我国二氧化碳回收和利用现状
二氧化碳的资源化利用
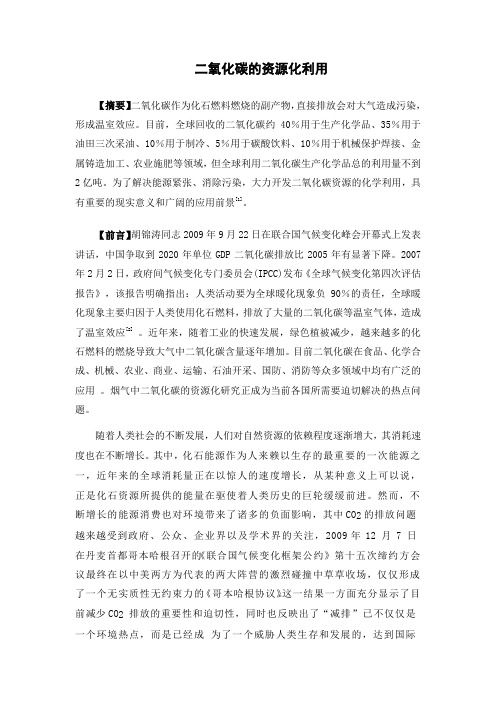
二氧化碳的资源化利用【摘要】二氧化碳作为化石燃料燃烧的副产物,直接排放会对大气造成污染,形成温室效应。
目前,全球回收的二氧化碳约40%用于生产化学品、35%用于油田三次采油、10%用于制冷、5%用于碳酸饮料、10%用于机械保护焊接、金属铸造加工、农业施肥等领域,但全球利用二氧化碳生产化学品总的利用量不到2亿吨。
为了解决能源紧张、消除污染,大力开发二氧化碳资源的化学利用,具有重要的现实意义和广阔的应用前景[1]。
【前言】胡锦涛同志2009年9月22日在联合国气候变化峰会开幕式上发表讲话,中国争取到2020年单位GDP二氧化碳排放比2005年有显著下降。
2007年2月2日,政府间气候变化专门委员会(IPCC)发布《全球气候变化第四次评估报告》,该报告明确指出:人类活动要为全球暖化现象负90%的责任,全球暖化现象主要归因于人类使用化石燃料,排放了大量的二氧化碳等温室气体,造成了温室效应[2]。
近年来,随着工业的快速发展,绿色植被减少,越来越多的化石燃料的燃烧导致大气中二氧化碳含量逐年增加。
目前二氧化碳在食品、化学合成、机械、农业、商业、运输、石油开采、国防、消防等众多领域中均有广泛的应用。
烟气中二氧化碳的资源化研究正成为当前各国所需要迫切解决的热点问题。
随着人类社会的不断发展,人们对自然资源的依赖程度逐渐增大,其消耗速度也在不断增长。
其中,化石能源作为人来赖以生存的最重要的一次能源之一,近年来的全球消耗量正在以惊人的速度增长,从某种意义上可以说,正是化石资源所提供的能量在驱使着人类历史的巨轮缓缓前进。
然而,不断增长的能源消费也对环境带来了诸多的负面影响,其中CO2的排放问题越来越受到政府、公众、企业界以及学术界的关注,2009年 12 月 7 日在丹麦首都哥本哈根召开的《联合国气候变化框架公约》第十五次缔约方会议最终在以中美两方为代表的两大阵营的激烈碰撞中草草收场,仅仅形成了一个无实质性无约束力的《哥本哈根协议》。
二氧化碳的捕集、封存及综合利用

二氧化碳的捕集、封存与综合利用前言近年来,温室效应加剧问题使环境与经济可持续发展面临严峻的挑战。
因此,引起温室效应和全球气候变化的二氧化碳的减排技术成为各国关注的焦点,如何从源头减少二氧化碳排放和降低大气中二氧化碳的含量成为挑战人类智慧的难题。
中国作为一个发展中国家,主要以煤炭的消费为主,主要的CO2排放源为燃煤的发电厂。
从总量上看,目前我国的二氧化碳排放量已位居世界第二,预计到2025年,我国的CO2总排放量很可能超过美国,位居世界第一。
因此,我国急需对所排放的二氧化碳进行捕获研究,以缓解我国的空气污染压力。
目前CO2的应用领域得到了广泛开拓,除了众所周知的碳酸饮料、消防灭火外,工业、农业、国防、医疗等部门都在使用CO2。
科学研究己经证明,CO2具有较高的民用和工业价值:以CO2为原料可合成基本化工原料;以CO2为溶剂进行超临界萃取;还可应用于食物工程、激光技术、核工业等尖端高科技领域;近年来开发出的新用途如棚菜气肥、保鲜、生产可降解塑料等也展现出良好发展前景。
[1]1.CO2捕集系统CO2捕获技术发展的方向是降低技术的投资费用和运行能耗。
依据捕获系统的技术基础和适用性,通常将火电厂CO2的捕集系统分为以下4种:燃烧后脱碳、燃烧前脱碳、富氧燃烧技术以及化学链燃烧技术。
1.1 燃烧后脱碳燃烧后脱碳是指采用适当的方法在燃烧设备后,如电厂的锅炉或者燃气轮机,从排放的烟气中脱除CO2的过程。
在燃烧后捕集技术中,由于烟气中CO2分压通常小于0. 15个大气压,因此需要与CO2结合力较强的化学吸收剂分离捕集CO2,用于CO2捕集的化学吸收剂主要是能与CO2反应生成水溶性复合物的有机醇胺类。
目前在CO2捕集方面研究和采用较多是醇胺法(MEA法)。
[2]燃烧后捕集技术是一种成熟的技术,这种技术的主要优点是适用范围广,系统原理简单,对现有电站继承性好。
但捕集系统因烟气体积流量大、CO2的分压小,脱碳的捕集成本较高。
CO2减排技术的研究及应用现状
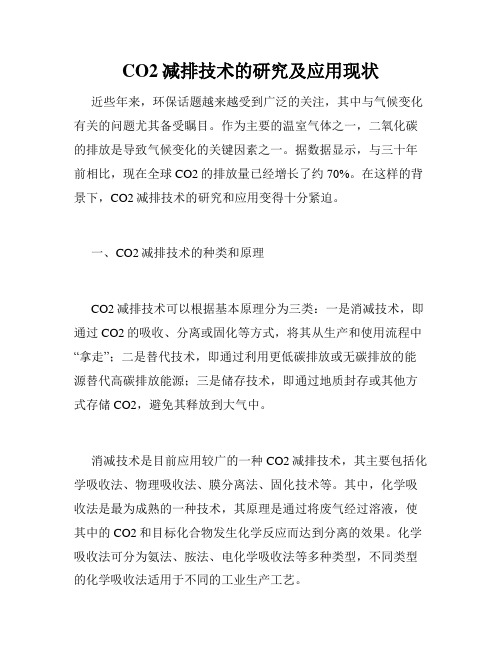
CO2减排技术的研究及应用现状近些年来,环保话题越来越受到广泛的关注,其中与气候变化有关的问题尤其备受瞩目。
作为主要的温室气体之一,二氧化碳的排放是导致气候变化的关键因素之一。
据数据显示,与三十年前相比,现在全球CO2的排放量已经增长了约70%。
在这样的背景下,CO2减排技术的研究和应用变得十分紧迫。
一、CO2减排技术的种类和原理CO2减排技术可以根据基本原理分为三类:一是消减技术,即通过CO2的吸收、分离或固化等方式,将其从生产和使用流程中“拿走”;二是替代技术,即通过利用更低碳排放或无碳排放的能源替代高碳排放能源;三是储存技术,即通过地质封存或其他方式存储CO2,避免其释放到大气中。
消减技术是目前应用较广的一种CO2减排技术,其主要包括化学吸收法、物理吸收法、膜分离法、固化技术等。
其中,化学吸收法是最为成熟的一种技术,其原理是通过将废气经过溶液,使其中的CO2和目标化合物发生化学反应而达到分离的效果。
化学吸收法可分为氨法、胺法、电化学吸收法等多种类型,不同类型的化学吸收法适用于不同的工业生产工艺。
物理吸收法则是利用介质吸附机理,将CO2从气流中吸收到介质中,并在介质中形成稳定的化合物,达到分离的效果。
物理吸收法主要包括活性碳吸附法、分子筛吸附法等,可用于工业废气的处理和二氧化碳的回收。
膜分离法则是将混有CO2的气体通过膜,在膜上形成分离层,从而实现CO2分离的技术。
膜分离法主要包括非选择性膜法、选择性膜法等。
非选择性膜法较为简单,但难以实现高纯度气体的产出;而选择性膜法可以实现高纯度气体的产出,但价格较高。
固化技术是利用CO2与某些材料之间的相互作用,将其固定在某种固体介质中,达到污染物的固化和处理的效果。
固化技术可以用于处理含CO2的水和气体,以及某些工业固体废料等。
二、 CO2减排技术的应用现状随着环保意识的不断提高,CO2减排技术的应用范围也不断扩大。
在国际上,各种CO2减排技术已经得到了广泛的应用,尤以气候变化较为敏感的西欧国家和北美国家为主。
二氧化碳回收率
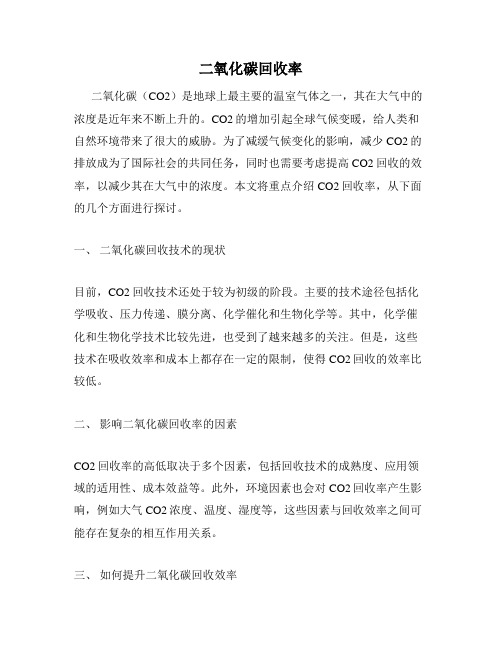
二氧化碳回收率二氧化碳(CO2)是地球上最主要的温室气体之一,其在大气中的浓度是近年来不断上升的。
CO2的增加引起全球气候变暖,给人类和自然环境带来了很大的威胁。
为了减缓气候变化的影响,减少CO2的排放成为了国际社会的共同任务,同时也需要考虑提高CO2回收的效率,以减少其在大气中的浓度。
本文将重点介绍CO2回收率,从下面的几个方面进行探讨。
一、二氧化碳回收技术的现状目前,CO2回收技术还处于较为初级的阶段。
主要的技术途径包括化学吸收、压力传递、膜分离、化学催化和生物化学等。
其中,化学催化和生物化学技术比较先进,也受到了越来越多的关注。
但是,这些技术在吸收效率和成本上都存在一定的限制,使得CO2回收的效率比较低。
二、影响二氧化碳回收率的因素CO2回收率的高低取决于多个因素,包括回收技术的成熟度、应用领域的适用性、成本效益等。
此外,环境因素也会对CO2回收率产生影响,例如大气CO2浓度、温度、湿度等,这些因素与回收效率之间可能存在复杂的相互作用关系。
三、如何提升二氧化碳回收效率为提高CO2回收的效率,需要采取一系列有效的措施。
首先,要加强相关技术的创新研究,提高吸收效率和成本效益。
其次,要推广应用这些技术,尤其是在能源、交通和工业等领域大规模应用。
此外,还需要加强全球合作,寻求更多的解决方案,制定更加合理的政策和法规,并加强环境宣传和教育工作,以提高公众的环保意识。
四、未来二氧化碳回收的前景和挑战二氧化碳回收技术的现状和成效仍然有待改进,未来的发展任务十分繁重和复杂。
其中,主要面临以下几个方面的挑战:技术水平有待提高,成本需要降低,应用领域需要扩大,政策和法规需要进一步完善,同时也需要加强公众的环保意识。
总之,二氧化碳回收率是一个重要的环保指标,其高低将直接影响到全球气候变化的趋势。
虽然目前CO2回收的技术和效率还有待改进,但是只要采取有效的措施,不断推动技术的创新和应用,加强全球合作和公众的环保教育,相信未来CO2回收的前景必然会更加美好。
工业废气二氧化碳的回收利用

工业废气二氧化碳的回收利用摘要:我国化工业发展迅速,在生产效率提升的同时,生产排放的废气总量也不断增加,其中二氧化碳是导致全球变暖的主要因素之一。
对于化工生产来说,二氧化碳可以进行回收重新利用,不但可以降低对环境的污染,同时也可以提高资源利用效率。
本文从技术角度出发,对二氧化碳的回收利用进行了简要分析。
关键词:二氧化碳;回收利用;效益引言对二氧化碳进行回收利用,是贯彻节能减排以及资源循环利用理念的要点。
想要提高二氧化碳回收利用效率,就需要结合其所具有的特征,从技术角度出发,分析回收、利用现状与要求,选择合适的技术,进行有效分离、回收,最后选择渠道进行重新利用,提高资源利用效率。
1.二氧化碳综合利用的必要性随着工业发展,我国二氧化碳的排放量也在逐年上升。
随着国际碳排放贸易(JT)和清洁开发机制(CDM)在发达国家的实施,温室气体排放的生产元素逐步由发达国家向发展中国家转移。
发达国家通过在国外获取温室气体减排抵消额的规模不断加大,速度也不断加快,我国已成为发达国家碳排放贸易交易的主要对象,而我国在2012年以后已经开始旅行高比例的温室气体减排义务,谈贸易的逐步深入、温室气体减排措施的缺乏和国内不断藏家的温室气体排放量的矛盾日趋明显,加快二氧化碳的利用研究已显得日益必要和迫切。
目前,我国二氧化碳的年排放量已超过30亿吨,占世界排放量的10%以上,居世界第二位。
搞好二氧化碳的综合利用,对发展循环经济、转变经济增长方式、建设资源节约型和环境保护型社会、环节资源短缺矛盾和环境压力、促进人与自然和谐发展具有重要意义。
2.二氧化碳回收技术在新型化工产品制造企业中的应用传统的化工产品制造业中,以耐火材料的主要原料氧化镁为例,主要生产方式为镁矿石的高温窑分解,反应为MgCO3→MgO+CO2,在生产过程中二氧化碳作为副产品与氧化镁的产量比约为1:1,回收利用效益价值显著。
目前全球范围内现有的窑分解技术主要有两种:一种是立窑(竖窑),一种是内燃式回转窑,由于技术的局限性,两种生产方式不可避免的燃料及空气均需与产品直接接触,二氧化碳产品气体因助燃空气中大量氮气及其他杂质气体的混入,以现有的二氧化碳回收技术手段而言,基本不具备回收利用的价值,大多数企业均作为工业废气利用或直接排放。
2024年二氧化碳回收市场环境分析

2024年二氧化碳回收市场环境分析1. 引言二氧化碳(CO2)的排放是导致全球气候变化的主要原因之一。
为了应对气候变化的挑战,二氧化碳回收技术逐渐兴起,并形成了一个新兴的市场。
本文将对二氧化碳回收市场的环境进行分析,包括市场规模、竞争格局、政策支持等方面。
2. 二氧化碳回收市场规模随着对气候变化问题的日益关注,二氧化碳回收市场逐渐扩大。
根据市场研究公司的数据显示,到2025年,全球二氧化碳回收市场规模预计将达到100亿美元。
随着越来越多的国家和企业投资于二氧化碳回收技术,市场规模有望进一步增长。
3. 竞争格局目前,二氧化碳回收市场存在着较为激烈的竞争。
主要的竞争对手包括科技公司、能源公司以及化工公司等。
这些公司通过技术创新和资本优势,争夺市场份额。
同时,一些创新型企业也在加入竞争,推动行业发展。
4. 政策支持政策支持是推动二氧化碳回收市场发展的重要因素之一。
许多国家都制定了相关政策来促进二氧化碳回收技术的应用和推广。
例如,一些国家提供了经济奖励和税收优惠,以鼓励企业投资于二氧化碳回收项目。
政府还加强了对二氧化碳排放的监管,为市场发展提供了合理的环境。
5. 持续创新持续创新是二氧化碳回收市场持续发展的关键。
通过不断改进技术和工艺,提高二氧化碳回收效率和成本效益,可以实现可持续发展。
同时,不断创新也可以改善产品的质量和多样性,满足消费者的需求,推动市场增长。
6. 机遇与挑战二氧化碳回收市场面临着一些机遇和挑战。
一方面,全球对气候变化问题的认识不断增强,促使政府和企业更加重视二氧化碳回收技术的应用。
另一方面,二氧化碳回收技术仍面临一些技术和经济上的挑战。
例如,高昂的成本、技术成熟度不高以及二氧化碳的回收与利用途径仍不完善。
因此,在市场发展中需要充分利用机遇,同时解决面临的挑战。
7. 总结二氧化碳回收市场作为一个新兴市场,具有巨大的潜力。
随着全球对气候变化问题的关注增加,市场规模将不断扩大。
然而,市场竞争激烈,政策支持、持续创新以及解决技术和经济上的挑战是市场发展的关键。
二氧化碳捕集和利用的技术发展

二氧化碳捕集和利用的技术发展随着全球气候变化的加剧,二氧化碳的排放问题日益引起人们的重视。
为了减缓全球气候变化的趋势,人们开始研究二氧化碳捕集和利用的技术。
这些技术不仅可以大幅减少二氧化碳的排放,还能将二氧化碳转化为有用的化学品,进一步促进环保产业的发展。
本文将详细介绍二氧化碳捕集和利用的技术发展现状及其未来展望。
一、二氧化碳捕集的技术现状1. 吸收碳捕集技术吸收碳捕集技术是目前应用最为广泛的二氧化碳捕集技术之一。
该技术利用化学吸收剂(如氨、甲醇等)与二氧化碳反应,产生二次化合物,将二氧化碳捕集起来。
这种技术操作简单、成本较低,其实际效率也较高,但排放的吸收剂可能对环境造成影响,并且再生的能量消耗大。
2.膜分离捕集技术膜分离技术是通过膜的孔隙和疏松表面来捕集二氧化碳。
这些膜通常利用聚合物、陶瓷或金属的性能,通过渗透压差将二氧化碳从气体中分离出来。
该技术操作简单,能源消耗较低,但其二氧化碳的捕集率不高,需要进一步提高膜的性能。
3.生物捕集技术生物采集技术是通过生物质转化作用(如藻类、菌类)将二氧化碳从空气中或烟气中捕集起来。
该技术不仅可以降低碳排放,还可以消耗与实际的生物量相当的二氧化碳,从而清除环境污染物。
但是这种技术的成本较高,规模较小,运营管理较为复杂。
二、二氧化碳利用技术现状随着技术的不断发展,二氧化碳不仅可以被捕集,还可以被利用。
二氧化碳利用可以将二氧化碳转化为有用的化学品,相应地减少了排放。
目前最常见的二氧化碳利用技术包括:1.合成气体制备二氧化碳可以与水反应,生成合成气体,也就是一种含有一氧化碳和氢气的气体混合物。
该混合物可以被用来生产涂料、气体燃料、化肥等等。
合成气体制备优势是二氧化碳的利用率高,且其可直接应用于工业过程。
2.生物固体制备二氧化碳可以与微生物和光合作用生物反应,将二氧化碳转化为奇异藻类、细菌、酵母和其他微生物可以生产的生物固体(如多糖、蛋白质等)。
这些生物固体可以被用于生产饲料、纺织品和生物染料等产品。
国内外二氧化碳的利用现状及进展_魏晓丹
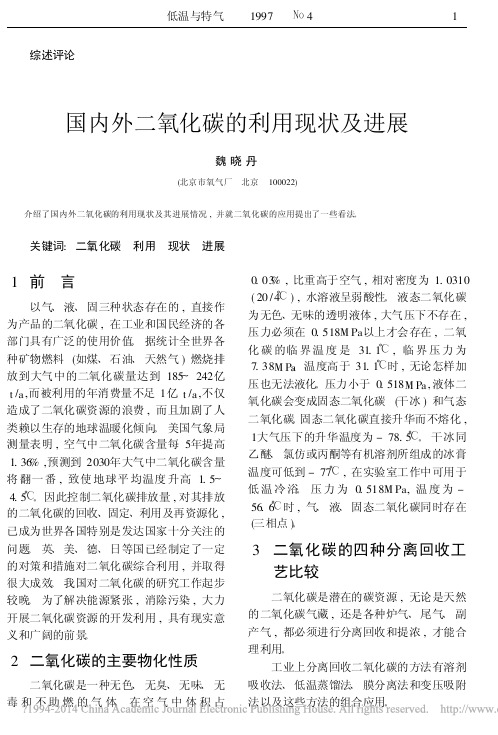
综述评论国内外二氧化碳的利用现状及进展魏晓丹(北京市氧气厂 北京 100022)介绍了国内外二氧化碳的利用现状及其进展情况,并就二氧化碳的应用提出了一些看法。
关键词:二氧化碳 利用 现状 进展1 前 言以气、液、固三种状态存在的,直接作为产品的二氧化碳,在工业和国民经济的各部门具有广泛的使用价值。
据统计全世界各种矿物燃料(如煤、石油、天然气)燃烧排放到大气中的二氧化碳量达到185~242亿t/a,而被利用的年消费量不足1亿t/a,不仅造成了二氧化碳资源的浪费,而且加剧了人类赖以生存的地球温暖化倾向。
美国气象局测量表明,空气中二氧化碳含量每5年提高1.36%,预测到2030年大气中二氧化碳含量将翻一番,致使地球平均温度升高 1.5~4.5℃。
因此控制二氧化碳排放量,对其排放的二氧化碳的回收、固定、利用及再资源化,已成为世界各国特别是发达国家十分关注的问题。
英、美、德、日等国已经制定了一定的对策和措施对二氧化碳综合利用,并取得很大成效。
我国对二氧化碳的研究工作起步较晚。
为了解决能源紧张,消除污染,大力开展二氧化碳资源的开发利用,具有现实意义和广阔的前景。
2 二氧化碳的主要物化性质二氧化碳是一种无色、无臭、无味、无毒和不助燃的气体。
在空气中体积占0.03%,比重高于空气,相对密度为1.0310 (20/4℃),水溶液呈弱酸性。
液态二氧化碳为无色、无味的透明液体,大气压下不存在,压力必须在0.518M Pa以上才会存在,二氧化碳的临界温度是31.1℃,临界压力为7.38M Pa。
温度高于31.1℃时,无论怎样加压也无法液化。
压力小于0.518M Pa,液体二氧化碳会变成固态二氧化碳(干冰)和气态二氧化碳。
固态二氧化碳直接升华而不熔化, 1大气压下的升华温度为-78.5℃。
干冰同乙醚、氯仿或丙酮等有机溶剂所组成的冰膏温度可低到-77℃,在实验室工作中可用于低温冷浴。
压力为0.518M Pa,温度为-56.6℃时,气、液、固态二氧化碳同时存在(三相点)。
- 1、下载文档前请自行甄别文档内容的完整性,平台不提供额外的编辑、内容补充、找答案等附加服务。
- 2、"仅部分预览"的文档,不可在线预览部分如存在完整性等问题,可反馈申请退款(可完整预览的文档不适用该条件!)。
- 3、如文档侵犯您的权益,请联系客服反馈,我们会尽快为您处理(人工客服工作时间:9:00-18:30)。
二 氧 化 碳 在 在 焊 接 中 的 应 用
与 手 工 电 弧 焊 相 比 . 二 氧 化 碳 气 体 保 护 焊 可 提 高
我 国 是 二 氧 化 碳 排 放 第 二 大 国 , 目前 排 放 的二 氧
化 碳 约 3 亿 吨 , 而 2 0 年 被 有 效 利 用 的 二 氧 化 碳 只 有 8 05
用 二 氧 化 碳 生产 降 解 塑 料 和 碳 酸 二 甲酯 技 术 ,被 誉 为 实现 二 氧化 碳 变废 为 宝 的 绿 色 化 工 科 技 ” ,这 些 技 术 目前 已 在 我 国 获 得 突 破 并 实 现 了工 业 化 生 产 。 据 预 测 ,被 誉 为 有机 合 成 “ 基 石 ”的 碳 酸 二 甲酯 今 新
.
并 因此 导 致 了温 室效 应 以及 引 发 了一 系列 与人 类 生 截 至2 0 年 全 世 界 二 氧 化 碳 排 放量 至 少在2 O 06 7 亿
2
、
二氧 化 碳 生产 可 降 解 塑料 和 碳 酸 二 甲酯
活 环 境 紧 密相 关 的 问题 ,严 重地 威 胁 着人 类 的 生存 。
二 氧化 碳 在 碳酸 饮 料 中 的利 用
与 传 统 的 机 械 冷 藏 相 比 .二 氧 化 碳 冷 冻 保 鲜 不 仅
2 0 年 我 国 碳 酸 型 饮 料 产 量 近5 0 万 吨 ,按 平 均 05 00
强 国 = 翥 化 碳 回 收 和 利 用 瑰 爿 犬
苏 元 伟 ’ 任 刚
( 1天 津 滨 海 供 热 有 限 公 司 天 津 3 0 5 0 4 6,2天 津 华 粲 实 业 有 限 公 司 天 津 3 0 4 ) 00 2
内 容 摘 要 :通 过 我 国 二 氧 化 碳 的 利 用 现 状 及 未 来 需 求 状 况 , 阐 述 了 利 用 科 技 创 新 研 发 解 决 二 氧 化 碳 变废 为宝 的途 径 。 关 键词 二 氧 化 碳 利 用 现 状 进 展 文 献 识 别 码 :A 中 图 分 类 号 :X 0 71
后 每 年 的 需 求 增 长 将 超 过 2 % , 到 2 2 年 我 国 的 碳 酸 O 0O 二 甲 酯 产 能 达  ̄ 4 0 吨 。 因 此 这 ~ 领 域 对 二 氧 化 碳 的 J l0 万
用 的 ,可 生 产 化 工 新 原 料 以及 有 许 多用 途 的重 要 原 料 需 求将 会 大 幅增 长 .加 上 以 二 氧 化 碳 为 原 料 生 产 降 解
功 效 1 倍 节 电5 % .因而 近 几 年在 汽 车 造 船 、化 —2 0
工 设 备 等 大 型 制 造 业 得 到 了 广 泛 应 用 。 尤 其 是 二 氧 化
8 万 吨 。 业 内认 识 指 出 应 大 力 度 开 发 二 氧 化 碳 潜 在 5 的 巨大 市 场 ,并 注 重 二 氧 化 碳 捕 集 、提 纯 与 回收 技 术
随 着 人 类 社 会 大 量 使 用 以 煤 和 石 油 为 代 表 的 化 石 料 , 净 水 、茶 饮 料 、乳 品 饮料 的冲 击 ,增 长速 度 已放 纯 燃 料 ,造 致 全 球 变 暖 的温 室气 体 一 一 二 氧化 碳 的排 放 慢 。 预 计 未 来 五 年 , 碳 酸 饮 料 行 业 虽 然 仍 是 二 氧 化 碳 量 急 剧 攀 升 .严 重 影 响 着 大 气 圈 与 生 物 圈 原 有 的 平 衡 主 要 消 费 领 域 . 但 所 占 比 例 将 会 明 显 下 降 。
的 研 发 .以实现 应 用 领域 的实 质 性拓 展 。 在 我 国 的 二 氧 化 碳 消 费 结 构 中 碳 酸 型 饮 料 占Байду номын сангаас
碳 和氢 气 混 合 气 体 保 护 焊 技 术 的 开 发 与 应 用 .不 仅 扩 大 了二 氧 化 碳 气 体 保 护 焊 的应 用 范 围 .而 且 克 服 了 二 氧 化 碳 气 体 保 护 焊 热 量 分 散 、 焊 点 大 、 焊 接 处 易 变 形 等 不 足 .这 必将 推 动该 领域 对 二 氧 化 碳 需 求 的 快 速 增 长 。预 计 需 求 量 将 有 目前 的3 万 吨 左 右 增 至6 5 万一8 万
万 吨 以 上 . 能 源 专 家 预 测 . 到 2 3 年 排 放 量 可 能 达 0O 到3 0 吨 以上 。据 美 国能 情 报 署20 年初 预测 . 8亿 06 2 5 年世 界 二氧 化 碳 排 放量 将 达 到3 8 吨 。 00 8亿 然 而 , 从 另 一 个 层 面 上 看 二 氧 化 碳 确 是 十 分 有 这 种 变 废 为 宝 的 二 氧 化 碳 利 用 新 途 径 正 在 受 到 人 们
吨。
4
、
7 % 碳 酸 二 甲酯 与 降 解 塑料 加 工 占1 % .二 氧 化 碳 0 O 保 护 焊 占6 ,超 市 食 品 保 鲜 占5 ,烟 丝 膨 化 及 其 他 % % 占5 % 油井 注 压 采 油 占4 。 %
1
、
二 氧 化碳 在 食 品 冷 藏 中 的应 用
p R o FES l Sl ON AL TH ESI 专 业 文 库 S
文 章编 号 :1 7 — 2 1( 0 )0 — 0 2 0 325 2 1 6 0 307~2
d i 0 9 9 i n 6 3 2 5 01 . 3 0 7 o :1 3 6 /j S 1 7 — 2 1 2 0 0 . 1 S
,
塑 料 技 术 的推 广 应 用 ,预 计 这 一 领 域 最 终 消 耗 的 二 氧
化 碳 将 占消费 总 量 的2 % 以上 。 0
3
、
越 来 越 多 的 关 注 。 当 今 .世 界 各 国 十 分 重 视 开 发 相 应 的 二 氧 化 碳 回 收 以 及 净 化 和 再 利 用 技 术 将 为 二 氧 化 碳 提 供 用 武 之 地 ,而 使 其 造 福 于 人 类 。