模具设计R角极限加工深度表
折弯半径和板厚的关联
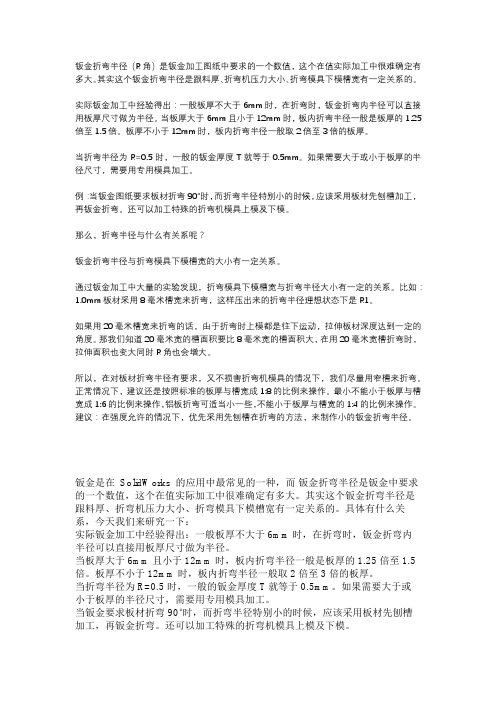
钣金折弯半径(R角)是钣金加工图纸中要求的一个数值,这个在值实际加工中很难确定有多大。
其实这个钣金折弯半径是跟料厚、折弯机压力大小、折弯模具下模槽宽有一定关系的。
实际钣金加工中经验得出:一般板厚不大于6mm时,在折弯时,钣金折弯内半径可以直接用板厚尺寸做为半径。
当板厚大于6mm且小于12mm时,板内折弯半径一般是板厚的1.25倍至1.5倍。
板厚不小于12mm时,板内折弯半径一般取2倍至3倍的板厚。
当折弯半径为R=0.5时,一般的钣金厚度T就等于0.5mm。
如果需要大于或小于板厚的半径尺寸,需要用专用模具加工。
例:当钣金图纸要求板材折弯90°时,而折弯半径特别小的时候,应该采用板材先刨槽加工,再钣金折弯。
还可以加工特殊的折弯机模具上模及下模。
那么,折弯半径与什么有关系呢?钣金折弯半径与折弯模具下模槽宽的大小有一定关系。
通过钣金加工中大量的实验发现,折弯模具下模槽宽与折弯半径大小有一定的关系。
比如:1.0mm板材采用8毫米槽宽来折弯,这样压出来的折弯半径理想状态下是R1。
如果用20毫米槽宽来折弯的话,由于折弯时上模都是往下运动,拉伸板材深度达到一定的角度。
那我们知道20毫米宽的槽面积要比8毫米宽的槽面积大,在用20毫米宽槽折弯时,拉伸面积也变大同时R角也会增大。
所以,在对板材折弯半径有要求,又不损害折弯机模具的情况下,我们尽量用窄槽来折弯。
正常情况下,建议还是按照标准的板厚与槽宽成1:8的比例来操作。
最小不能小于板厚与槽宽成1:6的比例来操作,铝板折弯可适当小一些,不能小于板厚与槽宽的1:4的比例来操作。
建议:在强度允许的情况下,优先采用先刨槽在折弯的方法,来制作小的钣金折弯半径。
钣金是在SolidWorks 的应用中最常见的一种,而钣金折弯半径是钣金中要求的一个数值,这个在值实际加工中很难确定有多大。
其实这个钣金折弯半径是跟料厚、折弯机压力大小、折弯模具下模槽宽有一定关系的。
具体有什么关系,今天我们来研究一下:实际钣金加工中经验得出:一般板厚不大于6mm时,在折弯时,钣金折弯内半径可以直接用板厚尺寸做为半径。
冲模设计规范

冲模模具设计规范设计准则冲模的设计是在合同评审后,IE会提出时候开模,PORJ相继会提供模具的下料尺寸,隔离膜的宽度,由PE去做设计与绘图。
从以上的几点信息,先判断是采用双坑设计还是单坑设计,判断的依据是根据电芯的型号。
大电池,冲模长度范围是75-200mm,宽度50-110mm,厚度6.0mm以下可以采用单坑设计;厚度 6.0mm以上可采用双坑设计。
中电池,冲模长度范围45-74mm,宽度范围30-49mm,厚度5.5mm以下的可采用单坑设计,厚度5.5mm以上采用双坑设计。
小电池,冲模长度范围15-44mm,宽度范围10-29mm,厚度4.0mm以下采用单坑设计,厚度4.0mm 以上就采用双坑设计。
最小可冲深的深度为1.2mm。
冲模间隙,冲模的间隙是模芯与模腔的距离,间隙可以影响到冲模成型时候存在裂纹或则是完全冲裂。
间隙取值是0.35-0.5之间,参与拉伸的面积大,深度深的时候,可以取间隙下限,反之则选下限。
R角的选择:R角H代表的是电芯宽度方向的R角,H=电芯的厚度/2,深度4.0mm以下,可以直接采用上面的公式,深度4.0mm以上H=电芯的厚度/2-0.5mm。
R角J代表的电芯的高度方向的R角,J的取值为R1.5R角I代表模腔上的R角,I的取值为R0.6-0.8。
冲模单坑模芯设计公式:模芯宽度D= 电芯设计总宽—1.2-1.5mm,模芯长度C= 电芯设计高度—单边间隙(0.4mm)*2—(经验值)0.8mm逆向设计:C=隔膜的宽度+0.3(隔膜与POCKET间隙)+单边间隙(0.4mm)*2+0.8mm(经验值)备注:这样可以判断PORJ给出的隔膜宽度是否能实现电芯不超高A = 10mm(这里讲的是冲模的有效模面,10mm是侧封边+拉伸面积)B=12mm(这里讲的是冲模的有效模面,12mm是侧封边+拉伸面积)G=2(B+C)E=A+D+气袋长度+拉伸面积F=冲模深度靠模设计R=模芯高度+0.6-0.8mm(经验值)S=R+L(3/3.5mm)T=2SP在7.5冲模深度以下,P=10-12mm,在7.5冲模深度以上,P=冲模深度+5mm Q在冲模深度5.0mm以下,取6.0mm,5.0以上Q=冲模深度+1mmM=7mm,代表的是侧封边宽度L=封头宽度+1mmN=模芯宽度+0.6-0.8mm(经验值)O=M+N+气袋宽度冲模单坑模芯设计公式:模芯宽度D= 电芯设计总宽—1.2-1.5mm,模芯长度C= 电芯设计高度—单边间隙(0.4mm)*4—模芯之间间隙(E=1.5mm)—(经验值)0.8mm靠模设计F/H=模芯高度+0.6-0.8mm(经验值)I/J =模芯宽度+0.6-0.8mm(经验值)。
冲压件模具设计常用公式

第三章常用公式及數據表第四節衝壓件模具設計常用公式一. 衝裁間隙分類見表4-1表4-1衝裁間隙分類(JB/Z271-86)分類依據類別ⅠⅡⅢ制 件 剪 切 面 質 量剪切面特征t=材料厚度塌角深度a (4~7)%t (6~8)%t (8~10)%t 光亮帶b (35~55)%t(25~40)%t(15~25)%t剪裂帶E 小 中 大 毛刺高度h 一般 小 一般 歪度β4°~7°7°~8°8°~11°制 件 精 度撓角f稍小 小 較大尺寸精度落料件接近凹模尺寸 稍小于凹模尺寸 小于凹模尺寸 沖孔件接近凸模尺寸稍小于凸模尺寸小于凸模尺寸模具壽命較低較高最高適用場合制件剪切面質量﹑尺寸精度要求高時采纳,模具壽命較低 制件剪切面質量﹑尺寸精度要求一般時采纳,適用于繼續塑變的制件制件剪切面質量﹑尺寸精度要求不高時采纳,以利提高模具壽命二. 衝裁間隙選取(僅供參考)見表4-2 (見下頁)表4-2衝裁間隙比值(單邊間隙)(單位:%t)(注:1.本表適用于厚度為10mm以下的金屬材料,厚料間隙比值應取大些;2.凸,凹模的制造偏差和磨損均使間隙變大,故新模具應取最小間隙;3.硬質合金衝模間隙比鋼模大20%左右.)注:衝裁間隙選取應綜合考慮以下因素:1.衝床﹑模具的精度及剛性.2.產品的斷面品質﹑尺寸精度及平坦度.3.模具壽命.4.跳屑.5.被加工材料的材質﹑硬度﹑供應狀態及厚度.6.廢料形狀.7.衝子﹑模仁材質﹑硬度及外表加工質量.三.衝裁力﹑卸(剝)料力﹑推件力﹑頂件力F衝=1.3*L*t*τ(N)(公式4-1)F卸=K卸*F衝(N)(公式4-2)F推=N*K推*K衝(N)(公式4-3)F頂=K頂*F衝(N)(公式4-4)其中:L――衝切線長度(mm)t――材料厚度(mm)τ――材料抗剪強度(N/mm2)1.3――平安系數K卸――卸(剝)料力系數K推――推料力系數K頂――頂料力系數K卸K推K頂數值見表4-3表4-3卸料力﹑推件力和頂件力系數料厚K卸K推K頂≦0.鋼鋁﹑鋁合金紫銅﹑黃銅注:卸料力系數K卸在衝多孔﹑大搭邊和輪廓復雜時取上限值.四.中性層彎曲曲折折曲曲折折折折曲曲折折曲曲折折折折折折半徑R=r+x*t(mm)(公式4-5)其中:R――中性層彎曲曲折折曲曲折折折折曲曲折折曲曲折折折折折折半徑(mm)r――零件內側半徑(mm)x――中性層系數中性層系數見表4-4(僅供參考)表4-4中性層系數x值注:彎曲曲折折曲曲折折折折曲曲折折曲曲折折折折折折件展開尺寸與以下因素有關:1.彎曲曲折折曲曲折折折折曲曲折折曲曲折折折折折折成形方式.2.彎曲曲折折曲曲折折折折曲曲折折曲曲折折折折折折間隙.3.有無壓料.4.材料硬度﹑延伸率﹑厚度.5.依据實際狀況精確修正.五.材料最小彎曲曲折折曲曲折折折折曲曲折折曲曲折折折折折折半徑,見表4-5表4-5最小彎曲曲折折曲曲折折折折曲曲折折曲曲折折折折折折半徑t≦2mm 2t 3t 4t 5t 注:表列數据用于彎曲曲折折曲曲折折折折曲曲折折曲曲折折折折折折中心角≧90∘﹑斷面質量良好的情況.六﹑彎曲曲折折曲曲折折折折曲曲折折曲曲折折折折折折回彈半徑及回彈角r凸=r0/(1+Kr0/t)(公式4-6)回彈角的數值為Δα=(180°-α0)(r0/r凸-1)(公式4-7)式中r凸――凸模的圓角半徑,[r凸]為mm;r0――工件的圓角半徑,[r0]為mm;α0――工件的彎曲曲折折曲曲折折折折曲曲折折曲曲折折折折折折角度,[α0]為(°);t――工件材料厚度,[t]為mm;K――簡化系數,見表4-6表4-6簡化系數k值名稱牌號狀態K 名稱牌號狀態K鋁L4,L6 退火磷青銅硬冷硬鈹青銅Qbe2軟防銹鋁LF21退火硬冷硬鋁青銅QA15 硬LF12 軟碳鋼08,10,A2硬鋁LY11軟20,A3 0.005硬30,35,A5LY12軟50硬碳工鋼T8退火銅T1,T2,T3 軟冷硬硬不銹鋼1Cr18Ni9Ti退火黃銅H62軟冷硬半硬彈簧鋼65Mn退火硬冷硬H68軟60Si2MnA 冷硬硬七﹑彎曲曲折折曲曲折折折折曲曲折折曲曲折折折折折折力計算針對“v〞型彎曲曲折折曲曲折折折折曲曲折折曲曲折折折折折折: F彎σb/(R+t)(N)(公式4-8)其中:b―――彎曲曲折折曲曲折折折折曲曲折折曲曲折折折折折折線長度(mm) t―――材料厚度(mm)r―――內側半徑(mm)σb――材料極限強度(N/mm2)k―――八﹑拉深(抽引)系數m=d/D(公式4-9)其中:d――拉深(抽引)后工件直徑(mm)D――毛坯直徑(mm)1.無凸緣或有凸緣筒形件用壓邊圈拉深系數見表4-7表4-7無凸緣或有凸緣筒形件用壓邊圈拉深的拉深系數(適用08,10號鋼)注:1)隨材料塑性上下,表中數值應酌情增減.2)――線上方為直筒件(d凸=d1).3)隨d凸/D數值增大,r/t值可相應減小,滿足2r1≦h1,保証筒部有直壁.4)查用時,可用插进法,也可用偏大值.5)屡次拉深首次形成凸緣時,為考慮多拉进材料,m1增大0.02.2.帶凸緣筒形件第一次拉深系見表4-8表4-8帶凸緣筒形件第一次拉深時的拉深系數m1注:適用于08﹑10號鋼3.無凸緣筒形件用壓邊圈拉深系數見表4-9表4-9無凸緣筒形件用壓邊圈時的拉深系數注:1.凹模圓角半徑大時(r凹=8~15t),拉深系數取小值,凹模圓角半徑小時(r凹=4~8t),拉深系數取大值.2.表中拉深系數適用于08﹑10S﹑15S鋼與軟黃銅H62﹑H68.當拉深塑性更大的金屬時(05﹑08Z及10Z鋼﹑鋁等),應比表中數值減小1.5-2%.而當拉深塑性較小的金屬時(20﹑25﹑A2﹑A3﹑酸洗鋼﹑硬鋁﹑硬黃銅等),應比表中數值增大1.5-2%(符號S為深拉深鋼,Z為最深拉深鋼).4.無凸緣筒形件不用壓邊圈拉深系數見表4-10表4-10無凸緣筒形件不用壓邊圈時的拉深系數注:適用于08﹑10以及15Mn等材料5.有工藝切口的第一次拉深系數見表4-11表4-11有工藝切口的第一次拉深系數m1(材料:08﹑10)6.有工藝切口的以后各次拉深系數見表4-12表4-12有工藝切口的以後各次拉深系數m n(材料:08﹑10))7.有工藝切口的各次拉深系數見表4-13表4-13有工藝切口的各次拉深系數軟鋼﹑鋁九﹑拉深(抽引)力F抽=3(σb+σs)(D–d-r凹)t(N)(公式4-10)其中:σb――材料極限強度(N/mm2)σs――材料屈服強度(N/mm2)D―――毛坯直徑(mm)d―――拉深凹模直徑(mm)r凹――拉深凹模圓角(mm)t―――材料厚度(mm)十﹑孔的翻邊1.翻邊系數K=d/D(公式4-11)d――預衝孔直徑(mm)D――翻邊后平均直徑(mm)各種材料極限翻邊系數見表4-14,表4-15表4-14低碳鋼的極限翻邊系數K翻邊方法孔的加工方法比值d/t100 50 35 20 15 10 8 5 3 1球形凸模鑚后往毛刺用沖孔模沖孔—圓柱形凸模鑚后往毛刺用沖孔模沖孔—表4-15其它一些材料的翻邊系數退火的材料翻邊系數K K min2.預衝孔直徑d=D-2(h-0.43r-0.72t)(公式4-12)h――翻邊高度(mm)r――翻邊圓角(mm)t――材料厚度(mm)3.翻邊高度h=D/[(1-k)/2]+0.4r+0.72t(公式4-13)4.翻邊口部材料厚度t1=t√k(mm)(公式4-14)πtσs(D-d)σs――材料屈服強度(Mpa)十一設計連接器五金零件應注重的要點1.尺寸標注:1)尺寸標注在最顯要位置,直觀,不封閉;2)重要﹑關鍵尺寸直截了当標注,不能有累積公差;3)尺寸公差大小應綜合考慮功能及制造本钞票,并非越小越好,体現“該精就精,該粗就粗〞一般經濟公差為:下料±0.03,成形±0.05,角度±°4)重要及關鍵尺寸應綜合考慮制程穩定性、裝配、使用功能并非多益善.5)設計基准,制造基准,測量基准相統一;2.形位公差:1)基准(面或線)不應有變形2)標注應清晰明確,方便量測;3)設計基准,制造基准,測量基准相統一;4)應綜合考慮制程穩定性及使用要求,并非多多益善,精度一般可達到0.10;5)特不穩定的尺寸,如下料尺寸等能够不標.3.結構設計及強度要求1)材料選用滿足使用要求,又方便采購的原料;2)零件外形園角,防止滾鍍外表刮傷;3)零件應有足夠的強度及剛性,防止在貯存,電鍍、搬運過程中的變形及尺寸變異;4)特别零件,可采纳多種工序組合方式,如多軸成形加工.五金模具+治具等不同方式來完成;5)連續料帶要求:A)Carrier應有足夠的強度及剛性B)盡量采纳雙側CarrierC)注重包裝時Carrier及零件是否變形D)連續電鍍的孔徑、孔距特别要求4.五金零件加工工藝:1)衝裁A)斷面質量、光亮面比例大小B)毛刺大小(一般不超過0.05)及方向,對外觀、功能的影響C)倒刺結構,不允許有園角D)盡量防止長懸臂或長槽2)彎曲曲折折曲曲折折折折曲曲折折曲曲折折折折折折A)最小彎曲曲折折曲曲折折折折曲曲折折曲曲折折折折折折半徑B)外側龜裂的影響C)彎起高度應大于2t,如圖4-4D)孔邊距離應大于t,如圖4-5,也可采纳如圖4-6所示工藝F)材料方向性對使用性能的影響3)抽引A)形狀盡量簡單對稱B)R角不應太小,一般可達R0.30,如圖4-7C)內外尺寸不可同時標注D)外表模痕不應有苛刻要求E)第八章工程圖面作業標准第二節五金模具一.五金模具開發流程,見表8-1二.五金模具裝配圖(圖8-1)三.模具圖面常見符號含義M,MC――銑SP――――基准點H―――熱處理TYP――――典型尺寸ELE――鍍鉻RP――――圓弧點DYE――染黑CEN,CL――中心線G―――磨TAN――――切點PG―――光學曲曲折折曲曲折折折折曲曲折折曲曲折折折折折折線磨THR――――穿孔JG―――座標磨BOTT―――底面W/C,W――線割TOP――――頂面E,EDM――放電SYM――――對稱L――――車T―――――厚度INT―――交點CB――――沉孔C――――倒角CLEAR―――間隙四.典型零件排樣1.H OOK類,見圖8-22.抽引類,見圖8-33.外殼類,見圖8-4。
模具倒角设计规范
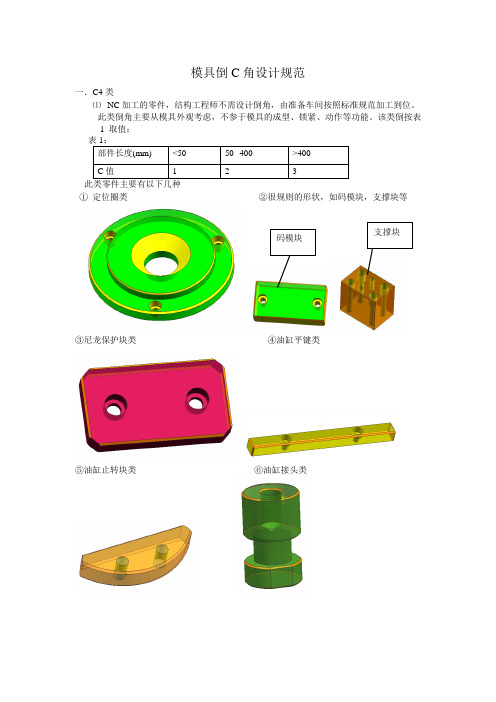
模具倒C 角设计规范一.C4类⑴ NC 加工的零件,结构工程师不需设计倒角,由准备车间按照标准规范加工到位。
此类倒角主要从模具外观考虑,不参于模具的成型、锁紧、动作等功能。
该类倒按表1 取值: 表1:部件长度(mm) <50 50--400 >400C 值123此类零件主要有以下几种① 定位圈类 ②很规则的形状,如码模块,支撑块等③尼龙保护块类 ④油缸平键类⑤油缸止转块类 ⑥油缸接头类码模块支撑块⑦U型块类⑧行程开关垫板类⑨行程开关撞块类⑩压线板类11.支撑柱类12.方导柱类13.集水器类14.插穿保护块类15.非标的耐磨板,承压板等16.锁模片类17.特制螺钉18.导套压板类19.推板导套压板类20.吊模块21.导滑块类22.垫片/压板类备注:工程师设计的倒角大小符合表1中所述的尺寸,工程师就不需要在图形上设计倒角,准备车间按照表1取值倒角。
如果有特殊情况不符合,工程师需要在3D图形上设计倒角,零件图上明确标准。
⑵有一部分需NC加工的C4类零件,工程师需要在3D图形上设计上,NC按照3D图形加工到位。
此类零件主要有以下几种1.形状比较复杂,小圆台,斜面准备无法加工的,如下图所示⑶.需要线割的零件,工程师需要在3D图形上设计上,线割完成后,转入准备车间,由准备工序加工倒角。
如方斜顶、小镶块排料等。
备注:如果工程师设计的倒角符合符合上面的标准二.模板类⑴.标准件建腔的,用lem软件都能检测到,研究所按照http://192.168.63.10:8880/jiedian/PTA030.htm将标准件建腔体更新到位,工程师直接用标准件建腔即可。
工程师发图之前,必须用lem软件检测一遍,所有网站上标准的型孔lem软件必须识别。
⑵.非标准建腔的,工程师需要在3D图形上设计上,NC按照3D图形加工到位。
1.各模板外凌边、孔必须倒角,倒角尺寸要一致,根据模架大小,以1.5*45°~3*45°为宜。
模具设计分模拨模表

PF铝合金
产品骨位加强筋
5mm内做单边不小于3.5-5°拨模
5-10mm内做单边不小于3°拨模
10mm以上做单边不小于2.5°拨模
产品外型及内部
5mm内做单边不小于4°拨模
5-10mm内做单边不小于3.5°拨模
10mm以上做单边不小于3°拨模
≥3.0
产品为表面抛光
30mm内做单边不小于1°拨模
50mm内做单边不小于1.5°拨模
大于50mm内做单边不小于2°拨模
产品外表面蚀纹
20mm内做单边不小于2°拨模
20mm以上做单边不小于2.5°拨模
ABS
产品骨位加强筋
5mm内做单边不小于1°拨模,大头≤1.0
PA
5-10mm做0.5-1°拨模,大头≤1.0
请注意甄别内容中的联系方式诱导购买等信息谨防诈骗
模具设计分模拨模表
模具设计分模拨模表
材料
对应胶厚
PP
产品骨位加强筋
1-10mm
单边做0.5-1°拨模,骨位部大头≤1.0
≥2.0
10-30mm
大头1.0,小头0.8
≥2.3
30-50mm
大头1.2,小头0.8
≥2.8
50-70mm
大头1.3,小头0.8
PC
10-30mm做保证骨位根部1.2,小头为0.9
AS
30-50mm做大头1.4,小头为0.9
PMMA
50-70mm做大头1.5,小头为0.9
POM
产品为表面抛光
30mm内做单边不小于1°拨模
PPS
50mm内做单边不小于1.5°拨模
大于50mm内做单边不小于2°拨模
模具设计标准
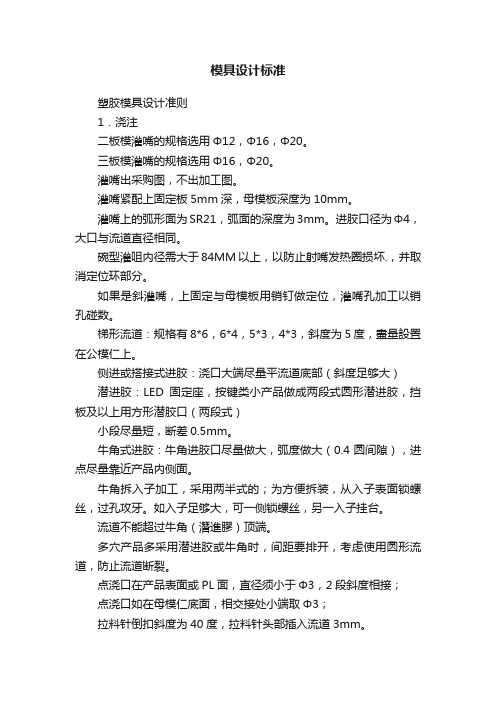
模具设计标准塑胶模具设计准则1.浇注二板模灌嘴的规格选用Φ12,Φ16,Φ20。
三板模灌嘴的规格选用Φ16,Φ20。
灌嘴出采购图,不出加工图。
灌嘴紧配上固定板5mm深,母模板深度为10mm。
灌嘴上的弧形面为SR21,弧面的深度为3mm。
进胶口径为Φ4,大口与流道直径相同。
碗型灌咀内径需大于84MM以上,以防止射嘴发热圈损坏.,并取消定位环部分。
如果是斜灌嘴,上固定与母模板用销钉做定位,灌嘴孔加工以销孔碰数。
梯形流道:规格有8*6,6*4,5*3,4*3,斜度为5度,盡量設置在公模仁上。
侧进或搭接式进胶:浇口大端尽量平流道底部(斜度足够大)潜进胶:LED固定座,按键类小产品做成两段式圆形潜进胶,挡板及以上用方形潜胶口(两段式)小段尽量短,断差0.5mm。
牛角式进胶:牛角进胶口尽量做大,弧度做大(0.4圆间隙),进点尽量靠近产品内侧面。
牛角拆入子加工,采用两半式的;为方便拆装,从入子表面锁螺丝,过孔攻牙。
如入子足够大,可一侧锁螺丝,另一入子挂台。
流道不能超过牛角(潛進膠)顶端。
多穴产品多采用潜进胶或牛角时,间距要排开,考虑使用圆形流道,防止流道断裂。
点浇口在产品表面或PL面,直径须小于Φ3,2段斜度相接;点浇口如在母模仁底面,相交接处小端取Φ3;拉料针倒扣斜度为40度,拉料针头部插入流道3mm。
三板模灌嘴倒扣全周,正面設計塑膠料厚2mm,以減少冷卻時間二板模主流道,三板模分流道入水正下方必須設置頂針(拉料頭)二.冷却模仁上水路为Φ6和Φ8的水牙为PT1/8,Φ10的水牙为PT1/4,模板上水牙为PT1/4,做Φ30*25的水路沉头孔。
常用防水圈规格为Φ14,Φ16,Φ18 ,Φ20,厚度3.0mm,防水圈槽的深度为 2.3mm,薄铁须保留。
6*8.5*16- Φ14*3,8*10.5*18- Φ16*3,10*12.5*20- Φ18*3水路尽量从非操作侧进出,数量尽量取偶数。
成型面较高的水路加隔水板,底部由机加工用铜堵(高>12mm),或底部用防水圈。
六面体的加工&磨床的加工原理&段差和槽的加工&斜度的加工&R角的加工方法

俯視 工件
5.找出三塊比工件寬度略矮的擋塊來,打干凈毛 邊呈這樣裝上磁盤如圖(1),並把工件夾好. 如圖所示
砂輪 見光 面
木槌敲擊方向
因為只夾寬度直角,所以我們敲擋塊時只敲 一個方向就好了(A)擋塊只是起到阻止工件向前 移動的作用,敲時用手扶A.B 及工件 6.為了得到良好的直角,我們的擋塊必須把工件牢 牢的夾住,下少量的料見光工件頂面,如果下的 料過多,在最后一定要好好的敲一敲擋塊.
2.鋼材特性: 硬度高,熱間硬度佳,耐磨性佳. 3.硬度: 65-69 HRC
4,火花特征:顏色暗紅,火花細且短. 5.用途: 要求高耐性的電子連續沖模,精密下料,深抽模.
材料簡介
七:G5
屬中粒碳化鎢,比重為14.2g/cm3硬度為87.5HRA,抗折
力為300kgf/mm2壓縮強度為430kgf/cm3,主要用于深抽
六面體的加工過程:
砂輪見 光面
敲時注意: 敲D擋塊 時一定要 用手頂住 B擋塊
手頂住 方向
敲擊方 向
10.寬度修好以后就修高度,先找出四塊比工件高 略矮的擋塊,擦凈油,打凈毛刺成圖(1)狀把工件夾 B D C. 好,放擋塊的順序為A 工件 B C D,敲時用手挾 敲的順序為工件 著A,B及工件.敲的力度及方向尤其注意.
六面體的加工過程:
7.把夾過的面作為底面去檢查直角,好就繼續,不 好就重復. 如圖所示
8.以寬度直角好的面為底面,把寬度尺寸磨到 20.01,然后用高度器測量工件實際寬度的平行, 平面度. 如圖所示
工件 俯視
9.再以直角好的寬度面為底面,把工件寬度剩余 的料磨到要求尺寸,再次裝上平台前一定要擦凈 工件,打凈毛刺.
4.火花特征: 研磨時火花黃色且明亮,火花形狀是頭大 尾小呈流星狀.
模具设计资料(全面最详细)

实用文档
)零件加工图表:)标准件表:
分型面注意点1
其它加工方法的问题点:
放电:速度慢,要做电极,且做自然不易排气,难成形.
在凸模或滑块等成型零件上,当部分形状异常高出其它面时,或者不利于加工时,可以拆镶件来节省备料,降低加工成本.
面的部分若不拆镶件那凸模备料多出一大截,而且加工也费时,成本将
拆镶件时无论是帖拆或通拆,在转角处要求设计尽可能大的R 角。
设计R角有两个目的:,防止模具由于应力集中出现开裂,尤其是硬模。
“A”尺寸要有足够的变形长度“B”尺寸要有比蕉型部分的长度更长,放水口弹偏无法完全定出。
- 1、下载文档前请自行甄别文档内容的完整性,平台不提供额外的编辑、内容补充、找答案等附加服务。
- 2、"仅部分预览"的文档,不可在线预览部分如存在完整性等问题,可反馈申请退款(可完整预览的文档不适用该条件!)。
- 3、如文档侵犯您的权益,请联系客服反馈,我们会尽快为您处理(人工客服工作时间:9:00-18:30)。
电话:0769-81503088 85091165 传真:0769-81503098
R角
标准加工深度
极限加工深度<预硬>
0.31
0.41
0.526
158
1.5820
21530
32030
42540
54060
65070
86080
1370100
1570120
17.5100150
25150
150
极限加工深度<热处理>
东 莞 市 崧 野 精 密 模 具 有 限 公 司
SONYE(DONG GUAN) PRECISION MOLD CO.,LTD
55
60
60
80
100
4
40
地址:东莞市长安镇沙头<咸西>东方科技园D栋 电子邮件:sonyemold@sonyemold.com
CNC R角深度加工表
6
15
25
30