不同材质选择切削液(油)的标准
切削液的选用原则

切削液的选用原则
切削液的选用原则
切削液的主要作用为润滑作用和冷却作用,加入特殊添加剂后,还可以起到清洗和防锈的作用,以保护机床、刀具、工件等不被周围介质腐蚀。
切削液的种类繁多,性能各异,在加工过程中应根据加工性质、工艺特点、工件和刀具材料等具体条件合理选用。
以下是一般选用的原则。
1、根据加工性质选用
(1)粗加工由于加工余量和切削用量均较大,因此在切削过程中产生大量的切削热易使刀具迅速磨损,这时应降低切削区域温度,所以应选择以冷却作用为主的乳化液或合成切削液。
(2)精加工为了减少、工件与刀具间的摩擦,保证工件地加工精度和表面质量,应润滑性能较好的极压切削油或高浓度极压乳化液。
(3)半闭式加工如钻孔、铰孔和深孔加工,排屑、散热条件均非常差,不仅使刀具磨损,容易退火,而且切屑容易拉毛工件已加工表面。
为此,须选用粘度较小的极压乳化液或极压切削油,并加大切削液的压力和流量,这样,一方面进行冷却、润滑,另一方面可将部分切屑冲刷出来。
2、根据工件材料用
(1)一般,粗加工时选用乳化液;精加工时,选硫化乳化液。
(2)加工铸铁、铸铝等脆性金属,为了避免细小切削堵塞冷却系统或粘附在机床上难以清除,一般不用切削液,但在精加工时,为提高工件表面加工质量,可选用润滑性好、粘度小的煤油或7﹪~10﹪的乳化液。
(3)加工有色金属或铜合金时,不宜采用含硫的切削液,以免腐蚀工件。
(4)加工镁合金时,不以用切削液,以免燃烧起火。
必要时,可用压缩空气冷却。
(5)加工难加工材料,如不锈钢、耐热钢等,应选用10﹪~15﹪的极压切削油或极压乳化液。
切削液标准号

切削液标准号摘要:1.切削液的概述2.切削液的分类3.切削液的作用4.切削液的选择5.切削液的使用与维护6.切削液的环保问题及发展趋势正文:切削液是一种用于金属加工过程中的润滑、冷却和清洁的液体。
它可以有效地降低刀具与工件之间的摩擦,提高加工效率,延长刀具寿命,并保持工件和刀具的清洁。
切削液的选择和使用对于金属加工的精度、效率和刀具寿命具有重要意义。
切削液可以根据其成分和性能分为以下几类:1.油性切削液:主要由矿物油、动植物油和酯类等油性物质组成,具有良好的润滑性能。
2.乳化液:油性切削液与水混合形成的乳状液体,兼具油性和水性的优点。
3.合成切削液:以合成油为基础,加入各种添加剂,具有良好的润滑、冷却和清洗性能。
4.极压切削液:在合成切削液的基础上加入极压添加剂,能在高温、高压下提供更好的润滑性能。
切削液的主要作用包括:1.润滑作用:降低刀具与工件之间的摩擦,减少刀具磨损,提高加工精度。
2.冷却作用:吸收加工过程中产生的热量,降低刀具和工件的温度,防止刀具磨损和工件变形。
3.清洗作用:清除刀具和工件表面的切屑、灰尘等杂物,保持刀具和工件的清洁。
选择切削液时需要考虑以下因素:1.加工材料:根据加工材料的性质选择合适的切削液。
2.刀具材料:切削液应与刀具材料相容,避免发生化学反应导致刀具磨损。
3.加工条件:根据加工温度、压力等条件选择合适的切削液。
4.环保要求:选择无毒、无害、易生物降解的切削液,以减少对环境和人体的影响。
在使用切削液过程中,需要注意以下几点:1.保持切削液的清洁,定期过滤、排放和添加新液。
2.合理控制切削液的浓度,避免浓度过高或过低影响加工效果。
3.不同种类切削液不要混合使用,以免发生化学反应。
随着环保意识的提高,切削液的环保问题越来越受到重视。
切削液知识与选用

切削液知识与选用一、前言合理选用冷却润滑液,可以有效地减小切削过程中的摩擦,改善散热条件,而降低切削力,切削温度和刀具磨损,提高刀具耐用度,切削效率和已加工表面质量及降低产品的加工成本。
随着科学技术和机械加工工业的不断发展,特别足大量的难切削材料的应用和对产品零件加工质量要求越来越高,这就给切削加工带来了难题。
为了使这些难题获得解决,除合理选择别的切削条件外,合理选择切削液也尤为重要。
二.切削的分类1.水溶液:其主要成分是水。
由于水的导热系数是油的导热系数三倍,所以它的冷却性能好。
在其中加入一定量的防锈和汕性添加剂,还能起到一定的防锈和润滑作用。
2.乳化液:(1)普通乳化液:它是由防锈剂,乳化剂和矿物油配制而成。
清洗和冷却性能好,兼有防锈和润滑性能。
(2)防锈乳化液:在普通乳化液中,加入大量的防锈剂,其作用同上,用于防锈要求严格的工序和气候潮湿的地区。
(3)极压乳化液:在乳化液中,添加含硫,磷,氯的极压添加剂,能在切削时的高温,高压下形成吸附膜,起润滑作用。
3.切削油:(1)矿物油:有5#、7#、10#、20#、30#机械油和柴油,煤油等,适用于一般润滑。
(2)动,植油及复合油:有豆油、菜子油、棉子油、蓖麻油、猪油等。
复合油是将动、植、矿三种油混合而成。
它具有良好地边界润滑。
(3)极压切削油:它是以矿物油为基础,加入油性,极压添加剂和防锈剂而成。
具有动,植物油良好地润滑性能和极压润滑性能。
三.切削液的作用1.冷却作用:它可以降低切削温度,提高刀具耐用度和减小工件热变形,保证加工质量。
一般的情况下,可降低切削温度50~150℃。
2.润滑作用:可以减小切屑与前刀面,工件与刀具后刀面的摩擦,以降低切削力,切削热和限制积屑瘤和鳞刺的产生。
一般的切削油在200℃左右就失去润滑能力。
如加入极压添加剂,就可以在高温(600~1000℃)、高压(1470~1960MPa)条件下起润滑作用。
这种润滑叫做极压润滑。
切削液的选用

不能使用水基切削液,以免引起燃烧
刀具材料
高速钢刀具
热硬性差,一般应使用切削液
硬质合金刀具
热硬性好,耐热、耐磨,一般不用切削液,必要时可使用低浓度的乳化液或合成切削液,但必须连续、充分浇注,以免刀片因冷热不均匀,产生较大内应力而导致破裂
加工方法
钻孔(尤其是钻深孔)、铰孔、攻螺纹、拉削等加工
因工具与已加工表面的摩擦严重,宜采用乳化液、极压乳化液、极压切削油,并充分浇注
使用螺纹刀具、齿轮刀具及成形刀具切削
刀具价格较贵,刃磨困难,要Байду номын сангаас刀具寿命高,宜采用极压切削油、硫化切削油等
磨削
因其加工时温度很高,且会产生大量的细屑及脱落的磨粒,容易堵塞砂轮和使工件烧伤,要选用冷却作用好、清洁能力强的切削液,如合成切削液和低浓度乳化液
磨削不锈钢、高温合金
应选用润滑性能较好的极压型合成切削液和极压乳化液
切削液的选用
选用依据
加工条件
切削液选用原则
工件材料
切削钢等塑性材料
需用切削液
切削铸铁等脆性材料
因使用切削液的作用不明显,且会弄脏工作场地和使碎屑黏附在机床导轨与滑板间造成阻塞和擦伤,故一般不使用切削液
切削高强度钢、高温合金等难切削材料
选用极压切削油或极压乳化液
切削铜、铝及其合金
因硫对其有腐蚀作用,故不能使用含硫的切削液
加工要求
粗加工
金属切除量大,切削温度高,应选用冷却作用好的切削液
精加工
为保证加工质量,宜选用润滑作用好的极压切削液
不同金属切削条件下切削液的选择
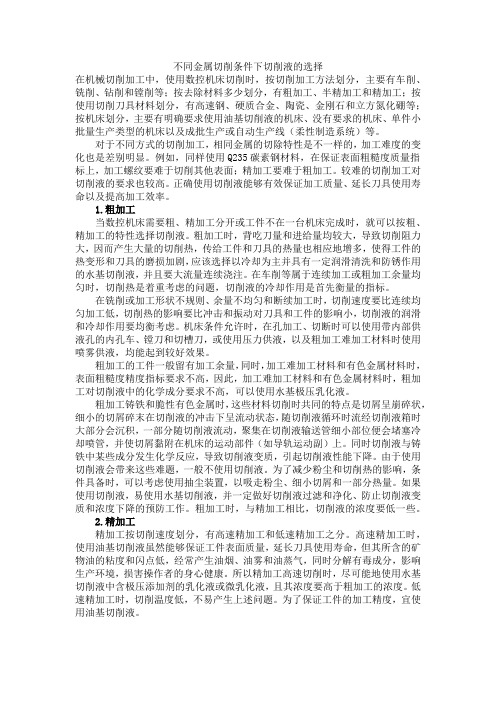
不同金属切削条件下切削液的选择在机械切削加工中,使用数控机床切削时,按切削加工方法划分,主要有车削、铣削、钻削和镗削等;按去除材料多少划分,有粗加工、半精加工和精加工;按使用切削刀具材料划分,有高速钢、硬质合金、陶瓷、金刚石和立方氮化硼等;按机床划分,主要有明确要求使用油基切削液的机床、没有要求的机床、单件小批量生产类型的机床以及成批生产或自动生产线(柔性制造系统)等。
对于不同方式的切削加工,相同金属的切除特性是不一样的,加工难度的变化也是差别明显。
例如,同样使用Q235碳素钢材料,在保证表面粗糙度质量指标上,加工螺纹要难于切削其他表面;精加工要难于粗加工。
较难的切削加工对切削液的要求也较高。
正确使用切削液能够有效保证加工质量、延长刀具使用寿命以及提高加工效率。
1.粗加工当数控机床需要粗、精加工分开或工件不在一台机床完成时,就可以按粗、精加工的特性选择切削液。
粗加工时,背吃刀量和进给量均较大,导致切削阻力大,因而产生大量的切削热,传给工件和刀具的热量也相应地增多,使得工件的热变形和刀具的磨损加剧,应该选择以冷却为主并具有一定润滑清洗和防锈作用的水基切削液,并且要大流量连续浇注。
在车削等属于连续加工或粗加工余量均匀时,切削热是着重考虑的问题,切削液的冷却作用是首先衡量的指标。
在铣削或加工形状不规则、余量不均匀和断续加工时,切削速度要比连续均匀加工低,切削热的影响要比冲击和振动对刀具和工件的影响小,切削液的润滑和冷却作用要均衡考虑。
机床条件允许时,在孔加工、切断时可以使用带内部供液孔的内孔车、镗刀和切槽刀,或使用压力供液,以及粗加工难加工材料时使用喷雾供液,均能起到较好效果。
粗加工的工件一般留有加工余量,同时,加工难加工材料和有色金属材料时,表面粗糙度精度指标要求不高,因此,加工难加工材料和有色金属材料时,粗加工对切削液中的化学成分要求不高,可以使用水基极压乳化液。
粗加工铸铁和脆性有色金属时,这些材料切削时共同的特点是切屑呈崩碎状,细小的切屑碎末在切削液的冲击下呈流动状态,随切削液循环时流经切削液箱时大部分会沉积,一部分随切削液流动,聚集在切削液输送管细小部位便会堵塞冷却喷管,并使切屑黏附在机床的运动部件(如导轨运动副)上。
五金加工切削液的选择标准

惠州五金冲压厂,五金加工切削液的选择标准
在五金加工的过程中会使用到各种切削液,惠州五金冲压厂经过众多生产案例的积累,熟悉各种切削液的原理和选择标准,一般来说对冲压件的生产具有冷却、润滑的作用,可根据加工要求有针对性地进行选择。
1.惠州五金冲压厂根据加工材料选择切削液:
①加工普通材料,在中低速切割时,可选用切削油、水基切削液、乳化液等
润滑性能较好的溶剂;在高速切割时,可选择冷却性能好的低浓度水基切
削液和乳化液。
②加工硬度大的材料时,对润滑和冷却的综合性能要求更高,可选用极压切
削液。
③加工塑性和脆性好的材料时,塑性好较好的选用润滑性能好的切削液,脆
性好的选用清洗性和渗透性较好的煤油或者水基切削液。
2.惠州五金冲压厂根据刀具材料选择切削液:
①当使用高速钢刀具时,如果切割的材料有很多,可采用水基切削液和乳化
液;如果切割材料比较少,可选择浓度较高,润滑性能较好的乳化液。
②当使用硬质合金或者金刚石刀具时,应使用低浓度切削液,持续供应,避
免刀具出现裂纹;如果加工表面要求不高,可不使用切削液。
此外,还可根据加工件的特性来一对一选择,例如钻孔、攻螺纹、拉削、铰孔时可选用乳化液和极压乳化液;齿轮形状加工时,为了保持形状和精度,应选择润滑性能好的挤压切削油或乳化液;磨削加工时,由于加工温度高,磨屑会对工件造成损伤,应选择冷却性和清洗性能耗的切削液。
以上就是惠州五金冲压厂在五金加工时针对切削液的选择方法,希望对你有帮助。
诚瑞丰冲压厂提供冲压件生产组装服务,按期输出高质量产品,欢迎联系合作。
切削液的正确选用

切削液的正确选用正确的选用切削液,可以提高金属切削的生产率,保证被加工材料的加工精度。
每种切削液都有各自的优缺点,各有各的用途。
因此在加工不同的金属材料时需要选用不同的切削液,这样才能使切削液和刀具有效地结合到金属切削加工中。
今天,金属切削行业已进入了系统解决方案的年代。
过去那种镶嵌法选用的工艺现已被简化,如果还不能称为“科学”的话,至少可称为“技术”。
各种等级的刀具、涂层及断屑装置等因素都应结合在一起统筹考虑和设计,使其适应更大的应用范围和工件材料,更有效地进行加工。
然而有时候,金属切削加工中有一个问题往往容易忽略,那就是如何适当地选用切削液。
将今天的系统方法应用于金属切削加工,需要正确地使用合适于金属加工的切削液,这与其它因素一样,已成为解决方案中的同样重要部分。
实际上,现在至少有一家公司正在将切削液和刀具有效地结合到金属切削系统之中。
当你选用以后的切削液时,应考虑到以下一些因素:四个关键问题在选用切削液时,有四大关键问题需要考虑,这些问题是:1.你在切削加工中加工的是什么材料?2.在你使用的切削液中含有哪些化学成分?3.你现在使用的是什么切削液?4.有哪些切削液可供你选用?5.你喜欢哪种切削液?6.你在切削加工的是什么材料?第一个问题是:你在切削加工中加工的是什么材料?回答这个问题往往是最困难的,因为在正常的情况下,大多数车间内所加工的工件材料是各种各样的。
如果答案毫不含糊的说是“铝”或“不锈钢”或“铸铁”,切削液的选用就可能相当简单和直截了当。
可惜在大批量生产的工厂,这样的情况极少。
如果所切削加工的绝大部分零件为铝或有色金属,那末切削加工时就必须采用非污染型切削液。
一般来说,所使用的切削液为加有特殊成分的半合成液体,可防止有色金属工件的双金属腐蚀和污染。
如果有色金属占绝大部分,选用通用的半合成或混合切削液比较经济。
第二个问题是:在你的切削液中含有哪些化学成分?这个问题可能涉及到切削液使用的成败原因。
切削液参数
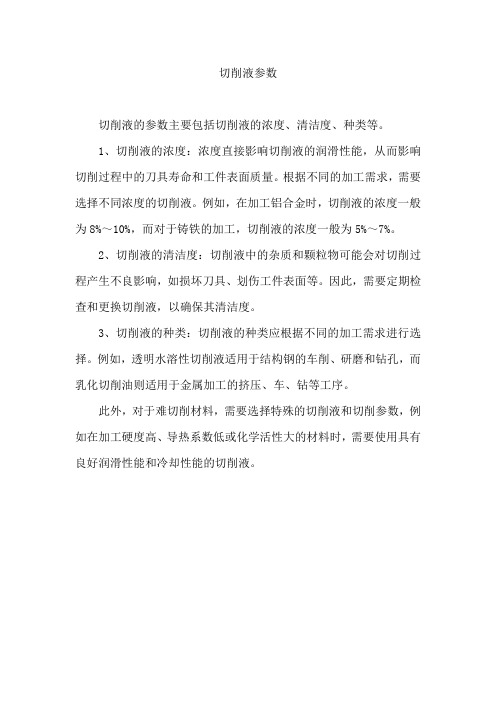
切削液参数
切削液的参数主要包括切削液的浓度、清洁度、种类等。
1、切削液的浓度:浓度直接影响切削液的润滑性能,从而影响切削过程中的刀具寿命和工件表面质量。
根据不同的加工需求,需要选择不同浓度的切削液。
例如,在加工铝合金时,切削液的浓度一般为8%~10%,而对于铸铁的加工,切削液的浓度一般为5%~7%。
2、切削液的清洁度:切削液中的杂质和颗粒物可能会对切削过程产生不良影响,如损坏刀具、划伤工件表面等。
因此,需要定期检查和更换切削液,以确保其清洁度。
3、切削液的种类:切削液的种类应根据不同的加工需求进行选择。
例如,透明水溶性切削液适用于结构钢的车削、研磨和钻孔,而乳化切削油则适用于金属加工的挤压、车、钻等工序。
此外,对于难切削材料,需要选择特殊的切削液和切削参数,例如在加工硬度高、导热系数低或化学活性大的材料时,需要使用具有良好润滑性能和冷却性能的切削液。
- 1、下载文档前请自行甄别文档内容的完整性,平台不提供额外的编辑、内容补充、找答案等附加服务。
- 2、"仅部分预览"的文档,不可在线预览部分如存在完整性等问题,可反馈申请退款(可完整预览的文档不适用该条件!)。
- 3、如文档侵犯您的权益,请联系客服反馈,我们会尽快为您处理(人工客服工作时间:9:00-18:30)。
不同材质选择切削液(油)的标准
福邦润滑油更新时间:2020.10.16
合理使用切削液能有效地减小切削力、降低切削温度、减小加工系统热变形、延长刀具使用寿命和改善加工表面质量。
选择切削液要根据加工材质及实际工况而定,切削加工的具体情况和要求不同,切削加工的难易程度就不同,使用的切削液也随之改变。
粗加工时,要求刀具的磨损慢和加工生产率高;精加工时,要求工件有高的精度和较小的表面粗糙度。
➢对于难加工的材料应选用活性高、含抗磨、极压添加剂的切削液;对于容易加工的材料则选用不含极压添加剂的切削液。
➢切削有色金属和轻金属时,切削力和切削温度都不高,可选用矿物油和高浓
度乳化液。
切削合金钢时,如果切削量较低、表面粗糙度要求较小(如拉
削以及螺纹切削),此时需要优异润滑性能的切削液,可选用极压切削油
和高浓度乳化液。
切削铸铁与青铜等脆性材料时,切削中常形成崩碎切屑,
容易随切削液到处流动,流入机床导轨之间造成部件损坏,可使用冷却和清洗性能好的低浓度乳化液。
➢较高切削速度的粗加工中(例如:车削、铣削、钻削),要求切削液具有良好的冷却性能,这时应选用水基切削液以及低浓度乳化液。
➢在一些精密的高强度加工中(例如:拉削、攻丝、深孔钻削、齿轮加工),此时需要切削液具有优异的润滑性能,可选用极压切削油和高浓度乳化液。
➢工具钢刀具:此类刀具的耐热温度在 200 — 300 o C ,耐热性能差,高温下会失去硬度,因此要求采用冷却性能好的切削液,以低浓度乳化液为宜。
➢高速钢刀具:高速粗切削时,切削量大,产生大量的切削热,为避免工件烧伤而影响加工质量,应采用冷却性好的水基切削液;如果用高速钢刀具进行中、低速的精加工时,为减小刀具和工件的摩擦黏结,抑制切削瘤生成,提高加工精度,一般采取油基切削液或高浓度乳化液。
➢硬质合金刀具:此类刀具熔点和硬度较高,化学和热稳定性较好,切削和耐磨性能比高速钢刀具要好的多。
在一般的加工中可使用油基切削液。
如果是重切削时,切削温度很高,容易极快磨损刀具,此时应使用流量充足的冷却润滑液,以 3% — 5% 的乳化液为宜(采用喷雾冷却,效果更好)。
➢陶瓷刀具、金刚石刀具、立方氮化硼刀具:这些刀具硬度和耐磨性较高,切削时一般不使用切削液,有时也可使用水基切削液。