不同金属切削条件下切削液的选择
金属切削工艺中冷却液的选择与性能分析
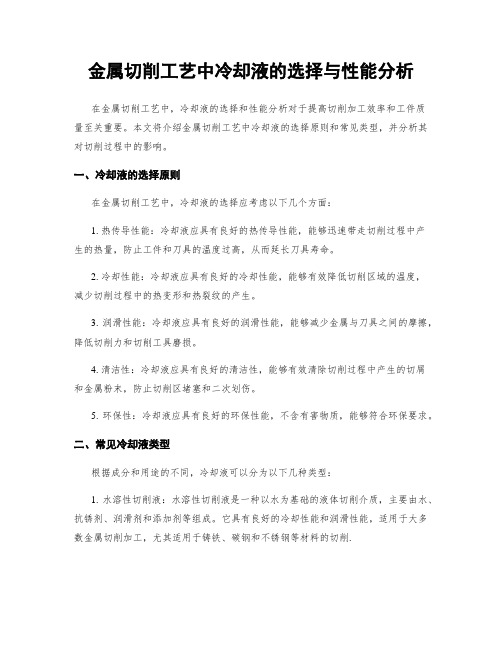
金属切削工艺中冷却液的选择与性能分析在金属切削工艺中,冷却液的选择和性能分析对于提高切削加工效率和工件质量至关重要。
本文将介绍金属切削工艺中冷却液的选择原则和常见类型,并分析其对切削过程中的影响。
一、冷却液的选择原则在金属切削工艺中,冷却液的选择应考虑以下几个方面:1. 热传导性能:冷却液应具有良好的热传导性能,能够迅速带走切削过程中产生的热量,防止工件和刀具的温度过高,从而延长刀具寿命。
2. 冷却性能:冷却液应具有良好的冷却性能,能够有效降低切削区域的温度,减少切削过程中的热变形和热裂纹的产生。
3. 润滑性能:冷却液应具有良好的润滑性能,能够减少金属与刀具之间的摩擦,降低切削力和切削工具磨损。
4. 清洁性:冷却液应具有良好的清洁性,能够有效清除切削过程中产生的切屑和金属粉末,防止切削区堵塞和二次划伤。
5. 环保性:冷却液应具有良好的环保性能,不含有害物质,能够符合环保要求。
二、常见冷却液类型根据成分和用途的不同,冷却液可以分为以下几种类型:1. 水溶性切削液:水溶性切削液是一种以水为基础的液体切削介质,主要由水、抗锈剂、润滑剂和添加剂等组成。
它具有良好的冷却性能和润滑性能,适用于大多数金属切削加工,尤其适用于铸铁、碳钢和不锈钢等材料的切削.2. 非水溶性切削液:非水溶性切削液由有机溶剂和添加剂组成,不含水分。
它可以有效减少金属与刀具之间的摩擦,提高切削效率。
非水溶性切削液适用于高速切削和切削困难材料,如合金钢、高硬度合金等。
3. 高分子切削液:高分子切削液由聚合物和添加剂组成,具有极佳的润滑性能和极高的抗热性能,适用于高温、高速切削加工。
4. 气雾切削液:气雾切削液是一种以气雾形式喷射到切削区域的切削液,具有良好的冷却和润滑效果。
它适用于高速切削、硬质合金切削和有高表面粗糙度要求的切削加工。
三、冷却液性能的分析冷却液的性能对金属切削过程中的加工效果有着直接的影响。
下面将对冷却液的性能进行分析:1. 冷却效果:合适的冷却液能够带走切削时产生的大量热量,降低切削区域的温度,减少工件和刀具的热变形,并提高刀具寿命。
切削液的常见问题和解决方案

切削液是在金属切削和加工过程中广泛使用的工业液体,它具有冷却、润滑、清洁和切屑排除等多种功能。
然而,在实际应用中,切削液也会面临一些常见问题,这些问题可能会影响到加工质量、工具寿命以及生产效率。
为了解决这些问题,需要对切削液的使用和维护进行合理管理。
以下是切削液的常见问题及相应的解决方案。
### 常见问题一:切削液温度过高切削液温度过高可能导致切削液的性能下降,加工件热变形,工具寿命缩短,甚至影响工件表面质量。
**解决方案:**1. **选择适当的切削液:** 不同类型的切削液对温度的抵抗能力不同,选择适合加工要求的切削液;2. **提高切削液流量:** 增加切削液的流量可以有效带走热量;3. **使用冷却设备:** 在切削过程中使用冷却设备,如冷却管或冷却系统,降低切削液温度。
### 常见问题二:切削液污染切削液在使用过程中会受到金属屑、油污、微生物等污染,导致切削液性能下降,产生异味,甚至对操作人员健康有影响。
**解决方案:**1. **定期更换切削液:** 按照生产工艺和使用情况,定期更换切削液;2. **使用过滤设备:** 安装过滤设备,过滤切削液中的杂质;3. **加强切削液维护:** 定期清理切削液槽,防止污染物积聚。
### 常见问题三:切削液泡沫过多切削液泡沫的过多会导致液位不稳定,影响切削液的性能,甚至引起泡沫溢出。
**解决方案:**1. **使用抗泡剂:** 添加抗泡剂来抑制切削液的泡沫生成;2. **调整切削液浓度:** 适量减少切削液的浓度,降低泡沫的生成倾向;3. **增加泡沫抑制设备:** 在切削液槽中安装泡沫抑制设备,减少泡沫的产生。
### 常见问题四:切削液pH值过高或过低切削液的pH值是影响其性能的关键因素,过高或过低都会导致切削液的腐蚀性增强,从而影响加工质量。
**解决方案:**1. **定期监测pH值:** 使用pH试纸或专业测试仪器定期监测切削液的pH值;2. **调整切削液配比:** 根据监测结果适当调整切削液的浓度;3. **添加pH调节剂:** 在切削液中添加pH调节剂,维持适当的酸碱平衡。
金属切削液的基本知识

金属切削的基本知识切削液的配比(1)苏打水苏打(无水碳酸钠):1% 亚硝酸钠:0.25%---0.6% 水:余量将上述物质,加以3---4倍质量的热水(水温40---50度),搅拌3---5分钟,再加入剩余质量的水,再搅拌5分钟。
优点:冷却性能好,防腐蚀作用,良好的洗涤性,成本低(2)乳化液取1.5%---2.5%左右的乳化油,先用少量的温水融化,然后倒入储有足量水的水箱中即可。
但要求有较高的防锈,防腐蚀性能时,加入苏打和亚硝酸钠各0.2%左右。
优点:具有良好的冷却性能和润滑性能,有防腐蚀作用。
常用刀具材料有碳素工具钢、合金工具钢、高速钢、硬质合金等。
(1) 碳素工具钢(如T10、T12A)及合金工具钢(如9SiCr)特点是淬火硬度较高,价廉。
但耐热性能较差,淬火时易产生变形,通常只用于手工工具及形状较简单、切削速度较低的刀具。
(2) 高速钢高速钢是含有较多W、Mo、Cr、V 等元素的高合金工具钢。
高速钢具有较高的硬度(热处理硬度可达HRC62-67)和耐热性(切削温度可达500-600°C)。
它可以加工铁碳合金、非铁金属、高温合金等广泛的材料。
高速钢具有高的强度和韧性,抗冲击振动的能力较强,适宜制造各类刀具。
但因耐热温度较硬质合金低,故不能用于高速切削。
常用牌号分别是W18Cr4V和W6Mo5Cr4V2等。
(3) 硬质合金硬质合金是在高温下烧结而成的粉末冶金制品。
具有较的硬度(70~175HRC),能耐850℃~1000℃的高温,具有良好的耐磨性和耐热性以及高硬度。
因而其切削速度比高速钢刀锯提高2到3倍,主要用于高速切削,但其强度、韧性和工艺性不如高速钢,因此通常将硬质合金焊接或机械夹固在刀体(刀柄)上使用(如硬质合金车刀)。
常用的硬质合金有钨钴类(YG类)、钨钛钴类(YT类)和钨钛钽(铌)类硬质合金(YW类)三类。
① 钨钴类硬质合金(YG类) YG类硬质合金主要由WC和Co组成, YG类硬质合金的抗弯强度和冲击韧性较好,不易崩刃,很适宜切削切屑呈崩碎状的铸铁等脆性材料。
切削液使用注意事项

切削液使用注意事项切削液是在机械加工过程中起到冷却、润滑和清洁作用的液体。
正确使用切削液可以提高加工效率、延长刀具寿命,并且保证加工表面质量。
以下是关于切削液使用的一些注意事项。
1. 选择合适的切削液不同的切削液适用于不同的加工材料和加工方式。
一般来说,切削液可以分为水溶性切削液和油溶性切削液两类。
水溶性切削液适用于大多数金属材料的加工,而油溶性切削液适用于特殊材料或特殊加工方式。
在选择切削液时,要考虑到加工材料、加工方式、刀具类型和润滑要求等因素。
2. 正确调配切削液切削液的浓度和pH值对加工效果和切削液的寿命有着重要影响。
一般来说,切削液的浓度过低会导致润滑效果不佳,切削液的浓度过高则会增加成本并可能导致切削液泡沫过多。
调配切削液时,应按照切削液供应商提供的配方和使用说明进行操作,并定期检测切削液的浓度和pH值,确保其在合适的范围内。
3. 控制切削液的温度切削液的温度对加工效果和切削液寿命有着重要影响。
切削液的温度过高会导致刀具磨损加剧和加工表面质量下降,切削液的温度过低会影响切削液的润滑效果。
因此,在使用切削液时,要采取措施控制切削液的温度,如使用冷却装置或适当增加切削液供给量。
4. 定期清洗切削液系统切削液系统中容易积聚切屑、沉淀物和细菌等污染物,长期积累会导致切削液的质量下降。
因此,需要定期清洗切削液系统,清除积聚的污染物,并更换新的切削液。
清洗切削液系统时,要注意选择合适的清洗剂,并按照清洗剂供应商提供的使用说明进行操作。
5. 保持切削液的清洁切削液的清洁度对加工效果和切削液寿命有着重要影响。
切削液中的杂质和污染物会导致刀具磨损加快和加工表面质量下降。
因此,在使用切削液时,要保持工作环境的清洁,并采取措施防止切削液受到外界污染,如使用密封容器存储切削液、避免切削液与废液混合等。
6. 定期检测切削液质量切削液的质量直接影响加工效果和切削液的寿命。
因此,需要定期检测切削液的质量,如测量切削液的浓度和pH值、检测切削液中的杂质和污染物等。
切削液及其选用

切削液及其选用一、前言合理选用冷却润滑液,可以有效地减小切削过程中的摩擦,改善散热条件,而降低切削力,切削温度和刀具磨损,提高刀具耐用度,切削效率和已加工表面质量及降低产品的加工成本。
随着科学技术和机械加工工业的不断发展,特别足大量的难切削材料的应用和对产品零件加工质量要求越来越高,这就给切削加工带来了难题。
为了使这些难题获得解决,除合理选择别的切削条件外,合理选择切削液也尤为重要。
二.切削液的分类1.水溶液:其主要成分是水。
由于水的导热系数是油的导热系数三倍,所以它的冷却性能好。
在其中加入一定量的防锈和汕性添加剂,还能起到一定的防锈和润滑作用。
2.乳化液:(1)普通乳化液:它是由防锈剂,乳化剂和矿物油配制而成。
清洗和冷却性能好,兼有防锈和润滑性能。
(2)防锈乳化液:在普通乳化液中,加入大量的防锈剂,其作用同上,用于防锈要求严格的工序和气候潮湿的地区。
(3)极压乳化液:在乳化液中,添加含硫,磷,氯的极压添加剂,能在切削时的高温,高压下形成吸附膜,起润滑作用。
3.切削油:(1)矿物油:有5#、7#、10#、20#、30#机械油和柴油,煤油等,适用于一般润滑。
(2)动,植油及复合油:有豆油、菜子油、棉子油、蓖麻油、猪油等。
复合油是将动、植、矿三种油混合而成。
它具有良好地边界润滑。
(3)极压切削油:它是以矿物油为基础,加入油性,极压添加剂和防锈剂而成。
具有动,植物油良好地润滑性能和极压润滑性能。
三.切削液的作用1.冷却作用:它可以降低切削温度,提高刀具耐用度和减小工件热变形,保证加工质量。
一般的情况下,可降低切削温度50~150℃。
2.润滑作用:可以减小切屑与前刀面,工件与刀具后刀面的摩擦,以降低切削力,切削热和限制积屑瘤和鳞刺的产生。
一般的切削油在200℃左右就失去润滑能力。
如加入极压添加剂,就可以在高温(600~1000℃)、高压(1470~1960MPa)条件下起润滑作用。
这种润滑叫做极压润滑。
切削液

切削液切削液的分类在切削加工中,合理使用切削液,可以改善切屑、工件与刀具间的摩擦状况,降低切削力和切削温度,延长刀具使用寿命,并能减小工件热变形,抑制积屑瘤和鳞刺的生长,从而提高加工精度和减小已加工表面粗糙度。
所以,对切削液的研究和应用应当予以重视金属切削加工中常用的切削液可分为三大类:水溶液、乳化液、切削油。
1.水溶液水溶液的主要成分是水,它的冷却性能好,若配成液呈透明状,则便于操作者观察。
但是单纯的水容易使金属生锈,且润滑性能欠佳。
因此,经常在水溶液中加入一定的添加剂,使其既能保持冷却性能又有良好的防锈性能和一定的润滑性能。
2.乳化液乳化液是将乳化油用水稀释而成。
乳化油是由矿物油、乳化剂及添加剂配成,用95—98%水稀释后即成为乳白色或半透明状的乳化液。
它具有良好的冷却作用,但因为含水量大,所以润滑、防锈性能均较差。
为了提高其润滑性能和防锈性能,可再加入一定量的油性、极压添加剂和防锈添加剂,配制成极压乳化液或防锈乳化液。
3.切削油切削油的主要成分是矿物油,少数采用动植物油或复合油。
纯矿物油不能在摩擦界面上形成坚固的润滑膜,润滑效果一般。
在实际使用中常常加入油性添加剂、极压添加剂和防锈添加剂以提高其润滑和防锈性能。
动植物油有良好的“油性”,适于低速精加工,但是它们容易变质,因此最好不用或少用,而应尽量采用其他代用品,如含硫、氯等极压添加剂的矿物油。
切削液的作用机理一、切削液的冷却作用切削液能够降低切削温度,从而可以提高刀具使用寿命和加工质量。
在刀具材料的耐热性较差、工件材料的热膨胀系数较大以及两者的导热性较差的情况下,切削液的冷却作用显得更为重要。
切削液冷却性能的好坏,取决于它的导热系数、比热容、汽化热、汽化速度、流量、流速等。
一般地说,水溶液的冷却性能最好,油类最差(表8—1),乳化液介于两者之间而接近于水。
二、切削液的润滑作用三、切削液的清洗作用当金属切削中产生碎屑(如切铸铁)或粉屑(如磨削)时,要求切削液具有良好的清洗作用。
切削液的使用与维护细则
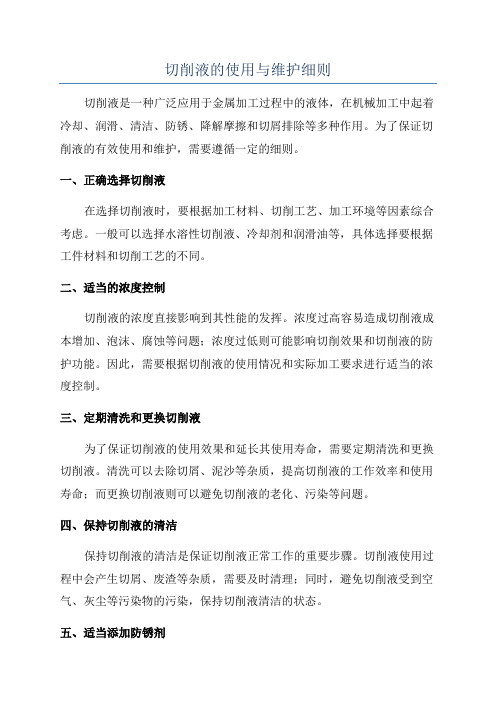
切削液的使用与维护细则切削液是一种广泛应用于金属加工过程中的液体,在机械加工中起着冷却、润滑、清洁、防锈、降解摩擦和切屑排除等多种作用。
为了保证切削液的有效使用和维护,需要遵循一定的细则。
一、正确选择切削液在选择切削液时,要根据加工材料、切削工艺、加工环境等因素综合考虑。
一般可以选择水溶性切削液、冷却剂和润滑油等,具体选择要根据工件材料和切削工艺的不同。
二、适当的浓度控制切削液的浓度直接影响到其性能的发挥。
浓度过高容易造成切削液成本增加、泡沫、腐蚀等问题;浓度过低则可能影响切削效果和切削液的防护功能。
因此,需要根据切削液的使用情况和实际加工要求进行适当的浓度控制。
三、定期清洗和更换切削液为了保证切削液的使用效果和延长其使用寿命,需要定期清洗和更换切削液。
清洗可以去除切屑、泥沙等杂质,提高切削液的工作效率和使用寿命;而更换切削液则可以避免切削液的老化、污染等问题。
四、保持切削液的清洁保持切削液的清洁是保证切削液正常工作的重要步骤。
切削液使用过程中会产生切屑、废渣等杂质,需要及时清理;同时,避免切削液受到空气、灰尘等污染物的污染,保持切削液清洁的状态。
五、适当添加防锈剂切削液使用过程中容易引发金属工件的锈蚀问题,为了减少锈蚀的发生,可以适当添加一些防锈剂。
防锈剂的添加可以提高切削液的防锈性能,延长切削液的使用寿命。
六、定期测量和调整PH值切削液的PH值直接影响到其对金属的腐蚀性和防锈性。
因此,定期测量和调整切削液的PH值是非常重要的。
一般来说,切削液的PH值应在正常范围内,过高或者过低都会对切削液的使用产生不良影响。
七、注意切削液的储存和使用环境切削液的储存和使用环境对其性能的发挥影响很大。
首先,要选择干燥、通风、避光的环境进行切削液的储存;其次,在使用过程中要避免切削液受到灰尘、杂质等污染;最后,在加工过程中要保持切削液的温度适宜,避免过高或者过低。
总之,正确使用和维护切削液对金属加工过程的顺利进行至关重要。
切削液的正确选用

切削液的正确选用正确的选用切削液;可以提高金属切削的生产率;保证被加工材料的加工精度..每种切削液都有各自的优缺点;各有各的用途..因此在加工不同的金属材料时需要选用不同的切削液;这样才能使切削液和刀具有效地结合到金属切削加工中..今天;金属切削行业已进入了系统解决方案的年代..过去那种镶嵌法选用的工艺现已被简化;如果还不能称为“科学”的话;至少可称为“技术”..各种等级的刀具、涂层及断屑装置等因素都应结合在一起统筹考虑和设计;使其适应更大的应用范围和工件材料;更有效地进行加工..然而有时候;金属切削加工中有一个问题往往容易忽略;那就是如何适当地选用切削液..将今天的系统方法应用于金属切削加工;需要正确地使用合适于金属加工的切削液;这与其它因素一样;已成为解决方案中的同样重要部分..实际上;现在至少有一家公司正在将切削液和刀具有效地结合到金属切削系统之中..当你选用以后的切削液时;应考虑到以下一些因素:四个关键问题在选用切削液时;有四大关键问题需要考虑;这些问题是:1. 你在切削加工中加工的是什么材料2. 在你使用的切削液中含有哪些化学成分3. 你现在使用的是什么切削液4. 有哪些切削液可供你选用5. 你喜欢哪种切削液6.你在切削加工的是什么材料第一个问题是:你在切削加工中加工的是什么材料回答这个问题往往是最困难的;因为在正常的情况下;大多数车间内所加工的工件材料是各种各样的..如果答案毫不含糊的说是“铝”或“不锈钢”或“铸铁”;切削液的选用就可能相当简单和直截了当..可惜在大批量生产的工厂;这样的情况极少.. 如果所切削加工的绝大部分零件为铝或有色金属;那末切削加工时就必须采用非污染型切削液..一般来说;所使用的切削液为加有特殊成分的半合成液体;可防止有色金属工件的双金属腐蚀和污染..如果有色金属占绝大部分;选用通用的半合成或混合切削液比较经济..第二个问题是:在你的切削液中含有哪些化学成分这个问题可能涉及到切削液使用的成败原因..很少有工厂会花费必要的资金;去投资安装采用等离子技术或逆向渗透技术的有效水净化系统.. 可惜在重新配制切削液的过程中;所使用水中的化学成分对切削液的性能和油箱的使用寿命会产生相当大的差别..大部分切削液生产厂将会做一些必要的用水试验;以确定溶解于水中的矿物质含量;并根据试验结果来推荐使用切削液..第三个问题是:你现在使用的是什么切削液解答这一问题有助于缩小选用切削液的范围..结合目前使用的切削液优缺点进行客观的分析;就能很快地对这一问题做出答复;使你在相对较少的、具有竞争性的各种替代切削液中选用;以满足你的切削要求.. 今天所使用的多数切削液都是以前所沿用下来的..如果一家公司永远不思进取的话;他们最终必将会被其竞争对手所取代;这是今天市场的严酷现实..第四个问题是:有哪些切削液可供你选用这个问题关系到一种切削液的最终选择..根据化学特性;切削液一般可分为4大类型;它们分别是:可溶解的油类------照字面解释;这种油可在水中溶合扩散;合成液------一种完全不含油的人造可溶性冷却液;半合成液------一种含有30 %矿物油的天然和合成润滑剂混合液;混合液------含有约15 %矿物油的特种半合成切削液..每种切削液都有各自的优缺点;因此各有各的用途..此外;在某些特殊的应用领域;各类切削液之间都提供有性/价比..例如;对某一特定的使用领域;也许混合液和半合成液都很适用;而使用混合液也许初期费用较高;但可提高油箱使用寿命;相反;一些半合成液可循环使用;或排放量少;比较经济;但油箱的使用寿命不那么长..在这种情况下;最终的决策取决于使用这种切削液车间的具体经济效益以及业主的个人喜好..可溶性油类可溶性油类是指那些加入乳化剂以后能够溶合扩散在水中的油类..这种切削液一般适合于各种有色金属、碳钢、铸钢等的中等和重型切削加工和磨削加工以及其他的应用领域;例如同时出现铝和钢等不同金属的应用场合..它们也适用于车削、钻削、攻丝、铰孔、切齿、拉削、内圆磨削和无心外圆磨削..可溶性油类对铝材和铜材具有优良的防腐蚀控制功能;良好的防腐臭控制功能;可延长切削液的使用寿命和提高无故障工作性能;其良好的浓缩性能和混合稳定性;通过微量的搅拌;可以很理想的使其与水混合..例如Valenite公司的VNTr-650就是一种适合于重型切削加工的可溶性油类..合成液合成液是一种完全无油的溶液;由聚合体、有机和无机材料与水混合配制而成..这类透明、低泡沫和生物性稳定的冷却液对有色金属、碳钢或铸铁的机加工和磨削加工十分理想..它们的复合润滑剂使这种合成液特别适合于难以加工的材料;例如不锈钢和高温合金..某些合成液专门适用于因侧面造成磨损的初期故障状态..有些合成液虽然有许多优点;但可能会引起有色金属的污染..半合成液半合成液由油类、合成乳化剂及水混合配制而成..它们的开发主要用于航空、核电及有关工业..因此;对于各种有色金属;如钛、铝、紫铜、黄铜、青铜和不锈钢的机加工和磨削加工;它们的工作性能都非常好..半合成液也适用于黑色金属的加工..它们不含氯;因此降低了双金属腐蚀和对金属的污染..使用时;根据不同严格程度的操作要求;采用5%~8 %的水稀释液..混合液混合液是专为满足用户的特殊要求和解决特殊的问题而配制的切削液..例如Valenite公司的VNTr-800切削液是专为铸铁的机加工和磨削加工而开发的;使用这种切削液的工作环境非常干净;其在硬水中的性能比较稳定;可以很好地排斥废油;从而提高了它的生物化学特性..在机加工和磨削加工中;混合液的工作性能特别优秀;适合于对各种金属的加工..使用时;应根据不同的水质情况;混合配制成5%~7 %的水稀释液..最后一个问题是:你喜欢哪一种切削液一般在有几种切削液供你选用的情况下;才会提出这一问题..在这种情况下;还是会涉及到目前你所使用的是哪一种切削液;关键是应客观地检查一下你的喜好;特别要分清这种喜好背后的真正原因..如果你说不出为什么喜欢某种切削液而不喜欢另一种切削液的特别原因;最好还是听从专业人员对你要求的分析;采纳他们的建议..今天;选用正确的切削液要比从前容易的多;因为可接受的、能提高金属切削生产率的系统解决方法在不断增加..像今天能够很容易地正确选用镶刀片和断屑装置那样;对于切削液来说;可以同样容易地选用全套解决方案的日子也不远了..答案已经提供了;其结果将由你选用正确切削液所花的时间来证实..刀具材料对切削液选用的影响刀具钢刀具:其耐热温度约在200-300℃之间;只能适用于一般材料的切削;在高温下会失去硬度..由于这种刀具耐热性能差;要求冷却液的冷却效果要好;一般采用乳化液为宜..·高速钢刀具:这种材料是以铬、镍、钨、钼、钒有的还含有铝为基础的高级合金钢;它们的耐热性明显地比工具钢高;允许的最高温度可达600℃..与其他耐高温的金属和陶瓷材料相比;高速钢有一系列优点;特别是它有较高的坚韧;适合于几何形状复杂的工件和连续的切削加工;而且高速钢具有良好的可加工性和价格上容易被接受..使用高速钢刀具进行低速和中速切削上;建议采用油基切削液或乳化液..在高速切削时;由于发热量大;以采用水基切削液为宜..若使用油基切削液会产生较多油雾;污染环境;而且容易造成工件烧伤;加工质量下降;刀具磨损增大..·硬质合金刀具:用于切削刀具的硬质合金是由碳化钨WC、碳化钛TiC、碳化钽TaC和5-10%的钴组成;它的硬度大大超过高速钢;最高允许工作温度可达1000℃;具有优良的耐磨性能;在加工钢铁材料时;可减少切屑间的粘结现象..在选用切削液时;要考虑硬质合金对骤热的敏感性;尽可能使刀具均匀受热;否则会导致崩刃..在加工一般的材料时;经常采用干切削;但在干切削时;工件温升较高;使工件易产生热变形;影响工件加工精度;而且在没有润滑剂的条件下进行切削;由于切削阻力大;使功率消耗增大;刀具的磨损也加快..硬质合金刀具价格较贵;所以从经济方面考虑;干切削也是不合算的..在选用切削液时;一般油基切削液的热传导性能较差;使刀具产生骤冷的危险性要比水基切削液小;所以一般选用含有抗磨添加剂的油基切削液为宜..在使用冷却液进行切削时;要注意均匀地冷却刀具;在开始切削之前;最好预先用切削液冷却刀具..对于高速切削;要用大流量切削液喷淋切削区;以免造成刀具受热不均匀而产生崩刃;亦可减少由于温度过高产生蒸发而形成的油烟污染..·陶瓷刀具:采用氧化铝、金属和碳化物在高温下烧结而成;这种材料的高温耐磨性比硬质合金还要好;一般采用干切削;但考虑到均匀的冷却和避免温度过高;也常使用水基切削液..·金刚石刀具:具有极高的硬度;一般使用于切削..为避免温度过高;也象陶瓷材料一样;许多情况下采用水基切削液..切削液及其选用一、前言合理选用冷却润滑液;可以有效地减小切削过程中的摩擦;改善散热条件;而降低切削力;切削温度和刀具磨损;提高刀具耐用度;切削效率和已加工表面质量及降低产品的加工成本..随着科学技术和机械加工工业的不断发展;特别足大量的难切削材料的应用和对产品零件加工质量要求越来越高;这就给切削加工带来了难题..为了使这些难题获得解决;除合理选择别的切削条件外;合理选择切削液也尤为重要..二.切削的分类1.水溶液:其主要成分是水..由于水的导热系数是油的导热系数三倍;所以它的冷却性能好..在其中加入一定量的防锈和汕性添加剂;还能起到一定的防锈和润滑作用..2.乳化液:1普通乳化液:它是由防锈剂;乳化剂和矿物油配制而成..清洗和冷却性能好;兼有防锈和润滑性能..2防锈乳化液:在普通乳化液中;加入大量的防锈剂;其作用同上;用于防锈要求严格的工序和气候潮湿的地区..3极压乳化液:在乳化液中;添加含硫;磷;氯的极压添加剂;能在切削时的高温;高压下形成吸附膜;起润滑作用..3.切削油:1矿物油:有5、7、10、20、30机械油和柴油;煤油等;适用于一般润滑..2动;植油及复合油:有豆油、菜子油、棉子油、蓖麻油、猪油等..复合油是将动、植、矿三种油混合而成..它具有良好地边界润滑..3极压切削油:它是以矿物油为基础;加入油性;极压添加剂和防锈剂而成..具有动;植物油良好地润滑性能和极压润滑性能..三.切削液的作用1.冷却作用:它可以降低切削温度;提高刀具耐用度和减小工件热变形;保证加工质量..一般的情况下;可降低切削温度50~150℃..2.润滑作用:可以减小切屑与前刀面;工件与刀具后刀面的摩擦;以降低切削力;切削热和限制积屑瘤和鳞刺的产生..一般的切削油在200℃左右就失去润滑能力..如加入极压添加剂;就可以在高温600~1000℃、高压1470~1960MPa条件下起润滑作用..这种润滑叫做极压润滑..3.清洗作用:可以将粘附在工件;刀具和机床上的切屑粉末;在一定压力的切削液作用下冲洗干净..4.防锈作用:防止机床、工件、刀具受周围介质水分、空气、手汗的腐蚀..四.冷却润滑液中的添加剂1.油性添加剂:动植物油、脂肪酸及其皂、脂肪醇及多元醇、酯类、酮类、胺类等化合物..2.极压添加剂:含硫、磷、氯等有机化合物..如氯化石腊、四氯化碳、硫化磷酸盐、二烷基二硫代磷酸锌等..含硫的极压切削油在切削过程中和金属起化学反应;生成硫化铁;它的熔点高1193℃;硫化膜在高温下不被破坏;在切削钢件时;能在1000℃左右的高温下;仍保持润滑性能;含氯的极压添加剂;如氯化石腊含氯量为40~50%;它的化学性能活泼;在200℃~300℃时和金属起化学反应;氯化物的摩擦系数低于硫化物;有良好地润滑性能;可耐600℃的高温;含磷极压添加剂;与钢铁接触即被吸附;生成磷酸铁化学润滑膜;降低摩擦;比硫氯的效果更为良好..如三种复合使用;润滑效果更为显着..3.防锈添加剂:1水溶性防锈添加剂:亚硝酸钠、磷酸三钠、磷酸氢二钠、苯甲酸钠、苯甲酸胺、三乙醇胺等..2油溶性防锈添加剂:石油磺酸钡、石油磺酸钠、环烷酸锌、三壬基萘磺酸钡等..4.防霉添加剂:苯粉、五氯粉、硫柳汞等化合物..加入万分之几的防霉添加剂;可杀死细菌和抑制细菌生长;以防切削液变质发臭..5.抗泡沫添加剂:二甲基硅油..以防止切削液的使用效果..6.助溶添加剂:乙醇、丁乙醇、苯二甲酸脂、乙二醇醚等..7.乳化剂:1阴离子型:石油磺酸钠、油酸钠皂、松香酸钠皂、高炭酸钠皂、磺化蓖麻油、油酸、三乙醇胺..2非离子型:聚氧乙烯脂肪醇醚平平加、聚氧乙烯烷基酚醚0P、山梨糖醇油酸酯司本、聚氧乙烯山梨糖醇油酸酯吐温..8.乳化稳定剂:乙二醇、乙醇、正丁醇、二乙二醇单正丁基醚、二甘醇、高碳醇、苯乙醇胺、三乙醇胺等..五.常用冷却润滑液的配方1.切削油:1矿物油:5、7、10、20、30机械油和轻柴油、煤油..机械油的号数越大;粘度越大..2植物油:豆油、菜子油、棉子油、蓖麻油等..3复合油:煤油50%+机械油50%;豆油50%+5..高速机油50%..4极压切削油:①氯化石腊20%+二烷基二硫代磷酸锌1%+高速机油79%..②氯化石腊40%+二烷基二硫代磷酸锌1%+石油磺酸钙1%+苯骈三氮唑0.2%+乙醇0.56~0.8%+5高速机油余量..③硫化棉子油7%+5高速机械油93%..④氯化石腊20%+5高速机械油80%..2.乳化液:1普通乳化液:3~5%乳化油70%+5机械油+22%脂肪酸及其皂+0.5%松香酸钠皂+4.5%乙醇+3%石油磺酸钠加水稀释..2极压乳化液:用5~20%极压乳化油10%石油磺酸钠+6%石油磺酸铅+4%氯化石腊+3%氯化硬脂酸+3%油酸+3%三乙酸胺+20机械油余量加水稀释..3防锈乳化液:是在普通乳化液中增加防锈剂的比例而成..3.水溶液:1用0.25~0.5%亚硝酸钠+0.25~0.3%无水碳酸钠+水余量..23%油酸钠皂+0.5%亚硝酸钠+水余量..310%癸二酸+17.5%三乙醇胺+8%亚硝酸钠+水余量..六.冷却润滑液的选择1.选择原则1.1根据工件材料选择1铸铁、青铜在切削时;一般不用切削液..精加工时;用煤油..2切削铝时;用煤油..3切削有色金属时;不宜用含硫的切削液..4切削镁合金时;用矿物油..5切削一般钢时;采用乳化液..6切削难切削材料时;应采用极压切削液..1.2根据工艺要求和切削特点选择1粗加工时;应选冷却效果好的切削液..2精加工时;应选润滑效果好的切削液..3加工孔时;应选用浓度大的乳化液或极压切削液..4深孔加工时;应选用含有极压添加剂浓度较低的切削液..5磨削时;应选用清洗作用好的切削液..6用硬质合金、陶瓷和PCD、PCBN刀具切削时;一般不用切削液..要用时;必须自始自终地供给..PCBN刀具在切削时;不能用水质切削液..固为CBN在1000℃以上高温时;会与水起化学反应而被消耗..2.选用2.1碳钢1粗加工:a3~5%乳化液..b铅油或红丹粉10%+机械油90%;用于粗车蜗杆..2精加工:a10~20%的乳化液..b10~15%极压乳化液..c硫化棉子油的切削油..d20%氯化石腊+80%变压器油或30%豆油+20%煤油+50%高速机械油;用于精车丝杠..eccl420%+80%机械油;用于精车蜗杆..3拉削、攻丝、铰孔:a10~20%极压乳化液..b含氯的切削油..c含硫;氯的切削油..d含硫化棉子油的切削油..e含硫;氯;磷的切削油..f30%煤油+70%机械油;用于光刀.. gMoS2与机械油混合;用于攻丝..4滚齿;插齿:a10~20%极压乳化液..b含硫;磷;氯的极压切削油..5钻孔:a3~5%乳化液..b5~10%极压乳化液..2.2合金钢1粗加工:a3~5%乳化液..b5~10%极压乳化液..2精加工:a10~20%乳化液..b10~15%极压乳化液..c含硫化棉子油的切削油..3拉削、攻丝、铰孔:a10~20%极压乳化液..b含硫、磷、氯极压切削油..c40机械油85%+二烷基二硫代磷酸锌5%+石油磺酸钙7%+二硫化钼1%氯化石腊1%+煤油1%..用于攻丝..效果:Vc从1m/min提高到7m/min;丝锥耐用度提高1~3倍;表面粗糙度由Ra6.3降低为Ra3.2..4滚齿、插齿:a10~20%极压乳化液..b极压切削油..5钻孔:a3~5%乳化液..b5~10%极压乳化液..cccl4和煤油的混合液钻膜具钢小孔..d氯化石腊20%+二烷基二硫代磷酸锌1%+高速机油79%..2.3不锈钢1粗加工:a3~5%乳化液..b10~15%极压乳化液..c极压切削油..d硫化油含硫2%的机械油..2精加工:a极压切削油..b10~15%乳化液..c15~20%极压乳化液..d硫化油或硫化油80~85%+ccl415~20%..e矿物油78~80%+黑机油或植物油和猪油18%+硫1.7%..f机械油90%+ ccl410%..h煤油50%+油酸25%或植物油25%..i煤油60%+松节油20%+油酸20%..3拉削、攻丝、铰孔:a15~20%极压乳化液..b极压切削油..c硫化豆油或植物油..d在硫化油中加ccl410~20%或在猪油中加20~30%ccl4或在硫化油中加10~15%煤油用于铰孔..e在硫化油中加入15~20%ccl4或白铅油加机械油或煤油稀释氯化石腊或MoS2切削膏用于攻丝..4滚齿、插齿:a20~25%极压乳化液..b极压切削油..5钻孔:a10~15%乳化液..b10~20%极压乳化液..c极压切削油..d硫化油..eMoS2切削剂..f用肥皂涂抹在小钻头上;用于在台钻小孔..2.4高温合金1粗加工:a3~5%乳化液..b10~15%极压乳化液..c极压切削油..d硫化油..e硫酸钾2%+亚硝酸钾1%+三乙醇胺7%+硼酸7~10%+甘油7~10%+水余量..f葵二酸7~10%+亚硝酸钠5%+三乙醇胺7~10%+硼酸7~10%+甘油7~10%+水余量..2精加工:a10~25%乳化液..b15~20%极压乳化液..c极压切削油..d煤油75%+油酸25%..3拉削、攻丝、铰孔:a10~20%极压乳化液..b极压切削油..c参照不锈钢所用切削液..d防锈和电解切削液也适合于拉削和铰孔..4钻孔:a10~15%乳化液..b10~20%极压乳化液..c极压切削油..d硫化油..eMoS2切削剂..2.5钛合金1粗加工:a3~5%乳化液..b极压乳化液..2精加工:a极压切削油石油磺酸钠10%+油酸3%+石油磺酸铅6%+三乙醇胺3.5%氯化石腊4%+氯化硬脂酸3%+20机械油70.5%..b极压水溶液氯化脂肪酸;聚氯乙烯0.5~0.8%+磷酸三钠0.5%+三乙醇胺1~2%+亚硝酸钠1.2%+水余量..cCCl4+等量的酒精..3拉削、攻丝、铰孔:a极压切削油..b蓖麻油..c油酸..d硫化油..e氯化油f蓖麻油60%+煤油40%g聚醚30%+酯类油30%+7机械油30%+防锈剂与抗泡剂10%;用于拉削..4钻孔:a极压乳化液..b极压切削油..c电解切削液癸二酸7~10%+三乙醇胺7~10%+甘油7~10%+硼酸7~10%亚硝酸钠3~5%+余下水..d硫化油..e30机械油60%+煤油40%或30机械油70%+煤油30%..2.6铸铁、黄铜1粗加工:a10~15%乳化液..2精加工:a煤油..b煤油与矿物油的混合油..3拉削、攻丝、铰孔:a10~15%乳化液..b10~20%极压乳化液..c煤油..d煤油与矿物油的混合油..2.7紫铜1粗、精加工:a3~5%乳化液..b煤油..c煤油与矿物油的混合油..d菜子油..2滚齿、插齿:a10~25%乳化液..b10~20%极压乳化液..c煤油..d煤油与矿物油的混合油..3钻孔:a3~5%乳化液..b煤油..c煤油与矿物油的混合油..2.8铝及其合金1粗、精加工:a3~5%乳化液..b煤油..c煤油与矿物油的混合油..d菜子油..2拉削、攻丝、铰孔、滚齿、插齿:a10~15%乳化液..b10~15%极压乳化液..c煤油..d煤油与矿物油的混合油..3钻孔:a3~5%乳化液..b煤油与矿物油的混合油..C煤油..2.9青铜1粗精加工及钻孔:a一般不用切削液..可用3~5乳化液..2拉削、攻丝、铰孔、滚齿、插齿a10~20%乳化液..b10~15%极压乳化液..c含氯的切削油..2.10高强度钢采用合金钢的切削液..用豆油或菜子油攻丝较好..2.11钼用ccl4加20机械油或用MoS2润滑脂..2.12纯铁用碳素钢的切削液..精加工时;可用酒精稀释蓖麻油作切削剂..2.13橡胶切削时用酒精或蒸馏水..磨削时;用苏打1%+亚硝酸钠0.25~0.5%+甘油0.5~1%+余下水..附:一.固体润滑剂——MoS21.特点:MoS2的摩擦系数很小;仅0.05~0.09;它的润滑膜有很高的抗压能力及附着能力;粘附在金属表面的二硫化钼薄膜;能承受3500MPa的压力不被破坏;有很高的化学稳定性;不易与酸碱起作用;温度稳定性好;在400℃左右才分解;当二硫化铝混于油或脂中;与空气接触不充分;氧化温度还可以提高..2.应用:它有油剂;水剂和润滑脂三种;也可将二硫化钼与硬脂酸和石腊制成腊笔..用时将二硫化钼润滑剂涂在刀具表面上;可以成倍地提高刀具耐用度和降低工件表面粗糙度;降低切削力;切削热;抑制积屑瘤的产生..二.MoS2在切削中的作用1.在车削方面:1在刀具上涂MoS2;刀具耐用度可提高一倍以上..2在精车蜗杆时;在切削剂中加2%的MoS2;可降低工件表面粗糙度..3铰65Mn孔时;在乳化液中加1%MoS2或铰不锈钢孔时;在乳化液中加3%MoS2;不仅工件表面粗糙度低;而且刀具耐用度高..2.在磨削方面:在砂轮表面上涂上MoS2;工件表面粗糙度可降低一级..3.在切削齿轮方面:在硫化油中加0.5~1%MoS2油剂后;切屑瘤可消除..4.在复杂刀具方面:在拉削和推削加工时;在原切削液中添加15~20%的MoS2油剂后;刀具寿命提高近60倍;工件表面粗糙度可降一级..5.在攻丝方面:它是润滑性能良好的攻丝切削剂..特别是在挤压攻丝时;唯有MoS2的润滑效果最好..6.在锯切方面:在锯条上涂上MoS2后;锯切时噪音小;锯条不易损坏..7.在难切削材料方面:如切削钛合金;高温合金;不锈钢时;在刀具上涂MoS2;效果也十分好根据工件材料选用切削液工件材料的性能对切削液的选择很重要..据文献介绍;可把被加工材料按其可切削性的难易划分为不同级别;以此作为选择切削液的依据..将铜在固定条件下的可切削性指数定为100;将其他材料的相同的条件下进行切削;按得出的刀具相对耐用度进行排列..·普通可切削钢;包括非合金钢、低合金钢及其淬火钢15;35;15CrMn、易切削钢Y12;Y12Mn、建筑钢材35;60;可切削系数为80;较难切削钢;包括高合金钢及其淬火钢20CrMo;42CrMo、高铬合金钢1Cr17;4Cr13、高铬镍合金钢12CrNi2、耐腐蚀耐酸的铬镍钢0Cr18Ni9;1Cr18Mo10Nb、铸钢;可切削系数为50;·难切削钢;包括镍和镍合金Ni10Cr10;Ni18Cr20、锰和镍硅钢40CrMn2;60Si2Mn、铬钼钢20CrMo、硅钢38Si2Mn、钛和钛合金;可切削系数为25;·灰铸铁和可锻铸件HT250;KTZ450-06;可切削系数为60-110;·有色金属;铜和铜合金ZCu Sn10Pbl;可切削系数为100-600;轻金属;铝和镁合金LF5;LF10;LDI;可切削系数为300-2000..切削指数越小的材料越难加工..在选择切削液时;对于难加工的材料应选择活性度高的含抗磨极压添加剂的切削液;对于易加工材料;可选用纯矿油或其他不含极压添加剂的切削液..切削加工是一个复杂过程;尽管是切削一种材料;但当切削速度改变或切削工件的几何形状改变时;切削液显示的效果就完全不同;所以在选择切削液时要结合加工工艺和加工工件的特点来综合考虑..。
- 1、下载文档前请自行甄别文档内容的完整性,平台不提供额外的编辑、内容补充、找答案等附加服务。
- 2、"仅部分预览"的文档,不可在线预览部分如存在完整性等问题,可反馈申请退款(可完整预览的文档不适用该条件!)。
- 3、如文档侵犯您的权益,请联系客服反馈,我们会尽快为您处理(人工客服工作时间:9:00-18:30)。
不同金属切削条件下切削液的选择
在机械切削加工中,使用数控机床切削时,按切削加工方法划分,主要有车削、铣削、钻削和镗削等;按去除材料多少划分,有粗加工、半精加工和精加工;按使用切削刀具材料划分,有高速钢、硬质合金、陶瓷、金刚石和立方氮化硼等;按机床划分,主要有明确要求使用油基切削液的机床、没有要求的机床、单件小批量生产类型的机床以及成批生产或自动生产线(柔性制造系统)等。
对于不同方式的切削加工,相同金属的切除特性是不一样的,加工难度的变化也是差别明显。
例如,同样使用Q235碳素钢材料,在保证表面粗糙度质量指标上,加工螺纹要难于切削其他表面;精加工要难于粗加工。
较难的切削加工对切削液的要求也较高。
正确使用切削液能够有效保证加工质量、延长刀具使用寿命以及提高加工效率。
1.粗加工
当数控机床需要粗、精加工分开或工件不在一台机床完成时,就可以按粗、精加工的特性选择切削液。
粗加工时,背吃刀量和进给量均较大,导致切削阻力大,因而产生大量的切削热,传给工件和刀具的热量也相应地增多,使得工件的热变形和刀具的磨损加剧,应该选择以冷却为主并具有一定润滑清洗和防锈作用的水基切削液,并且要大流量连续浇注。
在车削等属于连续加工或粗加工余量均匀时,切削热是着重考虑的问题,切削液的冷却作用是首先衡量的指标。
在铣削或加工形状不规则、余量不均匀和断续加工时,切削速度要比连续均匀加工低,切削热的影响要比冲击和振动对刀具和工件的影响小,切削液的润滑和冷却作用要均衡考虑。
机床条件允许时,在孔加工、切断时可以使用带内部供液孔的内孔车、镗刀和切槽刀,或使用压力供液,以及粗加工难加工材料时使用喷雾供液,均能起到较好效果。
粗加工的工件一般留有加工余量,同时,加工难加工材料和有色金属材料时,表面粗糙度精度指标要求不高,因此,加工难加工材料和有色金属材料时,粗加工对切削液中的化学成分要求不高,可以使用水基极压乳化液。
粗加工铸铁和脆性有色金属时,这些材料切削时共同的特点是切屑呈崩碎状,细小的切屑碎末在切削液的冲击下呈流动状态,随切削液循环时流经切削液箱时大部分会沉积,一部分随切削液流动,聚集在切削液输送管细小部位便会堵塞冷却喷管,并使切屑黏附在机床的运动部件(如导轨运动副)上。
同时切削液与铸铁中某些成分发生化学反应,导致切削液变质,引起切削液性能下降。
由于使用切削液会带来这些难题,一般不使用切削液。
为了减少粉尘和切削热的影响,条件具备时,可以考虑使用抽尘装置,以吸走粉尘、细小切屑和一部分热量。
如果使用切削液,易使用水基切削液,并一定做好切削液过滤和净化、防止切削液变质和浓度下降的预防工作。
粗加工时,与精加工相比,切削液的浓度要低一些。
2.精加工
精加工按切削速度划分,有高速精加工和低速精加工之分。
高速精加工时,使用油基切削液虽然能够保证工件表面质量,延长刀具使用寿命,但其所含的矿物油的粘度和闪点低,经常产生油烟、油雾和油蒸气,同时分解有毒成分,影响生产环境,损害操作者的身心健康。
所以精加工高速切削时,尽可能地使用水基切削液中含极压添加剂的乳化液或微乳化液,且其浓度要高于粗加工的浓度。
低速精加工时,切削温度低,不易产生上述问题。
为了保证工件的加工精度,宜使用油基切削液。
相对于粗加工而言,精加工时的切削速度高,切屑变形产生的切削热比刀具后刀面摩擦产生的切削热低,切削力小,即使高速切削,切削热对工件的热变形也没有粗加工明显,刀具之所以使用切削液主要是减少刀具后刀面的磨损。
刀具在精加工时,相对切削速度较高,切屑从工件上切除的瞬间的温度是很高的,即便使用切削液,若因切削液的渗透性不好或压力不够,切削液没有充分渗透到切削区,会使刀具极易出现后刀面磨损,即使刀具仍然能够使用,却使工件表面粗糙度质量达不到要求,仍然需要更换刀具。
所以精加工时,一定要使用润滑效果显著、渗透性好的切削液,以延长刀具的使用寿命,保证工件的加工精度和表面粗糙度质量要求。
低速精加工黑色金属材料时,可以选用活性极压切削油;低速精加工有色金属时,宜选用非活性极压切削油;高速精加工有色金属时,可以选用非活性极压添加剂的乳化液。
3.孔加工
在数控加工中,孔加工主要指钻孔、铰孔、在车床上车削内孔和在镗床上镗孔。
由于排屑、散热困难,刀具(杆)刚性差,孔加工的切削速度要低于外轮廓加工,难度也要高于外轮廓加工。
钻孔时使用一般的麻花钻钻孔,属于粗加工,钻削时排屑困难,不易散发切削热,往往造成刀刃退火,影响钻头使用寿命及加工效率。
选用性能好的切削液,可以使钻头的寿命显著延长,生产率也明显提高。
一般选用极压乳化液或极压合成切削液。
极压合成切削液表面张力低,渗透性好,能及时冷却钻头,对延长刀具寿命、提高加工效率十分有效。
对于不锈钢、耐热合金等难切削材料,可选用低粘度的极压切削油。
钻孔时,无论是普通钻孔还是深孔钻孔,散热条件差,会产生大量的切削热,切屑的排出方向与钻头的进给方向相反,切削液需渗入钻头刃部才能润滑、冷却和辅助排屑,切削液首先应该具备良好的渗透性,并且供液方式、流量和压力也要满足要求。
在提高钻头寿命指标上,油基切削液总体好于水基切削液,水基切削液中极压微乳液最好,油基切削液中低粘度的活性硫化油是所有切削液中整体性能最好的。
由于铰削属于精加工中低速薄屑切削加工,铰孔时,应该着重考虑铰孔的尺寸精度和表面粗糙度精度两项质量指标以及铰刀保持精度的使用寿命指标。
在控制孔径指标上,油基切削液均使孔径扩大,矿物油使孔径扩大量较大,极压切削油较小,活性硫化、氯化油最小;水基切削液使孔径减小,含硫极压微乳液、微乳液使孔径减少最大,乳化液居中,合成切削液最小。
鉴于此,为了控制铰孔尺寸,使用新铰刀时,使用水基切削液,使孔不易扩大,当铰刀磨损至一定程度时,可以使用油基切削液,使孔径稍微扩大。
在降低铰孔的表面粗糙度这一指标上,使用水基切削液要比使用油基切削液效果好。
油基切削液中,活性硫化氯化油效果最好,然后依次是含氯极压油、混合矿物油,纯矿物油最差;水基切削液中,乳化液、微乳液、含硫极压微乳液的效果基本相同,合成切削液最差。
在控制铰刀使用寿命方面,油基切削液中的非活性极压切削油和减摩切削油性能最好;水基切削液中,合成切削液最差。
除浮动镗刀外,车削内孔与镗削都属于单刃切削,散热条件比外圆差,切削液使用时与钻孔和铰孔一样,要适当增加流量和压力。
4.螺纹加工
螺纹加工属于成形加工,攻、套螺纹时,属于多刃低速切削,刀刃被切削材料所包围,切削力矩大,排屑较困难,热量不能及时由切屑带走,切屑碎片挤塞并且容易产生振动,刀具容易磨损。
尤其攻螺纹时切削条件更苛刻:排屑空间狭小、切屑不易折断和流出,攻丝和排屑产生较大的切削力、摩擦力,极易导致丝锥崩刃和折断。
要求切削液同时具备较低的摩擦系数和较好的渗透性,以减少刀具的摩擦阻力和延长刀具使用寿命。
切削黑色金属材料时,一般应选用硫、氯添加剂成分较多,低粘度,渗透性好的油基切削液。
使用高速钢低速车削螺纹时,其切削液与攻、套螺纹选用的原则相同。
使用硬质合金刀具车削螺纹,其切削速度快,冲击力大,切削温度高,切削刃面积小,承受的切削力大,螺纹牙型精度要求高,不易产生积屑瘤和鳞刺等影响螺纹表面质量的问题,对刀具的使用寿命指标要求高,要求切削液冷却、润滑、渗透性能同时具备,应选用含极压添加剂的水基切削液为宜。
5.不同刀具材料
很多时候,为了避免刀具受热不均导致破损,使用硬质合金刀具切削时,习惯采用干切削。
但在数控机床上,从效率、综合成本、加工质量全面衡量,最好使用切削液。
使用硬质合金刀具加工时,切削速度相对较高时,一般使用水基切削液,要大流量连续使用并注意观察,保证喷嘴始终对准切削位置;使用高速钢刀具切削,切削速度较低时,一般使用以润滑为主的油基切削液。
使用陶瓷刀具、金属陶瓷刀具、金刚石和立方氮化硼刀具主要适用于高速切削、干切削以及硬切削等加工方式,可以不使用切削液。
有时,为了避免切削温度过高,使用这些刀具多数情况下也要使用切削液。
由于切削速度高,使用水基切削液为宜。
6.结语
在数控切削过程中,合理使用切削液对提高加工效率、改善加工质量、延长刀具使用寿命以及降低综合成本具有十分重要的作用。
但是切削液在使用过程中会对加工者造成健康危害;废液处理和排放也会对环境造成污染。
针对绿色制造的提出,加工者应该探索不用切削液或少用切削液完成加工任务,相关企业和科研机构也应不断研发性能更好、绿色环保、通用性好和经济性好的切削液,来满足切削液使用者的要求。
机床的管理者、加工工艺技术人员和机床操作者应该及时跟踪、关注,并积极推广和使用新型环保切削液以及新型冷却润滑技术,以便能够选用更合适的切削液及技术应用于生产实际中。