基于有限元法的摇枕疲劳强度分析
重载货车转向架摇枕有限元分析及结构优化(1)
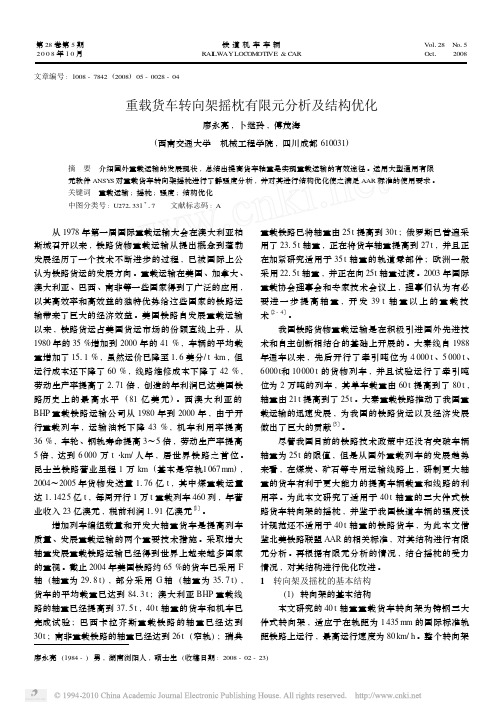
文章编号:1008-7842(2008)05-0028-04重载货车转向架摇枕有限元分析及结构优化廖永亮,卜继玲,傅茂海(西南交通大学 机械工程学院,四川成都610031)摘 要 介绍国外重载运输的发展现状,总结出提高货车轴重是实现重载运输的有效途径。
运用大型通用有限元软件ANSY S对重载货车转向架摇枕进行了静强度分析,并对其进行结构优化使之满足AAR标准的使用要求。
关键词 重载运输;摇枕;强度;结构优化中图分类号:U2721331+17 文献标志码:A 从1978年第一届国际重载运输大会在澳大利亚柏斯城召开以来,铁路货物重载运输从提出概念到蓬勃发展经历了一个技术不断进步的过程,已被国际上公认为铁路货运的发展方向。
重载运输在美国、加拿大、澳大利亚、巴西、南非等一些国家得到了广泛的应用,以其高效率和高效益的独特优势给这些国家的铁路运输带来了巨大的经济效益。
美国铁路自发展重载运输以来,铁路货运占美国货运市场的份额直线上升,从1980年的35%增加到2000年的41%,车辆的平均载重增加了1511%,虽然运价已降至116美分/t・km,但运行成本还下降了60%,线路维修成本下降了42%,劳动生产率提高了2171倍,创造的年利润已达美国铁路历史上的最高水平(81亿美元)。
西澳大利亚的BHP重载铁路运输公司从1980年到2000年,由于开行重载列车,运输油耗下降43%,机车利用率提高36%,车轮、钢轨寿命提高3~5倍,劳动生产率提高5倍,达到6000万t・km/人年,居世界铁路之首位。
昆士兰铁路营业里程1万km(基本是窄轨1067mm), 2004~2005年货物发送量1176亿t,其中煤重载运量达111425亿t,每周开行1万t重载列车460列,年营业收入23亿澳元,税前利润1191亿澳元〔1〕。
增加列车编组数量和开发大轴重货车是提高列车质量、发展重载运输的两个重要技术措施。
采取增大轴重发展重载铁路运输已经得到世界上越来越多国家的重视。
基于实测载荷谱的转K6转向架摇枕的疲劳寿命仿真分析

( 3) 有限元分析结果 加载计算后得出各载荷工况下的应力分布如图 3 ~ 图 6 所示 ( 取一半模型 ) 。根据计算结果, 选出摇枕 在各载荷作用下应力较大的点 , 从而确定摇枕上疲劳 损伤量最大的前 5 个测点, 在图 3~ 图 6 中标出 , 并列 出各点在各工况下的应力值见表 2 ( 各点应力以受拉 为正 , 受压为负) 。
m
( 2)
式中 s 0 为无限寿命时的疲劳极限 ; m 为斜率参数 ; N
第2期
基于实 测载荷谱的转 K6 转向架摇枕的疲劳寿命仿真分析
25
s 0 的方程。从物理意义上推断, 对于本文计算实例 B 级铸钢其 s 0 位于区间 [ 0,
e]
作用时, 造成临界部位疲劳损坏。这种情况下的疲劳 寿命在大多数情况下可近似为 疲劳寿命 = 5 计算结果 空车运行对摇枕产生的损伤极小 , 可以忽略不计。 重车运行情况决定着摇枕的疲劳寿命。因此, 重点分 析重车运行条件下摇枕的损伤和寿命。本文疲劳计算 依据 的摇枕载荷谱 是在 400 km 的 线路重车状态完 成 的, 实际运营中空重车的运行里程 约为 35∋65, 计算 所得的重车里程应当再乘以系数 65/ 100。按表 2 所列 节点及其应力 , 算出各点的疲劳损伤。其中旁承断面 突变处 ( 下弦板) 损伤量最大 , 为最危险部位 , 代表 了整个摇枕的寿命。由前面算出的 B 级铸钢材料在不 同疲劳降低系 数下的 S - N 曲线 ( 图 7) , 根据公 式 ( 4) 、 ( 5) 算出摇枕该部位在不同 k f 下的疲劳寿命 , 即整个摇枕的总寿命, 结果见图 8。计算结果表 明在
第 28 卷第 2 期 2008年4月 文章编号 : 1008- 7842 ( 2008) 02- 0023- 03
学生作业——货车摇枕的有限元分析
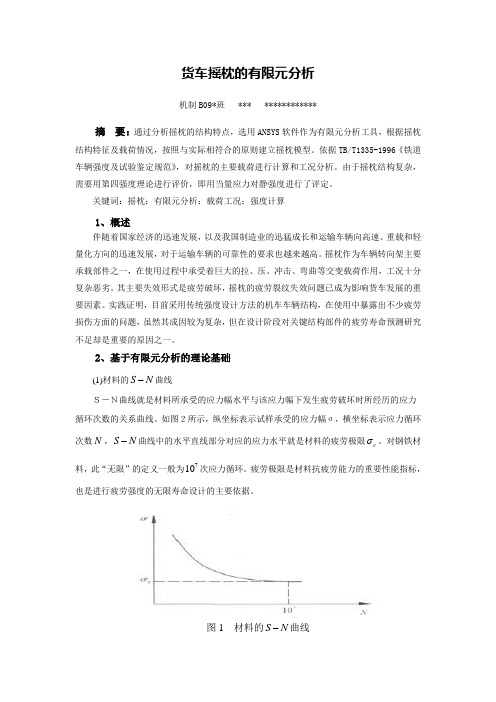
货车摇枕的有限元分析机制B09*班 *** ************摘要:通过分析摇枕的结构特点,选用ANSYS软件作为有限元分析工具,根据摇枕结构特征及载荷情况,按照与实际相符合的原则建立摇枕模型。
依据TB/T1335-1996《铁道车辆强度及试验鉴定规范》,对摇枕的主要载荷进行计算和工况分析。
由于摇枕结构复杂,需要用第四强度理论进行评价,即用当量应力对静强度进行了评定。
关键词:摇枕;有限元分析;载荷工况;强度计算1、概述伴随着国家经济的迅速发展,以及我国制造业的迅猛成长和运输车辆向高速、重载和轻量化方向的迅速发展,对于运输车辆的可靠性的要求也越来越高。
摇枕作为车辆转向架主要承载部件之一,在使用过程中承受着巨大的拉、压、冲击、弯曲等交变载荷作用,工况十分复杂恶劣。
其主要失效形式是疲劳破坏,摇枕的疲劳裂纹失效问题已成为影响货车发展的重要因素。
实践证明,目前采用传统强度设计方法的机车车辆结构,在使用中暴露出不少疲劳损伤方面的问题,虽然其成因较为复杂,但在设计阶段对关键结构部件的疲劳寿命预测研究不足却是重要的原因之一。
2、基于有限元分析的理论基础(1)材料的S N-曲线S-N曲线就是材料所承受的应力幅水平与该应力幅下发生疲劳破坏时所经历的应力循环次数的关系曲线。
如图2所示,纵坐标表示试样承受的应力幅σ,横坐标表示应力循环σ。
对钢铁材次数N,S N-曲线中的水平直线部分对应的应力水平就是材料的疲劳极限e料,此“无限”的定义一般为710次应力循环。
疲劳极限是材料抗疲劳能力的重要性能指标,也是进行疲劳强度的无限寿命设计的主要依据。
图1 材料的S N-曲线m N Cσ= (1)式(1)中 :σ ——— 应 力 幅 ;N ——— 达 到 疲 劳 破 坏 时 的 应 力 循 环 次 数 ; m C 、———材料数(2)疲劳载荷类型疲劳载荷一般有稳定循环变应力和非稳定性循环变应力2种。
稳定循环分为对称循环、脉动循环和非对称循环;非稳定性循环分为规律性非稳定循环和随机性的非稳定循环。
(完整版)疲劳分析的数值计算方法及ANSYS疲劳分析实例

第十四章疲劳分析的数值计算方法及实例第一节引言零件或构件由于交变载荷的反复作用,在它所承受的交变应力尚未达到静强度设计的许用应力情况下就会在零件或构件的局部位置产生疲劳裂纹并扩展、最后突然断裂。
这种现象称为疲劳破坏。
疲劳裂纹的形成和扩展具有很大的隐蔽性而在疲劳断裂时又具有瞬发性,因此疲劳破坏往往会造成极大的经济损失和灾难性后果。
金属的疲劳破坏形式和机理不同与静载破坏,所以零件疲劳强度的设计计算不能为经典的静强度设计计算所替代,属于动强度设计。
随着机车车辆向高速、大功率和轻量化方向的迅速发展,其疲劳强度及其可靠性的要求也越来越高。
近几年随着我国铁路的不断提速,机车、车辆和道轨等铁路设施的疲劳断裂事故不断发生,越来越引起人们的重视。
疲劳强度设计及其研究正在成为我国高速机车车辆设计制造中的一项不可缺少的和重要的工作。
金属疲劳的研究已有近150年的历史,有相当多的学者和工程技术人员进行了大量的研究,得到了许多关于金属疲劳损伤和断裂的理论及有关经验技术。
但是由于疲劳破坏的影响因素多而复杂并且这些因素互相影响又与构件的实际情况密切相关,使得其应用性成果尚远远不能满足工程设计和生产应用的需要。
据统计,至今有约90%的机械零部件的断裂破坏仍然是由直接于疲劳或者间接疲劳而引起的。
因此,在21世纪的今天,尤其是在高速和大功率化的新产品的开发制造中,其疲劳强度或疲劳寿命的设计十分重要,并且往往需要同时进行相应的试验研究和试验验证。
疲劳断裂是因为在零件或构件表层上的高应力或强度比较低弱的部位区域产生疲劳裂纹,并进一步扩展而造成的。
这些危险部位小到几个毫米甚至几十个微米的范围,零件或构件的几何缺口根部、表面缺陷、切削刀痕、碰磕伤痕及材料的内部缺陷等往往是这种危险部位。
因此,提高构件疲劳强度的基本途径主要有两种。
一种是机械设计的方法,主要有优化或改善缺口形状,改进加工工艺工程和质量等手段将危险点的峰值应力降下来;另一种是材料冶金的方法,即用热处理手段将危险点局部区域的疲劳强度提高,或者是提高冶金质量来减少金属基体中的非金属夹杂等材料缺陷等局部薄弱区域。
有限元法进行疲劳分析

元计算科技发展有限公司是一家既年青又悠久的科技型企业。年青是因为她正处在战略重组 后的初创期,悠久是因为她秉承了中国科学院数学研究所在有限元和数值计算方面所开创的光荣 传统。元计算的目标是做强中国人自己的计算技术,做出中国人自己的CAE软件。
元计算秉承中国科学院数学与系统科学研究院有限元自动生成核心技术(曾获中科院科技进 步二等奖、国家科技进步二等奖),通过自身不懈的努力与完善,形成一系列具有高度前瞻性和 创造性的产品。
5. 评估(Evaluation) 一般来说,我们可进行下列估算: ·事件损伤(Event Damage) ·事件损伤方向(Event Damage Direction) ·损伤累积(Accumulated Damage) ·事件寿命估算(Event Life Estimate)
6. 后处理(Post Processing) 疲劳分析的后处理与静力学的后处理完全一致,此处不再重复。
有限元法进行疲劳分析
一、有限元法疲劳分析的基本思路
用有限元法进行疲劳分析,其基本思路是:首先进行静或动强度分析,然后进入到后 处理器取出相关的应力应变结果,在后处理器中再定义载荷事件,循环材料特性,接着根 据所需要的疲劳准则对每一个载荷事件进行寿命计算,最后根据累计损伤理论判断是否开 始破坏。由于结构受力状态往往是一复杂的应力状态,而在实验中测 得的结构材料S-N曲 线又常是在简单应力状态下获得的,因此常用最小能量屈服准则或其它等效准则,将所研 究的疲劳点上的复杂应力用一个等效应力替代。对有限元法而言,这一过程很容易实现。 等效替代以后,即可参照原始材料的S-N曲线进行疲劳寿命评估。上述方法称之为应力-寿 命法或S-N法,该方法不严格区 分裂纹产生和裂纹扩展,而是给出结构发生突然失效前的 全寿命估计。当然,还可以采用更加现代化的局部应变法或初始裂纹法。因篇幅所限,因 此仅讨论S-N法,且针对车辆结构疲劳分析。
悬挂式单轨车辆摇枕强度分析
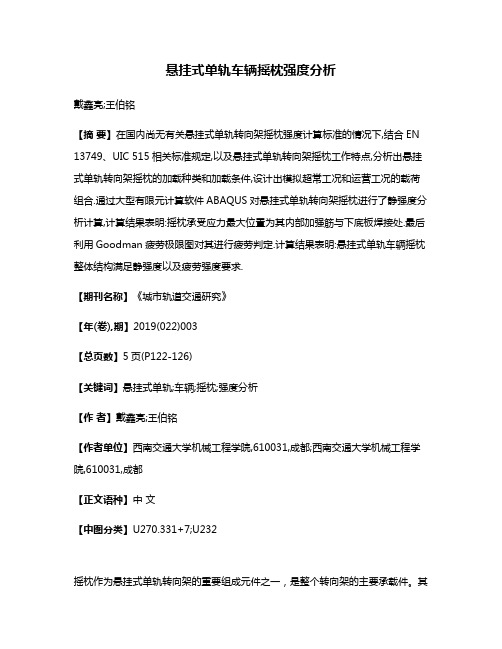
悬挂式单轨车辆摇枕强度分析戴鑫亮;王伯铭【摘要】在国内尚无有关悬挂式单轨转向架摇枕强度计算标准的情况下,结合EN 13749、UIC 515相关标准规定,以及悬挂式单轨转向架摇枕工作特点,分析出悬挂式单轨转向架摇枕的加载种类和加载条件,设计出模拟超常工况和运营工况的载荷组合.通过大型有限元计算软件ABAQUS对悬挂式单轨转向架摇枕进行了静强度分析计算,计算结果表明:摇枕承受应力最大位置为其内部加强筋与下底板焊接处.最后利用Goodman疲劳极限图对其进行疲劳判定.计算结果表明:悬挂式单轨车辆摇枕整体结构满足静强度以及疲劳强度要求.【期刊名称】《城市轨道交通研究》【年(卷),期】2019(022)003【总页数】5页(P122-126)【关键词】悬挂式单轨;车辆;摇枕;强度分析【作者】戴鑫亮;王伯铭【作者单位】西南交通大学机械工程学院,610031,成都;西南交通大学机械工程学院,610031,成都【正文语种】中文【中图分类】U270.331+7;U232摇枕作为悬挂式单轨转向架的重要组成元件之一,是整个转向架的主要承载件。
其功能包括传递车体与转向架之间的横向力、纵向力和垂向力,提供二系悬挂元件的安装位置,以及限制车体与转向架的相对摆角等。
摇枕可靠性的高低对整车的安全性以及平稳性有较大影响。
目前,与悬挂式单轨相关的标准、规范尚未成型,本文以EN 13749、UIC 515标准为基础,结合悬挂式单轨转向架在实际运用过程中的特性,推演出悬挂式单轨转向架摇枕的载荷工况,用于其静强度以及疲劳强度的分析。
1 摇枕有限元模型建立摇枕整体结构主要由薄板与中心实体部分焊接而成,通过UG软件建立其三维模型(见图1),将其几何外形导入Hypermesh软件中进行有限元前处理。
在建立摇枕有限元模型时采用2D壳单元对摇枕薄板进行划分,对于摇枕中部实体部分采用3D实体单元进行网格划分。
整个有限元模型(见图2)共使用S4R单元171 061个,C3D4单元142 632个,Beam单元32个。
货车转向架摇枕有限元计算及试验对比分析研究
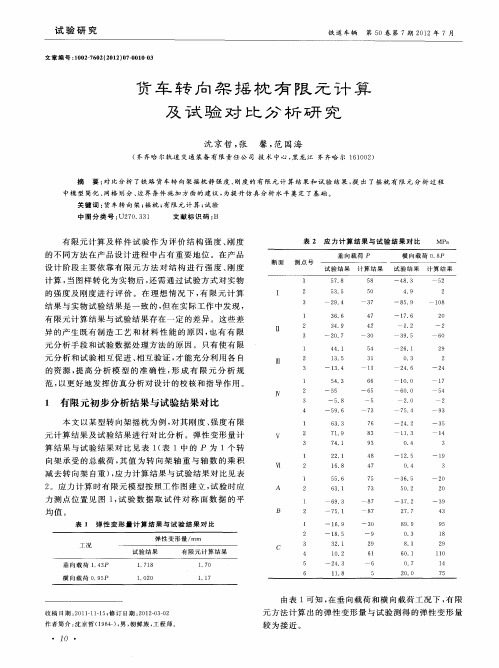
图 2 等 效 简 支 约 束
Z
≥
Y
1
为 了保 证其 强度 , 关键 尺寸往 往按 上公 差取值 , 摇枕 使 的实 际重量 大于名 义 重量 , 成应 力计 算结果 偏 大 。 造 2 2 边界 条件 . 试 验加 载时 , 用 的顶 头 刚度 较 大 。试 验 中垂 向 使
向架 承受 的总载 荷 , 其值 为 转 向架轴 重 与 轴 数 的乘 积
减 去 转 向架 自重 ) 应 力 计 算 结 果 与 试 验 结 果 对 比见 表 ,
2 。应 力计 算时有 限元 模型按 照工 作 图建立 , 验 时应 试
力 测 点 位 置 见 图 1 试 验 数 据 取 试 件 对 称 面 数 据 的 平 , 均值 。
试 验 研 究
文 章 编 号 :0 2 7 0 ( 0 2 0 — 0 00 1 0 — 6 2 2 1 ) 7 0 1 —3
铁道车 第5 卷第7 02 辆 O 期21 年7 月
货 车 转 向 架 摇 枕 有 限 元 计 算
及 试 验 对 比 分 析 研 究
沈京哲 , 张 馨 , 国海 范
MP a
设 计 阶段主要 依靠 有 限元 方 法 对 结 构进 行 强 度 、 度 刚 计算 , 当图样 转化 为实物 后 , 需通过 试验 方式 对实 物 还 的 强度及 刚度 进行 评 价 。在 理 想 情况 下 , 限元 计算 有 结果 与 实物试 验结 果是 一致 的 , 但在 实 际工作 中发 现 , 有 限元计 算 结果 与试验 结果 存在一 定 的差异 。这些 差 异 的产 生既有 制造 工 艺 和材 料 性 能 的原 因 , 有 有 限 也 元 分析 手段 和试验 数据 处理 方法 的原 因 。只有 使有 限 元 分析 和试 验相互 促进 、 相互 验证 , 能充分利 用各 自 才 的资源 , 高 分 析 模 型 的 准 确 性 , 成 有 限 元 分 析 规 提 形 范, 以更 好地 发挥仿 真 分析对 设计 的校 核和指 导作 用 。
基于有限元的疲劳分析方法及实践

基于有限元的疲劳分析方法及实践基于有限元的疲劳分析方法及实践疲劳是物体在循环荷载作用下发生的连续循环应力引起的损伤和破坏过程,对于工程结构的安全可靠性至关重要。
为了预测和评估结构在长期使用中的疲劳寿命,我们需要进行疲劳分析。
有限元方法是一种广泛应用的用于疲劳分析的数值模拟方法,它能够预测结构在不同应力循环下的寿命和破坏。
有限元方法基于结构的离散化,通过将结构划分为多个小单元来近似描述结构的力学行为。
在疲劳分析中,有限元方法可以应用于确定结构在复杂载荷历程下的应力和应变分布,并进一步评估结构的寿命。
下面将介绍有限元疲劳分析的基本步骤和实践经验。
首先,进行有限元模型建立。
有限元模型是指根据结构的几何形状和物性参数,以及实际工作条件建立的数值模型。
通过使用计算机辅助设计软件,我们可以将结构的几何形状进行精确建模,并定义结构中的材料参数和加载条件。
其次,确定结构的应力循环历程。
在实际工作中,结构往往会受到多种复杂的载荷作用,在疲劳分析中需要对这些载荷进行定量描述。
一般情况下,我们可以通过实验测量或者数值模拟来获取结构在不同工况下的应力循环历程。
接下来,进行疲劳寿命预测。
通过有限元分析软件,可以计算出结构在不同应力循环下的应力和应变分布。
利用经验公式或者材料的疲劳性能曲线,可以计算出结构在不同应力循环下的疲劳寿命。
疲劳寿命预测是疲劳分析的核心内容,它可以帮助工程师判断结构的安全性,进而进行优化设计。
最后,进行疲劳寿命验证。
在疲劳寿命预测的基础上,需要通过一定的实验验证来确定与有限元分析结果的一致性。
疲劳试验可以使用转子转速、台阶加载或实际工况加载等方法进行,通过实验可以验证有限元模型的准确性和可靠性。
对于疲劳分析的实践经验,有以下几点需要注意:1.准确建立有限元模型。
有限元模型的准确性关系到疲劳分析结果的可靠性。
在建模过程中,需要仔细考虑结构的几何形状、边界条件和材料参数等因素,确保模型与实际工程结构相匹配。
- 1、下载文档前请自行甄别文档内容的完整性,平台不提供额外的编辑、内容补充、找答案等附加服务。
- 2、"仅部分预览"的文档,不可在线预览部分如存在完整性等问题,可反馈申请退款(可完整预览的文档不适用该条件!)。
- 3、如文档侵犯您的权益,请联系客服反馈,我们会尽快为您处理(人工客服工作时间:9:00-18:30)。
划分 , 用 A Y 有 限元 分析软 件 , 利 NS S 分别计算 了典型裁荷 工况 下的摇枕应 力分布 , 而确 定 了 从 摇枕 的疲 劳薄弱部位 并
进 行 了局部优化 , 据 A I 准 , 根 AK标 评价 了摇枕 的疲劳强度 , 对摇枕进行 了寿命计算分析。 关键词 : 摇枕 ; 劳强度 ; 劳薄弱部位 ; 疲 疲 寿命
( 力 单 位 : a) 应 MP
应力及疲劳损伤 ( ) m, 计算结果 载荷工况 下表面 中央 下表面漏砂孔 下表面端部拐角 应 力 损伤 应 力 损伤 心 盘单独受载循环( ) 0万次 Q5 单侧 旁承受载循环∞ 2 万次 5 1 8 00 2 31 0 9 9 . .5 2 . 4 . O O0 .1 0 0 2 . 07 l. 87 0 0 应力 9. 93 l42 2. 5. 59 0 搠伤 O O O
图 2 摇 枕 加 载 模 型 示 意 图
1 摇 枕的疲 劳强度计算
11 单元 离散 化 .
通 过 Sl rs odWok 建立摇 枕 模 型 。把 建好 的模 型 i 导入 H pr e ye M s h软件划分 网格 ,有限元 的单元类型 选用四面体四节点单元 Sl 。根据摇枕模型的尺 od 5 i4 寸 , 合考虑计算量和准确性 , 综 网格 划 分 时 , 元 尺 单 寸取为 1 m 。 5 m 离散后可得单元数为 3 9 个 , 5 2 节点 7 数为 1 2个 。弹性 约束采用 Cm il , 中弹簧 09 8 o bn4 其 元 的单 元 数为 4 0个 , 图 1 示 。 如 所
表 3 A R载荷谱下摇 枕的疲劳 寿命 A
疲劳降低 系数 ( 母)
15 . 20 . 25 . 3O .
枕 的疲 劳 寿命变 化逐 渐变 慢 。
总损伤值 ( 谱长 1 . k 7万 m)
O0 18 8 .0 9 Oo 7 2 5 .o 8 O0 13 7 .2 6 O0 0Ol .6 l
1 7
E u p n Ma u a t n e h oo y No7, 01 q i me t n fc r gT c n lg . 2 i 2
图 4为摇枕在单侧旁承受载下 的第一主应力 云 分析。疲劳试验载荷与评定考核标准为 10万次载 0 图。 大应力值位置为摇枕的下表面端部拐角 , 最 应力 荷循环的疲 劳累计损伤值小于 1下面为疲劳试验载 , 值为 16 6 P ,摇枕在两侧旁承受载下的第一 主 荷 工况 : 8. a 2M 应 力 云 图 ,最 大应 力 值 位置 为 摇 枕 的下表 面 端部 拐 () 1 心盘单独受载循环不低于 5 万次 ; 0 角, 应力值为 8 . P 。 3 2M a 9 () 2 单侧旁承受载循环不低于 2 万次 ; 5
主 , 缩 平 均 应 力 作 用 时 ,一 曲线 上移 , 压 JⅣ s 同样 应 力 幅作 用 下 寿命增 大 [ 2 1 。应重 点考 虑摇 枕 的下表 面 。 本 文 通 过 有 限元 分 析 计 算 的结 果 找 到摇 枕 上 3 个 最 薄弱 的点 , 别 为下 表 面 中央 部位 , 表 面漏 砂 3 摇枕的寿命估算 分 下 孔 部位 , 表 面端 部拐 角部 位 。 下
两侧 旁承受载循环( - ) 5万次 9 Z Z’ 2 . 4 累积 损伤 ∑( l ) n 计算结果
00 . 5
O m
寿命要求 , 那么整个摇枕就满足寿命要求 , 因此 , 该
根 据 美 国 A R机 务 标 准 中 M一 0— 5 “ 钢 转 部位的寿命就代表 了整个摇枕的疲劳寿命 。 A 220 铸 表3 和图 5 为摇枕在不同疲劳 降低 系数下的疲 向架 摇 枕设 计 和 试验 规 范 ”1 摇 枕进 行 疲 劳强 度 [ 3 ,对
图 4 摇 枕 在 单 侧 旁 承 受 载 作 用 下 的 第 一 主应 力 图
情 况 下 , 枕 的应 力 比较 大 , 伤 也 不是 特别 大 ; 摇 损 在 高抗 疲劳 强度 ;
旁承均布受载的情况下 , 摇枕的受力 比较小 , 因此损 () 4 通过优化与其他构件 的配合情况 , 来改变摇 伤也 不 明显 。 枕的边界条件和载荷状况 ; 此外 , 枕 上表 面 以受压 为 主 , 摇 下表 面 以受拉 为 () 5 通过加工硬化或热处理 , 使下表面漏沙孑处 L
() 3 两侧旁承受载循环不低于 2 万次 。 5
由表 1 以看 出 , 可 在正常铸造质量水平 下( = 1 )总的载荷循环 数为 10万 次时 , 枕各 部位 的疲 ., 5 0 摇
劳累积损伤值均小于 I ,也就说明通过 10 0 万次 的载 荷循环后 , 该摇枕没有发生疲劳破坏 , 符合强度标准。 24 改进措 施 .
中图分 类号 : 2 03 U 7 .3 文献标识 码: A 文章编号 :6 2 5 5 ( 0 2)7 0 1 - 3 17 —4 X 2 1 0- 0 7 0
从 2 0 年开始 ,我 国铁路货 车运输全面提速 , 06 而且载重能力也大 幅增加 ,因此对铁路列车安全性 的要求越来越高 。摇枕是货车转向架三大件结构之 是重要的承载部件 , 是车辆车体和转 向架构架之 间的连接装置 , 主要承受和传递交变的垂 向力 、 向 横 力 和 纵 向力 , 转 向架 摇 枕 的疲 劳 强 度 , 铁道 机 车 故 对 车辆运行 的安全性 、 可靠性和经济性至关重要 。 在 车辆 运 用 中 , 枕 的运 营 工况 非 常 恶 劣 , 摇 这样 会 导致 摇枕 萌 生裂纹 和裂 纹扩 展 , 而线 路运 行 时 出现 的各 种 异 常情 况 , 剧 了裂纹 的产 生 和扩 展 , 终会 加 最 引起疲 劳破 坏 , 会对 行车 安全构 成严 重威 胁 。 因此 , 对 转 向架 摇枕 的疲 劳 问题进 行研究 具 有重要 意义 。
《 装备制造技术}o2 2 1 年第 7 期
基于有 限元法的摇枕疲劳 强度分析
夏祥春 1 I
(. 1河南理工大学 机械与动力工程学院, 河南 焦作 44 0 ;. 5 00 2永城职业学院, 河南 永城 4 60 ) 76 0
摘 要: 以货车转 K 6型转 向架摇枕 为研 究对 象, 建立 了摇枕 的三维几何模 型 , 用 HyeMeh软件对摇枕 进行 了网格 采 pr s
1 8
《 装备制造技术}0 2 2 1 年第 7 期
劳寿命 。
当疲劳降低系数较小 的时候 , 摇枕 的寿命较大。随着 的增大 , 摇枕疲劳寿命逐渐减小 。在 巧 = .— . 1 2 5 0
注 :疲劳降低系数 =1 ~ .代表了铸造件 . 2 5 0
随着 的降低 , 的疲劳寿命 急剧下降 ; 摇枕 的正 常品质水平 ,该水平 的铸造缺 陷是最常见的缺 区段时 , 在疲劳降低系数大于 2 时 , . 0 随着 的继续增大 , 摇 陷形 式 [ 4 】 。
产生残余压应力 ,残余压应力的引人会提高抗疲 劳
强度。
依据 A R标准 的脉 动循 环应力 一寿命 曲线 和 A 表 2列 出 了美 国 A R机 务 标准 中 9 .t 车重 A 07 敞 最大主应力考核准则 , 求得各载荷工况下 的损伤 , 再 空 车载荷 谱 的 记录里 程 。依 据美 国 A R货 车疲 劳设 A 利用 M nr i 线性 累积损伤理论 , e 求得摇枕各疲劳薄弱 计标准 中的载荷谱 , B 级铸钢在不同疲劳强度系 以 + 部位 的总损伤 , 计算结果及各薄弱点在各工况下 的 数下的 sJ 曲线作为基本 s Ⅳ曲线 ,结合有 限元分 —r 7 、 一 应 力值 如 表 1 所示 。 析计算得到的摇枕疲劳薄弱部位 , 最后利用 M nr i 线 e 性 累积损 伤 理论对摇 枕 的疲 劳寿命 进行 估 算 。 表 1 疲 劳试验载 荷下疲劳薄 弱部位损伤计算结果
1 . 7 I 13 . 1 1 . 2 1 12 .
表 2 载 荷谱 记 录 里 程 ( 位 : k ) 单 万 m
由表 1 知 ,摇枕 疲 劳最 薄 弱 部 位在 下 表 面 的 可 漏 砂 孔处 , 部位 损 伤最 严 重 , 该 只要 该 部 位达 到 疲 劳
图 1 摇枕离散 网格模型 图
12 载荷 工况 及 边界 条件 .
在摇枕的实 际运行中,摇枕承受 的载荷较为复
收 稿 日期 :0 2 0 — 5 2 1— 4 0
图 3 摇枕在心盘单独受载作用下的第一主应力云图
作者简 介 : 夏祥春 (9 1 ) 男 , 1 8一 , 河南永城市人 , 助教 , 工程 硕士学位 , 研究方 向为机械设计与制造。
其 中载荷 P等于转 向架轴重与轴数的乘 积减去 转向架 自重 , 为一个转向架承受的垂向静载荷[ 1 ] 。 P= 2 ( G—u) ( ×2 0 g= 2 70 0—50 0 × 98 0 ) . 4 00 0N 8 0 () 1 式 中, G为转 向架轴的净质量 , 2 为 7; t 日为转向架的 自身净质量 , 5 0 g 为 0k 。 0 13 有 限元应 力计 算 结果及 疲 劳强 度 评定 . 利用 A S S软件对摇枕进行有 限元静态分析 。 NY 图3 为摇枕在心盘单独载荷作用下 的第一 主应力云 图。最大应力值位置为摇枕 的下表面 中央和漏砂孔 , 应 力值 为 231 a 2 . MP 。 4
小应 集中系数 , 降低应力集中程度 ; ( ) 善下 表 面漏沙 孑处 的表面 粗糙 度 , 2改 L 以降 低 分析上图可知 , 心盘在单独受载的情况下 , 应力 疲 劳强度 ; 最大 , 对摇枕造成的损伤最严重 ; 在单侧旁承受载 的 ( ) 大部 件在 下表 面漏 沙孔 处 的厚 度 , 而 提 3增 进
由表 3可 以看 出 , 劳 降低 系数 为 2 疲 . , 到 0时 得 即为 2 8万 k 2 m。当按照 规 范 中规 定 的空 车与 重车 的 薄弱部位( 下表面漏砂孔处 ) 进行了寿命评估 , 其寿命 运行里程 比 0 5 . 计算 ,得到重车情况下摇枕的寿命 为 7 9 6—28万 k 2 m。如果 按 照重 车每 年运 行 1 5万 k m