铜合金线材表面裂纹形成原因及解决办法
金属裂缝的预防措施和处理方案

金属裂缝的预防措施和处理方案金属裂缝是在金属材料中产生的缺陷,可能导致结构的破坏和事故的发生。
为了确保金属结构的安全性和可靠性,采取适当的预防措施和处理方案是至关重要的。
下面是一些常见的预防措施和处理方案:预防措施1. 选择合适的材料:在设计和制造过程中,选择适合的金属材料可以减少裂纹的产生。
根据实际应用需求选择具有高强度和良好韧性的材料。
2. 控制应力:过高的应力可能导致金属材料的裂纹产生和扩展。
在加工和使用过程中,需要控制应力的大小和分布,避免产生应力集中区域。
3. 提供足够的支撑:对于承载重量的金属结构,提供足够的支撑可以减轻金属的应力,降低裂纹发生的概率。
4. 良好的设计:在金属结构的设计过程中,考虑到裂纹的产生和扩展的因素,采用合理的几何形状和结构设计,可以减少裂纹的可能性。
5. 定期检查和维护:定期对金属结构进行检查和维护是预防裂纹形成和发展的有效手段。
及时发现和修复潜在问题,可以防止裂纹的进一步发展。
处理方案1. 检测和评估:一旦发现金属结构中出现了裂纹,需要进行及时的检测和评估。
采用非破坏性检测技术,如超声波检测、射线检测等,确定裂纹的位置、大小和扩展情况。
2. 修复和加固:根据裂纹的具体情况,选择合适的修复和加固方法。
可能的处理方案包括焊接、补焊、全面更换或局部加固等。
3. 监测和验证:在处理完裂纹后,需要监测和验证修复效果。
采用合适的监测方法,如应变测量、振动监测等,确保修复后的金属结构能够正常工作。
总之,通过采取适当的预防措施和处理方案,可以有效地预防和处理金属裂纹问题,保证金属结构的安全和可靠性。
线材表面裂纹成因分析及控制方法

范要 求安装 , 成两 个辊 环上 对应 的上 下轧槽 错槽 ; 造
3 安装时与辊环接触配合 的抛油环 的制 造精度超 )
出尺 寸精 度要 求 , 造成 两 个 辊 环 上对 应 的上 下 轧槽 在安 装 时错槽 .
3 2 锯齿 裂纹 .
通条 的呈 一条 线或 两条线 沿 线材 长度 方 向分 布
的成品表面裂纹. 根据现场经验 , 一般可以确定 的原 因之一是 : 在预精轧机组 以后成 品道次前 的某个道 次, 轧机轧制 时轧 件过充满 , 出现 了单 边或双边耳 子, 再经过后续道次的轧制形成轧件表面裂纹缺陷.
轧件 在某 道 次形成 耳子 , 常见 原 因 主要有 下 面几 种 : 1 轧 件料 形尺 寸 分配 不 合 理 , 成某 道 次 轧 件 断 面 ) 造
Ab t a t h a s sr s o sb ef rt e s ra e c a k ome n w r o r nay e n d p e a t n g i s e d — sr c :T e c u e e p n i l o u fc r sf r d o ie r d a e a l z d,a rc u i s a a n tt e h c o h f cs p o o e n t e a t l . e t r p s d i h r c e i Ke r s i r o y wo d :w e r d;s ra e c a k;p e a t n uf r c c rcui o
按照 轧件 通过 的顺序 , 线工艺 布 置依 次为 : 轧 加
热后 钢坯 高压水 除鳞装 置一 粗轧机 组 ( 轧 机 ) 6架 一 1 飞剪 一 中轧 机 组 ( 号 6架 轧 机 ) 2号 飞剪 一 预精 — 轧机 组 ( 轧 机 , 6个立 活套 ) 1号 、 6架 有 一 2号 控 冷 水箱—3号飞 剪—水 平 侧 活 套一精 轧 机 ( G 8架 B V, 轧机 ) —3号 、 4号控 冷 水 箱一 双模 块 减 定 径 轧 机机
铜合金挤压材常见缺陷分析及预防

文章编号 : 1005- 2046 ( 2008) 02- 0081- 03
铜合金挤压材常见缺陷分析及预防
魏军伟
( 河南江河机械有限责任公司技术开发部 , 河南 鲁山 467337)
摘 要: 分析了铜合金挤压材常见缺陷 ( 裂纹、 气泡 、过热、 过烧、 划伤 、扭拧、 缩尾 、偏 心、 尺寸超差等 ) 的产生原因 , 提出了相应的预防措施 。生产实践表明 , 采取这些措施后 , 有效地改善了产品质量, 取得了良好的经济效益 。 关键词: 铜合金 ; 挤压材 ; 缺陷分析: 预防措施 +1 中图分类号 : TG146 1 文献标识码: C
2
2 1
气泡划伤、擦伤和碰伤
产生原因 划伤、擦伤和碰伤产生的原因 :
( 1) 由于挤压筒经长期使用后尺寸超差 , 挤 压时筒内气体未排除 , 变形金属表层沿前端弹性 区流出而造成气泡; ( 2) 铸锭表面有沟槽或铸锭组织中有气孔, 铸锭在镦粗时包进了气体 , 挤压时气体进入金属 表层 ; ( 3) 挤 压时铸锭或模 具表面带有水 分和油 污, 由于水和油污受热挥发成气体 , 在高温高压 的金属流动中被卷入金属表面而形成气泡; ( 4) 设备排气装置工作不正常; ( 5) 金 属挤压速 度过 快, 造成 挤压排 气不 良。 2 2 解决办法 解决的办法有: ( 1) 加强对铸锭的质量管理 , 严格控制铸锭 的表面质量; ( 2) 合理的选择和配备挤压工具 , 及时检查 更换。挤压筒直径方向的磨损量不得大于 2mm; ( 3) 保证设备的排气系统正常工作, 按要求 进行排气 ; ( 4) 剪刀、挤压筒和模具尽量不涂油 ; ( 5) 合理控制挤压速度。
( 1) 铸锭表面附有杂物或铸锭成分偏析。在 挤压过程中金属流经工作带时 , 这些偏析浮出物 或坚硬的金属颗粒附在工作带表面 , 或对工作带 造成损伤 , 最终对制品造成表面划伤; ( 2) 模具型腔或工作带上有夹杂物, 模具工 作带硬度较低 , 使工作面在挤压时受伤而划伤型 材; ( 3) 挤压工具 ( 模子、穿孔针) 变形或有裂 纹, 工具润滑不好; ( 4) 出料台不光或有尖角; ( 5) 在转下道工序时 , 制品的相互摩擦或挤 压造成损伤。 4 2 解决办法 解决的办法有: ( 1) 加强对铸锭质量的控制 ; ( 2) 提高修模质量, 模具定期氮化并严格执 行氮化工艺; ( 3) 用软质毛毡将制品与辅具分离, 尽量减 少制品与辅具的接触损伤 ; 生产中要轻拿轻放, 尽量避免随意拖动或翻 动型材。
详谈pcb钻孔孔壁镀铜开裂问题及解决方案-豆丁
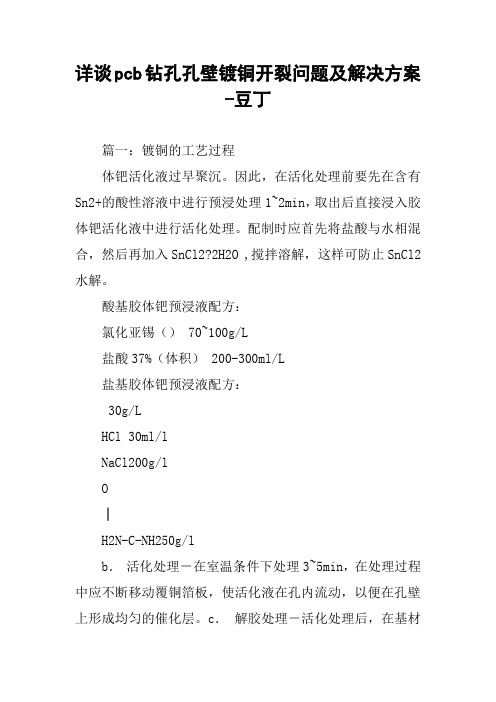
详谈pcb钻孔孔壁镀铜开裂问题及解决方案-豆丁篇一:镀铜的工艺过程体钯活化液过早聚沉。
因此,在活化处理前要先在含有Sn2+的酸性溶液中进行预浸处理1~2min,取出后直接浸入胶体钯活化液中进行活化处理。
配制时应首先将盐酸与水相混合,然后再加入SnCl2?2H2O ,搅拌溶解,这样可防止SnCl2水解。
酸基胶体钯预浸液配方:氯化亚锡() 70~100g/L盐酸37%(体积) 200-300ml/L盐基胶体钯预浸液配方:30g/LHCl 30ml/lNaCl200g/lO║H2N-C-NH250g/lb.活化处理-在室温条件下处理3~5min,在处理过程中应不断移动覆铜箔板,使活化液在孔内流动,以便在孔壁上形成均匀的催化层。
c.解胶处理-活化处理后,在基材表面吸附着以钯粒子为核心,在钯核的周围,具有碱式锡酸盐的胶体化合物。
在化学镀铜前,应将碱式锡酸盐去除,使活性的钯晶核充分暴露出来,从而使钯晶核具有非常强而均匀的活性。
经过解胶处理再进行化学镀铜,不但提高了胶体钯的活性,而且也显著提高化学镀铜层与基材间的结合强度。
常用的解胶处理液是5%的氢氧化钠水溶液或1%氟硼酸水溶液。
解胶处理在室温条件下处理1~2min,水洗后进行化学镀铜。
d.胶体铜活化液简介:明胶 2g/l/lDMAB(二甲胺基硼烷)5g/l水合肼 10 g/l钯20ppm配制过程:首先分别将明胶和硫酸铜用温水(40度C)溶解后将明胶加入至硫酸铜的溶液中,用25%H2SO4将PH值调至2..5当温度为45度C时,将溶解后DMAB在搅拌条件下缓慢加入上述的混合溶液中,并加入去离子稀释至1升,保温40~45度C,并搅拌至反应开始(约5~10分钟)溶液的颜色由蓝再变成绿色。
放置24小时颜色变成红黑色后加入水合肼。
篇二:PCB线路板镀铜表面粗糙问题原因分析PCB线路板镀銅表面粗糙问题原因分析可能原因如下:镀铜槽本身的问题1、阳极问题:成分含量不当导致产生杂质2、光泽剂问题(分解等)3、电流密度不当导致铜面不均匀4、槽液成分失调或杂质污染5、设备设计或组装不当导致电流分布太差…………当然作为镀铜本身来讲;以上问题导致粗糙的可能性不大前制程问题PTH制程带入其他杂质:1、活化成分失调钯浓度太高或者预浸盐残留板面2、速化失调板面镀铜是残有锡离子3、化学铜失调板面沉铜不均4、镀铜前酸洗不当导致板面残留杂质………………黑孔制程:微蚀不净导致残碳抗氧化不当导致板面不良烘干不良导致微蚀无法将板面碳剥除导致残碳电流输入输出不当导致板面不良…………篇三:化学镀铜常见故障和纠正方法-PCB工艺论文,SMT 技术文章-SMT专家网化学镀铜常见故障和纠正方法◎化学镀铜常见故障和纠正方法故障发生原因纠正方法化学镀铜空洞①钻孔粉尘,孔化后脱落①检查吸尘器,钻头质量,转速/进给等②加强去毛刺的高压水冲洗钻孔后孔壁裂缝或内层间分离检查钻头质量,转速/进给,以及层压板厚材料和层压工艺条件③除钻污过度,造成树脂变成海绵状,引起水洗不良和镀层脱落检查除钻污法工艺,适当降低去钻污强度④除钻污后中和处理不充分,残留Mn残渣检查中和处理工艺⑤清洁调整不足,影响Pd的吸附检查清洗调整处理工艺(如浓度、温度、时间)及副产物是否过量⑥活化液浓度偏低影响Pd吸附检查活化处理工艺补充活化剂⑦加速处理过度,在去除Sn的同时Pd也被除掉检查加速处理工艺条件(温度/时间/浓度)如降低加速剂浓度或浸板时间⑧水洗不充分,使各槽位的药水相互污染检查水洗能力,水量/水洗时间⑨孔内有气泡加设摇摆、震动等⑩化学镀铜液的活性差检查NaOH、HCHO、Cu2+的浓度以及溶液温度等⑾反应过程中产生气体无法及时逸出加强移动、振动和空气搅拌等。
黄铜带材冷轧开裂原因及其预防措施

裂, 造成产品改制 、 报废 的数量相 当惊人 , 严重影 响生
产效 率 , 经济 损失 巨大 。本 文 主 要分 析 造 成 黄铜 带 材 冷轧 开裂 的原 因 , 提 出 相 应 的控 制 与 预 防措 施 , 并 对
生产 具有 一定 的理论 和现 实 意义 。
黄铜带材开裂多属于前两种原因当存在有害元素或有害相时造成晶界偏析或反偏析导致晶界间结合力减弱因而在应力作用下产生沿晶开裂或断裂hj21金相组织的影响以h65黄铜为例由cu一盈相图可知缓慢冷却条件下h65为单相a黄铜而在实际生产中冷却速度较快为非平衡结晶包晶反应生成的b相来不及完全转化为a相而留在组织内部5
维普资讯
第3 7卷
第 5期
有 色 金 属 加 工
NONF ERROUS E M TAL S PROCESSI NG
Vo . 7 No 5 13 .
20 0 8年 8月
Oc o e o 8 tb r 0 2
黄铜 带材 冷 轧 开 裂原 因及 其 预 防措 施
致滑 移位错 在两 相 界 面形 成 塞 积群 , 当位 错 塞 积 造 成
1 黄 铜 带材 生产 工 艺
现代 黄铜板带材 的生产 , 通常采用水平连铸获取 大卷 重带 坯 J经 均匀 化退 火 、 面 后 , , 铣 以大 加工 率 冷
轧 开坯 , 后 再 进行 中 间退火 、 轧 等 工序 。此外 , 然 精 为
有 美丽 的光泽 , 良好 的强 度 、 性 与耐 蚀 性 , 来 越广 韧 越
变形程度时, 原子 问的结合力遭受破坏便 出现裂纹 。 按裂纹的扩展方式 , 可将开裂分为沿晶开裂 和穿晶开 裂。裂纹的扩展遵循能量消耗最小原理 , 也就是裂纹
铜合金锻件常见的缺陷与对策

铜合⾦锻件常见的缺陷与对策铜合⾦锻件常见的缺陷与对策(⼀)概述铜的最⼤特点是具有很⾼的导电、导热性能,以及良好的耐蚀性。
但是,⼯业纯铜的强度不⾼(约200MPa),因⽽限制了它作为结构材料的使⽤。
为了提⾼铜的强度,并赋予特殊的性能,在铜中加⼈适量的合⾦元素,从⽽获得铜合⾦。
铜合⾦具有较⾼的强度、韧性、耐磨性以及良好的导电、导热性能,特别是在空⽓中耐腐蚀。
因此,在电⼒、仪表、船舶等⼯业中得到了⼴泛的应⽤。
⼀些要求强度⾼、耐热、耐压⼜耐蚀的轴类、凸缘类和阀体类零件都⽤钢合⾦锻件来制造。
铜合⾦主要分为黄铜和青铜两⼤类。
以锌为主要合⾦元素的铜合⾦称为黄铜;以锡为主要合⾦元素的铜合⾦称为青铜。
此外,还有⽩钢等其它铜合⾦。
黄铜的牌号、代号和化学成分见表5-19。
变形青铜的牌号、代号和化学成分见表5-20及表5-21。
表5-21 特殊青铜的化学成分纯铜中的杂质主要有铅、铋、氧、硫、氢等。
铜中杂质的存在不仅对使⽤性能有较⼤影响,⽽且对铜的⼯艺性能也有极坏的作⽤。
加热温度和变形程度对铜合⾦的组织和性能影响很⼤,当变形程度处于临界变形程度范围时,将引起粗晶。
铜合⾦的临界变形程度范围⼤致是10%~15%,温度愈⾼,变形和再结晶后的晶粒尺⼨也愈⼤。
对于α+β铜合⾦(包括H62、H68、HPb59-1、QAl19-4等),如果加热温度超过α+β→β的转变点,此时由于失去了α相对β相晶界迁移的机械阻碍作⽤,因⽽晶界迁移速度很快,β晶粒迅速长⼤,使合⾦塑性降低,锻造中容易开裂,并常在锻件表⾯出现“蛤模⽪”。
粗化后的铜合⾦晶粒,即使采⽤⼤变形程度进⾏塑性变形,再结晶后的晶粒也是很粗的。
这是因为铜合⾦的层错能低,动态再结晶的速度快,⽽且,⼤变形时的热效应也较显著,故在⾼温下很快再结晶并迅速长⼤。
铜合⾦锻件组织中产⽣粗晶后,不能像碳钢那样,通过热处理的办法加以细化。
因此,将使产品的⼒学性能降低(见表5-22)。
冷变形和冷变形加时效处理对铜和铜合⾦性能有较⼤影响。
铜管裂缝修复方法
铜管裂缝修复方法全文共四篇示例,供读者参考第一篇示例:铜管在工业生产中被广泛使用,但由于使用时间较长或者其他原因可能会出现裂缝问题,裂缝会导致管道漏水,严重影响生产过程。
及时修复铜管裂缝至关重要。
下面将介绍一些常用的铜管裂缝修复方法。
一、替换法替换法是最常用和最有效的修复方法之一。
具体操作步骤如下:1、定位:首先需要确定裂缝的位置和大小。
可以通过视觉检查或使用专门的检测工具进行确认。
2、切割:在裂缝的周围留出一定的距离,使用管道切割工具将受损部分切割下来。
3、焊接:将新的铜管材料与原有管道焊接在一起,确保焊接质量。
4、检验:焊接完成后需要进行水压测试,确保管道没有漏水现象。
替换法的优点是修复效果好,可以保证管道的完整性和稳定性。
但缺点是需要专业的焊接技术和设备,操作难度较大,并且需要较长的维修时间。
二、充填法1、清洁:首先需要将裂缝周围清洁干净,去除杂质和污垢。
2、填充:使用专用的铜管填充胶或焊接胶填充裂缝,确保裂缝被填满。
3、固化:待填充胶固化后,再进行加固处理,确保填充物牢固。
充填法的优点是操作简单,成本较低,适用于临时的小裂缝修复。
缺点是修复效果不如替换法,且只能应对裂缝较小的情况。
三、升级法升级法是一种较为先进的修复方法,可以提高管道的整体强度和耐腐蚀性。
具体操作步骤如下:1、定位:确定裂缝的位置和大小。
2、表面处理:清洁裂缝周围的表面,去除氧化物和污垢。
3、涂层处理:在裂缝表面涂抹一层耐腐蚀的涂层,增加管道的耐腐蚀性。
4、局部加固:对裂缝处进行局部加固处理,增加管道的整体强度。
升级法的优点是能够增强管道的整体性能,延长使用寿命。
但缺点是操作相对复杂,需要专业的技术和设备支持。
对于铜管裂缝修复,不同的情况可采取不同的方法。
对于较大的裂缝,替换法是最佳选择;对于较小的裂缝,充填法比较适用;而对于提高管道整体性能的要求,升级法是不错的选择。
在实际应用中,需要根据具体情况选择合适的修复方法,并严格遵守操作规程,确保修复效果和管道的安全稳定运行。
铜棒型线材缺陷
铜及铜合金管棒型线材产品缺陷1 范围本标准规定了铜及铜合金管棒型线材中常见缺陷的定义及特征,分析了产生的主要原因,并给出部分典型图片。
本标准适用于铜及铜合金管棒型线材缺陷的分析与判定。
2 缺陷定义、特征、产生原因、典型图片。
2.1过热与过烧2.1.1定义及特征金属在加热或加工过程中,由于温度高、时间长,导致组织及晶粒粗大现象称为过热;严重过热,晶间局部低熔点组元熔化或晶界弱化现象称为过烧。
过热后管棒材表面出现麻点、桔皮、晶粒粗大、塑性下降;过烧管棒材表面粗糙,挤制后出现晶界裂纹,头部开花、张口裂或裂成碎块。
开裂部位能看到粗大枝晶和熔化的痕迹,显微组织中出现晶界加粗,熔化空洞或共晶球,熔化的液相网等。
2.1.2产生原因①加热温度高、时间长或者局部长时间处于高温源处②热挤终了温度过高或者在高温区停留时间长。
③合金中存在低熔点组元或低熔点夹杂较多。
2.2裂纹或开裂2.2.1定义及特征管棒型线材经加工或退火后出现连续和断续的不规则的裂缝,轻微的称为裂纹,严重的称为开裂。
开裂部位往往氧化有夹杂,形态各异,种类繁多。
常见的有:头部开裂、周期性横向开裂、纵向开裂、45°方向开裂、断裂以及热处理不当、氢气病等导致脆裂。
2.2.2产生原因①铸锭中存在裂纹、夹杂、缩孔、缩松及其它有害杂质,结晶组织、化学成份严重不均匀。
②铸锭中存在较大应力或加工工艺不当产生较大应力。
③加热温度过高、时间长导致过烧或加热温度低、时间过短、温度不均匀,材料塑性不良。
④挤压速度过快,加工率过大。
⑤热处理工艺不当,加工或热处理处于材料的脆性温度区。
2.2.3典型图片(图1-图13)图1 QSn7-0.2 1×图2 QSi1-3 1×过烧引起头部开裂热挤头部开裂图3 QAl10-3-1.5 2/3×图4 BAl10-2 1×周期性横裂周期性横裂图5 QAl10-3-1.5 1/2×图6 QSn7-0.2 1/2×45°方向开裂 45°方向开裂图7 HSn70-1 1×图8 QSn7-0.2 1×周期性横裂周期性横裂图9 Cu-Ni合金 1×图10 H62 1×塑性不良引起周期性裂口 45°方向开裂图11 H62 1/2×图12 HSn70-1 1/2×纵向、45°方向交错开裂纵向开裂图13 QAl10-4-4 1/3×加热工艺不当引起纵向开裂2.3应力腐蚀开裂2.3.1定义及特征铜制品(黄铜或白铜)在拉应力和特定腐蚀环境共同作用下发生脆性开裂现象称为应力腐蚀开裂。
铜合金线材表面裂纹形成原因及解决办法
铜合金线材表面裂纹形成原因及解决办法铜合金线材表面裂纹形成原因及解决办法现象:在铜及铜合金线的实际生产过程中,铜线坯杆、半成品或者成品表面经常会有裂纹的现象,表面裂纹的存在往往会造成后道加工困难(频繁断线)、产品性能无法达标、表面质量不符合客户的要求。
一旦线材表面有裂纹,通过后道加工消除,是比较困难的。
铜线常见的裂纹形成主要有以下几种:1、熔铸裂纹:上引生产工艺不当,生产的坯杆表面就有裂纹。
2、刨皮裂纹:坯杆拉丝刨皮量过大,造成产出的线材表面有裂纹。
3、模眼裂纹:拉伸模具内侧有缺陷,造成产出的线材表面有裂纹。
4、配模裂纹:拉丝配模不当,造成产出的线材表面有裂纹。
5、磨损裂纹:拉丝过线轮、电极轮或拉丝收线卷筒表面严重磨损,造成产出的线材表面有裂纹。
另外拉丝过程中,铜线不在正常轨道,和设备其他部位产生了接触,会产生轻微的划痕甚至是裂纹。
一、熔铸裂纹铸造温度过高,坯杆表面会出现裂纹例如H63 (Cu含量:64±0.5%,其余为Zn)铸造温度在1055℃以上、牵引速度2.1mm/min生产时, 8.0坯杆表面容易形成裂纹。
原因是铸造温度过高,坯杆冷却表面至内部的温度梯度大,偏析严重;在坯杆冷却凝固的末期,当结晶骨架已经形成并开始线收缩后,由于牵引速度相对过快,因收缩受阻而产生的应力或塑性变形超过了H63在该铸造温度的强度极限或延伸率,导致了裂纹的形成。
解决办法:(1)治本不治本的方法:若现有的铸造温度(1055℃以上)没有改变,只能尝试着调低牵引速度,直至坯杆表面没有裂纹产生为止。
这样往往使得牵引速度变得很低,大大降低了当天产能而且增加了能耗,是不利于工厂大批量生产的。
(2)治标治本的方法:是选择最佳的铸造温度。
生产上一般取液1.05~1.13倍温度作为铜合金的铸造温度,因此,准确定好铸造温度,通过调试其他参数(如牵引速度、冷却水温差、反推量、反推时间和节距)达到最佳配合,就能从根本上杜绝裂纹的产生。
铜管裂缝修复方法
铜管裂缝修复方法全文共四篇示例,供读者参考第一篇示例:铜管在日常生活和工业生产中广泛应用,但长期使用会出现裂缝,造成管道泄露或破损等问题。
对于铜管裂缝修复,我们需要采取一些方法来解决,保证管道的正常使用。
下面将介绍一些关于铜管裂缝修复的方法。
一、铜管裂缝的原因铜管裂缝的主要原因包括内外力的作用、温度变化等。
在管道使用过程中,外部受到挤压或冲击力,内部则受到介质的压力对管壁的挤压力,这些力的作用会导致管道表面出现不同程度的裂缝。
温度变化也是导致铜管裂缝的重要原因,当管道长时间受到高温或低温影响时,铜材会发生热胀冷缩,导致管道表面产生裂缝。
二、铜管裂缝修复方法1. 测定裂缝位置需要清除铜管表面的污垢和腐蚀物,使用光线或荧光探测器等工具找出裂缝位置,确定裂缝的大小和形状,为后续修复工作提供准确的参考。
2. 表面处理清除管道表面的污垢和氧化层,采用砂布、铜刷等工具对管道表面进行打磨,保证粘合材料的粘附性能。
3. 焊接或黏合对于较大的裂缝,可以使用铜焊条进行焊接修复。
首先清洁焊接区域,涂上焊接剂,然后用焊枪进行焊接,将裂缝处铜材加热到熔点,使焊料充分流淌填充裂缝。
对于较小的裂缝,可使用铜管胶水进行粘合修复,将胶水均匀涂抹在裂缝处,经过一定时间固化,就能达到修复效果。
4. 封闭裂缝在焊接或黏合修复后,需要对裂缝处进行封闭,防止继续裂开。
可以使用胶带、管带等材料进行封闭,保持修复处干燥和稳定。
5. 压力测试修复完成后,需要对铜管进行压力测试,确保管道的密封性和稳定性。
根据管道的安全使用要求,进行相应的压力测试,确保管道达到安全标准。
通过以上方法对铜管裂缝进行修复,可以有效解决管道泄露和破损问题,延长铜管的使用寿命,确保管道的正常运行。
在修复过程中,需注意安全操作,选择适当的修复方法和材料,确保修复效果稳定和可靠。
希望以上方法对大家在铜管裂缝修复过程中有所帮助。
第二篇示例:铜管在各种工业和家用设备中都得到广泛应用,但在长时间使用过程中,铜管可能会出现裂缝,导致泄漏和故障。
- 1、下载文档前请自行甄别文档内容的完整性,平台不提供额外的编辑、内容补充、找答案等附加服务。
- 2、"仅部分预览"的文档,不可在线预览部分如存在完整性等问题,可反馈申请退款(可完整预览的文档不适用该条件!)。
- 3、如文档侵犯您的权益,请联系客服反馈,我们会尽快为您处理(人工客服工作时间:9:00-18:30)。
铜合金线材表面裂纹形成原因及解决办法
现象:在铜及铜合金线的实际生产过程中,铜线坯杆、半成品或者成品表面经常会有裂纹的现象,表面裂纹的存在往往会造成后道加工困难(频繁断线)、产品性能无法达标、表面质量不符合客户的要求。
一旦线材表面有裂纹,通过后道加工消除,是比较困难的。
铜线常见的裂纹形成主要有以下几种:
1、熔铸裂纹:上引生产工艺不当,生产的坯杆表面就有裂纹。
2、刨皮裂纹:坯杆拉丝刨皮量过大,造成产出的线材表面有裂纹。
3、模眼裂纹:拉伸模具内侧有缺陷,造成产出的线材表面有裂纹。
4、配模裂纹:拉丝配模不当,造成产出的线材表面有裂纹。
5、磨损裂纹:拉丝过线轮、电极轮或拉丝收线卷筒表面严重磨损,造成产出
的线材表面有裂纹。
另外拉丝过程中,铜线不在正常轨道,和设备其他部位产生了接触,会产生轻微的划痕甚至是裂纹。
一、熔铸裂纹
铸造温度过高,坯杆表面会出现裂纹
例如H63 (Cu含量:64±0.5%,其余为Zn)铸造温度在1055℃以上、牵引速度2.1mm/min生产时, 8.0坯杆表面容易形成裂纹。
原因是铸造温度过高,坯杆冷却表面至内部的温度梯度大,偏析严重;在坯杆冷却凝固的末期,当结晶骨架已经形成并开始线收缩后,由于牵引速度相对过快,因收缩受阻而产生的应力或塑性变形超过了H63在该铸造温度的强度极限或延伸率,导致了裂纹的形成。
解决办法:(1)治本不治本的方法:若现有的铸造温度(1055℃以上)没有改变,只能尝试着调低牵引速度,直至坯杆表面没有裂纹产生为止。
这样往往使得牵引
速度变得很低,大大降低了当天产能而且增加了能耗,是不利于工厂大批量生产的。
(2)治标治本的方法:是选择最佳的铸造温度。
生产上一般取液相点的
1.05~1.13倍温度作为铜合金的铸造温度,因此,准确定好铸造温度,通过调试其他参数(如牵引速度、冷却水温差、反推量、反推时间和节距)达到最佳配合,就能从根本上杜绝裂纹的产生。
二、刨皮裂纹
熔铸的坯杆表面有竹节,所以需要在倒拉机上拉拔、刨掉表面的竹节层,以使得线材表面光滑。
若拉丝刀模选择不好,刨皮量过大,线材表面往往会有裂纹。
原因是刨皮过厚,模具内金属变形流动产生的阻力大,线材表面受到的各向应力难以达到平衡。
解决办法:实际生产中,要选择匹配度最佳的刀模和拉伸模,严格控制刨皮量大小。
三、模眼裂纹
拉丝模具内侧有裂纹、磨损或划痕,眼模进角不合理等。
拉丝过程中,金属流动不均匀,容易出现中央爆裂的现象。
中央爆裂:表面有明显的裂纹,断线处从铜线的中心部位断裂,一端表现为尖锥,另一端是尖锐的孔洞。
解决办法:(1)定期检查模具眼模的变形角,磨损多的立即更换。
(2)定期检查拉丝油的浓度、PH值、温度和导电率,发现异常及时处理。
(3)使用过的模具,必须及时清理掉模眼内的铜粉和其他脏物,避免堵塞模孔。
(4)定期检查拉丝机内的塔轮、模座,磨损严重时及时更换。
四、配模裂纹
对于一些黄铜,如上面讲到的H63,,若拉丝配模不当:加工变形量过大、和设备塔轮拉力不匹配,拉丝过程中,线材受力畸形,表面容易产生裂纹。
当然,这和它的生产工艺流程也有直接的关系(如拉丝进线尺寸和产出尺寸就限制了配模的道次)。
解决办法:(1)道次加工变形量不宜过大,选择恰当的配模方式。
(2)定期维护保养设备、保证拉丝机内的塔轮运转正常稳定。
五、磨损裂纹
(1)比较典型的是拉丝退火时,线材在镍带表面上打火而被刮出裂纹。
(2)收线卷筒和压线轮磨损严重,线材受到的拉力和压力异常。
解决办法:及时更换不光滑的退火镍带、更换收线机上磨损的压线轮和磨损严重的收线卷筒。