粉末与粘结剂
粉末冶金
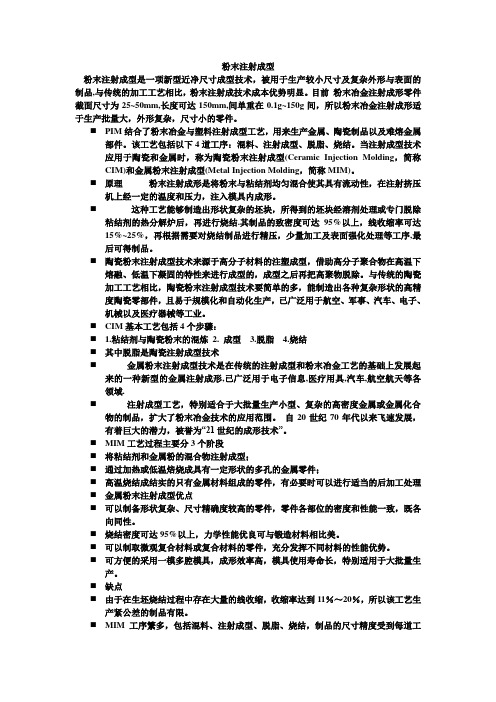
粉末注射成型粉末注射成型是一项新型近净尺寸成型技术,被用于生产较小尺寸及复杂外形与表面的制品,与传统的加工工艺相比,粉末注射成技术成本优势明显。
目前粉末冶金注射成形零件截面尺寸为25~50mm,长度可达150mm,间单重在0.1g~150g间,所以粉末冶金注射成形适于生产批量大,外形复杂,尺寸小的零件。
⏹PIM结合了粉末冶金与塑料注射成型工艺,用来生产金属、陶瓷制品以及难熔金属部件。
该工艺包括以下4道工序:混料、注射成型、脱脂、烧结。
当注射成型技术应用于陶瓷和金属时,称为陶瓷粉末注射成型(Ceramic Injection Molding,简称CIM)和金属粉末注射成型(Metal Injection Molding,简称MIM)。
⏹原理粉末注射成形是将粉末与粘结剂均匀混合使其具有流动性,在注射挤压机上经一定的温度和压力,注入模具内成形。
⏹这种工艺能够制造出形状复杂的坯块,所得到的坯块经溶剂处理或专门脱除粘结剂的热分解炉后,再进行烧结.其制品的致密度可达95%以上,线收缩率可达15%~25%,再根据需要对烧结制品进行精压,少量加工及表面强化处理等工序,最后可得制品。
⏹陶瓷粉末注射成型技术来源于高分子材料的注塑成型,借助高分子聚合物在高温下熔融、低温下凝固的特性来进行成型的,成型之后再把高聚物脱除。
与传统的陶瓷加工工艺相比,陶瓷粉末注射成型技术要简单的多,能制造出各种复杂形状的高精度陶瓷零部件,且易于规模化和自动化生产,已广泛用于航空、军事、汽车、电子、机械以及医疗器械等工业。
⏹CIM基本工艺包括4个步骤:⏹ 1.粘结剂与陶瓷粉末的混炼2. 成型 3.脱脂 4.烧结⏹其中脱脂是陶瓷注射成型技术⏹金属粉末注射成型技术是在传统的注射成型和粉末冶金工艺的基础上发展起来的一种新型的金属注射成形,已广泛用于电子信息,医疗用具,汽车,航空航天等各领域.⏹注射成型工艺,特别适合于大批量生产小型、复杂的高密度金属或金属化合物的制品,扩大了粉末冶金技术的应用范围。
MIM粉末注射制造工艺
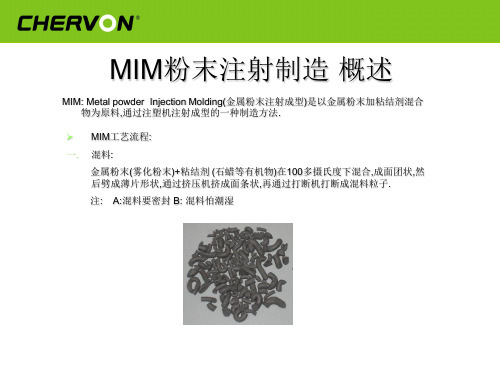
二.成形: 成形: 混料在150℃形成液体,通过注射成形机成形,成形好后将胶口及飞边去掉(该状态和面团一样, 混料在150℃形成液体,通过注射成形机成形,成形好后将胶口及飞边去掉(该状态和面团一样,刀 片可以刮) 片可以刮)
三.脱脂: 脱脂: 将成形好的工件埋在氧化铝粉里,然后放在脱脂炉里,以氢气为燃料,氨气为保护气, 将成形好的工件埋在氧化铝粉里,然后放在脱脂炉里,以氢气为燃料,氨气为保护气, 较高温脱脂. 较高温脱脂. 注:A:氧化铝粉的目的是使工件收热均匀. B:氨气的目的是防止工件氧化. :A:氧化铝粉的目的是使工件收热均匀. B:氨气的目的是防止工件氧化. 四.烧结: 烧结: 将脱脂好的工件整齐放在陶瓷托架上,脱架放在钼舟(M 将脱脂好的工件整齐放在陶瓷托架上,脱架放在钼舟(MO)上,然后放在烧结炉里,以氢气为燃料,氨 然后放在烧结炉里,以氢气为燃料, 气为保护气,1200℃ 1300℃高温烧结. 气为保护气,1200℃-1300℃高温烧结.
二.公差: 公差: MIM烧结时尺寸变化是各向同性的,即在各个方向上尺寸变化是一致的. MIM烧结时尺寸变化是各向同性的,即在各个方向上尺寸变化是一致的. 精度一般在IT11级 个别精度可达IT10级 标准公差如小表: 精度一般在IT11级,个别精度可达IT10级,标准公差如小表:
三.材料: 材料: 材料的选择主要由设计所要求的性能所决定,如强度,硬度,耐磨性等. 材料的选择主要由设计所要求的性能所决定,如强度,硬度,耐磨性等. 常用材料见下表: 常用材料见下表:
MIM粉末注射制造 MIM粉末注射制造 概述
MIM: Metal powder Injection Molding(金属粉末注射成型)是以金属粉末加粘结剂混合 Metal Molding(金属粉末注射成型) 物为原料,通过注塑机注射成型的一种制造方法. 物为原料,通过注塑机注射成型的一种制造方法. MIM工艺流程: MIM工艺流程: 一. 混料: 混料: 金属粉末(雾化粉末)+粘结剂 石蜡等有机物) 100多摄氏度下混合,成面团状, 金属粉末(雾化粉末)+粘结剂 (石蜡等有机物)在100多摄氏度下混合,成面团状,然 后劈成薄片形状,通过挤压机挤成面条状,再通过打断机打断成混料粒子. 后劈成薄片形状,通过挤压机挤成面条状,再通过打断机打断成混料粒子. 注: A:混料要密封 A:混料要密封 B: 混料怕潮湿
石粉用途 主要用途

石粉用途主要用途石粉是一种由石块破碎、研磨而成的细粒度无机粉末,它具有多种用途,广泛应用于各个领域。
下面我将详细介绍石粉的主要用途。
1. 建筑材料:石粉可以用作建筑材料的添加剂,混合在水泥、砂浆、混凝土等建筑材料中,提高其密实性和强度。
石粉中的细小颗粒可以填充材料中的微小孔隙,增加材料的紧密程度,提高材料的耐久性和抗压强度。
2. 粘结剂:石粉可以通过与水反应生成石灰浆,用来制作粘结剂。
石灰浆具有较高的黏性和耐久性,可以用于修补石材表面、粘接陶瓷瓷砖等。
3. 紫外线吸收剂:石粉中含有大量的金属离子,这些离子可以吸收紫外线,起到保护作用。
因此,石粉常被用于制作紫外线吸收剂,用于眼镜镜片、汽车玻璃等产品。
4. 涂料:石粉可以用作涂料的填料或颜料,它可以改善涂料的流动性、抗堆积性和遮盖力。
石粉还可以用来调整涂料的颜色和光泽,改善涂层的质感。
5. 塑料和橡胶制品:石粉可以与塑料和橡胶共混,用作填充剂。
它可以提高塑料和橡胶的强度、硬度和耐磨性,减少产品的成本。
此外,石粉还可以提高塑料和橡胶的绝缘性能和耐候性。
6. 纸张制品:石粉可以用作纸张制品的填料,如书写纸、包装纸、卡纸等。
它可以增加纸张的光泽度、平滑度和印刷性能,减少纸张的成本。
7. 食品添加剂:石粉可以用作食品的增稠剂、稳定剂和抗结剂。
它可以提高食品的质感和口感,增加食品的保鲜期,改善食品的外观和口感。
8. 玻璃制品:石粉可以用作玻璃制品的原料,如玻璃纤维、玻璃管、玻璃容器等。
它可以提高玻璃的透明度、强度和耐热性。
9. 化妆品:石粉可以用作化妆品的填料和稳定剂,如粉底、散粉、眼影等。
它可以调节化妆品的质地和光泽,提高化妆品的延展性和持久性。
10. 橡塑制品:石粉可以加入橡胶制品中,以提高其强度、硬度和耐磨性。
比如橡胶管、橡胶密封件等。
总之,石粉具有广泛的用途,可以在建筑、化工、食品、医药、化妆品等各个领域发挥作用。
随着科学技术的不断发展,石粉的应用范围还将进一步扩大。
粘结粉的配方和用途

粘结粉的配方和用途粘结粉是一种化学物质,主要由树脂、填充物和添加剂组成。
它通常以粉末形式存在,可以根据不同的需要和用途调整配方。
下面将重点介绍粘结粉的配方和主要用途。
粘结粉的配方可以根据具体的使用要求进行调整。
一般来说,树脂是粘结粉的主要成分,可以使用天然树脂或人工合成的树脂。
常用的树脂有乙烯基醇类树脂、丙烯酸酯类树脂、酚醛树脂等。
树脂的选择取决于粘结的材料和使用环境的要求。
填充物是粘结粉中的重要组成部分,可以增加粘结力和稠度。
常见的填充物有石英粉、滑石、硅酸钙、氧化锌等。
添加剂的作用是改善粘结粉的性能和加工性能,常用的添加剂有增稠剂、流动剂、固化剂等。
粘结粉的用途非常广泛。
下面将介绍常见的几种用途。
1. 木工粘结:粘结粉可以用于木工行业的胶合剂制作。
木工胶是粘结木材的常用材料,可以用于制作家具、地板、门窗等。
粘结粉可以提供强大的粘结力和耐水、耐黄变等性能,使得木材在加工和使用过程中能够保持良好的粘结性能。
2. 纸张粘接:用于纸张粘接的粘结粉可以提供较强的粘结力和耐湿性,广泛应用于纸张和纸板的制造过程中。
它可以使得纸张在印刷、包装、制造等过程中保持良好的粘结效果,增加纸张的强度和稳定性。
3. 包装和标签:粘结粉也广泛应用于包装和标签行业。
它可以用于制作各种粘性胶带、黏合剂、胶水等,用于包装、封箱、固定标签等。
粘结粉可以提供良好的粘结力和附着力,使得包装和标签在运输和使用过程中保持稳定。
4. 胶粘剂:粘结粉被广泛应用于胶粘剂制造行业。
胶粘剂可以用于制作各种胶水、胶带、剪纸胶等,用于书籍装订、工艺品制作、家庭装潢等。
粘结粉可以提供良好的附着力、耐高温性和耐化学性,使得胶粘剂在各种环境中保持稳定。
5. 建筑粘接:粘结粉也可以应用于建筑行业,用于各种建筑材料的粘接。
例如,水泥粘结剂可以用于粘结砖块、瓷砖、石材等。
粘结粉可以在施工过程中提供强大的粘结力和抗水性,使得建筑材料能够保持稳定和耐久。
总之,粘结粉是一种广泛应用于各个行业的化学物质。
陶瓷干压成型粘结剂 制备
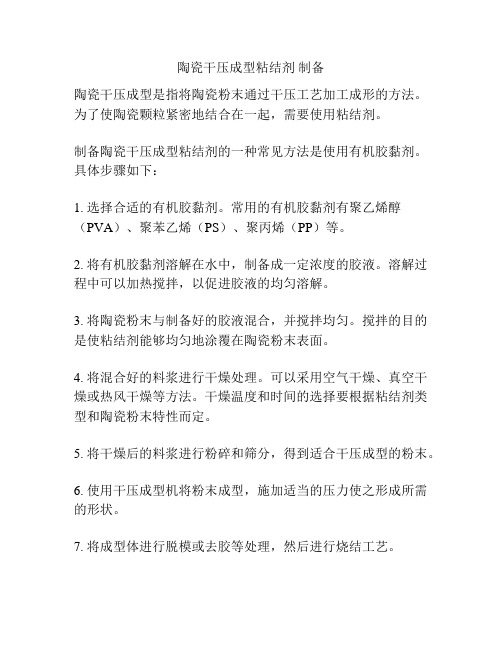
陶瓷干压成型粘结剂制备
陶瓷干压成型是指将陶瓷粉末通过干压工艺加工成形的方法。
为了使陶瓷颗粒紧密地结合在一起,需要使用粘结剂。
制备陶瓷干压成型粘结剂的一种常见方法是使用有机胶黏剂。
具体步骤如下:
1. 选择合适的有机胶黏剂。
常用的有机胶黏剂有聚乙烯醇(PVA)、聚苯乙烯(PS)、聚丙烯(PP)等。
2. 将有机胶黏剂溶解在水中,制备成一定浓度的胶液。
溶解过程中可以加热搅拌,以促进胶液的均匀溶解。
3. 将陶瓷粉末与制备好的胶液混合,并搅拌均匀。
搅拌的目的是使粘结剂能够均匀地涂覆在陶瓷粉末表面。
4. 将混合好的料浆进行干燥处理。
可以采用空气干燥、真空干燥或热风干燥等方法。
干燥温度和时间的选择要根据粘结剂类型和陶瓷粉末特性而定。
5. 将干燥后的料浆进行粉碎和筛分,得到适合干压成型的粉末。
6. 使用干压成型机将粉末成型,施加适当的压力使之形成所需的形状。
7. 将成型体进行脱模或去胶等处理,然后进行烧结工艺。
需要注意的是,在制备陶瓷干压成型粘结剂时,要选择与陶瓷粉末相容的粘结剂,并合理控制粘结剂的浓度,以保证成型后的陶瓷材料具有良好的力学性能和稳定的尺寸。
此外,制备过程中要注意控制干燥温度,以避免粘结剂的热失效。
粉末冶金原理

粉末冶金原理粉末冶金是一种利用金属粉末或者金属粉末与非金属粉末混合后,再经过压制和烧结等工艺制造金属零件的方法。
在粉末冶金工艺中,粉末的特性和原理起着至关重要的作用。
粉末冶金原理主要包括粉末的制备、成型、烧结和后处理等几个方面。
首先,粉末的制备是粉末冶金的第一步。
金属粉末的制备可以通过机械研磨、化学方法和物理方法等多种途径。
机械研磨是指将金属块或者金属棒经过研磨机械的加工,得到所需的金属粉末。
化学方法则是通过化学反应得到金属粉末,而物理方法则是通过物理手段如电解、喷雾等得到金属粉末。
在粉末冶金中,粉末的制备质量直接影响着最终制品的质量和性能。
其次,成型是指将金属粉末进行成型工艺,使其成为所需形状的工件。
成型方法包括压制成型、注射成型、挤压成型等多种方式。
压制成型是将金属粉末放入模具中,再经过压制机械的加工,使其成为所需形状的工件。
注射成型则是将金属粉末与粘结剂混合后,通过注射成型机械将其注射成型。
挤压成型是将金属粉末放入容器中,再通过挤压机械的作用,使其成为所需形状的工件。
成型工艺的精密度和成型质量对于最终产品的质量和性能至关重要。
接下来,烧结是粉末冶金中的关键工艺。
烧结是指将成型后的金属粉末在高温下进行加热处理,使其颗粒间发生结合,形成致密的金属材料。
烧结工艺的温度、压力和时间等参数对于最终产品的致密度、硬度和耐磨性等性能有着重要影响。
最后,后处理是指对烧结后的金属制品进行表面处理、热处理和精加工等工艺。
表面处理可以提高金属制品的耐腐蚀性和美观度,热处理可以改善金属制品的硬度和强度,精加工则可以提高金属制品的精度和表面质量。
总之,粉末冶金原理是一个复杂而又精密的工艺体系,涉及到材料科学、机械工程、化学工程等多个领域的知识。
通过对粉末的制备、成型、烧结和后处理等环节的深入研究和探索,可以不断提高粉末冶金工艺的精度和效率,为制造业的发展和进步提供更加可靠的技术支持。
粘结剂的分类:

粘结剂的分类:蜡基粘结剂;油基粘结剂;油加蜡基粘结剂;聚醛基粘结剂;蜡基粘结剂的组成:蜡+PP.PE.EVA+其他添加剂典型例子:PW+LDPE+SAPW+CW+LDPE+SAAW+LDPE+SA+DEP(增塑)PW+HDPE+SA 难度稍大PW+HDPE+EVA+SA=79:5:20:1 EVA过多容易造成开裂AW.CW国内难买到PW+BW+PE+SA油基粘结剂油+PS.PP.PE等+SA等耦合剂不能热脱脂(粘结剂组成决定脱脂方式)oil+PP+PE+SA=44:44:6:6 用于不锈钢美国专利oil+PP+PS=1:1:1 钨合金可快速脱脂保型性好混合难度大,温度达到250度以上适合粗大颗粒聚醛基粘结剂---德国BASF粘结剂离子表面活性剂+20-35%聚缩醛+10%其他粘结剂组元(LDPE.PP.EVA.PW.SA)+0.5-2.0%润滑剂+增塑剂(蜡。
聚硅酮等)+0.05-1%松弛剂聚缩醛:热固性;无支链聚合物解聚,加热时产生均匀挥发,同时不产生结构上的变形,无残留灰分适用于不锈钢。
陶瓷。
硬质合金(不太适合,碳含量过高,导致致密度不高,95%)水溶性粘结剂包括纤维素基,sps固体聚合物溶液和PEG基水溶液1.纤维素基粘结剂环保在陶瓷体系中使用更多分散剂(润湿颗粒表面)+具有交叉链节结构的聚合物+溶剂(水)特点:粉末含量高,脱脂时间短,毛坯强度高,稳定性好2。
sps固体聚合物溶液大量PEG(技术关键,随分子量的不同,性质不同)+少量的聚合物8PEG600+8PEG1000+64PEG1500+20PMMAPEG+POM(PVB)适合陶瓷涡轮盘刀刃凝胶水基粘结剂注射温度低(40度)提高磨具寿命流动性好,混料温度低于100度70分散剂+1-6琼脂+15-30水、酒精溶剂+润滑剂+润滑剂(甘油,减少液相载体的蒸发压)丙烯酸基粘结剂PAA+甘油+非反应性粘结剂(水、甲基纤维素、甘油、硼酸)使用:雾化、炭基Fe粉热固性粘结剂选择原则:1、固化温度:低于缩聚物的沸点,否则造成气体孔洞 2、在一定范围内,保持流变性各组元的作用:1、甘油:提高缩聚物沸点2、脲醛树脂。
htcc和ltcc的工艺流程

htcc和ltcc的工艺流程HTCC(高温共烧陶瓷)和LTCC(低温共烧陶瓷)是两种常见的陶瓷工艺流程。
本文将介绍它们的工艺流程及其特点。
一、HTCC工艺流程HTCC是一种高温共烧陶瓷工艺,其主要特点是在高温条件下进行烧结。
下面是HTCC的工艺流程:1. 材料准备:HTCC的主要原料是陶瓷粉末,如氧化铝、氧化锆等。
这些粉末需要经过筛选、混合等步骤,确保粉末的均匀性和纯度。
2. 成型:将混合好的陶瓷粉末与粘结剂混合,形成可塑性的糊状物料。
然后,将糊状物料通过注射成型、挤压成型等方式,得到需要的陶瓷零件形状。
3. 除蜡:成型后的陶瓷零件上会有粘结剂和蜡,需要通过高温烘烤的方式将其除去,得到纯净的陶瓷零件。
4. 烧结:将除蜡后的陶瓷零件放入高温炉中进行烧结。
在高温下,陶瓷粉末会发生化学反应,颗粒之间会相互融合,形成致密的陶瓷结构。
5. 表面处理:烧结后的陶瓷零件可能会出现一些表面缺陷,需要通过研磨、抛光等方式进行处理,提高表面的平整度和光洁度。
6. 检测和包装:对成品进行检测,确保其质量符合要求。
然后,将合格的陶瓷零件进行包装,以便运输和使用。
二、LTCC工艺流程LTCC是一种低温共烧陶瓷工艺,其主要特点是在相对较低的温度下进行烧结。
下面是LTCC的工艺流程:1. 材料准备:LTCC的主要原料也是陶瓷粉末,但相比HTCC工艺,LTCC的陶瓷粉末需要更细的颗粒大小和更高的纯度。
因此,材料准备步骤更为严格。
2. 成型:与HTCC类似,LTCC也需要将陶瓷粉末与粘结剂混合,形成可塑性的糊状物料。
然后,通过压延、切割等方式,得到所需的薄片或细丝状的陶瓷零件。
3. 堆叠:将成型好的薄片或细丝状陶瓷零件进行堆叠,形成多层结构。
在堆叠的过程中,需要在每层之间涂覆粘结剂,以确保各层之间的粘合。
4. 烧结:将堆叠好的陶瓷零件放入烧结炉中进行烧结。
与HTCC不同的是,LTCC的烧结温度较低,通常在1000°C左右。