普通运输带上覆盖胶工艺解析
输送带的制作工艺解析

输送带zui重要的两个步骤:成型、硫化,这两个过程直接影响到输送带的使用时间、带体光洁度等,是输送带制造中最重要的环节。
1、输送带成型的生产工艺是看不到输送带的组成,根据设计出的输送带体的形状,成型后的输送带带有胚胎,这一步称为输送带的成型。
各种输送带由于机构类型不同,其成型方法也不同。
输送带和平型传动带均属平带。
平带成型有专用的成型设备,主要由布架、工作台、压辊、包布装置等组成。
在成形过程中,采用机械牵引、自动压合、卷取得连续流水作业,生产效率高。
输送带和平型传动带的成型是由多层一次性叠片组成,包括覆盖输送带的橡胶和平型传动带的对口胶及封口胶条。
贴合时主要要求布层张力均匀,经向布纹正直不偏,各层间压合紧密、无气泡。
2、硫化输送带、平型传动带多用液压蒸汽加热的平板硫化机硫化。
常用的平板固化度一般为3-10米,宽度在3米以下。
因为平板硫化长度有限,因为输送带需要分段硫化。
若采用鼓式硫化机硫化,可连续操作,可避免因接头部位二次硫化而产生硫的现象。
硫化时,输送带要有一定的伸缩性,硫化温度的选择不在此时,输送带容易出现明疤。
覆盖带生产工艺

覆盖带生产工艺覆盖带是一种用于覆盖提升机、输送机和碎石机等机械设备传动带的一种零部件。
它主要由橡胶材料制成,具有良好的耐磨性和耐粘性,能有效保护传动带的芯线不受外界环境的侵蚀,从而延长传动带的使用寿命。
下面将对覆盖带的生产工艺进行详细介绍。
首先,覆盖带的生产工艺包括材料准备、橡胶混炼、挤出成型、硫化等多个环节。
材料准备阶段,首先需要准备适量的橡胶材料,通常采用天然橡胶或合成橡胶作为主要原料。
此外,还需要添加一定的填充剂、增强剂、硫化剂和促进剂等辅助材料,以提高覆盖带的性能。
所有的原料都需要进行严格的质量检验,确保其符合产品要求。
在橡胶混炼阶段,将准备好的橡胶材料和辅助材料按照一定的配方比例混合在一起,然后通过橡胶混炼机进行混炼。
混炼的目的是将各种材料充分混合,使之成为具有一定塑性和可加工性的橡胶混合料。
混炼过程中还需要控制适当的温度和时间,以确保混炼效果的均匀性。
接下来是挤出成型阶段,将混炼好的橡胶料通过挤出机进行挤出,以形成平坦的带状形状。
在挤出过程中,还需要加入一定的硫化剂,使橡胶料在经过挤出后能够保持一定的形状稳定性。
最后是硫化阶段,将挤出好的覆盖带放入硫化机中进行硫化处理。
硫化的目的是使橡胶料中的硫化剂与橡胶分子发生化学反应,从而形成橡胶网状结构,提高覆盖带的强度和耐磨性。
硫化过程中需要控制适当的温度和时间,以确保硫化效果的稳定性和一致性。
整个生产过程中,还需要进行严格的质量控制,对每个环节进行检测和检验,确保产品质量的稳定性和可靠性。
此外,还需要进行包装和运输,以确保产品在运输和使用过程中不受损坏。
总之,覆盖带的生产工艺涉及材料准备、橡胶混炼、挤出成型、硫化等多个环节,需要严格控制每个环节的质量和工艺参数,以保证最终产品的质量和性能。
只有做好每个环节的工作,才能生产出符合要求的覆盖带产品。
输送带覆盖胶ppt课件
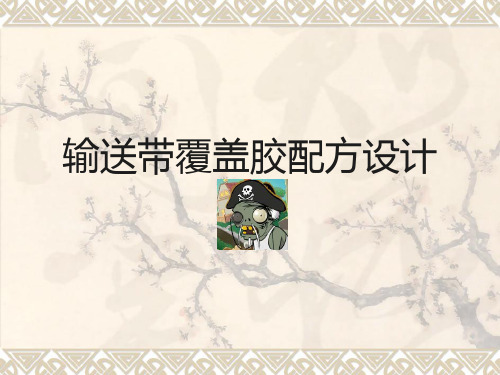
配方说明—阻燃剂
因此,输送带覆盖胶的难燃体系选择氯化石 蜡、十溴二苯醚、三氧化二锑、氢氧化铝和 硼酸锌并用体系
氢氧化钠等
配方说明—其他
㈠促进剂M、促进剂DM ㈡软化增塑剂—松焦油 ㈢填充补强体系—高耐磨炭黑、陶土、碳酸钙 ㈣偶联剂—NDZ-101 ㈤防老剂—4010
配方说明—阻燃剂
炭黑在橡胶制品中即是很好的补强剂又能有 效地降低制品表面电阻,但是炭黑的使用往 往使制品产生无焰燃烧(炭黑)
氯化石蜡和三氧化二锑并用能有效地阻止有 焰燃烧,但同时助长了无焰燃烧。氯化石蜡、 十溴二苯醚、氢氧化铝、硼酸锌体系虽能有 效地抑制无焰燃烧,但对阻止有焰燃烧效果 不够显著
输送带覆盖胶配方设计
性能要求
酒精喷灯安全覆盖层燃烧≤5秒 耐浓度为10%硝酸 20%的盐酸和硫酸 拉伸强度≥14mpa;伸长率≥350%;磨耗
量≤0.80㎡/1.61Km;老化后拉伸强度和伸 长变化率(70℃×7d):-25~25
配方
天然橡胶 促进剂M 促进剂 DM 松焦油 高耐磨炭 0-50
5 5
HDZ-101 填充剂30%
防老剂
3
4010
氯化石蜡
10
十溴二苯醚
10
三氧化二锑
10
氢氧化铝
10
硼酸锌
10
配方说明—天然橡胶性能
伸长率最大可达1000%。在0-100℃内回弹 性可达到50%-85%以上
纯胶硫化胶拉伸性能可以达到17~25MPa 耐屈挠疲劳性、耐磨性较好 耐10%氢氟酸、20%盐酸、30%硫酸、50%
橡胶输送带覆盖胶的生产配方

橡胶输送带覆盖胶的生产配方橡胶输送带是一种广泛应用于矿山、港口、电厂等行业的输送设备。
它由多层橡胶和纤维材料组成,其中覆盖胶是橡胶输送带的重要组成部分。
覆盖胶的质量直接影响到输送带的使用寿命和性能。
一、覆盖胶的作用覆盖胶主要起到保护输送带骨架材料不受外界环境侵蚀,提供与物料接触的摩擦力,以及防止物料溢出等作用。
覆盖胶需要具有良好的耐磨性、耐裂纹性、抗冲击性和耐化学腐蚀性。
二、常见的覆盖胶类型1. 通用型(General Purpose)通用型覆盖胶适用于大多数普通工况下的输送带,具有较好的耐磨性和耐裂纹性能。
2. 耐热型(Heat Resistant)耐热型覆盖胶适用于高温工况下的输送带,可以承受高温物料的传递,具有较好的耐热性和耐老化性能。
3. 耐油型(Oil Resistant)耐油型覆盖胶适用于输送带需要与油类物质接触的场合,具有较好的耐油性和抗溶胀性能。
4. 耐酸碱型(Acid and Alkali Resistant)耐酸碱型覆盖胶适用于输送带需要与酸碱物质接触的场合,具有较好的耐腐蚀性和抗溶胀性能。
5. 防火型(Fire Resistant)防火型覆盖胶适用于易燃易爆场所的输送带,具有自灭火、自冷却和不传播火焰等特点。
三、橡胶配方橡胶输送带覆盖胶的生产配方是根据不同类型的覆盖胶要求进行设计和调整的。
一般而言,橡胶配方包括以下几个主要组分:1. 橡胶基料橡胶基料是橡胶输送带覆盖胶的主要成分,常用的橡胶基料有天然橡胶(NR)、丁苯橡胶(SBR)、丁腈橡胶(NBR)等。
不同类型的橡胶基料具有不同的性能特点,需要根据具体要求进行选择。
2. 填料填料是橡胶配方中的重要组成部分,它可以增加覆盖胶的硬度、强度和耐磨性。
常用的填料有碳黑、硅灰、白炭黑等。
3. 功能性添加剂功能性添加剂包括增塑剂、防老化剂、抗氧剂等,它们能够改善橡胶的加工性能和使用寿命。
4. 加工助剂加工助剂主要包括硫化剂、促进剂和稳定剂等,它们能够促进橡胶的硫化反应,提高覆盖胶的物理性能。
输送带覆盖胶ppt课件

100 1 0.5
2 40-50
5 5
HDZ-101 填充剂30%
防老剂
3
4010
氯化石蜡
10
十溴二苯醚
10
三氧化二锑
10
氢氧化铝
10
硼酸锌
10
配方说明—天然橡胶性能
伸长率最大可达1000%。在0-100℃内回弹 性可达到50%-85%以上
纯胶硫化胶拉伸性能可以达到17~25MPa 耐屈挠疲劳性、耐磨性较好 耐10%氢氟酸、20%盐酸、30%硫酸、50%
输送带覆盖胶ppt课件
性能要求
酒精喷灯安全覆盖层燃烧≤5秒 耐浓度为10%硝酸 20%的盐酸和硫酸 拉伸强度≥14mpa;伸长率≥350%;磨耗
量≤0.80㎡/1.61Km;老化后拉伸强度和伸 长变化率(70℃×7d):-25~25
配方
天然橡胶 促进剂M 促进剂 DM 松焦油 高耐磨炭 黑 陶土 碳酸钙
氢氧化钠等
配方说明—阻燃剂
因此,输送带覆盖胶的难燃体系选择氯化石 蜡、十溴二苯醚、三氧化二锑、氢氧化铝和 硼酸锌并用体系
谢谢大家!
Hale Waihona Puke
活化胶粉在输送带覆盖胶中的应用概述

活化胶粉在输送带覆盖胶中的应用概述摘要:活化胶粉属于一种新型填料,能够在轮胎胶料中增强动态稳定性能,减少成本,在国外广泛应用。
近些年来,活化胶粉的应用范围有了明显的提高,在输送带覆盖胶中应用可以更好提高输送带的效果,延长覆盖胶的使用寿命。
随着活化胶粉的用量不断增多,活化胶粉混胶挤出应力也不断增加,挤出物外观会明显变差,导致出口膨胀下降。
挤出物的尺寸稳定性比较好,正硫化时间有效缩短,活化胶的共混硫化胶300%定伸力和硬度,都有不同程度的提升。
关键词:活化胶粉;输送带覆盖胶;应用策略引言在国外橡胶配方中掺入橡胶粉技术非常成熟的,但是掺入胶粉的硫化胶由于网络结构存在不均匀的特性,会直接导致硫化胶的整体性能受到影响。
为保证胶粉和生胶的相互作用扩大使用范围,我国对胶粉表面活化和细化投入了比较多研究力量。
根据实验结果显示,通过掺入活化胶粉尽管能够对硫化胶静态性能产生影响,但却有效改善加工工艺和动态疲劳性能。
所以活化胶粉在传输带覆盖中的应用具有科学性与合理性。
1胶粉性能目前活化胶粉不仅可以改善生胶基质的键合能力,同时也能够确保胶粉表面经过活化处理之后,还能够提高分子链的相互渗透效果,形成良好的共硫化性。
但拉伸强度拉伸伸长率会明显下降,根据实践经验表明,利用活化橡胶粉在输送带覆盖胶中应用是可行的。
2胶粉用量的影响因素为了探究胶粉用量的影响分析,笔者根据实践经验设计了实验,在实验过程中所有的原材料为标准材料,活化胶粉100、软化剂20、氧化锌3。
在实验时,根据GB13460-92的标准对胶粉的加热、失重、灰分以及丙酮抽出物进行检测。
橡胶混炼挤出物性能采用毛细管流变仪进行测定,挤出温度大约在120℃之间,挤出物出口膨胀比根据国标1233规定进行。
通过实验能够发现,随着活化胶粉用量的不断增加,混炼胶门尼粘度值也在变大,挤出物外观比较粗糙,但出口膨胀却明显下降。
当胶粉量超过规定值时,混炼胶可在发胶时间和正硫化时间之间进行调合。
耐高温阻燃输送带覆盖胶的研制

作者简介:赵明德(1969-),男,助理工程师,主要从事橡胶输送带的研发和管理。
收稿日期:2023-08-28我国是钢铁生产大国,在烧结矿、焦炭等高温物料输送过程中,经过处理后大部分物料的温度在300 ℃以下,但仍有小部分物料温度较高,甚至出现明火现象。
为保证生产的安全和使用寿命,不仅要求输送带既耐高温,又要具有一定的阻燃性能。
输送带的耐高温阻燃性能主要取决于覆盖胶的性能,为此,我们研制了耐高温阻燃输送带覆盖胶。
覆盖胶的耐热性能达到了GB/T20021—2017中T4级别的要求,阻燃性能达到了GB/T10822—2014标准中K2级别要求。
本文详细阐述了研制过程。
1 试验1.1 主要原材料二元乙丙橡胶CO054,意大利埃尼公司产品;三元元乙丙橡胶S537-3,韩国SK 公司产品;Sunpar2280石蜡油,美国太阳公司产品。
固体氯化石蜡70、十溴二苯醚、十溴二苯乙烷等均为市售材料。
1.2 主要仪器和检测设备DLL -5000N 拉力试验机,MDR -2000无转子硫化仪,均为上海德杰仪器设备有限公司产品。
GT -7017高温老化试验箱、滚筒磨耗试验机均为高铁检测仪器有限公司产品。
2 耐高温阻燃覆盖胶配方的研制2.1 胶种的选择我们都知道,橡胶所谓的耐热性就是在高温长时耐高温阻燃输送带覆盖胶的研制赵明德(山东一诺胶带有限公司,山东 潍坊 262600)摘要:介绍了耐高温阻燃输送带覆盖胶的研制,经优化组合最终确定覆盖胶配方为:乙丙胶CO054/S537-3 70/30,炭黑N220 50,Sunpar 2280/HY209树脂20,阻燃剂十溴二苯乙烷/三氧化二锑/硼酸锌 16/8/7,过氧化二异丙苯/TAIC 6,防老剂MB/MC445 4。
采用该配方生产的输送带耐热性能达到了GB/T20021—2017中T4级别要求,阻燃性能达到了GB/T10822标准K2级别要求。
关键词:耐高温阻燃输送带;耐高温;阻燃;覆盖胶中图分类号:TQ330.12文章编号:1009-797X(2024)03-0021-04文献标识码:B DOI:10.13520/ki.rpte.2024.03.005间热老化作用下保持原有物理性能的能力。
橡胶输送带覆盖胶的配方优化设计
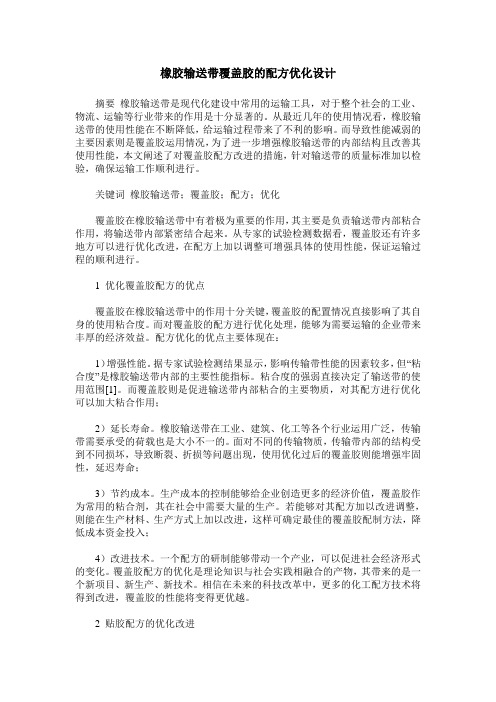
橡胶输送带覆盖胶的配方优化设计摘要橡胶输送带是现代化建设中常用的运输工具,对于整个社会的工业、物流、运输等行业带来的作用是十分显著的。
从最近几年的使用情况看,橡胶输送带的使用性能在不断降低,给运输过程带来了不利的影响。
而导致性能减弱的主要因素则是覆盖胶运用情况,为了进一步增强橡胶输送带的内部结构且改善其使用性能,本文阐述了对覆盖胶配方改进的措施,针对输送带的质量标准加以检验,确保运输工作顺利进行。
关键词橡胶输送带;覆盖胶;配方;优化覆盖胶在橡胶输送带中有着极为重要的作用,其主要是负责输送带内部粘合作用,将输送带内部紧密结合起来。
从专家的试验检测数据看,覆盖胶还有许多地方可以进行优化改进,在配方上加以调整可增强具体的使用性能,保证运输过程的顺利进行。
1 优化覆盖胶配方的优点覆盖胶在橡胶输送带中的作用十分关键,覆盖胶的配置情况直接影响了其自身的使用粘合度。
而对覆盖胶的配方进行优化处理,能够为需要运输的企业带来丰厚的经济效益。
配方优化的优点主要体现在:1)增强性能。
据专家试验检测结果显示,影响传输带性能的因素较多,但“粘合度”是橡胶输送带内部的主要性能指标。
粘合度的强弱直接决定了输送带的使用范围[1]。
而覆盖胶则是促进输送带内部粘合的主要物质,对其配方进行优化可以加大粘合作用;2)延长寿命。
橡胶输送带在工业、建筑、化工等各个行业运用广泛,传输带需要承受的荷载也是大小不一的。
面对不同的传输物质,传输带内部的结构受到不同损坏,导致断裂、折损等问题出现,使用优化过后的覆盖胶则能增强牢固性,延迟寿命;3)节约成本。
生产成本的控制能够给企业创造更多的经济价值,覆盖胶作为常用的粘合剂,其在社会中需要大量的生产。
若能够对其配方加以改进调整,则能在生产材料、生产方式上加以改进,这样可确定最佳的覆盖胶配制方法,降低成本资金投入;4)改进技术。
一个配方的研制能够带动一个产业,可以促进社会经济形式的变化。
覆盖胶配方的优化是理论知识与社会实践相融合的产物,其带来的是一个新项目、新生产、新技术。
- 1、下载文档前请自行甄别文档内容的完整性,平台不提供额外的编辑、内容补充、找答案等附加服务。
- 2、"仅部分预览"的文档,不可在线预览部分如存在完整性等问题,可反馈申请退款(可完整预览的文档不适用该条件!)。
- 3、如文档侵犯您的权益,请联系客服反馈,我们会尽快为您处理(人工客服工作时间:9:00-18:30)。
实验总结专业班级:高分子1033班组别:第三组姓名:蒋啟富学号:04指导老师:邹一明老师普通运输带上覆盖胶工艺任务一普通运输带上覆盖胶配方设计一、橡胶配方设计的原则橡胶配方设计的原则可以概况如下:1、保证硫化胶具有指定的技术性能,使产品优质。
2、在胶料和产品制造过程中加工工艺性能良好,使产品达到高产。
3、成本低、价格便宜。
4、所用的生胶、聚合物和各种原材料容易得到。
5、劳动生产率高,在加工制造过程中能耗少。
6、符合环境保护及卫生要求。
7、任何一个橡胶配方都不可能在所有性能指标上达到全优。
在许多情况下,配方设计应遵循如下设计原则:在不降低质量的情况下,降低胶料的成本;在不提高胶料成本的情况下,提高产品质量。
要使橡胶制品的性能、成本和加工工艺可行性三方面取得最佳的综合平衡。
用最少物质消耗、最短时间、最小工作量,通过科学的配方设计方法,掌握原材料配合的内在规律,设计出实用配方。
二、对运输带上覆盖胶的性能要求1、由于运输带上覆盖胶会与被输送物体直接接触,因此对上覆盖胶要求抗冲击性好,耐磨性好。
2、由于上覆盖胶直接暴露于空气中,且可能输送易腐蚀的物品,为提高运输带的使用时间及质量,因此要求上覆盖胶具有耐天候性。
3、由于上覆盖胶要与带芯贴合,因此,要求上覆盖胶必须具有一定的附着性。
4、由于配方不仅仅是理论上的,而且要用于实际的生产中,因此还要求配方设计的同时,还需考虑加工工艺的可行性。
三、配方(最终配方)装胶量:10kg换算系数=Q/基本配方总质量=2/154.5=0.0129含胶率=生胶份数/总份数*100% =100/154.5*100%=65%四、生胶的选用1、烟片胶2号:优点对橡胶具有防腐和老化的作用,且综合性能好,保存期长,物理性能好不足:价格较昂贵,成本较高2、丁苯橡胶:优点因为SBR中含苯环,苯环分子量高,较稳定,所以SBR 耐磨性好,耐化学腐蚀性好。
缺点就是丁苯胶结构不规整,在拉伸和冷冻条件下不能结晶,所以SBR无自补强性,且SBR硫化速度慢。
改善方法:①利用助剂来改善硫化速度②生胶的并用能改善不少性能。
这两种途径不仅提高了制品耐寒性、耐撕裂性,并且节约了一定的成本。
NR与SBR并用效果:NR/SBR并用时,硫化胶具有良好的物理机械性能,尤其是采用溶聚丁苯橡胶,并用后效果更加明显。
如:拉伸强度和定伸应力等都有大幅提高。
五、配合剂的选用1、硫化体系(硫磺、促进剂、活性剂、防焦剂)a、硫磺硫化剂:能使橡胶分子链起交联反应,使线形分子形成立体网状结构,可塑性降低,弹性剂强度增加的物质。
在天然胶中,与硫黄配合,能防止硫化返原,改善耐热性,降低生热,耐老化,提高橡胶与帘子线粘合力和硫化胶模量。
在本实验中,选用硫磺为硫化剂。
选择传统硫化体系(硫磺用量为2~3份),实际硫磺用量为2份,该体系能使硫化胶结构产生70%以上的多硫交联键,且硫化胶的拉伸强度高,耐磨性和抗疲劳龟裂性好。
缺点就是耐热老化性能差。
改善方法:有防老体系给予互补。
b、促经剂(促M、促NOBS)促M:具有快速硫化作用,对天然胶具有增塑作用,焦烧时间中等,增塑作用改善弹性,提高耐寒性。
促NOBS:本品为磺酰胺类硫化促进剂,是一种迟效高速硫化促进剂,起始硫化很慢,但后效优良。
可用作大多数橡胶的硫化促进剂,但不宜用于氯丁橡胶。
硫化时易分散,硫化后的产品不喷雾、色变小,可用于轮胎、内胎、胶鞋、胶带等胶料。
c、活性剂(HST、ZnO、MgO)HST(硬脂酸):可作硫化剂、增塑剂、软化剂,改善橡胶性能,使其橡胶分子双键酸性氧化,而加速交联键的形成,配合氧化锌的作用,使橡胶更易加工,也可用月桂酸代替。
ZnO(氧化镁):氧化镁在橡胶中的作用是用于作催化剂和促进剂。
他采用难于生成多硫键的硫化体系,使得过硫程度愈高愈好。
他的纯胶配方,若要加入填充剂时,尽量选用弱补强剂,而且用量愈少愈好。
氧化镁则是最好的选择。
氧化镁的白色填充剂与橡胶之间的结合,使得橡胶具有耐磨性。
MgO:可作硫化剂又可作活性剂,提高硫化速度和流化程度,因不溶于橡胶,所以必须加硬脂酸并用产生能溶于橡胶的锌皂,使其活性左用得以充分发挥。
d、防焦剂:无。
由于丁苯橡胶硫化速度慢,且软化增塑体系中使用的松焦油(在低温下有迟延硫化防止焦烧的作用),因此胶料在硫化时焦烧时间足够长,所以在该配方中无需加入防焦剂。
2、软化增塑体系固体古马隆:本品有助于配合剂在胶料中分散,并有增加黏性的作用,可以提高制品的耐寒性,为通用性软化剂。
在低温下有迟延硫化防止焦烧的作用,防止焦烧的作用。
且松焦油对噻唑类促进剂有活化作用。
3、补强填充体系1)、轻质碳酸钙:适用于丁苯橡胶,在高填充下不会导致过高定伸应力,能改善胶料的拉伸强度,撕裂强度和耐磨性,在胶料中易分散,不迟延硫化。
2)、陶土:补强剂填充剂,在再生胶中主要是提高再生胶的拉伸强度,但是副作用在于增加了再生胶的邵氏硬度和降低再生胶的扯断伸长率。
用陶土的胶料易加工,提高胶料粘度,增大挺性,减少收缩率,降低成本。
4、防老体系(防老剂A、防老剂D)橡胶的老化相关知识:橡胶老化是指橡胶分子在受到氧、臭氧、酸、碱、及水等物质的作用或在热、紫外线、放射线、机械力等物理、生物因素作用下,结构发生了复杂的物理化学变化。
使橡胶的使用物性出现逐渐降低的现象。
橡胶老化的因素众多,有热氧老化、重金属催化老化、紫外线催化裂解、臭氧老化及动态疲劳老化。
热氧老化是橡胶老化最重要的氧化作用,由于橡胶制品是在空气中贮存或使用。
所以氧化是最基本、最普遍的一种老化因素。
温度对氧化有很大的影响,提高温度会加快橡胶氧化反应。
橡胶制品在高温动态下使用时,生热提高,加快了橡胶的老化速度。
胺类防老剂,这类防老剂防护效果突出,品种最多它们的主要作用是抗氧剂、抗臭氧化,对热、重金属、紫外线催化及疲劳老化都有显著的防护效果。
唯一缺点是有污染性,不宜用于白色、浅色制品中。
这类防老剂又可分为胴胺类、醛胺类、二芳仲胺类、二苯胺类、对苯二胺类以及苯烷基芳基仲胺类六个类型。
二芳基仲胺类防老剂它是早期的品种之一,如防老剂A、D,对热氧化、屈挠疲劳有较好的防护效果,但对抗臭氧能力较差。
六、总结(四大体系详细资料)*软化增塑体系(一).增塑剂的作用1.改善橡胶的加工工艺性能:通过降低分子间作用力,使粉末状配合剂更好地与生胶浸润并分散均匀,改善混炼工艺;通过增加胶料的可塑性、流动性、粘着性改善压延、压出、成型工艺。
2.改善橡胶的某些物理机械性能:降低制品的硬度、定伸应力、提高硫化胶的弹性、耐寒性、降低生热等。
3.降低成本:价格低、耗能省。
(二).增塑剂的分类1.根据作用机理分:物理增塑剂:增塑分子进入橡胶分子内,增大分子间距、减弱分子间作用力,分子链易滑动。
化学增塑剂:又称塑解剂,通过力化学作用,使橡胶大分子断链,增加可塑性。
大部分为芳香族硫酚的衍生物如2-萘硫酚、二甲苯基硫酚、五氯硫酚等。
2.按来源分:①石油系增塑剂②煤焦油系增塑剂③松油系增塑剂④脂肪油系增塑剂⑤合成增塑剂(三).对增塑剂的要求增塑效果好,用量少,吸收速度快;与橡胶的兼容性好,挥发性小、不迁移、耐寒性好,耐水、耐油、溶剂;电绝缘性好,耐燃性好,无色、无毒、无臭,价廉易得。
(四)橡胶增塑剂的选用原则:一种理想的橡胶增塑剂应具备以下条件:①与橡胶等原材料的兼容性好;②对硫化胶或热塑性弹性体等产品的物理性能无不良影响;③充油和加工过程中挥发性小;④在用乳聚工艺合成的充油橡胶生产中应具有良好的乳化性能;⑤在生胶混炼过程中应使其具有良好的加工性、操作性及润滑性;⑥环保、无污染;⑦具有良好的光、热稳定性;⑧质量稳定,来源充足,价格适中。
当然,十全十美的理想橡胶增塑剂是没有的。
橡胶增塑剂生产厂通常按照用户的要求,有针对性地选择原料,重点解决用户所关心的主要性能指针,同时还提供系列产品供用户选择。
生胶、助剂、橡胶配合与加工共同组成了橡胶及其制品的生产过程。
橡胶增塑剂作为橡胶的增塑体系,在橡胶的配合与加工过程中应用得越来越广泛,是橡胶行业中仅次于生胶和炭黑的第三大材料。
(五)、橡胶增塑剂关键的特性是它们各自所表现的与橡胶的兼容性和稳定性,相对而言,三大类橡胶增塑剂的优缺点如下。
(1) 石蜡基橡胶增塑剂的抗氧化性和光稳定性较好,但兼容性和低温性相对较差,因此在很多应用场合,由于石蜡基橡胶增塑剂与橡胶的兼容性较差,无法提供良好的加工性能。
(2) 芳香基橡胶增塑剂与橡胶的兼容性最好,所生产的橡胶产品强度高,可加入量大,价格低廉;但颜色深、污染大、毒性大,随着环保要求的日益提高,使用上逐步受到限制。
(3) 环烷基橡胶增塑剂兼具石蜡基和芳香基的特性,其兼容性较好,且无污染、无毒,适应的橡胶胶种较多,应用广泛,是最理想的橡胶增塑剂。
通常遵循物质相似兼容原理,芳香基橡胶增塑剂主要用于SBR,BR,NR和CR等橡胶制品的生产;石蜡基橡胶增塑剂主要用于EPDM,IIR和IR等橡胶制品的生产;环烷基橡胶增塑剂主要用于SBR,BR和NR等热塑性弹性体及橡胶制品的生产,也广泛用于IIR,IR和EPDM 等橡胶制品的生产。
若是加工与生活日用品有关的橡胶制品,则橡胶增塑剂的毒性是关键指标,因此需要推荐使用优质环保型橡胶增塑剂,而芳香基橡胶增塑剂是目前世界公认的致癌物,故不可使用。
但是考虑到综合成本问题,芳香基橡胶增塑剂在对健康要求不高的场合仍然大量使用,如生产轮胎等橡胶制品,但在生产过程中要特别注意对工人的劳动保护。
选择橡胶增塑剂的种类和具体粘度等级主要根据用户所采用的原材料、生产工艺及生产成本等综合而定。
(六)各种橡胶与橡胶增塑剂类型的选择(1).SBR硫化胶中含有约百分之三十与硫化无关的低相对分子质量部分。
以适宜粘度的橡胶增塑剂加入高相对分子质量的SBR 中替代低相对分子质量部分,既可保持SBR硫化胶的物理性能,又改善了胶料的加工性能,同时还降低了胶料生产成本,增大了SBR的产量。
根据物质相似兼容原理及用途和使用场合的不同来选用橡胶增塑剂,如轮胎要求良好的物理性能,且基本不与人体长期接触,因此可填充芳香基橡胶增塑剂。
5.NR充油后具有以下特点:柔软性好,易于混炼加工;抗湿滑性能好,可提高轮胎的耐磨性;但抗撕裂性能下降,扯断永久变形大,主要适用于制造雪地防滑轮胎。
含油量大的NR硫化胶的物理性能明显低于普通NR硫化胶;而炭黑补强充油NR硫化胶老化后的物理性能保持率较好。
对于像NR这样的结晶性橡胶,如果填充稠环芳烃含量大的橡胶增塑剂,有可能破坏橡胶分子链的结晶性,使硫化胶的物理性能下降;而使用体积较大、稠环芳烃含量较小的橡胶增塑剂,对橡胶分子链的结晶性影响较小,橡胶增塑剂的添加量可以增大。
因此填充NR的橡胶增塑剂主要采用芳香基或环烷基橡胶增塑剂。
由于构成橡胶的单体不同,与之相适应的橡胶增塑剂种类也不同。