热轧窄带钢压下规程设计
(现场管理)5热轧板带轧制规程设计轧钢车间设计

学号:20 7H EBEI P OLYTECHNIC U NIVERSITY课程设计论文题目:1250热轧板带轧制规程设计学生姓名:专业班级:0 成型班学院:指导教师:教授2010年03月12日河北理工大学06级成型课程设计目录目录1 产品特点和轧制特点1 2原料及产品介绍23 轧机的选择33.1 轧机布置 (3)3.2 立辊选择 (4)3.3 粗轧机的选择 (5)3.4 精轧机的选择 (5)4 压下规程设计74.1 压下规程设计 (7)4.2 道次选择确定 (7)4.3 粗轧机组压下量分配 (7)4.4 精轧机组的压下量分配 (8)4.5 校核咬入能力 (9)4.6 确定速度制度 (9)4.7 轧制温度的确定 (12)4.8 轧制压力的计算 (13)4.9 辊缝计算 (16)4.10 精轧轧辊转速计算 (16)4.11 传动力矩 (17)5 轧辊强度校核与电机能力验算195.1 轧辊的强度校核 (19)5.1.1 支撑辊弯曲强度校核 (19)5.1.2 工作辊的扭转强度校核 (21)5.2 电机的校核 (22)5.2.1 静负荷图 (22)5.2.2 主电动机的功率计算 (23)5.2.3 等效力矩计算及电动机的校核 (23)5.2.4 电动机功率的计算 (24)6 板凸度和弯辊256.1 板型比例凸度计算 (25)6.2 板型控制策略 (26)6.3 凸度控制模型 (27)6.4 影响辊缝形状的因素 (28)6.4.1 轧辊挠度计算 (28)6.4.2 轧辊热膨胀对辊缝的影响 (29)6.4.3 轧辊的磨损对辊缝的影响 (31)6.4.4 原始辊型对辊缝的影响 (31)6.4.5 入口板凸度对辊缝的影响 (32)6.5 弯辊装置 (32)6.5.1 弯曲工作辊 (32)6.5.2 弯曲支撑辊 (32)I河北理工大学06级成型课程设计目录6.6 CVC轧机的抽动量计算 (33)参考文献 (36)II河北理工大学06级成型课程设计1产品特点和轧制特点1 产品特点和轧制特点不同宽度的热带有不同的用途,也需采用不同工艺技术。
压下规程
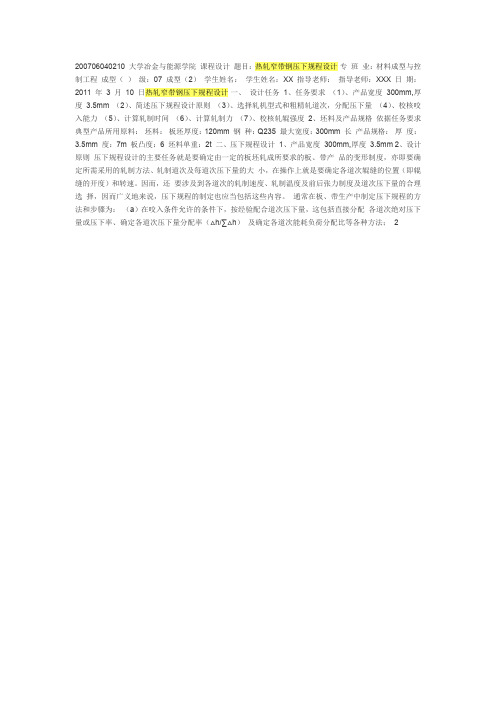
200706040210 大学冶金与能源学院课程设计题目:热轧窄带钢压下规程设计专班业:材料成型与控制工程成型()级:07 成型(2)学生姓名:学生姓名:XX 指导老师:指导老师:XXX 日期:2011 年3 月10 日热轧窄带钢压下规程设计一、设计任务1、任务要求(1)、产品宽度300mm,厚度3.5mm (2)、简述压下规程设计原则(3)、选择轧机型式和粗精轧道次,分配压下量(4)、校核咬入能力(5)、计算轧制时间(6)、计算轧制力(7)、校核轧辊强度2、坯料及产品规格依据任务要求典型产品所用原料:坯料:板坯厚度:120mm 钢种:Q235 最大宽度:300mm 长产品规格:厚度:3.5mm 度:7m 板凸度:6 坯料单重:2t 二、压下规程设计1、产品宽度300mm,厚度 3.5mm 2、设计原则压下规程设计的主要任务就是要确定由一定的板坯轧成所要求的板、带产品的变形制度,亦即要确定所需采用的轧制方法、轧制道次及每道次压下量的大小,在操作上就是要确定各道次辊缝的位置(即辊缝的开度)和转速。
因而,还要涉及到各道次的轧制速度、轧制温度及前后张力制度及道次压下量的合理选择,因而广义地来说,压下规程的制定也应当包括这些内容。
通常在板、带生产中制定压下规程的方法和步骤为:(a)在咬入条件允许的条件下,按经验配合道次压下量,这包括直接分配各道次绝对压下量或压下率、确定各道次压下量分配率(△h/∑△h)及确定各道次能耗负荷分配比等各种方法; 2热轧窄带钢压下规程设计(b)制定速度制度,计算轧制时间并确定逐道次轧制温度;(c)计算轧制压力、轧制力矩;(d)校验轧辊等部件的强度和电机功率;(e)按前述制定轧制规程的原则和要求进行必要的修正和改进。
板带轧制规程设计的原则要求是:充分发挥设备能力,提高产量和质量,并使操作方便,设备安全。
3、粗精轧道次,分配压下量粗精轧道次,3.1、轧制道次的确定有设计要求可知板坯厚度为120mm;成品厚度为 3.5mm,则轧制的总延伸率为:?∑ = 式中H 120 = = 34.28 h 3.5 ? ∑ 总延伸率H 坯料原始厚度h 产品厚度平均延伸系数取 1.36 则轧制道次的确定如下N= log ? ∑ log 34.28 = = 12(取整) log ? p log1.36 ? ps由此得实际的平均延伸系数为:= 12 ? ∑ =1 .3 4 ? ∑ 7 34.28 = =1.3 1.45 ?cp 5 由上面计算分配轧制道次,和粗精轧平均延伸洗漱如下:I :取粗轧 5 道次,平均道次延伸系数为 1.40。
热轧板带钢轧制规程设计

热轧板带钢轧制规程设计一、引言热轧板带钢是一种广泛应用于工业领域的金属材料,其性能的稳定性和质量的优越性对产品的质量和使用寿命至关重要。
因此,热轧板带钢的制造过程需要遵循一定的规程和标准,以确保产品质量的稳定性。
本文将介绍一个热轧板带钢的轧制规程设计。
二、设计目标本轧制规程的设计目标是制定一套科学合理的生产工艺和操作规程,以确保热轧板带钢的质量和性能达到预期要求。
具体的设计目标包括:1.确定合适的轧制温度和轧制速度,以确保给定的产品尺寸和机械性能的要求。
2.设计适当的冷却方式,以确保产品在冷却过程中达到理想的组织结构。
3.确定合适的轧制压力和辊缝尺寸,以确保产品的形状和尺寸的精度。
4.设计适当的轧制工艺和操作规程,以确保生产过程的稳定性和可控性。
5.设计合适的质量检验方法和标准,以确保产品的质量符合要求。
三、设计思路本轧制规程的设计思路是在充分了解产品需求和原材料性能基础上,通过迭代优化的方式确定最佳的轧制工艺和操作规程。
具体的设计思路包括:1.通过分析产品的尺寸要求、力学性能要求和成分要求等,确定轧制温度和轧制速度的范围。
根据产品的板厚和钢种,选择适当的温度和速度条件,以满足产品的性能要求。
2.设计合适的冷却方式,以确保产品在冷却过程中达到理想的组织结构。
根据产品的厚度和形状,选择适当的冷却方式,并确定冷却速度、冷却介质等参数。
3.确定合适的轧制压力和辊缝尺寸,以确保产品的形状和尺寸的精度。
通过分析产品的厚度、宽度和长度要求,选取合适的辊缝尺寸,并确定合适的轧制压力。
4.设计合适的轧制工艺流程和操作规程,以确保生产过程的稳定性和可控性。
根据产品的尺寸和性能要求,确定轧制的工艺流程,并设计详细的操作规程。
5.设计合适的质量检验方法和标准,以确保产品的质量符合要求。
制定合适的质量检验方法和标准,进行产品的质量检验和评价。
四、设计步骤1.分析产品需求和原材料性能,确定轧制温度和轧制速度的范围。
2.设计合适的冷却方式,确定冷却速度和冷却介质。
金属压力加工车间设计05+ 补充_热轧板带钢轧制规程设计
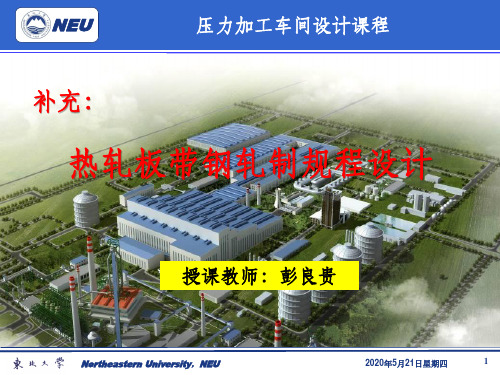
15
NEU
1 初始压下规程设计-精轧轧制规程
精轧机组压下量分配: 1)由7架四辊不可逆式轧机组成连轧机组。各机架采用PC 轧机,前三 架主要完成压下,后四架主要控制板形。各机架负荷分配亦不同,因 此前三台采用工作辊辊径较大,后四架采用较小的工作辊。精轧机组 前设置边部加热器。精轧机 F1~F7全部为液压压下并设弯辊装置; 2)精轧机组的总压缩率和最大延伸率与精轧机的数量有关;终轧变形 程度对钢材的金相组织有重要的影响,不同钢种的再结晶曲线是不同 的,为得到细晶粒组织,要根据不同钢种的终轧温度确定变形程度; 3)精轧机组最末两架基于板形考量,采用减小压下量的方法,减少带
热轧带钢时,最大咬入角一般为15°~20°,低速轧制时为20°, 所以上述咬入角符合条件,咬入能力满足。
Northeastern University,NEU
2017年11月10日星期五 19
NEU
3 速度制度设计-粗轧速度制度
不可逆轧机 可逆轧机
粗轧为可逆式轧制,一般采用梯形速度图
根据经验资料: 平均加速度a=40rpm/s, 平均减速度b=60rpm/s。 由于咬入能力很富余,且咬入时速度高有利于轴承油膜的形成,故可采用稳 定速度咬入。 根据实际生产情况,各道次速度可取为: R1架:第一、二道次取咬入速度和恒定转速为35rpm,抛出速度为20rpm ,第三道次咬入速度和恒定转速为40rpm ,抛出速度为25rpm R2架:由于为四辊可逆轧机,取第四道次咬入速度、恒定速度为40rpm ,抛出速度为25rpm。第五、六道次的咬入速度和恒定速度为60rpm,抛 出速度为30rpm。
Northeastern University,NEU
2017年11月10日星期五
H68(Y)热轧压下规程

18.09
5 44 33 11.00 25.00 16.67 462.05 466.58 464.32 4.53 20659 27278 10.91 10.00 20.91 9.22 773.78 3.60 16.03 757.75 765.77 68.37 31747 90.00 10.45 0.80 0.30 1.15 24.84 28.57 1.23 35.11 1119.99 0.44 67.39 2.42 0.80 3.22 5.39 16.45 2.01 681.50 2250.00 2500 8.597 0.91 540 0.004 29.54 2.91 639.10 150.32 105.98 90.00
32 轧制压力 P
KN
33 力臂系数x
34 轧制力矩MZ
KN*m
35 轧辊轴承中附加摩擦力矩Mf1 KN*m
36 传动机构中附加摩擦力矩Mf2 KN*m
37 摩擦力矩 Mf
KN-m
38 空转力矩 M0
KN-m
39 静力矩Mc
KN-m
40 等效力矩M'
10^4N-m
41 计算电机功率N
KW
42 选择电机功率N
2500 8.597 0.91 540 0.004 155.15 33.76
13.03
4 63 44 19.00 30.16 20.11 454.87 462.05 458.46 7.18 14656 20659 8.26 10.00 18.26 12.12 784.73 3.60 10.95 773.78 779.26 89.86 41198 90.00 9.88 0.85 0.29 1.12 24.85 28.57 1.20 34.43 1429.53 0.58 149.01 3.09 1.75 4.84 11.92 34.09
金属压力加工车间设计之热轧板带钢轧制规程设计(56页)
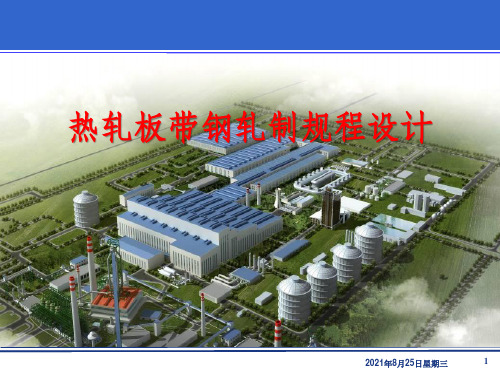
在校核粗轧机咬 入能力时,取机 架最大压下量的 那道次进行,精 轧F1~F3可取 F1较核,F4~ F7可取F4校核.
热轧带钢时,最大咬入角一般为15°~20°,低速轧制时为20°, 所以上述咬入角符合条件,咬入能力满足。
2021年8月25日星期三
19
3 速度制度设计-粗轧速度制度
粗轧为可逆式轧制,一般采用梯形速度图
38.1
34.8
16.76 9.69 6.00
7.07 9.69
3.69 6.00
2.09 3.91
F5 30.2 3.91 1.18 2.73
F6 24.6 2.73 0.67 2.06
F7 12.5 2.06 0.26 1.8
2021年8月25日星期三
18
2 咬入能力校核
压下量与咬入角的关系
h D (1 cos ) cos 1 h
No 轧制力能参数校核
Yes 压下规程、速度规程等
最终确定
结束
2021年8月25日星期三
2
压力加工车间设计课程
➢ 初始压下规程设计 ➢ 咬入能力校核 ➢ 速度制度设计 ➢ 轧制温度计算 ➢ 道次变形程度计算 ➢ 道次轧制力和轧制力矩计算
2021年8月25日星期三
3
压力加工车间产线概况
生产工艺流程
SF 2 4 9.69 1 2 0.25
7.07 400
0.13
SF3
3.69 4 6.00
1
1 2 0.25
3.69 400
0.12
SF 4
4
2.09 3.91
1
1 2 0.25
2.09 375
0.11
SF5
4
1880六机架热连轧压下规程完整

∴D 1=750~800mm 1.2、工作辊轴颈尺寸工作辊轴颈直径:d=(0.5~0.55)D 1 (D 1是新辊直径,且采用滚动轴承)∴d=400~440mm ,取d=440mm 工作辊轴颈长度:l=(0.83~1.0)d∴l=356~440mm ,取l=440mm (辊颈具体长度由轧辊结构确定,最终长度见图纸)圆角半径r=(0.05~0.12)D 1=37.5~90mm ,取r=80mm 1.3、工作辊传动端采用万向扁头,其尺寸如下图所示由轴肩及轴颈尺寸取d=414mm ,a=0.75d=310.5mm 1.4、工作辊尺寸如图2、支承辊尺寸2.1、轧辊直径: 1.3~1.5L=(热带钢精轧机组),且2 1.9~2.1D =21253.3~1446.2D mm =, 21425~1575D mm =比值2LD 标志着辊系的抗弯刚度,其值愈小,则刚度愈高;21D D 主要取决于工艺条件,当轧件较厚(咬入角较大)时,由于要求较大的工作辊直径,故选取较小的21D D 值;当轧件较薄时,则选用较大的21DD 值。
综合,取D 2=1440mm支承辊重车率取6%,2153216%D mm =-,取1530mm ,∴D 2=1440~1530mm 2.2、支承辊轴颈尺寸支承辊轴颈直径:d=(0.55~0.6)D 2 (D 2是新辊直径,且为滚动轴承) ∴d=841.5~918mm ,取d=900mm 。
圆角半径r=(50~90)mm ,取r=90mm 。
支承辊轴颈长度:l=(0.8~1.0)d∴l=720~900mm ,取l=900mm (辊颈具体长度由轧辊结构确定,最终长度见图纸)2.3、支承辊尺寸如图3、轧辊材料选择带钢热轧机的工作辊在选择轧辊材料时,应以硬度要求为主,同时兼4.2、支撑辊轴承的选择:四、轧辊强度校核四辊轧机,由于有支撑辊,存在工作辊与支撑辊之间弯曲载荷分配问题,其次它们之间存在相当大接触应力。
热轧板带钢轧制规程设计PPT课件

考虑轧辊与轧件之间的摩擦和张力等因素,计算轧制力矩,保证轧 制过程的稳定性。
速度制度设计
轧制速度
根据设备能力和生产节奏确定轧制速度,提高生产效率。
卷取速度
与轧制速度相匹配,保证带钢卷取整齐、紧密。
加速和减速
在轧制过程中适当进行加速和减速操作,以调整带钢厚度和板形。
张力制度设计
张力设定
01
热轧板带钢轧制规程设 计ppt课件
目录 CONTENT
• 热轧板带钢轧制概述 • 热轧板带钢轧制设备介绍 • 热轧板带钢轧制工艺参数设计 • 热轧板带钢质量控制与检测 • 热轧板带钢轧制过程自动化技术
应用 • 热轧板带钢轧制规程设计实践案
例分析
01
热轧板带钢轧制概述
热轧板带钢定义与分类
定义
热轧板带钢是指通过高温加热后 ,在轧机上经过多道次连续轧制 而成的具有一定厚度、宽度和长 度的钢板或钢带。
基于轧机刚度、轧辊磨损、热膨胀等因素,建立精确的厚度设定 模型。
厚度自动控制(AGC)
采用测厚仪对带钢实际厚度进行实时测量,通过AGC系统对轧机进 行调整,确保厚度精度。
厚度变化趋势预测
利用历史数据和机器学习算法,对带钢厚度变化趋势进行预测,提 前采取控制措施。
宽度控制方法与策略
1 2
宽度设定模型
预测控制
基于历史数据和当前状态,预测 未来一段时间内热轧板带钢生产 过程的发展趋势,提前采取控制 措施,确保生产过程的稳定性和 产品质量。
智能化技术在热轧板带钢生产中的应用展望
机器学习算法应用
通过机器学习算法对历史数据进行分析和学习,挖掘潜在规律并应用于生产过程优化和质量控制 。
智能感知与决策支持
- 1、下载文档前请自行甄别文档内容的完整性,平台不提供额外的编辑、内容补充、找答案等附加服务。
- 2、"仅部分预览"的文档,不可在线预览部分如存在完整性等问题,可反馈申请退款(可完整预览的文档不适用该条件!)。
- 3、如文档侵犯您的权益,请联系客服反馈,我们会尽快为您处理(人工客服工作时间:9:00-18:30)。
201224050120河北联合大学轻工学院课程设计题目:12mm热轧窄带钢压下规程设计专业:金属材料工程班级:12轧钢学生姓名:赵凯指导老师:李硕日期:2015年12月3日目录1 任务要求 (3)1.1 任务要求 (3)1.2 原料及产品规格 (3)2 压下规程设计 (3)2.1 产品规格 (3)2.2 设计原则 (3)2.3 粗精轧道次,分配压下量 (4)2.3.1轧制道次的确定 (4)2.3.2 粗轧机组压下量分配 (4)2.3.3 精轧机组的压下量分配 (5)2.4 咬入能力的校核 (6)2.5 计算轧制时间 (6)2.5.1 粗轧速度制度 (6)2.5.2 精轧速度制度 (7)2.5.3 各道轧件速度的计算 (8)2.6 轧制压力的计算 (9)2.6.1 粗轧温度的确定 (9)2.6.2 精轧机组温度确定 (10)2.6.3 粗轧段轧制力计算 (10)2.6.4 精轧段轧制力计算 (13)2.7 轧辊强度校核 (14)2.7.1 支撑辊弯曲强度校核 (15)2.7.2 工作辊的扭转强度校核 (16)3 设计总结 (19)一、设计任务1、任务要求(1)、产品宽度1650mm,厚度12mm(2)、简述压下规程设计原则(3)、选择轧机型式和粗精轧道次,分配压下量(4)、校核咬入能力(5)、计算轧制时间(6)、计算轧制力(7)、校核轧辊强度2、坯料及产品规格依据任务要求典型产品所用原料:坯料:板坯厚度:120mm钢种:Q235最大宽度:300mm长度:7m产品规格:厚度:12mm板凸度:6错误!未找到引用源。
坯料单重:2t二、压下规程设计1、产品宽度300mm,厚度12mm2、设计原则压下规程设计的主要任务就是要确定由一定的板坯轧成所要求的板、带产品的变形制度,亦即要确定所需采用的轧制方法、轧制道次及每道次压下量的大小,在操作上就是要确定各道次辊缝的位置(即辊缝的开度)和转速。
因而,还要涉及到各道次的轧制速度、轧制温度及前后张力制度及道次压下量的合理选择,因而广义地来说,压下规程的制定也应当包括这些内容。
通常在板、带生产中制定压下规程的方法和步骤为:(a )在咬入条件允许的条件下,按经验配合道次压下量,这包括直接分配各道次绝对压下量或压下率、确定各道次压下量分配率(△h/∑△h )及确定各道次能耗负荷分配比等各种方法;(b )制定速度制度,计算轧制时间并确定逐道次轧制温度; (c )计算轧制压力、轧制力矩;(d )校验轧辊等部件的强度和电机功率;(e )按前述制定轧制规程的原则和要求进行必要的修正和改进。
板带轧制规程设计的原则要求是:充分发挥设备能力,提高产量和质量,并使操作方便,设备安全。
3、粗精轧道次,分配压下量 3.1、轧制道次的确定有设计要求可知板坯厚度为120mm ;成品厚度为12mm ,则轧制的总延伸率为:式中 ∑μ 总延伸率 H 坯料原始厚度 h 产品厚度平均延伸系数取1.36则轧制道次的确定如下由此得实际的平均延伸系数为:由上面计算分配轧制道次,和粗精轧平均延伸洗漱如下: I : 取粗轧5道次,平均道次延伸系数为1.40。
II :精轧为7道次连轧,各道次平均延伸系数为按μ分配原则我们将粗、精轧的延伸系数如下:3.2、粗轧机组压下量分配12034.283.5H h μ∑===log log34.2812()log log1.36p N μμ∑===取整s = 1.34p μj p μ根据板坯尺寸、轧机架数、轧制速度以及产品厚度等合理确定粗轧机组总变形量及各道次压下量。
其基本原则是:(1)、由于在粗轧机组上轧制时,轧件温度高、塑性好,厚度大,故应尽量应用此有利条件采用大压下量轧制。
考虑到粗轧机组与精扎机组之间的轧制节奏和负荷上的平衡,粗轧机组变形量一般要占总变形量的60%--80%(2)、提高粗轧机组轧出的带坯温度。
一方面可以提高开轧温度,另一方面增大压下可能减少粗轧道次,同时提高粗轧速度,以缩短延续时间,减少轧件的温降。
(3)、考虑板型尽量按照比例分配凸度,在粗轧阶段,轧制力逐渐较小使凸度绝对值渐少。
但是,第一道考虑厚度波动,压下量略小,第二道绝对值压下最大,但压下率不会太高。
本设计粗轧采用四分之三式,轧机配置为四架,粗轧制度为:第一架轧机为二辊不可逆,轧制一道次;第二架轧机为四辊可逆,轧制三道次;第三架轧机为四辊不可逆,轧制一道次(预留一架)。
由此计算粗轧压下量分配数据如下表:3.3、精轧机组的压下量分配精轧连轧机组分配各架压下量的原则;一般也是利用高温的有利条件,把压下量尽量集中在前几架,在后几架轧机上为了保证板型、厚度精度及表面质量,压下量逐渐减小。
为保证带钢机械性能防止晶粒过度长大,终轧即最后一架压下率不低于10%,此外,压下量分配应尽可能简化精轧机组的调整和使轧制力及轧制功率不超过允许值。
依据以上原则精轧逐架压下量的分配规律是:第一架可以留有余量,即考虑到带坯厚度的可能波动和可能产生咬入困难等,使压下量略小于设备允许的最大压下量,中间几架为了充分利用设备能力,尽可能给以大的压下量轧制;以后各架,随着轧件温度降低、变形抗力增大,应逐渐减小压下量;为控制带钢的板形,厚度精度及性能质量,最后一架的压下量一般在10-15%左右。
精轧机组的总压下量一般占板坯全部压下量的10-25%。
本次设计采用7架连轧,结合设备、操作条件直接分配各架压下量如下:精轧机组压下量分配及各项参数如表(2)所示:4、咬入能力的校核热轧钢板时咬入角一般为15~22°,低速咬入可取20°,由公式其中D 为对应道次轧机工作辊直径。
轧辊的工作辊直径选用400mm ,粗精轧机工作辊相同。
将各道次压下量及轧辊直径代入可得各轧制道次咬入角为:粗、精轧各道次咬入角的校核5、计算轧制时间(1)粗轧速度制度粗轧为保证咬入,采用升速轧制。
根据经验资料,取平均加速度a=40rpm/s ,平均减速度b=60rpm/s 。
由于咬入能力很富裕故可采用稳定高道 次 F1 F2 F3 F4 F5 F6 F7 延伸系数分配1.321.35 1.32 1.30 1.28 1.27 1.26 出口厚度(mm ) 16.58 12.29 9.31 7.16 5.60 4.41 120 压 下 量(mm ) 5.82 4.29 2.98 2.15 1.56 1.19 0.91 压 下 率(%) 26.0 25.924.223.121.821.320.6轧件长度(m)50.66 68.35 90.23 117.32 150.00 190.48 240.00道 次:R1R2 R3R4R5F1F2F3F4F5F6F7轧辊直径(mm ) 400 400400 400 400 400 400 400 400 400 400 400压下量(mm ) 34.3 25.3 18.7 11.5 7.8 5.82 4.29 2.98 2.15 1.56 1.19 0.91咬入角(°)21222.5 19.3 15.2 12.4 10.5 9.2 7.5 6.4 5.4 4.6 4.2arccos(1)hDα∆=-速咬入,考虑到粗轧生产能力与精轧生产能力得匹配问题,确定粗轧速度如下:咬入速度为n 1=50rpm ,抛出速度为n 2=20rpm 。
粗轧各道次的轧制转速均可设置为n 1=50rpm ,则粗轧的稳定轧制速度为:因此,对于各架粗轧机减速用时:s b n n t 5.0605020122=--=-= 稳定轧制时间:间隙时间:s Dn lt j 5.3601==π t=0.5*5+9.33+13.34+19.18+26.50+35.71+12=110.06s(2)精轧速度制度确定确定精轧速度制度包括:确定末架的穿带速度和最大轧制速度;计算各架速度及调速范围;选择加减速度等。
精轧末架的轧制速度决定着轧机的产量和技术水平。
确定末架轧制速度时,应考虑轧件头尾温差及钢种等,一般薄带钢为保证终轧温度而用高的轧制速度;轧制宽度大及钢质硬的带钢时,应采用低的轧制速度。
本设计典型产品12mm ,终轧速度设定为12m/s 。
末架穿带速度在8m/s 左右,带钢厚度小,其穿带速度可高些。
穿带速度的设定可有以下三种方式:I 、当选用表格时,按标准表格进行设定;II 、采用数字开关方式时,操作者用设定穿带速度的数字开关进行设定,此时按键值即为穿带速度;12345 3.14500.41.05/6060nD v v v v v m sπ⨯⨯=======()Ri i wRi il l t v -=III 、其它各架轧制速度的确定:当精轧机末架轧制速度确定后,根据秒流量相等的原则,各架由出口速度确定轧件入口速度。
根据各架轧机出口速度和前滑值求出各架轧辊线速度和转速。
(3)各道轧件速度的计算:已预设末架出口速度为12 m/s 由经验向前依次减小以保持微张力轧制依据秒流量相等原则即其中i v 为各机架出口速度;i h 为各机架出口厚度。
根据以上公式可依次计算得:各道次精轧速度的确定道次F1 F2 F3 F4 F5 F6 F7 入口速度(m/s ) 1.9 2.5 3.4 4.5 5.9 7.5 9.5 出口速度(m/s) 2.53.44.55.97.59.512.0精轧阶段加速前纯轧时间:s v DN s t j s 3.137=+=π式中 j s ——精轧机组末架至卷曲机间距,取100m D ——卷取机卷筒直径 N ——参数,取57v ——第七架穿带速度,取8s m /精轧机组间机架间距为6米,各道次纯轧时间为t X =300×12/12/12=85.7s间隙时间分别为t j1=6/2.5=2.4s ;t j2=6/3.4=1.76s ;t j3=6/4.5=1.5s ;tj4=6/5.9=102s ;t j5=6/7.5=0.8s ; t j6=6/9.5=0.63s; t j7=6/12=0.5s 则精轧总延续时间s t t t t j x s 61.07161.87.8513.3=++=++=∑。
r i i c v H vh v h==6、轧制压力的计算(1)粗轧温度确定为了确定各道次轧制温度,必须求出逐道次的温度降。
高温轧制时轧件温度降可以按辐射散热计算,计算原则为:对流和传导所散失的热量可大致与变形功所转化的热量相抵消。
由于辐射散热所引起的温度降在热轧板带时可按下式计算:41)1000(9.12T h Z t =∆ 有时为简化计算,也可采用以下经验公式1116400h Z t t ⨯-=∆ο其中 ο1t 、1h ——分别为前一道轧制温度(℃)与轧轧出厚度,mm ;Z ——辐射时间即该道次轧制延续时间t j Z=t j ;T 1——前一道的绝对温度 ,K ; h ——前一道的轧出厚度。