切削液和磨削液的正确选用
切削液的合理选用

切削液的合理选用随着技术的发展,零件的加工精度要求越来越高,切削加工越来越困难。
为了满足加工质量要求,应合理设计加工工艺,选择合适切削用量,选择合理切削液。
加工过程中使用合适的切削液,能有效降低切削温度,提高切削加工质量,所以合理选用切削液是制定加工工艺的一个重要过程。
生产中使用的切削液种类较多,各种切削液的作用各不相同,每种切削液一般只适用于一种或少数几种加工过程。
批量生产中,因需要的切削液数量多,种类少,可查有关手册配制所需切削液,或定制所需切削液。
但单件小批生产时,因工件材料、所用刀具等变化大,所以需要的切削液种类多,数量少,因此在各种切削液中选择一种合适的切削液以满足加工需要是金属切削过程中的一个重要环节。
切削液应具备的作用研究表明,选用合适的金属切削液,能降低切削温度60~150℃,降低表面粗糙度1~2级,减少切削阻力15%~30%,成倍地提高刀具和砂轮的使用寿命。
故为保证产品质量,提高生产效率和刀具耐用度,切削液应具备以下几方面作用。
1 切削液应具备冷却作用加工中因摩擦、变形等原因而产生大量的切削热,形成较高的切削温度而影响加工过程,为了降低切削温度,切削液应有冷却作用。
切削液的冷却作用主要是通过传导、对流和汽化,带走切屑、刀具和工件上的热量,从而起到冷却作用。
2 切削液应具备润滑作用加工过程中,为了减少刀具与工件、刀具与切屑之间的摩擦作用,切削液应有良好的润滑作用。
切削液在刀具前刀面、后刀面与工件之间形成一层润滑膜,减少或避免刀具与工件或切屑间的直接接触,降低摩擦而减轻刀具磨损;此外,切削液形成的润滑膜能增大剪切角,减小切屑变形从而减小切削力,降低切削功率消耗。
3 切削液应具备清洗和排屑作用切削过程中产生的切屑和粉末,如果粘附在工件、刀具或机床上,可能磨损机床导轨,划伤工作表面,造成刀具磨损,为消除此不良影响,切削液应具有清洗和排屑作用。
切削液的清洗和排屑作用主要是使切削液具有一定压力,将切屑、粉末冲走,防止切屑或粉末研伤加工表面和机床导轨。
切削液,正确认识切削液,正确使用切削液

切削液,正确认识切削液,正确使用切削液
含油的产品很难和工业用水混合和乳化,尤其是水质硬的时候。在某些情况下,需 要利用混合设备或所用时间的技巧来达成令人满意的混合。半合成和合成切削液更 容易溶于水并且更容易在水中分散。由于含油的产品必须使用大量的乳化剂,其易 于吸收杂质油。一些剔除杂质油的循环系统也去掉了部分应该留在冷却液中的油。 因此,在循环使用包含溶解油或者半合成混合切削液时,由于在去除杂质油的同时 也去掉了有用的油性成分,而人为地增加了成本。
扫描关注
切削液,正确认识切削液,正确使用切削液
合成切削液,不含油,但是含有化学润滑剂和其它添加剂,以提供防腐蚀,生物控 制,湿润和消泡等性能。无论哪种类型的切削液,所必须定期进行的最重要的维护 项目是测量切削液的浓度。切削液浓度必须定期记录并且经常维护。切削液浓度通 常为容积的3%-10%。
切削液,正确认识切削液,正确使用切削液
切削液,正确认识Βιβλιοθήκη 削液,正确使用切削液金属离子会对乳化剂以及乳化剂与油的结合起到负面影响。弱乳化系统通常会引入 金属微粒将它们带入加工过程中。这些金属微粒会影响加工质量,对刀具寿命和表 面精度产生负面影响。另外,含油的切削液产品通常不能使用微细过滤的方法进行 精处理,因为这样的过滤会在去除掉杂质和无用的成分的同时去除了有用的油性成 分。
大部分切削液都可以通过预混合或者通过使用比例调节器与水或是现有的溶液进行混合。自动 的切削液比例调节器可以保证浓度的一致。不论使用哪种方法,都可以使切削液保持最佳水平 ,并且如果细致的记录了切削液和水的添加剂量,就可以跟踪所消耗的成本。然而,通过持续 的使用与循环,一些冷却液会选择性损失添加剂,这会引起一些严重的问题,例如,腐蚀,润 滑性降低,起泡,微生物生长引起的气味和刀具磨损加剧。含有多种功能成分的切削液配方一 般所损失添加剂会少一些。
切削液及其选用分析

切削液及其选用分析一、前言合理选用冷却润滑液,可以有效地减小切削过程中的摩擦,改善散热条件,而降低切削力,切削温度和刀具磨损,提高刀具耐用度,切削效率和已加工表面质量及降低产品的加工成本。
随着科学技术和机械加工工业的不断发展,特别足大量的难切削材料的应用和对产品零件加工质量要求越来越高,这就给切削加工带来了难题。
为了使这些难题获得解决,除合理选择别的切削条件外,合理选择切削液也尤为重要。
二.切削的分类1.水溶液:其主要成分是水。
由于水的导热系数是油的导热系数三倍,所以它的冷却性能好。
在其中加入一定量的防锈和汕性添加剂,还能起到一定的防锈和润滑作用。
2.乳化液:(1)普通乳化液:它是由防锈剂,乳化剂和矿物油配制而成。
清洗和冷却性能好,兼有防锈和润滑性能。
(2)防锈乳化液:在普通乳化液中,加入大量的防锈剂,其作用同上,用于防锈要求严格的工序和气候潮湿的地区。
(3)极压乳化液:在乳化液中,添加含硫,磷,氯的极压添加剂,能在切削时的高温,高压下形成吸附膜,起润滑作用。
3.切削油:(1)矿物油:有5#、7#、10#、20#、30#机械油和柴油,煤油等,适用于一般润滑。
(2)动,植油及复合油:有豆油、菜子油、棉子油、蓖麻油、猪油等。
复合油是将动、植、矿三种油混合而成。
它具有良好地边界润滑。
(3)极压切削油:它是以矿物油为基础,加入油性,极压添加剂和防锈剂而成。
具有动,植物油良好地润滑性能和极压润滑性能。
三.切削液的作用1.冷却作用:它可以降低切削温度,提高刀具耐用度和减小工件热变形,保证加工质量。
一般的情况下,可降低切削温度50~150℃。
2.润滑作用:可以减小切屑与前刀面,工件与刀具后刀面的摩擦,以降低切削力,切削热和限制积屑瘤和鳞刺的产生。
一般的切削油在200℃左右就失去润滑能力。
如加入极压添加剂,就可以在高温(600~1000℃)、高压(1470~1960MPa)条件下起润滑作用。
这种润滑叫做极压润滑。
常用的切削液种类及选用方法
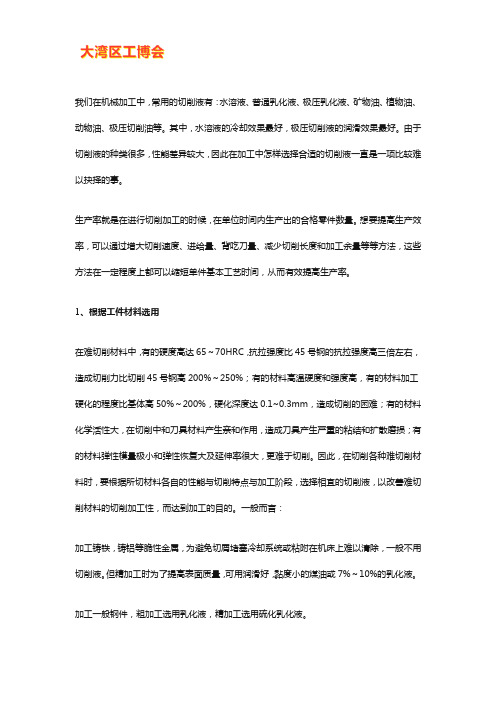
我们在机械加工中,常用的切削液有:水溶液、普通乳化液、极压乳化液、矿物油、植物油、动物油、极压切削油等。
其中,水溶液的冷却效果最好,极压切削液的润滑效果最好。
由于切削液的种类很多,性能差异较大,因此在加工中怎样选择合适的切削液一直是一项比较难以抉择的事。
生产率就是在进行切削加工的时候,在单位时间内生产出的合格零件数量。
想要提高生产效率,可以通过增大切削速度、进给量、背吃刀量、减少切削长度和加工余量等等方法,这些方法在一定程度上都可以缩短单件基本工艺时间,从而有效提高生产率。
1、根据工件材料选用在难切削材料中,有的硬度高达65~70HRC,抗拉强度比45号钢的抗拉强度高三倍左右,造成切削力比切削45号钢高200%~250%;有的材料高温硬度和强度高,有的材料加工硬化的程度比基体高50%~200%,硬化深度达0.1~0.3mm,造成切削的困难;有的材料化学活性大,在切削中和刀具材料产生亲和作用,造成刀具产生严重的粘结和扩散磨损;有的材料弹性模量极小和弹性恢复大及延伸率很大,更难于切削。
因此,在切削各种难切削材料时,要根据所切材料各自的性能与切削特点与加工阶段,选择相宜的切削液,以改善难切削材料的切削加工性,而达到加工的目的。
一般而言:加工铸铁,铸铝等脆性金属,为避免切屑堵塞冷却系统或粘附在机床上难以清除,一般不用切削液。
但精加工时为了提高表面质量,可用润滑好,黏度小的煤油或7%~10%的乳化液。
加工一般钢件,粗加工选用乳化液,精加工选用硫化乳化液。
加工有色金属或铜合金,不宜用含硫切削液,以免腐蚀工件。
可选用一般乳化液或切削油。
加工镁合金时,不能用切削液,否则会燃烧起火。
加工难切削工件,如不锈钢,耐热钢及含有铬,镍,钼,锰,钛,铌,钨等元素的材料时,因所含硬质点多,机械擦伤作用大,导热系数低,切削热不易散出,往往难以切削。
应选用10%~15%的极压切削油或极压乳化液。
2、根据刀具材料选用工具钢刀具:其耐热温度约在200~300℃之间,只能适用于一般材料的切削,在高温下会失去硬度。
磨削液的选择
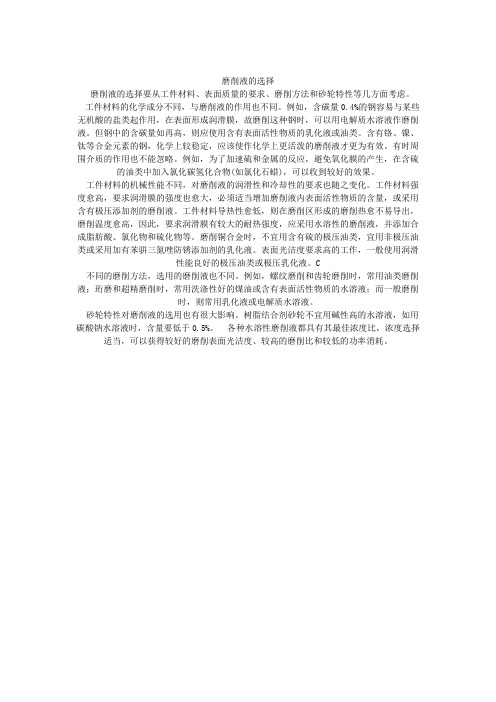
磨削液的选择磨削液的选择要从工件材料、表面质量的要求、磨削方法和砂轮特性等几方面考虑。
工件材料的化学成分不同,与磨削液的作用也不同。
例如,含碳量0.4%的钢容易与某些无机酸的盐类起作用,在表面形成润滑膜,故磨削这种钢时,可以用电解质水溶液作磨削液。
但钢中的含碳量如再高,则应使用含有表面活性物质的乳化液或油类。
含有铬、镍、钛等合金元素的钢,化学上较稳定,应该使作化学上更活泼的磨削液才更为有效。
有时周围介质的作用也不能忽略。
例如,为了加速硫和金属的反应,避免氧化膜的产生,在含硫的油类中加入氯化碳氢化合物(如氯化石蜡),可以收到较好的效果。
工件材料的机械性能不同,对磨削液的润滑性和冷却性的要求也随之变化。
工件材料强度愈高,要求润滑膜的强度也愈大,必须适当增加磨削液内表面活性物质的含量,或采用含有极压添加剂的磨削液。
工件材料导热性愈低,则在磨削区形成的磨削热愈不易导出,磨削温度愈高,因此,要求润滑膜有较大的耐热强度,应采用水溶性的磨削液,并添加合成脂肪酸、氯化物和硫化物等。
磨削铜合金时,不宜用含有硫的极压油类,宜用非极压油类或采用加有苯骈三氮唑防锈添加剂的乳化液。
表面光洁度要求高的工作,一般使用润滑性能良好的极压油类或极压乳化液。
C不同的磨削方法,选用的磨削液也不同。
例如,螺纹磨削和齿轮磨削时,常用油类磨削液;珩磨和超精磨削时,常用洗涤性好的煤油或含有表面活性物质的水溶液;而一般磨削时,则常用乳化液或电解质水溶液。
砂轮特性对磨削液的选用也有很大影响。
树脂结合剂砂轮不宜用碱性高的水溶液,如用碳酸钠水溶液时,含量要低于0.5%。
各种水溶性磨削液都具有其最佳浓度比,浓度选择适当,可以获得较好的磨削表面光洁度、较高的磨削比和较低的功率消耗。
切削液及其选用分析

切削液及其选用分析一、前言合理选用冷却润滑液,可以有效地减小切削过程中的摩擦,改善散热条件,而降低切削力,切削温度和刀具磨损,提高刀具耐用度,切削效率和已加工外表质量及降低产品的加工成本。
随着科学技术和机械加工工业的不断发展,特别足大量的难切削材料的应用和对产品零件加工质量要求越来越高,这就给切削加工带来了难题。
为了使这些难题获得解决,除合理选择别的切削条件外,合理选择切削液也尤为重要。
二.切削的分类1.水溶液:其主要成分是水。
由于水的导热系数是油的导热系数三倍,所以它的冷却性能好。
在其中加入一定量的防锈和汕性添加剂,还能起到一定的防锈和润滑作用。
2.乳化液:(1)普通乳化液:它是由防锈剂,乳化剂和矿物油配制而成。
清洗和冷却性能好,兼有防锈和润滑性能。
(2)防锈乳化液:在普通乳化液中,加入大量的防锈剂,其作用同上,用于防锈要求严格的工序和气候潮湿的地区。
(3)极压乳化液:在乳化液中,添加含硫,磷,氯的极压添加剂,能在切削时的高温,高压下形成吸附膜,起润滑作用。
3.切削油:(1)矿物油:有5#、7#、10#、20#、30#机械油和柴油,煤油等,适用于一般润滑。
(2)动,植油及复合油:有豆油、菜子油、棉子油、蓖麻油、猪油等。
复合油是将动、植、矿三种油混合而成。
它具有良好地边界润滑。
(3)极压切削油:它是以矿物油为基础,加入油性,极压添加剂和防锈剂而成。
具有动,植物油良好地润滑性能和极压润滑性能。
三.切削液的作用1.冷却作用:它可以降低切削温度,提高刀具耐用度和减小工件热变形,保证加工质量。
一般的情况下,可降低切削温度50~150℃。
2.润滑作用:可以减小切屑与前刀面,工件与刀具后刀面的摩擦,以降低切削力,切削热和限制积屑瘤和鳞刺的产生。
一般的切削油在200℃左右就失去润滑能力。
如加入极压添加剂,就可以在高温(600~1000℃)、高压(1470~1960MPa)条件下起润滑作用。
这种润滑叫做极压润滑。
数控切削加工时按材料选择切削液的原则与方法
数控切削加工时按材料选择切削液的原则与方法
数控切削加工时切削液的选择十分重要,不同材料需要不同种类的切削液,选择不当可能会影响到切削加工效率和加工质量。
下面介绍按照材料选择切削液的原则和方法:
金属材料
对于铝合金、镁合金等易产生热变形的材料,可选择含硫酸盐、硼酸盐等物质的切削液,以提高切削效率。
对于高硬度的材料如不锈钢、钢铁等,可选择含磷酸盐等物质的切削液,以减少工具磨损,提高加工质量。
非金属材料
对于塑料、玻璃等非金属材料,可以使用含有机物的切削液,以避免材料的变形和熔化。
综合选择
除了考虑材料性质外,还需综合考虑切削工艺、工件加工要求等因素。
例如,对于需要高表面质量的零件,需要选择具有优异冷却和润滑性能的切削液,以保证加工质量。
总之,在选择切削液时,需要根据不同材料的特性,选择具有合适化学成分的切削液,并综合考虑切削工艺和加工要求等因素,以保证切削加工效率和加工质量。
切削液的正确选用
切削液的正确选用正确的选用切削液,可以提高金属切削的生产率,保证被加工材料的加工精度。
每种切削液都有各自的优缺点,各有各的用途。
因此在加工不同的金属材料时需要选用不同的切削液,这样才能使切削液和刀具有效地结合到金属切削加工中。
今天,金属切削行业已进入了系统解决方案的年代。
过去那种镶嵌法选用的工艺现已被简化,如果还不能称为“科学”的话,至少可称为“技术”。
各种等级的刀具、涂层及断屑装置等因素都应结合在一起统筹考虑和设计,使其适应更大的应用范围和工件材料,更有效地进行加工。
然而有时候,金属切削加工中有一个问题往往容易忽略,那就是如何适当地选用切削液。
将今天的系统方法应用于金属切削加工,需要正确地使用合适于金属加工的切削液,这与其它因素一样,已成为解决方案中的同样重要部分。
实际上,现在至少有一家公司正在将切削液和刀具有效地结合到金属切削系统之中。
当你选用以后的切削液时,应考虑到以下一些因素:四个关键问题在选用切削液时,有四大关键问题需要考虑,这些问题是:1. 你在切削加工中加工的是什么材料?2. 在你使用的切削液中含有哪些化学成分?3. 你现在使用的是什么切削液?4. 有哪些切削液可供你选用?5. 你喜欢哪种切削液?6.你在切削加工的是什么材料?第一个问题是:你在切削加工中加工的是什么材料?回答这个问题往往是最困难的,因为在正常的情况下,大多数车间内所加工的工件材料是各种各样的。
如果答案毫不含糊的说是“铝”或“不锈钢”或“铸铁”,切削液的选用就可能相当简单和直截了当。
可惜在大批量生产的工厂,这样的情况极少。
如果所切削加工的绝大部分零件为铝或有色金属,那末切削加工时就必须采用非污染型切削液。
一般来说,所使用的切削液为加有特殊成分的半合成液体,可防止有色金属工件的双金属腐蚀和污染。
如果有色金属占绝大部分,选用通用的半合成或混合切削液比较经济。
第二个问题是:在你的切削液中含有哪些化学成分?这个问题可能涉及到切削液使用的成败原因。
切削液的选用方法
合肥力恒液压系统有限公司切削液的选用标准、用途、性能特点以及使用注意事项切削液的使用,可以改善难加工材料的切削加工性,适用于铸铁、碳钢、黑色金属、不锈钢等多种金属的切削,它在许多领域有着广泛的应用。
切削液的选用标准合理使用金属切削液,既可提高金属切削液的使用效果,保证工件加工质量,又可延长刀具寿命,降低加工成本。
在机械行业中,金属切削液(以下简称切削液)被广泛应用于各种切削加工中,如车削、铣削、钻削、磨削、切齿和切螺纹等。
合理使用切削液能有效地减小切削力、降低切削温度、减小加工系统热变形、延长刀具使用寿命和改善加工表面质量。
此外,使用高性能切削液也是改善某些难加工材料切削加工性的一项重要措施。
判定切削液性能优劣:1、刀具寿命采用刀具寿命评价切削液性能时,存在的主要问题是试验结果与工厂所测数据间的相关性常常很差。
因为对直刃刀具有效的切削液对成型刃刀具并不一定同样有效,反之亦然。
此外,切屑厚度对切削液的适应性也有影响。
若在同一特定加工条件下对几种切削液进行评价则要容易得多,因为通过测定刀具锐利度的变化值可得到刀具的平均寿命。
2、光洁度表面光洁度试验不如刀具寿命试验复杂,可采用一根试验长棒,合肥力恒液压系统有限公司用同一刀具进行切削加工,通过表面粗糙度测量仪获得试验数据来评价切削液的性能优劣。
此评定试验,切削类型是很重要的。
如在平面铣削中,光洁的表面是由第二切削刃形成的,而在外圆铣削中,则是由主切削刃(轴向平行)形成新生面。
因而由一种加工方法获得的数据不能用于另一种加工的评定。
3、冷却性能采用某些专业技术测量切削液在实际加工中的冷却能力可判定其效率。
由于刀-屑界面的温度与刀具寿命有很好的相关性,因而刀具工作热电偶是一项非常有用的技术。
但其不足之处是不能区分温度降低是由于切削液的热传递还是由于加工中所产生热量少所致。
4、润滑效率切削液润滑效率的测定需采用一台机床刀具测力计。
在切削加工试验中,切削液的润滑作用降低了进刀力和切削力。
机床加工所要用到的切削液如何选用
机床加工所要用到的切削液如何选用合理选用冷却润滑液,可以有效地减小切削过程中的摩擦,改善散热条件,而降低切削力,切削温度和刀具磨损,提高刀具耐用度,切削效率和已加工表面质量及降低产品的加工成本。
随着科学技术和机械加工工业的不断发展,特别足大量的难切削材料的应用和对产品零件加工质量要求越来越高,这就给切削加工带来了难题。
为了使这些难题获得解决,除合理选择别的切削条件外,合理选择切削液也尤为重要。
.切削的分类1.水溶液:其主要成分是水。
由于水的导热系数是油的导热系数三倍,所以它的冷却性能好。
在其中加入一定量的防锈和汕性添加剂,还能起到一定的防锈和润滑作用。
2.乳化液:(1)普通乳化液:它是由防锈剂,乳化剂和矿物油配制而成。
清洗和冷却性能好,兼有防锈和润滑性能。
(2)防锈乳化液:在普通乳化液中,加入大量的防锈剂,其作用同上,用于防锈要求严格的工序和气候潮湿的地区。
(3)极压乳化液:在乳化液中,添加含硫,磷,氯的极压添加剂,能在切削时的高温,高压下形成吸附膜,起润滑作用。
3.切削油:(1)矿物油:有5#、7#、10#、20#、30#机械油和柴油,煤油等,适用于一般润滑。
(2)动,植油及复合油:有豆油、菜子油、棉子油、蓖麻油、猪油等。
复合油是将动、植、矿三种油混合而成。
它具有良好地边界润滑。
(3)极压切削油:它是以矿物油为基础,加入油性,极压添加剂和防锈剂而成。
具有动,植物油良好地润滑性能和极压润滑性能。
.切削液的作用1.冷却作用:它可以降低切削温度,提高刀具耐用度和减小工件热变形,保证加工质量。
一般的情况下,可降低切削温度50~150℃。
2.润滑作用:可以减小切屑与前刀面,工件与刀具后刀面的摩擦,以降低切削力,切削热和限制积屑瘤和鳞刺的产生。
一般的切削油在200℃左右就失去润滑能力。
如加入极压添加剂,就可以在高温(600~1000℃)、高压(1470~1960MPa)条件下起润滑作用。
这种润滑叫做极压润滑。