精脱硫系统催化剂及转化催化剂的升温
制氢PSA操作工职业技能竞赛简答题题库
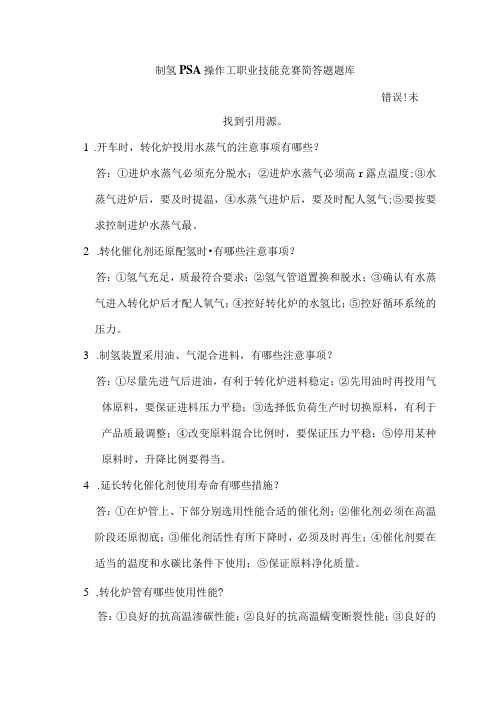
制氢PSA操作工职业技能竞赛简答题题库错误!未找到引用源。
1.开车时,转化炉投用水蒸气的注意事项有哪些?答:①进炉水蒸气必须充分脱水;②进炉水蒸气必须高r露点温度;③水蒸气进炉后,要及时提温,④水蒸气进炉后,要及时配人氢气;⑤要按要求控制进炉水蒸气最。
2.转化催化剂还原配氢时•有哪些注意事项?答:①氢气充足,质最符合要求;②氢气管道置换和脱水;③确认有水蒸气进入转化炉后才配人氧气;④控好转化炉的水氢比;⑤控好循环系统的压力。
3.制氢装置采用油、气混合进料,有哪些注意事项?答:①尽量先进气后进油,有利于转化炉进料稳定;②先用油时再投用气体原料,要保证进料压力平稳;③选择低负荷生产时切换原料,有利于产品质最调整;④改变原料混合比例时,要保证压力平稳;⑤停用某种原料时,升降比例要得当。
4.延长转化催化剂使用寿命有哪些措施?答:①在炉管上、下部分别选用性能合适的催化剂;②催化剂必须在高温阶段还原彻底;③催化剂活性有所下降时,必须及时再生;④催化剂要在适当的温度和水碳比条件下使用;⑤保证原料净化质量。
5.转化炉管有哪些使用性能?答:①良好的抗高温渗碳性能;②良好的抗高温蠕变断裂性能;③良好的抗高温热疲劳性能;④良好的抗高温氧化腐蚀性能;⑤良好的导热性能;⑥高温下组织结构能长期保持稳定;⑦良好的铸造和焊接质量。
6.压缩机汽缸带液有哪些现象?答:①出口温度突然降低;②汽缸内有撞击声,压差增大;③电流增大;④缸体振动。
7.压缩机跳闸的原因有哪些?答:①电机绕组短路;②电压低、电机过载电流升高;③继电器故障;④油压低至连锁值。
8.简述转化炉催化剂发生结炭的原因?答:①水碳比过低;②长期处在高负荷状态;③原料重质化;④催化剂活性衰减;⑤原料脱毒不彻底;⑥进料经常发生人幅波动。
9.简述悬浮物引起汽包汽水共沸的过程。
答:①杂质在炉水中浓缩;②炉水碱度增加产生泡沫;③泡沫厚度增高蒸发阻力增加;④汽水难以分离,形成汽水共沸现象。
PSA精脱硫岗位操作法要点
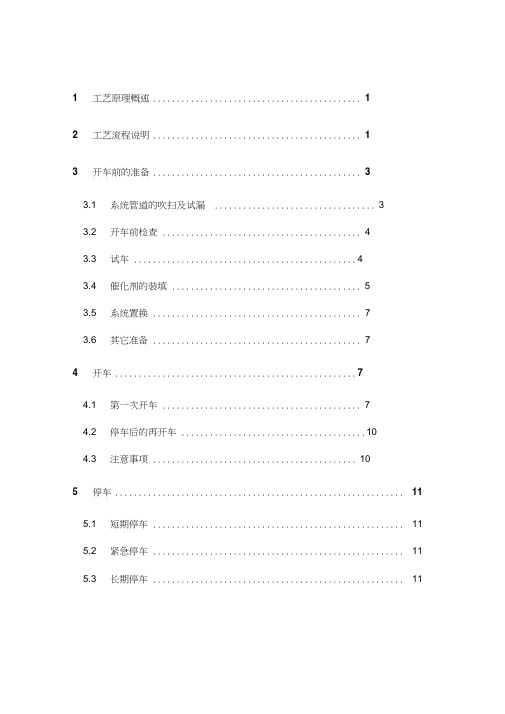
1 工艺原理概述 (1)2 工艺流程说明 (1)3 开车前的准备 (3)3.1 系统管道的吹扫及试漏 (3)3.2 开车前检查 (4)3.3 试车 (4)3.4 催化剂的装填 (5)3.5 系统置换 (7)3.6 其它准备 (7)4 开车 (7)4.1 第一次开车 (7)4.2 停车后的再开车 (10)4.3 注意事项 (10)5 停车 (11)5.1 短期停车 (11)5.2 紧急停车 (11)5.3 长期停车 (11)6 正常生产控制指标 (12)6.1压力.................... ................. 错误!未定义书签。
6.2温度.................... ................. 错误!未定义书签。
6.3流量.................... ................. 错误!未定义书签。
6.4组份.................... ................. 错误!未定义书签。
7 不正常情况及处理 (12)8 安全注意事项 (13)1 工艺原理概述经PSA脱碳后来的甲烷浓缩气,其中的无机硫(H2S)部分被除去(H2S < 10mg/Nm 3)。
系统中的有机硫也被部分除去(有机硫w 100g/Nm 3)。
为彻底脱除系统中的有机硫和无机硫,本工序采用预加氢、加氢转化有机硫为无机硫(H2S),然后再将无机硫(H2S)脱除,得到符合工艺要求的浓缩气。
其主要反应式如下:COS + H 2 == H 2S + COCS2 + 4H 2 == 2H 2S + CH 4RSH + H 2 == RH + H 2SC4H4S + 4H 2 == C 4H i o + H 2SC2H5S S C 2H5 + 3H 2 ==2 C 2H6 + 2H 2S加氢转化的副反应有:02 + 2H 2 == 2 H 20CO +3 H 2 == CH 4 + H 20生成的H2S通过干法(氧化锌)脱除,其主要反应式如下:ZnO + COS== ZnS + CO 2ZnO + CS2== ZnS + CO 2ZnO + H2S ==Z nS + H2O氧化锌脱硫不仅对脱除H2S有非常好的效果,而且能脱除部分有机硫。
变换催化剂硫化升温步骤及注意事项

变换催化剂硫化升温步骤及注意事项升温步骤及注意事项用氮气(也可用半水煤气,但控制速率,注意安全)对整个CO变换系统进行置换,置换至O2含量≤0.5%(体积分数)。
然后按制定的升温流程对催化剂进行升温,升温速率控制在15-25℃/h,当催化济床层温度升至80℃时,向升温载气中配入H2;在催化剂床层温度达120℃时,恒温约4h,以利催化剂吸附水的排放及吸附氧的释放、燃烧。
升温过程注意以下几点:一、根据实际情况制定升温流程,管线盲板倒换正确;二、用载气的温度将升温速率控制在安全范围内;三、配氢时,注意分析升温载气中的O2含量,严格控制载气中的O2含量≤0.5%(体积分数),超标时用放空进行调整;四、保持升温系统压力≤0.2Mpa。
变换催化剂硫化注意事项一、在升温、降温期间,采用大空速,要求电炉功率要大(用CS2硫化时,1m3催化剂的电炉功率为30kW,用固体硫化剂时,1m3催化剂的电炉功率要≥50kW,宜分为多组控制),以满足大负荷需要。
二、硫化期间,保持硫化载气中的H2含量≥25%,可采用部分放空和添加新鲜煤气的措施保证循环气中的H2浓度达标。
三、用CS2的加入量及硫化载气温度和流量控制催化剂床层的升温速率及热点温度,必要时可切气通蒸汽降温后再导气硫化,严禁床层温度暴涨、急降,进行强制硫化时,床层温度应控制在450-480℃,最高不得超过500℃。
四、在H2S穿透前,CS2量不可加入过多,否则会把催化剂中COO 直接还原为金属CO,CO有甲烷催化作用,不仅加剧超温,而且使硫化无法继续进行,同时损害催化剂的活性。
五、硫化系统压力应保持在0.2-0.3 Mpa。
六、因湿气硫化会使CO-MO系催化剂丧失部分活性,尤其是丧失低温活性,因此,系统保压、补氢时须用干气,并及时排放冷凝水,严禁冷凝水进入催化剂床层。
七、煤气中O2含量每升高0.1%,系统绝热温升约15℃。
O2会将催化剂中的活性组分氧化成硫酸盐,降低催化剂的活性,因此,在硫化全过程中,须严格控制煤气中O2含量<0.5%,当煤气中O2含量高时,必须迅速切气源,待O2浓度降至合格后再通气硫化。
焦炉煤气制甲醇装置运行探讨

从湿法脱 硫来 的含 HS 2质量 浓度 2 gm 以下 的 0m /。
焦 炉 煤气 , 3台往 复 式 压缩 机 ( 经 2开 l备 ) 压 到 加
2 1M a 温 度 4 . P 、 0℃ , 精脱硫 工段 。经油 水过 滤器 、 送
活性 炭预 脱硫槽 、 初预 热器 , 通过 两 级铁 钼加 氢转 再 化器 , 将煤气 中的有机 硫转化为 Hs 并 分别通 过铁锰 。,
精脱硫 和转 化催化 剂 的升 温 , 原设 计是 由 2台螺 杆式压缩 机提供 氮气进行 升温 , 总流量 约 24 0m h 0 V , 远不能满 足 80 0 3h 1 0 3 0 / ~ 00 0m h的升 温气 量要求 。 m /
在 工 艺 管 线 安 装 期 间 , 浩 化 工 对 空 分 氧 压 机 放 空 管 天
月投产 。运行 以来 , 通过对 工艺操 作要点 和系 统存在
的问题 积极探讨 、 解决 , 使生产稳 定运行 。
气从转 化炉上 部进入催 化剂床层 , 进行 甲烷 的催化 转 化 反应 , 生成 H O C 。控 制 转化 炉 出 口温 度 , 出 2C 、O, 使 工段转 化气 中 c H 体积 分数小 于 0 6 。 化气依 次经 .% 转 废热锅 炉 、 预热器 、 预热器 、 初 脱硫槽 ( 体 积分 数小 Hs
第 1 ( 期 总第 1 8 ) 5期
21 0 2年 2月
煤 化 工
C a e c lI d sr o lCh mia n u t y
N .(o l o1 8 o1 t N .5) T a
F b.2 1 e 0 2
焦炉煤气 制 甲醇 装 置运行 探讨
吴 波
( 山西 天 浩 化 工 股 份 有 限公 司 , 山西
高炉煤气精脱硫催化剂

高炉煤气精脱硫催化剂
高炉煤气精脱硫催化剂是一种用于高炉煤气脱硫的催化剂。
高炉煤气是高炉生产过程中产生的一种含有大量二氧化硫的气体,如果不进行处理,会对环境造成严重的污染。
因此,高炉煤气的脱硫处理是高炉生产过程中必不可少的环节。
传统的高炉煤气脱硫方法是采用吸收法,即将高炉煤气通过吸收液中,利用化学反应将二氧化硫转化为硫酸,从而达到脱硫的目的。
但是,这种方法存在着吸收液的成本高、脱硫效率低、废液处理难等问题。
为了解决这些问题,研究人员开发出了高炉煤气精脱硫催化剂。
这种催化剂采用先进的催化技术,能够将高炉煤气中的二氧化硫转化为硫酸,从而达到脱硫的目的。
相比传统的吸收法,高炉煤气精脱硫催化剂具有脱硫效率高、成本低、废液处理简单等优点。
高炉煤气精脱硫催化剂的主要成分是活性氧化铝和活性氧化钛。
这两种物质具有很强的催化作用,能够促进高炉煤气中的二氧化硫转化为硫酸。
此外,催化剂还添加了一些稀土元素,能够提高催化剂的稳定性和耐高温性能,从而延长催化剂的使用寿命。
高炉煤气精脱硫催化剂的使用方法很简单,只需要将催化剂放置在高炉煤气处理系统中即可。
在高炉煤气通过催化剂时,二氧化硫会被催化剂吸附并转化为硫酸,从而达到脱硫的目的。
催化剂的使用
寿命一般为1-2年,使用寿命结束后,只需要更换催化剂即可。
高炉煤气精脱硫催化剂是一种高效、环保、经济的高炉煤气脱硫方法。
它的出现,不仅能够有效地减少高炉煤气对环境的污染,还能够提高高炉生产的效率和经济效益。
精脱硫操作规程

精脱硫工段技术、操作规程一、岗位任务及职责范围 (2)二、产品说明 (2)三、原材料及化学品规格 (3)四、原材料及动力消耗定额 (3)五、生产原理 (4)六、岗位生产工艺流程 (7)七、本工段与其它工段的配合 (8)八、岗位操作程序 (9)(一)原始开车(检修后的开车) (9)(二)触媒的升温、还原、硫化: (10)(三)正常开车 (15)(四)正常停车 (16)(五)短期停车 (19)(六)紧急停车 (19)(七)正常调节 (19)(八)氧化铁、氧化锌倒槽操作 (20)(九)升温炉点火操作 (20)九、正常工艺指标 (21)十、异常现象及其处理 (22)十一、巡回检查 (23)十二、主要设备性能 (24)十三、附表 (25)十四、精脱硫安全技术规程 (27)一、岗位任务及职责范围1.岗位任务:从焦炉气压缩机来的经湿法脱硫后的焦炉煤气,流量30000M3,H2S含量小于20mg/Nm3,有机硫含量小于400mg/Nm3,通过两次有机硫加氢转化和两次脱除无机硫的干法流程,使焦炉气中的总硫含量(主要包括无机硫和有机硫)脱至0.1ppm以下,达到转化和甲醇合成的要求。
原料气H2S的存在,如果不脱除,会造成:○1设备、管道、阀门的腐蚀;○2转化催化剂、甲醇合成催化剂中毒,降低或失去活性。
2.岗位职责范围负责过滤器、预脱硫槽A/B、1#铁钼转化器、氧化铁脱硫槽A/B/C,2#铁钼转化器,氧化锌脱硫槽A/B,升温炉等设备及附属管道阀门,仪表的开停车、生产操作、维护保养;负责系统的缺陷检查、登记、消除及联系处理,防止系统泄漏污染环境。
做好设备检修前的工艺处理工作,检修后的运行和验收工作,负责本岗位消防器材,防毒面具等的使用与维护,负责本系统安全运行。
二、产品说明精脱硫后合格焦炉气:组成:V%H2:60.29 CO:6.35 CO2:2.75 CH4:26.04 N2:3.11 C mHn:0.71 总硫:0.1ppm三、原材料及化学品规格1、湿脱硫来原料焦炉气组成:V%H2:61.09 CO:6.28 CO2:2.72 CH4:25.76 N2:3.08 C mHn:0.70 O2:0.37 总硫:0.1ppm H2S:20mg/Nm3有机硫:400mg/Nm32、催化剂技术规格四、原材料及动力消耗定额3、原材料消耗4、催化剂、化学品消耗五、生产原理1、HT-03特种活性碳吸油剂HT-03特种活性碳吸油剂利用活性碳孔隙发达、比表面积大的特点,对大分子物质具有显著的吸附性,而且吸附饱和后可反复再生。
焦炉煤气制甲醇的补碳

焦炉煤气制甲醇的补碳摘要:目前甲醇生产原料比较复杂,不同原料气的氢碳比往往偏离理论值,需对其补碳或脱碳。
焦炉煤气制甲醇工艺刚刚兴起,其原料气也存在着氢过剩的现象,大量的氢被浪费掉,但至今一直未有对焦炉煤气制甲醇补碳的工艺。
自工业革命以来,向大气中排入的二氧化碳逐年增加,大气的温室效应也随之增强,已引起全球气候变暖等一系列严重问题。
用工业生产中这些排放的二氧化碳与焦炉煤气制甲醇工艺中过剩的氢合成甲醇,这样不仅可以节能减排、保护环境,还可以优化工艺,增加产量。
关键词:焦炉煤气甲醇补碳1 补碳方案的理论基础甲醇是由一氧化碳、二氧化碳与氢气在一定温度、压力和催化剂条件下反应生成的。
反应式如下:CO+2H2=CH3OH△H=-90.56kJ/molCO2+3H2=CH3OH+H2O△H=-49.43kJ/mol根据上述反应方程式可知,氢与一氧化碳合成甲醇的物质的量比为2,与二氧化碳合成甲醇的物质的量比为3。
当一氧化碳与二氧化碳都存在时,对原料气中氢碳比(M值)用下式表达:M=(H2-CO2)/(CO+CO2)=2.05~2.15生产中合理的氢碳比例应比化学计量比稍高一些,按化学计量比值,M值约为2,实际生产中控制得略高于2,即通常保持略高的氢含量。
过量的氢气可抑制羰基铁与高级醇的生成,并对延长催化剂寿命起着有益的作用。
补碳对焦炉煤气制甲醇工艺有如下优点:(1)利用合成反应中过剩的氢来合成甲醇,减少不必要的浪费,提高产量;(2)补碳后会将过量的氢消耗掉,减少压缩机的无用功,提高压缩机效率;(3)补碳可利用副产廉价二氧化碳,降低补碳成本,提高企业竞争力。
(4)补碳可减少污染,减少温室效应,保护环境。
2 补碳位置的选取补碳位置选取的不同,会有不同的影响。
2.1 转化炉前或转化炉后的补入转化气中CO与CO2的相对比例是由转化炉中的变换反应所决定的[2],CO+H2O==CO2+H2二氧化碳在转化炉前补入可抑制CO转化为CO2,提高入合成塔气CO含量。
C307型甲醇合成催化剂使用总结

精甲醇 2722t优等品率为 9 %。20 9 5 , 1 03年 1 0 月 , 系统进 行 了扩产 改造 , 该 新增 1台 180m 0 m 同类型合 成塔 ( 以下 简称 为小塔 ) 双塔并联运 , 行, 装填南化院新开发 的 C 0 37型低压 甲醇催化 剂 , 20 至 04年 l , 生 产 精 甲醇 1759 7t 2月 共 9 6 . 。 目前使用 的是第 三炉催化剂 , 然采用南化 院 依
2 催化 剂升温 还原情 况
1 C 0 甲醇合 成催 化剂 的性 能及装填 37型
() 1 物化 性能
( ) 次 2台合 成 塔 的 升 温还 原 同时 进 行 , 1本
为使整个升温还原工作顺 利进行 , 在总结前 2炉
催化 剂 升温还 原经 验 基 础上 , 定 了详 细 的 升温 制
束, 转人轻负荷期。整个还原过程历时9 , 6h有效 升温还 原时 间约 9 。在 整个 还 原过 程 中 , 0h 进展
比较 顺 利 , 化 剂 还 原 比较 彻底 , 催 累计 出 水 量 为
C 0 型 甲醇合成催化剂外观 为两端球面的 37 黑色圆柱体 , 规格为 0 m× 5m 堆密度为 5m 4— m,
15 7k/ , .8 gL 比表 面积 9 0—10m / , 1 g平均 径向抗
还原方案( 1 , 表 ) 同时对还原气提出了具体要求:
O < . %, 2 0 2 S<0 1m,m ( 态 ) N <1 . e 标 / ,H 0×
1’ 3 7m tao snh s a l t hog eueo trecagso ect yt esrsa r eC 0 e n l y tei ct y .T r ht s f he h re f h a l aue r ) p h s as u h t a sm e
- 1、下载文档前请自行甄别文档内容的完整性,平台不提供额外的编辑、内容补充、找答案等附加服务。
- 2、"仅部分预览"的文档,不可在线预览部分如存在完整性等问题,可反馈申请退款(可完整预览的文档不适用该条件!)。
- 3、如文档侵犯您的权益,请联系客服反馈,我们会尽快为您处理(人工客服工作时间:9:00-18:30)。
精脱硫转化系统开车方案及操作规程第一节精脱硫转化系统生产原理及流程一、原理1、精脱硫原理通过铁钼触媒及镍钼触媒将焦炉气中的硫醇(RSR),噻吩(C4H4S)、二硫化碳(CS2)、硫氧化碳(COS)等有机硫加氢转化成无机硫H2S、不饱和烃加氢转化为饱和烃;再利用铁锰脱硫剂及氧化锌脱硫剂,除去H2S,使焦炉气硫含量≤0.1ppm。
(1)加氢反应RSH+H2=RH+H2S+Q; RSR′+H2=RH+R′H+H2S+QC4H4S+4H2=C4H10+H2S+Q; CS2+4H2=CH4+2H2S+QCOS+H2=CO+H2S+Q; C2H4+H2=C2H6+Q生产中铁钼触媒在进行上述反应的同时还存在以下副反应:CO+3H2=CH4+H2O+Q (甲烷化反应)2H2+O2=2H2O+Q (燃烧反应)C2H4=C+CH4 +Q(析碳反应)2CO=C+CO2+Q(析碳反应)生产中加氢反应及副反应均为放热反应,在操作中应控制好触媒层温度。
铁钼触媒主要的副反应是甲烷化反应,因此操作中要注意原料气中CO含量的变化。
(2)脱硫反应○1铁锰脱硫剂对H2S的吸收反应:FeS+H2S=FeS2+H2MnO+H2S=MnS+H2OMnS+H2S=MnS2+H2○2氧化锌脱硫剂对硫的吸收反应:ZnO+H2S=ZnS+H2O2、转化原理在焦炉气中加入水蒸汽,在一定压力及温度下,通过催化剂作用,生成合成甲醇有用的H2、CO及CO2。
转化反应:CH4+H2O=CO+3H2-QCO+ H2O=CO2+H2+QCH4=C+2H2-Q二、流程1、精脱硫转化系统流程叙述来自焦炉气压缩机(C201)的焦炉气含H2S≤20mg/Nm3,有机硫250mg/Nm3,其压力为2.5MPa,温度100~110℃。
焦炉气通过两台并联的脱油剂槽(D106a、b)脱除掉焦炉气中的油水之后进入冷热交换器(E104),被来自铁锰脱硫槽D103a、D103b的一级脱硫气第一次加热;然后进入原料气第一预热器(E101)被来自转化气废热锅炉(E105)的转化气第二次加热;再经原料气第二预热器(E102)被来自气气换热器(E103)的转化气第三次加热;最后进入加热炉B101被第四次加热。
四次加热后焦炉气温度升至320℃,进入两台并联的铁钼预加氢槽(D101a、D101b)再进入一台铁钼加氢槽(D102)。
在铁钼触媒的作用下,焦炉气中绝大部分有机硫加氢转化成无机硫H2S,不饱和烃加氢转化为饱和烃。
由铁钼加氢槽出来的焦炉气进入两台可并可串的铁锰脱硫槽(D103a、D103b),焦炉气中的大部分无机硫H2S 被脱除(此焦炉气称为一级脱硫气)。
一级脱硫气经冷热交换器(E104)与原料气换热,温度降至360℃之后进入镍钼加氢槽(D104),在镍钼催化剂的作用下,焦炉气中剩余的少量有机硫进一步加氢转化成无机硫,之后进入两台可串可并的氧化锌脱硫槽(D105),最终将焦炉气中的总硫脱除至小于0.1PPm(此焦炉气称为二级脱硫气,或净化气)。
净化气送往转化工序。
来自脱硫系统装置的净化气,总S≤0.1ppm,配入中压蒸汽混合后进入气-气换热器E103被转化气加热后,进入开工加热炉B101b升温,温度至到500℃,进入换热式转化炉H101管程在催化剂作用下CH4经过初步转化,混合气进入二段转化炉B102内,与从开工加热炉B101b来的热氧气混合燃烧,为二段炉催化剂内转化反应提供热量,二段炉出口转化气CH4≤0.1℅,温度900℃,进入H101壳程放热,为H101管程内初步转化反应提供热量,从H101壳程出来的气体,温度为600-700℃,依次进入多个换热器、预热原料气、精馏液及副产中压蒸汽回收转化气热量,进换热器的次序为:气-气换热器E103、原料气第二预热器E102、转化废锅E105、原料气第一预热器E101、第一锅炉给水预热器E106、第一分离器F102及精馏主塔再沸器E405、预塔再沸器E404、脱盐水预热器E107及转化气水冷器E108,再进入第四分离器F105,分离冷凝液后,转化气去循环压缩机供合成甲醇用。
2、 精脱硫转化方块流程B101a 盘管D101aD101bD102D103aD105b B101b 中间煤气盘管 H101管程 E105管程 H101壳程 F102 E106管程 E101管程 E103管程E102管程 B102 E104管程D103bE107管程 E108管程F203 F105 去压缩工序O 2E102壳程 E101壳程 焦炉气来自压缩 D106aD106bE104壳程 D104 D105bE103壳程第二节精脱硫系统催化剂的硫化与还原方案一、原理及目的1、加氢催化剂的硫化原理及目的加氢催化剂是指铁钼加氢催化剂与镍钼加氢催化剂。
加氢催化剂在使用前必须对其进行硫化,也即使其在较高温度下与H2S反应,催化剂则由氧化态变为硫化态,获得较高的活性。
硫化剂为H2S。
H2S来源于CS2+H2的反应或者高硫焦炉煤气。
FeO+H2S=FeS+H2O+QMoO2+2 H2S=MoS2+2H2O+QFe2O3+2 H2S+H2≒2FeS+3H2O+QNiO+ H2S≒NiS+H2O+Q转化为FeS 、MoS2的硫化态催化剂对有机硫加氢具有催化作用。
2、脱硫剂升温还原的原理及目的脱硫剂是指铁锰脱硫催化剂与氧化锌脱硫催化剂。
脱硫剂的升温还原指的是铁锰脱硫剂的升温还原,即将氧化态的铁锰与H2、CO反应,成为还原态的铁锰。
还原态的铁锰催化剂具有吸附H2S活性。
还原剂为焦炉气中的H2、CO。
铁锰催化剂还原反应:MnO2+H2=MnO+H2O+QMnO2+CO=MnO+CO2+Q3Fe2O3+H22Fe3O4+H2O+Q3Fe2O3+CO 2Fe3O4+CO2+Q氧化锌脱硫剂本身具有吸附H2S的活性,只需要升温,不需要进行还原操作。
3、转化催化剂升温还原的原理及目的转化催化剂的主要成分为镍。
厂家提供的催化剂为氧化态形式,使用前必须使其与H2、CO反应,将其还原成具有活性的还原态形式,同时脱除催化剂中少量的毒物(硫化物)。
还原剂为S≤0.1ppm的合格焦炉气(H2、CO)。
还原反应如下:NiO+ H2=Ni+ H2O-Q NiO+CO=Ni+ CO2+Q3 NiO+CH4=3Ni+ CO+2 H2O-Q转化催化剂还原需在650℃以上进行。
还原压力为0.5~2.0MPa,空速40~60h-1,还原时间达规定温度后不小于8 h。
还原初期要求水碳比5~7,随还原过程的进行和结束水碳比逐渐调至正常。
二、脱硫转化系统升温(一)升温1、升温流程脱硫转化系统升温用N2作为载体。
脱硫装置与转化系统串联进行升温。
流程如下:空分来的低压N2经焦炉气压缩机C201压缩后,通过正路也即煤气管线依次进入油过滤器D106ab、冷热交换器E104壳程、原料气第一预热器E101壳程、第二预热器E102壳程及开工加热炉B101a盘管进行加热。
B101a出来后的热N2,沿N2升温线进入并联的单槽铁钼预加氢槽,然后依次串联进入铁钼加氢槽D102、并联的铁锰脱硫槽D103ab、镍钼加氢槽D104及并联的氧化锌脱硫槽D105ab。
从D105ab出来的N2沿主流程管线进入转化系统。
N2首先进入E103壳程,再进入开工加热炉B101b中间盘管进行再加热,再加热N2沿主流程依次进入一段转化炉H101管程、二段转化炉B102、一段转化炉H101壳程、气气换热器E103管程、原料气第二预热器E102管程、废热锅炉E105管程、原料气第一预热器E101管程、第一锅炉给水预热器E106管程、第一分离器F102、脱盐水换热器E107管程、转化气水冷器E108管程、第四分离器F105,最后进入新鲜气入口缓冲罐F203。
将F203来的N2与空分来的中压N2引入联合压缩机C202,启动C202,将压缩后的N2一部分与C201出口N2混合补充进入D106ab,一部分沿O2管线直接进入B101b上层、与下层盘管加热后进入B102,与主流程N2混合,进入下一轮升温循环。
升温方块流程图:D106aN2E104壳程C201D106bE102壳程E101壳程E102壳程D102放空 放空 放空B101a 盘管D101aD101b D102D103a D105aD105b E103壳程B101b 中间煤气盘管 H101管程 E105管程 H101壳程F102 E106管程 E101管程 E103管程E102管程 B102两路 N 2合并 升温线D104D103b E107管程 E108管程 F203 放空 放空 F105 C202 D106ab 循环 B101b 第一组盘管B102两路N 2合并 B101b 第三组盘管 放空空分氮气 C201 D106ab 循环2.升温开工加热炉点火开车依开车方案进行(见开工加热炉B101ab操作规程)。
(1)B101a升温速率控制从C201来的N2温度约90~100℃,在B101a内被加热升温,升温速率控制在20~50℃/h。
通过B101a第一组盘管后温度计TI-126及第二组盘管后温度计TI-166观察温度;用HIC102a调节进B101a的燃料气量来控制升温速率。
N2流量依空分送来的气量,通过精脱硫煤气调节阀FRCA102控制稳定。
(2)B102升温速率控制经过加热升温脱硫催化剂后,温度降低的N2进入B101b中间盘管继续加热,同时联压机C202送出的N2沿O2管线进入B101b上层盘管与下层盘管加热,观察进入B102前后温度TI-116、TI-117及TI-112、TI-115,通过HIC102b调节进B101b燃料气量,控制其升温速率为20~50℃/h。
(3)压力控制升温阶段系统压力可控制在0.3~0.5MPa。
3、升温、恒温阶段,脱除催化剂的吸附水(1)空分N2量约2500~3000Nm3/h, 通过煤气流量调节阀FRCA102控制稳定其流量;通过HIC101b调节燃气量,控制B101a盘管出口气温度TI-166(TI-176) ≯首先加热催化剂床层温度50℃,调节床层升温速率为20~50℃/h,通过升温管线对串联的脱硫转化系统进行升温。
(2)当首先加热的D101ab床层温度升到120℃时,打开D102升温线阀门,同时关小D101ab升温线阀,关闭D101ab出口阀,用其放空阀控制压力为0.3~0.5MPa,120℃恒温2~3小时。
D102催化剂则成为首先加热对象。
(3)当D102床层温度达120℃时,打开并联的D103ab升温线阀,同时关小D102升温线阀,关闭D102出口阀,用其放空阀控制压力为0.3~0.5MPa,120℃恒温2~3小时。
并联的D103ab催化剂则成为首先加热对象。