常减压蒸馏装置规格
常减压装置说明书

一、工艺流程1.1装置概况本装置为石油常减压蒸馏装置,原油经原油泵(P-1/1.2)送入装置,到装置内经两路换热器,换热至120℃,加入一定量的破乳剂和洗涤水,充分混合后进入电脱盐罐(V1)进行脱盐。
脱后原油经过两路换热器,换热至235℃进入初馏塔(T1)闪蒸。
闪蒸后的拔头原油经两路换热器,换热至310℃,分四股进入常压塔加热炉(F1)升至368℃进入常压塔(T2)。
常压塔塔底重组分经泵送到减压塔加热炉(F2)升温至395℃进入减压塔(T4)。
减压塔塔底渣油经两路换热器,送出装置。
1.2工艺原理1.2.1原油换热罐区原油(45℃)经原油泵P-1/1.2进入装置,分两路进行换热。
一路原油与E-1(常顶气)、E-2(常二线)、E-3(减一线)、E-4(减三线)、E-5(常一线)、E-6(减渣油)换热到120℃;二路原油与E-14(常顶气)、E-16(常二线)、E-17(减二线)换热到127.3℃。
两路原油混合换热后温度为120℃,注入冷凝水,经混合阀(PDIC-306)充分混合后,进入电脱盐罐(V-1)进行脱盐脱水。
脱后原油分成两路进行换热,一路脱后原油与E-7(常二线)、E-8(减二线)、E-9/1.2(减三线)、E-10/1~4(渣油)换热到239.8℃;二路脱后原油与E-11/1.2(减一中)、E-12/1.2(常二线)、E--13/1.2(减渣)换热到239.7℃。
两路脱后原油换热升温到230℃合为一路进入初馏塔(T-1)汽化段。
初馏塔塔顶油气经空冷气(KN-5/1~5)冷凝到77℃,进入初顶回流罐(V-2)。
油气经分离后,液相用初顶回流泵(P-4/1.2)打回初馏塔顶作回流,其余油气继续由初顶空冷器(KN-1/1~3)、初顶后冷器(N-1)冷却到40℃,进入初顶产品罐(V-3)。
初馏塔侧线油从初馏塔第10层用泵(P-6/1.2)抽出与常一中返塔线合并送到常压塔第33层塔盘上。
初馏塔底拔头油,经初底泵(P-2/1.2)抽出分两路换热。
常减压装置简介

原油常压蒸馏及其特点
4.常压塔常设置中段循环回流
即从精馏塔上部的精馏段引出部分液相热油(或者是侧线产品), 经与其它冷流介质换热或冷却后再返回塔中,返回口比抽出口通 常高2~3层塔板。 作用:在保证各产品分离效果的前提下,取走精馏塔中多余的热
量
优点:在相同的处理量下可缩小塔径,或者在相同的塔径下可提 高塔的处理能力;可回收利用这部分温度较高的热源。
实际装置图片
工艺流程简图
电脱盐工艺流程简图
原油电脱盐简介
一、原油电脱盐的工序包括: (1) 脱盐前水洗。用于除去原油中溶于水的酸(Sour) 、碱( alkali )、盐( salt) 等无机物。 (2) 沉淀(Precipitation)。某些不溶于水的杂质,可以吸附在固体颗 粒表面或聚集在水滴表面,随固体物或水滴一起沉淀,与油分离 。 (3)破乳( Demulsification )。通过向原油中加入破乳剂,使水流管,耐火衬里,管线 支撑和挂钩,主要传热方式是对流,对流室一 般担负全炉热负荷的20%~30%,对流室吸热 量的比例越大,全炉的热效率越高,为了尽量 提高传热效果,对流室多采用钉头管和翘片管。 燃烧器是产生热量部件,是炉子的重要组成部 分。要保证火焰不冲刷炉管并实现低氧完全燃 烧。
加热炉简介
余热回收系统是从离开对流室的烟气中进一步 回收余热的部分。回收方法分为两类,一类采 用空气预热方式回收热量;另一类是采用余热 锅炉回收热量。 通风系统的任务是将燃烧用空气导入燃烧器, 并将废烟气引出炉子,它分为自然通风方式和 强制通风方式两种。
蒸馏的形式
3.精馏(rectification)
精馏是分离液相混合物的有效手段,它是在多次部分 气化和多次部分冷凝过程的基础上发展起来的一种蒸 馏方式。
150万吨常减压蒸馏装置工艺管道试压措施
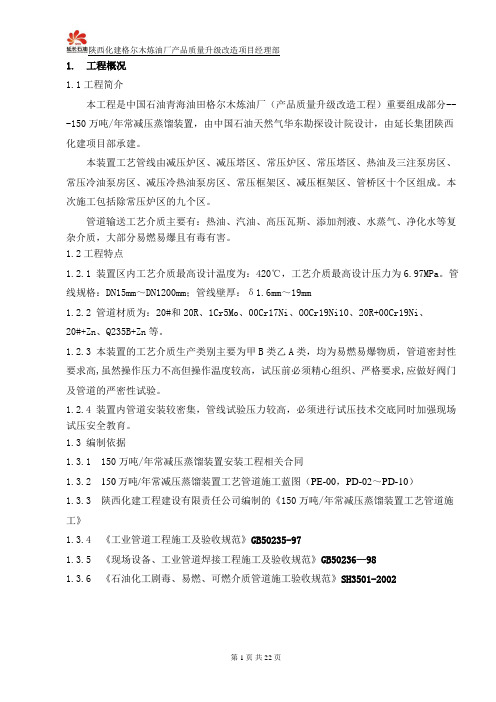
1.1工程简介本工程是中国石油青海油田格尔木炼油厂(产品质量升级改造工程)重要组成部分---150万吨/年常减压蒸馏装置,由中国石油天然气华东勘探设计院设计,由延长集团陕西化建项目部承建。
本装置工艺管线由减压炉区、减压塔区、常压炉区、常压塔区、热油及三注泵房区、常压冷油泵房区、减压冷热油泵房区、常压框架区、减压框架区、管桥区十个区组成。
本次施工包括除常压炉区的九个区。
管道输送工艺介质主要有:热油、汽油、高压瓦斯、添加剂液、水蒸气、净化水等复杂介质,大部分易燃易爆且有毒有害。
1.2工程特点1.2.1 装置区内工艺介质最高设计温度为:420℃,工艺介质最高设计压力为6.97MPa。
管线规格:DN15mm~DN1200mm;管线壁厚:δ1.6mm~19mm1.2.2 管道材质为:20#和20R、1Cr5Mo、00Cr17Ni、OOCr19Ni10、20R+00Cr19Ni、20#+Zn、Q235B+Zn等。
1.2.3 本装置的工艺介质生产类别主要为甲B类乙A类,均为易燃易爆物质,管道密封性要求高,虽然操作压力不高但操作温度较高,试压前必须精心组织、严格要求,应做好阀门及管道的严密性试验。
1.2.4 装置内管道安装较密集,管线试验压力较高,必须进行试压技术交底同时加强现场试压安全教育。
1.3 编制依据1.3.1 150万吨/年常减压蒸馏装置安装工程相关合同1.3.2 150万吨/年常减压蒸馏装置工艺管道施工蓝图(PE-00,PD-02~PD-10)1.3.3 陕西化建工程建设有限责任公司编制的《150万吨/年常减压蒸馏装置工艺管道施工》1.3.4 《工业管道工程施工及验收规范》GB50235-971.3.5 《现场设备、工业管道焊接工程施工及验收规范》GB50236—981.3.6 《石油化工剧毒、易燃、可燃介质管道施工验收规范》SH3501-20022.1管道试压程序:试压前准备---试压前检查---临时管线的铺设,试压管线间的连接---管道吹扫—加设盲板,进行系统隔离---管道设置压力表位置,设置排空点、安装试压泵---试压前流程检查---进水---升压---稳压---检查---合格后放水---拆卸盲板、管道复位2.2管道试压分组:2.2.1管道试压按分组进行,分组原则:按管道压力等级进行分组:对压力等级一样或相近的管道划为一组进行跨系统试压。
常减压讲解

原油与~2(常顶循)、E-8(常一)、~2(常三2)、~2(常四2)、~2(减五2)、~2(减渣一路6)、~2(减二)换热到140℃。
两路原油换热混合后分四路进行换热:
一路:
原油经E-14(减三2)、~2(减渣二路5)、E-16(常二中2)、E-17/1~2(减二中3)、E-18(减三1);
二路:
减三线油从减压塔第4层集油箱馏出,进减三线汽提塔(C-5II),汽提出的轻组分和水蒸汽返回减压塔。汽提后的减三线油287℃经减三线泵(~2)抽出,与原油(E-
18、E-14)换热,经ER-2发汽后,再经减三线冷却器(~2)冷却到90℃~98℃出装置作HVI
150、HVI200润滑油基础油原料。
减四线油从减压塔第6层集油箱馏出,进入减四线汽提塔(C-5III),汽提出的轻组分和水蒸汽返回减压塔,汽提过的减四线油328℃经减四线泵(~2)抽出,依次与~
原油经E-19(常三1)、~2(减渣一路5)、~2(常四1)、~2(常二1)、~2(减二中2);
三路:
原油经E-24(减一中2)、E-25(常一中1)、~2(减渣二路4)、~2(减六1)、~2(减渣二路3);
四路:
原油经~2(减四3)、E-30(减一中2)、E-31(常一中1)、~2(减渣一路4)、~2(减四2)、~2(减渣一路3)。
41、42、43后进入装置。自
2004年4月下旬开始,在大庆原油中掺混5%~10%的俄罗斯原油。###
4主要产品及付产品
主要产品:
初顶汽油、常顶汽油、常一线、常二线、常三线、常四线、减顶油、减一线、减二线、减三线、减四线、减五线、减六线、热渣油、冷渣油。
付产品:
初顶瓦斯、常顶瓦斯、减顶瓦斯。5工艺原理
常减压精馏塔机械设计

DN4200/DN3000减压塔机械设计摘要本设计是对工艺设计中的常滴油精馏塔进行设计,设计过程主要依据GB150-1998《钢制压力容器》标准和JB/T4710-2005《钢制塔式容器》标准进行设计计算的。
该减压塔采用的是变径板式塔结构,并采用单溢流型塔盘与泡罩塔盘,操作介质为常底油。
精馏塔是目前石油化工领域应用的最多的塔设备。
在说明部分中,主要介绍塔设备在石油化工生产中的作用、地位、发展现状、特点以及分类,优先选用板式塔的条件,以及舌型塔盘和泡罩塔盘的结构和优缺点,同时又对塔的材料选择,筒体和封头的选用进行了说明和论述。
接下来又介绍了塔的附属构件结构,对筒体、裙座、封头、吊柱、地脚螺栓座、基础换班、筋板的选用进行了介绍并且校核了他们的强度,同时也对裙座与通体的连接方式与结构进行了说明。
在计算部分主要是针对塔体的筒体、封头的材料选择、壁厚的选取进行了计算,还有稳定性的校核。
对自振周期、地震载荷、风载荷进行了计算,同事又进行了该筒体的轴向强度以及稳定性的校核,全做的设计计算及其校核,地脚螺栓座的设计及其强度校核、筋板、盖板及开孔补强的设计计算校核。
最后经过计算以及强度校核,设计出合理的减压精馏塔的结构,并绘制出图纸。
关键词:筒体、封头、强度、校核。
1 说明部分1.1 前言在石油炼化厂的生产装置中,气-液和液-液2相直接接触进行传质传热的工艺很多。
例如,精馏、吸收、解吸、萃取和气体增湿等。
这些公益大多数都在塔内完成。
因此,塔设备的性能对炼油、化工装置的生产能力、产品质量与消耗指标以及三废处理以及环境保护等各个方面都有较大影响。
据统计,在石油炼化厂中,塔设备的投资额占到总投资额的10%-20%,塔设备消耗的钢材量占总投资刚才量的25%-30%。
塔设备之所以被大量采用,是因为它可以为气-液之间的传质传热提供了适宜的条件。
这些条件除了维持一定的塔内压力、温度、气液流量以外,一些特定的塔内件还从结构上保证了上升气体和下降气体的充分接触时间、空间和表面积,从而能够达到较理想的传质、传热效果。
常减压蒸馏装置简介
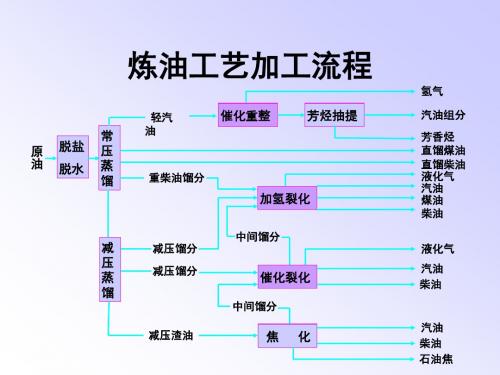
氢气 轻汽 油
催化重整
芳烃抽提
汽油组分 芳香烃 直馏煤油 直馏柴油 液化气 汽油 煤油 柴油 液化气
原 油
脱盐
脱水
常 压 蒸 馏
重柴油馏分
加氢裂化
中间馏分
减 压 蒸 馏
减压馏分 减压馏分
催化裂化
中间馏分
汽油 柴油
减压渣油
焦
化
汽油 柴油 石油焦
一、常减压装置基本原理
• 原油主要由碳氢化合物组成的复杂混合物,主要由碳 和碳两种元素组成。其中:碳占83~87%,碳占11~ 14%总重,此外,有少量氧、氮、硫等,在石油灰份 中还有微量非金属和金属元素。 • 蒸馏是将一种混合物反复地使用加热汽化和去热冷凝 相结合的手段,使其部分或完全分离的过程。它是利 用液体混合物中各组分沸点和蒸汽压(即相对挥发度) 的不同,在精馏塔内,轻组分不断汽化上升而提浓, 重组分不断冷凝下降而提浓,相互间不断地进行传热 和传质过程,在塔顶得到纯度较高的轻组分产物,在 塔底得到纯度较高的重组分产物,它是实现分离目的 的一种最基本也是最重要的一种手段。
3 腐蚀形态、部位及原因
3.2高温(240~425℃)部位的高温硫的均匀腐蚀及环烷酸的沟槽状 腐蚀
减压塔的腐蚀
①
②
③
④
炼制大庆原油,减压塔使用碳钢基本不腐蚀和腐蚀轻微,进料段塔 壁可用碳钢防冲板。 炼制辽河原油,减压塔进料段20g塔壁及其上、下四层A3F塔盘板, 腐蚀速度均大于3mm/a,腐蚀形态为“沟槽”状 炼制胜利原油,减压塔切线进料段塔壁(20g)年腐蚀率>4.3mm/a, “冲蚀”。塔底液相部位塔壁(20g)年腐蚀率2.5mm,均匀腐蚀, 塔底1~3层塔盘及内构件,碳钢年腐蚀率>2.0mm,15CrMo为1.46mm, 均匀腐蚀。塔底4~5层塔盘及内构件,碳钢年腐蚀率为3mm,均匀腐 蚀加冲蚀(靠近切线进料侧) 炼制管输原油减压塔其腐蚀较高硫低酸值原油严重,塔体改用20g+ 00Cr18Ni12Mo2Ti复合板可以拟制腐蚀,但进料处塔壁的冲蚀不可避 免。
石油炼制常压减压蒸馏装置
第十四章石油炼制常压减压蒸馏装置一、常减压蒸馏装置概述及工艺流程说明1、装置概述装置主要设备有30台, 各类设备参数如下。
(1) 加热炉2台常压炉1 台, 138,160,000 kJ/h减压炉1台, 75,360,000 kJ/h(2) 蒸馏塔4座初馏塔(塔-1):φ 3000×26033 mm常压塔(塔-2):φ3800×34962 mm汽提塔(塔-3):φ1200×24585 mm减压塔(塔-4):φ6400/φ3200×38245 mm(3) 冷换设备116台(不包括空气预热器)换热器76台,总换热面积11455 m2,其中用于发生蒸汽有1140 m2,用于加热电脱盐注水175 m2;冷凝冷却器40 台,总冷却面积10180 m2。
(4) 泵55台电动离心泵42台,蒸汽往复泵1台,计量泵10台,刮板泵2台。
(5) 风机1台。
(6) 容器 33个(7) 吹灰器26台其中伸缩式4台,固定式22台。
2、工艺流程说明(1)原油换热系统①原油从油罐靠静位能压送到原油泵(1#、2#)进口,在原油泵进口注入利于保证电脱盐效果的破乳剂和新鲜水,经泵后再注入热水,然后分三环路与热油品换热到110~120℃,进入电脱盐罐进行脱盐脱水。
②原油在电脱盐罐内经20000V高压交流电所产生的电场力作用,微小的水滴聚集成大水滴,依靠密度差沉降下来,从而与原油分离。
因原油中的盐分绝大部分溶于水中,故脱水其中也包括脱盐。
③原油从电脱盐罐出来后注入NaOH,目的是把原油残留的容易水解的MgCl、CaCl2转2化为不易水解的NaCl,同时中和原油中的环烷酸、H2S等,降低设备腐蚀速率,延长开工周期。
然后经接力泵(01#,02#)后分三路,其中二路继续与热油品换热到220~230℃后进初馏塔,另一路则先后经过炉-2、炉-1对流室冷进料管加热到210~220℃后进初馏塔。
(2)初馏系统被加热至220~230℃的原油进入初馏塔(塔-1)第6层(汽化段)后,分为汽液两相,汽相进入精馏段(第6层上至塔顶),液相进入提馏段(第6层下至塔底)。
常减压装置新技术介绍
1.7 塔内件
近年来常减压蒸馏系统的主要进步在于新 型或改进塔内部的开发。其发展方向是首先实现 汽液混合(操作条件甚至远在液泛点以上)然后 用辅助设施实现汽液相分离。这样可以大大提高 处理量,脱除以前不能超过液泛点的制约。采用 这一理念,各塔器内部构件供应商相继推出了一 系列专利新产品,据称新型塔板可以提高能力 30%~50%或更多。
常减压装置新技术介绍
主要内容
1、国外蒸馏装置技术现状及发展趋势 2、国内蒸馏装置技术现状
1. 国外蒸馏装置技术现状及发展趋势
1.1 单套蒸馏装置的能力
随着炼厂规模的扩大,单套蒸馏装置的加工规 模也日益大型化。美国ExxonMobil公司贝汤炼油厂 的一套蒸馏装置规模为1300x104t/a常压塔直径9.75 米。
1.3减压渣油的切割点温度和总拔出率
对于不同的原油,减压拔出率的要求和意义是 完全不同的。对于低硫低金属石蜡基原油的燃料型 常减压装置,由于其减压渣油可以全部进入重油催 化裂化装置加工,因此不必追求减压拔出率,甚至 可以不需要减压蒸馏,全部常压渣油都可以直接进 入重油催化裂化装置。对于生产润滑油的常减压装 置,减压拔出率应根据对润滑油的粘度要求和丙烷 脱沥青装置的情况来决定减压拔出率。对于生产道 路沥青的常减压装置,减压拔出率应根据沥青的生 产要求而定。
近几年来,国外蒸馏装置工艺又有了新的 进展。法国的ELF和Technip公司共同开发了一 种次分馏技术,主要将汽,煤,柴油等各种产 品逐渐进行分离,从而降低工艺总用能,可以 降低能耗30%左右。
壳牌石油公司提出的整体蒸馏装置(Shell Bulk Distillation Unit),将原油蒸馏装置,加氢脱硫装置, 高真空减压蒸馏装置和减粘装置作为一个整体加以 优化。整体分馏装置将原油分为:常压渣油,含蜡 馏分油,中间馏分油和石脑油组分。常压部分分出 常压渣油,中间馏分和石脑油以下的馏分。中间馏 分在加氢分馏脱硫塔中分离为煤油,轻,重柴油, 常压渣油进入高真空减压蒸馏,分馏出的蜡油作为 催化裂化装置和加氢裂化装置的原料。整体整流装 置可以节省投资的30%左右。
常减压 常三线 馏程范围
常减压常三线馏程范围1.引言1.1 概述概述在石油工业中,常减压、常三线和馏程范围是重要的概念和技术。
它们在石油炼制过程中的应用不仅能够提高生产效率,还有助于改善产品质量。
因此,对于了解和掌握这些概念和技术的原理和应用具有重要的意义。
常减压是指在油品的加热过程中,通过降低压力来使得沸点降低的一种工艺。
在石油炼制中,高温和高压是常见的操作条件,而常减压则能够有效地降低产物的沸点,以达到更好的分离和提纯效果。
通过控制不同阶段的压力变化,可以实现对油品的分馏过程,使得不同沸点范围的组分得以分离。
常减压技术广泛应用于石油炼制和化工领域,对于提高产品质量和产能具有重要的作用。
常三线是指石油产品在通常温度下的蒸馏过程中,分馏过程中沸点范围内的部分。
常三线通常是指在石油炼制过程中进行几次蒸馏后,可分为功能等级不同的三个主要组分。
这三个组分分别是轻质油、中质油和重质油。
常三线技术能够有效地对原油进行分级,从而使得不同组分能够在相应的温度下得以分离和提纯。
通过常三线技术,可以将石油产品进一步细分,以满足不同领域和工业的需求。
馏程范围是指在石油产品的蒸馏过程中,油品的不同组分之间的沸点范围。
不同的沸点范围对应不同的油品组分。
馏程范围的大小和清晰度,对于石油产品的提纯和分离效果有直接影响。
较大的馏程范围意味着更清晰的组分分离,而较小的馏程范围可能导致组分之间的混合和交叉。
因此,在石油炼制过程中,合理控制馏程范围的大小和清晰度对于产品的质量和产能具有重要的影响。
本文将深入探讨常减压、常三线和馏程范围的背景、原理和应用。
将重点介绍它们在石油炼制过程中的重要性和作用,并对未来的发展方向进行展望。
希望通过本文的阐述,读者能够更加全面地了解常减压、常三线和馏程范围对于石油炼制的重要意义,从而在实践中能够更好地应用和运用这些技术,提高生产效率和产品质量。
1.2文章结构文章结构部分可以按照以下方式进行描述:1.2 文章结构本文将分为三个主要部分,分别是常减压、常三线和馏程范围。
常减压蒸馏装置设计-38页精选文档
设计说明书1.1装置的概况和特点本设计主要以锦州石化公司二套常减压为设计原型,主要数据取自生产实际。
所处理的原料为70%辽河原油、20%的江西原油、10%的冠军原油,经过常压塔、减压塔的分离得到合格的产品。
辽河原油属于低硫中间基原油,含环烷酸多根据原油的性质、特点和市场的需求主要生产重整汽油、航空煤油、轻柴油、重柴油、混合蜡油、渣油等。
装置由原油电脱盐、常减压蒸馏、航煤精制部分组成。
根据加工含环烷酸原油的特点,结合加工含环烷酸原油的经验,优化了设备选型及选材,采用了目前最先进技术既初馏塔、常压塔塔盘为ADV高效塔盘。
减压塔采用规整填料,处理物料能力大,汽、液接触均匀,传质效果较好。
以实现装置长周期运行。
高温部位设备和管线全部采用不锈钢材质,以达到防腐的目的。
初顶、常顶用空冷代替水冷,节约了用水量,也减少了三废处理量。
常压塔设顶循环回流和二个中段回流,以使塔内汽、液相负荷分布均匀,提高塔的处理能力,减小塔顶冷凝器的负荷。
为了降低减压塔内真空高度,提高沸点,减压塔采用二级抽真空器。
即蒸汽喷射泵和水环抽真空泵。
在采用新工艺新设备的同时优化了工艺流程,为了节能常压系统采用4台空冷器,为增加处理量常压炉四路进料四路出。
环烷酸对金属的腐蚀一般发生在介质流速高和涡流状态处,其温度范围为230~280℃和350~400℃。
常减压蒸馏装置受环烷酸腐蚀较重的部位常发现在下述几处:常压炉出口部分炉管、减压炉全部炉管、常减压炉转油线和塔汽化段。
采取的防护措施除原油住碱外,适当地增加炉子转油线尺寸以降低介质流速,并结合具体条件选用耐腐蚀材质,可以减少有关部位的腐蚀速率。
综上所述,在采取了“一脱四注”的综合措施后,常减压蒸馏装置有关系统的腐蚀率大大下降。
为使相当数量的中间馏分得到合理利用,因为它们是很多的二次加工原料,又能从中生产国民经济所需的各种润滑油、蜡、沥青的原料。
因此本设计采用三段汽化蒸馏,即预汽化—常压蒸馏—减压蒸馏。
- 1、下载文档前请自行甄别文档内容的完整性,平台不提供额外的编辑、内容补充、找答案等附加服务。
- 2、"仅部分预览"的文档,不可在线预览部分如存在完整性等问题,可反馈申请退款(可完整预览的文档不适用该条件!)。
- 3、如文档侵犯您的权益,请联系客服反馈,我们会尽快为您处理(人工客服工作时间:9:00-18:30)。
常减压蒸馏装置规格
常减压蒸馏装置是一种常减压工艺,用于分离混合物中不同组分的技术。
常减压蒸馏装置的规格对于提高装置的效率和产品质量至关重要。
本文将从装置的结构、规格及其应用等方面进行详细介绍。
一、装置结构
常减压蒸馏装置由以下几个主要部分组成:
1. 蒸馏塔:蒸馏塔是装置的核心部分,用于实现混合物的分离。
常见的蒸馏塔结构包括板式塔和填料塔两种,根据不同的分离要求选择不同的结构。
2. 蒸汽发生器:蒸汽发生器用于产生蒸汽,提供给蒸馏塔中进行蒸馏过程所需的能量。
3. 冷凝器:冷凝器用于冷却蒸汽,使其变为液体,以便继续循环使用。
4. 回流器:回流器用于将部分冷凝后的液体回流至蒸馏塔,以提高分离效果。
5. 泵:泵用于循环液体,保持蒸馏塔内的流体循环。
二、规格选择
常减压蒸馏装置的规格选择应根据分离要求、原料性质和产品要求等因素进行综合考虑。
以下是常减压蒸馏装置规格选择的几个关键因素:
1. 蒸馏塔高度:蒸馏塔高度决定了分离过程的效率,一般情况下,
塔高越高,分离效果越好。
但高度过高会增加装置的投资成本和能耗。
2. 塔内板数或填料量:塔内板数或填料量直接影响分离效果,一般情况下,板数或填料量越多,分离效果越好。
但过多的板数或填料量会增加装置的复杂性和能耗。
3. 冷凝器冷却面积:冷凝器冷却面积的大小决定了冷却效果,一般情况下,冷却面积越大,冷凝效果越好。
但过大的冷却面积会增加装置的体积和成本。
4. 泵的流量和扬程:泵的流量和扬程应根据装置的设计要求确定,以保证装置的正常运行。
三、应用领域
常减压蒸馏装置广泛应用于石油化工、化学工程、精细化工等领域。
具体应用包括以下几个方面:
1. 石油行业:常减压蒸馏装置用于石油的裂解、提炼等工艺,实现原油的分离和产品的提纯。
2. 化学工程:常减压蒸馏装置用于化学反应的产物分离、溶剂回收等工艺,实现产品的纯化和资源的循环利用。
3. 精细化工:常减压蒸馏装置用于精细化工领域的高纯度产品制备,实现高品质产品的生产。
总结:
常减压蒸馏装置规格的选择对于装置的效率和产品质量具有重要影
响。
在实际应用中,需要根据具体情况进行综合考虑,选择合适的装置结构和规格。
常减压蒸馏装置在石油化工、化学工程、精细化工等领域有着广泛的应用前景,为相关行业的发展提供了强有力的支持。