连续搅拌釜式反应器(CTRS)控制系统设计
05《工业组态控制技术》项目五 反应釜监控系统项目设计

(3) 添加6个手动按钮,用于手动控制。在对象元件管理对话框在对象元件 库找到按钮类别,选择按钮82,作为系统的手动控制。双击添加的按钮, 在动态组态属性设置窗口中单击“按钮动作”标签,勾选下面的数据对 象值操作,选择操作为取反,连接变量依次为“进料开关信号”、“排 液开关信号”、“搅拌开关信号”、“加热开关信号”、“制冷开关信 号”、“自定义信号”。
任务5.1 反应釜监控组态系统设计
1 组态实时数据库对象
对象名称
排液开关信号
设备0_通讯状态设备0_通讯状态
手自动信号 温度上限 温度下限 制冷开关信号 制冷开启 制热开启 自定义信号
a b c 打卡按钮 当前计时值 反应液
反应原料浓度
反应原料浓度1
类型
开关型
开关型
开关型 开关型(报警信号) 开关型(报警信号)
开关型 开关型 开关型 开关型 数值型 数值型 数值型 数值型 数值型 数值型
数值型
数值型
注释
排液开关按钮
通讯状态
手动/自动切换按钮 达到温度上限报警 达到温度下限报警
制冷开关按钮 制冷开启 制热开启 自定义按钮
搅拌器浆叶可见度 搅拌器浆叶可见度
搅拌器浆叶角度 用于运维人员的监视控制
定时器当前计时值 反应液动画连接变量
3 制作反应釜系统监控画面 (9) 制作流动块。根据需要绘制进料、排 液、制冷管道。如图5-15所示。
图 5-15 绘制流动块管道
(10) 分别双击选择进料电磁阀、制冷电磁阀、排液电磁阀,在弹出的动画 组态属性设置窗口单击“填充颜色”标签依次连接变量为“进料阀开 启信号”、“制冷开启”、“排液阀开启反馈信号”。填充颜色连接 都设置一致,填充颜色0为红色、1为绿色。
理想混合连续搅拌釜式反应器(CSTR)
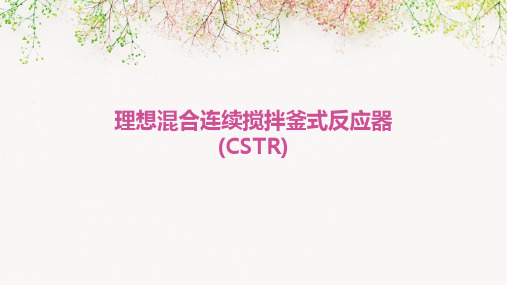
理想混合状态
物料在反应器内达到完全混合,不存在浓度和温度 的梯度分布。
反应器内各点的物料性质(如浓度、温度等)完全 相同,且随时间保持不变。
在理想混合状态下,反应器的性能达到最优,反应 效率和产物质量得到保证。
03
CSTR反应器的数学模型
物料平衡方程
进入反应器的物料流量与离开 反应器的物料流量相等,即输 入等于输出。
用于连续加入反应物和排出产物,实现连续化生产 。
工作流程
01
02
03
04
物料进入
反应物通过进料口连续加入反 应器内。
充分混合
在搅拌装置的作用下,物料在 反应器内充分混合,达到浓度 和温度的均匀分布。
反应进行
在适宜的反应条件下,物料在 反应器内进行化学反应。
产物排出
反应完成后,产物通过出料口 连续排出反应器。
100%
平均停留时间
表示物料在反应器内的平均停留 时间,影响反应器的生产能力和 产品质量。
80%
停留时间分布曲线
通过实验测定,可直观反映反应 器内物料的停留时间分布情况。
转化率与选择性
转化率
表示原料在反应器内转化为产 品的程度,是衡量反应器性能 的重要指标。
选择性
表示在给定转化率下,生成目 标产物的能力,反映反应器的 选择性能。
THANK YOU
感谢聆听
缺点与挑战
能耗较高
连续搅拌过程需要消耗大量能量,导致CSTR反应器的能耗相对较 高。
设备复杂度高
CSTR反应器结构复杂,涉及搅拌、传热、传质等多个过程,设备 设计、制造和维护难度较大。
放大效应
在将实验室规模的CSTR反应器放大至工业生产规模时,可能会遇到 放大效应问题,影响反应器的性能和产物质量。
连续生产反应釜的设计
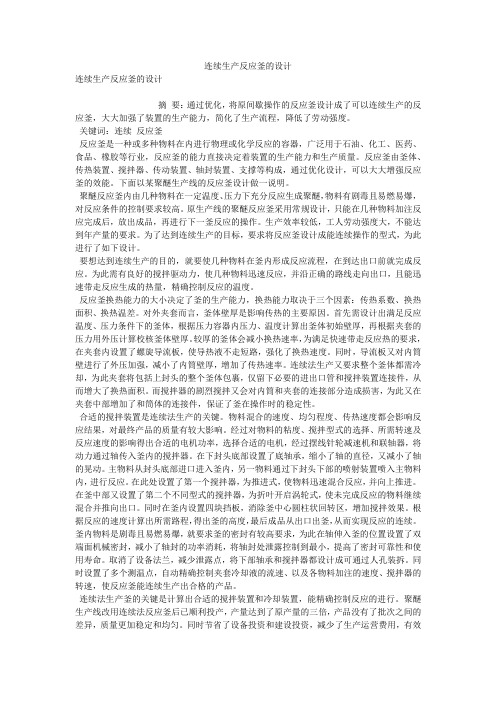
连续生产反应釜的设计连续生产反应釜的设计摘要:通过优化,将原间歇操作的反应釜设计成了可以连续生产的反应釜,大大加强了装置的生产能力,简化了生产流程,降低了劳动强度。
关键词:连续反应釜反应釜是一种或多种物料在内进行物理或化学反应的容器,广泛用于石油、化工、医药、食品、橡胶等行业,反应釜的能力直接决定着装置的生产能力和生产质量。
反应釜由釜体、传热装置、搅拌器、传动装置、轴封装置、支撑等构成,通过优化设计,可以大大增强反应釜的效能。
下面以某聚醚生产线的反应釜设计做一说明。
聚醚反应釜内由几种物料在一定温度、压力下充分反应生成聚醚,物料有剧毒且易燃易爆,对反应条件的控制要求较高。
原生产线的聚醚反应釜采用常规设计,只能在几种物料加注反应完成后,放出成品,再进行下一釜反应的操作。
生产效率较低,工人劳动强度大,不能达到年产量的要求。
为了达到连续生产的目标,要求将反应釜设计成能连续操作的型式,为此进行了如下设计。
要想达到连续生产的目的,就要使几种物料在釜内形成反应流程,在到达出口前就完成反应。
为此需有良好的搅拌驱动力,使几种物料迅速反应,并沿正确的路线走向出口,且能迅速带走反应生成的热量,精确控制反应的温度。
反应釜换热能力的大小决定了釜的生产能力,换热能力取决于三个因素:传热系数、换热面积、换热温差。
对外夹套而言,釜体壁厚是影响传热的主要原因。
首先需设计出满足反应温度、压力条件下的釜体,根据压力容器内压力、温度计算出釜体初始壁厚,再根据夹套的压力用外压计算校核釜体壁厚。
较厚的釜体会减小换热速率,为满足快速带走反应热的要求,在夹套内设置了螺旋导流板,使导热液不走短路,强化了换热速度。
同时,导流板又对内筒壁进行了外压加强,减小了内筒壁厚,增加了传热速率。
连续法生产又要求整个釜体都需冷却,为此夹套将包括上封头的整个釜体包裹,仅留下必要的进出口管和搅拌装置连接件,从而增大了换热面积。
而搅拌器的剧烈搅拌又会对内筒和夹套的连接部分造成损害,为此又在夹套中部增加了和筒体的连接件,保证了釜在操作时的稳定性。
过程控制过程控制过程控制过程控制系统设计系统设计系统设计系统设计
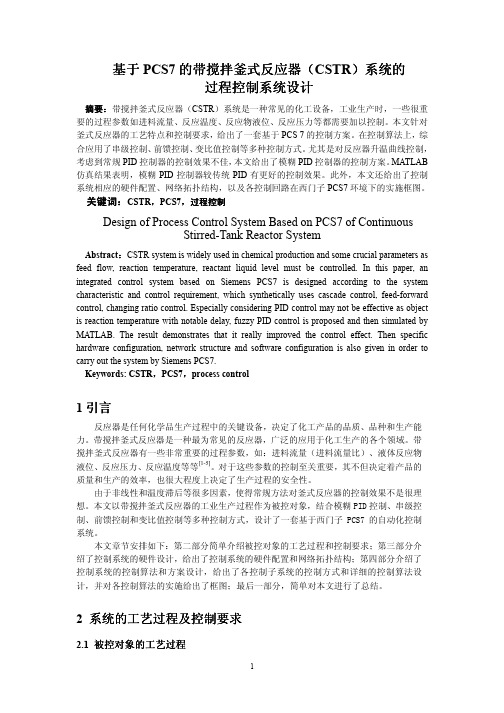
搅拌釜式反应器( 基于 PCS7 的带搅拌釜式反应器(CSTR)系统的 )系统的 过程控制系统设计 过程控制系统设计摘要: 摘要:带搅拌釜式反应器(CSTR)系统是一种常见的化工设备,工业生产时,一些很重 要的过程参数如进料流量、反应温度、反应物液位、反应压力等都需要加以控制。
本文针对 釜式反应器的工艺特点和控制要求,给出了一套基于 PCS 7 的控制方案。
在控制算法上,综 合应用了串级控制、 前馈控制、 变比值控制等多种控制方式。
尤其是对反应器升温曲线控制, 考虑到常规 PID 控制器的控制效果不佳, 本文给出了模糊 PID 控制器的控制方案。
MATLAB 仿真结果表明,模糊 PID 控制器较传统 PID 有更好的控制效果。
此外,本文还给出了控制 系统相应的硬件配置、网络拓扑结构,以及各控制回路在西门子 PCS7 环境下的实施框图。
关键词: 关键词:CSTR,PCS7,过程控制 , ,Design of Process Control System Based on PCS7 of Continuous Stirred-Tank Reactor SystemAbstract:CSTR system is widely used in chemical production and some crucial parameters as : feed flow, reaction temperature, reactant liquid level must be controlled. In this paper, an integrated control system based on Siemens PCS7 is designed according to the system characteristic and control requirement, which synthetically uses cascade control, feed-forward control, changing ratio control. Especially considering PID control may not be effective as object is reaction temperature with notable delay, fuzzy PID control is proposed and then simulated by MATLAB. The result demonstrates that it really improved the control effect. Then specific hardware configuration, network structure and software configuration is also given in order to carry out the system by Siemens PCS7. Keywords: CSTR,PCS7,process control , ,1 引言反应器是任何化学品生产过程中的关键设备,决定了化工产品的品质、品种和生产能 力。
连续釜式反应流程设计
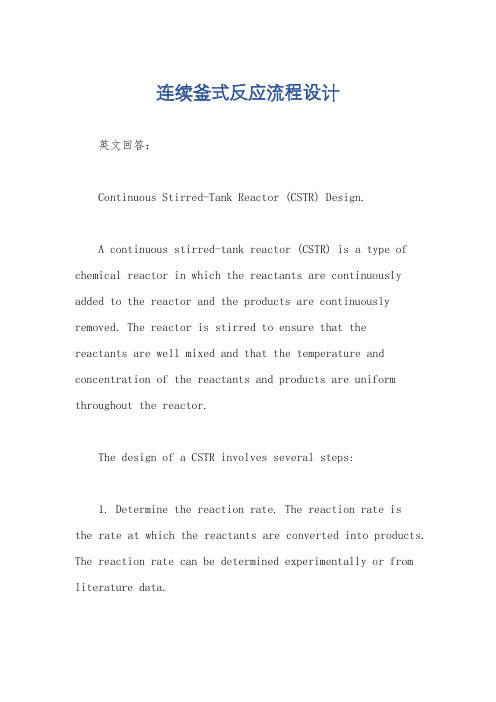
连续釜式反应流程设计英文回答:Continuous Stirred-Tank Reactor (CSTR) Design.A continuous stirred-tank reactor (CSTR) is a type of chemical reactor in which the reactants are continuously added to the reactor and the products are continuously removed. The reactor is stirred to ensure that thereactants are well mixed and that the temperature and concentration of the reactants and products are uniform throughout the reactor.The design of a CSTR involves several steps:1. Determine the reaction rate. The reaction rate isthe rate at which the reactants are converted into products. The reaction rate can be determined experimentally or from literature data.2. Determine the reactor volume. The reactor volume is the volume of the reactor that is required to achieve the desired conversion of reactants into products. The reactor volume can be calculated using the following equation:V = F / (-rA)。
一种聚合反应釜的自动控制系统设计
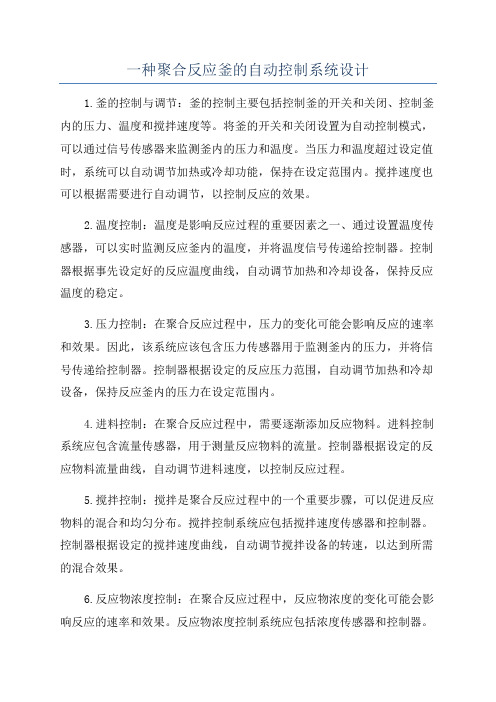
一种聚合反应釜的自动控制系统设计1.釜的控制与调节:釜的控制主要包括控制釜的开关和关闭、控制釜内的压力、温度和搅拌速度等。
将釜的开关和关闭设置为自动控制模式,可以通过信号传感器来监测釜内的压力和温度。
当压力和温度超过设定值时,系统可以自动调节加热或冷却功能,保持在设定范围内。
搅拌速度也可以根据需要进行自动调节,以控制反应的效果。
2.温度控制:温度是影响反应过程的重要因素之一、通过设置温度传感器,可以实时监测反应釜内的温度,并将温度信号传递给控制器。
控制器根据事先设定好的反应温度曲线,自动调节加热和冷却设备,保持反应温度的稳定。
3.压力控制:在聚合反应过程中,压力的变化可能会影响反应的速率和效果。
因此,该系统应该包含压力传感器用于监测釜内的压力,并将信号传递给控制器。
控制器根据设定的反应压力范围,自动调节加热和冷却设备,保持反应釜内的压力在设定范围内。
4.进料控制:在聚合反应过程中,需要逐渐添加反应物料。
进料控制系统应包含流量传感器,用于测量反应物料的流量。
控制器根据设定的反应物料流量曲线,自动调节进料速度,以控制反应过程。
5.搅拌控制:搅拌是聚合反应过程中的一个重要步骤,可以促进反应物料的混合和均匀分布。
搅拌控制系统应包括搅拌速度传感器和控制器。
控制器根据设定的搅拌速度曲线,自动调节搅拌设备的转速,以达到所需的混合效果。
6.反应物浓度控制:在聚合反应过程中,反应物浓度的变化可能会影响反应的速率和效果。
反应物浓度控制系统应包括浓度传感器和控制器。
控制器可以根据浓度传感器测量到的反应物浓度,自动调节进料速度或反应时间,以控制反应物浓度在设定范围内。
以上是一种聚合反应釜的自动控制系统设计,包括釜的控制与调节、温度控制、压力控制、进料控制、搅拌控制和反应物浓度控制等方面。
通过自动控制系统的设计,可以提高反应的稳定性和效率,减少人工操作并降低安全隐患。
连续搅拌釜式反应器

3. 质量检测
本实验中采用电导方法测量反应物A的浓度变化。 对于乙酸乙酯皂化反应,参与导电的离子 有Na+、OH-和CH3COO-。Na+在反应前后浓 度不变,OH-的迁移率远大于CH3COO-的迁移率。随 着反应的进行,OH-不断减少,物 系的电导值随之不断下降。因此,物系的电导值的变化与CH3COOH的浓度变化成正 比,而由电导电极测得的电导率L与其检测仪输出的电压信号U也呈线性关系,则如 下关系式成立:
续搅拌釜式反应器液相反应的速 率常数测定 一、实验目的
本实验采用连续流动搅拌釜式反应器进 行液相反应动力学研究。实验用连续输入 的方法,在定常流动下,测定乙酸乙酯皂 化反应的反应速率和反应速率常数。
二、实验原理
1. 2.
3.
反应速率 反应速率常数 质量检测
1. 反应速率 连续流动搅拌釜式反应器的摩尔衡算基本方程:
FAO-FA-∫0V(-rA)dV=dnA/dt
对于定常流动下的全混流反应器,上式可简化为:
FAO-FA-(-rA)V=0→ (-rA)= FAO-FA /V
对于恒容过程而言,流入反应器的体积流率Vs,0等于流出反应器的体积流率Vs。 若反应物A的起始浓度为CA,0,反应器出口亦即反应器内的反应物A的浓度为 CA,则上式可改写为:(-rA)= (CA,0-CA)/(V/Vs,0)=(CA,0-CA)/τ
2. 标定浓度曲线的实验步骤
3.测定反应速率和反应速率常数的实验步骤
(1)停止加热和搅拌后,将反应器内的纯水放尽。启 动并调定计量泵,同时以等流率向器 内加入料液A和 B。待液面稳定后,启动搅拌器和加热器并控制转速和 温度恒定。当搅拌转速 在600r· min-1时,总体积流率 在2.7~16L· h-1(相当于计量泵显示10~60 r·min-1)范围 内,均可接近全混流。 (2)当操作状态达到稳定之后,按数据采集键,采集 与浓度CA相应的电压信号U。待屏幕 上 显示的曲线平直 之后,按终止采集键,取其平直段的平均值,即为与釜 内最终浓度CA相应 的U值。 (3)改变流量重复上述实验步骤,测得一组在一定温 度下,不同流量时的U值数据。
搅拌反应釜设计范文
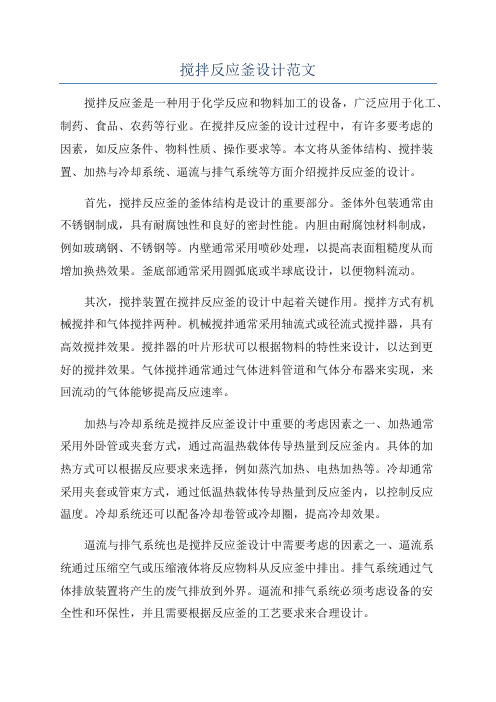
搅拌反应釜设计范文搅拌反应釜是一种用于化学反应和物料加工的设备,广泛应用于化工、制药、食品、农药等行业。
在搅拌反应釜的设计过程中,有许多要考虑的因素,如反应条件、物料性质、操作要求等。
本文将从釜体结构、搅拌装置、加热与冷却系统、逼流与排气系统等方面介绍搅拌反应釜的设计。
首先,搅拌反应釜的釜体结构是设计的重要部分。
釜体外包装通常由不锈钢制成,具有耐腐蚀性和良好的密封性能。
内胆由耐腐蚀材料制成,例如玻璃钢、不锈钢等。
内壁通常采用喷砂处理,以提高表面粗糙度从而增加换热效果。
釜底部通常采用圆弧底或半球底设计,以便物料流动。
其次,搅拌装置在搅拌反应釜的设计中起着关键作用。
搅拌方式有机械搅拌和气体搅拌两种。
机械搅拌通常采用轴流式或径流式搅拌器,具有高效搅拌效果。
搅拌器的叶片形状可以根据物料的特性来设计,以达到更好的搅拌效果。
气体搅拌通常通过气体进料管道和气体分布器来实现,来回流动的气体能够提高反应速率。
加热与冷却系统是搅拌反应釜设计中重要的考虑因素之一、加热通常采用外卧管或夹套方式,通过高温热载体传导热量到反应釜内。
具体的加热方式可以根据反应要求来选择,例如蒸汽加热、电热加热等。
冷却通常采用夹套或管束方式,通过低温热载体传导热量到反应釜内,以控制反应温度。
冷却系统还可以配备冷却卷管或冷却圈,提高冷却效果。
逼流与排气系统也是搅拌反应釜设计中需要考虑的因素之一、逼流系统通过压缩空气或压缩液体将反应物料从反应釜中排出。
排气系统通过气体排放装置将产生的废气排放到外界。
逼流和排气系统必须考虑设备的安全性和环保性,并且需要根据反应釜的工艺要求来合理设计。
另外,搅拌反应釜的设计还需要考虑控制系统和安全系统。
控制系统通常包括温度、压力、搅拌速度等参数的监测和控制。
安全系统通常包括温度、压力、液位等参数的监测和报警装置,以确保设备的安全运行。
总结起来,搅拌反应釜的设计需要综合考虑釜体结构、搅拌装置、加热与冷却系统、逼流与排气系统等因素。
- 1、下载文档前请自行甄别文档内容的完整性,平台不提供额外的编辑、内容补充、找答案等附加服务。
- 2、"仅部分预览"的文档,不可在线预览部分如存在完整性等问题,可反馈申请退款(可完整预览的文档不适用该条件!)。
- 3、如文档侵犯您的权益,请联系客服反馈,我们会尽快为您处理(人工客服工作时间:9:00-18:30)。
河南工业大学开放实验室实验项目设计报告连续搅拌釜式反应器(CTRS)控制系统设计学校:河南工业大学学院:机电工程学院专业:机械设计制造及其自动化姓名:X X X学号:目录1 前言 (2)2 工艺过程简介 (2)2、1 过程变量说明 (3)2、2 操作变量说明 (3)3 反应过程特性 (3)4 实验内容 (5)5 反应过程开车及正常运行 (6)6 开车步骤顺序控制 (7)7 思考题 (8)8 心得体会 (9)连续搅拌釜式反应器(CTRS)控制系统设计1、前言本连续反应过程是工业常见的典型的带搅拌的釜式反应器(CSTR)系统,同时又是高分子聚合反应。
本实验是当前全实物实验根本无法进行的复杂、高危险性实验,又是非常重要的基础反应动力学实验和反应系统控制实验内容。
此外,全实物实验还面临物料消耗、能量消耗、反应产物的处理、废气废液的处理和环境污染问题,以上各项问题比间歇反应更严重,因为连续反应的处理量大大超过间歇过程。
现有的连续反应实验系统实际上都是水位及流量系统,根本没有反应现象。
在本连续反应实验系统上除了进行常规控制系统实验外,还可以进行模糊控制、优化控制、深层知识专家系统(例如SDG法)故障诊断等高级控制实验。
2、工艺过程简介连续反应实验系统以液态丙烯为单体、以液态已烷为溶剂,在催化剂与活化剂的作用下,在反应温度70 1.0℃下进行悬浮聚合反应,得到聚丙烯产品。
在工业生产中为了提高产量,常用两釜或多釜串联流程。
由于在每一个反应釜中的动态过程内容相似,为了提高实验效率、节省实验时间,特将多釜反应器简化为单反应器连续操作系统。
丙烯聚合反应是在己烷溶剂中进行的,采用了高效、高定向性催化剂。
己烷溶剂是反应生成物聚丙烯的载体,不参与反应,反应生成的聚丙烯不溶于单体丙烯和溶剂,反应器内的物料为淤浆状,故称此反应为溶剂淤浆法聚合。
见图1-1所示,连续反应实验系统包括:带搅拌器的釜式反应器。
反应器为标准盆头釜,为了缩短实验时间,必须减小时间常数,亦即缩小反应器容积,缩小后的反应器尺寸为:直径1000 mm,釜底到上端盖法兰高度1376 mm,反应器总容积1.037 m3 ,反应釜液位量程选定为0-1300 mm (0-100%)。
反应器耐压约2.5MPa,为了安全,要求反应器在系统开、停车全过程中压力不超过1.5 MPa。
反应器压力报警上限组态值为1.2 MPa。
丙烯聚合反应过程主要有三种连续性进料(控制聚丙烯分子量的氢气在实验中不考虑),第一种是常温液态丙烯,F4为丙烯进料流量、V4是丙烯进料双效阀;第二种是常温液态己烷,F5己烷进料流量、V5己烷进料阀;第三种是来自催化剂与活化剂配制单元的常温催化剂与活化剂的混合液,F6为催化剂混合液进料流量、V6催化剂混合液进料阀。
催化剂可以用三氯化钛(TiCl3),活化剂可以用一氯二乙基铝(Al(C2H5)2Cl),两种化合物用己烷溶剂稀释成混合液,催化剂浓度4%,活化剂与催化剂克分子浓度之比为2∶1。
由于催化剂量小,常用计量泵控制,在本实验中用精小型控制阀代替。
反应器内主产物聚丙烯重量百分比浓度为A,反应温度为T1,液位为L4。
反应器出口浆液流量F9,出口双效阀V9,出口泵,出口泵开关S5(开关),反应器夹套第一冷却水入口流量F7,双效阀V7,反应器夹套第二冷却水入口流量F8,双效阀V8,反应器夹套加热热水阀S6(开关),反应器搅拌电机开关S8。
2、1 过程变量说明连续反应实验系统在盘面所涉及的传感器输出变量、变量正常工况的数据、计量单位如下。
F4 丙烯进料流量729 kg/hF5 己烷进料流量1540 kg/hF6 催化剂进料流量88 kg/hF7 冷却水流量(第一)25 t/h (最大)F8 冷却水流量(第二)42 t/h (最大)F9 反应器出口流量kg/hT1 反应温度℃P7 反应压力MPa(绝压)L4 反应器料位% (0-1.3m,0-100%)A 出口聚丙烯重量百分比浓度%2、2 操作变量说明连续反应实验系统在盘面所涉及的操作、控制阀门及开关,已注明阀门公称直径、国标流通能力(Kv)如下。
V4 丙烯进料阀Dg25 Kv=3.42 (Cv=4)V5 己烷进料阀Dg25 Kv=5.38 (Cv=6.3)V6 催化剂进料阀Dg20 Kv=0.214 (Cv=0.25)V7 冷却水阀(第一)Dg40 Kv=25.64 (Cv=30)V8 冷却水阀(第二)Dg50 Kv=42.73 (Cv=50)V9 反应器出口阀Dg25 Kv=8.54 (Cv=10)S6 热水加热阀S8 反应器搅拌电机开关3、反应过程特性为了设计和实施有效且高质量的控制,必须首先对连续反应过程的主要变量之间的影响关系和动态特性进行分析,必要时需定量测试。
这些特性、影响关系和数据完全可以通过对本实验系统实施开车、停车或对主要变量进行拉偏试验得到。
然而,在真实系统上,由于安全或经济效益的考虑,多数试验是不允许进行的。
下面对本连续反应过程的特性进行简要介绍。
(1)全混流反应器特征由于本反应器有强烈地搅拌作用,已烷溶剂又起到了很好的分散与稀释功能,使得反应器中的物料流动状态满足全混流假定,即反应器内各点的组成和温度都是均匀的,反应器的出口组成和温度与反应器内相等。
(2)反应停留时间从反应物料进入反应器开始至该反应物料离开反应器为止所历经的时间称为停留时间。
该时间与反应器中实际的物料容积和物料的体积流量有关。
一般来说停留时间长,进料流量小,反应的转化率高。
也就是说为了使出口聚丙烯的浓度提高,必须减少进料和出料流量。
由于本反应器的物料流动状态满足全混流假定,可以采用平均停留时间的方法表达,反应平均停留时间等于反应器中物料实际容积除以反应器中参与反应的物料体积流量。
(3)反应温度丙烯聚合反应属于放热反应,因此,根据反应温度的高低能判断聚合反应速度的快慢。
即当反应速度加快时,放出的热量增加,导致系统温度升高;反之系统温度下降,因为此时出口物料流量和夹套冷却水会带走热量。
放热反应属于非自衡的危险过程,当反应温度过高时,聚合反应速度加快,使得反应放出的热量增加,如果热量无法及时移走,则反应温度进一步升高。
这种“正反馈”作用将导致“暴聚”事故。
此时由于温度超高,系统压力必定超高,如果超过反应器所能耐受的压力,可能发生爆炸与火灾事故。
即使不发生恶性事故,由于反应速度太快,聚合生成的都是低分子无规则状聚合物,产品也不合格。
在反应停留时间相同、催化剂量相同的条件下,聚合反应的转化率由反应温度所决定。
控制反应温度的主要手段是夹套冷却水的流量。
反应温度要求控制在70 1.0℃。
影响夹套冷却作用的相关因素是反应器内料位的高低、冷却水与反应温度的温度差,料位高换热面积大,温度差大热交换推动力大。
反应温度和反应转化率的变化属于时间常数较大、惯性较大的高阶特性。
冷却水流量的变化随阀门的开关变化较快、时间常数较小。
当冷却水压力下降时(这种干扰在现场时有发生),即使阀位不变,冷却水流量也会下降,冷却水带走的热量减少,反应器中物料温度会上升。
由于温度变化的滞后,当传感器和控制器进行调节时,已经滞后了。
针对这一问题,应当选用能够减小滞后影响的控制方案。
例如,串级控制系统的副回路能减少对象的时间常数。
(4)反应压力反应压力的高低主要取决于反应器中丙烯的百分比含量和反应温度。
纯丙烯的饱和蒸汽压在20℃时约为1.0 MPa,70℃时已超过3.0 MPa,温度继续升高,压力还会急剧升高。
用不着达到100℃,本反应器就可能发生爆炸危险。
实践证明丙烯与己烷混合后,饱和蒸汽压会降低,而且在温度不变的前提下,己烷的百分比含量越高,系统压力越低。
因此,在反应器中必须防止丙烯的百分比含量过高、反应温度过高的情况发生。
另外,在温度不变的条件下,调整丙烯与己烷的进料流量比可以在一定的范围内控制反应器内压力。
在丙烯与己烷的进料流量比不变的前提下,反应压力随反应温度变化,即反应温度上升,反应压力也同步上升,反应温度下降,反应压力也同步下降。
亦即,反应压力升高表征着反应速度加快,转化率提高。
图1-1 带搅拌器的釜式反应器(CSTR)图1-2连续反应正常工况流程图画面4、实验内容(1)实验设备及连接1)在上位计算机启动连续反应软件,选择并进入连续反应工程。
2)盘台上线路连接。
(2)控制系统组态1)完成液位L4和温度T1控制系统组态,以便尽快进入测试前的稳定工况。
控制系统组态如图1-3 所示:图1-3控制系统组态对组态图中的PIC参数设置如表1-1所示:表1-1 PID参数控制2)完成趋势画面组态,选择L4、A、T1、P1、V8、V9共计6个变量进行趋势记录。
如图1-4所示:图1-4 趋势画面13)阀门V4、V5、V6、V7、V8、V9选线性特性。
5、反应过程开车及正常运行启动连续反应器实验软件。
完成与连续反应有关的盘面信号线插接。
检查接线是否正确。
要求进行反应器液位L4的控制系统组态。
1)初始化检查,系统处于开车前状态。
2)开V5(己烷进料阀)约60%,使F5(己烷进料流量)达到约1540 kg/h,关注液位L4上升。
由于己烷在常温下饱和蒸汽压较低,反应器内压力不会大幅升高。
如果先加入纯丙烯则反应器内压力会大幅升高。
3)液位L4上升至50%左右,开V4(丙烯进料阀)约55%,使F4(丙烯进料流量)达到约729 kg/h。
由于混合蒸汽压低于纯丙烯饱和蒸汽压,因此避开了反应器内压力大幅升高的可能。
4)当液位L4上升至75%左右,开V9(反应器出口阀)约55%。
应防止液位上升过快,导致液位超限。
5)当液位L4上升至80-90%左右,将L4投自动控制。
注意,为了控制液位稳定,必须在运行前完成本液位单回路控制组态。
应将反应器出口阀V9定义为液位控制输出控制阀,当液位超高时,V9应开大,所以本控制器应设定成正作用。
为了使控制器正常工作,必须对P.I.D.参数进行整定。
6)开S8(反应器搅拌电机开关)。
使物系处于全混状态。
7)开S6(热水加热阀),诱发反应。
热水流入夹套,通过夹套对反应器内物料加热,可见,夹套具有加热和冷却双重作用。
用热水最高可将物系加热到50℃(当物系没有化学反应时)。
8)开V6(催化剂进料阀)约55%,使F6(催化剂进料流量)达到约88 kg/h。
所加入的实际上是催化剂与活化剂的混合液,此时,反应器的三股物料都已按要求连续进入反应器。
由于反应尚未诱发,三股物料的混合物也在连续地流出反应器。
此状态应当尽量短暂,因为没有产品生成,只有能量及物料损耗。
9)当T1(反应温度)达到约40℃,关S6(热水加热阀),若T1继续上升,则反应诱发成功。
由于丙烯聚合是放热反应,反应速度会随温度升高而不断加快。
10)当T1(反应温度)达到约45℃,逐渐以小开度开V8(夹套冷却水阀),为了防止反应温度上升幅度过快而失控,超前进行适当冷却是必要的。