集装箱船船体建造施工工艺模板
船体拼板工艺

拼板工艺一、适用范围1. 适用于内底板、各层甲板、平台板、纵横舱壁、围壁、及平直的外板的拼板。
2.二、工艺内容1、拼板工艺过程船体内底板、各层甲板、平台板、纵横舱壁、围壁、及平直的外板等大面积平板均需预先拼板,其工艺过程如下:1)按照施工图纸(或样台草图)的要求,核对钢板后,同时检查钢板正反面,严重锈蚀夹层或被割穿等,直线边缘平直度边缘坡口等情况,然后,在拼板前应将刨过边的钢板边缘用砂轮或角磨机等工具除锈,一切符合拼板要求后,将钢板铺放在平台上。
2)将钢板基准端的边缘校对平齐,用花篮螺丝紧固,对于薄板可用撬杆撬紧,如果不用花篮螺丝紧固,在定焊时要先在中间和两端固定,然后在加紧密定位焊。
3) 拼板时,若有边缝、端缝时,一般先拼装边缝。
若先装端缝,由于边缝尺寸较长,定位焊的收缩变形较大,可能产生如下图所示的间隙,则边缝的修正量就较大。
但在焊接时为了减少焊接应力,应按先焊端缝,后焊边缝的工艺程序。
4)对于大面积钢板拼接可分成几片分别拼接,随后再进行片与片之间的横向拼接,为了减少横缝的切割工作量,在拼接时应尽将端缝对齐。
5)采有自动焊时,应在板缝的两端设置引弧板和熄弧板其规格一般为100×100左右,厚度与所拼钢板厚度相当。
板缝间隙要求板厚(mm)手工焊自动焊≤6 0.5-10(局部允许<2)不开坡口:全部≤0.5若>0.5时,应先作手工封底焊。
开坡口:1∶1.57-10 1-1.5(<2.5)12-14 1.5-2(<3)14-16 2-2.5板缝应平齐错边量:≤1mm2、T型材的装配焊接2.1T型材的装配焊接T型材是由腹板和面板组合而成,其中较宽的腹板上安装一定数量的型钢扶强材。
T型材采用在船体结构中有如下构件:强肋骨;强横梁、舷侧纵桁、甲板纵桁、单底船的肋板、中龙骨、旁内龙骨、舱壁的水平桁材和垂直桁材等等。
T型材分平直与曲线两类,凡是平直T型材采用翻身装法,曲线T型材在简易胎架上进行侧装法装焊。
855TUE集装箱船体施工要领
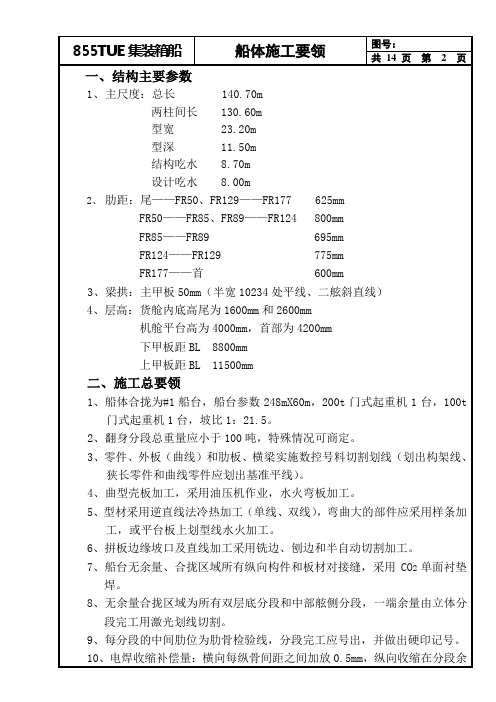
855TUE集装箱船船体施工要领图号:共14 页第 2 页一、结构主要参数1、主尺度:总长 140.70m两柱间长 130.60m型宽 23.20m型深 11.50m结构吃水 8.70m设计吃水 8.00m2、肋距:尾——FR50、FR129——FR177 625mmFR50——FR85、FR89——FR124 800mmFR85——FR89 695mmFR124——FR129 775mmFR177——首 600mm3、梁拱:主甲板50mm(半宽10234处平线、二舷斜直线)4、层高:货舱内底高尾为1600mm和2600mm机舱平台高为4000mm,首部为4200mm下甲板距BL 8800mm上甲板距BL 11500mm二、施工总要领1、船体合拢为#1船台,船台参数248mX60m,200t门式起重机1台,100t门式起重机1台,坡比1:21.5。
2、翻身分段总重量应小于100吨,特殊情况可商定。
3、零件、外板(曲线)和肋板、横梁实施数控号料切割划线(划出构架线、狭长零件和曲线零件应划出基准平线)。
4、曲型壳板加工,采用油压机作业,水火弯板加工。
5、型材采用逆直线法冷热加工(单线、双线),弯曲大的部件应采用样条加工,或平台板上划型线水火加工。
6、拼板边缘坡口及直线加工采用铣边、刨边和半自动切割加工。
7、船台无余量、合拢区域所有纵向构件和板材对接缝,采用CO2单面衬垫焊。
8、无余量合拢区域为所有双层底分段和中部舷侧分段,一端余量由立体分段完工用激光划线切割。
9、每分段的中间肋位为肋骨检验线,分段完工应号出,并做出硬印记号。
10、电焊收缩补偿量:横向每纵骨间距之间加放0.5mm,纵向收缩在分段余2、分段上船台、货舱平行舯体部分立体分段无余量船台合拢。
首尾立体分段一端正作,另一端留有船台切割余量。
3、横向纵骨间加放0.5、纵向强框架间加放1mm焊接补偿值。
4、机舱FR50向尾分段、首部FR170向首分段、基线放1/1000船台反变形,详见第十条船体变形控制。
(完整版)建造船舶船体焊接工艺
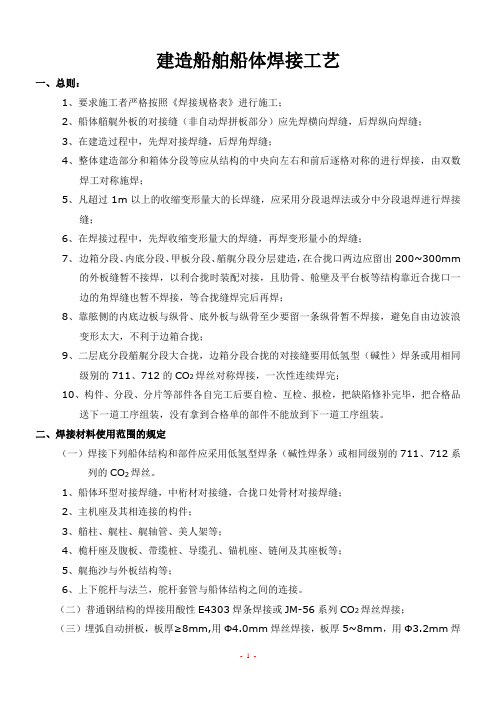
建造船舶船体焊接工艺一、总则:1、要求施工者严格按照《焊接规格表》进行施工;2、船体艏艉外板的对接缝(非自动焊拼板部分)应先焊横向焊缝,后焊纵向焊缝;3、在建造过程中,先焊对接焊缝,后焊角焊缝;4、整体建造部分和箱体分段等应从结构的中央向左右和前后逐格对称的进行焊接,由双数焊工对称施焊;5、凡超过1m以上的收缩变形量大的长焊缝,应采用分段退焊法或分中分段退焊进行焊接缝;6、在焊接过程中,先焊收缩变形量大的焊缝,再焊变形量小的焊缝;7、边箱分段、内底分段、甲板分段、艏艉分段分层建造,在合拢口两边应留出200~300mm的外板缝暂不接焊,以利合拢时装配对接,且肋骨、舱壁及平台板等结构靠近合拢口一边的角焊缝也暂不焊接,等合拢缝焊完后再焊;8、靠舷侧的内底边板与纵骨、底外板与纵骨至少要留一条纵骨暂不焊接,避免自由边波浪变形太大,不利于边箱合拢;9、二层底分段艏艉分段大合拢,边箱分段合拢的对接缝要用低氢型(碱性)焊条或用相同级别的711、712的CO2焊丝对称焊接,一次性连续焊完;10、构件、分段、分片等部件各自完工后要自检、互检、报检,把缺陷修补完毕,把合格品送下一道工序组装,没有拿到合格单的部件不能放到下一道工序组装。
二、焊接材料使用范围的规定(一)焊接下列船体结构和部件应采用低氢型焊条(碱性焊条)或相同级别的711、712系列的CO2焊丝。
1、船体环型对接焊缝,中桁材对接缝,合拢口处骨材对接焊缝;2、主机座及其相连接的构件;3、艏柱、艉柱、艉轴管、美人架等;4、桅杆座及腹板、带缆桩、导缆孔、锚机座、链闸及其座板等;5、艉拖沙与外板结构等;6、上下舵杆与法兰,舵杆套管与船体结构之间的连接。
(二)普通钢结构的焊接用酸性E4303焊条焊接或JM-56系列CO2焊丝焊接;(三)埋弧自动拼板,板厚≥8mm,用Ф4.0mm焊丝焊接,板厚5~8mm,用Ф3.2mm焊丝焊接;三、间断焊角接焊缝,局部加强焊的规定1)组合桁材、强横梁、强肋骨的腹板与面板的角焊接缝在肘板区域内应为双面连续焊;2)桁材、肋板、强横梁、强肋骨的端部加强焊长度应不小于腹板的高度,但间断的旁桁材端部可适当减小但要≥300mm;3)纵骨切断处端部的加强焊长度应不小于1个肋距;4)骨材端部削斜时,其加强焊长度不小于削斜长度,在肘板范围内应双面连续焊;5)用肘板连接的肋骨、横梁、扶强材的端部的加强焊,在肘板范围内应双面连续焊;6)各种构件的切口、切角、开孔(如流水孔、透气孔、通焊孔等)的两端应按下述长度进行包角焊;①当板厚>12mm时,包角焊长度≥75mm;②当板厚≤12mm时,包角焊长度≥50mm;7)各种构件对接接头的两侧应有一段对称的角焊缝其长度不小于75mm;四、其他的规定:1)锚机座、链闸、系缆桩底座、桅杆底座等受力部位的甲板与横梁、纵骨等是间断焊缝的应改为双面连续角缝。
35M—406TEU集装箱船船体建造施工工艺 1

135M—406TEU集装箱船船体建造施工工艺1、概述1-1本船船型方艏方艉、双桨双舵并设置导流管装置,全船FR0~FR19为艉尖舱;FR19~FR39为机舱;FR39~FR44为隔离舱;FR44~FR237为货舱;FR237~FR250为辅机舱;FR250~艏为艏尖舱。
1-2本船船体建造按“LR”船级社《入级和建造规范》和有关法定检验技术规则及图纸和CCS检验标准及生产设计图纸建造工艺等有关技术文件。
1-3主尺度:船长134.92M两柱间长132.54M船宽15.00M型深4.90M满载吃水3.60M肋距0.52M梁拱0.200M1-4船体结构:本船主船体为双层底、双舷侧、单甲板、大舱口;艏艉尖舱、机舱及辅机舱均为单底、单舷侧、单甲板;艉甲板室为半埋入式。
该船结构形式:货舱区;双层底;舷侧箱体均为混合骨架式,艏艉舱、机舱、辅机舱及甲板室均为横骨架式结构。
1-5船体材料:⑴本船船体采用钢材经“LR”船级社认可,应符合“LR”船级社《入级和建造规范》技术要求。
全船板材及型材,根据规定的要求进行预处理。
⑵焊接材料①埋弧自动焊焊丝及焊剂选用。
对AH36高强度结构钢,选用H08MnA焊丝,选配焊剂430;其它普通结构钢均采用H08A焊丝,选配焊剂430或431均可采用。
②CO2气保焊丝的选用;对AH36高强度结构钢,选用H08Mn2siA焊丝;其它普通结构钢均选用H08Mn2si焊丝。
③手工焊焊条的选用;对AH36高强度结构钢焊缝,大环缝及重要结构焊缝均采用E5015低氢焊条,船体其它结构选用4303酸性焊条。
2、船体建造方案:根据本厂起重设备、生产场地、生产加工设备及船体分段转场运输,起吊能力等因素;⑴FR0~FR19(即101艉分段)采用反身建造法;⑵FR19~FR44(BL102机舱双层底分段)采用反身建造法;舷侧(SL102p/s)分段采用卧式建造法;⑶FR44~FR237(BL201~BL208货舱双层底分段)采用正造法;舷侧(SL201~SL208p/s分段)采用卧式建造法;⑷FR237~FR250(BL301辅机舱双层分段)采用反身建造法;舷侧(SL301p/s分段)采用卧式建造法;其FR237~FR250较甲板及平台甲板分段采用反身建造法;⑸FR250~艏(即301艏分段)采用反身建造法;⑹103甲板室分段采用平面分段制造然后组成立体分段;2-1分段划分和分段布置<详见生产设计分段划分图>2-2船体建造程序:2-2-1部件与组合件的装配——将加工各种零件组成部件和组合件(小合拢)2-2-2分段制造——将各种零件、部件组合件组成分段(中合拢)2-2-3将各分段及组合件、部件组成船体(大合拢)2-3船舶建造工艺流程:生产设计各种零件、构件数控下料及加工零件、构件装配及组合件组装船体分段的各种板件拼板埋弧自动焊各分段胎架制作各分段制造各分段船台大合拢各分段合拢缝的焊接焊缝无损探伤检测船体各舱室密性试验船、机、电、舾装件的装焊船体除锈涂装机电安装各居住舱室装潢机电设备调试和系泊试验航行试验船、机、电消缺交船。
集装箱船建造工艺流程
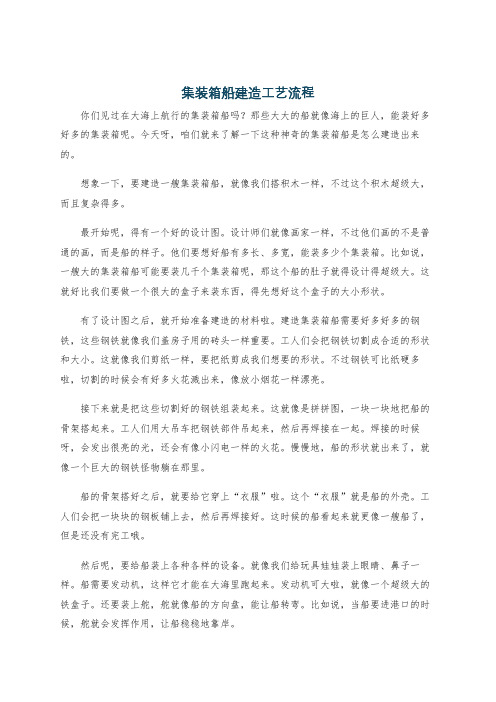
集装箱船建造工艺流程你们见过在大海上航行的集装箱船吗?那些大大的船就像海上的巨人,能装好多好多的集装箱呢。
今天呀,咱们就来了解一下这种神奇的集装箱船是怎么建造出来的。
想象一下,要建造一艘集装箱船,就像我们搭积木一样,不过这个积木超级大,而且复杂得多。
最开始呢,得有一个好的设计图。
设计师们就像画家一样,不过他们画的不是普通的画,而是船的样子。
他们要想好船有多长、多宽,能装多少个集装箱。
比如说,一艘大的集装箱船可能要装几千个集装箱呢,那这个船的肚子就得设计得超级大。
这就好比我们要做一个很大的盒子来装东西,得先想好这个盒子的大小形状。
有了设计图之后,就开始准备建造的材料啦。
建造集装箱船需要好多好多的钢铁,这些钢铁就像我们盖房子用的砖头一样重要。
工人们会把钢铁切割成合适的形状和大小。
这就像我们剪纸一样,要把纸剪成我们想要的形状。
不过钢铁可比纸硬多啦,切割的时候会有好多火花溅出来,像放小烟花一样漂亮。
接下来就是把这些切割好的钢铁组装起来。
这就像是拼拼图,一块一块地把船的骨架搭起来。
工人们用大吊车把钢铁部件吊起来,然后再焊接在一起。
焊接的时候呀,会发出很亮的光,还会有像小闪电一样的火花。
慢慢地,船的形状就出来了,就像一个巨大的钢铁怪物躺在那里。
船的骨架搭好之后,就要给它穿上“衣服”啦。
这个“衣服”就是船的外壳。
工人们会把一块块的钢板铺上去,然后再焊接好。
这时候的船看起来就更像一艘船了,但是还没有完工哦。
然后呢,要给船装上各种各样的设备。
就像我们给玩具娃娃装上眼睛、鼻子一样。
船需要发动机,这样它才能在大海里跑起来。
发动机可大啦,就像一个超级大的铁盒子。
还要装上舵,舵就像船的方向盘,能让船转弯。
比如说,当船要进港口的时候,舵就会发挥作用,让船稳稳地靠岸。
船里面也要装修呢。
要划分出不同的房间,有船员住的地方,还有放各种东西的仓库。
船员住的房间就像我们的小卧室一样,不过在船上会晃来晃去的。
就是把集装箱的固定装置安装好。
船舶建造报告模板范文

船舶建造报告模板范文1. 引言本报告基于 XXX 公司委托,描述了一艘载重量为 XXX 吨的集装箱货船的建造过程,包括设计、制造、试航和交付等环节。
船舶建造是一项繁琐复杂的过程,在本次建造中,我们克服了许多技术困难和挑战,最终按照客户的要求完成了船舶建造任务。
2. 设计根据客户的需求,我们设计了一艘载重量为XXX 吨的集装箱货船,船长XX 米,船宽 XX 米,船高 XX 米,吃水 XX 米。
此外,我们还为船舶装备了强大的动力系统和电子辅助设备,以确保船舶在航行中的安全和稳定性。
设计阶段是船舶建造过程中最关键的一步。
我们的设计团队经过反复打磨和优化,确保了船舶结构合理、功能齐备、稳定性良好。
其中最为关键的是船体设计,我们采用了独特的船体结构和材料,以提高船舶的承载能力和耐久性。
3. 制造制造阶段是船舶建造过程中最为繁琐的一步。
在制造过程中,我们遵循了严格的质量标准和流程,确保每一个细节都精益求精。
具体来说,我们采用了现代化的数控机床和自动化生产线,以提高生产效率和产品质量。
在制造过程中,我们还注重环保和可持续发展,采用了绿色材料和工艺,以降低船舶的碳排放和环境损害。
同时,我们还关注员工的健康和安全,提供了良好的工作环境和培训机会,以提高员工的专业素质和工作热情。
4. 试航试航阶段是船舶建造过程中最为关键的一步。
在试航过程中,我们通过测试和验证,确保船舶的性能和功能符合客户的要求和国际标准。
具体来说,我们进行了以下测试:•航速和馆速测试•航行稳定性和机动性测试•动力系统和电子设备测试•载重量和舱口封闭性测试所有的测试结果都证明了我们的船舶具有出色的性能和功能,能够满足客户的要求和航行需要。
5. 交付交付阶段是船舶建造过程中最为重要的一步。
在交付过程中,我们向客户交付了一艘完整的、符合要求的船舶,以满足客户的业务需求和市场需求。
在交付过程中,我们还提供了:•船舶操作和维护手册•船舶维修和保养服务•技术支持和培训服务通过交付阶段的工作,我们确保客户能够正确使用和维护船舶,并且能够最大限度地提高船舶的使用寿命和价值。
船体结构安装施工方案范本

一、工程概况工程名称:XX船舶建造项目工程地点:XX船厂工期:XX个月工程内容:船体结构安装,包括船体分段、肋骨、纵骨、横梁等主要构件的安装。
二、施工准备1. 人员准备(1)成立项目施工团队,明确各岗位责任;(2)组织施工人员参加技术培训,确保掌握施工技术要求;(3)配备充足的技术人员、管理人员和施工人员。
2. 材料准备(1)检查船体结构材料,确保符合设计要求;(2)对材料进行验收、检验,确保质量合格;(3)准备施工所需的各种工具、设备。
3. 施工设备准备(1)检查起重设备、焊接设备、切割设备等,确保其性能良好;(2)调试设备,确保其正常运行;(3)对设备进行定期保养和维护。
4. 施工场地准备(1)清理施工场地,确保场地平整、干净;(2)设置施工安全警示标志;(3)搭建施工临时设施,如办公室、休息室、仓库等。
三、施工工艺1. 船体分段安装(1)根据设计图纸,将船体分段运至施工现场;(2)采用吊装设备将分段吊装至指定位置;(3)对接分段,检查缝隙,调整尺寸;(4)进行焊接,确保焊接质量。
2. 肋骨、纵骨、横梁安装(1)根据设计图纸,将肋骨、纵骨、横梁等构件运至施工现场;(2)采用吊装设备将构件吊装至指定位置;(3)进行焊接,确保焊接质量;(4)检查构件连接部位,确保连接牢固。
3. 船体结构调整(1)根据设计图纸,调整船体结构,确保其符合设计要求;(2)检查船体结构,确保其稳定性;(3)进行加固处理,提高船体结构强度。
四、质量控制1. 材料质量:严格控制材料质量,确保材料符合设计要求;2. 施工质量:严格按照施工工艺进行施工,确保施工质量;3. 焊接质量:加强焊接过程控制,确保焊接质量;4. 结构调整质量:严格按照设计要求进行结构调整,确保结构质量。
五、安全措施1. 严格遵守国家有关安全生产法律法规;2. 加强施工人员安全教育培训,提高安全意识;3. 设置安全警示标志,确保施工安全;4. 定期检查施工设备,确保其安全运行;5. 制定应急预案,确保发生安全事故时能及时处理。
船体建造工艺

139.5米甲板驳船体建造工艺、概述1 •船型及航区1 -1本船为舟尾机型、球鼻首、单机单桨、双底单壳、单甲板结构型式。
货舱区底部及甲板舷侧为纵骨架式,赠醍区域为横骨架式。
1 • 2本船为139.5米甲板驳,设计航速12kn船舶主尺度:总长:139.50m垂线间131.40m 型宽32.00m型深:8.00m满载吃水5.40m二、建造方法根据该船纵向结构特点,本厂在船台上建造和船台上有起吊能力以双层底分段及舷侧分片,首、尾总装,构件组装等。
完成该船的建造。
三、船舶施工要求1 •放样与下料。
1 - 1肋骨型线放样在铁平台上进行。
铁平台应平整,四周应圈栏保护。
1 •2型线放样应按设计单位提供的型值表型值攀顺,凡涉及船舶主尺度、船体最大轮廓、设计水线进水角等位置点,不能改动。
1 - 3结构放样前,应先将结构位置线,夕卜板接缝线在肋骨型线图上划好。
1 •4所用钢材应预处理,原材料均应由CCS认可的钢厂生产,并盖有船检部门的印记,其表面不准有砂眼,凹陷、夹层、裂纹等缺陷。
1 •5曲线另件必须用样板下料,不能徒手划线;结构上的各种开孔,也应用开孔样板划线,用手工圆规切割。
1 •6结构下料时,应按板材规格事先作好套料卡片,然后按套料卡进行下料。
1 •7所有气割件的自由边缘应用电动砂轮机打磨光顺,焊接边应去徐毛疵;入孔、流水孔、透气孔、自由边应无毛刺,无割手感觉,具体标准按《中国造船质量标准》1998并经自检和检验合格后方送船台装配及组装成形边缘应整磨光顺。
1 •8尽量采用剪床剪切、圆规切割方法,进行零件下料切割。
1• 9本船采用整体建造法,如双层底结构,舷侧结构,机舱结构,首部结构。
局部采用分段分片建造,如横舱壁结构,球鼻首结构,主层甲板室结构等,局部采用分段建造,其分段完工后除留船台安装余量夕卜,其他装配余量或加工余量一律切除。
分段制作组立后,应注明中凡线、水平线和左右拢线,并打上仲痕作明显的标记,各散装件必须打上段号和件号。
- 1、下载文档前请自行甄别文档内容的完整性,平台不提供额外的编辑、内容补充、找答案等附加服务。
- 2、"仅部分预览"的文档,不可在线预览部分如存在完整性等问题,可反馈申请退款(可完整预览的文档不适用该条件!)。
- 3、如文档侵犯您的权益,请联系客服反馈,我们会尽快为您处理(人工客服工作时间:9:00-18:30)。
135M —272TEU集装箱船船体建造施工工艺1、概述1-1本船船型为尖船、方船艉、双渠、四舵并设导流管装置, 全船FR0~FR6为艉尖舱; FR6~FR37为机舱; FR37~FR213为舱口大货舱;FR213~FR224为辅机舱; FR224~FR235为艏尖舱。
1-2本船船体建造按”LR”船级社《入级和建造规范》和有关法定检验技术规则; [ CCS质量检验]标准及图纸; 生产设计工艺图纸; 工艺文件要求等有关技术文件。
1-3主尺度:船长135.00M船宽11.40M型深 3.95M满载吃水 3.50M肋距: FR0~FR37 0.50MFR212~FR235FR37~FR212 0.60M梁拱0.20M1-4船体材料:⑴本船船体结构? 用钢材为”LR”船级社认可的船用结构钢, 应符合”LR”船级社《入级和建造规范》要求。
全船船用板材及型材, 根据规格要求进行预处理。
⑵焊接材料①埋弧自动焊焊丝及焊剂选用H08A; 选配焊剂431或430均可。
②CO2气保焊焊丝选用H08Mnzsi。
③手工焊焊条: 船体合拢焊; 主副机座、系缆设备及盘轮系、轴系等重要结构均采用E5015低氢焊条, 船体其它结构选用E3015酸性焊条。
1-5船体结构:本船主船体结构: FR0~6为单底、单舷侧、单甲板; FR6~37为单底、双舷侧、单甲板; FR37~213为双底、双舷侧、单甲板; FR213~224为双底、双舷侧、双甲板; FR224~235为双底、单舷侧、单甲板。
本船结构型式均横骨架式。
2、船体建造方案:根据本厂起重设备、生产场地、生产加工设备及船体分段转场运输, 起吊能力等因素;⑴FR0~FR6艉分段采用反身建造法;⑵FR6~FR37机舱分段、船体分段采用反身建造法; 其舷侧箱体采用卧式建造法;⑶FR37~FR21大货舱双层底分段采用正造法; 其舷侧箱底分段采用卧式建造法;⑷FR213~FR224辅机舱双层分段采用反身建造法; 其舷侧箱体分段采用卧式建造法; 其升高甲板及平台甲板平面分段和FR224~FR235艏分段均采用反身建造法。
2-1 船体分段划分和编号<详见生产设计分段划分图>2-2 船体建造程序:2-2-1 部件与组合件的装配——将下料和加工的各种零件, 构件组装成部件和组合件( 小合拢)2-2-2 分段制造——将各种零件、组合件、部件组成分段( 中合拢)2-2-3 将各分段及组合件、部件组装成船体( 大合拢)2-3 船舶建造工艺流程:生产施工设计各种零件、构件数控下料及加工零件、构件及组合件的组装船体分段各种板件拼板自动焊各分段胎架制造各种分段制造各分段船台大合拢各分段合拢缝的焊接全船焊缝无损探伤检测船体各舱室密性试验船体、机、电、舾装件的装焊全船除锈涂装机电安装居住舱室装潢机电调试和系泊试验航行试验船、机、电消缺交船。
2-4 FR37~FR223货舱双层底分段制造工艺流程;分段胎架制作报检船底外板拼板自动焊及构件预制巡检船底板上胎架定位及勘划结构安装理论线报检安装实肋板安装船底纵桁及箱脚加强材船底结构焊接及打磨光洁报检除锈涂装内底板根据图纸要求开塞焊孔安装中部内底板( 边内底板待舷侧合拢焊接后安装) 内底板焊接脱胎架分段完整性的报检检测数据通待合拢。
2-5 FR37~FR213舷侧箱体制造工艺流程:分段胎架制作报检内外舷侧板拼板自动焊及框架、肋板预制巡检内舷侧上胎架定位及勘划结构理论线报检安装肋板及框架安装甲板边板及舱口围板加强材和舭部外板内结构焊接及打磨光洁报检安装外舷侧板分段结构焊接打磨光洁脱胎架后分段完整性的报检数据检测分段内部除锈涂装待合拢。
2-6 FR6~FR37机舱、船底、平面分段制造工艺流程;分段胎架制作报检纵横结构件及主机座预制主机座及船底纵向构件定位安装实肋板和各连接肘板及加强筋报检船底结构焊接安装船底外壳板外壳板缝刨焊外壳打磨光洁分段脱胎架翻身外壳板缝清根焊接及结构焊接和分段打磨光洁分段完整性报检数据检测分段内除锈涂装待合拢2-7 FR6~37机舱舷侧箱体分段和FR213~FR224辅机舱舷侧箱体分段, 制造工艺流程与”2-5”条款相类似。
2-8 FR0~FR6艉分段制造工艺流程:分段胎架制作报检艉封板、FR6横壁拼板自动焊及构件预制边甲板上胎架定位及勘划结构安装理论线肋板及纵向构件报检平台板结构及各连接肘板、加强筋的结构安装艉封板和FR6横舱壁的安装分段结构焊接外壳板安装外壳板缝刨焊艉轴弄结构及舵套筒的装焊脱架翻身分段内板缝刨焊及结构焊接分段打磨光洁分段完整性的报检数据检测内部除锈涂装。
2-9 FR224-FR235艏分段制造工艺流程与”2-8”条款相类似。
2-10 FR0~6升高甲板平面分段和FR213~FR224升高甲板及平台甲板制造工艺流程( 略)2-11 FR213~FR224辅机舱双层底分段制造工艺流程与””3、船体建造对各工艺阶段和各工序生产过程中的工艺要求2-4: 条款相似。
3-1、船体线型放样:根据线型图及型值采用电脑1: 1实尺放样。
3-1-1、船体线型放样时, 对线型图中的型值的修改一般不超过线型图中的图面比例。
3-1-2、船体线型放样时, 对船体主要尺度{总长、型宽、型深}; 船体艏艉, 舭部形状甲板边线型值和轴线尺寸, 均不允许修改。
3-1-3、船体外板、甲板、舱壁板排板时, 应根据板材规格, 船体结构; 外板加工能力, 同时, 结合《建造规范》有关规定和分段的加放余量等因素, 在提高钢材充分利用率的前提下, 应注意以下几点;⑴、船体外板, 甲板排板时, 应保证船底平板龙骨, 舭部外板, 舷侧顶列板, 甲板边板及重要区域结构板的加厚尺寸均应符合{规范}和图纸等有关技术要求。
⑵、船体外板, 甲板排板时, 船体平直面部分的板缝要求排成一条直线, 曲面部分的板缝要求光顺, 整齐, 以保证板缝美观; 根据{规范}有关规定: 对接板缝之间的平行距离应≥100mm; 板缝与结构角焊缝平行距离应≥50mm; 其板缝之间应尽量避免尖角相交, 若无法避免时, 其交角≥15。
⑶、放样完工后应提供完整的下料草图, 下料数据, 零构件的排板套料草图及加工样板, 下料清册等, 并标明零构件的编码代号, 加工符号, 安装理论线及余量的加放等因素。
3-2、进厂原材料的管理;3-2-1、进厂入库的原材料{若要求板材进行预处理的, 必须经预处理后入库}应检查钢材表面是否有麻点, 夹渣, 夹层及同板差等缺陷, 同时核对钢材的材质、规格、数量和钢材”质保书”等, 方能入库。
3-2-2、仓库保管员应根据钢材规格, 材质分别掛牌堆放。
3-3、船体板件、零构件的下料号料:3-3-1、船体结构件下料前, 应校对钢材的规格, 材质, 对钢材有明显的变形的应进行矫平, 校直后进行下料, 同时应检查其表面是否有缺陷和污物。
3-3-2、根据计算机的编程数控套料程序切割下料, 若采用手工下料构件的直线部分应尽量采用自动或半自动切割机下料, 手工下料时, 其切割边缘无明显的”锯齿形”, 应保证切割边缘的光洁度。
其切割边缘光洁度技术要求见{ CCS}质量检验标准。
3-3-3、构件下料时, 应尽量减少内结构件的接头, 若构件相接时, 接长部分应≥500mm, 其按头应尽量避免在构件的端部; ”T”构件的面板与腹板的接头应相互错开≥100mm; 其接头应开”V”型剖口焊透。
{剖口要求见生产设计分段图}3-3-4、对板厚差≥4mm的对接缝, 应削斜过渡, 其削斜长度应不小于板厚差的4倍{削斜结点图见生产设计分段图}3-3-5、零构件号料时, 应标明工程代号, 零构件名称和数量, 并号上安装, 加工理论线, 加工符号及加工装配余量线等。
3-4、零构件的加工;3-4-1、钢板弯曲和型材的弯制加工, 应尽量采用冷加工的方法; 若有部分零构件采用热加工时, 其加热温度应<900。
C; 加热重复次数不得超过三次以防降低钢材强度。
对零构件冷或热加工时, 表面要求光顺、光洁、无明显的压痕、皱折及”桔皮状”等缺陷。
3-4-2、零构件的机械剪切、折边、火焰切割等应确保零构件的外型尺寸,其误差≤1mm, 切割自由边打磨光洁。
3-4-3、对埋弧自动焊的钢板边缘加工, 若采用刨边或铣边时, 其边缘的直线度应控制≤1mm; 若采用自动或半自动切割其板边缘直线度≯1.5mm, 其边缘应打磨光洁。
3-5、部件, 组合件的装配; {小合拢}3-5-1、”T”型件的预制前应将该腹板、面板矫平、校直后进行装配; 腹板与面板装配后应加临时支撑固定后施焊; 施焊后应矫平、校直打磨光洁。
3-5-2、肋骨框架和半框架的装配;⑴、铁样台放样前, 对样台应保证平整, 其不平度≯2mm/m2; 放样时, 其线型与型值或样板的误差≤1.5mm, 其型线应用洋冲打制, 同时打制肋位号码。
⑵、肋骨框架预制时, 其框架与铁样台的型线误差≤1mm; 同时应保证肋骨与舭肘板及梁肘板的搭接长度符合图纸要求; 框架装成型后应加临时支撑固定后施焊; 并将舷侧桁安装位置线, 板缝线等标注在框架上{用洋冲打制}。
3-6、船体外板、内底板、内舷侧、甲板板缝等埋弧自动焊;3-6-1、焊接前的准备;⑴、钢板拼板前, 板边端面若有加工条件, 应进行刨边或铣边; 若无加要条件亦可采用其它方法加工, 但必须保证板缘直线度≤1.5mm, 拼板间隙≯2mm, 板边端面和板缝两边100mm范围内打磨光洁; 拼板时的点焊长度10mm, 点焊间距100~150mm。
⑵、焊接前焊剂应烘焙2~3小时, 其烘焙温度250~300。
C, 保温1-2。