生产线中在制品库存数量的改善——以A公司为例
第五章:精益生产--精益布局
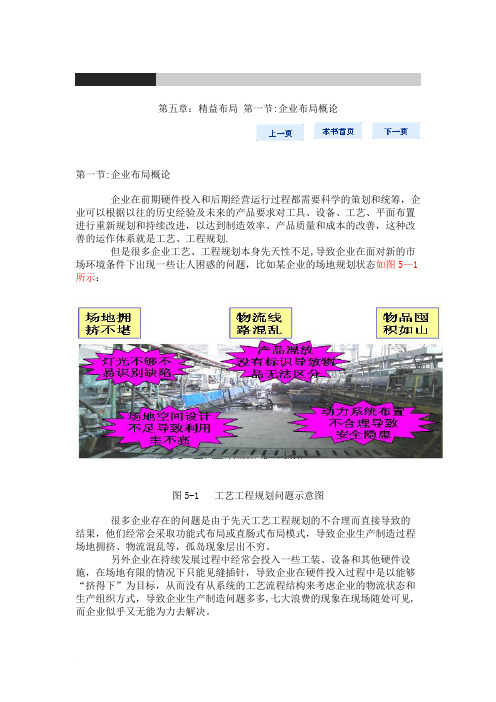
第五章:精益布局第一节:企业布局概论第一节:企业布局概论企业在前期硬件投入和后期经营运行过程都需要科学的策划和统筹,企业可以根据以往的历史经验及未来的产品要求对工具、设备、工艺、平面布置进行重新规划和持续改进,以达到制造效率、产品质量和成本的改善,这种改善的运作体系就是工艺、工程规划.但是很多企业工艺、工程规划本身先天性不足,导致企业在面对新的市场环境条件下出现一些让人困惑的问题,比如某企业的场地规划状态如图5—1所示:图5-1 工艺工程规划问题示意图很多企业存在的问题是由于先天工艺工程规划的不合理而直接导致的结果,他们经常会采取功能式布局或直肠式布局模式,导致企业生产制造过程场地拥挤、物流混乱等,孤岛现象层出不穷。
另外企业在持续发展过程中经常会投入一些工装、设备和其他硬件设施,在场地有限的情况下只能见缝插针,导致企业在硬件投入过程中是以能够“挤得下”为目标,从而没有从系统的工艺流程结构来考虑企业的物流状态和生产组织方式,导致企业生产制造问题多多,七大浪费的现象在现场随处可见,而企业似乎又无能为力去解决。
我们来看一家企业的生产现场布局结构模拟图5-2所示:图5-2 传统布局结构运行示意图通过对企业的现状布局结构进行改善,分析过程的七大浪费环节,建立一个流畅、精益的布局规划,从而为企业实现单件流模式提供条件,如图5—3所示。
图5-3 现代布局结构运行示意图精益专家解析:传统布局结构没有考虑到生产制造过程中的工艺路线的紧密程度和生产组织过程中的流动要求,严重制约着企业精益物流的运行和精益制造模式的建立,对企业生产制造现场的管理带来了很大的难度,现场混乱不堪、物流资源耗费巨大、场地拥挤无序等现象严重阻碍了“单件流”的实现,整个制造周期由于传统的布局结构而无法得到有效改善。
企业可以用“单件流”的思想实现企业现场精益布局来克服企业制造过程中所面对的问题.【读书心得】第二节: 传统布局解析国内很多企业是在社会主义市场经济刚刚建立之初才组建起来,在特定的历史环境条件下,企业面对的市场环境比较特殊,没有激烈的竞争压力,产品系列比较单一,生产规模比较小,在公司筹建的过程中没有对设备、厂房等硬件的配置和布局进行整体规划。
生产七大浪费及改善八大步骤
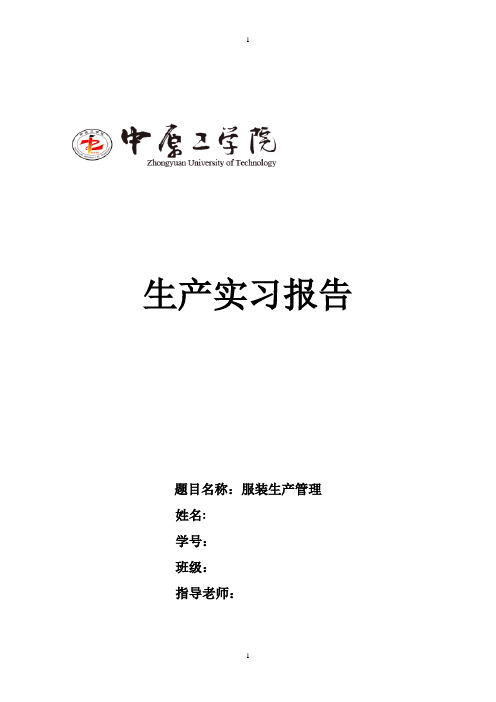
生产实习报告题目名称:服装生产管理姓名:学号:班级:指导老师:企业中普遍存在的八大浪费涉及过量生产、等待时间、运输、库存、过程(工序)、动作、产品缺陷以及忽视员工创造力,在生活中的现象和改善方法具体如下:1.、等待的浪费:即等着下一动作的来临。
造成原因常例如生产线的品种切换、作业不平衡、上下工序延误,下游无事可做、时常缺料设备闲置、品质不良、修机,制造通知或设计图未送到等。
改善:不要监视机器、不要巡逻救生、不要袖手旁观2.、搬运的无驮:搬运的动作分解开来,包含放置、堆积、移动、整理等动作,是传统的机能别水平式的布置造成的。
若使用输送带、无人搬运车不是搬运的合理化。
增加搬运批量、以及减少搬运频率、也不是合理化的搬运。
改善:不要乱流、不要粗流、不要停留3.、不良的浪费:任何的不良品产生,皆造成材料、机器、人工等的浪费。
造成原因为制程能力不足的技术层有问题及生产现物管理方式或管理观念错误所造成。
改善:不接受不良品、不制造不良品、不流出不良品。
减少不良的二十字真言:保持新鲜、迅速确实、三线一体、不要碰触、要一致性。
4.、动作的浪费:是指作业过程中不佳的浪费。
常见的浪费动作有:转向、反转、距离、寻找、堆叠、移动。
将产品重复从箱子里拿出来加工、加工后再放回箱子排列整齐、这是取放动作堆叠、移动的无驮。
改善:不插秧、不摇头、不弯腰。
5.、加工的浪费:指在生产过程中有些加工程序是可以省略、替代、重组或合并的。
如“压缩空气”“切削空气”冲床机器在整个加工过程中“碰碰”声音间接短效率高、较少发生“压缩空气”的现象。
否则相反。
改善:不做切削空气、不做木偶动作、不做立正动作。
6.、库存的浪费(为万恶之源):是因传统以来的许多错误生产观念所造成的。
分三种:1)材料库存:大量采购成本低。
2)在制品库存:不良重修机器故障。
3)成品库存:预测生产与实际需求量不同。
库存所带来的弊端:1)产生不必要的搬运、堆积、放置、防护处理找寻等浪费;2)使先进先出作业困难;3)损失利息及管理费用;4)物品贬值的风险以及占用空间而引起的投资浪费等。
TPS丰田生产方式——消除浪费的过程.

TPS(Toyota Production System)丰田生产方式第一部总体系——丰田生产方式的构思第一章丰田生产方式的体系本章目的丰田生产方式由丰田汽车公司开发、推广,1973年石油危机之后被众多的日本公司所采用。
该生产方式的主要目的是通过改善活动消除隐藏在企业里的种种浪费现象,进而降低成本。
这种生产方式,是继泰勒生产方式(科学管理法)和福特生产方式(大量装配线方式)之后诞生的生产方式。
一、生产方式的目的(一)、最终目的是通过降低生产成本产生效益丰田生产方式是生产产品的合理方法。
这里的“合理”,是指它对整个公司产生效益这个最终目的来说是行之有效的方法。
为了实现这个最终目的,丰田生产方式将降低成本作为基本的第一位的目标。
降低成本的目标,即提高生产率的目标。
成本从本质上来说,是指为了实现利润应该从销售额中扣除过去、现在以及将来的所有的现金支出。
所以,丰田生产方式中所说的成本,不仅仅是制造成本。
而且还包括销售费用、一般管理费用以及财务费用。
(二)、消除制造过剩的浪费降低成本图1.1 消除浪费降低成本的过程丰田生产方式,主要着眼于消除浪费降低成本。
我们按图1.1加以说明。
制造现场的浪费,第一层次是过剩的生产要素的存在。
第二层次是制造过剩的浪费。
第三层次是过剩的库存的浪费。
第四层次是1、如果库存在现场容纳不下,就要修建多余的仓库;2、雇佣搬运工将库存运到仓库(搬运的浪费);3、给每位搬运工购买一台叉车;4、为了防止产品在库房中锈蚀和管理库存,就必须增加人员;5、为了随时掌握库存的数量,管理部门需要相当数量的工时;6、需要用计算机管理库存的人员。
这四个层次的浪费存在递进关系。
所有这些第一层次、第二层次、第三层次、第四层次的浪费,都会增加直接材料费、直接劳务费、折旧费等间接经费、一般管理费,从而增大成本。
削减浪费应该先从第一层次开始,第一层次的重点为----削减过剩的人员。
因此,抑制生产过剩时极其重要的。
制造业提案范文生产车间的管理方案写

制造业提案范文生产车间的管理方案写一、序二、管理理念和方法三、实现目标的过程四、其它改进方法一、序:一个团队就象人一样,有出生、成长和成熟的过程。
二、管理理念——精益生产管理精益生产是永无止境的精益求精的过程,它致力于改进生产流程和流程中的每一道工序,尽最大可能消除价值链中一切不能增加价值的活动,提高劳动利用率,消灭浪费。
精益是一种全新的企业文化,而不是最新的管理时尚。
精益生产方式的目的是——最大限度地消除浪费(过多制造造成的浪费;库存的浪费;品质不良的浪费;等待造成的浪费;搬运造成的浪费;加工造成的浪费;动作造成的浪费)管理方法:团队工作法、注重关键细节团队工作法(Teamwork)努力营造一种“团队协作”的整体氛围。
团队工作的基本氛围是信任,以一种长期的监督控制为主,而避免对每一步工作的稽核,提高工作效率。
每位管理人员在工作中不仅是执行上级的命令,更重要的是积极地参与,起到决策与辅助决策的作用。
团队成员强调一专多能,要求能够比较熟悉团队内其他工作人员的工作,保证工作协调的顺利进行。
团队成员要增强大局观念。
当发生不协调时,应该“求大同存小异”。
在工作中应发扬“有人负责我服从,无人负责我负责”的精神,但不主张盲目而越位负责,这将会严重影响管理的执行力。
在团队当中,知识是一种共同的思维基础。
在传统观念中,知识是个人私有的力量、权力,是不可以共享给别人的。
要充分发挥团队的力量,只有大家把知识经验共享出来,才更易碰撞出创新的火花。
每个员工的成功才有企业的成功。
只有把团队成员的利益放在心上才有凝聚力。
注重关键细节:小天鹅公式海尔法则三、实现目标的过程;3.1 生产现状品质不良状况;管理人员主要精力处理事物,如生产异常?、品质异常?员工是否劳动效率低?原、辅料是否没有进行有效控制?3.2 管理意识的更新如何提高产品的一次合格率?如何通过 ___消除各类损耗和浪费,提高生产效率和降低生产成本?如何通过建设优秀现场管理文化,创造环境整洁、设备完好、管理有序的工厂?如何开展5S活动,改善员工精神面貌,激活员工和员工团队精神?3.3 改进生产活动3.3.1 品质不良原因分析及对策3.3.2 设备管理设备维护的状况直接影响到生产管理和产品质量的好坏消除停机时间。
库存管理生产与运作管理

• Example: If Q' = 2Q; then the ratio of the actual to
optimal cost is 1/22 + 1/2 = 1 25
EOQ模型—灵敏度分析续
• 若T‘用代替T;则实际成本与最优成本的比
率为:
aan nn nccu uo oaa u usslln n tt d d T T* eerr1 2T T* T T*
1 2 3 4 5 6 7 8 9 10 Zt
jt
Planning Horizon (t) 1 2 3 4 5 6 7 8 9 10 100 150 170 320
200 210 310 250 300 270 320 340 400 560 370 380 420 540 420 440 520 440 480 520 610 500 520 580 580 610 620
100 150 170 270 320 340 400 480 520 580
1 1 1 4 4 4 4 7 7 or 8 8
动态批量确定法续
• 最优解:
– 第8 生产8; 9; 10 周期需求40 + 20 + 30 = 90单 位
– 第4 生产 4; 5; 6; 7 周期需求50 + 50 + 10 + 20 = 130 单位
t 1 2 3 4 5 6 7 8 9 10 Dt 20 50 10 50 50 10 20 40 20 30 ct 10 10 10 10 10 10 10 10 10 10 At 100 100 100 100 100 100 100 100 100 100 ht 1 1 1 1 1 1 1 1 1 1
生产线平衡

精益 IE第六讲: 生产线平衡精益 IE一、生产线平衡的概念生产线上的各道工序布置的效益取决于将所需工作划分成一系列 单元而工作的能力,而此单元工作能迅速而例行化地由技术工人 和专业设备来执行。
大部分的加工时间都很短,以至于只指定一 项工作给每个工人是很不实际的。
相反的,工作经常组成容易管 理的群组,并分发到一两位操作者的工序去。
平衡生产线(LineBalancing)指的就是这种分配 工作到各道工序上的决策过程,通过对人力、机械设备和工作任 务的恰当分配,使整个生产线达到平衡状态。
21精益 IE平衡生产线的注意点为了较容易地达到生产线的平衡,需要关注瓶颈工序的工序改 善,整个生产线的效率最容易受到瓶颈工序的限制,对瓶颈工序 予以平衡显得尤为必要。
通过对瓶颈工序的分析,拆分作业动 作,尽可能地将瓶颈工序的动作分配到其它工序,由前后道的工 序来帮助完成。
在进行动作分配之前,首先计算瓶颈工序内作业人员的人均产 量,如果负荷过重,可以增加必要的操作人员,以便提高工序的 平衡率。
瓶颈工序内增加的操作人员,可能来源于其它工序合并 或简化所减掉的操作人员,这样,整个生产线的人员并不需要增 加,只是将多余的人员分配到更需要人员的地方,从而达到整条 生产线的平衡,实现效率和效能的最大化。
3精益 IE生产线平衡的改善方法分担转移的方法 作业改善压缩的方法 加人缩短循环时间的方法 拆解去除的方法 重排的方法 作业改善后合并的方法42精益 IE1.分担转移的方法5精益 IE2.作业改善压缩的方法63精益 IE3.加人缩短循环时间的方法7精益 IE4.拆解去除的方法84精益 IE5.重排的方法9精益 IE6.作业改善后合并的方法105精益 IE案例11精益 IE改善分析这条生产线可以发现,瓶颈工序就是钻孔的工序。
针对这八道工序的特 点,分解工序3(钻孔)的作业动作,提出以下的平衡改善措施: 改善瓶颈作业(即工序3钻孔),将工序3的定位动作(8秒)分担给工序2完 成。
流水生产线平衡方法培训课件

案例二
总结词
某电子产品制造公司通过不断优化生产线平衡,提高了生产效率,降低了生产成本。
详细描述
该公司针对生产线不平衡问题,运用ECRS原则进行流程优化,同时加强员工培训,使生产线平衡率得 到了显著提高,从而提高了企业的竞争力。
案例三:某家具制造公司的生产线平衡调整
总结词
某家具制造公司通过调整生产线平衡, 成功地提高了生产效率,降低了生产成 本。
自适应调度算法
利用先进算法,根据实时生产数据,动态调整生产计划 和调度,以适应市场需求和生产条件的变化。
高度自动化生产线的进一步发展
机器人与自动化设备
进一步发展机器人技术和自动化设备 ,实现生产过程的全面自动化,提高 生产效率和降低人工成本。
智能制造系统
构建智能制造系统,实现生产全流程 的智能化、柔性化、个性化,满足市 场需求的多样化。
流水生产线平衡的优化算法
1. 算法的准确性和效率 2. 算法的可解释性和可接受性
3. 算法的灵活性和适应性
04 生产线平衡的案例分析
案例一:某汽车制造公司的生产线平衡改进
总结词
通过运用生产线平衡理论,某汽车制造公司成功地改进了生产线,提高了生产效 率。
详细描述
该汽车制造公司针对生产线存在的瓶颈问题,采取了调整工作站、优化流程等措 施,使生产线平衡率得到了显著提高,从而降低了生产成本,提高了产品质量。
流水生产线平衡方法 培训课件
目录
• 流水生产线平衡概述 • 生产线平衡的基本原理 • 生产线平衡的方法和技巧 • 生产线平衡的案例分析
目录
• 生产线平衡的常见问题与解决方案 • 生产线平衡的未来发展趋势与展望
01 流水生产线平衡概述
定义与特点
生产线个人工作总结(5篇)

生产线个人工作总结(5篇)生产线个人工作总结1很快到公司已经一年了,在这一年时间里,我受益匪浅,首先要感谢领导的鼓励与支持,同事的帮助与积极配合,使我对自己的工作不断的检讨和提高,同时也发现自己的缺点和不足。
下面将这一年的工作做如下个人工作总结,望领导及同事批评指正:1、每日早晚会传达相关信息,根据生产计划安排工作,进行合理的人力调配,提高产线品质及效率,确保产线计划如期完成。
2、产线设备的.操作和简单维护,使设备正常运行。
3、统计数据做生产周报表、员工出勤及离岗顶替、产品入库及每日盘点等4、在生产的过程中发现问题,提出问题,配合相关同事及工程师及时处理产线各种异常问题。
5、做好整理、整顿、清扫、清洁、安全和素养,监督生产线的纪律,指导新员工工作,服从主管工作安排,处理日常其它事物。
通过以上工作我发现自己虽然熟知了自己的工作内容和职责,但对于人员管理和工作的综合能力还有待提高,遇事比较被动,没能完全主动发现问题提高自身能力,很少能做到与领导及时有效的沟通,没有完全意识到下级与上级沟通的重要性。
今后我会多加注意,与同事及领导及时沟通。
生产线个人工作总结2日月如梳、正泰为伴、同事为侣,在这紧张具有丰富节奏的生产任务中,正泰之声的音符又伴随我们度过了四季,在这即将告别迎来新春的脚步里,我随着正泰旋律为年的工作变化描绘出自己的工作总结与展望。
在这生产量日益提升的一年里,对于我来说是一个特别的一年,我自己也没想到,能在正泰集团应聘上行政管理岗位工作,虽然曾在一线工作了几年对各部门人员生产流程都比较熟知,但我深知自己有很多地方需要学习改进,自从我从一线员工转换为管理员的那天起,我才感觉到不是每一件工作都是让人事事如意,我的一言一行都有无数双明亮的眼睛看着我,所以不管是跟领导的`交流还是线上的员工沟通,都要全面了解和掌握每个人的性格与想法去完成工作达成共识,在此,也感谢公司领导和同事能给我这次展翅的机会,在这次学习起飞的起跑线上,我现将20xx年学习工作总结如下:一、班组长工作职责的了解1、严格执行安排生产计划,及时组织落实物料发放工作,并跟踪生产计划的完成情况;2、实施生产车间现尝条件及安全管理,严格落实“6S”要求,做好生产设备的日常维护保养;3、负责工艺文件、设备操作规程执行的现场检查、质量状态标识,现场问题的处理、反馈,做好重复性、批量性问题记录及处理结果,如实记录工作时间、核算工资;4、采用良好的沟通方式,积极主动与员工交流,掌握员工的思想动态,了解员工想法,及时分析、反馈;5、负责对在制品、成品数量的管理、交接及工序确认,保证产品及物料处于受控状态;6、组织并现场监督退货产品的处理,确保方案合理、执行严格,对批量未使用产品的处理过程给予记录。
- 1、下载文档前请自行甄别文档内容的完整性,平台不提供额外的编辑、内容补充、找答案等附加服务。
- 2、"仅部分预览"的文档,不可在线预览部分如存在完整性等问题,可反馈申请退款(可完整预览的文档不适用该条件!)。
- 3、如文档侵犯您的权益,请联系客服反馈,我们会尽快为您处理(人工客服工作时间:9:00-18:30)。
2012年第7期
/A 公司生产现状及存在问题
1.A 公司现状
该公司是一家以生产自行车为主的外资企业,目前,属于中等规模,因此还具有很大的提升空间。
其生产流程如图1所示:
图1:A 公司生产流程图
该公司每个工序的具体内容及特点是:
(1)加工:主要有管件裁剪、皂化处理、表面油污处理、退火、冲压成型、弯管、裁斜、冲角、钻孔、表面研磨、附件氨焊等。
主要特点:不同车种的制造流程时间及工量差异较大;对作业人员技能要求较高。
(2)焊接:主要有组立点焊、校正、铣弧、氢弧焊、打记号、
号码登记、车架精加工等。
主要特点:采用25人左右的流水线作业;对加工精度要求较高;人员作业技能要求较高且多功能化。
(3)前处理:主要有表面皮膜处理、清洁等。
主要特点:设备大型化,不易动;设备自动化程度高;不同车种工量变化不大。
(4)涂装:主要有吹风、补涂、喷漆、贴标等。
主要特点:不同车种工量差异较大;与环境变化关系较大;设备非常大,流水线作业。
(5)备料:主要有外购零件配送、部分产品附件组装配送等。
主要特点:不同零件要求同步化配送;部分产品附件组装保证不因为库存不够而停组装线,或者库存过高而浪费资源。
(6)装配:主要有整车完整组装、包装、封箱、入库。
主要特点:流水线作业,平衡度要求高;员工技能训练期短;整条流水线人员、物料入口较多,对异常的控制管理要求较高。
2.A 公司生产线存在的问题
该公司目前存在的主要问题是在制品库存量非常大,造成了大量的资金浪费[4],使公司经营面临着一定的风险。
其各个工序及工序内部在制品数量如表1所示。
表1:A 公司生产流程中各工程间及工程内在制品库存数据表(注:每天生产7000件产品为基准)
由表1可知,涂装工序的在制品库存数量是15000件,明显多于其它各个工序的在制品库存量,如果将该工序前后的缓存数量(即前处理至涂装的过程和涂装至装配的过程)也计算进来,那么,这一工序的在制品数量将达到38000件之多,
成为该生产线的“瓶颈”。
3.造成在制品数量大的原因
(1)每两个工程间在制品数量多的原因是:工厂设备采用程序式布置,各作业工程之间相互独立及批量化生产,各工程加工出来的产品积累到一定数量后才运送到下个工程,必然导致工程间大量在制品出现,也会造成某些工序出现因产品数量不够、
停滞或堆积的状况[5]。
(2)各工程内在制品库存高的主要原因为:生产线中的各道工序只是根据各工序本身的生产能力进行生产,并未考虑上道工序的产品积压和下道工序的需求,这样必然导致各工序内的在制品库存数量大[6]。
(3)采用因果分析图,从人、机、料、法等方面着手分析,造成在制品数量大的原因如图2所示。
生产线中在制品库存数量的改善
———以A 公司为例
■哈尔滨/孙丹丹
孙福田
许智慧
摘要:本文通过对A 公司生产线各个生产工序的详细研究,利用工业工程基本的改善方法对其进行改进,减少生产线中的在制品数量,降低生产过程中原材料和资金的浪费。
关键词:在制品;工业工程;看板管理;
生产效率
序号12345
678910合计
项目加工工序内加工到焊接焊接工序内焊接至前处理前处理工序内前处理至涂装涂装工序内涂装至装配装配工序内备料工序内
库存12000100001000011000500010000150001300020002000109000
93
2012年第7期
/参考文献:
[1]蓝伯雄,陈晖娜.一个集成化企业计划模型[J].系统工程理论与实践,2001(9).[2]邬适融.现代企业管理[M ].北京:清华大学出版社,2008.[3]刘丽文.生产与运作管理[M ].北京:清华大学出版社,2006.
[4]李瑾.基于知识挖掘的制造企业ER P 生产流程优化研究[D ].青岛:中国海洋大学,2009.
[5]M oham m ad Jaf ar Tarokh,Eslnail Shlarif i,EslamN azem i,Survey of B PRexperienees In lran reasons f or sueeess
and f ailure[J].Journal of B usiness &Indust rial M arket ing.2008,23(5):350一362.[6]郭咸纲.企业柔性战略模式[M ].北京:清华大学出版社,2005.[7]李晓勇.陇兴公司生产流程再造研究[D ].兰州大学,2011.
[8]G uangning C ao,St eve C larke et e.A crit ique of B PR f rom a holist ic Perspeet ive[J].B usiness Process M an-agem ent Journal.2001,7(4):332一339.
[9]陈亭,陈俊芳.建立企业的竞争优势———业务流程再造[J],上海企业,2001(6).
[10]周荣辅.基于先进制造技术的制造业生产流程再造研究[D ].秦皇岛:燕山大学,2007.[11]杨尊琦,林海.企业资源规划原理与应用[M ].北京:机械工业出版社,2006.[12]顾新建.智能制造系统[J].成组技术和生产现代化,2001(2).
[13]陈颖祥.杭州摩托罗拉M S 产品生产流程整合管理研[D ].兰州:兰州大学,2011.[14]蔡启明,张庆,庄品.基础工业工程[M ](第二版).北京:科学出版社,2009.
(作者单位:东北农业大学工程学院)
编辑
沈德力
图2:在制品数量原因分析图
改善措施及结果
1.提高生产人员素质
培养多功能的工人,采用“一人多机”的布置形式,也就是在同一道工序中一个生产人员负责多个机器,或者同一个生产人员负责不同工序中的机器[9]。
以此来降低人员的闲置,减少生产人员数量。
而且还应在一些大型设备的操作中,实行操作人员站立式作业的措施[10]。
2.“瓶颈”工序的改善
由表1中的在制品数量可以看出,本例中的“瓶颈”是涂装工序。
因为,该公司的生产线每个工序都采用一组生产人员,每一组为15人的作业方式,即每个工序15个工作站。
为此,采用增加涂装工序工作站的方法,将原来的15个工作站增加到25个,即在该工序增加10人,这样就大大降低了涂装工序的在制品数量[12]。
3.施行看板管理
看板管理是一种目视化的管理方式。
该公司适宜采
用拉式生产(Pull )[14]
,即每道工序应根据其下一道工序
的需求量来生产适量的工件,以此来达到降低在制品数量,减少浪费的目的。
例如,涂装生产工序根据装配工序的工件需求量来进行生产,将装配工序的需求量写在看板上,以此来联系各道工序,使得每道工序的生产都有据可依,不盲目生产。
4.改善结果
通过以上措施,该公司近两年在制品库存量大的问题得到了很好的解决。
表2为改善前后的对比数据。
表2:在制品数量改善前后对比表
从上表可以看出,改善之前的在制品数量为109000件,约为该厂15.5天的生产量。
进行改善以后,在制品数量降为42500件,约为该厂6天的生产量,降幅高达61%,给A 公司带来了很大的经济效益。
结论
A 公司通过对在制品库存量过大的问题进行改进,在制品数量得到了大幅度下降,同时也减少了资金的占用。
由此可以看出,减少A 公司的在制品数量,使该公司的经济效益在各个方面都得到了很大的提升。
经管研究J INGGUANY ANJ IU
序号
12345678910合计
项目加工工程内加工到焊接焊接工程内焊接至前处理前处理工程内前处理至涂装涂装工程内涂装至装配装配工程内备料工程内
改善前库存(台)
20000180001000014000500010000150001300020002000109000
改善后库存(台)
7000500050003000100055001000040001000100042500
94。