耐火材料的生产工艺
耐火材料生产工艺流程

耐火材料生产工艺流程耐火材料是一种特殊的工业材料,常用于高温环境下的建筑、电力、冶金等行业。
其生产工艺流程通常包括原料选取、原料处理、成型、烧结和后处理等步骤。
下面将详细介绍耐火材料的生产工艺流程。
一、原料选取耐火材料的主要成分通常包括粘土、刚玉、膨胀珍珠岩、石英砂等。
在原料选取阶段,需要根据所需耐火材料的性能要求和使用环境的特点选择合适的原料。
二、原料处理原料处理是将选取好的原料进行破碎、筛分、配料等工序,以确保原料颗粒饱满、均匀,符合成型要求。
其中,破碎工序可以使用颚式破碎机、破碎辊等设备进行;筛分工序可以使用振动筛、鼓式筛等设备进行;配料工序则需要将各种原料按一定比例混合搅拌,通常使用混合机进行。
三、成型成型是将经过原料处理的混合材料进行加工成型,一般可分为干法成型和湿法成型两种方法。
干法成型通常采用压片机进行,湿法成型则需要在混合材料中加入一定量的水或其它成型剂以形成湿性固体原料,再通过压制成型。
常见的成型方式包括挤出成型、模压成型、注射成型等。
四、烧结烧结是将成型好的耐火材料在高温条件下进行煅烧,使其获取良好的结构和性能。
烧结的主要目的是将成型的材料中的水分、有机物和氧化物等物质热解分解,同时进行颗粒之间的结合,使其具有一定的耐火性和热稳定性。
常见的烧结方式有干式烧结和湿式烧结两种。
五、后处理经过烧结的耐火材料需要进行后处理,以提高其性能和外观质量。
常见的后处理工艺包括退火、表面涂覆、打磨、抛光等。
退火是指将烧结好的材料再次加热至一定温度并进行保温一段时间,以消除内部应力,提高材料的机械性能和耐火性能。
表面涂覆可以应用高温涂料,提高材料的耐火性能和抗腐蚀性能。
打磨和抛光可以提高材料的光洁度和外观质量,以适应不同的应用场合。
以上就是耐火材料的典型生产工艺流程。
不同种类的耐火材料在工艺流程上可能会有所差异,但总体上都包括原料选取、原料处理、成型、烧结和后处理等步骤。
通过合理控制每个步骤的工艺参数,可以生产出具有良好性能和质量的耐火材料,以满足不同领域的应用需求。
耐火材料生产工艺流程

耐火材料生产工艺流程耐火材料是一种能在高温环境下具备一定的稳定性和耐火性能的材料。
耐火材料的生产工艺流程一般分为原材料准备、原材料混合、成型、烘焙、检测和包装等几个主要步骤。
首先是原材料准备阶段。
根据耐火材料的种类和使用要求,需要准备相应的原材料。
常见的耐火材料原材料包括石英砂、高岭土、膨胀土、高岭石、氧化铝、硅酸铝等。
这些原材料需要进行筛分、研磨和干燥等处理,以保证材料的纯度和颗粒度的合理范围。
接下来是原材料混合。
将经过处理的原材料按一定比例进行混合,以获得具备所需性能的均匀混合物。
混合的方法有干混和湿混两种。
干混是将原材料直接放入混合机中搅拌,湿混是将原材料按比例加入水中,形成泥浆状,再进行搅拌。
然后是成型阶段。
混合好的原料需要进行成型,常见的成型方法有压制成型、注浆成型和浇注成型。
压制成型是将混合物放入压力机中,通过给予一定的压力来使其形成坯体。
注浆成型是将混合物转化为泥浆状,通过注入模具中,然后排除多余的水分,使其形成坯体。
浇注成型是将混合物转化为流体状,然后倒入模具中,使其在模具中形成坯体。
进入烘焙阶段后,将成型成的坯体置于高温炉中进行高温烧结。
烧结的温度和时间是根据耐火材料的种类和使用要求来确定的。
烧结的目的是使原料中的有机物和水分挥发,同时使不同组分之间发生化学反应和晶体相变,使其形成致密坚固的矿物结构。
烧结完成后,需要对产品进行检测。
常见的检测方法有外观检查、尺寸测量、物理性能测试和化学成分分析等。
通过检测可以确定产品是否达到要求,以便进行后续的包装和出厂。
最后是包装阶段。
将通过检测合格的耐火材料按一定规格包装,以便于储存和运输。
常见的包装方式有塑料袋包装、纸箱包装和托盘包装等。
总之,耐火材料的生产工艺流程包括原材料准备、原材料混合、成型、烘焙、检测和包装等几个主要步骤。
每个步骤都需要严格控制,以确保产品的质量和稳定性。
这些工艺流程可以根据具体的耐火材料的种类和使用要求进行调整和优化。
耐火材料制备工艺_
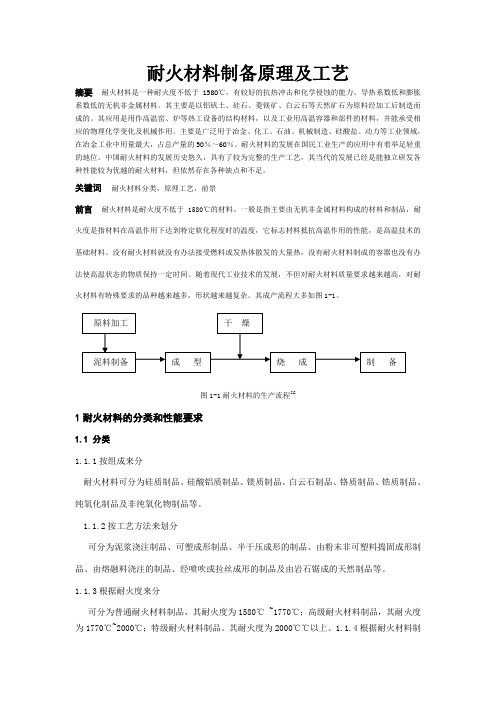
耐火材料制备原理及工艺摘要耐火材料是一种耐火度不低于1580℃,有较好的抗热冲击和化学侵蚀的能力、导热系数低和膨胀系数低的无机非金属材料。
其主要是以铝矾土、硅石、菱镁矿、白云石等天然矿石为原料经加工后制造而成的。
其应用是用作高温窑、炉等热工设备的结构材料,以及工业用高温容器和部件的材料,并能承受相应的物理化学变化及机械作用。
主要是广泛用于冶金、化工、石油、机械制造、硅酸盐、动力等工业领域,在冶金工业中用量最大,占总产量的50%~60%。
耐火材料的发展在国民工业生产的应用中有着举足轻重的地位。
中国耐火材料的发展历史悠久,具有了较为完整的生产工艺,其当代的发展已经是能独立研发各种性能较为优越的耐火材料,但依然存在各种缺点和不足。
关键词耐火材料分类,原理工艺,前景前言耐火材料是耐火度不低于1580℃的材料。
一般是指主要由无机非金属材料构成的材料和制品,耐火度是指材料在高温作用下达到特定软化程度时的温度,它标志材料抵抗高温作用的性能,是高温技术的基础材料。
没有耐火材料就没有办法接受燃料或发热体散发的大量热,没有耐火材料制成的容器也没有办法使高温状态的物质保持一定时间。
随着现代工业技术的发展,不但对耐火材料质量要求越来越高,对耐火材料有特殊要求的品种越来越多,形状越来越复杂。
其成产流程大多如图1-1。
图1-1耐火材料的生产流程[1]1耐火材料的分类和性能要求1.1分类1.1.1按组成来分耐火材料可分为硅质制品、硅酸铝质制品、镁质制品、白云石制品、铬质制品、锆质制品、纯氧化制品及非纯氧化物制品等。
1.1.2按工艺方法来划分可分为泥浆浇注制品、可塑成形制品、半干压成形的制品、由粉末非可塑料捣固成形制品、由熔融料浇注的制品、经喷吹或拉丝成形的制品及由岩石锯成的天然制品等。
1.1.3根据耐火度来分可分为普通耐火材料制品,其耐火度为1580℃ ~1770℃;高级耐火材料制品,其耐火度为1770℃~2000℃;特级耐火材料制品。
耐火材料的生产过程及过程步骤介绍

耐火材料的生产过程及过程步骤介绍耐火材料的品种和质量取决于耐火材料的原料及其生产工艺.在原料确定的情况下,耐火材料的生产工艺方法与制度是否正确与合理.对所得耐火制品的质量影响极大。
耐火材料性能的控制.必须通过特定的工艺手段来实现。
因此.耐火材料的生产者必须精子此道,使用者为能正确选用具有某一特性的耐火材料,使其物尽其用,也必须对耐火材料的生产工艺有所了解。
耐火材料的生产工艺流程。
对块状制品,一般包括如下儿个过程:原料的加工一配料一混练一成塑-干燥-烧成-拣选一成品。
原料的质量是耐火材料质觉的基本保证。
要发展优质高效的耐火制品,必须有纯净的质量均一和性质稳定的原料。
因此,选取适宜作为耐火材料原料的天然矿石,开采后必须再经过加工。
原料的加工主要包括原料的精选提纯(或均化、合由)原料的干燥和锻烧,原料的破粉碎和分级。
(1)原料的精选提纯和均化。
为了提高原料纯度.一般需经拣选或冲洗.剔除杂质:有的还需采用适当的选矿方法进行精选提纯。
原料中成分不均的需要均化。
有的在精选后还可引人适量有益加人物,高性能的复合原料需采用人工合成方法。
(2)原料的锻烧。
为了保证原料的高溢体积稳定性、化学稳定性和高强度.多数夭然原料和合成原料需经高溢锻烧制成熟料或经熔融制成熔块。
熟料缎烧溢度一般多控制在使其达到烧结致密化的范田内。
对主晶相为氧化物的原料,烧结温度Ts约为其熔点Tm的0.7-0.9倍,即Ts=(0.7-0.9)Tm,多高于制品的烧成似度,更高于制品的使用滋度。
熟料煅烧一般在竖窑或回转窑中进行。
有的原料,如软质耐火钻土作为钻合剂虽不经锻烧.但若含水过多.应经于燥,以便破碎和分级。
(3)原料的破粉碎和分级。
原料破粉碎是为了制成不同粒级的颗位及细粉,以便于调整成分,进行级配,便多组分间混合均匀,便于相互反应,并获得致密的或具有一定粒状结构的制品坯体。
一般先将颗粒破碎到极限位径40 -50mm;再将位度破碎到极限粒径4一5mm(中碎),然后细碎。
耐火材料(3)_生产工艺

定 型 带:保证坯体的光滑和质量的均匀。 挤出速率:速度过快时弹性后效易造成坯体变形
3 挤压缺陷及防止
坯料质量问题造成的缺陷:
混入气体; 湿度不均匀;塑性不好
挤压机的问题造成的缺陷 安装问题:壁厚不等 压力不稳:密度不均不光滑
4 挤压成型工艺的优缺点
Hale Waihona Puke 优点:欲知后事如何。。。 。。。
水 ,酒精,丙酮等
安全 廉价 环保
2、选择塑化剂的原则
能润湿和吸附在颗粒表面,粘合性强, 有利于成型并保证生坯强度
与粉料不发生化学反应 成型时、排除时均不反应
挥发温度宽,残留灰分少
二、挤压成型
1 挤压成型的过程
F
挤压筒
压缩段 定型带
2 挤压参数
挤制压力:与坯料的流动性和机嘴锥角大小有关。
效率高,自动化程度高,可连续生产
缺点:
机嘴结构复杂,加工精度要求高; 含有大量塑化剂,干燥时收缩大
适用:
等截面产品,大批量生产,管材、线材、片材
三、轧膜成型 四、其他塑性成型方法 车坯法,旋坯法,滚压成型等
三、耐火材料的烧结
常用烧结工艺 烧结对材料性能的影响 影响烧结的主要因素 烧结收缩变形
第三章 耐火材料的制备工艺
一、原材料及其制备 二、成型工艺 三、烧结
一、原料及其制备
一、原料种类 二、机械破碎法制备粉料 三、化学方法制备粉料 四、粉体的表征
二、耐火材料的成型
如何选择成型方法
一、干压成型 二、塑性成型 三、注浆成型
二、耐火材料的成型
耐火材料

耐火材料的生产过程生产过程中一般都要经过原料破碎、细碎、筛分、配料、混练、成型、干燥和烧成等加工工序而成。
一原料加工一、破粉碎生产耐火材料用熟料或生料的块度,尺寸大小不一,其大小是粉末状至350mm左右的大块,块状耐材原料经拣选后必须进行破粉碎,才能达到制备泥料的粒度要求。
(一)、粗碎粗碎(破碎)物料块度从350mm破碎到小于50-70mm。
粗碎通常选用不同型号的颚式破碎机。
(二)、中碎中碎(粉碎)物料块度从50-70mm粉碎到小于5-20mm。
中碎设备主要有圆锥破碎机、双辊式破碎机、冲击式破碎机、锤式破碎机等。
(三)、细碎细碎(细磨)物料粒度从5-50mm细磨哦小于0.088mm 或0.044,mm,甚至0.002mm。
细碎设备有筒磨机、雷蒙机(悬辊式磨机)、震动磨机等。
二、筛分耐火原料经破碎后,大中小颗粒混在一起。
为了得到符合规定尺寸的颗粒,需要进行筛分。
筛分是指破粉碎的物料,通过一定尺寸的筛孔,使不同粒度的原料分开的工艺过程。
目前,耐火材料生产用的筛分设备主要有震动筛和固定斜筛两种,前者筛分效率90%以上,后者70%左右。
三、粉料贮存耐火原料经过粉碎、细磨、筛分,存放在贮料仓内供配料使用。
生产中会出现贮料仓颗粒分布不均,最好将粉料分离放置。
二泥料的备置一配料将不同材质和不同粒度的物料按一定比例进行配合的工艺为配料。
配料规定的配合比例也称配方。
(一)粒度组成包括:颗粒的临界尺寸、各种大小颗粒(3-4mm)的百分含量和颗粒的形状等。
颗粒组成对胚体的致密度有很大影响。
普通耐火制品为三级配料,这类制品如普通粘土砖、高铝砖等。
耐火材料制品用泥料的颗粒组成大多采取“两头大,中间小”的粒度配比,即中粗、细颗粒多,中间颗粒少。
因此,在实际生产中,对大多数制品的粉料或泥料,只控制粗颗粒筛分(3-2mm或2-1mm)和细颗粒筛分(小于0.088mm或小于0.5mm)两部分的数量。
中、高档耐火材料制品采用多级配料,如镁碳砖、铝碳滑板砖、刚玉砖等,根据制品的性能要求配料更为细致。
耐火材料生产工艺流程
耐火材料生产工艺流程
耐火材料是一种具有高温抗热性能的材料,广泛应用于冶金、建筑、化工等领域。
以下是耐火材料生产的一般工艺流程。
首先是原料的准备。
耐火材料的主要原料包括氧化铝、酸性硅砂、白云石、石墨粉等。
这些原料需要经过筛选和称量来确保其质量和配比的准确性。
然后是原料的预处理。
原料中可能含有一定的杂质和水分,需要通过破碎、磨粉、烘干等处理步骤来去除杂质,并将水分控制在一定的范围内。
接下来是配料和混合。
按照一定的配比将预处理好的原料加入到搅拌机中进行混合,以确保不同原料充分混合均匀,并形成颗粒状的混合料。
混合后的料进入成型阶段。
根据不同的产品要求,混合料可以通过挤压、压制、注射等方法进行成型。
成型后的材料需要经过一定时间的湿负荷处理,以增强其粘结力和强度。
然后是干燥和煅烧。
成型后的材料需要经过干燥和煅烧来消除残余水分和有机物,并形成结晶化的物相。
干燥和煅烧的温度和时间根据不同的材料和产品要求进行调控。
煅烧后的产品需要经过精加工。
这包括修整、切割、打磨等工序,以使成品的外观和尺寸符合要求。
最后是质检和包装。
生产出的成品需要经过严格的质量检测,包括物理性能、耐火性能、化学性能等方面的测试。
合格的材料将进行包装,以确保在运输和储存过程中不受损坏。
以上是一般耐火材料生产工艺的主要流程。
每个生产厂家可能根据自身的工艺和产品特点有所不同,但基本原理和步骤是相似的。
耐火材料的生产过程需要严格控制原料质量、配比和生产条件,以确保最终产品的质量达到要求。
第三章-耐火材料生产过程
(2)虽然增加颗粒粒度的组份数量有利于提高堆积密度,但当组 份数目超过时,效果不再明显。故在实际生产中,通常采取三组份 颗粒配料,有时也采取四组份颗粒配料。
2. 拣选对象:耐火粘土、高铝矾土、菱镁矿等
方法:根据熟料的外观颜色、有无显而易见的杂质、比重、致密度等 情况进行人工拣选。
三、原料的破粉碎
1. 破粉碎的重要意义
(1)各种原料只有破粉碎到一定细度,才可能充分混合均匀,从而 保证制品组织结构的均匀性。
(2)通过破粉碎将各种原料加工成适当粒度,以保证制品的成型密度。 (3)只有将原料粉碎到一定细度,才能提高原料的反应活性,促进高 温下的固相反应,形成预期的矿物组成和显微组织结构,以及降低烧成 温度。
B P2
C
坯料被进一步压缩,但呈
阶梯式变化——坯料被压
P1
缩到一定程度后,即阻碍
进一步压缩,一旦压力继 续增大到使颗粒再度产生
压缩,mm
变形的外力时,坯料的体积又得以被压缩。这种增压—压缩的
过程短促而频繁,最后,压制过程进入第三阶段。
阶段C: 在极限压力 P2 作用下,坯料不再被压缩,坯体的密度不 再增大。
2. 颗粒组成(颗粒级配)设计 (1)颗粒级配的含义
(2)调配颗粒组成的必要性 保证坯体的成型密度
减小坯体的烧成收缩
保证制品的质量与性能
§3-2 坯料的制备
颗粒组成和制品性质的关系:
(a)—气孔率;(b)—常温耐压强度;(c)—烧成收缩 (d)—透气率;(e)—耐热冲击性
§3-2 坯料的制备
精品课件-耐火材料生产基本工艺原理
混练时的加料顺序: 通常先加入粗颗粒料,然后加水或泥浆、纸浆废液,混合1~2min后,再 加细粉。 若粗细颗粒同时加入,易出现细粉集中成小泥团及“白料”。
坯料的塑化处理可采用困料(陈腐)
困料中的水化反应,有时能产生胶体物质 例如含CaO偏高的镁质坯料在困料时发生下述化学反应:
MgO+H2O →Mg(OH)2 CaO十H2O→ Ca(OH)2 生成物呈胶体性质,提高坯料的结合性和可塑性,降低体积效应的危害性。
则:5-3 18.5%;3-1 29%;1-0 17.5%
七、配料 1、配料的组成 包括按规定比例配合的各种原料和同一原料的各不同颗粒组 成的粉料。 (1) 配料的化学组成必须能满足制品的要求,并且应比制品指标要求高些。 (2) 在配料中应含有结合成分,使坯料具有足够的结合性。 (3)原料中含有水分和灼减成分时,原料、配料和制品的化学组成之间应进行换 算。
●助磨剂
一、选矿与提纯
选矿:利用多种矿物的物理和化学性质的差别,将矿物集合体的原矿粉碎,并分离 出多种矿物。 提纯:利用一系列化学及物理化学反应,矿物富集的过程。
选矿方法:机械法、物理-化学法、纯化学法、电气法等。
二、原料的煅烧
原料煅烧时产生一系列物理化学反应,能改善制品的成分及其组织结 构,保证制品的体积稳定及其外形尺寸的准确性,提高制品性能。
矽肺病。
五、助磨剂 助磨剂在粉磨过程中,吸附在物料颗粒表面,使物料表面自由能和晶格畸变 程度减小,促使颗粒软化,另外,助磨剂的吸附可平衡颗粒表面上因粉碎而 产生的不饱和价键,防止颗粒重新聚结。
水是一种最简单的助磨剂,适量水可助磨又可防尘。
第二节 坯料的制备 耐火材料制品几乎都是由粉料颗粒经加工制备而成,所涉及的颗粒,通常是指 毫米至微米级的颗粒。 一、颗粒的几何学性质 1、粉体颗粒的构造 一次颗粒 ;二次颗粒或团聚体。 废旧制品重新利用
耐火材料生产工艺
混练设备
混练机
困料
作用
使结合粘土进一步分散,从而使其与水分分布更均匀, 发挥其可塑性能与结合性能,以改善泥料的成型性能
1对粘土砖的作用
氧化钙在泥料中充分消化,避免CaO水化
2钙含量高的镁砖泥料
去除料内因化学反应产生的气体
2.泥浆注入石膏模中,石膏吸收水分,并在其 表面集结成水分较少的泥料膜
半干法成型坯体密实程度
1.泥料性质2.压制压力 3.增压速度 4.加压时间
有触变性的泥料 1.成型易水化的物料如焦油白云石和焦
油镁砂料
2.浇注料
压力机
干燥
干燥:提高坯体的机械强度,有利于装窑操作并保证
烧成初期能够顺利进行
过程
1.结合粘土的干燥 2.熟料的干燥
原料的煅烧
1.形成熟料:密度高,强度大,体积稳定性好, 具有良好的物理-化学性能和外形质量,从而 保证耐材制品的外形尺寸
2.煅烧的天然矿石有粘土、高铝矾土、菱镁矿 和白云石等
3.不煅烧的天然矿物有硅石、叶蜡石等 4.煅烧温度Ts约为其熔点的0.7~0.9倍,多高 于制品的烧成温度,更高于制品的使用温度。
从最高烧成温度至室温的冷却过程中, 主要发生耐火相的析晶、某些晶相的 晶型转变、玻璃相的固化等过程,在 此过程中坯体的强度、密度、体积依 品种不同都有相应的变化
坯体中各种反应趋于完全、充分、液 相数量继续增加,结晶相进一步成长 而达到致密化
烧结过程的宏观结构变化及其影响因素
宏观结构变化
坯体的烧结可以概括为三个阶段1.热态接触:物料内部各组分质点间的接触增加,但仍 保留其边界2.开始阶段:质点间的边界被打开,但新的气孔尚未形成3.形成封闭气孔阶
- 1、下载文档前请自行甄别文档内容的完整性,平台不提供额外的编辑、内容补充、找答案等附加服务。
- 2、"仅部分预览"的文档,不可在线预览部分如存在完整性等问题,可反馈申请退款(可完整预览的文档不适用该条件!)。
- 3、如文档侵犯您的权益,请联系客服反馈,我们会尽快为您处理(人工客服工作时间:9:00-18:30)。
2010级化学班孟享洁2010061415
耐火材料的制备
耐火材料是一种耐火度不低于1580℃,有较好的抗热冲击和化学侵蚀的能力、导热系数低和膨胀系数低的无机非金属材料。
其主要是以铝矾土、硅石、菱镁矿、白云石等天然矿石为原料经加工后制造而成的。
其应用是用作高温窑、炉等热工设备的结构材料,以及工业用高温容器和部件的材料,并能承受相应的物理化学变化及机械作用。
主要是广泛用于冶金、化工、石油、机械制造、硅酸盐、动力等工业领域,在冶金工业中用量最大,占总产量的50%~60%。
耐火材料的发展在国民工业生产的应用中有着举足轻重的地位。
中国耐火材料的发展历史悠久,具有了较为完整的生产工艺,其当代的发展已经是能独立研发各种性能较为优越的耐火材料,但依然存在各种缺点和不足。
其制备流程图如下所示:
耐火材料制备原理:
1.耐火原料的加工
原料的加工主要包括原料的精选提纯.均化或合成;原料的干燥和煅烧;原料的破粉碎和分级。
原料的精选提纯和均化为了提高原料的纯度,一般需经拣选或冲洗,剔除杂质,有的还需要采用适当选矿方法进行精选提纯。
有的原料中成分不均,需要均化。
原料的煅烧:为了保证原料的高温体积稳定性。
化学稳定性和高强度,多数天然原料和合成原料,需经高温煅烧制成熟料或熔融成熔块。
烧结温度T约为其熔点的0.7~0.9倍。
原料的破粉碎和分级:原料的破粉碎的目的是按照配料要求制成不同粒级的颗粒及细粉,进行级配,使多组分间混合均匀,以便相互反应,并尽可能获得
致密的或具有一定粒状结构的制品胚体。
2耐火材料成型工艺
耐火材料借助于外力或模型,成为具有一定尺寸。
形状和强度的胚体或制品的过程。
压制或成型是耐火材料生产工艺过程中的重要环节。
按胚料含水量的多少,分为半干法.可塑法.注浆法。
3耐火材料的干燥
干燥过程可分为三个阶段。
在此之前有一个加热阶段。
一般加热阶段时间很短,胚体温度上升到湿球温度。
第二阶段是降速阶段,随着干燥时间的延长,或胚体含水量的减少,胚体表面的有效蒸发面积逐渐减少,干燥速度逐渐降低。
第三阶段干燥速度逐渐接近零,最终胚体水分不再减少。
4耐火材料的烧成
烧成是耐火制品生产中最后一道工序。
制品在烧成过程中发生一系列物理化学变化,随着这些变化的进行,气孔率降低,体积密度增大,使胚体变成具有一定尺寸.形状和结构强度的制品。
耐火材料的生产工艺
1原料的加工
原料的加工主要包括原料的精选提纯.均化或合成;原料的干燥和煅烧;原料的破粉碎和分级。
2配料与混练
配料组成:(1).化学组成:主成分,易熔杂质总量和有害杂质量的规定(2).颗粒配比(3).常温结合剂(4).原料中水分和灼减的换算。
配料方法:重量:磅秤、自动称量称、称量车、电子称、光电数字显示称。
容积:带式、板式、槽式、圆盘式、螺旋式、振动给料机。
混练:使不同组分和粒度的物料同的物料同
适量的结合剂经混合和挤压作用达到分布均匀和充分润湿的泥料制备过程。
其中混练设备: 单轴和双轴搅拌机、混砂机(混合、搅拌)
湿碾机(混合、搅拌和挤压,更均匀)
3砖坯的成型
耐火坯料借助于外力和模型,成为具有一定尺寸、形状和强度的坯体或制品的过程
方法:
1.半干法
2.可塑法
3.注浆法
4.振动成型
5.热压注成型6热压成7.电熔注法
8.等静压成型
4 砖坯干燥:提高坯体的机械强度,有利于装窑操作并保证烧成初期能够顺利进行: 1.等速干燥阶段 2.降速干燥阶 3.低速及平衡干燥阶段(干燥方式: 1.间歇式室式 2.隧道式)
5制品烧成:坯体中各种反应趋于完全、充分、液相数量继续增加,结晶相进一步成长而达到致密
结论
作为中国工业生产进步中不可或缺的生产因素,耐火材料在中国的发展是有着长久的历史的,当今的发展已经研究开发了高铝砖、镁铝砖、焦炉硅砖、碳砖、碳化硅砖、电熔莫来石砖、耐火混凝土和不烧砖等广泛应用在国民工业生产中的较好的耐火材料。
而今后的发展前景是朝着原料优质化、向质量型转变、开拓新品种、新工艺、耐火材料综合消耗等方向发展,继续研发科学高效的耐火材料。