橡胶快速硫化技术
橡胶硫化促进剂M合成技术

橡胶硫化促进剂M合成技术摘要:橡胶促进剂是一类非常重要的添加助剂,促进剂 M可以使橡胶在硫化时迅速硫化,并表现出较好的硫化性;硫化橡胶是一种性能优良、用途广泛的材料。
此外,促进剂M还可作为其它后效应催化剂(例如磺酰胺催化剂)的原料。
由于像橡胶这样的基本工业的蓬勃发展,对助剂的要求也在不断提高。
但近几年,随着我国环保工作的不断加强,部分橡胶助剂的生产企业被迫停产,造成了橡胶助剂的供求矛盾不断加剧。
目前,国内促进剂M的制造技术还不完善,尤其是对母液污水、硫化氢等含硫气体等的后处理技术还很薄弱,对环境的影响也很大。
因此,从根本上解决促进剂M存在的问题,必须大力发展、推行清洁生产、减少原料消耗。
关键词:橡胶硫化;促进剂;合成技术引言硫化促进剂 M是一种在橡胶工业中应用非常普遍的一种助进剂,其化学名是2-巯基苯并噻唑类,是世界上最大的一种橡胶硫化助剂,也是制造氨基磺基助剂的主要原材料。
然而,无论采用何种方法,均存在着大量“三废”的问题。
在橡胶促进剂 M的生产中,环境污染问题已经成为限制其进一步发展的一个重要因素。
如何有效地处理和回收利用“三废”,是目前橡胶助剂工业所关注的问题。
一、苯胺法合成技术研究(一)苯胺法促进剂M合成反应机理研究在此基础上,对反应体系中各物种尤其是中间物种种类、数量的变化进行辨识,从而揭示其作用机制。
采用28 ml小型反应器对促进剂M的合成机理进行了研究。
反应器被浸泡在熔盐中用于加热,并且通过调整熔盐的温度,可以调整反应温度,使之符合要求的温度范围。
当温度上升到室温时,将硫化氢释放,将该混合物溶于乙酸乙酯中,并将该混合物的体积固定为500毫升。
采用 HPLC对混合液进行组分分析。
在各个步骤中,反应液除了含有苯胺和 MBT外,还含有苯并噻唑,二苯硫醚和苯胺基苯并噻唑。
在促进剂M含量未达到峰值(91.1%)以前,促进剂M与残留的苯胺,中间体二苯基硫化物,苯胺基苯并噻唑,以及苯并噻唑等全部被转换成苯胺,占原料苯胺总量的96%-99%。
橡胶硫化工艺流程

橡胶硫化工艺流程橡胶硫化是指将橡胶中的双键或多键化合物与硫或其它硫化剂反应生成交联结构的化学反应过程。
硫化是橡胶制品加工中必不可少的一道工艺,它可以提高橡胶制品的耐磨性、耐老化性和强度,使橡胶制品具有更好的物理性能。
橡胶硫化工艺流程是指橡胶硫化过程中所涉及到的各个环节和步骤,下面将详细介绍橡胶硫化工艺流程。
首先,橡胶硫化的原料准备。
在橡胶硫化工艺流程中,首先需要准备好橡胶和硫化剂。
橡胶可以是天然橡胶、合成橡胶或再生橡胶,而硫化剂主要是硫磺。
在一般情况下,还需要添加一些促进剂、活化剂和防老化剂等辅助原料,以提高硫化效果和橡胶制品的性能。
其次,橡胶混炼。
橡胶混炼是指将橡胶和各种硫化剂、促进剂等原料混合均匀的过程。
混炼的目的是使各种原料充分分散,以便硫化剂能够均匀地和橡胶发生化学反应。
混炼过程中需要控制好温度、时间和机械作用,以确保橡胶和各种原料充分混合。
然后,硫化成型。
混炼后的橡胶料需要进行硫化成型,即将橡胶料放入硫化模具中,加热使其发生硫化反应,并得到所需形状的橡胶制品。
硫化成型的温度、时间和压力等参数需要根据具体橡胶制品的要求来进行控制,以确保橡胶制品的质量。
最后,橡胶制品的后处理。
硫化成型后的橡胶制品需要进行后处理,包括去除模具、修整边角、清洗等工序。
有些橡胶制品还需要进行硫化后的热处理或冷却处理,以进一步提高其性能。
总之,橡胶硫化工艺流程是一个复杂的过程,需要严格控制各个环节和步骤,以确保橡胶制品的质量和性能。
只有在整个硫化工艺流程中严格执行标准操作规程,才能生产出优质的橡胶制品,满足不同行业的需求。
丁腈橡胶快速硫化体系

丁腈橡胶快速硫化体系
丁腈橡胶快速硫化体系是一种用于丁腈橡胶的加硫工艺,能够在较短的时间内实现橡胶的硫化。
该体系通常包括以下成分:
1. 主硫化剂:主要指硫化剂,常用的有硫磺和加速器硫化铜。
2. 辅助硫化剂:常用的辅助硫化剂有加速剂和促进剂。
加速剂可提高硫化反应速度,常用的加速剂有硫化氮、硫化羰基、硫醇等。
促进剂主要用于提高硫化效率,常用的促进剂有金属氧化物和有机化合物。
3. 防老剂:常用的防老剂有抗氧化剂和紫外线吸收剂,用于延缓橡胶老化过程。
丁腈橡胶快速硫化体系的实现需要合适的工艺条件,如适宜的温度和时间。
此外,体系中各成分的配比也需要经过实验和优化,以保证最佳的硫化效果和橡胶性能。
橡胶快速硫化技术
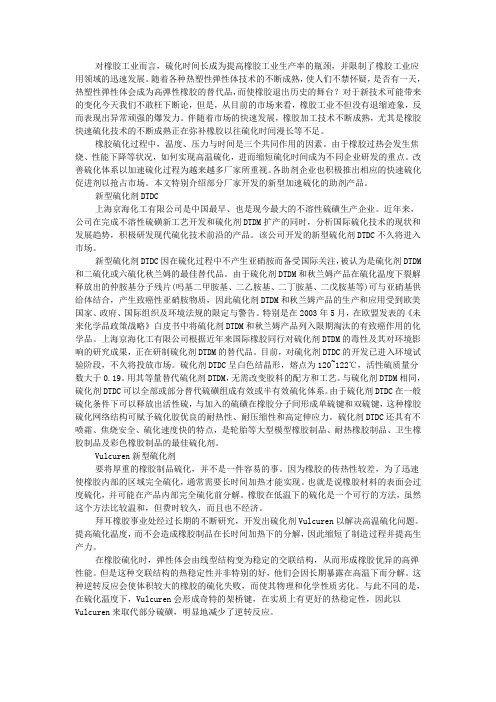
对橡胶工业而言,硫化时间长成为提高橡胶工业生产率的瓶颈,并限制了橡胶工业应用领域的迅速发展。
随着各种热塑性弹性体技术的不断成熟,使人们不禁怀疑,是否有一天,热塑性弹性体会成为高弹性橡胶的替代品,而使橡胶退出历史的舞台?对于新技术可能带来的变化今天我们不敢枉下断论,但是,从目前的市场来看,橡胶工业不但没有退缩迹象,反而表现出异常顽强的爆发力。
伴随着市场的快速发展,橡胶加工技术不断成熟,尤其是橡胶快速硫化技术的不断成熟正在弥补橡胶以往硫化时间漫长等不足。
橡胶硫化过程中,温度、压力与时间是三个共同作用的因素。
由于橡胶过热会发生焦烧、性能下降等状况,如何实现高温硫化,进而缩短硫化时间成为不同企业研发的重点。
改善硫化体系以加速硫化过程为越来越多厂家所重视。
各助剂企业也积极推出相应的快速硫化促进剂以抢占市场。
本文特别介绍部分厂家开发的新型加速硫化的助剂产品。
新型硫化剂DTDC上海京海化工有限公司是中国最早、也是现今最大的不溶性硫磺生产企业。
近年来,公司在完成不溶性硫磺新工艺开发和硫化剂DTDM扩产的同时,分析国际硫化技术的现状和发展趋势,积极研发现代硫化技术前沿的产品。
该公司开发的新型硫化剂DTDC不久将进入市场。
新型硫化剂DTDC因在硫化过程中不产生亚硝胺而备受国际关注,被认为是硫化剂DTDM 和二硫化或六硫化秋兰姆的最佳替代品。
由于硫化剂DTDM和秋兰姆产品在硫化温度下裂解释放出的仲胺基分子残片(吗基二甲胺基、二乙胺基、二丁胺基、二戊胺基等)可与亚硝基供给体结合,产生致癌性亚硝胺物质,因此硫化剂DTDM和秋兰姆产品的生产和应用受到欧美国家、政府、国际组织及环境法规的限定与警告。
特别是在2003年5月,在欧盟发表的《未来化学品政策战略》白皮书中将硫化剂DTDM和秋兰姆产品列入限期淘汰的有致癌作用的化学品。
上海京海化工有限公司根据近年来国际橡胶同行对硫化剂DTDM的毒性及其对环境影响的研究成果,正在研制硫化剂DTDM的替代品。
橡胶怎么快速凝固的原理

橡胶怎么快速凝固的原理一、原料制备
1. 选择好质量的天然橡胶或合成橡胶作为主要原料。
2. 加入硫化剂、促进剂、老化防护剂等配料。
3. 使用开式混炼机充分混炼,使配料均匀分散。
二、加速硫化原理
1. 硫化反应是形成橡胶网络结构的关键过程。
2. 加入硫化促进剂,可以缩短硫化反应时间,提高硫化速率。
3. 常用的硫化促进剂有肽类、硫脲类等有机物。
4. 促进剂可与硫化剂生成活性硫化中间体,加速硫化反应。
三、提高温度
1. 硫化反应属于化学反应,反应速率随温度升高而加快。
2. 通过选择高温硫化工艺,可以大幅缩减硫化用时。
3. 一般采用140-160C进行高温硫化,速度比常温快数倍。
4. 但温度过高会引起橡胶TEXTURE劣化,需控制适宜温度。
四、使用高能辐射
1. 采用电子束或γ射线辐照混炼橡胶,可引发硫化反应。
2. 高能辐射产生的自由基可直接发生硫化反应。
3. 辐射硫化法快速、环保,可精确调控,是新兴的快速硫化技术。
五、注意事项
1. 硫化速率过快会影响产品质量,需要控制适宜。
2. 不同配方及硫化工艺要进行定制优化。
3. 保证硫化均匀一致非常关键,否则会影响制品性能。
4. 快速硫化技术投入使用还需大量数据支撑。
橡胶硫化工艺流程
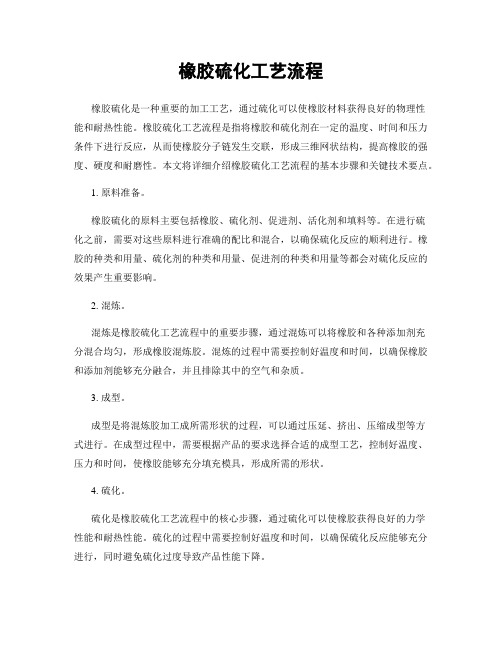
橡胶硫化工艺流程橡胶硫化是一种重要的加工工艺,通过硫化可以使橡胶材料获得良好的物理性能和耐热性能。
橡胶硫化工艺流程是指将橡胶和硫化剂在一定的温度、时间和压力条件下进行反应,从而使橡胶分子链发生交联,形成三维网状结构,提高橡胶的强度、硬度和耐磨性。
本文将详细介绍橡胶硫化工艺流程的基本步骤和关键技术要点。
1. 原料准备。
橡胶硫化的原料主要包括橡胶、硫化剂、促进剂、活化剂和填料等。
在进行硫化之前,需要对这些原料进行准确的配比和混合,以确保硫化反应的顺利进行。
橡胶的种类和用量、硫化剂的种类和用量、促进剂的种类和用量等都会对硫化反应的效果产生重要影响。
2. 混炼。
混炼是橡胶硫化工艺流程中的重要步骤,通过混炼可以将橡胶和各种添加剂充分混合均匀,形成橡胶混炼胶。
混炼的过程中需要控制好温度和时间,以确保橡胶和添加剂能够充分融合,并且排除其中的空气和杂质。
3. 成型。
成型是将混炼胶加工成所需形状的过程,可以通过压延、挤出、压缩成型等方式进行。
在成型过程中,需要根据产品的要求选择合适的成型工艺,控制好温度、压力和时间,使橡胶能够充分填充模具,形成所需的形状。
4. 硫化。
硫化是橡胶硫化工艺流程中的核心步骤,通过硫化可以使橡胶获得良好的力学性能和耐热性能。
硫化的过程中需要控制好温度和时间,以确保硫化反应能够充分进行,同时避免硫化过度导致产品性能下降。
5. 后处理。
硫化完成后,还需要进行后处理工艺,如冷却、清洗、修整等,以确保产品的质量和外观。
同时还需要进行产品的检验和包装,最终将产品送往市场。
总之,橡胶硫化工艺流程是一个复杂而精细的加工过程,需要严格控制各个环节,以确保产品的质量和性能。
只有在每个步骤中严格执行工艺要求,才能生产出符合要求的橡胶制品。
希望本文对橡胶硫化工艺流程有所帮助,谢谢阅读。
橡胶的硫化方法
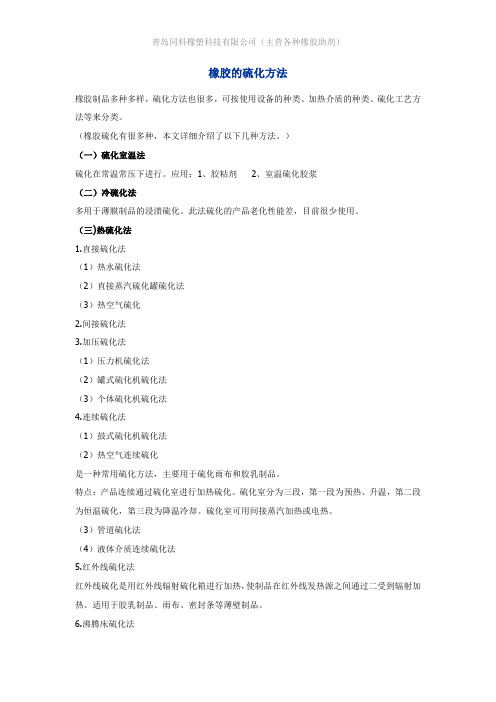
橡胶的硫化方法橡胶制品多种多样,硫化方法也很多,可按使用设备的种类、加热介质的种类、硫化工艺方法等来分类。
(橡胶硫化有很多种,本文详细介绍了以下几种方法。
)(一)硫化室温法硫化在常温常压下进行。
应用:1、胶粘剂2、室温硫化胶浆(二)冷硫化法多用于薄膜制品的浸渍硫化。
此法硫化的产品老化性能差,目前很少使用。
(三)热硫化法1.直接硫化法(1)热水硫化法(2)直接蒸汽硫化罐硫化法(3)热空气硫化2.间接硫化法3.加压硫化法(1)压力机硫化法(2)罐式硫化机硫化法(3)个体硫化机硫化法4.连续硫化法(1)鼓式硫化机硫化法(2)热空气连续硫化是一种常用硫化方法,主要用于硫化雨布和胶乳制品。
特点:产品连续通过硫化室进行加热硫化。
硫化室分为三段,第一段为预热、升温,第二段为恒温硫化,第三段为降温冷却。
硫化室可用间接蒸汽加热或电热。
(3)管道硫化法(4)液体介质连续硫化法5.红外线硫化法红外线硫化是用红外线辐射硫化箱进行加热,使制品在红外线发热源之间通过二受到辐射加热。
适用于胶乳制品、雨布、密封条等薄壁制品。
6.沸腾床硫化法沸腾床的结构原理与液体硫化槽类似,床内贮存的是由固体、气体构成的悬浮系统。
沸腾床硫化的优点:热传递能力高;受热均匀;比液体介质的温度极限和化学惰性高;操作安全;不沾污成品和简化清洁工序等。
沸腾床除用于硫化橡胶制品外,还可用于金属、织物、坯料、模型的预热及原料的干燥等。
沸腾床硫化被广泛应用于无芯制品的连续硫化,如海绵条、门窗条、胶绳、胶条及异型压出制品、电线、电缆、纯胶管、薄膜制品等。
7.微波预热热空气硫化法微波预热热空气硫化法是压出制品先采用微波预热,接着让其进入热空气管道中进行硫化。
微波通常指频率在300-30000MHz之间的电磁波,只需要30-40s就可以使胶料的温度从90摄氏度升至190摄氏度。
橡胶硫化工艺技术的对比

橡胶硫化工艺技术的对比橡胶硫化是指将橡胶原料经过一系列的加工工艺,使其在一定的温度和压力下与硫化剂发生化学反应,从而形成交联结构,使橡胶具有良好的弹性和耐用性。
橡胶硫化工艺技术的发展经历了多个阶段,目前主要的硫化工艺技术有热硫化、自发硫化和微波硫化。
热硫化是最早使用的硫化工艺技术,其原理是将橡胶材料和硫化剂混合均匀后,放入硫化机内进行硫化处理。
硫化机会提供一定的温度和压力,使橡胶与硫化剂发生化学反应,形成交联结构。
热硫化的优点是成本低、工艺简单,并且可以用于各种类型的橡胶材料。
但是,热硫化的缺点是硫化时间较长,硫化温度相对较高,容易导致橡胶老化,对环境也有一定的污染。
自发硫化是一种新兴的硫化工艺技术,其原理是利用自发生成的硫化剂来进行硫化。
自发硫化的优点是硫化速度快、硫化温度低,对橡胶材料的老化影响小。
同时,自发硫化还能减少硫化机的能耗和环境污染。
然而,自发硫化的缺点是硫化剂的自发性不稳定,需要进行严密的控制和监测工作。
微波硫化是一种新型的硫化工艺技术,其原理是利用微波加热橡胶材料,使其快速硫化。
微波硫化的优点是硫化速度非常快,能够在数分钟内完成硫化过程;而且微波加热橡胶材料时可以实现内外均匀加热,减少加热不均匀导致的硫化不良问题。
微波硫化还能节约能源和减少环境污染。
不过,微波硫化设备的成本相对较高,操作技术要求更高,需要注意橡胶材料的选择和硫化时间的控制。
综上所述,不同的橡胶硫化工艺技术各有优缺点。
热硫化工艺技术成本低、工艺简单,但是硫化时间长,环境污染较大;自发硫化工艺技术硫化速度快,对橡胶材料老化影响小,但是硫化剂自发性不稳定,需要进行严密的控制;微波硫化工艺技术硫化速度快,能够内外均匀加热橡胶材料,节约能源和减少环境污染,但操作技术要求高和设备成本高。
根据不同的应用场景和要求,可以选择适合的硫化工艺技术。
- 1、下载文档前请自行甄别文档内容的完整性,平台不提供额外的编辑、内容补充、找答案等附加服务。
- 2、"仅部分预览"的文档,不可在线预览部分如存在完整性等问题,可反馈申请退款(可完整预览的文档不适用该条件!)。
- 3、如文档侵犯您的权益,请联系客服反馈,我们会尽快为您处理(人工客服工作时间:9:00-18:30)。
橡胶快速硫化技术·
橡胶快速硫化技术
对橡胶工业而言,硫化时间长成为提高橡胶工业生产率的瓶颈,并限制了橡胶工业应用领域的迅速发展。
随着各种热塑性弹性体技术的不断成熟,使人们不禁怀疑,是否有一天,热塑性弹性体会成为高弹性橡胶的替代品,而使橡胶退出历史的舞台?对于新技术可能带来的变化今天我们不敢枉下断论,但是,从目前的市场来看,橡胶工业不但没有退缩迹象,反而表现出异常顽强的爆发力。
伴随着市场的快速发展,橡胶加工技术不断成熟,尤其是橡胶快速硫化技术的不断成熟正在弥补橡胶以往硫化时间漫长等不足。
橡胶硫化过程中,温度、压力与时间是三个共同作用的因素。
由于橡胶过热会发生焦烧、性能下降等状况,如何实现高温硫化,进而缩短硫化时间成为不同企业研发的重点。
改善硫化体系以加速硫化过程为越来越多厂家所重视。
各助剂企业也积极推出相应的快速硫化促进剂以抢占市场。
本文特别介绍部分厂家开发的新型加速硫化的助剂产品。
新型硫化剂DTDC
上海京海化工有限公司是中国最早、也是现今最大的不溶性硫磺生产企业。
近年来,公司在完成不溶性硫磺新工艺开发和硫化剂DTDM扩产的同时,分析国际硫化技术的现状和发展趋势,积极研发现代硫化技术前沿的产品。
该公司开发的新型硫化剂DTD C不久将进入市场。
新型硫化剂DTDC因在硫化过程中不产生亚硝胺而备受国际关注,被认为是硫化剂DTDM和二硫化或六硫化秋兰姆的最佳替代品。
由于硫化剂DTDM和秋兰姆产品在硫化温度下裂解释放出的仲胺基分子残片(吗基二甲胺基、二乙胺基、二丁胺基、二戊胺基等)可与亚硝基供给体结合,产生致癌性亚硝胺物质,因此硫化剂DTDM和秋兰姆产品的生产和应用受到欧美国家、政府、国际组织及环境法规的限定与警告。
特别是在2003年5月,在欧盟发表的《未来化学品政策战略》白皮书中将硫化剂DTDM和秋兰姆产品列入限期淘汰的有致癌作用的化学品。
上海京海化工有限公司根据近年来国际橡胶同行对硫化剂DTD M的毒性及其对环境影响的研究成果,正在研制硫化剂DTDM的替代品。
目前,对硫化剂DTDC的开发已进入环境试验阶段,不久将投放市场。
硫化剂DTDC呈白色结晶形,熔点为120~122℃,活性硫质量分数大于0.19。
用其等量替代硫化剂DTDM,无需改变胶料的配方和工艺。
与硫化剂DTDM相同,硫化剂DTDC可以全部或部分替代硫磺组成有效或半有效硫化体系。
由于硫化剂DTDC在一般硫化条件下可以释放出活性硫,与加入的硫磺在橡胶分子间形成单硫键和双硫键,这种橡胶硫化网络结构可赋予硫化胶优良的耐热性、耐压缩性和高定伸应力。
硫化剂DTDC还具有不喷霜、焦烧安全、硫化速度快的特点,是轮胎等大型模型橡胶制品、耐热橡胶制品、卫生橡胶制品及彩色橡胶制品的最佳硫化剂。
Vulcuren新型硫化剂
要将厚重的橡胶制品硫化,并不是一件容易的事。
因为橡胶的传热性较差,为了迅速使橡胶内部的区域完全硫化,通常需要长时间加热才能实现。
也就是说橡胶材料的表面会过度硫化,并可能在产品内部完全硫化前分解。
橡胶在低温下的硫化是一个可行的方法,虽然这个方法比较温和,但费时较久,而且也不经济。
拜耳橡胶事业处经过长期的不断研究,开发出硫化剂Vulcuren以解决高温硫化问题。
提高硫化温度,而不会造成橡胶制品在长时间加热下的分解,因此缩短了制造过程并提高生产力。
在橡胶硫化时,弹性体会由线型结构变为稳定的交联结构,从而形成橡胶优异的高弹性能。
但是这种交联结构的热稳定性并非特别的好,他们会因长期暴露在高温下而分解。
这种逆转反应会使体积较大的橡胶的硫化失败,而使其物理和化学性质劣化。
与此不同的是,在硫化温度下,Vulcuren会形成奇特的架桥键,在实质上有更好的热稳定性,因此以Vulcuren来取代部分硫磺,明显地减少了逆转反应。
目前制造体积较大的橡胶制品,例如工程车的橡胶实心轮胎或宽大输送带,因使用Vulcuren,可以使橡胶制品的生产比较快速而且更经济。
此外,产品的物性,例如耐磨性、抗张强度和抗撕裂强度等都可维持在很高的标准。
Pckacil TBzTD
化学名为二硫化四基秋兰姆,是尤尼罗伊尔公司新开发的秋兰姆类促进剂,可替代TMTD(四甲基二硫化秋兰姆)、TMTM(一硫化四甲基秋兰姆)、TETD(二硫化四乙基秋兰姆),加工安全性更好,比TMTD有更长的焦烧时间,可作为天然橡胶、丁橡胶和丁苯橡胶的快速硫化主促进剂或助促进剂,有时也用于PVC橡胶硫化抑制剂。
TBzTD分子量大,熔点高,不易分解,故不产生亚硝胺;其硫化速度稍低于TMTD,其他物性与TMTD几乎相同,目前已成为极具发展潜力的秋兰姆类硫化促进剂新品种。
Santocure TBBS
化学名为N-叔丁基-2-苯并唑次磺胺类促进剂,是一种性能很好的次磺胺类促进剂,由孟山都公司开发。
在天然橡胶、丁苯橡胶、丁二烯橡胶和其并用胶种中使用时,具有硫化速度快和模量高等特点。
一般可单独使用或与少量促进剂一起使用;在轮胎和工业橡胶制品中使用时,需配用氧化锌和硬脂酸,也可用秋兰姆、二硫代氨基甲酸盐、醛胺、胍类促进剂和酸性物质活化。
TBBS以叔丁胺和促进剂M为原料合成,不存在亚硝胺致癌问题,是全球主导的促进剂品种,消费量占全球促进剂消费量的35%以上。
中国也有部分企业进行小规模生产,但由于受原料叔丁胺的制约,未能大规模生产与应用,但其作为环保高效的新型次磺胺类促进剂发展前景很好。
Santocure TBSI
化学名为N-叔丁基双-2-苯并唑次磺胺类促进剂,由孟山都公司开发,在操作温度下非常安全,不产生致癌亚硝胺。
与TBBS相比,TBSI具有分子量大、熔点高30℃以上、热稳定性能好、焦烧时间长、硫化速度快等优点,通常与防焦剂CTP共用,可完全替代TBBS。
另外,TBSI还具有遇水稳定、易于贮存;在硫化天然胶时,可明显提高橡胶的抗硫化返原性;在橡胶与钢丝粘接的化合物中表现良好的性能。
TBSI可用于天然橡胶、丁苯橡胶、顺丁橡胶、异戊橡胶等,尤其适用于硷性较强的炉法炭黑混炼胶料及对抗返原要求很高的厚制品,活性大于目前广泛使用的CBS、NOBS等促进剂。
多功能促进剂TiBTM
化学名为N,N,N''-硫化四异丁基秋兰姆,由美国固持里奇公司开发,为一种既具有次磺胺类促进剂的助促进剂作用,又具有防焦剂作用的多功能促进剂。
在SBR/B R胶料中,TiBTM和CTP分别与TBBS和CBS并用时,两种防焦剂对焦烧延迟作用相同;但TiBTM还可明显加快硫化速度,而CTP则没有加速硫化的作用,甚至有时会引起硫化速度下降。
试验表明,在SBR/BR之类的合成橡胶体系中,TiBTM可同时发挥防焦剂和助促进剂两种功能。
但在天然橡胶中,TiBTM的防焦效果明显比CTP差,TiBTM主要用作助促进剂;但TiBTM可增加天然橡胶的抗硫化返原性,提高硫化温度、变化硫磺用量及加入白炭黑都不会影响TiBTM防焦烧和加速硫化速度的效果,而且对硫化橡胶的物理性能无不良影响。
不断提高生产效率将是各种技术竞争中不变的主题之一。
在橡胶加工与橡胶助剂的各种技术之中,加速硫化的促进剂技术在推动橡胶工业及其加工技术发展的同时,并将成为各助剂供应商继续研发的重点。