耐火材料生产工艺
耐火材料工艺学 氧化镁-氧化钙系耐火材料

3)MF在MA中的溶解度较在方镁石中的溶解度大 得多,因此MA能从方镁石中转移MF从而消除了 MF因温度波动引起的向方镁石中溶解或自其内部 析出的作用,从而提高方镁石的塑性,消除对热 震稳定性的不良影响; 4)MA与FeO反应可生成含有氧化铁的尖晶石; 5)尖晶石的熔点为2135℃,且与方镁石形成二元 系的始熔温度较高(1995℃),因而以MA作结合 物的制品的耐火度和荷重变形温度较高。
广泛采用的稳定剂有CaO、MgO及其混合物,其中 CaO较有效,MgO次之。 CaO加入量通常为3~8%或更多 (按质量计)。
31
ZrO2—MgO 系 的 立 方 固 溶 体 在 长 时 间 加 热 处 理 (1000 ~ 1400℃)后会发生分解,导致制品破坏。ZrO2—CaO系立方 固溶体虽较稳定,但长时间加热时亦会发生部分分解,而 使ZrO2失去稳定作用。ZrO2—Y2O3固溶体与其它ZrO2固溶 体相比最主要优点是在1100~1400℃长时间加热不发生分 解,但这类氧化物稀缺,价格昂贵,只能局限于某些特殊 要 求 的 地 方 使 用 。 多 种 复 合 稳 定 剂 , 如 ZrO2—MgO 和 ZrO2—CaO固溶体中加入1~2%Y2O3即可显著提高其热震 稳定性。加入3~5%Y2O3可以使固溶体完全不分解,而且 有很高的机械强度和较低的热膨胀系数。
27
锆英石是ZrO2—SiO2二 元系中唯一的化合物(图71)。它在1676℃分解并在 1687℃ 异 成 分 熔 化 , 纯 ZrSiO4 耐 火 度 在 2000℃ 以 上,随杂质含量增加,耐 火度亦相应降低。
28
第二节 氧化锆制品
一、原料的制取和稳定
氧化锆在地壳中的含量约占0.026%,分布极为分散。在自 然界中主要有两种含锆矿石。
耐火材料浇注料配方工艺
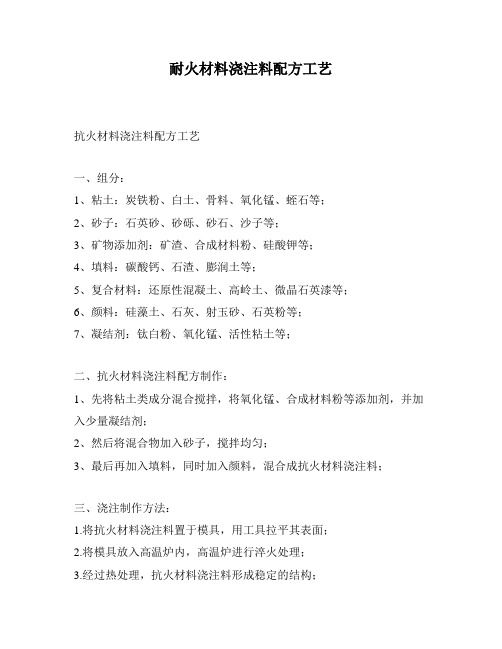
耐火材料浇注料配方工艺
抗火材料浇注料配方工艺
一、组分:
1、粘土:炭铁粉、白土、骨料、氧化锰、蛭石等;
2、砂子:石英砂、砂砾、砂石、沙子等;
3、矿物添加剂:矿渣、合成材料粉、硅酸钾等;
4、填料:碳酸钙、石渣、膨润土等;
5、复合材料:还原性混凝土、高岭土、微晶石英漆等;
6、颜料:硅藻土、石灰、射玉砂、石英粉等;
7、凝结剂:钛白粉、氧化锰、活性粘土等;
二、抗火材料浇注料配方制作:
1、先将粘土类成分混合搅拌,将氧化锰、合成材料粉等添加剂,并加入少量凝结剂;
2、然后将混合物加入砂子,搅拌均匀;
3、最后再加入填料,同时加入颜料,混合成抗火材料浇注料;
三、浇注制作方法:
1.将抗火材料浇注料置于模具,用工具拉平其表面;
2.将模具放入高温炉内,高温炉进行淬火处理;
3.经过热处理,抗火材料浇注料形成稳定的结构;
4.取出后,抗火材料浇注料即可使用。
四、注意事项:
1.在抗火材料浇注料的制作过程中,湿度和温度都要控制在一定范围内,以保证配方的准确性;
2.热处理的温度和时间也要控制,防止材料超过终点温度,使浇注料受损;
3.抗火材料浇注料一旦成型,就不能随意更改。
否则会影响其性能和使用寿命。
碳酸镁的生产工艺

碳酸镁的生产工艺
碳酸镁是一种化学物质,化学式为MgCO3,是一种白色结晶
体粉末。
碳酸镁广泛用于制造耐火材料、陶瓷、肥料、化妆品等领域。
下面将介绍碳酸镁的生产工艺。
碳酸镁的生产可以通过多种工艺实现,下面以溶液法为例进行阐述。
首先,将矿石(如菱镁矿)破碎并磨成粉末,目的是提高碳酸镁的产率。
然后,将粉末与稀硫酸混合,在搅拌的同时加热,使反应加速。
反应方程式为:MgCO3 + H2SO4 → MgSO4 + CO2↑ + H2O。
当硫酸和镁碳酸反应完全后,产生的镁硫酸溶液通过过滤得到,滤渣是未反应的杂质和冶炼出的镁硫酸。
滤液的pH值较低,
需要进行中和处理。
可通过加入饱和碳酸氢钠溶液,使滤液中的镁离子与氢氧根结合,形成沉淀。
方程式为:MgSO4 +
2NaHCO3 → MgCO3 + Na2SO4 + CO2↑ + H2O。
沉淀可以利用旋流分离机进行分离。
沉淀物为碳酸镁。
此时的碳酸镁含有一定的杂质,为了提高纯度,还需要进行洗涤。
通常会使用稀盐酸进行洗涤,以去除杂质,然后再进行过滤分离。
洗涤后的碳酸镁经过干燥,得到成品。
总结起来,碳酸镁的生产工艺主要包括矿石破碎、与稀硫酸反应、滤液中和、沉淀分离、洗涤和干燥等步骤。
这些步骤可以
保证碳酸镁的纯度和质量。
随着工艺的不断改进和技术的提高,碳酸镁的生产工艺也在不断完善,以提高生产效率和降低成本。
耐火材料球磨机的工艺流程

耐火材料球磨机的工艺流程1.首先,将原材料进行粉碎,以便提高后续球磨的效果。
First, crush the raw materials to improve the grinding effect.2.然后将粉碎后的原材料进行混合,以保证成分均匀。
Then mix the crushed raw materials to ensure uniform composition.3.接下来,将混合后的原料送入球磨机中进行混合和研磨。
Next, feed the mixed raw materials into the ball mill for mixing and grinding.4.球磨机在高速旋转的情况下,将原料进行连续的研磨和混合。
The ball mill continuously grinds and mixes the raw materials under high-speed rotation.5.球磨过程中需要加入适量的水和其他添加剂,以提高材料的粘合性和流动性。
During the grinding process, it is necessary to add an appropriate amount of water and other additives to improvethe bonding and flow properties of the materials.6.经过一定时间的球磨,原料逐渐变成了细小的颗粒状物料。
After a certain period of grinding, the raw materials gradually become fine granular materials.7.最后,将球磨后的物料进行干燥,以保证其水分含量符合要求。
Finally, dry the ground materials to ensure that their moisture content meets the requirements.8.经过干燥处理后的物料即成为成品的耐火材料,可用于各种高温工业领域。
耐火材料工艺学(PPT 39页)
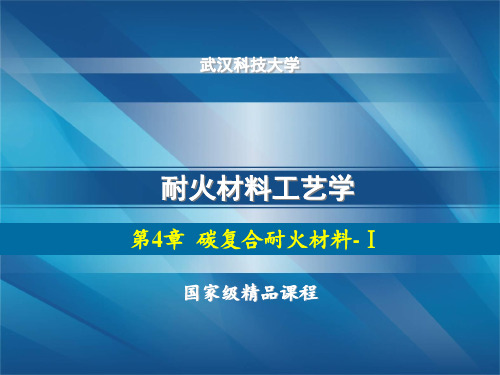
(4) “碳”与“炭”的区别
002
004
101
三维结构
“碳”是一种元素,符号为C。 “炭” 是碳,且以无定形碳为主
100
102
103
006
112 110
104
105
的人造物质(artifact, non-natural )。 10 20 30 40 50 60 70 80 90 100
炭的化学成分主要是碳,且其中
Al2O3-SiC-C Al2O3-SiC-C Al2O3-SiC-C
高炉出铁口用
Al2O3-SiC-C炮泥 Al2O3-SiC-C铁沟浇注料
高炉出铁口组成 渣沟
主沟
沟盖 出铁口
铁沟 摆动流槽
Al2O3-SiC-C质炮泥 高炉出铁口
Ironmaking——torpedo ladle(鱼雷罐)
炼铁——鱼雷罐(运送铁水、铁水预处理脱P,S)
与炉渣亲和性润湿性好、脆性材料、热导率小
抗渣性与热震稳定性差
铁水的预处理 顶吹、顶底复吹、超高功率电炉 炉外精炼、连铸比的不断提高。 要求耐火材料使用寿命(service life)要高。
新的冶炼技术的需要
上个世纪80年代初至80年代末的二伊战争 石油危机
重油紧缺----如何节能降耗? 能源危机的需要
➢ 考虑材料的致密度。满足前述条件下,尽量选择体积 密度小的材料,以减少蓄热增强体温。
➢ 在用作电炉内衬时,还需考虑其导电性。 耐火材料的性能必须要满足生产要求,在此基础上, 考虑其经济要求,尽量使生产成本最低。
4.1 碳复合耐火材料发展概况(背景、历程和地位) (1)背景
传氧统化耐物火为材主料:MgO、Al2O3 、MA、A3S2…… 特点:离子晶体、熔点高、储量丰富
耐火材料现有原料加工工艺的优化和改进

耐火材料现有原材料加工工艺的优化和改进在现有原材料的基础上对生产工艺进行优化和改进,或选择全新的生产工艺,从而使原材料具有改进的特性或低的成本。
近期这方面的进展较多,下面从工艺角度,包括改进生产工艺、添加生产工序和采纳全新生产工艺等方面分别予以简单介绍。
1改进生产工艺工艺改进是在原材料现有工艺基础上,通过调整工艺参数、添加外加剂等,使原材料具有特别的性能或性能更为稳定。
这方面的例子有:1.1具有增塑性的煅烧氧化铝在传统的喷补料中,通常加入含SiO2的物质如硅灰和软质粘土等(称之为增塑剂)来改善喷补料的流变性,从而加添喷补料的粘性和削减物料反弹。
当采纳铝酸盐水泥作为结合剂时,加入含SiO2的增塑剂由于低熔物相的形成会降低材料的高温性能,从而降低喷补料的使用寿命。
某厂家的CT10SG型煅烧氧化铝是一种可以取代硅灰和软质粘土的新型增塑剂,它具有高的比表面积(13m/g),d50为3m,并且具有独特的保水性能,可以加添喷补料的粘性。
1.2易施工活性氧化铝刚玉和尖晶石基高性能高纯泵送浇注料的关键技术问题是在低加水量的情况下具有可泵送本领。
但一般刚玉和尖晶石质高纯浇注料在不含硅微粉时,浇注料的剪切应力过大,有时还存在严重的胀性现象,使得浇注料的加水混合和泵送变得困难。
虽然二氧化硅微粉的加入可使浇注料获得理想的流变性(较低的屈服应力和塑性粘度),可以实现泵送,但它将降低高温下的热机械性能和抗侵蚀性。
国外某公司开发了新型氧化铝微粉,使得浇注料在双活塞泵的极大压力下也能表现出适合的流变行为。
1.3抗老化铝酸盐水泥“老化”是浇注料干混料在保存期间,水泥、浇注料原材料以及保存环境氛围之间相互作用,对水泥反应以及浇注料性能影响的通称。
老化导致浇注料施工性能变化,如硬化和脱模时间延长。
依据铝酸盐水泥老化机理的讨论,某水泥厂家在原铝酸钙水泥的基础上开发了新型铝酸钙水泥。
这种新的水泥基本性能同原铝酸钙水泥相当,但能够有效防范老化,为低水泥浇注料供给一个稳定的施工性能,延长浇注料的保存期。
烧结致密刚玉生产工艺

烧结致密刚玉生产工艺烧结致密刚玉是一种优质的耐火材料,广泛应用于高温炉窑、耐火衬里、切割工具等领域。
它具有高硬度、高强度、耐磨损、耐酸碱腐蚀等优良特性,因此其生产工艺也颇为复杂。
下面介绍一种常见的烧结致密刚玉生产工艺:首先,制备原料。
烧结致密刚玉的主要成分是高纯度的氧化铝粉末。
这些粉末需要通过高温处理来消除其不纯物质,并通过粉碎等工艺获得适当的颗粒大小。
其次,混合原料。
将前一步制备好的氧化铝粉末与其他辅助材料混合均匀,辅助材料通常包括增加致密性和耐火性能的添加剂。
混合的过程可以使用球磨机等设备进行,以确保混合均匀度。
接下来,成型。
将混合好的原料放入成型模具中,常见的成型方式有压制和注射成型。
压制成型中,将原料放入模具中,施加较高的压力使其变形成型;注射成型则是将原料糊状注入模具中,等其固化后取出。
然后,干燥处理。
成型后的刚玉坯体需要进行干燥处理,以去除其内部的水分。
一般会将刚玉坯体放入干燥设备中,在适当的时间和温度条件下进行干燥处理,确保坯体完全干燥。
接着,烧结处理。
将干燥处理后的刚玉坯体放入烧结炉中进行烧结处理。
烧结的目的是使刚玉坯体内的颗粒之间发生结合,从而形成致密的坚固结构。
烧结温度和时间的控制对最终产品的质量至关重要。
最后,进行后处理。
烧结致密刚玉在烧结后需要进行一系列的后处理工艺,包括抛光、加工成形、研磨等过程,以获得最终的产品形态和表面光洁度。
这些后处理工艺会对产品的精度和质量产生直接的影响。
以上就是烧结致密刚玉的生产工艺简要介绍。
当然,实际的生产过程中还有很多细节和注意事项需要考虑,以确保产品的质量和性能。
随着技术的不断进步,烧结致密刚玉的生产工艺也在不断改进和优化,以满足不同领域的需求。
陶粒的生产工艺

陶粒的生产工艺陶粒是一种轻质多孔的耐火材料,由于其独特的性能,在建筑、冶金、化工、农业等领域得到广泛应用。
陶粒的生产工艺主要包括原料配比、成型、烧结和制粒等环节。
下面将详细介绍陶粒的生产工艺。
首先是原料配比。
陶粒的原料主要包括膨胀高岭土、膨胀石英、膨胀蛭石等,它们具有较高的熔点和耐火性能。
原料配比的目的是确定各个成分的比例,以保证陶粒具有良好的物理性能和化学稳定性。
配料时需要将原料进行粉碎和筛选,以确保颗粒大小的均匀性,为后续成型提供良好的条件。
接下来是成型。
成型可以采用干压成型和湿法成型两种方式。
干压成型是将粉状原料加入模具中,通过压力使其变形成型。
湿法成型是将原料与适量的水混合,形成泥状物质后进行成型。
湿法成型的方法多样,包括滚筒成型、喷射成型、挤出成型等。
不同成型方法的选择取决于陶粒的用途和生产要求。
然后是烧结。
烧结是将成型后的陶粒在高温下进行加热,使其发生化学变化和物理结构的改变。
烧结温度和时间的选择对陶粒的性能有较大的影响。
一般情况下,烧结温度较高、时间较长,可以得到较高的烧结度和较好的力学性能。
烧结过程中还要控制气氛的氧化性,以避免陶粒表面的氧化。
最后是制粒。
制粒是为了提高陶粒的粒度分布和形状均匀性。
制粒一般采用颗粒机进行,将烧结后的陶粒进行粉碎、筛分和石英砂的混合,制成符合要求的颗粒。
制粒过程中需要控制破碎机的破碎度和破碎时间,以保证制得的陶粒质量。
以上就是陶粒的生产工艺,其中每个环节都需要精确控制和严格操作,以确保陶粒具有较好的物理性能和化学稳定性。
随着科学技术的发展,陶粒的生产工艺将会不断改进和完善,以适应不同的需求和应用领域的发展。
- 1、下载文档前请自行甄别文档内容的完整性,平台不提供额外的编辑、内容补充、找答案等附加服务。
- 2、"仅部分预览"的文档,不可在线预览部分如存在完整性等问题,可反馈申请退款(可完整预览的文档不适用该条件!)。
- 3、如文档侵犯您的权益,请联系客服反馈,我们会尽快为您处理(人工客服工作时间:9:00-18:30)。
混练设备
混练机
困料
作用
使结合粘土进一步分散,从而使其与水分分布更均匀, 发挥其可塑性能与结合性能,以改善泥料的成型性能
1对粘土砖的作用
氧化钙在泥料中充分消化,避免CaO水化
2钙含量高的镁砖泥料
去除料内因化学反应产生的气体
2.泥浆注入石膏模中,石膏吸收水分,并在其 表面集结成水分较少的泥料膜
半干法成型坯体密实程度
1.泥料性质2.压制压力 3.增压速度 4.加压时间
有触变性的泥料 1.成型易水化的物料如焦油白云石和焦
油镁砂料
2.浇注料
压力机
干燥
干燥:提高坯体的机械强度,有利于装窑操作并保证
烧成初期能够顺利进行
过程
1.结合粘土的干燥 2.熟料的干燥
原料的煅烧
1.形成熟料:密度高,强度大,体积稳定性好, 具有良好的物理-化学性能和外形质量,从而 保证耐材制品的外形尺寸
2.煅烧的天然矿石有粘土、高铝矾土、菱镁矿 和白云石等
3.不煅烧的天然矿物有硅石、叶蜡石等 4.煅烧温度Ts约为其熔点的0.7~0.9倍,多高 于制品的烧成温度,更高于制品的使用温度。
从最高烧成温度至室温的冷却过程中, 主要发生耐火相的析晶、某些晶相的 晶型转变、玻璃相的固化等过程,在 此过程中坯体的强度、密度、体积依 品种不同都有相应的变化
坯体中各种反应趋于完全、充分、液 相数量继续增加,结晶相进一步成长 而达到致密化
烧结过程的宏观结构变化及其影响因素
宏观结构变化
坯体的烧结可以概括为三个阶段1.热态接触:物料内部各组分质点间的接触增加,但仍 保留其边界2.开始阶段:质点间的边界被打开,但新的气孔尚未形成3.形成封闭气孔阶
5.烧结方法有机械活化烧结、轻烧活化、二步 煅烧和直接死烧等
原料的破粉碎和筛分
原料的破碎 1.目的 2.设备
原料的粉碎 1.目的 2.两种方法的区别 3.设备
原料的筛分 1.目的 2.设备
湿法多用于陶瓷及特种耐火材料生产, 其优点为:1.粉碎粒度小2.粉碎效率高, 不易产生干粉料的粉料凝聚现象
3磷酸或硫酸铝作胶结剂的耐火混凝土
缺点
1.条件要严格控制 2.过高或时间过长时,生产的胶体老化,水分散失 3.时间长,占用场地面积大
目前状况
1.耐材生产技术水平的发展提高 (高压力液压机)
2.原料质量提高
成型
成型
耐火坯料借助于外力和模型,成为具有一定尺寸、形状和强 度的坯体或制品的过程
方法:
1.半干法 2.可塑法
颗粒组成容积:带式、板式、槽式、圆盘式、螺旋式、振动给料机 1.临界颗粒的确定 (硅质,镁质,砖及浇注料) 2.颗粒配比 a.连续颗粒的调整 b.不连续颗粒的调整. c颗粒对制品性能的影响
热震稳定性好:可适当提高颗粒部分数量和临界粒度 致密性和抗渣性好:提高颗粒部分数量,降低临界粒度 提高烧结能力,提高制品的密度:降低临界粒度,提高细粉
3.有利于制品的生产
它聚集晶界,阻止烧结
还原气氛下火焰长,温度均匀,有利于均匀缓和地加热制 品,缓和高温下强氧化焰对制品有冲击的不利作用
对不同制品的要求
干燥方式
粘土砖在隧道窑烧成时,残 余水分应低于2~3%,在其
1.间歇式室式 2.隧道式
他窑烧成应低于4~5%。硅
砖烧成前要求干燥到1 ~ 2
其送风和排气温度分别为:粘土制品 120 ~ % ,镁砖0.6 ~ 1.0%
200℃,30~90℃;硅质制品80~120℃,50
~ 80℃;镁质制品110~130℃,50~70℃。
3.设备及研磨体摩擦损失小 4.防尘好
泥料的配料
泥料(砖料)的定义: 配料组成
按一定比例配合的各种原料(含粉 料),在混练机混练过程中加入水或 其它结合剂而制得的混合料
配料方法
1.化学组成:主成分,易熔杂质总量和有害杂质量的规定 2.颗粒配比3.常温结合剂4.原料中水分和灼减的换算
重量:磅秤、自动称量称、称量车、电子称、光电数字显示称
烧 成窑
窑
推板窑
烧成过程中的物理化学变化
烧成过程中的物理化学变化是确定制品烧成热工 制度的重要依据,分三个阶段
加热阶段(室温~最高烧成温度)
1.排出自由水和大气吸附水2.坯体中形成气
⑴排水阶段(室温~200℃)
孔,具有透气性,有利用下一阶段反应
⑵分解氧化阶段 (200物 燃烧等3.晶型转变及少量低熔液相的形成4.质量
烧成制度的确定
最高烧成温度和保温时间 升温和冷却速度 烧成气氛
1.保证某些物理化学过程的实现
碳砖还原气氛;去掉有机杂质 氧化气氛
2.有利于烧结反应的进行 1.硅砖(>1000℃),还原性气氛使制品烧成较为缓和,
形成足够的液相,有利于鳞石英形成2.镁砖应在弱氧化
气氛下进行,氧化性强,则Fe2O3增加,形成铁酸镁,
段:随着温度和时间的变化,物料收缩,气孔率下降,体积密度增大,这一系列变化 是一个渐变过程;完成此过程的两个必要条件是温度和时间
烧结过程影响因素
1.液相和重结晶作用 2.固相反应
3.再结晶和聚集再结晶
1.液相能填充空隙,可使颗粒靠近,从而提高致密度2.细小结 构的不完整晶体不断溶解,而结构完整的晶体不断从液相中 析出,并且不断地逐渐长大,这个过程叫重结晶过程3.液相 中成分少些,重结晶能力就大些4.降低粘度和提高温度有利 于烧结和加速重结晶作用
⑶液相形成和耐火相合成阶段( >1减0轻0,0气孔℃增加),强度也有较大变化
烧结阶段 冷却阶段
1.分解作用将继续完成2.随温度升高,液相量增加,液相粘度 降低,某些新耐火物相开始形成,并进行熔融重结晶3.由于液 相的扩散、流动、溶解沉析过程的进行,颗粒在液相表面张力
的作用下,进一步靠拢而促使坯体致密化,强度增加,体积缩 小,气孔率降低,烧结急剧进行
晶体的内部和表面缺陷,促使晶体很不稳定,表面活性大,
其力图降低表面活性,以处于稳定状态,在高温作用下,如
烧结主要是由于晶体长大果这,种作用在同一晶体内部进行,则能够消除组成晶格质点 的空位,校正晶体的缺陷;若在晶粒间接触面进行,则使接
新晶体形成和长大,以及液触面逐渐扩大,达到晶粒的聚集和结合。
相形成、充填空隙、粘结晶体,从而促使烧结
耐火材料生产工艺
耐火材料一般生产工艺
原料加工 配料 混练 成型 干燥 烧成 检验 成品入库
原料的选矿
✓ 颗粒粒度 ✓ 颗粒形状 ✓ 颗粒密度 ✓ 浮选法(矿物被液态润湿程度) ✓ 重液选矿法 ✓ 静电选矿 ✓ 磁力选矿法 ✓ 电渗选矿法 ✓ 化学方法选矿法 ✓ 生物选矿法
原料干燥与煅烧
原料干燥
烧成
烧成设备 1.倒焰窑 2.隧道窑 3.推板窑 4.梭式窑等
烧成工序 1.装窑 2.烧成制度
间歇式,热效率低,生产能力低,劳动 强度大,操作条件差,周转时间长
连续式,自动化、机械化程度高, 生产能力较大,热效率较高
1. 烧成的最高温度 2. 各阶段的升温速度 3.在各阶段中窑内的气氛性质 4.在最高温 度下的保温时间5.制品冷却时的降温速度
仅在坯体表面上,干燥速度等于自由水面的蒸发速 度,与坯体厚度及最初含水量无关,只与干燥介质
1.等速干燥阶段 (空气)的温度、湿度、及运动速度有关
2.降速干燥阶段
水分从表面蒸发的速度超过自坯体内部向表面扩散的速度, V取决于含水量、内部结构、水的粘度、物料性质等
3.低速及平衡干燥阶段
干燥速度趋于0,水分不再减少,此时保留 在坯体中的水分叫平衡水分
混练
混练 使不同组分和粒度的物料同的物料同适量的结合剂经混合和挤压 作用达到分布均匀和充分润湿的泥料制备过程
影响因素: 混练设备、混练时间、结合剂的选择及其加入量、
加料顺序、粉料颗粒形状
混练设备
单轴和双轴搅拌机、混砂机 (混合、搅拌) 湿碾机(混合、搅拌和挤压,更均匀)
混炼时间:如用湿碾机,粘土砖料4-10min,
1.坯体水分5%左右,多采用压砖机、捣固机成型 2.密度高、强度大、干燥和烧成收缩小、尺寸易控等特点
3.注浆法
坯体水分大概在16~25%,一般用挤泥机成型
4.振动成型 5.热压注成型 6热压成型 7.电熔注法 8.等静压成型
1.坯体水分在35~45%,生产薄壁中空制品。 如热电偶套管、高温炉管、坩埚等