流延成型法
塑料薄膜流延成型操作流程

塑料薄膜流延成型操作流程英文回答:Plastic Film Extrusion Coating Process.Introduction.Plastic film extrusion coating is a process of applying a thin layer of plastic to a substrate material, such as paper, metal, or plastic. The process involves extruding molten plastic through a die and onto the substrate material. The plastic film is then cooled and solidified to form a permanent bond with the substrate.Process Steps.The plastic film extrusion coating process typically involves the following steps:1. Preparation of the substrate material: The substratematerial is cleaned and prepared to ensure proper adhesion of the plastic film.2. Extrusion of the plastic film: Molten plastic is extruded through a die to form a thin film.3. Application of the plastic film to the substrate: The plastic film is applied to the substrate material using a variety of methods, such as roll coating, extrusion coating, or lamination.4. Cooling and solidification: The plastic film is cooled and solidified to form a permanent bond with the substrate.5. Finishing: The finished product is inspected and cut to the desired size and shape.Advantages of Plastic Film Extrusion Coating.Plastic film extrusion coating offers a number of advantages over other methods of applying a plastic coatingto a substrate material, including:High production rates.Uniform film thickness.Excellent adhesion.Ability to apply a wide range of plastic materials.Versatility in terms of substrate materials.Applications of Plastic Film Extrusion Coating.Plastic film extrusion coating is used in a wide variety of applications, including:Packaging.Construction.Automotive.Medical.Electronics.中文回答:塑料薄膜流延成型操作流程。
波纹膜片成型方法

波纹膜片的成型方法
波纹膜片的成型方法主要有压膜成型和流延成型两种。
压膜成型是制备波纹膜片的一种常用方法。
其工艺过程为:将平膜片加热至软化状态,然后通过模具在平膜片上施加压力,使平膜片产生弯曲变形,从而形成波纹膜片。
在压膜成型过程中,需要控制压力和温度等因素,以保证波纹膜片的质量和稳定性。
流延成型是一种将流体物质连续不断地涂覆在运转着的支撑体上的成型方法,也被应用于制备波纹膜片。
其工艺过程为:将平膜片作为支撑体,将波纹形模具放在平膜片上,然后将熔融状态的聚合物从模具的一侧引入,在重力的作用下聚合物在模具内流延,形成波纹膜片。
流延成型制备的波纹膜片具有较高的弹性恢复率和良好的稳定性。
此外,还可以采用化学腐蚀法、光刻法、热膨胀法等方法制备波纹膜片。
不同的制备方法适用于不同类型和规格的波纹膜片,需要根据具体需求选择合适的方法。
特种陶瓷的成型方法

第三节 成型工艺
一、压力成型方法
所谓压力成型是用粉料,即以固体颗粒为原料在一定的 压力下进行成型的方法,也叫模压成型或干压成型。 为了减少摩擦和增加强度,粉料中可能含有少量液体、 粘结剂包裹在颗粒外面。粘结剂含量较低(一般为 7~ 8% )。
(一)干压成型
干压成型又称模压成型,是将粉料经过造粒、流动性好,颗粒级配 合适的粉料,装入模具内,通过压机的柱塞施以外加压力,使粉料压 成制一定形状的坯体的方法。 这是最常用的成型方法之一。由于粉末 颗粒之间,粉末与模冲、模壁之间的摩擦,使压制压力损失,造成压 坯密度分布的不均匀。单向压制时,密度沿高度方向降低。
条件下,快速充填到模具内,避免架桥和死角形成,对获得均匀坯体 尤为重要。 c.粘结剂和润滑剂:选择合适的润滑剂和粘结剂将有助于降低模壁与粉 体以及粉体之间的磨擦,从而使素坯密度保持均匀,也降低了模具的 磨损。 d.模具设计。很大程度上依赖于工程师们的经验,以及材料烧结收缩率, 选择合适的形状和公差,来保证成型工艺的质量和成品率。
第三节 成型工艺
(二) 挤压成型 挤压是利用液压机推动活塞,将已塑化的坯料从挤压
嘴挤出。由于挤压嘴的内型逐渐缩小,从而使活塞对泥团 产生很大的挤压力,使坯料致密并成型。
挤压被广泛用于生产砖、地砖、管子、棒以及具有等 截面的长形部件。截面形状非常复杂的部件也可采用挤压, 最具代表性的是大量用于汽车尾气排放的蜂窝陶瓷的生产, 目前国内制造陶瓷蜂窝体均采用此方法 。也可用于生产热 交换器的蜂窝结构。
(3)挤压法的优点: 污染小,操作易于自动化,可连续生产,效率高。
干式等静压制原理图
¾ 干压等静压成型的特点:
¾ 干式等静压更适合于生产形状简单的长形、壁薄、 管状制品。
异丙醇浓度对流延法成型玉米醇溶蛋白膜性质的影响

( 天津科技大学食品工程与生物技术学院,天津 3 0 0 4 5 7 )
摘要:通过对蛋 白膜进行拉伸强度 ,水蒸气透过率、吸水性、接触 角、A F M 和 DS C测定,研究不同浓度的异 丙醇溶液制备玉
米醇溶蛋白膜性质 。结果表明:随异丙醇浓度的增加 ,拉伸强度逐渐增加 ,浓度为 9 0 %时达到最大值 5 7 . 7 Me a 。水蒸气透过率和吸 帕J 生随着浓度的增加 而降低,浓度为 9 0 %时,最低值 为 0 . 0 7 5 x 1 0 g r r g ( m2 一 h P a ) f x , 3 7 . 2 %;接触角实验 表明:异 丙醇浓度为 9 0 %时, 接触角最大为 6 7 o ,蛋白膜具有 良好的疏抽 } 生。9 0 %异丙醇溶液制备 的玉米醇溶蛋白膜进行 A F M 测定,结果表明:玉米醇溶蛋白形
o f z e i nf i m p l r o d u c d f e r o m9 0 % i s o p r o p a n o l s o l u i t o nwa s6 7 。a nd s h o we dg 0 o dwa t e r p r o o f p r o p e r t i e s . Me a s u r e me nt o f AF M s h o we dt h a t z e i n
流延膜成型工艺及设备讲解学习

高分子材料专业 高分子成型加工技术Ⅰ(塑料)
四、流延薄膜的特性
• 流延薄膜具有优越的热封性能和优良的透明性,是主要的 包装复合基材之一,用于生产高温蒸煮膜、真空镀铝膜等, 市场极为看好。而且,随着国产流延膜生产设备的发展, 其中部分技术指标均达到国际先进水平。因而,进入流延 膜生产的门槛越来越低。正因为如此,一些企业为了一步 到位,争相进口流延薄膜生产线,在档次上追求层次越高 越好,而把市场需求和投资回报率抛到一边,这种做法将 造成巨大的资源浪费。
五、流延薄膜的原材料
• 挤出流延薄膜的树脂: • PP、PE、PA等,PS、PET主要用于双向拉伸薄
膜,在流延薄膜中叶使用,对氧气、水蒸气的透 过具有良好阻隔作用的EVOH和PVDC常用于多 层共挤流延薄膜中。
高分子材料专业 高分子成型加工技术Ⅰ(塑料)
六、挤出流延膜的工艺流程
高分子材料专业 高分子成型加工技术Ⅰ(塑料)
七、流延膜的成型设备
• 流延膜典型的成型设备包括“挤出机、机头、冷却装置、 测厚装置、切边装置、电晕处理装置、收卷装置等组成。
挤出机
• 螺杆直径:Φ90~ Φ200 • 长径比:25~33 • 挤头出机必须安装在移动的基座上
机头
• 1.支管式机头(亦称歧管式) • 2.衣架式机头 • 3.分配螺杆机头 • 4.其它形式的机头 • 5.过滤熔料装置
大,结构比较疏松,薄膜的强度较低。 • (5) 生产成本高,能耗大、溶剂用量大,生产速度低。
三、挤出熔融流延膜
1、流延涂布法
• 流延涂布法,属于挤出熔融流延膜的一种,其基本原理是 通过涂布头空腔的压力注入粘合剂,涂布头的顶端是一个 可调大小的细缝,涂布时随着底纸的运行,粘合剂均匀的 由涂布头的细缝中流出并涂布在底纸表面。
塑料薄膜挤出流延成型工艺过程图示详解
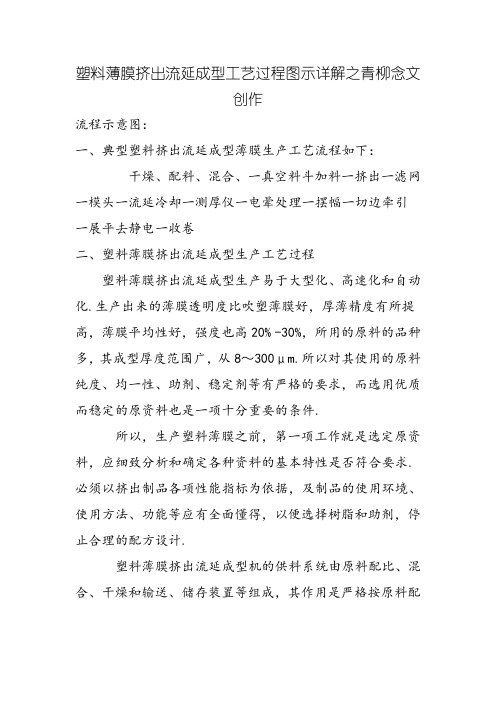
塑料薄膜挤出流延成型工艺过程图示详解之青柳念文
创作
流程示意图:
一、典型塑料挤出流延成型薄膜生产工艺流程如下:
干燥、配料、混合、一真空料斗加料一挤出一滤网一模头一流延冷却一测厚仪一电晕处理一摆幅一切边牵引一展平去静电一收卷
二、塑料薄膜挤出流延成型生产工艺过程
塑料薄膜挤出流延成型生产易于大型化、高速化和自动化.生产出来的薄膜透明度比吹塑薄膜好,厚薄精度有所提高,薄膜平均性好,强度也高20% -30%,所用的原料的品种多,其成型厚度范围广,从8~300μm.所以对其使用的原料纯度、均一性、助剂、稳定剂等有严格的要求,而选用优质而稳定的原资料也是一项十分重要的条件.
所以,生产塑料薄膜之前,第一项工作就是选定原资料,应细致分析和确定各种资料的基本特性是否符合要求.必须以挤出制品各项性能指标为依据,及制品的使用环境、使用方法、功能等应有全面懂得,以便选择树脂和助剂,停止合理的配方设计.
塑料薄膜挤出流延成型机的供料系统由原料配比、混合、干燥和输送、储存装置等组成,其作用是严格按原料配
比要求,及时为挤出机供料,以使挤出机生产持续平稳地停止.
为了确保塑料薄膜挤出流延成型质量,及产品的物理力学性能,需准确计量各种原料的加入量.对于高质量的流延成型薄膜(如多层、多种原料的混合挤出等),应配备高精度的矢量计重系统.。
压延法、吹塑法、流延法、多层共挤生产工艺及产品性能差别

压延法、吹塑法、流延法、多层共挤生产工艺及产品性能差别一、生产工艺1、流延树脂经挤出机熔融塑化,从机头通过狭缝型模口挤出,使熔料紧贴在冷却辊筒上,然后再经过剥离、位伸、分切、卷取得到成品。
流延生产工艺示意图2、吹塑树脂经挤出机熔融塑化,从环形机头垂直向上引出,经吹胀后由人字板导入牵引辊,再经导向辊及卷取装置得到成品。
吹塑生产工艺示意图3、压延树脂经挤出机熔融塑化,从机头通过狭缝型模口挤出,经三辊压光机压延、次却,再经过冷却输送辊及卷取装置得到成品。
压延生产工艺示意图4、多层共挤多层共挤流延膜挤出技术是一种将两种或两种以上的不同塑料利用2台或2台以上的挤出机通过一个多流道的复合模头,汇合生产多层结构的复合薄膜,并通过急冷辊成型的技术。
多层共挤流延膜挤出技术也是传统的生产薄膜的挤出生产工艺。
采用这种方法可生产各种不同材料的薄膜,且具有很高的加工精度,尤其是在加工半结晶热塑性塑料时,这种加工方法能够充分地发挥被加工材料的性能,同时又能保持最佳的尺寸精度。
所制得的流延膜具有优良的光学性能和厚薄均匀度,并且由于采用急冷辊可以获得很高的生产速度,并改善薄膜的形态结构。
此法制得的薄膜与其他薄膜(如吹膜)相比,其优点是生产速度快,产量高,有利于大批量生产;产品的厚薄控制精度较高,厚度均匀性较好;透明性和光泽性俱佳;各向平衡性能优异。
某些材料,例如聚丙烯(PP)膜、聚脂(PET)膜加工的通用方法甚至是唯一的方法就是多层共挤流延法。
二、吹塑法和压延法的主要区别:(1)在同样生产能力,生产相同规格产品时,投资上压延式工艺比吹塑式工艺要高出大约十倍以上,大的投资才能保证好的质量。
(2)压延式生产工艺远远先进于吹塑式,在产品的各个性能指标(拉伸强度、拉伸断裂伸长率、直角撕裂强度、水蒸气渗透系数)上均高于吹塑产品,尤其在膜的厚度均匀程度上,压延式远比吹塑式均匀。
(3)从材料取向上讲,不同的生产工艺也直接影响到施工焊接二次加热时的稳定性,压延法生产的土工膜焊接时产生的收缩性远远小于吹塑式工艺生产的土工膜。
聚合物基复合材料的工艺

3.聚合物基复合材料的工艺(重要)(1)预浸料的制备工艺1.热固性预浸料的制备1)溶液浸渍法。
将树脂基体个组分按规定的比例溶解于低沸点的溶剂中,使之成为一定浓度的溶液,然后将纤维束或织物以规定的速度通过基体溶液,使其浸渍上定量的基体溶液,并通过加热除去溶剂,使树脂得到合适的黏性。
2)热熔法。
分为直接熔融法和胶膜压延法。
2.热塑性预浸料制备。
可分为预浸渍技术与后浸渍技术两类。
(2)手糊成型工艺。
先在磨具上涂刷一层脱膜剂,后加入含固化剂树脂混合物,再在其上铺贴一层按要求剪裁好的纤维织物,用刷子、压辊或刮刀压挤织物,使其均匀浸胶并排除气泡,再涂刷树脂混合物和铺贴第二层纤维织物,反复上述过程直至达到所需厚度为止。
然后再固化、脱膜、修边,得到复合材料制品。
(3)模压成型工艺。
是将一定量的预混料或预浸料加入金属对模内,经加热、加压固化成型的方法。
是广泛使用的对热固性树脂和热塑性树脂都适用的纤维复合材料成型方法。
(4)喷射成型工艺。
将分别混有促进剂和引发剂的不饱和聚酯树脂从喷枪两侧测(或在喷枪内混合)喷出,同时将玻璃纤维无捻粗纱用切割机切断并由喷枪中心喷出,与树脂一起均匀沉积到模具上。
持沉积到一定厚度,用手辊滚压,使纤维浸透树脂、压实并除去气泡,最后固化成制品。
(5)连续缠绕工艺。
一种将浸渍了树脂的纱或丝束缠绕在回转芯模上。
常压下在室温或较高温度下固化成型的一种复合材料制造工艺。
是一种生产各种尺寸回转体的简单有效的方法。
(6)注射成型。
将颗粒状树脂、短纤维送入注射腔内,加热熔化、混合均匀,并以一定的挤出压力,注射到温度较低的密闭模具中,经过冷却定型后,开模便得到复合材料制品。
6.陶瓷基复合材料的制备工艺(成型工艺)(1)等静压成型。
一般等静压指的是湿袋式等静压(也叫湿法等静压),就是将粉料装入橡胶或塑料等可变形的容器中,密封后放入液压油或水等流体介质中,加压获得所需的坯体。
(2)热压铸成型。
热压铸成型是将粉料和蜡(或其他有机高分子黏结剂)混合后,加热使蜡(或其他有机高分子黏结剂)熔化,使混合料具有一定流动性,然后将混合料加压注入模具,冷却后即可得到致密的较硬实的坯体。
- 1、下载文档前请自行甄别文档内容的完整性,平台不提供额外的编辑、内容补充、找答案等附加服务。
- 2、"仅部分预览"的文档,不可在线预览部分如存在完整性等问题,可反馈申请退款(可完整预览的文档不适用该条件!)。
- 3、如文档侵犯您的权益,请联系客服反馈,我们会尽快为您处理(人工客服工作时间:9:00-18:30)。
0 0
2
4
6
8
pH值
10
12
14
内,沉积率低于15%,浆料的分散稳定性更 好。另一方面,在pH>12时,沉积率均有所
增加。这是因为加入了较多的NaOH,引起
离子强度的增加,双电层厚度减小,由于范
德华力的作用,陶瓷颗粒相互靠近,从而影
响浆料的稳定性,使沉积率增加。
分散剂对ZrO2浆料粘度的影响
▪ 粉料和溶剂恒定时,浆料粘度与分散
流延成型溶剂
▪ 选择溶剂的基本原则为:必须能溶解其它添加成分,包括分散剂、 粘结剂和增塑剂等;在浆料中能保持化学稳定性,不与粉料发生 化学反应;易于挥发与烧除;使用安全卫生和对环境污染少。最 常用的溶剂分为有机溶剂和水两大类。因用有机溶剂所得的浆料 粘度低,溶剂挥发快,干燥时间短,所以流延法制膜中使用有机 溶剂较多,但使用有机溶剂存在易燃和有毒的缺点,而用水作溶 剂则具有成本低、使用安全卫生和便于大规模生产等优点,其缺 点是:对粉料颗粒的湿润性能较差、挥发速度慢和干燥时间长;浆 料除气困难,气泡的存在会影响素坯的质量;水基浆料所用粘结 剂多为乳状液,品种较少使粘结剂的选择受到限制。溶剂对粉料 的湿润性能主要与其表面张力有关,表面张力越小,对粉料颗粒 的湿润性能越好。有机溶剂的表面张力比水要低得多,所以其湿 润性能比水好。混合溶剂的表面张力和介电常数等综合性能较单 一组分要好,且沸点低,对分散剂、粘结剂和塑性剂的溶解性能 也较佳。研究表明,所谓“动力学溶剂”(小分子如乙醇)和 “热力学溶剂”(酯、酮)的混合物是最有效的。为确保干燥过 程中同时挥发,流延浆中常用二元共沸混合物。最常用的有乙醇/ 甲乙酮、乙醇/三氯乙烯、乙醇/水和三氯乙烯/甲乙酮等。
流延陶瓷片基元件用途
1陶瓷单层
A电容器 B压电陶瓷 C电子陶瓷
2多层陶瓷部件
A多层平板式传感器 B固体氧化物燃料电池(SOFC)
3.2厚膜成型工艺 陶瓷片基元件总生产流程图
目前得到广泛应用的流延成形工艺为非水基流延成型工艺,即传统的流延工艺,其工艺 包括浆料制备、球磨、脱泡、成型、干燥、剥离基带等工序。该工艺的特点是设备简单,
流延等静压复合成型工艺
▪ 流延等静压复合成型工艺是以非水基和水基流延成型工艺为 基础的工艺过程,它把流延成型工艺和等静压成型工艺有效 的结合起来,以提高素坯的成型密度和烧结密度,工艺过程 较为简单,易于陶瓷膜的工业化生产。由于流延素坯本身制 备工艺的限制,其浆料固含量较低,虽然通过增大粒径,可 以提高浆料固含量和提高素坯密度,但粉体粒子粒径过大, 其烧结性能就会下降,反而会导致烧结膜材密度下降。另一 方面在素坯干燥过程中,因溶剂的挥发,粘结剂和塑性剂难 以在干燥前填充溶剂挥发留下的气孔,从而在素坯表面和内 部留有许多凹坑和孔洞,使素坯结构疏松,密度较低,而单 层流延膜由于厚度较小,不能采用一些非常规烧结手段(如 热压烧结),只能采用无压烧结,加上烧结过程中大量有机 添加剂的烧除,很难获得致密的流延烧结膜材。因素坯密度 较低,结构疏松但延展性较好,故对素坯采用等静压二次成 型提高素坯成型密度,将提高烧结膜材密度。
陶瓷流延成型法
▪ 流延工艺是由Glenn N.Howatt最早提出并应用于陶瓷成型领 域,并于1952年获得专利。流延法是一种制备大面积、薄平 陶瓷材料的重要成型方法,流延成型自出现以来就用于生产 单层或多层薄板陶瓷材料。现在,流延成型已成为生产多层电 容器和多层陶瓷基片的支柱技术,同时也是生产电子元件的必 要技术:如用Al2O3制得各种厚度的集成电路基板和衬垫材 料;用BaTiO3制成电容器介质材料;用ZrO2制成固体氧化 物燃料电池、氧泵和氧传感器等。此外,流延成型工艺还可用 于造纸、塑料和涂料等行业。流延成型工艺包括浆料制备、 成型、干燥、剥离基带等过程。该工艺的特点是设备简单,工 艺稳定,可连续操作,生产效率高,可实现高度自动化。
50
位增大,静电稳定作用增强,有利于稳定分
40
散。相反,浆料电动电位降低,颗粒容易团
聚。由于加入不同分散剂后浆料等电点并不
30
相同,因此不同分散剂的最佳pH范围也有
20
所不同。比较三条曲线可知,磷酸三丁酯和
10
松油醇作分散剂时,其沉积率均在25%以上。 而三乙醇胺作分散剂时,在9.5<pH<11范围
量。针对上述缺点,研究人员开始尝试用水基溶剂体系替代有机溶剂体系。
脱脂 烧结
水基流延成型工艺
▪ 水基流延成型工艺使用水基溶剂替代有机溶剂,由 于水分子是极性分子,而粘结剂、增塑剂和分散剂 等是有机添加剂,与水分子之间存在相容性的问题, 因此在添加剂的选择上,需选择水溶性或者能够在 水中形成稳定乳浊液的有机物以确保得到均一稳定 的浆料。同时还应在保证浆料稳定悬浮的前提下, 使分散剂的用量尽量地少,同时在保证素坯强度和 柔韧性的前提下使粘结剂、增塑剂等的有机物的用 量尽可能少。
流延法分散剂
▪ 在实际的流延悬浮液中,空间位阻和静电排斥力一般同时存 在,称之为静电位阻稳定作用。
▪ 流延法制膜中常用的分散剂按类型分为非离子、阴离子、阳 离子和两性离子四种。一般说来,阴离子表面活性剂主要用 于颗粒表面带正电的中性或弱碱性浆料,而阳离子型表面活 性剂主要用于颗粒表面带负电的中性或弱酸性浆料。
剂浓度呈非线性关系。随着分散剂用
量的增加,分散剂对颗粒的静电位阻 110
作用增强,浆料的流动性明显改善, 粘度也不断下降,直至达到最低粘度。 100
三乙醇胺 磷 酸三丁酯 松油醇
继续增加分散剂用量,浆料的粘度又
90
粘度 /mpa.s
有所增加,这是因为出现过饱和吸附
80
的情况,过量的分散剂分子相互桥联
工艺稳定,可连续操作,生产效率高,可实现高度自动化。
溶剂
粘结剂
陶瓷粉料
球磨
混磨
真空除泡 粘度调节 流延成型
干燥
分散剂
增塑剂
传统的非水基流延成型已经较为成熟,在陶瓷领域有广泛的应用,如用流延成 型制备氧化铝陶瓷膜、制备ALN膜、制备YSZ膜、流延成型制备陶瓷燃料电池 电解质膜等,也可以制备包含有晶须的复合陶瓷膜。 传统的流延成型工艺不足之处在于所使用的有机溶剂(如甲苯、二甲苯等)具有 一定的毒性,使生产条件恶化并造成环境污染,且生产成本较高。此外,由于浆 料中有机物含量较高,素坯密度低,脱脂过程中坯体易变形开裂,影响产品质
40
球磨时 间 /h
100
1200℃煅烧未球磨
煅烧后球磨40h
80
60
40
20
0
0.0 0.2 0.4 0.6 0.8 1.0 1.2 1.4 1.6 1.8 2.0 2型工艺中,稳定浆料的制备是成型低缺陷高质量陶 瓷坯片的关键。浆料制备过程中产生的缺陷难以通过后续工 艺步骤的调整来消除,粉料颗粒在流延浆料中的分散性和均 匀性直接影响素坯的质量及烧结特性,从而影响烧结致密性、 气孔率和机械强度等一系列特性。因此,在成型过程中,控 制浆料中颗粒的作用力,以便排除团聚体,改善浆料的流变 学性质对于坯体的成型和坯体性质的优化至关重要。为了制 备结构均匀的高固相含量浆料,必须了解粉料颗粒在浆料中 的受力情况,采用合适的评价指标,考察不同分散剂及其用 量、浆料pH值、粘结剂、增塑剂以及球磨时间等因素对浆料 粘度和稳定性的影响规律,为制备稳定分散的浆料提供依据。
水基流延成型工艺优缺点
▪ 水基流延成型具有价格低廉,无毒性,不易燃等优 点,但也存在一些问题:a)蒸发速度低;b)所需的 粘结剂浓度高;c)氢键引起陶瓷粉末团聚导致絮凝; d)浆料对工艺参数变化敏感,不易成型表面致密光 滑的陶瓷膜;e)坯体结合不充分,干燥易起泡开裂, 脆性大,易弯曲变形;f)缺陷引起应力集中,导致 烧结开裂。目前,水基流延成型的研究主要应用于 Al2O3, ZrO2等少数的氧化物陶瓷,对TiC也有研 究。
分散剂和pH值对氧化锆浆料稳定性的影响
沉积率RSH(%)
80
▪ 随着pH值的改变,沉积率均有较大变化。
三乙醇胺
这是因为调节浆料pH值使其接近或远离等
70
磷 酸三丁酯 电点(isoelectric point, IEP),会相应的引
60
松油醇
起浆料电动电位的减少或增大,根据静电稳
定理论,pH值远离等电点时,浆料电动电
凝胶流延成型工艺
▪ 水基凝胶流延成型工艺是利用有机单体的聚合原理进行流延 成型。该法是将陶瓷粉料分散于含有有机单体和交联剂的水 溶液中,制备出低粘度且高固相体积分数的浓悬浮体(<50 %体积分数),然后加引发剂和催化剂,在一定的温度条件
下引发有机单体聚合,使悬浮体粘度增大,从而导致原位凝
固成型,得到具有一定强度、可进行机加工的坯体。水基凝
陶瓷流延成型法
▪ 流延成型的具体工艺过程是将陶瓷粉末与分散剂、 粘结剂和增塑剂在溶剂中混合,形成均匀稳定悬浮 的浆料。成型时浆料从料斗下部流至基带之上,通 过基带与刮刀的相对运动形成坯膜,坯膜的厚度由 刮刀控制。将坯膜连同基带一起送入烘干室,溶剂 蒸发,有机结合剂在陶瓷颗粒间形成网络结构,形 成具有一定强度和柔韧性的坯片,干燥的坯片连同 基带一起卷轴待用。在储存过程中使残留溶剂分布 均匀,消除湿度梯度。然后可按所需形状切割、冲 片或打孔。最后经过脱脂烧结得到成品。
70
成网络结构,极大地限制了颗粒的运 60
动,再加上离子强度的增加,从而使 50
浆料粘度升高。故每种分散剂用量均 40
有一个最佳范围,使浆料粘度达到最 30
粉末处理工艺
煅烧温度与球磨时间:球磨工艺不仅减小了平均粒径,而且也使粒 径分布区域变窄。
粒度分析
原始粉料
煅烧
球磨
烘干
过筛
实验用粉料
平均粒径 /μm 百 分 数 /%
0.70 0.65 0.60 0.55 0.50 0.45 0.40