特性来进行合理的选择。
其次,确定合适的切削深度。
切削深度是指刀具在每一次切削中切削面的高度。
合理选择切削深度对于保证加工表面质量、延长刀具寿命具有重要作用。
一般而言,在加工塑料材料时,应选择较小的切削深度,以保证切削力的稳定和切削表面质量的提高。
同时,切削深度也受到刀具的寿命和切削稳定性的限制,需根据具体刀具的寿命和切削稳定性进行调整。
再次,选取适合的进给速度。
进给速度是指工件在切削过程中沿切削方向的运动速度。
合理选择进给速度可以有效控制切削温度和切削力,提高加工质量。
对于塑料材料而言,较低的进给速度有利于减少切削温度,减少加工质量波动。
然而,进给速度过低也会导致切削效率低下。
因此,在选择进给速度时,需综合考虑切削效率和加工质量,根据具体材料的特性进行合理选择。
此外,刀具的选择也是影响切削效果的重要因素。
切削塑料材料的刀具应具备良好的耐磨性、切削刚度和切削浸入效果。
常见的可选刀具包括硬质合金刀具、聚晶金刚石刀具等。
根据具体的加工要求,选择合适的刀具材料和型号。
最后,为了确保切削效果和加工质量,还需要注意切削液的选择和使用。
切削液可以有效冷却刀具和工件,并清洁切削产生的切屑。
3.7切削条件的合理选择

3.7 切削条件的合理选择一、刀具几何参数的合理选择刀具几何参数包含四方面内容:几何角度、刃形、刃面、刃口型式及参数(一)前角的选择1.前角的作用γ↑→变形程度↓→F↓q ↓→θ ↓→T↑振动↓质量↑0刀刃和刀头强度↓散热面积容热体积↓断屑困难在一定的条件下,存在一个合理值对于不同的刀具材料和工件材料,T 随γ的变化趋势为驼峰形。
高速钢的合理前角比Y合金的大。
加工塑材的合理前角比脆材的大2.合理前角的选择原则①粗加工、断续切削、刀材强度韧性低工材强度硬度高,选较小的前角;②工材塑韧性大、系统刚性差,易振动或机床功率不足,选较大的前角;③成形刀具、自动线刀具取小前角;④Aγ磨损增大前角,Aα磨损减小前角(二)后角的选择1.后角的作用α0↑→rn↓锋利、lα↓摩擦F↓→质量↑VB 一定,磨损体积↑→T↑但NB↑刀头强度↓散热体积↓重磨体积↑在一定的条件下,存在一个合理值2.合理后角的选择原则①粗加工、断续切削、工材强度硬度高,选较小后角, 已用大负前角应↑α;②精加工取较大后角,保证表面质量;③成形、复杂、尺寸刀具取小后角;④系统刚性差,易振动,取较小后角;⑤工材塑性大取较大后角,脆材↓α(三)主偏角的选择1.主偏角的作用κr ↓→ac↓aw↑→单位刃长负荷↓→T↑刀尖强度↑散热体积↑,Ra↓Fp↑→变形↑加工精度↓,易振动→Ra↑,T↓在一定的条件下,存在一个合理值2.合理主偏角的选择原则①主要看系统刚性。
若刚性好,不易变形和振动,κr取较小值;若刚性差(细长轴),κr取较大值(90°);②考虑工件形状、切屑控制、减小冲击等,车台阶轴,取90 °;镗盲孔>90 °;κr小切屑成长螺旋屑不易断;较小κr,改善刀具切入条件,不易造成刀尖冲击。
(四)副偏角的选择副偏角的主要作用是形成已加工表面。
副偏角↓→Ra↓刀尖强度↑散热体积↑↑易振动→Ra↑,T↓副刃工作长度↑→摩擦↑Fp在一定条件下,存在一合理值。
切削 用量的合理选择
2)根据机床说明书,取机床实际进给量 =0.51mm/r。 3)检验机床进给机构允许的进给量。参考CA6140车床说 明书,查出机床进给机构允许的最大进给抗力为:FMfmax= 3528N。 计算切削时进给力为:
统、工件刚度以及精加工时表面粗糙度要求,确定进给量。
3)根据刀具寿命,确定切削速度。 4)所选定的切削用量应该是机床功率所允许的。
1.2切削用量的合理选择方法
1.背吃刀量的合理选择
背吃刀量一般是根据加工余量来确定。 粗加工(表面粗糙度Ra=50~12.5μm)时,尽可能一 次走刀即切除全部余量,在中等功率的机床上加工,取 ap=8~10mm;加工余量太大或余量不均匀、工艺系统刚性 不足或者断续切削时,可分几次走刀。 半精加工(Ra=6.3~3.2μm)时,取ap=0.5~2mm。 精加工(Ra=1.6~0.8μm)时,取ap=0.1~0.4mm。
1.5切削用量的优化概念
切削用量的优化是指在一定的预定目标及约束条件下, 选择最佳的切削用量。
在实际生产中,由于各种条件(加工零件、机床、刀 具、夹具等)都在变化,很难确定出一组最合理的切削用 量数值。
利用切削用量优化的方法,在确定加工条件下,综合 考虑各个因素,通过计算机辅助设计,能找出满足高效、 低成本、高利润和达到表面质量要求的一组最佳的切削用 量参数。实际切削用量的优化过程就是建立优化目标的数 学模型,用计算机求极值。主要目标函数有三个。
床功率是否允许。 在实际生产中,切削用量的合理选择,既可参照有关 手册的推荐数据,也可凭经验根据选择原则确定。
1.3车削用量的合理选择例题
刀具及切削参数选择
刀具及切削参数选择在进行刀具及切削参数选择时,需要考虑多个因素,包括材料的性质、刀具的材质和几何形状、切削速度、进给速度、切削深度等。
正确选择刀具及切削参数可以提高加工效率、降低成本,同时还能保证加工质量和延长刀具寿命。
首先,需要根据被加工材料的性质选择合适的刀具材料。
一般来说,刀具材料应具有高硬度、高耐磨性、高热稳定性和良好的切削刚性。
常用的刀具材料包括高速钢、硬质合金、陶瓷、多晶立方氮化硼等。
不同的材料对应不同的切削速度和进给速度。
其次,刀具的几何形状也是选择的重要因素之一、常见的刀具几何形状包括平底刀、球头刀、角度刀、T型刀等。
不同的几何形状适用于不同的加工操作,如开槽、铣削、钻孔等。
切削速度是刀具及切削参数选择的关键因素之一,它直接影响加工效率和刀具寿命。
切削速度过高会导致刀具温度升高,容易磨损或变形;切削速度过低则会造成加工效率低下。
切削速度的选择应考虑材料的硬度、刀具材料和涂层等因素。
进给速度是指刀具在单位时间内移动的距离,它也是影响加工效率和刀具寿命的重要因素。
进给速度过高会导致切削力增大,容易造成刀具断裂;进给速度过低则会导致切屑不容易排除,造成切削过程中的堆积现象。
进给速度的选择应考虑刀具的切削刚性、加工表面质量和加工要求等因素。
切削深度是指刀具每次切削时所进入被加工材料的深度。
切削深度的选择应根据被加工材料的硬度和强度、刀具的刚性和稳定性来确定。
切削深度过大会导致切削力增大,容易造成刀具断裂;切削深度过小则会导致加工效率低下。
此外,还需要考虑刀具的冷却方式和切削液的选择。
刀具在切削过程中会产生大量的热量,如果不及时冷却,会导致刀具温度过高,影响刀具寿命。
常见的冷却方式包括气体冷却、液体冷却和固体冷却等。
切削液的选择应考虑被加工材料的性质和切削过程中的润滑和冷却效果。
综上所述,刀具及切削参数选择是一个综合考虑材料性质、刀具几何形状、切削速度、进给速度、切削深度、冷却方式和切削液等多个因素的过程。
切削用量的合理选择
切削用量的合理选择切削用量的合理选择(2021-07-1315:37:22)标签:刀具寿命用量生产率切削性能杂谈分类:数控刀具技术切削用量不仅就是在机床调整前必须确认的关键参数,而且其数值合理是否对加工质量、加工效率、生产成本等有著非常关键的影响。
所谓“合理的”切削用量就是指充分利用刀具切削性能和机床动力性能够(功率、扭矩),在保证质量的前提下,赢得低的生产率和高的加工成本的切削用量。
一制订切削用量时考虑的因素切削加工生产率在焊接加工中,金属切除率与切削用量三要素ap、f、v均维持线性关系,即为其中任一参数减小一倍,都可以并使生产率提升一倍。
然而由于刀具寿命的制约,当任一参数减小时,其它二参数必须增大。
因此,在制定切削用量时,三要素获得最佳女团,此时的高生产率才就是合理的。
刀具寿命切削用量三要素对刀具寿命影响的大小,按顺序为v、f、ap。
因此,从保证合理的刀具寿命出发,在确定切削用量时,首先应采用尽可能大的背吃刀量;然后再选用大的进给量;最后求出切削速度。
加工表面粗糙度精加工时,减小进给量将减小加工表面粗糙度值。
因此,它就是精加工时遏制生产率提升的主要因素。
二刀具寿命的选择原则切削用量与刀具寿命存有密切关系。
在制订切削用量时,应当首先挑选合理的刀具寿命,而合理的刀具寿命则应当根据优化的目标而的定。
通常分后最低生产率刀具寿命和最高成本刀具寿命两种,前者根据单件工时最少的目标确认,后者根据工序成本最高的目标确认。
挑选刀具寿命时可以考量如下几点:根据刀具复杂程度、制造和磨刀成本来选择。
复杂和精度高的刀具寿命应选得比单刃刀具高些。
对于机夹可以移调刀具,由于再加刀时间长,为了充分发挥其切削性能,提升生产效率,刀具寿命附加得高些,通常挑15-30min。
对于装刀、换刀和调刀比较复杂的多刀机床、组合机床与自动化加工刀具,刀具寿命应选得高些,尤应保证刀具可靠性。
车间内某一工序的生产率管制了整个车间的生产率的提升时,该工序的刀具寿命必须挑选得高些;当某工序单位时间内所分摊至的全厂支出m很大时,刀具寿命也高文瑞得高些。
数控机床加工不同硬度材料的最佳切削参数选择方法
数控机床加工不同硬度材料的最佳切削参数选择方法引言:数控机床作为现代制造业中的重要设备,广泛应用于各种工业领域。
在加工过程中,选择合适的切削参数对于实现高效、高质量的加工非常重要。
本文将介绍数控机床加工不同硬度材料的最佳切削参数选择方法,以帮助读者在实践中获得更好的加工效果。
一、硬度对切削参数的影响切削硬度是指材料对刀具切削时的硬度,硬度越高通常表明切削难度越大。
硬度对切削参数的选择有以下几个方面的影响:1. 切削速度:硬度较低的材料可以使用较高的切削速度,以提高加工效率。
而对于硬度较高的材料,则需要采用较低的切削速度,这样能减少切削时的磨损,提高刀具使用寿命。
2. 进给速度:硬度较低的材料可以采用较大的进给速度,以加快切削进程。
而对于硬度较高的材料,需要降低进给速度,以减少切削时的切屑形成和排出的困难。
3. 切削深度:对于硬度较低的材料,可以选择较大的切削深度,以减少加工时间。
而对于硬度较高的材料,则需要采用较小的切削深度,以避免刀具过度磨损和工件变形。
二、选择最佳切削参数的方法正确选择切削参数可以提高加工效率、降低成本,并保证加工质量。
以下是一些建议的方法:1. 参考切削参数手册:数控机床切削参数手册是宝贵的参考资料,其中列出了不同硬度材料的推荐切削参数。
可以根据工件材料的硬度,查找手册并参考建议的切削参数进行调整。
2. 经验法则:经验法则可以作为初步选择切削参数的参考。
例如,对于硬度较低的材料,可以尝试切削速度为材料硬度的2倍,进给速度为材料硬度的0.5倍,切削深度为3mm。
然后根据实际情况进行微调。
3. 切削试验:切削试验是一种有效的方法,可以根据试验结果来选择最佳切削参数。
在实际加工之前,可以准备一块与工件材料相似的试验材料,进行切削试验,并记录加工时间、表面粗糙度、切削力等参数。
根据实验结果调整切削参数,以得到最佳加工效果。
4. 刀具选择:选择合适的刀具也是选择最佳切削参数的重要因素。
- 1、下载文档前请自行甄别文档内容的完整性,平台不提供额外的编辑、内容补充、找答案等附加服务。
- 2、"仅部分预览"的文档,不可在线预览部分如存在完整性等问题,可反馈申请退款(可完整预览的文档不适用该条件!)。
- 3、如文档侵犯您的权益,请联系客服反馈,我们会尽快为您处理(人工客服工作时间:9:00-18:30)。
切削用量的合理选择
切削用量不仅是在机床调整前必须确定的重要参数,而且其数值合理与否对加工质量、加工效率、生产成本等有着非常重要的影响。
所谓“合理的”切削用量是指充分利用刀具切削性能和机床动力性能(功率、扭矩),在保证质量的前提下,获得高的生产率和低的加工成本的切削用量。
一制订切削用量时考虑的因素
1.切削加工生产率
、f、v均保持线性关系,即其中任一参数增大一倍,在切削加工中,金属切除率与切削用量三要素a
p
都可使生产率提高一倍。
然而由于刀具寿命的制约,当任一参数增大时,其它二参数必须减小。
因此,在制订切削用量时,三要素获得最佳组合,此时的高生产率才是合理的。
.刀具寿命。
因此,从保证合理的刀具寿命出发,切削用量三要素对刀具寿命影响的大小,按顺序为v、f、a
p
在确定切削用量时,首先应采用尽可能大的背吃刀量;然后再选用大的进给量;最后求出切削速度。
.加工表面粗糙度
精加工时,增大进给量将增大加工表面粗糙度值。
因此,它是精加工时抑制生产率提高的主要因素。
二刀具寿命的选择原则
切削用量与刀具寿命有密切关系。
在制定切削用量时,应首先选择合理的刀具寿命,而合理的刀具寿命则应根据优化的目标而定。
一般分最高生产率刀具寿命和最低成本刀具寿命两种,前者根据单件工时最少的目标确定,后者根据工序成本最低的目标确定。
选择刀具寿命时可考虑如下几点:
1.根据刀具复杂程度、制造和磨刀成本来选择。
复杂和精度高的刀具寿命应选得比单刃刀具高
些。
2.对于机夹可转位刀具,由于换刀时间短,为了充分发挥其切削性能,提高生产效率,刀具寿
命可选得低些,一般取15-30min。
3.对于装刀、换刀和调刀比较复杂的多刀机床、组合机床与自动化加工刀具,刀具寿命应选得
高些,尤应保证刀具可靠性。
4.车间内某一工序的生产率限制了整个车间的生产率的提高时,该工序的刀具寿命要选得低些;
当某工序单位时间内所分担到的全厂开支M较大时,刀具寿命也应选得低些。
5.大件精加工时,为保证至少完成一次走刀,避免切削时中途换刀,刀具寿命应按零件精度和
表面粗糙度来确定。
三切削用量制定的步骤
1.背吃刀量的选择
2.进给量的选择
3.切削速度的确定
4.校验机床功率
四提高切削用量的途径
1.采用切削性能更好的新型刀具材料;
2.在保证工件机械性能的前提下,改善工件材料加工性;
3.改善冷却润滑条件;
4.改进刀具结构,提高刀具制造质量。