统计过程控制分析与研究SPC培训讲义
SPC培训讲义---基础知识

SPC培训讲义—基础知识简介SPC(Statistical Process Control,统计过程控制)是一种基于统计方法的质量管理工具,旨在通过对过程数据的统计分析,帮助组织识别和解决可能导致质量问题的根本原因,从而提高产品的稳定性和可靠性。
本讲义将介绍SPC的基础知识,包括SPC的原理、常用的SPC 工具和应用案例等内容。
1. SPC的原理SPC的核心原理是基于过程数据的统计分析,通过对数据的收集和分析,识别和排除可能导致质量问题的特殊原因,同时通过控制图的使用,监控和改进过程的稳定性和可靠性。
1.1 正态分布在SPC中,数据的正态分布是一个重要的假设。
正态分布是一种对称的概率分布,其特点是均值和标准差能够完全描述分布的情况。
正态分布的图形呈钟形曲线,均值位于曲线的中央。
在实际应用中,SPC 通常假设数据是近似正态分布的,以方便进行统计分析。
1.2 变异性与稳定性在质量管理中,变异性是指同一过程在不同时间或不同条件下相同测量项的数值差异。
通过SPC的应用,可以发现原本被认为是随机变动的过程,实际上可能存在特殊原因造成的异常波动。
稳定性是指过程在一段时间内的变异性较小,并且符合预期的性能要求。
通过SPC 的控制图,可以监控过程的稳定性,并及时采取措施防止不稳定状态的出现。
2. 常用的SPC工具SPC工具是SPC实施过程中使用的具体方法和技术,下面介绍几种常用的SPC工具。
2.1 控制图控制图是SPC中最常用的一种工具,它用来监控过程在一段时间内的变异情况。
控制图是一种统计图表,将过程数据按时间顺序绘制在图表上,同时画出上下限和中心线。
如果过程数据处于控制限之内,说明过程处于稳定状态;如果过程数据超过控制限,说明过程发生了特殊原因的变异,需要进行分析和改进。
2.2 直方图直方图是一种用柱形表示数据分布的图表,它可以直观地展示数据的中心趋势、波动幅度以及偏态情况。
通过直方图,可以判断数据是否符合正态分布,如果数据呈现钟形分布,则可以认为数据符合正态分布的假设。
SPC培训资料

a.样本平均数 表示数据集中位置,常用符号 表示,其计算公司为:式中: ——样本的算术平均值 N ——样本数例如,有统计数据x1,x2,x3.x4,x5为2,3,4,5,6五个数据,则其平均数据为: 2+3+4+5+6 X = ————— =4 5
2、控制图的发展
控制图(SPC)的起源和发展
定义---控制图是对过程品质特性值进行测量、记录、评估,从而监视过程是否处于控制状态的一种用统计方法所设计出來的图表。 图上有中心线、上控制限和下控制限,并有按时间顺序抽取的样本统计,所得数值的描绘点。
三、控制图常用术语
设计规格与控制界限设计规格:规格上限(USL),目标值(SL),规格下限(LSL)之间的关系。双边规格,不对称规格,单边规格(上,下)定义。控制界限:控制上限(UCL),控制中心(CL),控制下限(LCL)之间的关系。控制界限是基于制程的数据而不是制造的规格。如果过程受控的话,计算的控制界限要比设计规格严。如果过程受控,但产品仍然不合格,则说明现有的生产工艺生产不出符合条件的产品。
波动源
基本原理:预防为主是SPC的重要原则工序诊断是排除异动的主要手段必须有效利用系统分析方法归纳起来20个字: 查找异因(特殊原因),采取措施, 加以消除,纳入标准,不再发生。
2024版SPC培训教材全课件
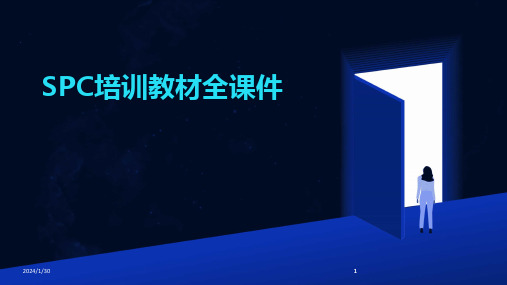
假设检验的基本概念
明确假设检验的定义、原假设与备择假设的设立原则及两类错误 的含义。
参数假设检验
掌握正态总体均值、方差的假设检验方法及步骤,理解t检验和F 检验的原理及应用场景。
非参数假设检验
了解非参数假设检验的适用条件及常用方法,如秩和检验、符号 检验等。
16
方差分析、回归分析应用举例
方差分析
掌握方差分析的基本原理、计算步骤及结果解释,理解其在多因素实验设计中的应用。
化。
大数据在SPC中的应用
大数据技术的不断发展将为SPC提供更丰富的数据来源和分析手段,有助于提高SPC的 应用效果。
2024/1/30
SPC在服务业的拓展
随着服务业的不断发展,SPC的应用领域将逐渐拓展到服务业领域,为服务业的质量管 理提供新的思路和方法。
36
下一讲预告及预备知识
2024/1/30
01
02
03
04
明确数据收集目标
根据业务需求,明确所需数据 的类型、范围和质量要求。
2024/1/30
制定数据收集计划
设计合理的数据收集流程,包 括数据源选择、采集频率、存
储方式等。
执行数据收集
运用合适的数据收集工具和技 术,按照计划进行数据采集。
数据质量监控
建立数据质量评估机制,确保 数据的准确性、完整性和一致
下一讲内容
下一讲将介绍SPC在企业中的实际应 用案例,包括不同行业和不同场景下 的SPC应用实践。
预备知识
为了更好地理解下一讲内容,建议学 员提前了解相关行业的生产流程和质 量管理要求,以及SPC在实际应用中 的挑战和解决方案。
37
THANKS
感谢观看
2024/1/30
《SPC培训教案》课件

《SPC培训教案》PPT课件第一章:SPC概述1.1 SPC的定义统计过程控制(Statistical Process Control,SPC)通过统计学方法监控和改进过程质量1.2 SPC的历史与发展起源于20世纪20年代的工业工程1950年代,W. Edwards Deming将SPC推广到日本,对日本质量管理产生深远影响1990年代至今,SPC与现代质量管理方法结合,如六西格玛1.3 SPC的应用范围制造业服务业医疗卫生教育及其他行业第二章:SPC基本概念2.1 过程输入、输出和转换连续和离散过程2.2 控制图控制图的类型(X-R图、X-bar图、p图、np图等)控制图的构成(中心线、控制限、数据点)2.3 过程稳定性随机变异与系统变异判断过程稳定的准则(规则1-4)第三章:控制图的应用3.1 控制图的制定数据收集与整理选择适当的控制图确定控制限3.2 控制图的解读数据点的含义判断过程是否失控的准则控制图的报警信号(点出界、链或趋势)3.3 控制图的分析与改进分析过程变异的原因采取措施改进过程重新制定控制图第四章:过程能力分析4.1 过程能力的概念过程固有的变异能力满足顾客要求的能力4.2 过程能力分析的方法计算过程能力指数(Cp、Cpk)判断过程能力是否满足要求4.3 过程改进策略提高过程能力的方法(减少变异、优化过程参数)过程改进的目标(提高产品质量、降低成本)第五章:SPC软件与应用5.1 SPC软件的功能与选择数据采集、处理和分析控制图绘制与监控过程改进工具(如鱼骨图、帕累托图等)5.2 SPC软件的操作步骤数据输入与设置控制图绘制与分析报告与输出5.3 SPC软件在实际应用中的案例分享制造业案例服务业案例其他行业案例第六章:SPC在制造业中的应用案例6.1 案例一:汽车制造业中的SPC应用描述汽车制造过程中如何运用SPC监控装配质量,减少缺陷率。
分析控制图在检测生产线上的作用,及时发现问题并采取措施。
统计过程控制培训讲义

存在过大的普通原因及特殊原因的变差。 需要进行100%检测以保障客户利益。 必须采取紧急措施使过程稳定,并减小变差。
40
过程控制和过程能力
判断一个过程是否满足规格要求: 能力指数-Cpk 性能指数-Ppk
判断一个过程是否受控: 控制图
41
控制图
42
控制图
什么是控制图? 控制图是对过程质量加以测定、记录从而
25
过程变差
生产/装配
设备及工装夹具的差异 随时间而产生的摩损,漂移等 操作工之间的差异(如手工操作的过程) 设置的差异 环境的差异
26
测量系统的变差
量具精确度(偏差)
量具精确度是指测量观察平均值与真实值(基准值) 的差异。 真实值由更精确的测量设备所确定
27
测量系统变差
量具重复性 量具重复性是由一个操作者采用一种测量
仪器,多次测量同一零件的同一特性时获得的 测量值变差。
28
测量系统变差
量具再现性 量具再现性是由不同的操作者,采用相同
的测量仪器,测量同一零件的同一特性时测量 平均值的变差。
29
测量系统变差
量具稳定性 量具稳定性是同一测量系统在不同时间测
量同一零件时,至少两组测量值的总变差。
30
测量系统变差
9.99 10.04 9.22 9.76 10.06 10.12 9.99 9.77 9.53 9.97
9.85 9.98 10.01 10.15 10.42 10.14 9.89 9.58 9.95 9.91
9.94 9.81 9.85 10.11 10.24 10.17 9.83 10.33 10.39 9.64
取局部措施或对系统采取措施的指南。
统计过程控制SPC培训讲义PPT课件

——当数据以百分率表示时,要判断它是计量数据还是计数数据, 应取决于给出数据的计算公式的分子。
12
第二讲:控制图
13
统计过程控制的实施过程
经由制程中去收集资料,而加以统计分 析,并从分析中发觉制程的变异,并经 由问题分析以找出异常原因,立即采取 改善措施,使制程恢复正常。再借由制 程能力分析与标准化,以不断提高制程 能力。
P(x)
0
1
2
3
4
5
6
μ μ+σ
9
关于正态分布
固定标准差σ时,不同的均值,如μ1 <μ2,对应的正态曲线的形状完 全相同,仅位置不同。
N(μ1,σ2)
N(μ2,σ2)
固定均值μ时,不同的标准差,如σ1< σ2,对应的正态曲线的位置相同, 但形状(高低与胖瘦)不同。
N(μ1,σ2)
N(μ2,σ2)
0
不合格品率 (PPM) 317300
45500 2700 63 0.57 0.002
11
二、计数数据
——凡是不能连续取值的,或者说即使使用测量工具也得不到小数 点以下数值,而只能得到0或1,2,3•••等自然数的这类数据。
——计数数据还可细分为记件数据和记点数据。记件数据是指按件 计数的数据,如不合格品数、彩色电视机台数、质量检测项目数等;记点 数据是指按缺项点(项)计数的数据,如疵点数、砂眼数、气泡数、单位 (产品)缺陷数等。
很多质量特性X随机取值的统计规律性。 • 如:一个班级中学生的身高、体重、成绩;加工一批轴的外
径尺寸等。 • 正态分布的图形是对称的钟形曲线,称为正态曲线。 • 正态分布含有两个参数μ和σ,其中μ为正态分布的均值,它
SPC统计过程控制培训讲义(ppt 132页)
持续改进及统计过程概述
四.现有已完成的例子仅是为说明如何运用SPC ,要真正理解SPC需要进一步与过程实际联系, 现有的过程信息不能代替实际工作经验。
·控制限或描点已计算错或描错; ·过程或取样方法被分层;每个子组系统化包括了从两 个或多个具有完全不同的过程均值的过程流(例如,用 几根测量轴每一轴测一个数); ·数据已经过编辑(极差与均值相差甚远的几个子组被 更改或删除)。
分组情况
显著少于2/3以下的描点落在离R很近的区域(对于 25个子组,如有40%或少于40%的点落在中间1/3的 区域)
产品
机器
过程
设备
人
Cmk机器能力
工装
料 环
测量系统
MSA
法
Cpk过程能力
❖影响测量结果的因素
❖测量系统分析 MSA
测量系统误差的类型
偏倚 (Bias)
❖测量系统分析 MSA
测量系统误差的类型
稳定性 (Stability)
❖测量系统分析 MSA
测量系统误差的类型
线性 (Linearity)
A.5 将均值和极差值画到控制图上
B. 计算控制项
B.3 在控制图上作出平均值和极差值控制限的控制线 在初始研究阶段,UCL、LCL被称为试验控制限。
a.超出控制限的点
超出上控制限 ·控制限计算错误或描点时描错; ·零件间的变化性或分布的宽度已经增大(即变坏),这种增 大可以发生在某个时间点上,也可能是整个趋势的一部分; ·测量系统变化(例如,不同的检验员或量具); ·测量系统没有适当的分辨力。
SPC培训讲义(PPT47页).pptx
二、SPC的起源和发展
1924年由美国贝尔电话实验室W.A. Shewhart(休哈特)博士提出。 1932年,英国邀请W.A. Shewhart (休哈特)博士到伦敦,主讲统计质量控
制,英国成为了最早在工业方面使用控制图的国家。
1939年休哈特博士与戴明博士合写了《品质观点的统计方法》
1950~1952年,日本两次邀请美国统计学家戴明( W.E. Deming )传授 SPC 。
波动的概念是指在现实生活中没有两件东西是
完全一样的。生产实践证明,无论用多么精密的
设备和工具,多么高超的操作技术,甚至由同一
2、波动的概念:
操作工,在同一设备上,用相同的工具,生产相 同材料的同种产品,其加工后的产品质量特性(
如:重量、尺寸等)总是有差异,这种差异称为
波动。公差制度实际上就是对这个事实的客观承
三、SPC统计若干概念
▪ 数据的种类:计量型、计数型 ▪ 波动(变差)——波动的概念、原理及波动的种类 ▪ 普通原因/异常原因 ▪ 基础的统计量——平均值X—、中位数X~、极差R、标
准偏差、S
1、数据的种类
计量型 特点:可以连续取值也称连续型数据。 如:零件的尺寸、强度、重量、时间、温度等
计数型 特点:不可以连续取值,也称离散型数据。 如:废品的件数、缺陷数等
统计过程控制分析与研究
Statistical Process Control
课程内容及目录
▪ 什么是SPC ▪ SPC的起源和发展 ▪ SPC统计概念 ▪ SPC使用的统计技术 ▪ SPC控制图的种类及选择 ▪ SPC控制图的设计原理 ▪ 计量型控制图的制作步骤 和判定原则 ▪ SPC控制图的异常的判断和处理 ▪ SPC与过程能力分析 ▪ 使用SPC益处
SPC统计培训讲义
SPC统计培训讲义什么是SPC统计SPC(Statistical Process Control),即统计过程控制,是一种通过对过程进行统计分析和控制,以提高产品质量和生产效率的管理方法。
SPC统计是建立在统计学原理基础上的一种管理工具,通过收集和分析数据,用于监控和控制生产过程中的变化和不良情况。
SPC统计的目标是实现过程稳定性,减少不良品数量和降低产品缺陷率。
通过SPC统计,企业可以及时发现和解决生产过程中的问题,降低生产成本,提高产品质量,增强市场竞争力。
SPC统计的基本原理SPC统计是基于统计学原理的管理方法,通过收集和分析过程数据,判断过程的稳定性和可控性。
SPC统计的基本原理包括以下几个方面:1.过程稳定性:SPC统计通过对过程数据进行统计分析,判断过程是否稳定。
过程稳定意味着过程的变异是正常的,不受特殊因素的影响,且在可接受的范围内变化。
2.过程控制:SPC统计通过建立控制图,对过程进行连续的监控和控制。
控制图是一种图表,通过在图上绘制过程数据和控制界限,可以直观地反映过程的稳定性和变化情况。
3.统计分析:SPC统计通过对过程数据进行统计分析,可以了解过程的平均水平、变异程度和分布情况。
常用的统计分析方法包括均值控制图、极差控制图和正态性检验等。
4.过程改进:SPC统计通过及时发现和解决过程问题,实现过程的持续改进。
通过统计分析和控制图,可以找出过程中的异常点和特殊因素,分析原因,并采取相应的改进措施。
SPC统计的重要工具SPC统计是建立在统计学原理上的一种管理方法,其中涉及到很多重要的工具和技术。
下面介绍几个常用的SPC统计工具:控制图控制图是SPC统计最常用的工具之一,用来监控和控制过程的变化和稳定性。
常见的控制图有均值控制图、极差控制图和标准差控制图。
通过绘制实际数据和控制界限,可以直观地了解过程的变化情况。
直方图直方图是一种用来表示数据分布情况的图表,通过将数据分成若干个区间,然后统计每个区间的频数或频率,可以了解数据的分布情况。
SPC(Statistical Process Control) 统计过程控制培训课件
Statistical Process Control
二.SPC的作用(续)发展企业文化,提高职工素质严谨的工作态度认真负责的精神形成一个有效的分析、解决问题的网络用共同的语言讨论质量问题自我参与和完善的意识
特殊原因
四. 持续改进及统计过程控制概述2.变差的普通原因和特殊原因(续)(通常也叫可查明原因)是指造成不是始终作用于过
每件产品的尺寸与别的都不同
范围但它们形成一个模型,
范围 范围 范围若稳定, 可以描述为一个分布
范围
范围
范围分布可以通过以下因素来加以区分
位置 分布宽度
形状
或这些因素的组合
目标值线
不精密
精密
准确
不准确
• •
••
••••
•
•
•• •
••••
•••
•••
Statistical Process Control
使用控制图的准备1、建立适合于实施的环境a 排除阻碍人员公正的因素b 提供相应的资源c 管理者支持2、定义过程根据加工过程和上下使用者之间的关系,分析每个阶段的影响因素。
Statistical Process Control
三.SPC常用术语解释(续)
名 称
解 释
总 体
又称母体,是指所要研究对象的全体;
样 本
从总体中随机抽取出来的,对它进行测量、分析的一部分个体;
样 品
又称个体,样本中的每一个研究对象;
样本大小
- 1、下载文档前请自行甄别文档内容的完整性,平台不提供额外的编辑、内容补充、找答案等附加服务。
- 2、"仅部分预览"的文档,不可在线预览部分如存在完整性等问题,可反馈申请退款(可完整预览的文档不适用该条件!)。
- 3、如文档侵犯您的权益,请联系客服反馈,我们会尽快为您处理(人工客服工作时间:9:00-18:30)。
特殊原因:
当过程中存在系统因素的影响,不是始终作用于过程的 变差的原因,即当它们出现时将造成(整个)过程的分布改变, 即过程处于统计失控状态(简称失控状态)。
除非所有的特殊原因都被查找出来并且采取了措施,否 則它们将继续用不可预测的方式来影响过程的输出。
控制限的宽度就是根据这一原理定为3。99.Fra bibliotek3% 95.45%
68.26%
0.27%
-3σ -2σ -1σ μ +1σ +2σ +3σ
控制图的形成
1、在产品的生产过程中,计量值的分布形式有: 位置:中心值 形状:峰态
分布宽度
将正态分布曲线顺时针旋转90°后,在由下向上翻转180 °,即得到控制图
C 缺陷数量
Number of defects
U 单位缺陷数量
Number of defects per “unit”
六、控制图的设计原理
工序处于稳定状态下,其计量值的分布大致符合正态分布。由正态分 布的性质可知:质量数据出现在平均值的正负三个标准偏差(X3) 之外的概率仅为0.27%。这是一个很小的概率,根据概率论 “视小概 率事件为实际上不可能” 的原理,可以认为:出现在X3区间外的 事件是异常波动,它的发生是由于异常原因使其总体的分布偏离了正 常位置。
二、SPC的起源和发展
1924年由美国贝尔电话实验室W.A. Shewhart(休哈特)博士提出。 1932年,英国邀请W.A. Shewhart (休哈特)博士到伦敦,主讲统计质量控
制,英国成为了最早在工业方面使用控制图的国家。
1939年休哈特博士与戴明博士合写了《品质观点的统计方法》
1950~1952年,日本两次邀请美国统计学家戴明( W.E. Deming )传授 SPC 。
通过1950~1980这30年对于SPC理论和实践的不断发展,日本一跃而居世界 质量与劳动生产率的领导地位,引起西方及美国的震惊。尤其在汽车零部件 方面:美国不合格率:1%~4%,日本不合格率:0.001%。
四、SPC使用的统计技术
Count Percent
Pareto Chart of Z006605
300
100
250 80
200 60
150
40 100
50
20
0
0
外废失效模式
法兰夹渣 止口加工余量不足 缸孔夹渣 法兰缺肉(小于5mm) 窗口面夹渣
后孔夹渣
Count
112
67
58
32
16
11
Percent
单位大小 是否一定
一定
X-s
图
X-R 图
~
X-R 图
I-MR 图
“p”
图
“np”“c”
图图
“u”
图
不同偏差的控制图
Different Variables Control Charts
I-MR
单值-移动极差图
Individuals - Moving Range
X-Bar-R
均值-极差图
Average –Range Chart
SPC在日本工业界的大量推广应用对日本产品质量的崛起起到了至关重要的 作用。
八十年代以后,世界许多大公司纷纷在自己内部积极推广应用SPC ,而且对 供应商也提出了相应要求。在标准ISO9000以及QS9000中也提出了在生产控 制中应用SPC方法的要求。
三、SPC统计若干概念
数据的种类:计量型、计数型 波动(变差)——波动的概念、原理及波动的种类 普通原因/异常原因 基础的统计量——平均值X—、中位数X~、极差R、标
37.8
22.6
19.6
10.8
5.4
3.7
Cum %
37.8
60.5
80.1
90.9
96.3
100.0
五、控制图的种类
1、按数据性质分类:
控制图的选定
计量值 资料性质
计数值
平均值
n≥2 样本大小 n≤2
CL的性质
n是否较大
中位数
“n”=2~5
不良数
缺陷数
不良数或
缺陷数 n=1
不一定
一定
n是否一定
统计过程控制分析与研究
Statistical Process Control
课程内容及目录
什么是SPC SPC的起源和发展 SPC统计概念 SPC使用的统计技术 SPC控制图的种类及选择 SPC控制图的设计原理 计量型控制图的制作步骤 和判定原则 SPC控制图的异常的判断和处理 SPC与过程能力分析 使用SPC益处
准偏差、S
1、数据的种类
计量型 特点:可以连续取值也称连续型数据。 如:零件的尺寸、强度、重量、时间、温度等
计数型 特点:不可以连续取值,也称离散型数据。 如:废品的件数、缺陷数等
波动的概念是指在现实生活中没有两件东西是
完全一样的。生产实践证明,无论用多么精密的
设备和工具,多么高超的操作技术,甚至由同一
不同属性的控制图:缺陷
Different Attribute Control Charts: Defectives
NP 不合格品数量
Number ofnon-conforming units
P 不合格率
Proportion of non-conforming units
不同属性的控制图:缺陷
Different Attribute Control Charts : Defects
2、波动的概念:
操作工,在同一设备上,用相同的工具,生产相 同材料的同种产品,其加工后的产品质量特性(
如:重量、尺寸等)总是有差异,这种差异称为
波动。公差制度实际上就是对这个事实的客观承
认。消除波动不是SPC的目的,但通过SPC可以
对波动进行预测和控制。
三、普通原因、特殊原因
普通原因:
过程仅受随机因素影响,随着时间推移具有稳定的且可 重复的分布过程中的许多变差的原因,我们称之为:“处于 统计控制状态”、“受统计控制”,或有时称“受控”。
99.73% 95.45%
一、什么是SPC
SPC:
“Statistical Process Control”之缩写,意为 “统计过程控制”
统计过程控制:
主要是指应用统计分析技术对生产过程进行实时监控, 科学的区分出生产过程中产品质量的随机波动与异常波动, 从而对生产过程的异常趋势提出预警,以便生产管理人员及 时采取措施,消除异常,恢复过程的稳定,从而达到提高和 控制质量的目的。