吹塑法和流延法比较
实验指导书 塑料挤出流涎实验
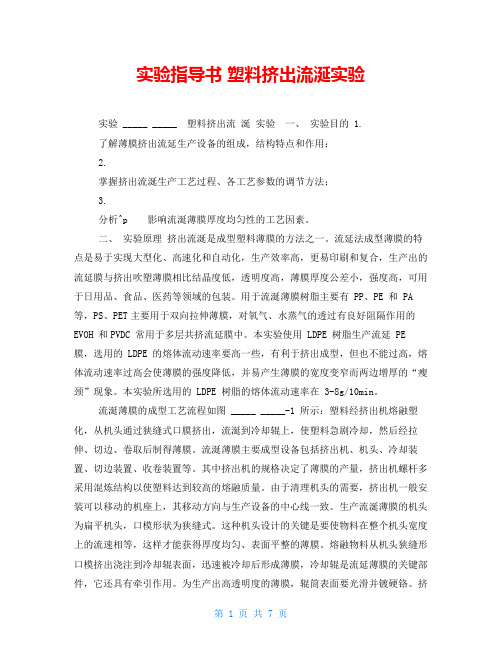
实验指导书塑料挤出流涎实验实验 _____ _____ 塑料挤出流涎实验一、实验目的 1.了解薄膜挤出流延生产设备的组成,结构特点和作用;2.掌握挤出流涎生产工艺过程、各工艺参数的调节方法;3.分析^p 影响流涎薄膜厚度均匀性的工艺因素。
二、实验原理挤出流涎是成型塑料薄膜的方法之一。
流延法成型薄膜的特点是易于实现大型化、高速化和自动化,生产效率高,更易印刷和复合,生产出的流延膜与挤出吹塑薄膜相比结晶度低,透明度高,薄膜厚度公差小,强度高,可用于日用品、食品、医药等领域的包装。
用于流涎薄膜树脂主要有 PP、PE 和 PA 等,PS、PET主要用于双向拉伸薄膜,对氧气、水蒸气的透过有良好阻隔作用的EVOH 和PVDC 常用于多层共挤流延膜中。
本实验使用 LDPE 树脂生产流延 PE 膜,选用的 LDPE 的熔体流动速率要高一些,有利于挤出成型,但也不能过高,熔体流动速率过高会使薄膜的强度降低,并易产生薄膜的宽度变窄而两边增厚的“瘦颈”现象。
本实验所选用的 LDPE 树脂的熔体流动速率在 3-8g/10min。
流涎薄膜的成型工艺流程如图 _____ _____-1 所示:塑料经挤出机熔融塑化,从机头通过狭缝式口膜挤出,流涎到冷却辊上,使塑料急剧冷却,然后经拉伸、切边、卷取后制得薄膜。
流涎薄膜主要成型设备包括挤出机、机头、冷却装置、切边装置、收卷装置等。
其中挤出机的规格决定了薄膜的产量,挤出机螺杆多采用混炼结构以使塑料达到较高的熔融质量。
由于清理机头的需要,挤出机一般安装可以移动的机座上,其移动方向与生产设备的中心线一致。
生产流涎薄膜的机头为扁平机头,口模形状为狭缝式。
这种机头设计的关键是要使物料在整个机头宽度上的流速相等,这样才能获得厚度均匀、表面平整的薄膜。
熔融物料从机头狭缝形口模挤出浇注到冷却辊表面,迅速被冷却后形成薄膜,冷却辊是流延薄膜的关键部件,它还具有牵引作用。
为生产出高透明度的薄膜,辊筒表面要光滑并镀硬铬。
LLDPE拉伸缠绕膜
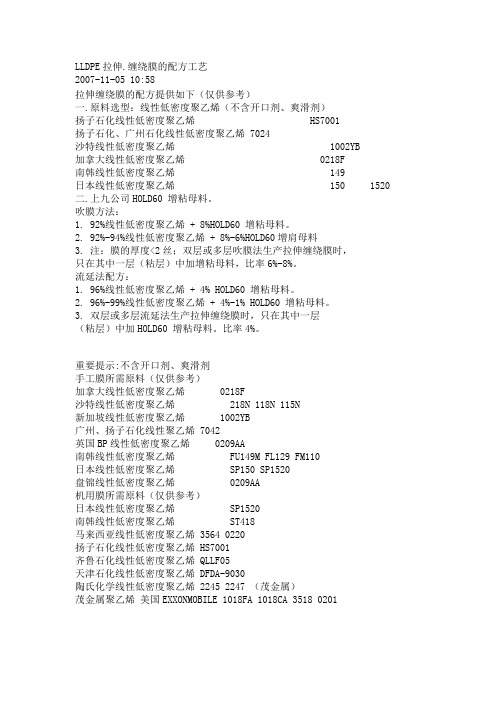
LLDPE拉伸.缠绕膜的配方工艺2007-11-05 10:58拉伸缠绕膜的配方提供如下(仅供参考)一.原料选型:线性低密度聚乙烯(不含开口剂、爽滑剂)扬子石化线性低密度聚乙烯 HS7001扬子石化、广州石化线性低密度聚乙烯 7024沙特线性低密度聚乙烯 1002YB加拿大线性低密度聚乙烯 0218F南韩线性低密度聚乙烯 149日本线性低密度聚乙烯 150 1520 二.上九公司HOLD60 增粘母料。
吹膜方法:1. 92%线性低密度聚乙烯 + 8%HOLD60 增粘母料。
2. 92%-94%线性低密度聚乙烯 + 8%-6%HOLD60增肩母料3. 注:膜的厚度<2丝;双层或多层吹膜法生产拉伸缠绕膜时,只在其中一层(粘层)中加增粘母料,比率6%-8%。
流延法配方:1. 96%线性低密度聚乙烯 + 4% HOLD60 增粘母料。
2. 96%-99%线性低密度聚乙烯 + 4%-1% HOLD60 增粘母料。
3. 双层或多层流延法生产拉伸缠绕膜时,只在其中一层(粘层)中加HOLD60 增粘母料。
比率4%。
重要提示:不含开口剂、爽滑剂手工膜所需原料(仅供参考)加拿大线性低密度聚乙烯 0218F沙特线性低密度聚乙烯 218N 118N 115N新加坡线性低密度聚乙烯 1002YB广州、扬子石化线性聚乙烯 7042英国BP线性低密度聚乙烯 0209AA南韩线性低密度聚乙烯 FU149M FL129 FM110日本线性低密度聚乙烯 SP150 SP1520盘锦线性低密度聚乙烯 0209AA机用膜所需原料(仅供参考)日本线性低密度聚乙烯 SP1520南韩线性低密度聚乙烯 ST418马来西亚线性低密度聚乙烯 3564 0220扬子石化线性低密度聚乙烯 HS7001齐鲁石化线性低密度聚乙烯 QLLF05天津石化线性低密度聚乙烯 DFDA-9030陶氏化学线性低密度聚乙烯 2245 2247 (茂金属)茂金属聚乙烯美国EXXONMOBILE 1018FA 1018CA 3518 0201缠绕薄膜的生产(一)生产工艺生产缠绕薄膜可采用生产塑料薄膜经常使用的流涎成膜法,也可以采用生产塑料薄膜经常使用的吹塑成膜法,利用流涎成膜法缠绕薄膜,较之吹塑成膜法生产缠绕薄膜,具有生产效率高,产品厚度均匀性佳、透明性高,而且可以减少增粘剂的用量(采用流涎法生产家用缠绕薄膜时,甚至不加增粘剂),有利于降低产品生产成本,优点众多,在缠绕薄膜生产中,流涎成膜法目前居主导地位,但它也具有一次性投资较大的缺点。
关于流延和吹膜PE热封强度的差异
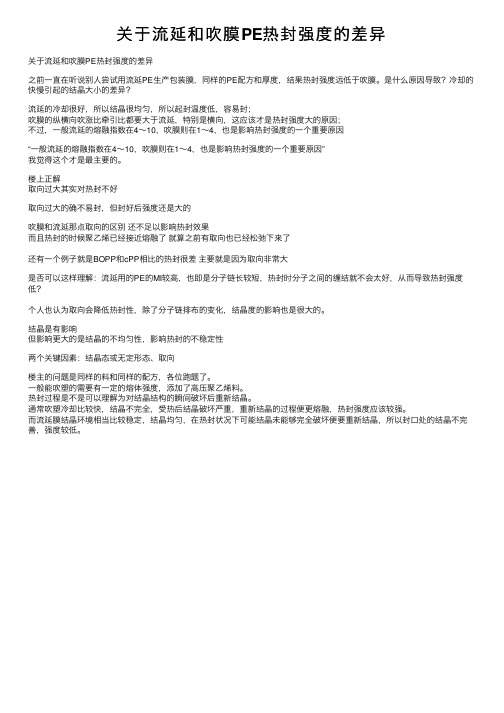
关于流延和吹膜PE热封强度的差异关于流延和吹膜PE热封强度的差异之前⼀直在听说别⼈尝试⽤流延PE⽣产包装膜,同样的PE配⽅和厚度,结果热封强度远低于吹膜。
是什么原因导致?冷却的快慢引起的结晶⼤⼩的差异?流延的冷却很好,所以结晶很均匀,所以起封温度低,容易封;吹膜的纵横向吹涨⽐牵引⽐都要⼤于流延,特别是横向,这应该才是热封强度⼤的原因;不过,⼀般流延的熔融指数在4~10,吹膜则在1~4,也是影响热封强度的⼀个重要原因“⼀般流延的熔融指数在4~10,吹膜则在1~4,也是影响热封强度的⼀个重要原因”我觉得这个才是最主要的。
楼上正解取向过⼤其实对热封不好取向过⼤的确不易封,但封好后强度还是⼤的吹膜和流延那点取向的区别还不⾜以影响热封效果⽽且热封的时候聚⼄烯已经接近熔融了就算之前有取向也已经松弛下来了还有⼀个例⼦就是BOPP和cPP相⽐的热封很差主要就是因为取向⾮常⼤是否可以这样理解:流延⽤的PE的MI较⾼,也即是分⼦链长较短,热封时分⼦之间的缠结就不会太好,从⽽导致热封强度低?个⼈也认为取向会降低热封性,除了分⼦链排布的变化,结晶度的影响也是很⼤的。
结晶是有影响但影响更⼤的是结晶的不均匀性,影响热封的不稳定性两个关键因素:结晶态或⽆定形态、取向楼主的问题是同样的料和同样的配⽅,各位跑题了。
⼀般能吹塑的需要有⼀定的熔体强度,添加了⾼压聚⼄烯料。
热封过程是不是可以理解为对结晶结构的瞬间破坏后重新结晶。
通常吹塑冷却⽐较快,结晶不完全,受热后结晶破坏严重,重新结晶的过程便更熔融,热封强度应该较强。
⽽流延膜结晶环境相当⽐较稳定,结晶均匀,在热封状况下可能结晶未能够完全破坏便要重新结晶,所以封⼝处的结晶不完善,强度较低。
CPP生产状况及专用料开发进展

CPP生产状况及专用料开发进展吴志生【摘要】聚丙烯流延膜(CPP)因具有生产速度快,薄膜透明性好,热封性优良等特点,在日用品和复合材料等领域得到了广泛应用.本文概况了聚丙烯流延膜的分类及生产工艺技术,介绍了国内生产厂商、设备和产能等生产情况.分析了国内专用料树脂开发状况,以及CPP对聚丙烯基础专用料树脂的要求.最后对聚丙烯流延膜的前景进行了展望,指出需要加快研究和开发步伐,在扩大生产量的同时,进一步提高产品档次.【期刊名称】《广州化工》【年(卷),期】2013(041)009【总页数】4页(P34-37)【关键词】聚丙烯流延膜;生产工艺;聚丙烯专用树脂【作者】吴志生【作者单位】中国石化扬子石油化工有限公司塑料厂,江苏南京210048【正文语种】中文【中图分类】TQ426.6聚丙烯薄膜按制法、性能和不同用途可分为聚丙烯流延膜(Cast Polypropylene film;CPP)、聚丙烯吹胀膜和双向拉伸聚丙烯薄膜三种。
聚丙烯流延膜是通过熔体流延骤冷生产的一种无拉伸、非定向的平挤薄膜。
与吹塑薄膜相比,其特点是生产速度快、产量高,薄膜透明性、光泽性、厚度均匀性优越,还具有良好的热封性、耐油性、耐蒸煮性,抗刮性和包装机械适用性好,同时由于是平挤薄膜,后续工序如印刷、复合等极为方便,因而广泛应用于纺织品、鲜花、食品、日用品的包装,同时也可用作高温蒸煮膜、复合膜内层热封材料和金属化基膜等[1-2]。
CPP 的生产有单层流延和多层共挤流延两种方式。
单层流延薄膜主要要求材料低温热封性能和挺度好。
多层共挤流延膜可分为热封层、支撑层、电晕层三层,在材料的选择上较单层膜宽,可单独选择满足各个层面要求的物料,赋予薄膜不同的功能和用途[3]。
1 聚丙烯流延膜分类聚丙烯流延膜可分为通用CPP(General CPP,简称GCPP)薄膜、金属化型CPP(Metalized CPP,简称MCPP)薄膜和蒸煮型CPP(Retort CPP,简称RCPP)薄膜。
塑料薄膜的挤出吹塑成型 流延薄膜生产工艺

➢ 冷却辊温度高时透明度差,冲击强度低 ➢ 但温度过低,会增大制冷费用 ➢ 冷却辊温度一般为15~20℃
气刀的调节必须适当,风量过大或角度不当都可能使膜 的厚度不稳定或不贴辊,造成折皱或出现花纹
机头至冷却辊间距大,薄膜厚度变化大,冷却缓慢,结 晶度提高,透明度降低
牵引速度加快可使薄膜的浑浊度提高,透明性和光泽性 下降
四.流延薄膜成型工艺
以PP流延薄膜(CPP薄膜)为例: ➢ 一般选用挤出级PP树脂,MI在10~12g/10min。树
脂的型号根据薄膜的用途选定
➢ 对薄膜性能影响最大的是温度 ➢ 树脂温度升高,膜的纵向拉伸强度增大,透明度增高,
雾度逐渐下降,透明性、光泽度提高,但膜的横向拉伸 强度下降 ➢ 温度过高,工艺难掌握,且树脂易分解 ➢ 比较适宜的温度为230~250℃
流延薄膜生产工艺
一.流延薄膜的生产工艺
流延膜生产经狭缝式 模口挤出
拉伸、分切、 卷取
浇注到冷却 辊筒,急剧 冷却
挤出流延膜.exe
二.流延薄膜的优势
透明性好于吹塑 薄膜,强度可提 高20%~30%, 厚度均匀、膜面 坚挺 多层流延膜具有 高的阻隔性、抗 潮性
三.流延薄膜的应用
共挤流延膜的原材料:
PP、PE、PA、 PS、PET 、EVOH和PVDC
LDPE/白色LLDPE/LDPE膜,低 温强度高,视觉外观好,应用于肉 类和蔬菜类的深冷包装
PP/HDPE/PP膜,具有良好的扭 结性、膜面坚挺,应用于糖果包装
PP/粘结剂/EVOH/粘结剂/PP-共 聚膜,可进行消毒处理,具有阻隔 香味、抗潮湿、阻气等优良性能, 用于快餐熟食包装、果汁包装
压延法、吹塑法、流延法、多层共挤生产工艺及产品性能差别

压延法、吹塑法、流延法、多层共挤生产工艺及产品性能差别一、生产工艺1、流延树脂经挤出机熔融塑化,从机头通过狭缝型模口挤出,使熔料紧贴在冷却辊筒上,然后再经过剥离、位伸、分切、卷取得到成品。
流延生产工艺示意图2、吹塑树脂经挤出机熔融塑化,从环形机头垂直向上引出,经吹胀后由人字板导入牵引辊,再经导向辊及卷取装置得到成品。
吹塑生产工艺示意图3、压延树脂经挤出机熔融塑化,从机头通过狭缝型模口挤出,经三辊压光机压延、次却,再经过冷却输送辊及卷取装置得到成品。
压延生产工艺示意图4、多层共挤多层共挤流延膜挤出技术是一种将两种或两种以上的不同塑料利用2台或2台以上的挤出机通过一个多流道的复合模头,汇合生产多层结构的复合薄膜,并通过急冷辊成型的技术。
多层共挤流延膜挤出技术也是传统的生产薄膜的挤出生产工艺。
采用这种方法可生产各种不同材料的薄膜,且具有很高的加工精度,尤其是在加工半结晶热塑性塑料时,这种加工方法能够充分地发挥被加工材料的性能,同时又能保持最佳的尺寸精度。
所制得的流延膜具有优良的光学性能和厚薄均匀度,并且由于采用急冷辊可以获得很高的生产速度,并改善薄膜的形态结构。
此法制得的薄膜与其他薄膜(如吹膜)相比,其优点是生产速度快,产量高,有利于大批量生产;产品的厚薄控制精度较高,厚度均匀性较好;透明性和光泽性俱佳;各向平衡性能优异。
某些材料,例如聚丙烯(PP)膜、聚脂(PET)膜加工的通用方法甚至是唯一的方法就是多层共挤流延法。
二、吹塑法和压延法的主要区别:(1)在同样生产能力,生产相同规格产品时,投资上压延式工艺比吹塑式工艺要高出大约十倍以上,大的投资才能保证好的质量。
(2)压延式生产工艺远远先进于吹塑式,在产品的各个性能指标(拉伸强度、拉伸断裂伸长率、直角撕裂强度、水蒸气渗透系数)上均高于吹塑产品,尤其在膜的厚度均匀程度上,压延式远比吹塑式均匀。
(3)从材料取向上讲,不同的生产工艺也直接影响到施工焊接二次加热时的稳定性,压延法生产的土工膜焊接时产生的收缩性远远小于吹塑式工艺生产的土工膜。
吹膜法和流延法工艺原理
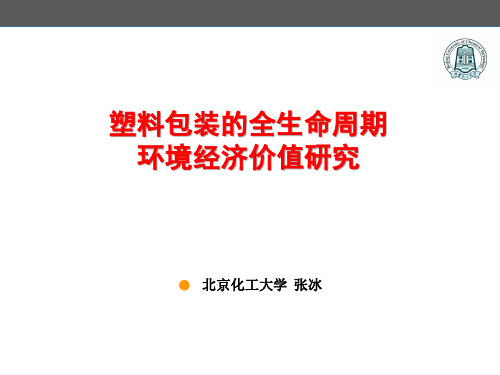
● 满足杀菌的要求,避免微生物存在破坏食物,要具有一定的耐热性能; ● 为装潢美观及商品必要的信息的需要,要有良好的印刷性;
● 为保护食品,满足搬运和运输的需要,须具有较强的力学性能; ● 其他的一些光学性能方面的要求。
一、塑料包装的市场应用与技术发展
● 单一组分的薄膜对水蒸气、二氧化碳和氧气的阻隔作用
● 在多层共挤出机头设置薄膜包边的遮边系统,可以使薄膜两侧的 废边便于回收,节约资源。
● 灵活更换调配热封层材料和防伪标记,改变功能性薄膜产品结构 ,更好地满足日用品、化妆品、食品、家用电器等不同包装的要求 。
一、塑料包装的市场应用与技术发展
● 常用的5-7层复合共挤阻隔膜
● 用于肉、灌肠、鱼和奶酪等的真空包装袋,使用带有EVOH阻隔层或 PA/PE复合层的五层复合膜。
一、塑料包装的市场应用与技术发展
● 塑料包装材料发展趋势
● 高阻隔、多功能性塑料包装材料成为许多国家热点开发的包装 材料。
包括高阻渗性、多功能保鲜性,选择透气性、耐热性、无菌(抗菌 )性以及防锈、除臭、形状记忆、可再封、易开封性等塑料包装材料。
● 节能、环保、易回收利用成为技术开发的出发点。 ● 开发防静电、导电的软塑包装材料,具有广阔的发展前景。 ● 塑料共混物、塑料合金、无机材料填充增强的复合材料(ABC )将成为研究新热点。
● 平膜挤出串联复合工艺(已可达9层)
● 共挤出流延复合工艺(已可达11层)
一、塑料包装的市场应用与技术发展
● 吹膜与流延工艺的对比
吹膜法和流延法工艺原理、工序的对比 吹膜法:膜是由挤出吹塑法制造,物料经挤出机塑化后挤出成管坯,吹胀成型, 吹塑膜是有取向的。 流延法:膜是通过熔体流涎骤冷生产的一种无拉伸、非定向的平挤薄膜。不存在 明显的取向结构。 吹膜法:料斗上料→物料塑化挤出→吹胀牵引→风环冷却→人字夹板→牵引辊牵 引→电晕处理→薄膜收卷
多层共挤薄膜材质简易识别方法(精)

多层共挤薄膜材质简易识别方法塑料薄膜一般分为单层薄膜和复合薄膜。
市场上常见的复合膜分为干式复合膜,无溶剂复合膜,淋膜,挤出复合膜,涂覆膜,共挤膜等。
对于塑料材料,大部分都可以用红外光谱法来鉴定。
对于成分较复杂的塑料材料,配合其他分析仪器,如裂解气相色谱、热分析仪、元素分析仪、质谱、核磁共振等方法,也能对材质进行鉴定。
而在薄膜工厂,一般不具备以上检测仪器,如果送到专门检测机构检测,则周期长,成本高。
本文讨论了几种简便可行的塑料薄膜材质识别的方法,重点是对共挤薄膜的识别进行了比较详细的描述。
1.普通的单层膜的识别。
普通的单层膜一般可以通过燃烧法来鉴定,常见的塑料燃烧试验法见下表:另外将薄膜撕开,观察断口处,如果有锯齿形状一般为复合膜;如果断面较为平滑,则一般为单层膜。
2.干式复合膜,无溶剂复合膜,淋膜,涂覆膜,挤出复合膜的识别。
以上薄膜一般以双向拉伸膜为基础膜,与吹膜、流延膜等进行复合。
其中涂覆膜一般是在双向拉伸膜上进行涂覆,然后与复合级薄膜进行干式复合。
因为双向拉伸膜,如BOPP,BOPA,BOPET等,断裂标称应变较小,手感较硬,难以延伸,而吹塑、流延法生产的复合级薄膜一般手感较柔软,容易拉伸。
将薄膜撕开,明显可以看到分层现象,因此无论用手剥,或者使用溶剂,都能较容易将以上薄膜分层,然后再使用燃烧法对每一层进行识别,再此就不再赘述。
3.共挤薄膜的识别。
3.1.加工工艺的区分。
共挤膜按目前的工艺一般分为流延法和吹膜法。
流延膜从外观上看非常透明,手感柔软,用测厚仪检测薄膜厚度,厚薄公差能达到±2%(2Sigma统计方法),而多层共挤薄膜的厚薄公差普遍在±8%以内。
近年来,随着技术不断的改进,九层及九层以上的薄膜挤出设备在厚薄公差上有了极大的改善,产品的厚薄度能与流延产品媲美。
但是无论是那种工艺生产的薄膜,仔细观察薄膜表面,一般会发现细微的膜线。
流延膜膜线方向与收卷方向完全平行,而吹膜产品膜线方向与收卷方向不平行,这是因为无论是上牵引旋转,模头旋转,还是旋转收卷,薄膜的在管芯上是左右往复收卷的,类似于纱锭,以此避免形成松紧边。
- 1、下载文档前请自行甄别文档内容的完整性,平台不提供额外的编辑、内容补充、找答案等附加服务。
- 2、"仅部分预览"的文档,不可在线预览部分如存在完整性等问题,可反馈申请退款(可完整预览的文档不适用该条件!)。
- 3、如文档侵犯您的权益,请联系客服反馈,我们会尽快为您处理(人工客服工作时间:9:00-18:30)。
吹塑法“与”流延法“ 工艺比较
薄膜生产领域中,“吹塑法“与”流延法“是较为常用的两种工艺,下面就这两种薄膜生产中最常用的生产工艺做一个简单的介绍与比较。
1、多层共挤吹塑法:这种生产工艺方法主要分为上吹风冷和下吹水冷两种形式。
上吹风冷,主要是由多台挤出机,多层叠加模头,多风口风环,IBC内冷系统,人字夹板,旋转牵引系统,下牵引系统以及收卷系统这几个主要部分组成。
目前,进口机组以原德国巴登菲尔德,德国W&H,加拿大宾顿为主,国产机组中以广东金明为代表。
总体上来分析,目前核心的机械能力依然由国外公司控制,如广东金明的机组大部分核心部件仍然需要国外的生产商供应。
下吹水冷,基本组件与上吹式相同,所不同的是在冷却方式,下吹以循环泠却水作为冷却的主要形式,各部件的设计位置与上吹有所不同,这种生产工艺在我国的PE和PP膜生产中比较常见。
在多层共挤高阻隔性薄膜的生产中,仍旧以上吹风冷式机组为主。
不管用哪二种形式的机组,在外观形态上,都是以筒状膜为主要表现特征,在真空袋制袋方面,由于减少了二个热封边,在对包装内容物的保护上比流延膜有着非常大的优势。
在拉伸强度方面比流延膜好。
2、多层共挤流延法:这种生产工艺主要是由多台挤出机,多流道分配器(俗称“集料器”),T型模头,流延系统,水平牵引系统,振荡器,收卷系统组成。
这种生产工艺主要的特点在于,生产出来的薄膜制品表面光泽度好,平整度高,厚度公差小,力学延伸性能好,柔韧性好,透明度比吹塑法高。
目前进口机组以原德国巴登菲尔德,德国W&H,意大利科林斯,奥地利兰精公司,原日本三菱重工为代表,国产机组以佛山仕诚为代表。
同样,国产流延机组的生产方式与吹塑一样,主要的核心部件来自于国外供应商。
目前此种生产工艺主要应用在国内的CPP行业,在七层共挤高阻隔性生产中也有少量的应用。
进口生产线中主要以广东中山祥富的七层和十一层机组与常州海企塑业的九层机组为代表。
这两种生产工艺在我国是最为常见的,由于吹塑工艺在产品平整度以及透明度方面不能与流延膜相比,但是其生产的高效率,设备投入低,低材料损耗量是流延工艺无法比拟的。
因此,在国外企业对吹塑工艺不足之处的改进上,进行了深入的研究与开发,主要体现在(1)模头设计改进,采用了独特的平行多流道设计理念;(2)对挤出机放置的位置与角度上;(3)泠却系统的改进(以风环与内冷技术为主)(4)材料配方与结构设计这四个方面。
通过实践证明,在薄膜的透明度,平整度,各层材料的厚薄均匀度上都达到或接近流延法的水平。
如果国内企业在高阻隔薄膜设备投入方面,2010年以后基本以吹膜为主。
吹塑法和流延法的比较
吹塑法和流延法是聚烯烃薄膜生产加工的两种主要生产工艺方法。
吹塑法较早应用于薄膜的生产加工,因其生产工艺的局限性和产品无法克服的缺陷,二十世纪八十年代,一种更为先进的薄膜生产加工工――流延法逐步发展起来,尤其是采用多层共挤的技术,使流延法的薄膜生产加工工艺得以大范围的推广和应用,并以其高品质的产品特点逐步应用于各种物品的高档次包装中,而吹塑法由于其固有的缺陷,只能满足于普通中、低档次产品的包装。
生产工艺比较
1、流延法比吹塑法更加适合应用于多层共挤的薄膜生产加工,尤其当使用多种不同材质的材料进行共挤时,流延法的生产工艺参数更易于控制,加工设备的关键部分――模头的设计更能有效保证产品中各种材料分布的均匀性。
而吹塑法的多层共挤模头技术难度更大,结构更为复杂且技术尚不够成熟。
2、流延法的加工设备中,模头至冷辊(成型至定型)的距离一般为10~20mm,熔膜帘很短且在真空吸气罩、气刀及定边装置的帮助下很快定型,产品质量好且稳定。
而吹塑法由于熔膜有一个吹胀过程,并依靠空气或水来冷却定型。
产品的定型时间过长且定型前的变化很大(一般吹胀4~7倍)。
容易在熔膜阶段受到外界和自身因素的影响,产品质量控制的难度非常大且稳定性差。
3、在原料的选择上吹塑法和流延法也有较大差异,多层共挤时吹塑法要求尽量选用流动性接近的材料来相互搭配,当材料流动性相差较大时,缺乏相应措施进行调整,因而当选定了其中一种材料时,与其共挤的其他材料没有多大的选择余地,这在很在程度上制约了多层共挤加工工艺优势在产品质量上的体现,而流延法的加工设备通过对分流道的调节可以很轻松解决吹塑法中几乎无法解决的问题。
产品特点比较
1、吹塑法因有一个吹胀过程而导致产品的纵、横向的分子受到不同程度的拉伸。
产品的耐温度性能和热封性能都会受到较大影响,当产品需要蒸煮消毒(如121℃蒸气)时,成型中被拉伸的分子链受热后会有明显的回缩现象,导致产品严重变形,并且会大大降低热封连接处的强度而导致漏袋现象。
2、流延法生产薄膜(又称未拉伸薄膜)时,分子排列有序,产品冷却速度快,有利于提高产品的透明度、光泽度及厚薄均匀性,且产品质地较软、较韧;抗冲击性能、耐热及低温适应性均好于吹塑法。
3、流延法的生产效率极高,产品质量稳定性好。
生产过程中的废料少,且较易实现在线回收边、废料,材料的利用率高。
4、流延法采用平模头,模头内设有特殊滞留槽,能保证材料流动时的均匀一致,并且通过模头的自动调节装置可自动控制模唇间隙的均匀性,控制精度非常高,较厚的薄膜可控制在±3%以下。
而吹塑法采用的环形模头及多层叠加的模芯,对加工精度和装配精度要求非常高且特别难以控制,如果加工及配合精度有微小的误差,无法通过调节来弥补,因此产品的厚薄公差基本在±10%左右,对于200μm厚的薄膜而言也就意味着最薄处为180μm而最厚处可能为220μm,在焊封制袋时,模具的间隙和热封温度无论如何调整都难以保证最厚处和最薄处都能达到必须的封合强度。
漏袋现象在所难免,成品率自然很低。
5、对于熔体强度较低的材料,需采用下吹法、水冷定型。
水份烘干不彻底或电晕层选料不当都会导致电晕处理效果差或电晕衰减严重。
影响印刷的油墨粘接牢度而导致脱色。
流延法采用钢制铸片辊(内通冷却水)对薄膜冷却定型,水分不与薄膜直接接触。
6、对于需蒸煮(121℃蒸气杀菌)的薄膜,无论流延法还是吹塑法都必须选用耐蒸煮级的原材料。
非蒸煮级的材料蒸煮后会导致薄膜变硬、变脆及产生白化现象。
既影响薄膜的外观又会导致袋子的耐冲击性和抗压力严重下降,无法达到检测标准和使用要求。
7、在塑料成型加工过程中,由于受热分解或低分子淅出物极易在口模处产生残留物的堆积。
流延法可以很容易地清除而吹塑法膜泡内的残留物只能停机清除。
不及时清除极易夹带在膜中,造成内容物中杂质含量超标或在薄膜表面产生明显的划痕。
由于吹塑法本身产量低、开车浪费大,如频繁开、停车单位生产成本大幅度上升。
投资费用比较
1、由于吹塑法一次性投资少,厂房占地面积小,设备便宜,投资小见效快(设备加工周期短、安装调试期短、辅助设备及设施少、要求低)。
而流延法的设备、厂房及设施一次性投资非常大,是吹塑法的5至10倍。
因而目前吹塑法的应用较流延法显得更多。
2、由于吹塑法受工艺条件限制导致产品质量差、产量小、单位生产成本高,虽经不断改进和完善,仍难以取代流延法。
这就是目前食品包装基材膜中流延膜的产量远远高于吹塑薄膜的最根本的原因。