粉末冶金介绍
粉末冶金基础知识(三篇)

粉末冶金基础知识(一)粉末的化学成分及性能尺寸小于1mm的离散颗粒的集合体通常称为粉末,其计量单位一般是以微米(m)或纳米(nm)。
1.粉末的化学成分常用的金属粉末有铁、铜、铝等及其合金的粉末,要求其杂质和气体含量不超过1%~2%,否则会影响制品的质量。
2.粉末的物理性能⑴粒度及粒度分布粉料中能分开并独立存在的最小实体为单颗粒。
实际的粉末往往是团聚了的颗粒,即二次颗粒。
实际的粉末颗粒体中不同尺寸所占的百分比即为粒度分布。
⑵颗粒形状即粉末颗粒的外观几何形状。
常见的有球状、柱状、针状、板状和片状等,可以通过显微镜的观察确定。
⑶比表面积即单位质量粉末的总表面积,可通过实际测定。
比表面积大小影响着粉末的表面能、表面吸附及凝聚等表面特性。
3.粉末的工艺性能粉末的工艺性能包括流动性、填充特性、压缩性及成形性等。
⑴填充特性指在没有外界条件下,粉末自由堆积时的松紧程度。
常以松装密度或堆积密度表示。
粉末的填充特性与颗粒的大小、形状及表面性质有关。
⑵流动性指粉末的流动能力,常用50克粉末从标准漏斗流出所需的时间表示。
流动性受颗粒粘附作用的影响。
⑶压缩性表示粉末在压制过程中被压紧的能力,用规定的单位压力下所达到的压坯密度表示,在标准模具中,规定的润滑条件下测定。
影响粉末压缩性的因素有颗粒的塑性或显微硬度,塑性金属粉末比硬、脆材料的压缩性好;颗粒的形状和结构也影响粉末的压缩性。
⑷成形性指粉末压制后,压坯保持既定形状的能力,用粉末能够成形的最小单位压制压力表示,或用压坯的强度来衡量。
成形性受颗粒形状和结构的影响。
(二)粉末冶金的机理1.压制的机理压制就是在外力作用下,将模具或其它容器中的粉末紧密压实成预定形状和尺寸压坯的工艺过程。
钢模冷压成形过程如图7.1.2所示。
粉末装入阴模,通过上下模冲对其施压。
在压缩过程中,随着粉末的移动和变形,较大的空隙被填充,颗粒表面的氧化膜破碎,颗粒间接触面积增大,使原子间产生吸引力且颗粒间的机械楔合作用增强,从而形成具有一定密度和强度的压坯。
粉末冶金的定义

粉末冶金的定义粉末冶金是一种通过将金属或非金属粉末进行冶炼和成形的加工方法。
粉末冶金技术广泛应用于制造业中,包括航空航天、汽车、电子、医疗器械等行业。
本文将从粉末冶金的定义、原理、工艺流程和应用领域等方面进行介绍。
粉末冶金是一种以金属或非金属粉末为原料,通过粉末的加工和烧结等工艺,制造出具有特定形状和性能的零部件的方法。
相比传统的加工方法,粉末冶金具有独特的优势。
首先,粉末冶金能够制造出复杂的形状,例如孔洞、槽口和凹凸等。
其次,粉末冶金能够制造出高精度的零件,满足不同行业对产品精度的要求。
此外,粉末冶金还能够制造出具有特殊性能的材料,例如高强度、耐磨、耐腐蚀等。
粉末冶金的基本原理是将金属或非金属原料粉末通过特定的工艺进行成型和烧结。
首先,将金属或非金属原料粉末进行混合,可以根据需要添加一定比例的添加剂。
然后,将混合后的粉末进行成型,常用的成型方法有压制、注射成型和挤压成型等。
成型后的粉末零件具有一定的强度和形状,但还不能满足使用要求,需要进行烧结。
烧结是将成型后的粉末零件在高温下进行热处理,使粉末颗粒之间发生结合,形成致密的材料。
粉末冶金的工艺流程主要包括原料制备、混合、成型、烧结和后处理等环节。
首先,需要对金属或非金属原料进行制备,通常采用机械研磨、球磨和化学还原等方法。
制备好的原料粉末需要进行混合,以保证成品的均匀性。
混合的方法有干法混合和湿法混合两种。
接下来,将混合后的粉末进行成型,可以根据需要选择不同的成型方法。
成型后的粉末零件需要进行烧结,烧结温度和时间根据原料和产品要求进行调控。
最后,对烧结后的产品进行后处理,包括热处理、表面处理和精加工等。
粉末冶金技术在众多领域中得到了广泛应用。
首先,在航空航天领域,粉末冶金技术可以制造出轻质高强度的零部件,提高航空器的性能。
其次,在汽车工业中,粉末冶金技术可以制造出高强度、耐磨的发动机零部件,提高汽车的可靠性和经济性。
此外,粉末冶金技术还可以应用于电子行业,制造出高导电性和磁导率的材料,用于电子元器件的制造。
粉末冶金原理-中文
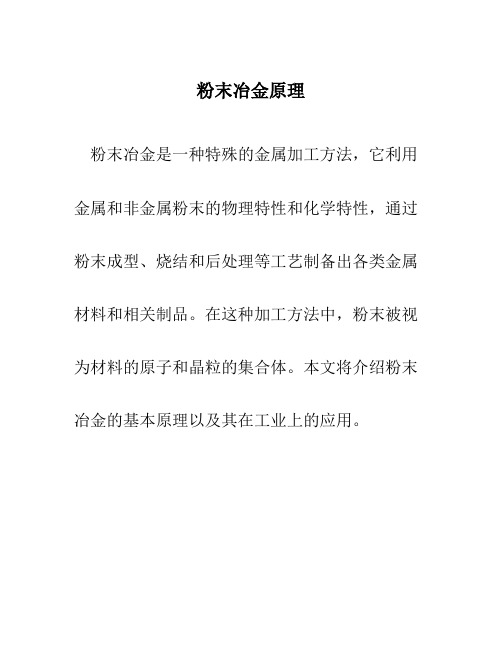
粉末冶金原理粉末冶金是一种特殊的金属加工方法,它利用金属和非金属粉末的物理特性和化学特性,通过粉末成型、烧结和后处理等工艺制备出各类金属材料和相关制品。
在这种加工方法中,粉末被视为材料的原子和晶粒的集合体。
本文将介绍粉末冶金的基本原理以及其在工业上的应用。
粉末冶金的基本原理1.原料选择:粉末冶金的首要任务是选择适当的原料。
原料可以是金属、合金或陶瓷等材料的粉末。
原料的选择应该考虑材料的化学成分、晶体结构、粒子形状和尺寸分布等因素。
2.粉末的制备:粉末的制备是粉末冶金的关键步骤之一。
常见的粉末制备方法包括研磨、机械合金化、溶液沉淀和气相反应等。
不同的制备方法可以获得不同尺寸和形状的粉末。
3.粉末的成型:成型是将粉末转变为所需形状的工艺。
常用的成型方法包括压制、挤出、注射成型和3D打印等。
通过成型,粉末可以被固化成具有一定强度和形状的零件。
4.烧结:烧结是粉末冶金过程中的关键步骤之一。
经过成型的粉末件放入高温环境中,粉末颗粒与颗粒之间发生扩散和结合,形成致密的材料。
烧结温度和时间会影响材料的致密性和力学性能。
5.后处理:烧结后的材料可能需要进行后处理。
常用的后处理方法包括热处理、表面处理和加工等。
通过后处理,可以改善材料的性能和功能。
粉末冶金的应用领域粉末冶金广泛应用于各个领域,包括汽车、航空航天、电子、能源、医疗和军工等。
1.汽车行业:粉末冶金技术在汽车行业中得到广泛应用。
例如,通过粉末冶金可以制备高强度和轻质的发动机零件和齿轮等关键部件,提高汽车的燃油效率和排放性能。
2.航空航天:航空航天行业对材料的要求非常高。
粉末冶金可以制备出具有优异的高温强度和耐腐蚀性能的钛合金和镍基合金等材料,用于制造航空发动机和航天器件。
3.电子:在电子行业中,粉末冶金可以制备具有高导电性和磁导率的材料,例如铜粉末用于制造电子线路板和电磁元件。
4.能源:粉末冶金在能源领域的应用主要集中在制备高温抗氧化和热电材料。
例如,通过粉末冶金可以制备铁素体不锈钢和铬基合金等材料,用于制造高温炉和热交换器等设备。
粉末冶金的原理
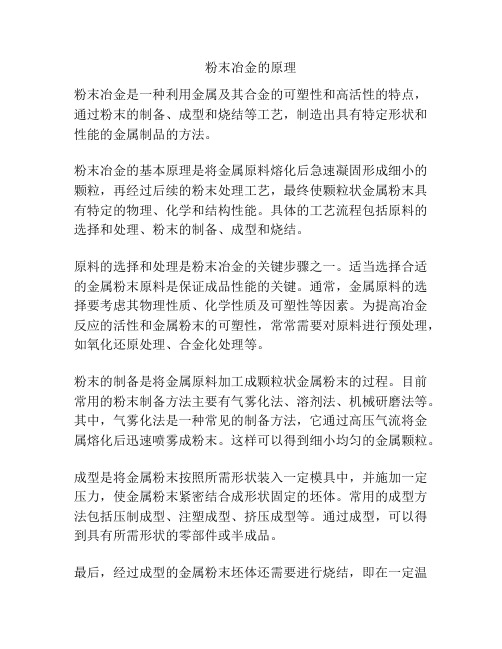
粉末冶金的原理粉末冶金是一种利用金属及其合金的可塑性和高活性的特点,通过粉末的制备、成型和烧结等工艺,制造出具有特定形状和性能的金属制品的方法。
粉末冶金的基本原理是将金属原料熔化后急速凝固形成细小的颗粒,再经过后续的粉末处理工艺,最终使颗粒状金属粉末具有特定的物理、化学和结构性能。
具体的工艺流程包括原料的选择和处理、粉末的制备、成型和烧结。
原料的选择和处理是粉末冶金的关键步骤之一。
适当选择合适的金属粉末原料是保证成品性能的关键。
通常,金属原料的选择要考虑其物理性质、化学性质及可塑性等因素。
为提高冶金反应的活性和金属粉末的可塑性,常常需要对原料进行预处理,如氧化还原处理、合金化处理等。
粉末的制备是将金属原料加工成颗粒状金属粉末的过程。
目前常用的粉末制备方法主要有气雾化法、溶剂法、机械研磨法等。
其中,气雾化法是一种常见的制备方法,它通过高压气流将金属熔化后迅速喷雾成粉末。
这样可以得到细小均匀的金属颗粒。
成型是将金属粉末按照所需形状装入一定模具中,并施加一定压力,使金属粉末紧密结合成形状固定的坯体。
常用的成型方法包括压制成型、注塑成型、挤压成型等。
通过成型,可以得到具有所需形状的零部件或半成品。
最后,经过成型的金属粉末坯体还需要进行烧结,即在一定温度下对金属粉末进行加热处理,使其颗粒之间发生结晶和扩散,相互融合并形成坚固的金属材料。
烧结可以通过自发热烧结、辅助烧结等方法来实现。
烧结过程中,金属粉末之间的氧化物和杂质也会在高温下被还原和挥发。
通过以上的处理工艺,粉末冶金可以制备出具有复杂形状、高强度、良好磨损性能和耐磨性能的金属制品。
由于粉末冶金具有成本低、能耗少、无需后加工等优势,因此在汽车、航空航天、工具等领域得到广泛应用。
粉末冶金知识大全
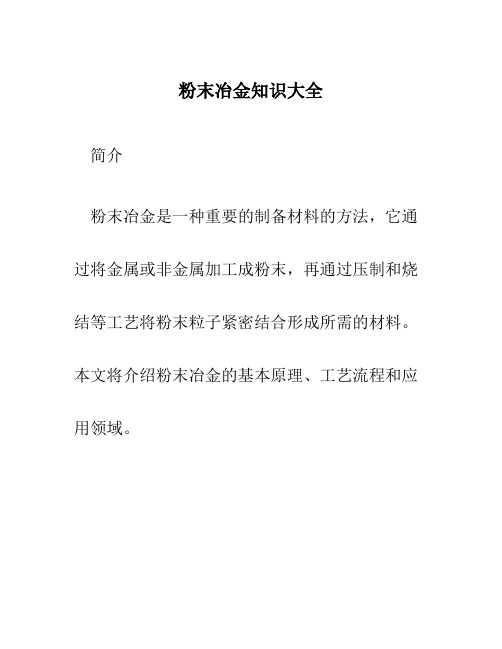
粉末冶金知识大全简介粉末冶金是一种重要的制备材料的方法,它通过将金属或非金属加工成粉末,再通过压制和烧结等工艺将粉末粒子紧密结合形成所需的材料。
本文将介绍粉末冶金的基本原理、工艺流程和应用领域。
1. 粉末制备粉末冶金的第一步是制备粉末。
常见的粉末制备方法包括:•原子熔化法:通过将金属或合金加热到高温,使其熔化后迅速冷却,冷却过程中形成的微细颗粒即为粉末。
•机械研磨法:将金属块或合金块放入球磨机中与球磨介质一起磨碎,经过一定时间后得到所需的粉末。
•物理气相法:通过高温蒸发和凝聚,使金属或合金从气相转变为粉末。
常见的物理气相制备方法有气体凝聚法、物理溅射法等。
2. 粉末冶金工艺粉末冶金包括压制、烧结和后处理等多个工艺步骤。
2.1 压制压制是将制备好的粉末以一定的压力塑造成所需形状的过程。
常见的压制方法有:•静态压制:即将粉末放置在模具中,施加垂直于模具方向的压力,使粉末颗粒之间发生塑性变形,形成一定形状的绿体。
•动态压制:即通过提供一个快速冲击力,使粉末颗粒互相碰撞并发生变形,形成一定形状的绿体。
2.2 烧结烧结是将压制好的绿体在一定温度下进行加热,使粉末颗粒之间发生扩散和结合,形成致密的材料。
常见的烧结方法有:•常压烧结:将绿体放在电炉或气炉中进行加热,使粉末颗粒熔结或固相扩散结合。
•热等静压烧结:在加热的同时施加一定的压力,用于加强绿体的结合。
2.3 后处理烧结完成后,还需要进行一些后处理步骤以提高材料的性能。
常见的后处理方法有:•热处理:通过控制温度和时间,在一定的条件下改变材料的组织结构,提高其硬度、强度等性能。
•表面处理:在材料表面形成覆盖层、涂层或改变表面形貌,以提高耐磨、耐腐蚀等性能。
3. 应用领域粉末冶金在许多领域都有着广泛的应用。
3.1 金属制品粉末冶金可以制备各种金属制品,如汽车零部件、工具等。
由于独特的结构和物理性能,粉末冶金制品具有优异的耐磨、抗拉伸和耐腐蚀等特点。
3.2 陶瓷制品通过粉末冶金技术可以制备出高纯度、高强度的陶瓷制品,如陶瓷刀具、陶瓷齿轮等。
粉末冶金手册

粉末冶金手册粉末冶金是一种将金属或非金属粉末通过压制、烧结等工艺加工成成型品的制造工艺。
粉末冶金具有高效、低成本、可成型性好、材料利用率高等优势,因此在航空航天、汽车工业、电子行业等领域得到广泛应用。
本手册将介绍粉末冶金的基本原理、工艺流程、材料选择、设备介绍等内容。
一、粉末冶金的基本原理粉末冶金的基本原理是将金属或非金属物质经过粉碎或原料特殊制备得到的粉末,经过压制成型或注射成型,再经过高温烧结得到所需产品。
这种工艺利用了粉末颗粒之间的相互扭曲和扩散,从而实现了物质的成型。
同时,由于粉末冶金是一种非液态冶金工艺,不需要溶解和凝固过程,避免了材料在液态下的气体、夹杂物等问题,因此可以获得更高的材料纯度和均匀性。
二、粉末冶金的工艺流程粉末冶金的一般工艺流程分为原料制备、混合、成型、烧结和后处理等步骤。
1.原料制备:原料制备阶段主要包括选料和粉末制备。
选料是指根据成品的要求选择合适的原料,如金属、合金、陶瓷或复合材料等。
粉末制备可以通过粉碎、化学方法、电化学方法等得到所需粉末。
2.混合:将所选的原料粉末按照一定比例进行混合。
混合的目的是使各种材料的粒子均匀分散,以获得更高的均匀性。
3.成型:将混合好的粉末通过压制成型,可以使用冷压、热压或注射成型等方法。
成型一般可以分为干压成型和液相成型两种方式。
4.烧结:成型件通过高温烧结,使粉末颗粒之间发生结合,形成致密的材料。
烧结温度和时间根据材料种类、成型件形状等因素确定。
5.后处理:烧结后的材料可以进行表面处理、热处理、加工等工艺。
目的是使产品达到所需的性能和尺寸要求。
三、粉末冶金的材料选择粉末冶金可以应用于各种金属和非金属材料的制备,包括纯金属、合金、陶瓷、塑料等。
在选择材料时需要考虑材料的物理性质、化学性质、应用环境等因素。
例如,对于需要高强度和耐磨性的零件可以选择使用金属粉末冶金制备的合金材料;对于需要绝缘性能和耐高温的零件可以选择使用陶瓷粉末冶金制备的材料。
粉末冶金概念

粉末冶金概念一、什么是粉末冶金粉末冶金是一种通过粉末冶金工艺制备金属制品的方法。
它将金属粉末进行混合、压制和烧结等一系列工艺,最终制得具有一定形状和性能的金属制品。
粉末冶金通常包括粉末的制备、粉末混合、压制、烧结等过程。
二、粉末冶金的制备过程粉末冶金的制备过程主要包括原料制备、粉末的制备和形状成型。
2.1 原料制备原料制备过程是粉末冶金的第一步。
原料通常是金属或非金属的块材料,通过一系列的物理和化学方法,使其转化为适合制备粉末的形态。
2.2 粉末的制备在粉末制备过程中,通常采用机械化方法将块材料加工成颗粒状物料。
常见的粉末制备方法有研磨、球磨和气流研磨等。
2.3 形状成型形状成型是指将粉末加工成具有一定形状的工件。
常见的形状成型方法有压制、注塑和挤压等。
在形状成型的过程中,可以通过加入不同的添加剂和改变工艺参数,来调控工件的性能。
三、粉末冶金的优势和应用领域粉末冶金具有以下的优势:1.单一制备能力:粉末冶金可以制备纯净度高、化学成分准确的金属制品。
2.可混合性:粉末冶金可以将不同成分的粉末进行混合,制备出具有特殊性能的材料。
3.无损制造:粉末冶金通过压制和烧结等过程,可以制备出具有复杂形状和良好性能的工件,且不需要进行二次加工。
4.可持续发展:粉末冶金过程中产生的废料可以进行回收再利用。
粉末冶金在许多领域都有广泛的应用,包括:1.汽车工业:粉末冶金可以制备出高强度、高耐磨的汽车零部件,如发动机曲轴和齿轮等。
2.电子工业:粉末冶金可以制备出具有高热导率和高耐腐蚀性能的电子散热器和接触材料等。
3.医疗器械:粉末冶金可以制备出无毒、无菌的医疗器械,如人工关节和牙科种植体等。
4.能源领域:粉末冶金可以制备出高温合金和热电材料等,用于核能、航天和新能源等领域。
四、粉末冶金的未来趋势粉末冶金作为一种高效、环保的金属制造技术,具有广阔的发展前景。
未来,粉末冶金可能会在以下几个方面实现进一步的发展:1.新材料的研发:随着科学技术的不断进步,新材料的研发成为粉末冶金的一个重要方向。
粉末冶金原理简介课件
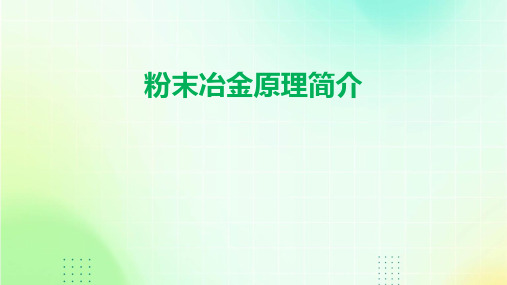
化学共沉淀法
总结词
通过化学反应使金属离子共沉淀形成均匀的金属氧化物或硫化物粉末。
详细描述
化学共沉淀法是一种制备金属粉末的方法,通过化学反应使金属离子共沉淀形成 均匀的金属氧化物或硫化物粉末。在沉淀过程中,控制溶液的pH值和浓度等条 件,使不同金属离子同时沉淀,形成成分均匀的混合物粉末。
喷雾干燥法
定义
粉末烧结是一种通过加热使粉末颗粒 间发生粘结,从而将它们转化为致由烧结和压制烧结。
烧结原理与过程
原理
烧结过程中,粉末颗粒通过表面扩散、粘性流动和塑性变形等机制相互粘结, 形成连续的固体结构。
过程
烧结过程通常包括加热、保温和冷却三个阶段,其中保温阶段是粉末颗粒粘结 的主要阶段。
能源领域
粉末冶金多孔材料可用于制造 燃料电池电极、核反应堆控制 棒等能源相关领域。
医疗器械
粉末冶金材料具有生物相容性 和耐腐蚀性,适用于医疗器械 制造,如人工关节、牙科植入
物等。
粉末冶金的发展历程
01
02
03
早期发展
粉末冶金起源于古代金属 加工技术,如青铜器时代 的铜合金制造。
20世纪发展
随着科技的发展,粉末冶 金在20世纪得到了广泛研 究和应用,涉及领域不断 扩大。
05
粉末冶金材料性能
力学性能
高强度和硬度
粉末冶金材料通过细晶强 化等手段,表现出较高的 硬度和强度,能够满足各 种复杂工况的需求。
良好的耐磨性
由于粉末冶金材料的晶粒 细小且均匀,其耐磨性优 于传统铸造和锻造材料。
抗疲劳性能
由于材料的内部结构均匀 ,可以有效抵抗疲劳裂纹 的扩展,提高零件的寿命 。
特点
粉末冶金具有能够制备传统熔炼 方法难以制备的合金、材料纯度 高、材料性能可调范围广、节能 环保等优点。
- 1、下载文档前请自行甄别文档内容的完整性,平台不提供额外的编辑、内容补充、找答案等附加服务。
- 2、"仅部分预览"的文档,不可在线预览部分如存在完整性等问题,可反馈申请退款(可完整预览的文档不适用该条件!)。
- 3、如文档侵犯您的权益,请联系客服反馈,我们会尽快为您处理(人工客服工作时间:9:00-18:30)。
目錄
1粉末射出成形
2粉末射出成形過程
3好處,
4製程比較
5材料選擇
6第二段加工
7品質體系及量測設備
8模具設計
9成品設計
10創新應用的個案研究
11粉末射出成形設計重點
1粉末射出成形
粉末射出成形應用了塑膠射出成形的原理去完成成形.
粉末射出成形是在這幾十年前商業化的. 不過它的過程很快的就成長成為一個製造業低成本高效率來取代傳統的技術. 在現今的工業, 粉末射出成形是一個能夠提供高度的設計應用性和節省費用最佳的製造過程.
成品需要形狀的複雜性和要求最後機械特性及密度,磁性,熱性質,化學性質和電器性質的應用過程高於其他製程. 射出成形的合金粉提供了在塑膠和輕合金不可能的完成特性.
2粉末射出成形過程
混料:非常精細的合金粉與熱朔性黏結劑混合. 混合物再再造粒成顆粒狀
射出:在成形時,給料會被加熱來達到溶解黏合劑的目的. 然後射出成想要的形狀. 那個模型製品的部份叫做“Green Part”.
去除黏結劑:聚合的黏合劑在這個步驟裡將會用溶劑脫酯及加熱的方法去移除黏結劑. 去除黏結劑後, 它將會是由很易碎的和多孔的粉末骨架所組成. 再高溫的處理的同時, 粉末部份還必須要保持它原有的大小和形狀.
燒結:粉末射出成形的最後一個步驟是燒結. 在燒結時,多孔的粉末骨架將會被加熱到差不多是材料熔點的90%. 燒結中,密度上升,小孔消除,和部份收縮. 最後的燒結密度是理論上的大約96%,達到所須要理論上物理特性.
3好處,
-能節省相當的費用
-能做的複雜零件形狀和大小的範圍很廣(從0.1克到200克)
-有能力做出很薄的壁到最小到0.4厘米
-有能力組合不同的功能來除去多餘的配件減少組配的工作
-有很好的尺寸控制和一般的公差(+-0.3%)
-減少多餘的形狀製造或排除加工
-範圍廣大包含了各種材料和不同特性
-中到高的生產量有很好的成本效率
-很適合難以理解和很複雜的形狀
-設計可以很有彈性
-最低或是沒有浪費的材料
-很好的表面加工(32RMs;Ra0.8)
4製程比較
粉末射出成形和傳統的金屬成形過程的比較
工業化和自動化長久以來一直是製造工程業所尋求的發展. 當傳統的方法例如加工,沖壓,鍛造,鑄造和粉末冶金還很重要時,粉末射出成形已經快速的成為金屬成形中的一個重要的製程.
材料一覽表
-實際的特性數值依類產品規格,包含密度,顯微結構,純度,和過程,這些都會因為特種的結構而有所不同.
-全部材料不僅僅這些而已,如果需要更多的資料請聯絡本公司.
*抗拉強度(MPa)
5第二段加工
粉末射出成形中的材料特性跟運作中的棒料很類似. 所以加工,表面處理,和熱處理加工可以在燒結後來處理
賣主和後勤管理
依照客戶的要求,本公司提供了SPC品質管理和評估還有裝配的服務. 作為一個完整的解答供應商,本公司成為了賣方和分包商管理者. 此外,本公司還可以提供存貨管理去迎合客戶特別的需求來達到一個削減存貨和後勤的重擔.
6品質體系
本公司通過了ISO9000認證. 從開始到結束,整個製造過程經過了很詳細的審查來符合國際標準和客戶所設的規範.
量測設備
I.非接觸式三次元測量機
II.投影機
III.表面粗糙度測試儀
IV.客戶設計的檢具標準
冶金
I.比重機
II.硬度試驗機
III.黏度機
IV.粒度分析儀
7模具的設計
根據一個部份的形狀,大小和生產數量,一套模具可以製作在1和16之間的空穴. 本公司的模具壽命的保證是1000,000次,同時還會提供各彈性的模具選項來達到顧客方面個別的需求.
以下是模具及成品的設計要求
包含:
--成形設計標準
-圓弧,孔和鋸齒形
-拔模角度
-頂針和澆口位置
-均衡的橫斷面
-平的表面(有利於燒結擺放)
避免:
-尖銳的內圓角和邊緣
-在功能的地方,避免有分模線及融合線
-更精準的尺寸公差小於±0.5%
尺度公差
8成品設計
在設計粉末射出成品時,參考以下的方針是很重要的. 在堅持住這些簡單的設計方針,設計者可以很有效的利用粉末射出成形的優點然後減少加工的費用.及重量
1.圓弧和孔
i.避免材料過重. 提供圓弧和孔來達到減重和結構改良如以下的圖
建議避免把澆口擺在不重要的面上.
10.建議使用可以把最後粉末射出成形的部份的重量控制在200克的方法.
這個使用孔,圓弧,或是其他的重量減少的方法來達成.
11.在射出成形的過程中,避免設計長的零件跟澆口的方向平行. 改變澆口
流進的方向來減少噴流和流痕確保層流才能達成填模最佳的效果.
以下的圖面各個部份的結合來達到一個多功能的機構. 像這樣的考量可以大大的降低成本.
創新應用的個案研究
综合
四個單獨的配件被組合成一件成品. 這樣子的設計改良有更好的機械結構表現和減少的花費.
創新的設計
原本的設計有一個沒有辦法被澆鑄的清角沿著它的外環. 新的六墊片設計取代了清角,同時也允許了使用金屬射出成形來大量生產.
薄壁的能力
這個零件有很複雜的形狀,中空的結構和一整個部分小於1mm的壁厚度.
複雜化&小型化
這些零件有很複雜的形狀和小於1.0克的重量圖解了本公司金屬射出成形的能力.
高縱橫比和高精準度
這塊尺寸105mm X 105mm X 1.5mm的光纖連接器是用科瓦鐵鎳鈷合金做成的. 這個零件挑戰了為了達到精準尺寸和氣封要求的傳統金屬射出成形的縱橫比和尺寸.
材料的創新–新材料
拥有專利和材料的技術秘訣,本公司有能力去依照客戶特別的要求去研發不標準的材料
材料:粉末射出成形是最適用於某些很難加工的材料,這些材料包括了不銹鋼或是加工硬化材料.
表面加工: 粉末射出成形可以達到高品質的表面和低的加工花費.
複雜性: 複雜性非常高,有多軸的分度及設計用粉末射出成形是最好的選擇.
數量: 一年>20,000個,模具及上模的花費才有符合經濟效率.
結合: 結合多個零件成為一個一個可以減少存貨成本和裝配成本,同時也增強機械性能.
性能: 開發新的產品要預先考慮低衝擊韌性,斷裂韌度,疲勞和腐蝕性質. 如果說性能很重要,則需要高密度製造過程. 這些高性能性質可以使用粉末射出成形來達到.
公差: 在所有的生產程序中,精密的公差有它本身須要的費用. 本公司透過和客戶一起,在設計過程中減少不必要的加工花費來設置公差尺寸是非常的重要的.
設計櫥窗: 產品的設計是非常重要的,因為這是跟後面生產的良率及成本有很大的關係粉末射出成形主要的產品設計標準包含了拔模推拔角度,壁厚度,角弧度,連同其他的.
缺陷: 粉末射出成形會在分模線和澆口區域製造出表面缺陷. 這些缺陷需要被擺置在零件上不重要的區域.。