叶片泵有哪些优缺点(内容清晰)
叶片泵有哪些优缺点(内容清晰)
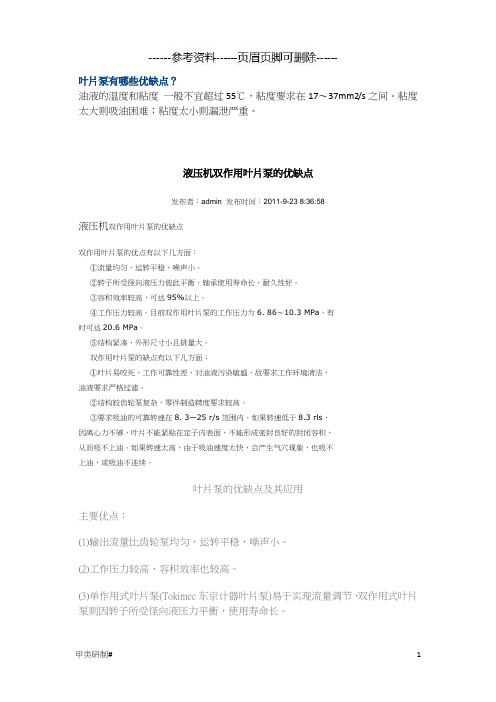
叶片泵有哪些优缺点?油液的温度和粘度一般不宜超过55℃,粘度要求在17~37mm2/s之间。
粘度太大则吸油困难;粘度太小则漏泄严重。
液压机双作用叶片泵的优缺点发布者:admin 发布时间:2011-9-23 8:36:58液压机双作用叶片泵的优缺点双作用叶片泵的优点有以下几方面:①流量均匀,运转平稳,噪声小。
②转子所受径向液压力彼此平衡.轴承使用寿命长,耐久性好。
③容积效率较高,可达95%以上。
④工作压力较高。
目前双作用叶片泵的工作压力为6. 86~10.3 MPa,有时可达20.6 MPa。
⑤结构紧凑,外形尺寸小且排量大。
双作用叶片泵的缺点有以下几方面:①叶片易咬死,工作可靠性差,对油液污染敏感,故要求工作环境清洁,油液要求严格过滤。
②结构较齿轮泵复杂,零件制造精度要求较高。
③要求吸油的可靠转速在8. 3—25 r/s范围内。
如果转速低于8.3 rls,因离心力不够,叶片不能紧贴在定子内表面,不能形成密封良好的封闭容积,从而吸不上油。
如果转速太高,由于吸油速度太快,会产生气穴现象,也吸不上油,或吸油不连续。
叶片泵的优缺点及其应用主要优点:(1)输出流量比齿轮泵均匀,运转平稳,噪声小。
(2)工作压力较高,容积效率也较高。
(3)单作用式叶片泵(Tokimec东京计器叶片泵)易于实现流量调节,双作用式叶片泵则因转子所受径向液压力平衡,使用寿命长。
(4)结构紧凑,轮廓尺寸小而流量较大。
主要缺点:(1)自吸性能较齿轮泵差,对吸油条件要求较严,其转速范围必须在500~ 1500 r/min范围内。
(2)对油液污染较敏感,叶片容易被油液中杂质咬死,工作可靠性较差。
(3)结构较复杂,零件制造精度要求较高,价格较高。
叶片泵一般用在中压(6.3 M Pa)液压系统中,主要用于机床控制,特别是双作用式叶片泵(东京计器SQP叶片泵)因流量脉动很小,因此在精密机床中得到广泛使用。
叶片泵运行注意事项发布时间:2012-09-03 09:58:30浏览次数:127作为泵产品,叶片泵更多地指滑片泵,例如:东京计器SQP叶片泵,油研PV2R 叶片泵,丹尼逊T6叶片泵,叶片泵的管理要点除需防干转和过载、防吸入空气和吸入真空度过大外,还应注意:1、泵转向改变,则其吸排方向也改变,叶片泵都有规定的转向,不允许调反。
叶片泵工作原理及应用

降低噪音和振动
优化流体动力学设计
通过改进泵的流体动力学设计,降低 泵运行时的噪音和振动。例如,优化 进出口管道设计、减少流体阻力等措 施,以减小泵的振动和噪音。
减震和隔振措施
在泵的底座或支撑结构中采取减震和 隔振措施,以减小泵运行时的振动和 噪音对周围环境的影响。例如,安装 减震器和隔振器等装置。
优点
效率高
叶片泵由于其独特的工作原理, 能够在输送介质时减少摩擦和能 量损失,因此具有较高的效率。
流量稳定
叶片泵的流量输出相对稳定,不 受压力和温度等因素的影响,适 用于需要稳定流量的场合。
寿命长
由于叶片泵内部结构简单,磨 损较小,因此具有较长的使用 寿命。
适用范围广
叶片泵可以适用于各种不同的介质 和工况条件,如油、水、气体等, 因此在许多领域都有广泛的应用。
降低噪音和振动
优化流体动力学设计
通过改进泵的流体动力学设计,降低 泵运行时的噪音和振动。例如,优化 进出口管道设计、减少流体阻力等措 施,以减小泵的振动和噪音。
减震和隔振措施
在泵的底座或支撑结构中采取减震和 隔振措施,以减小泵运行时的振动和 噪音对周围环境的影响。例如,安装 减震器和隔振器等装置。
离心式叶片泵的优点是流量大、扬程低、结构简单、使用维 护方便,适用于输送不含固体颗粒和纤维的液体,尤其适用 于输送粘度较大的液体。
轴流式叶片泵工作原理
轴流式叶片泵是利用叶轮的高速旋转来输送液体的叶片泵 ,其工作原理是:当泵轴旋转时,叶片在离心力的作用下 向外甩出,将液体沿叶片泵的压出室甩出,进入压出室, 然后进入排出管路或下一级叶轮。
混流式叶片泵的优点是流量大、扬程低、结构简单、使用维护方便,适用于输送 不含固体颗粒和纤维的液体,尤其适用于输送粘度较大的液体。
叶片式液压助力泵的作用

叶片式液压助力泵的作用叶片式液压助力泵是一种常见的液压泵,它的作用是为液压系统提供液压动力,并在系统中提供辅助的液压助力。
下文将从叶片式液压助力泵的工作原理、结构特点、应用领域和优缺点等方面进行详细介绍。
一、叶片式液压助力泵的工作原理叶片式液压助力泵是利用偏心机构带动转子,使转子旋转以及叶片的伸缩来实现泵的工作。
当转子旋转时,离心力将叶片推向泵体内壁,形成密封工作腔,同时吸入液体进入工作腔。
当转子进一步旋转时,叶片被迫跟随转子旋转,并推开内壁密封圈,将液体排出泵体,从而形成连续的液压压力和流动。
在液压助力泵的工作过程中,液体从进口处吸入,然后通过转子的旋转和叶片的伸缩不断被挤压和排出,最后从出口处流出。
转子旋转的速度和叶片伸缩的幅度决定了液体的流量和压力。
当系统液压助力泵的工作压力达到一定程度时,压力控制装置会自动调节泵的输出压力,以保证系统的正常运行。
二、叶片式液压助力泵的结构特点1.泵体结构简单:叶片式液压助力泵只有少数几个主要部件,包括泵体、转子、叶片和轴承等,结构简单、制造成本低。
2.体积小、重量轻:叶片式液压助力泵的体积和重量都相对较小,适用于安装空间有限的场合。
3.输出压力稳定:由于叶片式液压助力泵在工作过程中叶片可以伸缩,可以根据系统液压需求自动调节输出压力,使系统压力保持稳定。
4.启动转矩小:叶片式液压助力泵的启动转矩相对较小,可以在较低的起动电流下启动,降低系统能耗。
5.噪音低:叶片式液压助力泵的噪音较低,利于提高工作环境的舒适性。
三、叶片式液压助力泵的应用领域叶片式液压助力泵广泛应用于各种液压系统中,特别是对于对压力和流量要求较高的系统。
以下是一些常见的应用领域:1.工程机械:叶片式液压助力泵可以应用于挖掘机、起重机、装载机等各种工程机械上,用来提供液压动力,并提供辅助助力。
2.汽车工业:叶片式液压助力泵用于汽车的液压助力转向系统,可以提供转向动力,使驾驶员更轻松地操纵转向。
叶片泵的原理特点和应用
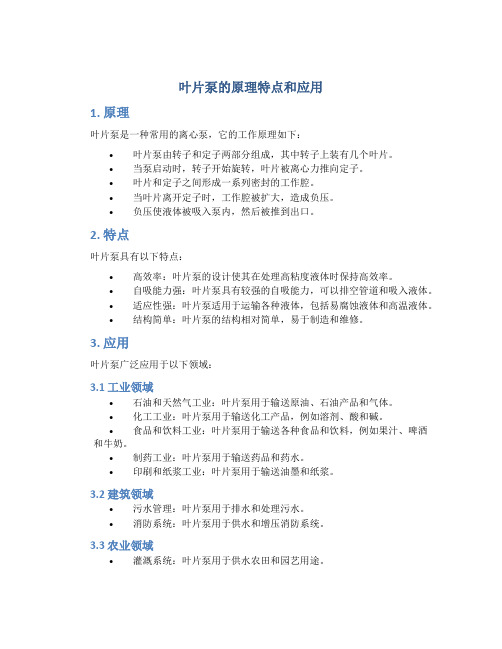
叶片泵的原理特点和应用1. 原理叶片泵是一种常用的离心泵,它的工作原理如下:•叶片泵由转子和定子两部分组成,其中转子上装有几个叶片。
•当泵启动时,转子开始旋转,叶片被离心力推向定子。
•叶片和定子之间形成一系列密封的工作腔。
•当叶片离开定子时,工作腔被扩大,造成负压。
•负压使液体被吸入泵内,然后被推到出口。
2. 特点叶片泵具有以下特点:•高效率:叶片泵的设计使其在处理高粘度液体时保持高效率。
•自吸能力强:叶片泵具有较强的自吸能力,可以排空管道和吸入液体。
•适应性强:叶片泵适用于运输各种液体,包括易腐蚀液体和高温液体。
•结构简单:叶片泵的结构相对简单,易于制造和维修。
3. 应用叶片泵广泛应用于以下领域:3.1 工业领域•石油和天然气工业:叶片泵用于输送原油、石油产品和气体。
•化工工业:叶片泵用于输送化工产品,例如溶剂、酸和碱。
•食品和饮料工业:叶片泵用于输送各种食品和饮料,例如果汁、啤酒和牛奶。
•制药工业:叶片泵用于输送药品和药水。
•印刷和纸浆工业:叶片泵用于输送油墨和纸浆。
3.2 建筑领域•污水管理:叶片泵用于排水和处理污水。
•消防系统:叶片泵用于供水和增压消防系统。
3.3 农业领域•灌溉系统:叶片泵用于供水农田和园艺用途。
3.4 其他领域•汽车工业:叶片泵用于发动机冷却和润滑系统。
•船舶工业:叶片泵用于泵舱排水和船用提取水源。
结论叶片泵是一种应用广泛的离心泵,其原理简单而高效。
它具有自吸能力强、适应性强和结构简单等特点,被广泛应用于工业、建筑、农业和其他领域。
在未来,叶片泵还将继续发展,以满足不同行业的需求。
第八章 叶片泵

第八章 叶片泵叶片泵具有流量均匀,运转平稳,噪音低,体积小,重量轻等优点。
在机床、工程机械、船舶、压铸及冶金设备中得到广泛的应用。
中低压叶片泵的工作压力一般为8MPa ,中高压叶片泵的工作压力可达25MPa 至32MPa 。
泵的转速范围为600~2500r/min 。
叶片泵对油液的清洁度要求较高。
此外,与齿轮泵相比,叶片泵的制造工艺要求也较高。
叶片泵主要分为单作用(转子每转完成吸、排油各一次)和双作用(转子每转完成吸、排油各二次)两种形式。
双作用叶片泵与单作用式相比,其流量均匀性好,转子体所受的径向液压力基本平衡。
双作用叶片泵都做成定量泵形式,单作用叶片泵一般设计成可以无级调节排量的变量泵。
§8-1 双作用叶片泵的工作原理和流量一、双作用叶片泵工作原理图8-1是双作用叶片泵的工作原理图。
定子的腰圆形表面由二段半径为R 的大圆弧,二段半径为r 的小圆弧以及四段连接大小圆弧的平滑曲线组成。
叶片在转子的叶片槽内可以滑动。
转子、叶片、定子都夹在前后两个配流盘中间。
当转子旋转时,叶片受离心力而紧贴定子内表面,起密封作用,将吸油腔与排油腔隔开。
当转子与叶片从定子内表面的小圆弧区向其大圆弧区移动时,两个油封叶片之间的容积增大,通过配流盘上的配油窗口(吸油槽)吸油;由大圆弧区移向小圆弧区时,通过配流盘上的配油窗口(排油槽)排油。
转子转一周,叶片在槽内往复两次,完成两个吸、排油过程,故称双作用式。
泵转子体中的叶片槽底部通排油腔。
因此在建立排油压力后,处在吸油区的叶片贴紧定子内表面的压紧力为其离心力和叶片底部液压力之和。
在压力还未建立起来的启动时刻,此压紧力仅由离心力产生。
如果离心力不够大,叶片就不能与定子内表面贴紧以形成高,低压腔之间的可靠密封,泵由于吸、排油腔沟通而不能进行正常工作。
这就是叶片泵最低转速不能太低的原因。
双作用叶片泵的两个排油腔及两个吸油腔均为对称布置,故作用在转子上的液压力互相平衡,轴和轴承的寿命较长。
3-3 叶片泵
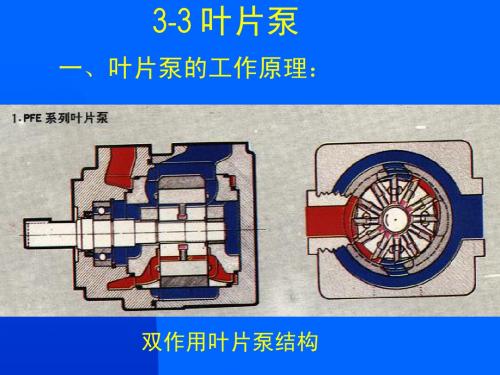
八、双作用叶片泵的结构设计要点
(1)、叶片数和定子曲线的确定
叶片数Z多选12,在流量较小时可取为10, 以减少叶片槽的加工量并增加根部强度。 当Z=12时,定子曲线多用等加速曲线;当 值比较小时也可用正弦加速曲线,可消除 “软冲”点; Z=10时可选用修正的等加速(或正弦加速) 修正曲线,以使流量均匀。
B 0.45 ~ 1.0r
式中 ——定子小半径。 最终经验算油窗口的流速不要超过6~9m/s,确定 轴向宽度值
r
四、双作用叶片泵的设计要点
(5)、定子短半径和长半径的计算
小圆弧半径一般取
r rz (0.5 ~ 1) mm,
根据选用的过渡曲线不“脱空”条件的最
R 大值 r max ,可初步确定长半径,然后 由排量计算公式校核设计排量与要求达到 排量(设计参数)的误差不超过5%。
(7)、主要零件的材料与技术要求
b、转子
材料:40Cr、20Cr或12CrNi3 热处理:HRC50~60,20Cr和12CrNi3要渗碳淬火。 加工要求:转子宽度比定子宽度小0.02~0.04mm; 端面平行度0.003mm;端面粗糙度0.2~0.1μm;叶片 槽平行度0.01mm;叶片槽粗糙度0.2~0.1μm。
1、对定子曲线的要求
c.使泵的排出流量均匀
为了使泵的瞬时流量均匀,叶片数和定子 曲线形状的选择应使吸油区过渡曲线上所有叶 片径向速度之和在整个运行过程(即不同转角 时)中等于或接近常数。
2、定子过渡曲线及其特点
修正的阿基米德螺线;正弦加速曲线;等加速 等减速曲线;高次曲线。
a
等加速、等减速曲线
叶片泵的工作原理

工作原理
流体传输路 线
配油盘
配油盘吸入口流速 一般为4~5m/s,最高不超过 6 m/s,防止流动阻力大而 产生气穴现象; 配油盘上开盲孔是 为了平衡轴向力; 配油盘上排出窗口 开三角形节流是为了防止液 压冲击和噪声; 定子圆弧段的圆心角 α ≥配油盘上密封区圆心象。 角β ≥两叶片之间的圆心角γ ,以防止发生困 油现
泵的流量减小 当pAx大于Ksx0时,定子右移,
pAx 有偏心距e e max x0 Ks
kq Ksk 1 q kq( x0 e max) ( Ax )p Ks kq
由以上公式可得内反馈限压式变量叶片泵的静特性曲线: 1、当泵的工作压力p小 于限定压力pB 时,油 压作用力不能克服弹簧 的预紧力,定子压紧在 流量调节螺钉上,泵的 流量如AB所示:
结构
• 如图所示双作用式叶片 泵是由定子、转子、叶 片、配流盘和泵体组成, 转子与定子同心安装, 定子的内曲线是由两段 长半径圆弧、两段短半 径圆弧和四段过度曲线 所组成,共有八段曲线。
工作原理
• 如图所示,转子做顺时针旋转,叶 片在离心力作用下径向伸出,其顶 部在定子内曲线上滑动。此时,由 两叶片、转子外圆、定子内曲线及 两侧配有盘所组成的密闭的工作腔 的容积在不断地变化,在经过右下 角以及左上角的配油窗口处时,叶 片伸出,工作腔容积增加,形成真 空,油液通过吸油窗吸入;在经过 右上角及左下角的配油窗口处时, 叶片回缩,工作腔容积变小,压强 增大,液压缸油液通过液压窗口输 出。
限压式变量叶片泵适用于工作机构要求快速轻载和 慢速重载要求的液压系统中。 快速轻载时,变量泵工作在曲线AB段,此时泵的压 力小于限定压力,定子在流量调节螺钉上,泵的流 量大。 慢速重载时,变量泵工作在曲线BC段,此时泵的压 力大于限定压力,泵的流量降低。 与定量泵相比优点: 减少功率损耗,降低油液温升。
叶片泵
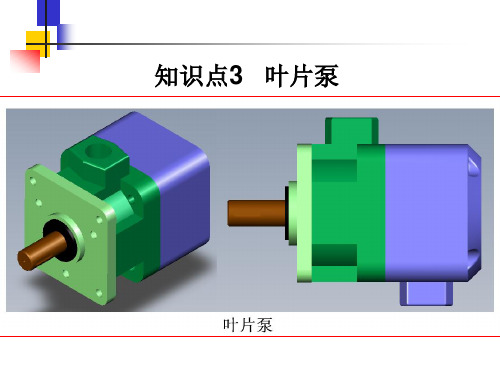
4、 提高双作用叶片泵压力,需要采取以下措施 (a)端面间隙自动补偿 这种方法是将配油盘的一 侧与压油腔连通,使配油盘在液压油推力作用下压 向定子端面。泵的工作压力越高,配油盘就会自动 压紧定子,同时配油盘产生适量的弹性变形,使转 子与配油盘间隙进行自动补偿,从而提高双作用叶 片泵输出压力。该方法与提高齿轮泵压力方法中的 齿轮端面间隙自动补偿相类似。 (b)减少叶片对定子作用力 前已阐述,为保证叶 片顶部与定子内表面紧密接触,所有叶片根部都与 压油腔相通。当叶片在吸油腔时,叶片底部作用着 压油腔的压力,而顶部却作用着吸油腔的压力,这 一压力差使叶片以很大的力压向定子内表面,在叶 片和定子之间产生强烈的摩擦和磨损,使泵的寿命 降低。
3.叶片倾角 FN 分解
FT=FNsinβ
——垂直于叶片,增大了 摩擦,且易使叶片折断 Fp =FNcosβ ——和叶片底部液压力平 衡 压力角: 定子对叶片的法向反力FN与 叶片运动方向的夹 角。 倾角:叶片与径向半径的夹角。
叶片泵的叶片倾角一般取为10°~14°。
Go
一般叶片倾角 为13 °
所以作用在转子上的油液压力相互平衡,因此双作用
叶片泵又称为卸荷式叶片泵。
3、双作用叶片泵流量
结 论
双作用叶片泵为定量泵,双作用叶片 泵仍存在流量脉动,当叶片数为4的整数 倍、且大于8时的流量脉动较小,故 通常 取叶片数为12或16。
4、结构特点
1、定子工作表面曲线 2、配油盘
(1)叶片间的夹角 (2) 卸荷三பைடு நூலகம்槽 (3)环形槽
外反馈式变量叶片泵-通过限定泵的工作压力来调节 从而调节q
限压式变量叶片泵
限压式变量叶片泵的应用
执行机构需要有快、慢速运动的场合, 如:组合机床进给系统实现快进、工进、快退等
- 1、下载文档前请自行甄别文档内容的完整性,平台不提供额外的编辑、内容补充、找答案等附加服务。
- 2、"仅部分预览"的文档,不可在线预览部分如存在完整性等问题,可反馈申请退款(可完整预览的文档不适用该条件!)。
- 3、如文档侵犯您的权益,请联系客服反馈,我们会尽快为您处理(人工客服工作时间:9:00-18:30)。
叶片泵有哪些优缺点?
油液的温度和粘度一般不宜超过55℃,粘度要求在17~37mm2/s之间。
粘度太大则吸油困难;粘度太小则漏泄严重。
液压机双作用叶片泵的优缺点
发布者:admin 发布时间:2011-9-23 8:36:58
液压机双作用叶片泵的优缺点
双作用叶片泵的优点有以下几方面:
①流量均匀,运转平稳,噪声小。
②转子所受径向液压力彼此平衡.轴承使用寿命长,耐久性好。
③容积效率较高,可达95%以上。
④工作压力较高。
目前双作用叶片泵的工作压力为6. 86~10.3 MPa,有
时可达20.6 MPa。
⑤结构紧凑,外形尺寸小且排量大。
双作用叶片泵的缺点有以下几方面:
①叶片易咬死,工作可靠性差,对油液污染敏感,故要求工作环境清洁,
油液要求严格过滤。
②结构较齿轮泵复杂,零件制造精度要求较高。
③要求吸油的可靠转速在8. 3—25 r/s范围内。
如果转速低于8.3 rls,
因离心力不够,叶片不能紧贴在定子内表面,不能形成密封良好的封闭容积,
从而吸不上油。
如果转速太高,由于吸油速度太快,会产生气穴现象,也吸不
上油,或吸油不连续。
叶片泵的优缺点及其应用
主要优点:
(1)输出流量比齿轮泵均匀,运转平稳,噪声小。
(2)工作压力较高,容积效率也较高。
(3)单作用式叶片泵(Tokimec东京计器叶片泵)易于实现流量调节,双作用式叶片泵则因转子所受径向液压力平衡,使用寿命长。
(4)结构紧凑,轮廓尺寸小而流量较大。
主要缺点:
(1)自吸性能较齿轮泵差,对吸油条件要求较严,其转速范围必须在
500~ 1500 r/min范围内。
(2)对油液污染较敏感,叶片容易被油液中杂质咬死,工作可靠性较差。
(3)结构较复杂,零件制造精度要求较高,价格较高。
叶片泵一般用在中压(6.3 M Pa)液压系统中,主要用于机床控制,特别是双作用式叶片泵(东京计器SQP叶片泵)因流量脉动很小,因此在精密机床中得到广泛使用。
叶片泵运行注意事项
发布时间:2012-09-03 09:58:30
浏览次数:127
作为泵产品,叶片泵更多地指滑片泵,例如:东京计器SQP叶片泵,油研PV2R 叶片泵,丹尼逊T6叶片泵,叶片泵的管理要点除需防干转和过载、防吸入空气和吸入真空度过大外,还应注意:
1、泵转向改变,则其吸排方向也改变,叶片泵都有规定的转向,不允许调反。
因为转子叶槽有倾斜,叶片有倒角,叶片底部与排油腔通,配油盘上的节流槽和吸、排口是按既定转向设计,因此可逆转的叶片泵必须专门设计。
2、叶片泵装配配油盘与定子用定位销正确定位,叶片、转子、配油盘都不得装反,定子内表面吸入区部分最易磨损,必要时可将其翻转安装,以使原吸入区变为排出区而继续使用。
3、拆装注意工作表面清洁,工作时油液应很好过滤。
4、叶片在叶槽中的间隙太大会使漏泄增加,太小则叶片不能自由伸缩,会导致工作失常。
5、叶片泵的轴向间隙对ηv影响很大。
a)小型泵-0.015~0.03mm
b)中型泵-0.02~0.045mm
6、油液的温度和粘度一般不宜超过55℃,粘度要求在17~37mm2/s之间。
粘度太大则吸油困难;粘度太小则漏泄严重。
来源:滚动(右击停止滚动)
叶片泵的优点是结构紧凑,体积小(单位体积的排量较大)运转平稳,输出流量均匀,噪声小,寿命长,即可做成定向齿轮泵,也可制成变量齿轮泵,定量泵(双作用或多作用)轴向受力平衡,使用寿命较长,变量泵变量方式可以有多种,且结构简单(如压力补偿变量泵)
叶片泵的缺点是吸油能力稍差,对油液污染较敏感,叶片受离心力外伸,所以转速不能太低,叶片在转子槽内滑动时受接触应力和摩擦力的影响很限制,其压力和转速难以提高,要提高叶片齿轮泵的使用压力,须采用各种措施,必然增加其结构的复杂程度,另外定量泵的定子曲线面,叶片和转子的加工略有难度,一浅谈定量叶片泵的优点和缺点:
1、由于流体流动的阻力和泄露较大,所以效率较低。
如果定量叶片泵处理不当,泄露不仅污染场地,而且还可能引起火灾和爆炸事故。
2、由于工作性能易受到温度变化的影响,因此不宜在很高或很低的温度条件下工作。
3、定量叶片泵元件的制造精度要求较高,因而价格较贵。
4、由于液体介质的泄露及可压缩性影响,不能得到严格的传动比。
5、液压传动出故障时不易找出原因;使用和维修要求有较高的技术水平。
般要求专用设备,且加工精度稍高。
\
\
叶片泵:结构紧凑,外形尺寸小,运转平稳,流量均匀,脉动及噪声较小,寿命较长,效率一般高于齿轮泵,价格低于柱塞泵。
中小流量的叶片泵常用在节流调节系统中,大流量的叶片泵,为避免功率损失过大,一般只用在非调节液压系统中。
叶片泵多用在机床、油压机、车辆、工程机械和塑料注射机的液压系统中。
齿轮泵:结构简单,价格较低,工作可靠,维护方便,对冲击负载适应性好,旋转部分惯性小。
轴承负载较大,磨损较快,同叶片泵、柱塞泵比较,效率最低。
多用在机床、工程机械、矿山机械、农业机械上。
柱塞泵:结构紧凑,寿命长,噪音低,压力高,流量大,单位质量功率较大,易于实现流量的调节和流向的改变,但结构复杂,价格较高。
柱塞泵特别是轴向柱塞泵,被广泛的应用在要求压力高,流量大并需要调节的大功率液压系统中。
螺杆泵实质上是一种齿轮泵,其特点是结构简单,重量轻,流量及压力的脉动小,输送均匀,无絮流,无搅动,很少产生气泡;工作可靠,噪声小,运转平稳性比齿轮泵和叶片泵高,容积效率高,吸入扬程高。
但加工较难,不能改变流量。
适用于机床或精密机械的液压传动系统。
一般应用两螺旋杆或三螺旋杆泵,有立式及卧式两种安装方式。