分析国内外压铸模具发展历程及现状.
压铸技术的发展现状与展望

压铸技术的发展现状与展望摘要:本文简述了压铸工艺的特征及工艺的发展历程。
简要介绍了国外的最新压铸工艺发展状况,并与国外的先进技术进行比较,从压铸设计、工艺、设备、模具等几个方面进行了总结。
本文主要阐述了压铸、固态压铸、加氧压铸和真空压铸等几种新的压铸技术。
本文主要阐述了计算机技术在铸造工艺中的应用,以及CIMS的应用。
并对今后的发展方向进行了预测。
关键词:压铸工艺;压铸设计;模具;真空压铸;发展方向1.压铸技术的特点与发展历史1.1压力铸造技术的特点在加压过程中,通常对原材料施加20-200 MPa的压力,填充时的初始速度是15-70米/秒,填充时只有0-01-0.20秒。
正是因为这种特殊的注塑方法和凝固方法,才使它有了自己的特色。
(1)能够得到具有复杂形状和薄壁但外形清楚的铸件。
铸件的壁厚度一般为1至6毫米,较小的铸件可能较薄,较大的铸件可能较厚。
对于复杂部件或者其它铸造工艺不能生产的部件,可以采用压力浇铸工艺。
(2)铸造精度高,尺寸稳定,加工余量少,表面光洁。
加工余量通常为2~5毫米。
采用压铸工艺生产的铸件具有良好的可互换性。
通常情况下,只需要稍加加工即可组装,而有些部件则可以不经过任何加工就可以组装起来。
(3)铸件组织致密,机械性能好。
铸件在加压下凝固,得到了细小的颗粒,因此铸件的组织非常紧密,并且具有很高的强度。
此外,在铸造过程中,激光冷却会使铸件表面发生硬化,从而使铸件具有较好的耐磨性能。
(4)高效的生产。
该工艺具有较短的生产周期,且一次运行周期为5~3分钟,适合大规模生产。
(5)采用嵌铸法进行压力浇铸,可以减少组装过程,简化生产过程。
镶嵌材料一般为钢,铸铁,铜,绝缘材料等。
采用嵌铸工艺可以生产出具有特定需求的铸件。
1.2压铸技术的历史自1855年 Mergenthaler将活塞压射圆筒浸泡在熔化合金中,制成条形活字铸件至今已有153年。
1869年,巴巴奇使用了“锌加强铅锡合金压铸工艺”制造了部分部件。
中国压铸行业发展历程及现状
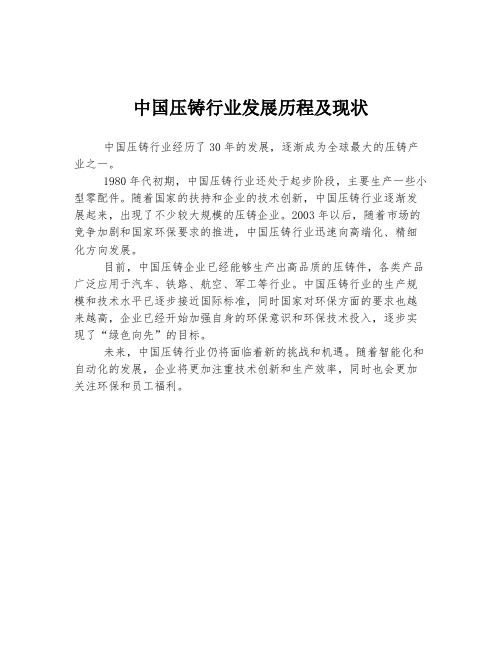
中国压铸行业发展历程及现状
中国压铸行业经历了30年的发展,逐渐成为全球最大的压铸产业之一。
1980年代初期,中国压铸行业还处于起步阶段,主要生产一些小型零配件。
随着国家的扶持和企业的技术创新,中国压铸行业逐渐发展起来,出现了不少较大规模的压铸企业。
2003年以后,随着市场的竞争加剧和国家环保要求的推进,中国压铸行业迅速向高端化、精细化方向发展。
目前,中国压铸企业已经能够生产出高品质的压铸件,各类产品广泛应用于汽车、铁路、航空、军工等行业。
中国压铸行业的生产规模和技术水平已逐步接近国际标准,同时国家对环保方面的要求也越来越高,企业已经开始加强自身的环保意识和环保技术投入,逐步实现了“绿色向先”的目标。
未来,中国压铸行业仍将面临着新的挑战和机遇。
随着智能化和自动化的发展,企业将更加注重技术创新和生产效率,同时也会更加关注环保和员工福利。
我国铸造模具发展现状及发展建议

我国铸造模具发展现状及发展建议摘要:随着时代的发展,相应的一系列工业方面的需求也在不断提高,正因如此,工业科技的提高和发展也成为了时代与社会的硬性要求。
我国作为工业大国,相应的模具等方面的技术发展也是十分关键的一个版块。
相关科技、工艺等多方面都是十分重要的,对于其现有生产技术和未来发展情况进行有效分析,也可以进一步辅助该类工艺进一步的加强和提高,从而进一步提升相关工艺的有效性和精准性。
本文就铸造类模具的发展现状做简单的分析和探讨。
关键词:铸造类模具;发展现状;分析探讨;0 引言铸造模具是压铸生产中三大必备因素之一, 模具制造的好坏直接影响到压铸的生产效率和产品的质量, 关系着压铸的成本。
中国铸造模具工业发展到今天,经历艰辛的历程。
通过派人出国考察, 引进国外铸造模具先进技术, 制定有关铸造模具国家标准一系列措施, 使得铸造模具工业有了很大发展, 并在某些技术方面有所突破。
第二汽车制造厂采用新技术、新材料为日本五十铃厂制造了高质量的大型铸造模具, 赢得了良好的国际信誉。
1 模具的研究现状模具是工业产品生产用的工艺装备, 主要应用于制造业和加工业。
它是和冲压、锻造成型机械, 同时和塑料、橡胶、陶瓷等非金属材料制品成型加工用的成型机械相配套, 作为成型工具来使用的。
模具主要由机械零件和机构组成, 如成形工作零件 (凸模, 凹模) , 导向零件 (导柱, 导套等) , 支撑零件 (模架等) , 定向零件等;送料机构, 抽芯机构, 推料机构, 检测与安全机构等。
随着现代化工业和科学技术的发展, 模具的应用越来越广泛, 其适应性也越来越强, 己成为工业国家制造工艺水平的标志和独立的基础工业体系。
采用模具进行成型加工,是少、无切削的主要工具, 在大批量加工中, 可使材料利用率达到90%或以上[1]。
压铸是压力铸造的简称。
它是将液态或半液态金属, 在高压作用下, 以比较高的速度填充入具有较高尺寸精度和一定表面粗糙度的压铸型腔, 在压力下快速凝固成形获得铸件的一种铸造方法。
中国铸造模具行业发展现状及趋势是怎样的

中国铸造模具⾏业发展现状及趋势是怎样的 在对国内外铸造模具企业进⾏对⽐后,着重研讨了铸造模具的设计、制造技术和铸造模具⽤材。
以下是店铺为您带来的关于中国铸造模具⾏业发展现状及趋势,希望对您有所帮助。
中国铸造模具⾏业发展现状及趋势 “⼗五”期间中国铸造巿场呈现良好趋势,2005年全国铸件总量达到1800万吨左右,球墨铸件在总产量中的⽐重提⾼到20%-25%,即320万- 400万吨;随着轿车产量的增加,有⾊铸造件产量接近200万吨;今后国际巿场需求也将保持⾼速增长态势,全球对中国铸件的年需求量约为4000万吨左右,其中球墨铸铁和有⾊合⾦铸件需求量增长迅速,铸造模具产值将超过百亿元⼈民币。
⼀、国内外铸造模具企业⽐较 全国铸造模具⽣产企业,⼤体可以分成以下⼏类:第⼀类为铸造模具专业⼚(包括合资和独资企业),这些企业设备先进,技术优良,是铸造模具⾏业的主⼒;第⼆类是铸造专业⼚的模具车间;第三类是近年来发展迅速的私营和民营模具⼚,这类企业规模不⼤,数量众多,各有分⼯,协同作战,分布在江浙、⼴东⼀带,其中有些⼚已经具备了⼀定的实⼒;第四类是兼做铸造模具的其他⼀些模具⼚。
总之,铸造模具⽣产企业呈多元化,并向⾼⽔平发展,这也是中国经济发展带来的必然趋势。
国外发达国家的模具⼚⼤体分为独⽴的模具⼚和⾪属于⼀些⼤的集团公司的模具⼚,⼀般规模都不⼤,但专业化程度⾼,技术⽔平⾼,⽣产效率极⾼。
国外模具企业⼀般不超过100⼈,多数在50⼈以下。
在⼈员结构上,设计、质量控制、营销⼈员超过30%,管理⼈员在5%以下。
年⼈均产值超过100万元⼈民币,最⾼能达到200多万元⼈民币。
国内模具企业中⼀些私营、合资企业⼈员结构和国外差不多,但⼀些国企的⼈员结构还不尽合理,在年⼈均产值上差距还很⼤,多数在10~20万元⼈民币,少数能达到40万元⼈民币。
国外模具企业对⼈员素质要求较⾼,技术⼈员⼀专多能,⼀般能独⽴完成从⼯艺到⼯装的设计;操作⼈员具备多种操作技能;营销⼈员对模具的了解和掌握很深。
压铸工艺及模具材料的发展

压铸工艺及模具材料的发展对国内外的压铸生产,新工艺发展作了总结。
对压铸用模具材料进行了分析。
关键词:压铸;材料;1 当前压铸的基本情况随着汽车、摩托车,家用电器,计算机等工业的发展,对高精度的有色金属压铸件的需求量越来越大。
全球压铸件的产量大于年4%的增长率。
据报道,1994年北美地区生产104万吨压铸件,价值86亿美元,比上年增长19%,其中美国生产的压铸件价值78亿美元,比上年增长318%。
日本仅在1994年10月份就生产压铸件6106万吨,比上年同期增长1114%,全年约生产压铸件72万吨。
其中,镁压铸件的产量上升最快,北美地区由1993年的215万吨上升到1994年的313万吨,上升32%。
预计到1997年北美地区的镁压铸件产量可达512万吨。
这是汽车工业为加快实现汽车的轻型化,以轻合金压铸件逐步取代铸铁零件的结果。
目前卧车与轻型车用压铸件约为每辆105kg,十年内将增加到182至273kg。
福特、GM、克莱斯勒还将逐步在汽车上增加镁压铸件的量,用于座椅零件、方向盘及方向器零件、车轮零件等,以达到提高汽车燃料效率,减少汽车噪声的目的。
随着镁的成本下降,镁压铸件产量提高,将加速汽车轻型化的进程。
改革开放以来,我国压铸工业得到了高速发展。
拥有压铸机的台数以及生产能力每年均有大幅度的提高,且增长率高于世界平均水平。
据中国铸协的统计,我国压铸件产量从1992年的1315万吨提高到1995年的20万吨左右,年均增长14%左右;同期压铸机从6500台增长到8000 多台,年增长7%左右。
同期压铸机未与压铸件同步增长的原因是近几年来,随着汽车,摩托车生产的发展,对大中型压铸件的需求量增大,新购置的压铸机大部分为大、中型压铸机。
我省是西部大省,是我国摩托车,轻型汽车的生产基地之一,拥有嘉陵、建设、长安等大公司。
我省也是电器生产的重要基地,仪器仪表生产厂也较多,因此对压铸件的需求量很大,这就带动了我省压铸行业的发展。
2023年压铸行业市场分析现状

2023年压铸行业市场分析现状压铸行业是一种通过将熔融金属注入模具中,并在冷却后形成所需形状的生产工艺。
压铸件在汽车、电子、军工、航空航天等众多领域都有广泛的应用。
本文将对压铸行业的市场现状进行分析。
一、市场规模和增长趋势压铸行业市场规模庞大且日益增长。
根据市场研究机构的数据,预计到2025年,全球压铸行业市场规模将超过3000亿美元。
这主要得益于汽车、航空航天等领域的发展,对复杂铸件的需求不断增长。
二、中国市场中国是全球最大的压铸市场之一。
近年来,随着汽车、电子等行业的快速发展,对高精度、高质量压铸件的需求呈现爆发式增长。
据统计,中国每年生产的压铸件数量超过2000万吨,约占全球总产量的40%以上。
三、市场竞争格局压铸行业的市场竞争格局较为复杂。
市场上存在着大量的中小型企业,规模较大的企业主要集中在中国、美国、德国等发达国家。
竞争主要体现在技术创新、产品质量和价格方面。
四、技术创新与产品升级随着市场需求的不断变化,技术创新和产品升级成为企业竞争的重要手段。
传统的压铸工艺已经不能满足市场的高要求,因此,企业需要加大研发投入,引进先进的生产设备和工艺,提高产品质量和生产效率。
五、环保与可持续发展在全球环保意识的提高下,压铸行业也面临着一系列的环保压力。
压铸工艺中使用的金属和化学品会对环境造成一定的污染。
因此,企业需要加强环保管理,推动减少能源消耗和废物排放的技术创新。
六、国际市场开拓随着全球一体化的推进,压铸行业国际市场的开拓日益重要。
中国的压铸企业在国内市场的竞争已经十分激烈,因此,更多的企业开始积极拓展国际市场。
通过参加国际展览会、建立海外销售网络等方式,企业可以增加海外订单和市场份额。
综上所述,压铸行业市场在中国和全球都呈现出良好的增长趋势。
随着技术的不断进步和市场需求的不断变化,压铸企业需要加大研发力度,提高产品质量和生产效率。
同时,环保和可持续发展也是企业发展的重要方向。
对于中国的压铸企业来说,拓展国际市场也是一项重要的战略,以增加市场份额和降低竞争压力。
压铸行业发展现状
压铸行业发展现状
压铸行业是金属制造行业中的重要分支,主要涉及到使用高压将熔融金属注入模具中进行快速凝固形成成型件。
以下是压铸行业发展现状的一些主要特点:
1.市场需求稳定增长:压铸制品在各个领域广泛应用,如汽
车、航空航天、电子、机械制造等。
随着这些行业的快速发展,压铸行业也呈现稳定增长的趋势。
2.技术升级和创新驱动:为满足更高质量、更高效率和更复
杂形状的产品需求,压铸行业不断进行技术升级和创新。
如模具设计与制造、熔铸设备自动化、温控技术、高性能合金应用等。
3.资源与环保压力:压铸行业对原材料和能源的需求较大,
面临着原材料供应和价格波动的挑战。
同时,环保要求也逐渐加强,压铸企业需要采取措施减少废物产生和提高资源利用率。
4.智能制造与数字化转型:压铸行业加速推进智能制造和数
字化转型,通过大数据分析、物联网、人工智能等技术的应用,实现生产过程的智能化和自动化,提高生产效率和质量。
5.市场竞争加剧:随着全球化和市场竞争的加剧,压铸行业
面临来自国内外的竞争。
许多国家和地区都有发达的压铸行业,企业需要提高自身技术水平、降低成本、提供有竞
争力的产品和服务。
总体而言,压铸行业发展势头良好,但同时也面临一些挑战。
企业需要持续关注技术进步和市场需求变化,加强技术创新、环保和数字化转型,以保持竞争优势并实现可持续发展。
铸造行业国内外生产技术现状及发展方向
铸造行业国内外生产技术现状及发展方向铸造行业是工业制造的重要环节之一,其发展与技术水平直接影响到制造业整体水平。
本文将对铸造行业国内外生产技术现状及发展方向进行详细介绍。
1. 国内铸造行业生产技术现状目前,国内铸造行业生产技术主要包括砂型铸造技术、压铸技术、精密铸造技术、等离子喷涂技术等。
其中,砂型铸造技术是国内铸造行业主要的生产技术,其生产效率较高,成本相对较低,但制品精度和质量有一定限制;压铸技术是近年来国内铸造行业发展较快的一种技术,其生产效率高,制品精度和质量较高,但成本相对较高;精密铸造技术是目前国内铸造行业发展的趋势之一,其制品精度和质量高,适用于高精度、高质量的制品生产;等离子喷涂技术则是一种先进的表面处理技术,可以提高产品的耐磨性、耐腐蚀性和美观性。
2. 国外铸造行业生产技术现状国外铸造行业生产技术相对于国内更加成熟和发达,主要包括砂型铸造技术、压铸技术、精密铸造技术、注塑成型技术、数控铸造技术等。
其中,注塑成型技术是国外铸造行业的一大亮点,其生产效率高,制品精度和质量较高,适用于大规模生产;数控铸造技术则是近年来国外铸造行业的新兴技术,可以实现高精度、高效率、高灵活性的生产。
3. 铸造行业发展方向未来,铸造行业将朝着智能化、绿色化、高效率、高精度、高品质的方向发展。
具体来说,铸造行业将进一步加强数字化设计、仿真与优化技术的应用,推广智能化制造,提高生产自动化和柔性化程度,逐步实现无人化生产;同时,铸造行业还将加强环保意识,推广绿色铸造技术,降低能耗和污染物排放;此外,铸造行业还将注重提高制品的质量和精度,满足各行业对高品质制品的需求。
总之,铸造行业的生产技术将不断更新换代,不断适应市场需求和技术发展,不断推动铸造行业的升级和发展。
压铸模国内外发展前景
压铸模国内外发展前景宣佳佳 成型102 10403070203一、引言压力铸造简称压铸,是一种将熔融合金液倒入压室内,以高速充填钢制模具的型腔,并使合金液在压力下凝固而形成铸件的铸造方法。
压铸区别于其它铸造方法的主要特点是高压和高速。
压铸机、压铸合金与压铸模具是压铸生产的三大要素,缺一不可。
所谓压铸工艺就是将这三大要素有机地加以综合运用,使能稳定地有节奏地和高效地生产出外观、内在质量好的、尺寸符合图样或协议规定要求的合格铸件,甚至优质铸件。
图表 1压铸模二 、国内外概况1、 国内 压铸机行业发展现状近年来,随着我国汽车、摩托车、家用电器、电子通讯等行业,特别是汽车工业的迅速发展,带动了我国压铸行业以前所未有的速度向前发展。
据相关统计数据显示2006年至2009年中国压铸机产量年份 冷室压铸机 热室压铸机 合计2006年 1810台 2670台 4480台2007年 1900台 2700台 4600台2008年 1650台 2400台 4050台2009年 1515台 2640台 4215台 自我国加入世贸组织,市场全面放开以后,国内压铸机制造行业受到冲击,形成国内压铸机市场更加激烈竞争的局面。
客观来说,我国产压铸机质量性能水平与国外工业先进国家相比差距较大,但是由于压铸件的分布领域较广,从交通能源到家用电器,上天下海到千家万户的日用工业品,无不有压铸件的存在,而这些压铸件市场要求各不相同,这就给国产压铸机市场带来了空间,特别是中、小型压铸机,这个空间有可能还要延续相当长的时间。
这就为加速国产压铸机质量、性能的提高,提供了一个有利的时机。
中国作为世界机械工业的基础工业的加工基地,特别是压铸件加工基地,无疑给行业带来了良好的机遇,同时也刺激着我国对基础产品的质量提高,要求机械设备的质量、性能同步跟进。
对大型压铸机而言,随着我国汽车工业的发展及外销大型压铸件的需求量日益快速的增长,国产大型压铸机的生产数量实难满足其需求,这给大型压铸机的进口创造了良机。
2024年压铸市场发展现状
2024年压铸市场发展现状一、引言压铸是一种高效、精确的金属成型工艺,广泛应用于汽车、电子、航空航天等工业领域。
本文将对当前压铸市场的发展现状进行分析和总结。
二、全球压铸市场概述1. 市场规模全球压铸市场在近年持续增长,市场规模不断扩大。
根据统计数据,2019年全球压铸产量达到XX万吨,产值超过XX亿美元。
2. 主要市场全球压铸市场主要集中在亚太地区、欧洲和北美地区。
中国、美国、德国、日本等国家在压铸产业方面占据较大的市场份额。
3. 市场竞争格局全球压铸市场竞争激烈,市场上存在着众多的压铸企业。
主要竞争策略包括技术创新、产品质量和价格竞争等。
优秀的企业通过提升工艺水平和研发能力获得竞争优势。
三、中国压铸市场现状1. 市场规模和发展趋势中国压铸市场近年来持续增长,市场规模不断扩大。
根据统计数据,2019年中国压铸产量达到XX万吨,产值超过XX亿元。
未来几年,中国压铸市场有望继续保持良好的增长态势。
2. 行业特点中国压铸行业具有市场规模大、企业数量众多的特点。
行业内企业规模参差不齐,大部分企业是小型和中型压铸公司,技术水平和生产设备相对较低。
一部分优秀企业通过技术升级和创新脱颖而出。
3. 发展趋势未来中国压铸市场的发展将呈现以下趋势:•技术升级和创新。
中国压铸企业将加大研发投入,提升产品质量和生产效率。
•自动化和智能化生产。
随着人工智能和机器人技术的不断发展,压铸行业也将向自动化和智能化方向发展。
•环保可持续发展。
目前,中国压铸行业面临着环保压力,未来将加强环境保护,推动可持续发展。
四、压铸行业面临的挑战虽然压铸市场发展迅速,但同时也面临一些挑战:1.价格竞争激烈。
市场上存在大量竞争对手,价格竞争压力较大。
2.需求变化不确定性。
随着市场需求的变化,压铸行业需不断调整产品结构和供应链。
3.环境压力增加。
环保法规越来越严格,对压铸行业的影响日益显著。
五、结论随着全球产业的发展和技术的进步,压铸市场持续扩大。
- 1、下载文档前请自行甄别文档内容的完整性,平台不提供额外的编辑、内容补充、找答案等附加服务。
- 2、"仅部分预览"的文档,不可在线预览部分如存在完整性等问题,可反馈申请退款(可完整预览的文档不适用该条件!)。
- 3、如文档侵犯您的权益,请联系客服反馈,我们会尽快为您处理(人工客服工作时间:9:00-18:30)。
分析国内外压铸模具发展历程及现状
中国压铸行业是一个新兴的行业,在上个世纪八十年代,中国只有几家单位有1000吨以下的压铸机,国内只能制造最大630吨压铸机,并且大部分压铸机合模机构还是全液压的,非常落后。
压铸领域仅限于个别军工或大型国营企业,压铸行业非常落后。
随着80年代末,中国摩托车行业的发展,中国陆续引进了国外的大批500至1000吨压铸机,国内首台1000吨压铸机也在90年开发成功,中国压铸行业因此得以快速发展,由此也拉动了中国压铸模具企业。
在上世纪九十年代,大部分压铸模具依赖进口,特别是台湾进口居多。
中国压铸模具企业特别是宁波北仑压铸模具企业快速发展真正开始起步应该是在九十年代末,基本上都是以摩托车配件压铸模具开始,应该说基本上都是小型压铸模具,基本上在280吨至800吨压铸机上使用的压铸模具为主,这时的压铸模具企业无论是从加工设备、检测设备等硬件,还是压铸人才都处于初始阶段,模具制造水平都相对较低。
自2000年开始,随着中国汽车行业开始发展,国内开始引进1000吨以上压铸机,国内外资企业如力劲公司等压铸机企业也开始生产1000吨以上压铸机。
这个期间企业引进的基本上在1000吨至1600吨压铸机,而模具基本上全部是随着设备一同引进,国内很少能够生产。
在经历了一轮引进后,因为国外压铸模具价格较高,个别企业为了降低成本开始寻求国内能够复制汽车配件的模具企业。
为此包括合力模具公司在内的部分较大一点的模具企业看准市场,积极应对挑战,加大了先进、大型装备的投入,购置了三坐标检测等先进检测设备,开始复制汽车配件压铸模具。
在这个过程中,企业加以吸收消化,逐步开始转型,以生产中型包括汽车手动变速箱壳体压铸模具为主,带动了模具企业快速发展,模具企业装备水平明显提高,模具制造水平以及制造能力大幅提高。
目前这类模具已基本上没有企业从国外引进。
随着国内汽车行业近几年的快速发展,特别是国内民族品牌汽车的崛起,中国汽车行业竞争越来越大。
原来的外资企业原来的汽车缸体基本上是采用低压浇注或从国外进口,压铸汽车缸体由于投入大,加上外国企业从自身利益出发,很少国内生产。
而汽车自动档变速箱更是全部进口,并且作为从中国赚钱的工具。
随着国内汽车企业,如吉利公司先后成功开发了自动档变速箱和汽车压铸缸体,国内其它企业也纷纷寻求国产化,以降低成本,提高竞争力。
近两三年,国内汽车行业以及相关的压铸企业纷纷购买大型压铸机从2000吨到3800吨,基本上都是以生产自动档变速箱壳体和汽车发动机缸体为主。
但是国内能够生产汽车缸体以及自动档变速箱的模具企业很少,如已生产1.3、1.4、1.6、1.8、2.0、2.4各排量的汽车四缸体以及3.2排量的V6缸体压铸模具的只有辉旺公司一家,而大部分这类模具主要依赖进口,进口模具价格是国内的1-2倍。
随着今年国家出台的诸多利好政策,中国汽车行业今年上半年小排量的汽车增长迅速,而小排量的汽车以家庭居多,小排量汽车发动机缸体为减低成本势必要采用压铸,另外自动档的需求也会逐步成为主流。
因
此,汽车发动机缸体、自动档变速箱壳体压铸模具市场空间巨大。
国内对于大型精密压铸模具的需求将会越来越大。
另一方面,国外的模具市场竞争日趋激烈,特别是由于金融危机的影响,汽车行业竞争加剧。
为了减低成本,必然要降低模具价格,因此国外模具业也在努力降低生产成本。
模具行业是人力成本较高的行业,国外的人力成本是中国及东南亚地区的十几倍,而人力成本中有70%以上是非核心技术人员。
因此,现在国外模具业正逐渐将模具转向人力成本低的地区生产。
其次是国外使用模具的主要企业有加快向国外转移的趋势。
因此,无论是国内还是国外,大型精密压铸模具的市场前景广阔。