TM1型机车齿轮箱铸件工艺特点分析[1]
矿山机械设备铸件铸造工艺分析

矿山机械设备铸件铸造工艺分析随着经济的发展和社会的进步,矿产资源的挖掘和利用日益广泛,对矿山机械设备的需求也越来越多。
作为矿山机械设备的核心部件,铸件不仅需要具有良好的综合机械性能,还要满足矿山环境的特殊要求。
因此,矿山机械设备铸件的铸造工艺至关重要。
一、材料选择首先,铸造工艺的成功与否与材料的选择密切相关。
矿山机械设备铸件的材料选择应在满足其机械性能和使用要求的基础上,考虑制造成本。
一般来说,铸造材料主要包括铁、钢、铜合金和铝合金。
对于矿山机械设备铸件,因其工作环境的特殊性,大多采用高强度的铸造钢或合金钢。
二、模具制造模具制造是矿山机械设备铸件铸造工艺的重要环节。
模具的质量和制造精度直接影响到铸件的质量和制造周期。
模具制造应根据铸件的形状、尺寸、结构、材料和工艺要求进行设计。
同时,应注意模具的强度、刚度和耐磨性等性能,以确保其使用寿命和生产效率。
三、浇注系统设计浇注系统是指将熔融金属从炉子中输送到模具中并充填模腔的系统。
浇注系统的设计应考虑铸件的凝固过程和金属的充填情况。
在矿山机械设备铸件铸造中,为了减少金属氧化和流动的阻力,一般采用底部浇口或侧面浇口的方式进行浇注。
同时,还应注意浇注口的大小和位置,以确保铸件的充填完整和凝固均匀。
四、熔炼和浇注熔炼和浇注是矿山机械设备铸件铸造过程的核心环节。
在熔炼过程中,应注意金属的温度、化学成分和渣分的控制,以确保其符合工艺要求。
在浇注过程中,应严格控制浇注时间、浇注温度和浇注速度,以避免铸件出现缩孔、孔洞和错型等缺陷。
同时,应避免金属气孔和夹杂物等缺陷的产生。
五、热处理和表面处理矿山机械设备铸件在铸造完成后,还需要经过热处理和表面处理等工序。
热处理可以改善铸件的性能和组织,提高其耐磨性和强度等指标。
表面处理可以改善铸件的表面质量和外观,提高其防腐蚀和耐磨性能。
常见的热处理工艺包括正火、淬火和回火等,常见的表面处理工艺包括喷砂、喷丸和镀锌等。
综上所述,矿山机械设备铸件的铸造工艺涉及到多个环节,需要高度关注每个环节的细节和要求。
某型机车齿轮箱漏油原因分析及改进措施
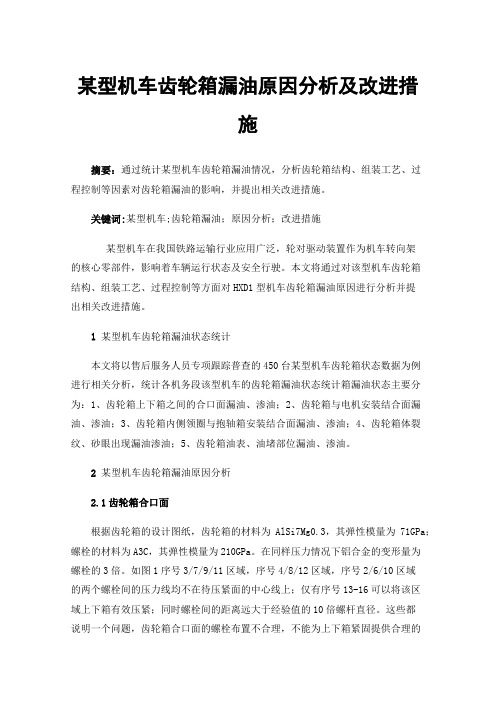
某型机车齿轮箱漏油原因分析及改进措施摘要:通过统计某型机车齿轮箱漏油情况,分析齿轮箱结构、组装工艺、过程控制等因素对齿轮箱漏油的影响,并提出相关改进措施。
关键词:某型机车;齿轮箱漏油;原因分析;改进措施某型机车在我国铁路运输行业应用广泛,轮对驱动装置作为机车转向架的核心零部件,影响着车辆运行状态及安全行驶。
本文将通过对该型机车齿轮箱结构、组装工艺、过程控制等方面对HXD1型机车齿轮箱漏油原因进行分析并提出相关改进措施。
1某型机车齿轮箱漏油状态统计本文将以售后服务人员专项跟踪普查的450台某型机车齿轮箱状态数据为例进行相关分析,统计各机务段该型机车的齿轮箱漏油状态统计箱漏油状态主要分为:1、齿轮箱上下箱之间的合口面漏油、渗油;2、齿轮箱与电机安装结合面漏油、渗油;3、齿轮箱内侧领圈与抱轴箱安装结合面漏油、渗油;4、齿轮箱体裂纹、砂眼出现漏油渗油;5、齿轮箱油表、油堵部位漏油、渗油。
2某型机车齿轮箱漏油原因分析2.1齿轮箱合口面根据齿轮箱的设计图纸,齿轮箱的材料为AlSi7Mg0.3,其弹性模量为71GPa;螺栓的材料为A3C,其弹性模量为210GPa。
在同样压力情况下铝合金的变形量为螺栓的3倍。
如图1序号3/7/9/11区域,序号4/8/12区域,序号2/6/10区域的两个螺栓间的压力线均不在待压紧面的中心线上;仅有序号13-16可以将该区域上下箱有效压紧;同时螺栓间的距离远大于经验值的10倍螺杆直径。
这些都说明一个问题,齿轮箱合口面的螺栓布置不合理,不能为上下箱紧固提供合理的密封性能。
根据该设计图可以预测漏油最初始位置可能为序号3/7区域和4/8区域。
考虑大小齿轮啮合部位气压变化和振动的影响,合口面最容易泄露的位置为3/7区域。
图 1 螺栓紧固应力圆图2.1.1抱轴箱O型圈位置根据设计图,可得出抱轴箱体与齿轮箱的配合间隙为 0.08-0.20mm。
O型圈压缩比大于20%,完全满足静密封要求。
2.1.2电机领圈位置电机领圈与齿轮箱密封依靠O型密封圈和外圈螺栓在平面密封胶的作用下实现,该处设计保证了密封性能。
矿山机械设备铸件铸造工艺分析
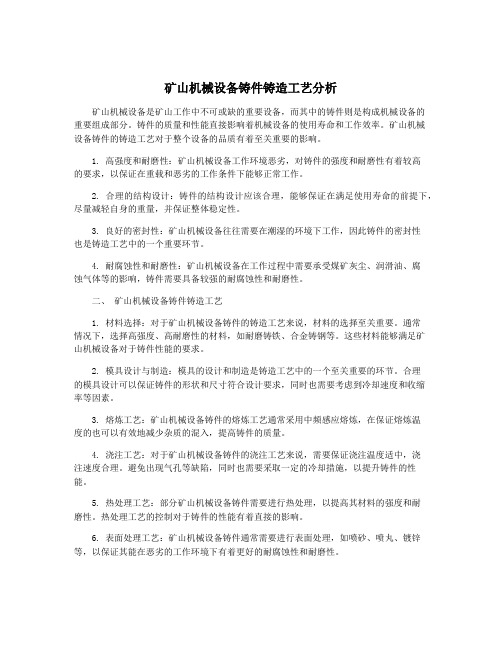
矿山机械设备铸件铸造工艺分析矿山机械设备是矿山工作中不可或缺的重要设备,而其中的铸件则是构成机械设备的重要组成部分。
铸件的质量和性能直接影响着机械设备的使用寿命和工作效率。
矿山机械设备铸件的铸造工艺对于整个设备的品质有着至关重要的影响。
1. 高强度和耐磨性:矿山机械设备工作环境恶劣,对铸件的强度和耐磨性有着较高的要求,以保证在重载和恶劣的工作条件下能够正常工作。
2. 合理的结构设计:铸件的结构设计应该合理,能够保证在满足使用寿命的前提下,尽量减轻自身的重量,并保证整体稳定性。
3. 良好的密封性:矿山机械设备往往需要在潮湿的环境下工作,因此铸件的密封性也是铸造工艺中的一个重要环节。
4. 耐腐蚀性和耐磨性:矿山机械设备在工作过程中需要承受煤矿灰尘、润滑油、腐蚀气体等的影响,铸件需要具备较强的耐腐蚀性和耐磨性。
二、矿山机械设备铸件铸造工艺1. 材料选择:对于矿山机械设备铸件的铸造工艺来说,材料的选择至关重要。
通常情况下,选择高强度、高耐磨性的材料,如耐磨铸铁、合金铸钢等。
这些材料能够满足矿山机械设备对于铸件性能的要求。
2. 模具设计与制造:模具的设计和制造是铸造工艺中的一个至关重要的环节。
合理的模具设计可以保证铸件的形状和尺寸符合设计要求,同时也需要考虑到冷却速度和收缩率等因素。
3. 熔炼工艺:矿山机械设备铸件的熔炼工艺通常采用中频感应熔炼,在保证熔炼温度的也可以有效地减少杂质的混入,提高铸件的质量。
4. 浇注工艺:对于矿山机械设备铸件的浇注工艺来说,需要保证浇注温度适中,浇注速度合理。
避免出现气孔等缺陷,同时也需要采取一定的冷却措施,以提升铸件的性能。
5. 热处理工艺:部分矿山机械设备铸件需要进行热处理,以提高其材料的强度和耐磨性。
热处理工艺的控制对于铸件的性能有着直接的影响。
6. 表面处理工艺:矿山机械设备铸件通常需要进行表面处理,如喷砂、喷丸、镀锌等,以保证其能在恶劣的工作环境下有着更好的耐腐蚀性和耐磨性。
石油机械铸件的铸造特点相关介绍

石油机械铸件的铸造特点相关介绍石油机械铸件是指用于石油工业中的各种机械设备的铸件。
这些铸件大多数是比较大型的铸件,通常需要在高温高压的环境下工作,同时还需要具备高强度和抗腐蚀等特点。
因此,石油机械铸件的铸造工艺相对比较繁琐,需要掌握一定的技术要求和专业知识。
以下将介绍石油机械铸件的铸造特点。
1. 材料选用在石油机械铸件的铸造过程中,材料的选用非常重要。
通常情况下,石油机械铸件采用的铸造材料主要包括高硬度合金铸铁、高温合金和不锈钢等。
这些材料具有较高的强度和抗腐蚀能力,并且能够在高温和高压环境下工作。
因此,在选择铸造材料时,需根据具体的使用条件进行选择,确保材料能够满足使用要求。
2. 铸造工艺在石油机械铸件的铸造过程中,需要掌握一定的铸造工艺。
首先,在铸型制备时需采用耐火材料制作铸型,并且要做好密封工作,防止铸造中的缩孔等问题。
其次,在浇注时需要注意熔体的温度和流速,并且要控制好浇注的时间和位置,确保浇注均匀。
最后,在铸造完成后需进行微观结构分析和缺陷检测等工作,保证铸件的质量。
3. 后续处理在铸造完成后,还需要进行后续处理。
其中,常用的后续处理工艺包括热处理、加工和涂装等。
热处理工艺主要是针对石油机械铸件的材料进行处理,以改善铸件的强度和硬度等性能,并且能够提高铸件的抗腐蚀能力。
加工工艺则是对铸件进行加工,以达到制造要求。
涂装则是对铸件进行表面处理,增加铸件的装饰性和美观性。
4. 铸造特点总的来说,石油机械铸件的铸造特点主要包括以下几个方面:1.产品结构复杂,需要制作复杂的模具和铸型;2.材料具有高强度和抗腐蚀能力,能够在高温高压环境下工作;3.铸件体积较大,常常需要进行分次浇注;4.铸件中常常会存在缩孔、气孔等缺陷,需要进行微观结构分析和缺陷检测等工作。
结语石油机械铸件的铸造特点是比较独特的,需要掌握一定的铸造工艺和专业知识。
通过上述介绍,我们对石油机械铸件的铸造特点有了一定的了解。
当然,由于石油机械铸件的种类和使用条件千差万别,铸造工艺和材料选用也会有所不同。
铸钢齿轮的生产工艺探析

铸钢齿轮的生产工艺探析作者:梁立锋王建发来源:《神州》2012年第26期摘要:通过分析磨机中大齿轮的结构及工艺基准,阐述了铸钢齿轮的加工工艺的制定过程。
关键词:铸钢齿轮;加工工艺;基准目前,市面上生产的各种磨机中,大多采用边缘传动方式。
其特点是用一对大小齿轮啮合,驱动磨机筒体。
由于磨机筒体直径大、转速高、安装方式的要求高,并且大齿轮结构较为复杂性,因此采用何种加工方法,对于齿轮啮合精度,保证传动的平稳及载荷均布是非常重要的。
下面就以φ2.2x6.5m磨机用大齿轮为例,对其机加工工艺的制定作一分析。
1. 大齿轮结构及工艺基准分析φ2.2X6.5m磨机大齿轮材料为ZG310—570,精度等级为9—9—8一JK(JBl79—83),参数为尺数Z:158;模数Mn:22;压力角a:20o;齿项系数X:2.7;齿顶圆直径为Da3622.87mm;主要结构尺寸精度如图1。
从图中精度要求及根据大齿轮安装需要,基准圆直径为φ2440+0.440,同时基准端面出B 和C与A的位置偏差将影响到8一φ38孔位置基准的精确性,也将影响大齿轮安装精度,进而也就影响磨机筒体的运转工况。
2.主要工序过程的制定大齿轮是一个大型铸件,加工余量较大,由于是两半组合成一体,因此半齿圈铸件也极易发生变形。
为保证工件各部分加工余量,首先必须安排划线工序,其目的除了为加工连接对口划出找正基准,也为各端面、外圆等划出加工线,同时也能够检验毛坯是否够加工。
在将工件两分体组合到一起时,要按已划好的端面线、圆线找正。
划、钻连接孔。
销钉孔,并用螺栓连接好。
组对好后,在立式车床上加工内外圆及各端面。
这里在车削过程中及加工完以后工件不变形,各部位尺寸,形状,位置等精度达到图纸要求,具体可按下述方法进行加工。
(1)以毛坯光面为基准,放在可调整垫铁上,按已划好的端面线,圆线及对口找正,用盘爪装卡粗车能加工部位,留量5mm,调个后粗车剩余部位,留量5mm;(2)将工件移离车床,放在平台上,松开对口螺栓,使工件自然变形24小时以上,其目的是消除工件粗加工之后的内应力;’(3)重新紧固螺栓、铰制销、装配销钉;(4)将工件平放在等高垫铁上,装卡φ3446;圆按已加工好的各面及对口找正(夹紧力不必过大,以防止变形);(5)精车各部位达图纸要求,并用尖刀划出节圆线,此时加工好φ2440内孔及端面即可作为安装基准;在车削工序完成之后,即进行齿形加工。
机车牵引齿轮箱有限元分析及结构优化
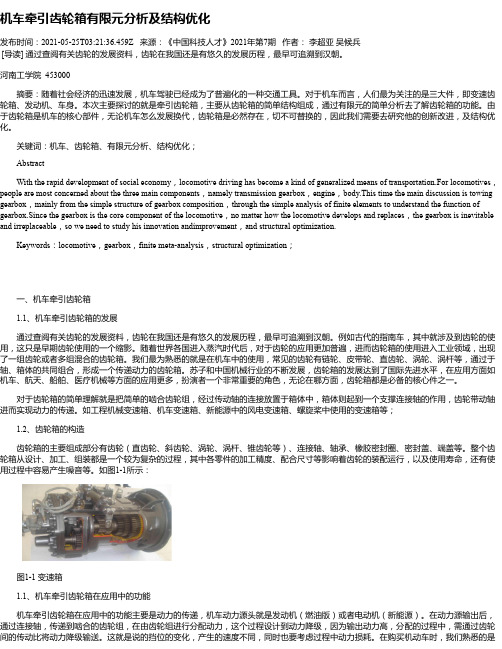
机车牵引齿轮箱有限元分析及结构优化发布时间:2021-05-25T03:21:36.459Z 来源:《中国科技人才》2021年第7期作者:李超亚吴候兵[导读] 通过查阅有关齿轮的发展资料,齿轮在我国还是有悠久的发展历程,最早可追溯到汉朝。
河南工学院 453000摘要:随着社会经济的迅速发展,机车驾驶已经成为了普遍化的一种交通工具。
对于机车而言,人们最为关注的是三大件,即变速齿轮箱、发动机、车身。
本次主要探讨的就是牵引齿轮箱,主要从齿轮箱的简单结构组成,通过有限元的简单分析去了解齿轮箱的功能。
由于齿轮箱是机车的核心部件,无论机车怎么发展换代,齿轮箱是必然存在,切不可替换的,因此我们需要去研究他的创新改进,及结构优化。
关键词:机车、齿轮箱、有限元分析、结构优化;AbstractWith the rapid development of social economy,locomotive driving has become a kind of generalized means of transportation.For locomotives,people are most concerned about the three main components,namely transmission gearbox,engine,body.This time the main discussion is towing gearbox,mainly from the simple structure of gearbox composition,through the simple analysis of finite elements to understand the function of gearbox.Since the gearbox is the core component of the locomotive,no matter how the locomotive develops and replaces,the gearbox is inevitable and irreplaceable,so we need to study his innovation andimprovement,and structural optimization.Keywords:locomotive,gearbox,finite meta-analysis,structural optimization;一、机车牵引齿轮箱1.1、机车牵引齿轮箱的发展通过查阅有关齿轮的发展资料,齿轮在我国还是有悠久的发展历程,最早可追溯到汉朝。
机械齿轮加工工艺分析

机械齿轮加工工艺分析经济新常态下,机械制造企业迎来了全新的发展机遇,尤其是随着机械制造技术水平的不断提高,对机械齿轮加工工艺也提出了全新要求。
只有在机械齿轮运行完整与精准的前提下,才能确保整个机械制造系统的常态化运行,可见其重要地位。
但就现状来讲,机械齿轮加工还存在许多问题,一定程度地制约了机械制造行业的健康发展。
对此,本文在简要阐述机械齿轮加工现状的基础上,分析了其加工过程中存在的问题,并针对性地提出了相应工艺的应用要点,以期广大业内同仁提供一定启发。
标签:机械制造;齿轮加工;现实问题;应用要点21世纪以来,随着我国市场结构的升级转型,机械制造业也同样迎来了属于自己的春天。
在机械制造实践中,齿轮无疑扮演着至关重要的角色,它是决定整个机械共工程能否顺利运转的根本所在,但就国内齿轮加工现状来讲,工艺质量尚无法满足现实发展要求,一定程度地制约了机械制造行业的健康发展。
因此加强机械齿轮加工工艺优化对策的研究,具有非常重要的现实意义和指导价值。
1、机械齿轮基本介绍在整个机械设备的构成系统中,齿轮的功能作用十分突出,某种意义上讲,机械齿轮决定着整个机械设备能否正常运转。
就机械齿轮的机构来讲,主要分为轮齿、齿槽、齿面和齿圆四大构件,而就齿轮类型来讲,我们可依据具体的参数进行相应的划分,具体如下:1.1 齿轮齿形。
以齿形的不同来划分的话,齿轮主要分为渐开线齿轮、大压力角齿轮、小压力角齿轮和摆线齿轮等。
其中的渐开线齿轮生产成本较低,有着非常广泛的应用范围。
而大压力角齿轮有着较强的结构稳定性,可确保机械设备的持续化运转,因此也有着较为广泛的应用。
但相比于这两类齿轮,摆线齿轮因生产工艺要求较高,所以应用范围也相对有限,而小压力角齿轮因抗压性较弱,破损率较高,同样限制了其广泛应用。
1.2 齿轮外形。
以齿轮不同外形进行划分的话,机械齿轮主要分为圆形齿轮、直线齿轮、锥形齿轮和斜线齿轮等。
1.3 齿轮表面。
以齿轮不同表面进行划分的话,机械齿轮主要分为外部齿轮和内部齿轮两种。
浅谈机车齿轮箱加工工艺的改进

浅谈机车齿轮箱加工工艺的改进机车齿轮箱是转向架驱动单元里的主要配件,该车型齿轮箱中设有各种油槽,将齿轮旋转飞溅起的部分润滑油引流到尺侧抱轴承箱轴承室和电机输出端轴承室,以润滑和冷却轴承。
因此齿轮箱的使用性能和安全性能很高,产品的结构复杂,生产制造要求精度高,不易加工,加工质量一直不稳定,严重影响组装质量。
1 现状调查针对影响和谐机车齿轮箱一次交检合格率的10个检查项点,抽查某月生产的60件产品进行跟踪检查,并对其合格情况进行了统计,其加工一次交检合格率仅为70.67%。
上、下箱体错箱尺寸超差73.86%,是影响HXD2齿轮箱加工一次交检合格率的主要问题。
2 原因分析运用头脑风暴法从人、机、料、法、环五个方面寻找由于上、下箱体错箱尺寸超差造成的齿轮箱质量不合格的原因,并绘制出因果分析图(见图1),从因果分析图中收集所有末端因素进行原因分析。
2.1 培训效果未达到要求做为生产一线单位,查阅关键工序——铣镗工序操作人员的教育培训档案,对操作工熟悉、掌握工艺规程和工艺文件程度进行了打分评定。
检查结果:已对员工进行了培训,并进行了考试,技术理论平均83.4分,质量知识平均85.6分,实际操作平均89.7分,操作工对工艺规程、工艺文件掌握良好。
符合要求。
2.2 机床设备使用频率高由于车间每月的生产任务十分繁忙,相对于机床设备的使用频率高,工作负荷大。
有时为保证生产进度,每天机床的使用时间在20个小时以上,所以对(MCX1000)型卧式加工中心进行了设备精度检验,对运转精度误差进行检测,并对检测的实际情况进行了记录。
检查结果:人员按照保养手册保养;(MCX1000)型卧式加工中心运转精度误差<0.01mm。
符合要求。
2.3 上、下箱合箱任意匹配小组成员仔细研究了HXD2齿轮箱机械加工的工艺规程,齿轮箱加工的精度要求比较高,上、下箱合箱不能任意匹配。
检查结果:通过对现有产品10件产品统计(见表1),任意匹配的合格率仅为30%,因此现有工艺不能满足加工质量要求。