常减压装置新技术的应用
先进控制技术在常减压装置的应用
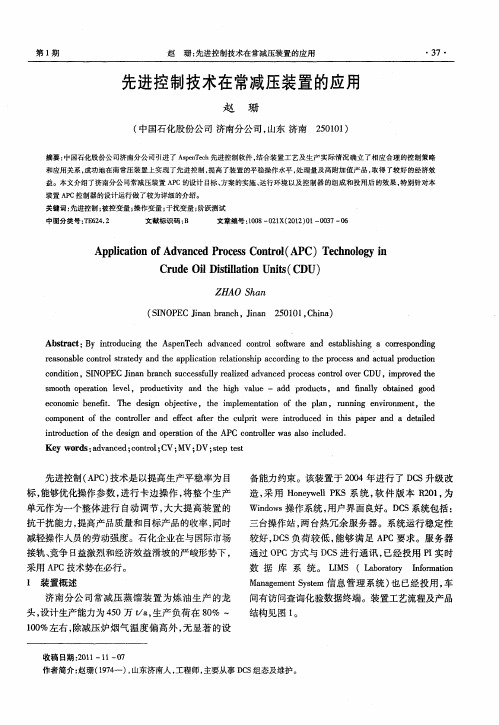
采用 A C技术势在必行。 P
l 装置概 述
数 据 库 系 统 。 LM (Lbr o I o ao IS ao t y n r tn ar fm i M ngm n Ss m信息 管理系统 ) 已经投用 , aae et y e t 也 车 间有访问查询化验数据终端。装置工艺流程及产品
c mp n n f t e c n o lr a d e e t atr t e c l r e e i t d c d i h s p p r a d a d ti d o o e t o o t l n f c fe u p i w r n r u e n t i a e n e al h r e h t o e i t d cin o e d s n p r t n o e AP o t l rwa l n l d d n o u t f e i a d o e a o ft C c nr l sa s i cu e . r o h t n g i h oe o Ke r s a v n e c n r l CV; y wo d : d a c d; o t ; o MV; V ;t p t s D s e t e
s ot prtn l e,pouti ad tehg a e— ad pout,ad f a otnd go m o oeao e l rdcv h i v i  ̄ n h ih vl u d rdc s n nl ba e od i  ̄ i
eoo i b nf .T e d s n ojc v ,te i pe n t n o h ln u nn n i n n ,te cn m c e e t h ei bet e h m l i g i met i fte pa ,rn ig e v omet h ao r
常减压装置新技术的应用
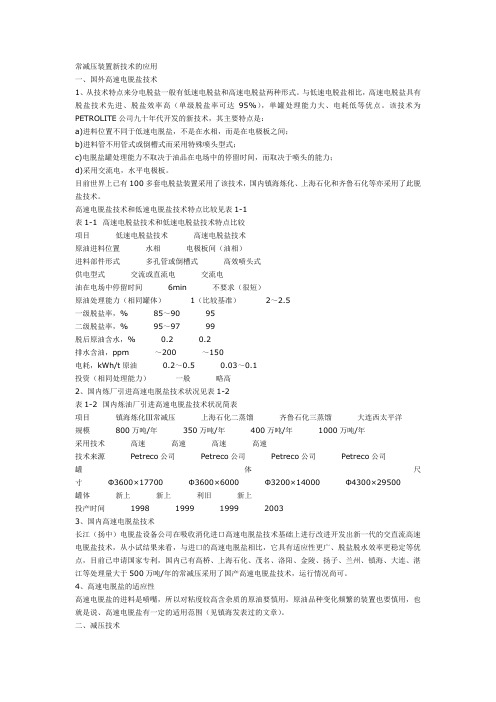
常减压装置新技术的应用一、国外高速电脱盐技术1、从技术特点来分电脱盐一般有低速电脱盐和高速电脱盐两种形式。
与低速电脱盐相比,高速电脱盐具有脱盐技术先进、脱盐效率高(单级脱盐率可达95%),单罐处理能力大、电耗低等优点。
该技术为PETROLITE公司九十年代开发的新技术,其主要特点是:a)进料位置不同于低速电脱盐,不是在水相,而是在电极板之间;b)进料管不用管式或倒槽式而采用特殊喷头型式;c)电脱盐罐处理能力不取决于油品在电场中的停留时间,而取决于喷头的能力;d)采用交流电,水平电极板。
目前世界上已有100多套电脱盐装置采用了该技术,国内镇海炼化、上海石化和齐鲁石化等亦采用了此脱盐技术。
高速电脱盐技术和低速电脱盐技术特点比较见表1-1表1-1 高速电脱盐技术和低速电脱盐技术特点比较项目低速电脱盐技术高速电脱盐技术原油进料位置水相电极板间(油相)进料部件形式多孔管或倒槽式高效喷头式供电型式交流或直流电交流电油在电场中停留时间6min 不要求(很短)原油处理能力(相同罐体)1(比较基准)2~2.5一级脱盐率,% 85~90 95二级脱盐率,% 95~97 99脱后原油含水,% 0.2 0.2排水含油,ppm ~200 ~150电耗,kWh/t原油0.2~0.5 0.03~0.1投资(相同处理能力)一般略高2、国内炼厂引进高速电脱盐技术状况见表1-2表1-2 国内炼油厂引进高速电脱盐技术状况简表项目镇海炼化Ⅲ常减压上海石化二蒸馏齐鲁石化三蒸馏大连西太平洋规模800万吨/年350万吨/年400万吨/年1000万吨/年采用技术高速高速高速高速技术来源Petreco公司Petreco公司Petreco公司Petreco公司罐体尺寸Φ3600×17700Φ3600×6000Φ3200×14000Φ4300×29500罐体新上新上利旧新上投产时间1998 1999 1999 20033、国内高速电脱盐技术长江(扬中)电脱盐设备公司在吸收消化进口高速电脱盐技术基础上进行改进开发出新一代的交直流高速电脱盐技术,从小试结果来看,与进口的高速电脱盐相比,它具有适应性更广、脱盐脱水效率更稳定等优点,目前已申请国家专利,国内已有高桥、上海石化、茂名、洛阳、金陵、扬子、兰州、镇海、大连、湛江等处理量大于500万吨/年的常减压采用了国产高速电脱盐技术,运行情况尚可。
新型计量泵在常减压装置的应用
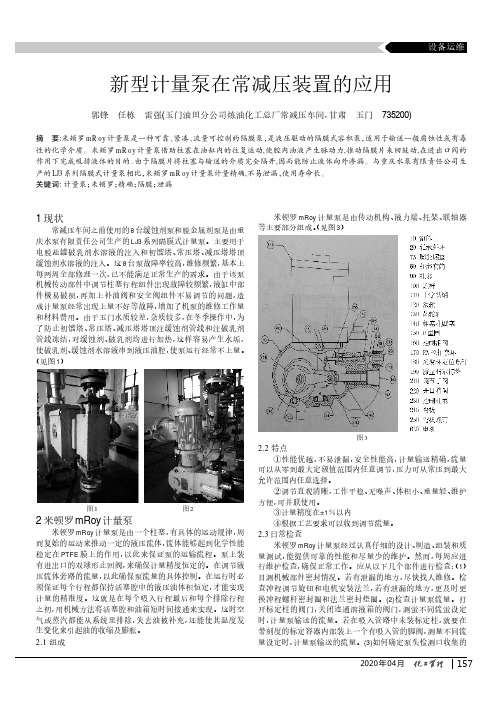
2020年04月新型计量泵在常减压装置的应用郭锋任栋雷强(玉门油田分公司炼油化工总厂常减压车间,甘肃玉门735200)摘要:米顿罗mRoy 计量泵是一种可靠、紧凑、流量可控制的隔膜泵,是液压驱动的隔膜式容积泵,适用于输送一般腐蚀性或有毒性的化学介质。
米顿罗mRoy 计量泵借助柱塞在油缸内的往复运动,使腔内油液产生脉动力,推动隔膜片来回鼓动,在进出口阀的作用下完成吸排液体的目的.由于隔膜片将柱塞与输送的介质完全隔开,因而能防止液体向外渗漏。
与重庆水泵有限责任公司生产的LJ3系列隔膜式计量泵相比,米顿罗mRoy 计量泵计量精确,不易泄漏,使用寿命长。
关键词:计量泵;米顿罗;精确;隔膜;泄漏1现状常减压车间之前使用的8台缓蚀剂泵和脱金属剂泵是由重庆水泵有限责任公司生产的LJ3系列隔膜式计量泵。
主要用于电脱盐罐破乳剂水溶液的注入和初馏塔、常压塔、减压塔塔顶缓蚀剂水溶液的注入。
这8台泵故障率较高,维修频繁,基本上每两周全部修理一次,已不能满足正常生产的需求。
由于该泵机械传动部件中调节柱塞行程组件出现故障较频繁,液缸中部件极易破损,再加上补油阀和安全阀组件不易调节的问题,造成计量泵经常出现上量不好等故障,增加了机泵的维修工作量和材料费用。
由于玉门水质较差,杂质较多,在冬季操作中,为了防止初馏塔、常压塔、减压塔塔顶注缓蚀剂管线和注破乳剂管线冻结,对缓蚀剂、破乳剂均进行加热,这样容易产生水垢,使破乳剂、缓蚀剂水溶液串到液压油腔,使泵运行经常不上量。
(见图1)图1图22米顿罗mRoy 计量泵米顿罗mRoy 计量泵是由一个柱塞,有具体的运动规律,周而复始的运动来推动一定的液压流体,流体能够起到化学性能稳定在PTFE 膜上的作用,以此来保证泵的运输流程。
泵上装有进出口的双球形止回阀,来确保计量精度恒定的。
在调节液压流体旁路的流量,以此确保泵流量的具体控制。
在运行时必须保证每个行程都保持活塞腔中的液压油体积恒定,才能实现计量的精准度。
炼油常减压装置特点及节能新技术

炼油常减压装置特点及节能新技术摘要:常减压装置能够回收余热、降低过剩空气系数,本文对如何控制常减压装置的能耗展开研究,分析常减压装置的特性,然后分析当前可以采取的技术措施。
通过研究帮助工厂解决常减压装置的运行能耗问题,提升综合效益。
关键词:常减压装置;特点;技术;应用引言:现代炼油厂为了保证工作的顺利进行,会使用常减压装置开展工作。
但是常减压装置同样有耗能较大的问题,为了保证生产的顺利进行,需要使用有效的技术,控制常减压装置的能耗。
1炼油常减压装置特性分析1.1加强烟气余热回收使用常减压装置能够回收炼油厂的烟气余热,常减压装置的余热回收系统会包括高温段空气预热器、低温段空气预热器两种装置,在高温段使用了高效的导热元件是,低温段使用双向板翅预热器[1]。
通过使用这些装置,常减压装置能够有效控制烟气余热所导致的露点腐蚀问题,控制烟气温度在130℃的安全范围以内。
通过使用常减压装置,其中的余热回收系统可以有效利用炼油系统的余热,解决温度浪费问题,并降低炼油系统的能耗临。
目前一般使用冷凝技术进行烟气的低温余热回收,可以有效提升热炉的热反应效率。
1.2减少过剩空气炼油厂工作中,如果剩余的空气系数比较小,加热炉内部的燃烧就会缺少足够的空气,很难满足加热炼油的要求,不仅会造成工作效率降低,还会释放出比较多的废物,对环境造成比较严重的损害。
但是如果盲目提升空气系数,过剩的空气就会将炉内多余的热量带走,同样会导致炼油设备热强度不能达标的问题,还会严重影响系统的热传递效率,也会缩短锅炉的使用寿命,以及造成空气污染。
为了解决上述问题,在目前的炼油工作中会使用常减压设备将空气系数控制在合理的范围内。
工作人员在点燃火嘴含氧量会比较高,常减压设备也会同时对气压进行调节,让设备的火焰能始终处于燃烧的状态下,并保证锅炉温度保持正常,工作人员通过随时控制常减压设备可以进行工作方式的调节,让炉内的空气系数保持最佳的运行状态。
1.3能源消耗大在目前的炼油厂生产中,常减压设备的装置会占据比较大的能源消耗,普遍超过了30%,在很多炼油厂重,常减压设备已经成为了最为主要的生产成本要素。
浅谈绕管换热器在常减压装置创新应用

设备运维减速器异常如漏油、磨损甚至停止运转;机械密封失效;罐体掉瓷。
减少、消除减速器故障的最有效办法就是做好润滑工作。
定点、定时、定量、定质、定人进行润滑仍然是最常见最有效的润滑管理模式。
对于机械密封,保持密封油盒洁净、油面稳定是延长机械密封寿命的最简单有效的方式。
目前也出现了无油润滑的干磨式机械密封。
更换反应釜机械密封是一个危险而工作量又大的维修活动,因此,在建立装置时就要重视维修设计,不用拆卸减速器及搅拌轴、人员不进入反应釜内即可更换机械密封。
搪瓷反应釜一旦掉瓷,尤其是反应釜下封头及罐体掉瓷,反应釜将无法继续使用。
引起掉瓷的原因除制造缺陷外,大多数情况下是异物撞击瓷面及冷热交替冲击;如给反应釜内投料时固体物料中混有石头、铁块等坚硬的异物击打瓷面;在给反应釜内升温或者降温时急冷或者快速升温。
因此避免物料中混入大块坚硬异物,精细操作,反应釜缓慢降温或者缓慢升温均是避免反应釜掉瓷的有效办法。
4.2离心分离设备的维修技术离心机是化工新行业使用广泛而价值较高的设备,其主要故障为主轴承轴封系统失效,机组振动超过允许值,安全联锁装置失效。
离心泵是化工行业最常见的机械设备之一,离心泵运行过程中常见的故障主要有设备抽空、泵不打量、轴承温度过高、泵体振动大、密封泄漏。
主要的处理方法为调节润滑油量、更换合适间隙的轴承、更换清洁的润滑油,去除机械杂质;泵体振动过大可能的原因为电动机与泵轴不同心、泵抽空、基础不牢、泵轴弯曲、轴承损坏或间隙过大。
主要的解决方法为对联轴器重新进行找正、加固基础、校正或更换泵轴、更换轴承、调整轴承间隙等;密封泄漏过大主要原因有填料磨损严重、轴或轴套磨损、动静环划伤或间隙不合适、弹簧压缩量不合适。
主要处理的方法有修复或更换动静环、调整弹簧压缩量等。
4.3静止设备的维修技术静止设备主要包括反应器、塔、换热器、储罐等。
静止设备的故障主要包括跑、冒、滴、漏以及设备腐蚀、压力容器的失效等情况。
静止设备主要通过日常巡检、定期检测缺陷、设备壁厚定期测量等方法进行维修保养。
先进控制技术在常减压装置上的开发与应用

夕 ) C (一 ) ∑c u —) ( ( = A p+ A B( f 5 k )
i =1
根据 输 出预测 值 再计 算 多变 量 预 测控 制 系统 的最 优控 制律 。
23 1 先 进 过 程 控 制软 件 应 用 介 绍 。.
S el h l 多变 量 优 化控 制器 (MOC 是 壳牌 全 球解 决 S p )
2 3 多变 量模 型预 测 控 制 .
上世 纪 8 0年 代以来 , S系统得 到了广泛应 用 , D 但
灰 箱 模 型 将 过 程 与 模 型 之 间 的 失 配 包 含 在 内 , 高 了控 提
制 器 的 鲁棒性 。在 控制 器 中引入 状 态变 量 来改 善对 大
《 动 技 与应 21 年 0 第5 自 化 术 用 0 1 第3 卷 期
工 业 控 制I 应 用 与
n s r on r l d Ap ia i n du ty C to an pl to s c
时 滞 过 程 的 预 测 精 度 。 例 如 , 常 压 塔 的 产 品 组 成 的 改 在 变 往 往 会 滞 后 于 塔 顶 灵 敏 板 的 温 度 。 使 用 灵 敏 板 温 度
流量的 影响耦 合严 重 , 常 波动较 大 。 通
x k+l =Ax k 4Bu k ( 、 ()- () ) 足 =C ( ) , ) x k (
其 中 : ∈ , e , ET, e y U I'A , e B , e C
() 1
,
不失一般性 , 假设矩 阵 是列满秩 的 , rn B m; 即 a k = 矩阵
2 1 工 艺 特 点
本装置 主要 由电脱盐 系统 、初 馏和常压 系统 、航煤
减压深拔技术在常减压蒸馏装置上的应用
减压深拔技术在常减压蒸馏装置上的应用
减压深拔技术是指在常减压蒸馏装置中,通过在蒸馏过程中采取一系列的措施,减少
或排除对组分塔底部的推动力,以达到减小深拔浸出塔对底部塔板气液分布状态影响的目的。
常减压蒸馏装置是一种在一定条件下进行分馏的设备,它可根据不同组分的沸点差异,将混合物中的各个组分分离出来。
在常减压蒸馏装置中,底部塔板的气液分布状态会受到
深拔浸出塔的推动力的影响,造成气液分布不均匀,严重时可能导致组分的“垫底”现象,即轻组分在塔底集聚,重组分在塔顶集聚,使得分馏效果下降,生产成本增加。
为了解决这个问题,减压深拔技术应运而生。
减压深拔技术主要包括以下方面的应
用:
1. 更换深拔浸出塔结构:采用新型的深拔浸出塔结构,如配置高效的减压深拔浸出
塔板或板栅等,在一定程度上减小对底部塔板气液分布状态的影响,提高分馏的效果。
2. 优化操作条件:通过控制塔底回流液量、塔顶蒸汽流量等操作参数,使得塔底塔
顶的液相质量更均匀,减小分馏过程中组分的集聚现象。
3. 引入额外的混合物进料点:在常减压蒸馏装置中,引入额外的混合物进料点,将
一部分混合物在塔底而非塔顶注入,调节塔内的气液分布,改善深拔浸出塔对底部塔板的
推动力,提高分馏效果。
减压深拔技术的应用可以有效地改善常减压蒸馏装置的分馏效果,降低生产成本。
它
不仅适用于石油化工行业,还可以应用于化工领域的其他分馏装置,如煤化工、精细化工等。
未来,减压深拔技术还有很大的发展空间,可以通过改进装置结构、调节操作参数等
方式,进一步提高分馏的效果,降低能耗,实现更加可持续发展的目标。
2024年炼油常减压装置中减压塔技术优化
2024年炼油常减压装置中减压塔技术优化减压塔是炼油常用的一种设备,用于降低石油产品中的压力和温度,将过热蒸汽或气体转化为液体。
随着炼油工艺的不断发展和炼油设备的不断升级,减压塔的技术也需要不断优化,以提高效率、降低能耗和减少对环境的影响。
2024年炼油常减压装置中减压塔技术优化主要包括以下几个方面:材料选择、结构设计、流动动力学分析、操作参数优化、节能降耗与环保措施等。
一、材料选择减压塔材料的选择直接影响到其使用寿命和安全性能。
2024年,炼油常减压装置中的减压塔可以采用更先进的高强度、高温抗腐蚀材料,如高温合金、镍基合金等。
这些材料具有良好的抗腐蚀性能和高温稳定性,可以有效延长减压塔的使用寿命,并提高设备的安全性。
二、结构设计减压塔的结构设计要考虑到流体动力学和传热性能等因素。
优化的设计可以提高减压塔的传质传热效率,并降低能耗。
结构设计需要考虑到流体的流动状态、流速和压降等参数,通过合理的结构设计可以减小流体的阻力和压降,提高减压塔的流动动力学性能。
三、流动动力学分析流动动力学分析是减压塔优化设计的关键环节。
减压塔内流体的流动状态对传质传热效率和能耗有着直接影响。
可以通过数值模拟等方法,研究减压塔内流体的流动规律,优化设计减压塔的内部结构和分布组件等,改善流体的分布和流动状态,提高传热效率,降低能耗。
四、操作参数优化优化减压塔的操作参数,可以提高减压塔的工艺效率和能源利用率。
操作参数优化主要包括进料压力、温度、流速等参数的优化。
合理的操作参数可以提高减压塔的转化率和产品质量,降低能耗和生产成本。
通过优化操作参数,可以实现能耗和产量的双重优化。
五、节能降耗与环保措施炼油常减压装置中减压塔的技术优化还需要考虑到节能降耗和环保问题。
可以采用一些节能措施,如余热回收、换热器优化设计等,降低能耗。
同时,还可以采用一些环保措施,如废气处理、废水处理等,减少对环境的影响。
技术优化的目标是在提高效率的同时,降低能耗和对环境的影响。
常减压蒸馏装置的节能分析
常减压蒸馏装置的节能分析常减压蒸馏装置是一种高效节能的分离技术,广泛应用于石油化工、化工、石油炼制等行业。
该装置通过降低系统压力,利用较低温度下的蒸馏和蒸汽重整技术,实现对混合物的分离和纯化。
下面将对常减压蒸馏装置的节能效果进行分析。
常减压蒸馏装置的节能效果主要体现在以下几个方面:1. 低温利用效率高:常减压蒸馏装置利用较低温度下的蒸馏技术,可以在较低的能耗下完成分离过程。
相比于传统的常压蒸馏装置,常减压蒸馏装置可以降低蒸馏过程中的能量损耗,提高能源利用效率。
2. 降低蒸汽消耗量:常减压蒸馏装置采用蒸汽重整技术,通过蒸汽的循环利用减少了蒸馏过程中的蒸汽消耗量。
这不仅可以降低能耗,同时也减少了对环境的影响。
3. 节水节热效果明显:常减压蒸馏装置在蒸馏过程中减少了水的使用量,可以有效地节约水资源。
降低了系统的压力还可以减少蒸发过程中的热能损失,提高热能利用效率。
4. 降低设备维护成本:由于常减压蒸馏装置在工作中采用较低的压力,减少了设备的应力和磨损,延长了设备的使用寿命,降低了维护成本和维修频率。
5. 提高产品纯度:常减压蒸馏装置通过较低的工作压力和温度,可以更加精确地控制物料的挥发和分离过程,提高产品的纯度和质量。
要实现上述的节能效果,还需要对常减压蒸馏装置的设计、操作和维护进行科学管理。
在设备的设计中应充分考虑热能的回收和利用,采用高效的换热器和双效换热器技术;在操作中应遵循节能减排的原则,合理控制温度、压力和流量等参数;在设备的维护中应定期进行检修和维护,及时处理故障,确保设备的正常运行和高效能利用。
常减压蒸馏装置是一种高效节能的分离技术,通过降低系统压力和利用较低温度的蒸馏和蒸汽重整技术,实现了对混合物的分离和纯化。
其节能效果主要包括低温利用效率高、降低蒸汽消耗量、节水节热效果明显、降低设备维护成本和提高产品纯度等。
为了实现更好的节能效果,还需要科学管理和合理运营该装置。
常减压蒸馏新技术
四、减压深拔技术
• 提高常压拔出率,促进减压深拔 • 采用新型填料,减少压降,提高闪蒸段真空度 • 减压炉炉管多次扩径和低速转油线 • 加入活性添加剂,提高减压拔出率 • 控制减压塔底温度,减少裂解气生成 • 改善减压塔闪蒸段分离效果,减少雾沫夹带 图 • 一段净洗和低液量分配,改善深拔蜡油的质量 图 • 减压塔深拔生产重交沥青 切换
环形填料
拉西环 勒辛环
十字环
内螺旋环
开孔环形填料
鲍尔环
共轭环
阶梯环型填料
鞍形填料的发展
弧鞍填料
矩鞍填料
环矩鞍型填料
球形填料的发展
多面球形填料
TRI球形填料
海尔环
麦勒环
返回
波纹板填料
金属板波纹填料
SK型薄壁陶瓷波纹填料
陶瓷规整
格栅型填料组装图
液体分布器
• 液体初始分布对填料塔性能的影响最大, 故液体分配器是最重要的塔内件;
三、低温位热的回收利用
问题的提出: • 低温位热源来自两个方面:
– 高温位热源经过多次换热,最终变成低温位 热源
– 直接来自温度不高的塔内馏出的轻质油
• 轻质原油轻组分多,低温位热源过多, 高温位热源明显不足
三、低温位热的回收利用
• 采取措施: • 原油分多段换热,充分利用低温位热源 • 采用“窄点”技术,优化换热网络 • 采用高效换热器,提高换热效率,如:
压塔回收其中的柴油; • 提高减压塔顶部的分离精度,直接出柴
油。
二、轻烃回收
• 采用初馏塔提压操作来实现回收轻烃
– 可免去气体压缩机,节省投资 – 降低能耗 – 不影响催化裂化• 采用增压机增压的方法回收轻烃
- 1、下载文档前请自行甄别文档内容的完整性,平台不提供额外的编辑、内容补充、找答案等附加服务。
- 2、"仅部分预览"的文档,不可在线预览部分如存在完整性等问题,可反馈申请退款(可完整预览的文档不适用该条件!)。
- 3、如文档侵犯您的权益,请联系客服反馈,我们会尽快为您处理(人工客服工作时间:9:00-18:30)。
常减压装置新技术的应用
一、国外高速电脱盐技术
1、从技术特点来分电脱盐一般有低速电脱盐和高速电脱盐两种形式。
与低速电脱盐相比,高速电脱盐具有脱盐技术先进、脱盐效率高(单级脱盐率可达95%),单罐处理能力大、电耗低等优点。
该技术为PETROLITE公司九十年代开发的新技术,其主要特点是:
a)进料位置不同于低速电脱盐,不是在水相,而是在电极板之间;
b)进料管不用管式或倒槽式而采用特殊喷头型式;
c)电脱盐罐处理能力不取决于油品在电场中的停留时间,而取决于喷头的能力;
d)采用交流电,水平电极板。
目前世界上已有100多套电脱盐装置采用了该技术,国内镇海炼化、上海石化和齐鲁石化等亦采用了此脱盐技术。
高速电脱盐技术和低速电脱盐技术特点比较见表1-1
表1-1 高速电脱盐技术和低速电脱盐技术特点比较
项目低速电脱盐技术高速电脱盐技术
原油进料位置水相电极板间(油相)
进料部件形式多孔管或倒槽式高效喷头式
供电型式交流或直流电交流电
油在电场中停留时间6min 不要求(很短)
原油处理能力(相同罐体)1(比较基准)2~2.5
一级脱盐率,% 85~90 95
二级脱盐率,% 95~97 99
脱后原油含水,% 0.2 0.2
排水含油,ppm ~200 ~150
电耗,kWh/t原油0.2~0.5 0.03~0.1
投资(相同处理能力)一般略高
2、国内炼厂引进高速电脱盐技术状况见表1-2
表1-2 国内炼油厂引进高速电脱盐技术状况简表
项目镇海炼化Ⅲ常减压上海石化二蒸馏齐鲁石化三蒸馏大连西太平洋
规模800万吨/年350万吨/年400万吨/年1000万吨/年
采用技术高速高速高速高速
技术来源Petreco公司Petreco公司Petreco公司Petreco公司
罐体尺寸Φ3600×17700Φ3600×6000Φ3200×14000Φ4300×29500
罐体新上新上利旧新上
投产时间1998 1999 1999 2003
3、国内高速电脱盐技术
长江(扬中)电脱盐设备公司在吸收消化进口高速电脱盐技术基础上进行改进开发出新一代的交直流高速电脱盐技术,从小试结果来看,与进口的高速电脱盐相比,它具有适应性更广、脱盐脱水效率更稳定等优点,目前已申请国家专利,国内已有高桥、上海石化、茂名、洛阳、金陵、扬子、兰州、镇海、大连、湛江等处理量大于500万吨/年的常减压采用了国产高速电脱盐技术,运行情况尚可。
4、高速电脱盐的适应性
高速电脱盐的进料是喷嘴,所以对粘度较高含杂质的原油要慎用,原油品种变化频繁的装置也要慎用,也就是说、高速电脱盐有一定的适用范围(见镇海发表过的文章)。
二、减压技术
1、全填料干式减压蒸馏
该工艺流程是国外七十年代逐渐发展起来的,其特点是在塔和炉内不注入水蒸汽,通过塔顶采用的三级抽空冷凝冷却系统,使减压塔的进料段和减压炉出口获得较高的真空度,在较低的操作温度下完成相同的减压拔出率。
减压塔内件采用了处理能力高、压力降小、传质传热效率高的新型、高效金属填料(如:规整填料)及相应的液体分布器,有利于提高减压馏分油的收率并降低了装置能耗。
2、大直径低速转油线及减压塔进料分布器
与全填料干式减压蒸馏相适应,发展了大直径低速转油线及新式结构的减压塔进料分布器。
采用大直径低速转油线的主要目的在于进一步降低减压炉出口压力,以获得较高的减压馏分油收率或较低的减压炉出口温度;采用新式结构的进料分布器的主要目的在于提高减压塔进料段的汽液分离效果,减少上升汽体的雾沫夹带量,同时有利于上升汽体的均匀分布提高填料的传热传质效果,改善产品质量。
3、加热炉及减压转油线
采用热管式空气预热器,尽量降低加热炉排烟温度,使加热炉热效率达92%以上。
采用大直径低速转油线及100%炉管吸收转油线热膨胀技术,使减压转油线温降控制在10℃以内。
4、减顶抽真空系统
影响减压拔出率的主要因素有减压塔蒸发层的温度、压力和汽提蒸汽量。
温度提高,减压拔出率提高,生产经验表明:进料段温度每提高10℃,总拔出率可提高2%~4%。
对于燃料型减压塔,由于炉出口的温度受油品热稳定性的限制,一般炉出口温度控制在不大于400~410℃。
进料段的压力降低,在相同的拔出率下,炉出口温度降低,炉负荷减少。
过低的塔顶压力会导致全塔压降的增加,使蒸发层压力的降低不明显,同时还将导致抽空系统能耗的增加。
大连1000万吨/年常减压装置为燃料型,减压的任务是为加氢裂化装置和渣油加氢脱硫装置提供原料,他们综合比较减压塔顶压力与减压炉出口温度和炉负荷的关系,选定减压塔顶压力为20mmHg。
表4-1 减压塔顶压力与抽空器耗量和减压炉负荷的比较
塔顶压力10mmHg 15mmHg 20mmHg 25mmHg 30mmHg
蒸汽耗量,kg/h 27763 22190 17813 16944 16537
蒸汽单耗,×104kcal/t 2.77 2.21 1.78 1.69 1.65
燃料单耗,×104kcal/t 6.35 6.51 6.59 6.67 6.74
总单耗,×104kcal/t 9.12 8.72 8.37 8.36 8.39
节能,×104kcal/t -0.73 -0.33 0.02 0.03 0
减压塔顶采用高效喷射式蒸汽抽真空加机械抽真空混合抽真空系统,在保证减顶真空度的前提下节约能量。
减压塔顶的操作压力设计值为12mmHg(绝)。
减顶抽真空系统目前一般采用水蒸汽抽真空系统,维护工作量小,可靠性高;但对于大型装置,机械抽真空系统愈显出其经济性的优点,节能降耗显著。
青岛1000万吨/年常减压装置减压塔顶采用高效喷射式蒸汽抽真空加机械抽真空混合抽真空系统,与采用全水蒸汽喷射式抽真空系统对比数据如下:混合抽真空方案全部水蒸汽抽真空方案
投资万元人民币+180 基准
水蒸汽耗量:吨/时基准+7.63
电 KW +160 基准
循环水:吨/时+100 基准
软化水:吨/时基准+3.0
折算能耗:千克标准/吨原油:-0.4413 基准
操作费用:万元人民币/年:-337.6632 基准
静态投资回收期:年0.533
由上表可见,采用混合抽真空系统比完全水蒸汽抽真空系统节能0.4413千克标油/吨原油,投资回收期只需0.533年。
5、减压深拔
减压深拔工艺技术目前在国内还未自主开发,少数几个新建的大型常减压装置的减压深拔技术均从国外Shell(壳牌)和KBC二个公司引进。
根据情报调研和技术交流,对这二个公司的减压深拔工艺技术初步了解如下:
壳牌公司的HVU减压蒸馏技术,是在传热段采用空塔喷淋传热技术,将减压塔全塔压降降低,达到更高的拔出率。
此项空塔喷淋传热技术目前也只有壳牌公司可以设计,但该公司对减压深拔后减压炉管内可能生焦,导致危及安全生产及缩短操作周期等工程问题的解决未做深入介绍,只是壳牌公司保证减压炉在430℃左右的出口温度下可连续操作4年以上。
KBC公司的减压深拔的技术核心是对减压炉管内介质流速、汽化点、油膜温度、炉管管壁温度、注汽量(包括炉管注汽和塔底吹汽)等的计算和选取,以防止炉管内结焦,保证四年以上的操作周期和安全生产。
并且该公司对减压塔及其内构件的选取无特殊要求。
通过最近的技术交流和谈判、二家公司的技术特点不同,工艺思路也不一样,技术服务的内容及报价差别更大,各有其适用性。